文章编号: 1004-0609(2005)08-1200-08
铝合金铸件充型过程及氧化膜卷入的数值模拟
赵海东1, I. Ohnaka2
(1. 华南理工大学 机械工程学院, 广州 510640; 2. 大阪大学 智能工学系, 大阪 5650871)
摘 要: 对于直接有限差分法, 提出了单元表面无量纲距离、 表面充填比率和体积充填比率, 以描述铸件充型过程中自由表面的形状, 建立了相应的充型过程数学模型, 考虑了自由表面形状对动量、 质量和能量传输的影响; 提出了充型过程自由表面碰撞中表面氧化膜破碎, 及其后破碎氧化膜流动的计算模型。 对实验铝合金铸件进行了模拟应用, 通过实际铸件充型过程的特殊X射线实时观察和记录, 及实际铸件的气孔、 收缩缺陷分布的检测, 对模拟结果进行了验证分析。 结果表明: 充型过程模拟结果与X射线实时观察结果吻合较好, 尤其是自由表面的变化; 氧化膜卷入模拟结果与实际铸件气孔、 收缩缺陷的分布存在一定的对应关系。
关键词: 铝合金铸件; 充型过程; 自由表面; 氧化膜卷入; X射线实时观察; 数值模拟
中图分类号: TG24
文献标识码: A
Numerical simulation of oxide entrapment and mold filling process of Al casting
ZHAO Hai-dong1, I. Ohnaka2
(1. College of Mechanical Engineering,South China University of Technology, Guangzhou 510640, China;
2. Department of Adaptive Machine Systems,Osaka University, Osaka 5650871, Japan)
Abstract: Surface dimensionless distance, surface filled ratio and volume filled ratio for the direct finite difference method(DFDM) elements were proposed to describe the shape and position of free surface in simulation of mold filling process. The model of the process, taking into account the effect of free surface on transfer of momentum, mass and energy, was established. The method of estimating the breakup of oxide films on free surfaces during collision of the surfaces as well as judging movement of the entrapped broken oxide films was proposed. The model and method were applied to an experimental Al casting. By in-situ observation and recording actual mold filling process of the casting with special X-ray apparatus, and measuring porosities of the casting, the simulation results were further verified and analyzed. The simulation results indicate that mold filling are in good agreement with in-situ X-ray observation, especially in the evolution of free surface, and that the simulation results of entrapped oxides has some relationships with the distribution of porosities in the actual casting.
Key words: Al casting; mold filling; free surface; oxide entrapment; in-situ X-ray observation; numberical simulation
铸件充型过程的数值模拟对于优化设计铸件和铸型结构、 浇注系统及工艺参数具有重要意义, 已成为当前铸造过程数值模拟的热点。 虽然研究者对此进行了大量的研究, 但是, 在VOF(volume of fluid)方法中, 如何准确描述自由表面的形状和位置及考虑其对流体流动的影响, 需要进一步深入的研究和验证[1-5]。 铝合金铸件充型过程中, 液态金属流体自由表面通常覆盖有氧化膜, 在发生自由表面间或自由表面与型壁碰撞时, 这些氧化膜将发生破碎, 并随液态金属流至铸件不同部位, 发生氧化膜卷入而形成氧化膜夹杂物[6]。 在其后的凝固过程中, 这些氧化膜可以作为气孔的异质形核基底和影响铸件的补缩, 促进气孔和收缩缺陷的形成, 严重降低了铸件的力学性能[7-9]。 研究工作者对该氧化膜卷入的模拟研究工作刚刚开展[10-12]。
本文作者对直接有限差分法(direct finite difference method, DFDM)单元提出了表面无量纲距离、 表面充填比率和体积充填比率, 以描述充型过程中自由表面的形状和位置, 建立了相应的充型过程模型; 通过判断自由表面的碰撞, 提出了氧化膜破碎与卷入, 及破碎氧化膜随液态金属流动的数学模型, 以预测充型过程氧化膜的卷入。 对实验铝合金铸件进行了模拟应用, 使用特殊X射线装置对该铸件实际充型过程及自由表面进行了实时观察验证, 对氧化膜卷入的模拟结果进行了验证分析和讨论。
1 充型过程的数学模型
1.1 自由表面的描述
在使用DFDM进行充型过程模拟中, 为了描述自由表面在单元中的形状和位置(图1), 将自由表面近似处理为与单元的表面平行, 并提出了如下单元变量[13]:
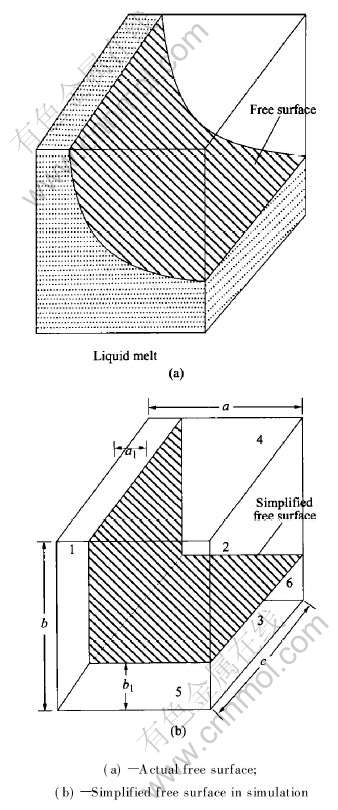
图1 自由表面描述的示意图
Fig.1 Schematics of description of free surface(1-6 are six surfaces)
1) 表面无量纲距离βD, k(k=1, 6), 指自由表面距离单元各个表面的距离与单元在垂直于该表面方向的垂直距离的比;
2) 表面充填比率βS, k(k=1, 6), 指液体金属流体在单元各个表面所充填的面积与该表面面积之比;
3) 体积充填比率βV, 指单元液态金属流体所充填的体积与单元体积之比。
对于未充满的单元表面, 其表面无量纲距离为0。 对于液态金属流体完全未充填单元, 其上述所有单元变量均为0; 对于完全充满的单元, 其表面无量纲距离为0.5, 而其他变量均为1.0。
以图1为例, 上述各变量计算如下:
βD, 1=a1/a, βD, 3=b1/b, βD, 2=βD, 4=0,
βD, 5=βD, 6=0, βS, 1=1, βS, 2=b1c/(bc),
βS, 3=1, βS, 4=a1c/(ac),
βS, 5=βS, 6=(a1b+b1a-a1b1)/(ab)
βV=(a1bc+b1ac-a1b1c)/(abc)
1.2 动量守恒
对于DFDM单元, 充型过程动量方程可以离散为[14]

根据上述自由表面的描述方法, 考虑自由表面对动量传输的影响, 对式(1)进行改进, 得出充型过程的动量方程式(2):
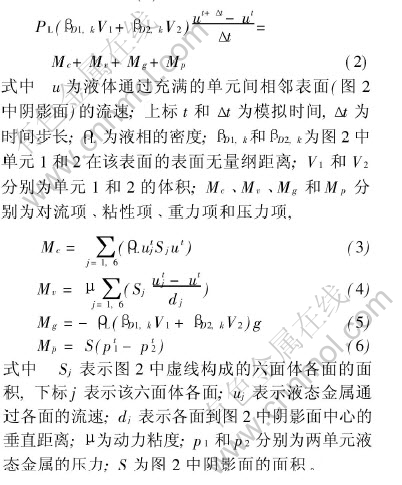
可按如下公式计算:
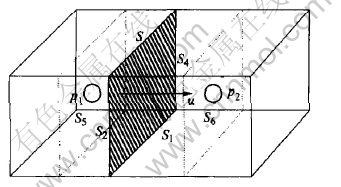
图2 充型过程动量守恒示意图
Fig.2 Schematics of momentum conservation during mold filling
1.3 质量守恒
忽略充型过程液体金属密度的变化, 考虑自由表面在单元中的形状和位置, 结合上述定义的单元变量, 液体金属流动所引起的单元质量变化可以表示为

式中 V为DFDM单元的体积, 下标i为单元编号; S为单元表面的面积, 下标k为单元6个面的编号; n为流动方向指数(流入为1, 流出为-1)。
1.4 能量守恒
由液体金属流动、 单元间的传热所引起的流体单元温度变化可求解为
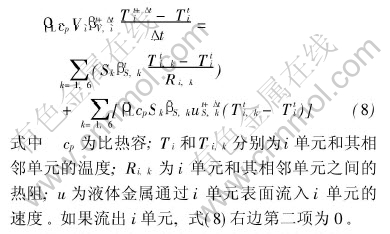
铸型单元之间及其与液态金属流体间的传热可计算为
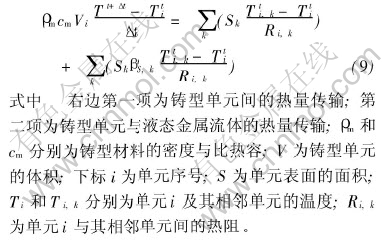
2 氧化膜卷入的数学模型
由于液态铝合金非常容易氧化的特性[15], 因此, 假设充型过程液态铝合金流体自由表面始终覆盖有氧化膜(图3)。 当发生自由表面间以及自由表面与型壁碰撞时, 自由表面氧化膜均将发生不同程度的破碎, 破碎后的氧化膜存在于自由表面碰撞处, 其后随碰撞处液态金属流动至铸件的不同部位, 发生氧化膜的卷入。
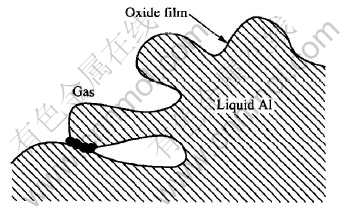
图3 充型过程氧化膜卷入的示意图
Fig.3 Schematic diagram of oxide entrapment during mold filling
2.1 氧化膜的破碎
如图4所示, 对充型过程中自由表面间以及自由表面与型壁碰撞进行判断, 由于自由表面氧化膜的破碎程度取决于合金特性和相对碰撞的速度[16], 本文作者提出通过下式计算碰撞后破碎氧化膜的密度[10]:
Nis=α1|ujs1-ujs2|+α2(10)
式中 Nis为破碎氧化膜的密度, 表示碰撞中氧化膜破碎的程度, m-2; α1和α2为与液态金属合金特性相关的系数, 其量纲分别为s/m3和m-2; ujs1和ujs2为发生碰撞自由表面的流动速度; ujs1-ujs2为碰撞的相对速度。 因此, 破碎氧化膜的平均大小可描述为
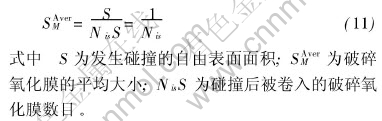
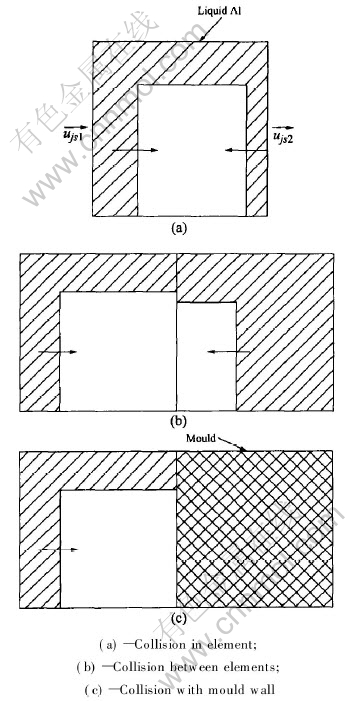
图4 充型过程自由表面碰撞示意图
Fig.4 Schematic diagram of collision of free surfaces during mold filling
2.2 破碎氧化膜的流动
在液固两相流中, 当固相粒子尺度较小且固相粒子密度比液相高出不多的情况下, 可以认为该液固两相流为均质流[17]。 研究表明, 铸件中卷入的氧化膜尺寸通常在几十个至几百个微米范围[6-9], 因此, 模拟中认为碰撞后的破碎氧化膜与液态金属流体发生均质流, 流动至铸件不同部位, 发生氧化膜卷入。 破碎氧化膜的流动由所在单元液态金属的流动所决定:
lv=uvΔt(12)
式中 lv为破碎氧化膜的移动距离, 下标v表示x、 y和z方向; uv为氧化膜所在单元液态金属流体在各方向的分速度。
3 模拟应用及验证
使用所建立的数学模型对图5的实验铝合金铸件进行了模拟应用。 实验中铸件材质为AC4C(日本牌号), 铸型材质为普通硅砂, 在普通重力条件下采用自动浇包进行浇注, 浇注温度为720℃。 由于在普通重力条件下浇注充型, 同时根据浇包浇注口距离直浇道入口距离为0.1m, 因此在模拟中将直浇道的上表面设置为压力边界, 其压力为:
pb=pLgh=2.33×104 Pa(13)
式中 Pb为直浇道入口处的边界压力; ρL为铝合金液态金属的密度; h为自动浇注口距离直浇道入口的距离。 根据计算得到的卷入氧化膜尺寸分布, 得出AC4C铝合金α1和α2的合适取值分别约为1×108s/m3和2×103 m-2。 模拟中使用的其他热物性参数如表1所示。
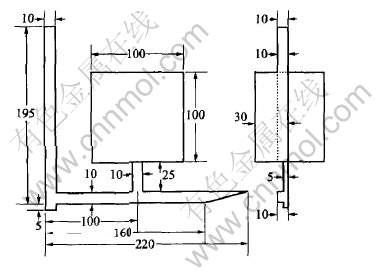
图5 实验铝合金铸件的形状和尺寸
Fig.5 Shape and dimensions of experimental Al casting(mm)
表1 模拟中使用的热物性参数
Table 1 Thermal-physical data used in simulation

3.1 充型过程模拟及验证
图6所示为实验铝合金铸件充型过程中液态金属流动与自由表面的模拟结果。 为了观察和记录实验铝合金铸件的实际充型过程, 制作了一套特殊X射线装置。 其中, X射线的电压为190kV、 电流为9mA, 小焦点时最大输出功率为640W, 大焦点时最大输出功率为3000W, 观察范围大小为90mm×90mm, 采用每秒可记录250~2000幅图像的高速摄像记录仪进行图像记录, 为了跟踪充型过程中自由表面的移动, X射线发生器和图像记录装置可以以0.01~0.20m/s的速度在水平和垂直方向移动。 图7所示为观察到的实验铸件实际充型过程。
X射线直接观察结果(图7(a))和模拟结果(图8(a))均表明液态金属流体在通过内浇口后, 其流向为略偏直浇道方向的垂直地流向上方。 图7(b)中箭头所示位置可能存在气体卷入现象, 图8(b)的模拟结果表明了在相近的位置存在着气体被自由表面包围。 由于铸件采用了压力式浇注系统(直浇道底部面积∶横浇道面积∶内浇道面积=1∶2∶1), 图6表明在型腔充满一半时, 充型自由表面前方存在的半球形突出, 而其下方的型腔处于充满状态, 因此, 在图7(c)所示的X射线图像上, 半球形突出部为浅黑色, 底部充满部分吸收了较多的X射线, 所以其显示为深黑色。 而当型腔大部分被液态金属充满后, 受到该部分液态金属的作用, 液态金属动量损失增加, 液态金属通过内浇口后难以使得自由表面形成较大的半球形突出(图7(d)和图8(d))。
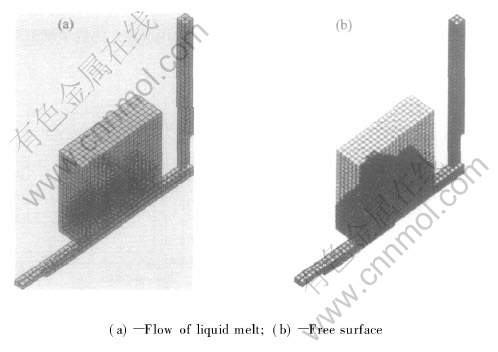
图6 实验铸件充型过程中液态金属流动与自由表面的模拟结果
Fig.6 Simulation results of liquid melt flow and free surface during mold filling of casting
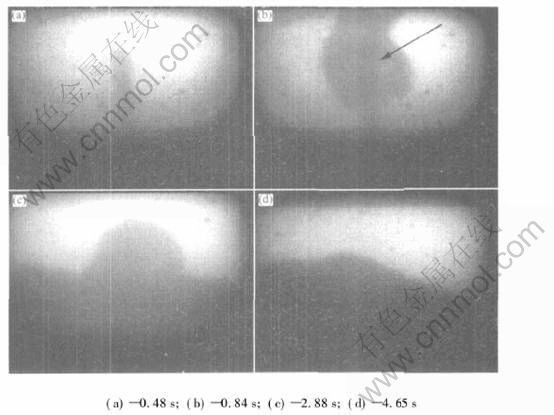
图7 实验铸件充型过程X射线实时观察
Fig.7 In-situ X-ray observation of mold filling of casting
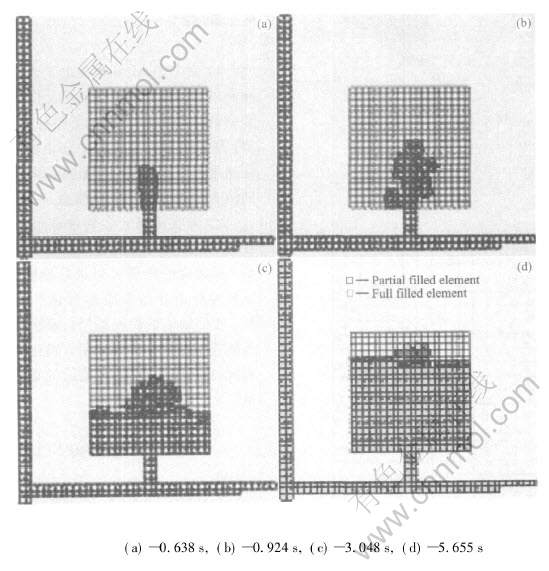
图8 实验铸件充型过程的模拟结果
Fig.8 Simulation results of mold filling of casting
上述验证和分析表明, 本文所建立的模型可以较好地模拟铸件充型过程, 及该过程中自由表面的变化。
3.2 氧化膜卷入的模拟
图9所示为实验铸件氧化膜卷入过程的模拟结果, 图10所示为充型结束后铸件中心截面氧化膜卷入的模拟结果。 由于氧化膜的很薄, 直接进行氧化膜的定量验证目前尚存在一定难度。 研究表明[8, 9], 在铝合金铸件中, 气孔和收缩缺陷优先在卷入的氧化膜上形核和生长, 这些缺陷位置通常存在着氧化膜。 实际铸件中心截面的致密度检测(图11)表明, 中心截面右上部分气孔和收缩缺陷最多, 其次依次是左上、 下部两侧, 中心部分较少, 这与图10所示的氧化膜卷入数量模拟结果顺序相同。
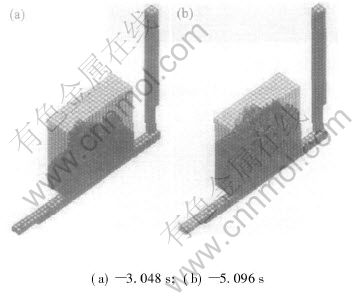
图9 充型过程氧化膜卷入的模拟结果
Fig.9 Simulation results of oxide entrapment during mold filling
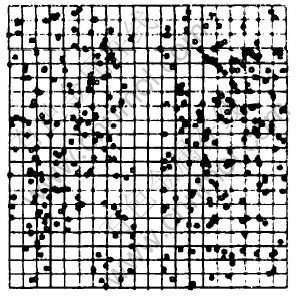
图10 充型完毕后氧化膜卷入的模拟结果
Fig.10 Simulation results of oxide entrapment after mold filling

图11 铸件致密性的定性检测
Fig.11 Qualitative measurement of porosities in casting
4 结论
1) 对DFDM单元提出了表面无量纲距离、 表面充填比率和体积充填比率, 以描述自由表面在单元中形状和位置, 建立了相应的充型过程数学模型; 通过判断充型过程中自由表面的碰撞, 提出了碰撞中自由表面氧化膜破碎及卷入, 及破碎氧化膜随液态金属流动的数学模型。
2) 对实验铝合金铸件进行了模拟应用和验证分析。 实际铸件充型过程的X射线实时观察验证表明, 所建立的模型可以较好地模拟铸件充型过程, 及该过程中自由表面的变化; 采用实际铸件的气孔、 收缩缺陷的检测结果, 定性地验证了氧化膜卷入的模拟结果。 结果表明, 氧化膜卷入模拟结果与实际铸件气孔、 收缩缺陷的分布存在一定的对应关系。
REFERENCES
[1] Mirbagheri S M H, Shrinparvar M, Ashory H, et al. Simulation of surface roughness on the flow pattern in the casting process[J]. Materials and Design, 2004, 25(8): 655-661.
[2] Lee S L, Sheu S R. A new numerical formulation for incompressible viscous free surface flow without smearing the free surface[J]. International Journal of Heat and Mass Transfer, 2001, 44(10): 1837-1848.
[3] Cleary P, Ha J, Alguine V, et al. Flow modelling in casting processes[J]. Applied Mathematical Modelling, 2002, 26(2): 171-190.
[4] Shin S, Lee W. Finite element analysis of incompressible viscous flow with moving free surface by selective volume of fluid method[J]. International Journal of Heat and Fluid Flow, 2000, 21: 197-206.
[5] 周彼德, 薛 祥, 糜忠兰, 等. 铸件三维充型过程耦合的数值模拟[J]. 中国有色金属学报, 2000, 10(2): 230-233.
ZHOU Bi-de, XUE Xiang, MI Zhong-lan, et al. 3D coupling simulation of mold filling[J]. The Chinese Journal of Nonferrous Metals, 2000, 10(2): 230-233.
[6] Campbell J. Castings[M]. 2nd ed. Oxford: Butterworth Heinemann, 2003. 52-150.
[7] Dai X, Yang X, Campbell J, et al. Influence of oxide film defects generated in filling on mechanical strength of aluminium alloy castings[J]. Materials Science and Technology, 2004, 20(4): 505-513.
[8] Fox S, Campbell J. Visualization of oxide film defects during solidification of aluminium alloys[J]. Scripta Materials, 2000, 43(10): 881-886.
[9] Liu L, Samuel A M, Samuel F H, et al. Influence of oxides on porosity formation in Sr-treated Al-Si casting alloys[J]. Journal of Materials Science, 2003, 38(6): 1255-1267.
[10] Zhao H D, Ohnaka I, Sako Y, et al. Estimation of porosity defects with consideration of oxide entrapment[A]. Hong C P. The 65th World Foundry Congress[C]. Korea: The Korean Foundrymens Society, 2002. 749-754.
[11] Lai N W, Griffiths W D, Campbell J, et al. Modelling of the potential for oxide film entrainment in light metal alloy castings[A]. Stefanescu D. Modeling of Casting, Welding and Advanced Solidification Processes X[C]. Destin: The Minerals, Metals and Materials Society, 2003. 415-422.
[12] Griffiths W D, Lai N W. Mould filling: the critical ingate velocity for aluminium and magnesium alloy castings[J]. Foundry Trade Journal, 2004, 178(10): 344-348.
[13] Zhu J D, Ohnaka I. Three dimensional computer simulation on mold filling of casting by direct finite difference method[J]. Journal of Japan Foundry Engineering, 1996, 68: 668-676.
[14] Kanatani R, Ohnaka I, Zhu J D. A new algorithm of mold filling simulation using non-orthogonal elements[A]. Liu B C, Jing T. 3rd Pacific Rim International Conference on Modeling of Casting and Solidification Process[C]. Beijing: International Academic Publishers, 1996. 124-129.
[15] Divandari M, Campbell J. Oxide film characteristics of Al-7Si-Mg alloy in dynamic conditions in casting[J]. International Journal of Cast Metals Research, 2004, 17(3): 182-187.
[16] Papworth A, Fox P. Disruption of oxide defects within aluminum alloy castings by the addition of bismuth[J]. Materials Letters, 1998, 35: 202-206.
[17] Saleh J M. Fluid Flow Handbook[M]. New York: McGraw-Hill, 2002. 350-375.
基金项目: 日本产学官联合“革新的铸造模拟技术”资助项目(11305054); 教育部科学技术研究重点资助项目(105138); 教育部留学回国人员科研启动基金资助项目
收稿日期: 2005-01-21;
修订日期: 2005-04-25
作者简介: 赵海东(1970-), 男, 副教授, 博士.
通讯作者: 赵海东, 电话: 020-87113832; E-mail: hdzhao@scut.edu.cn
(编辑 龙怀中)