网络首发时间: 2017-01-19 08:27
稀有金属 2018,42(05),524-530 DOI:10.13373/j.cnki.cjrm.xy16110004
结合层对铜/铝复合材料力学性能的影响
王艳艳 刘平 刘新宽 王子延 王冰 陈小红
上海理工大学材料科学与工程学院
亚仕龙汽车科技(上海)有限公司
摘 要:
运用新型感应加热工艺, 通过固-液-固相复合法制备铜/铝复合材料。分析了结合层的成分、硬度、线膨胀系数对铜/铝复合材料机械性能的影响。用热机械分析仪对结合层线膨胀系数进行测量, 用扫描电子显微镜 (SEM) 和偏光显微镜 (PM) 观察界面形貌, 用电子探针 (EPMA) 和X射线衍射仪 (XRD) 进行物相分析, 用显微硬度计对结合层的硬度进行测量。结果表明:界面中间化合物主要为CuAl2, Cu9Al4和AlCu;不同成分的结合层具有不同的硬度值, Cu9Al4层、AlCu层和CuAl2层的硬度依次为:HV 204.5, HV 271.5, HV 233.9;铜/铝复合材料结合层线膨胀系数为27.0×10-6℃-1, 结合层与铜之间较大的线膨胀系数差是造成铜/铝复合材料经热循环后易在界面层靠近铜侧区域出现裂纹的主要原因。
关键词:
铜铝复合材料;结合层;硬度;显微组织;线膨胀系数;热循环;
中图分类号: TB331
作者简介:王艳艳 (1992-) , 女, 甘肃平凉人, 硕士研究生, 研究方向:铜铝复合材料;E-mail:yanyanwang1511@163.com;;刘平, 教授;电话:13817077795;E-mail:liuping@usst.edu.cn;
收稿日期:2016-11-02
基金:国家自然科学基金项目 (51201107) 资助;
Mechanical Properties of Copper/Aluminum Composite with Bonding Layer
Wang Yanyan Liu Ping Liu Xinkuan Wang Ziyan Wang Bing Chen Xiaohong
School of Materials Science and Engineering, University of Shanghai for Science and Technology
ASL Automobiles Science & Technology (Shanghai) Co., Ltd.
Abstract:
Copper/aluminum composite was prepared by solid-liquid-solid method using a new type of induction heating process.Effects of microstructures, hardness and thermal expansion coefficient of bonding layers on the mechanical properties of copper/aluminum composite were studied. The thermal expansion coefficient was observed by thermal mechanical analyzer. The microstructures of the interface were observed by scanning electron microscope ( SEM) and polarizing microscope ( PM) , and the interfacial reaction products were analyzed by X-ray diffraction ( XRD) and electron probe micro-analyzer ( EPMA) . The hardness was analyzed by microscope hardness tester. The results showed that the main interface reaction products of Cu/Al composite were Cu Al2, Cu9 Al4 and Cu Al, and different bonding layers had different hardness. The hardnesses of Cu9 Al4, Al Cu and Cu Al2 layer were HV 204. 5, HV 271. 5 and HV 233. 9, respectively. The thermal expansion coefficient of copper/aluminum composite was 27. 0 × 10-6℃-1, and the relatively large thermal expansion coefficient between copper and bonding layer was the main reason for the crack close to the copper side after thermal cycling.
Keyword:
copper-aluminum composite; bonding layer; hardness; microstructure; coefficient of thermal expansion; thermal cycle;
Received: 2016-11-02
世界上铝资源比较丰富, 而铜相对不足[1]。因此以铝代替部分铜, 开发铜铝复合材料, 不仅可节约铜资源, 还可使材料获得人们所需要的特性[2]。铜/铝复合材料由于同时具有铜的高导电性、高导热率、低接触电阻以及铝的质轻、耐蚀等优点, 而受到了电力、电器、冶金、汽车、机械和生活用品等领域的青睐[3,4,5,6,7,8]。目前对铜铝复合材料性能的研究大多把铜铝复合材料及结合层作为整体研究, 在国内外尚未检索到单独对结合层的性能的研究。因而制备可控厚度的铜铝复合材料结合层对于丰富结合层对铜铝复合材料性能影响的研究具有一定的意义。铜、铝复合时, 铜铝复合材料界面上会生成有某些金属间化合物组织 (如Cu Al2等) [9,10,11,12,13], 这类金属间化合物硬脆, 导致铜铝复合材料的结合强度和弯曲性能降低, 导电性变差[14,15]。通常铜铝结合界面易发生开裂, 导致铜铝复合材料的机械性能减弱, 人们普遍认为是由于Cu, Al线膨胀系数之间的差异导致冷却过程中复合界面产生较大应力的缘故。因此, 本课题运用新型感应加热工艺, 通过固-液-固相复合法制备了可控厚度的铜铝复合材料结合层, 研究了结合层的显微硬度、界面组织及线膨胀系数对铜铝复合材料强度及热疲劳的影响。
1 实验
1.1 材料
实验用焊接材料为8 mm厚的6005铝及2 mm厚的T2纯铜。采用运用新型感应加热工艺, 快速加热使铜铝结合面的温度达到铝的熔点温度, 铜铝接触面上薄层的铝融化, 在铝铜的结合面上施加一定的压力, 使铜铝材料结合而获得铜铝复合材料。图1为感应焊接工艺示意图。
热循环实验在自主开发的热循环试验机完成, 热循环试样规格为100 mm×20 mm×6 mm。其中工件的加热由一台高频感应加热装置完成, 加热温度和循环次数由CPU控制, 步进电机可实现工件由加热端向水冷端垂直位移, 实验冷却方式为水冷, 图2为循环试验台装置示意图。
1.2 方法
Cu/Al复合材料界面反应产物采用JXA-8500F型电子探针 (EPMA) 分析, 界面形貌采用Quanta型扫描电子显微镜 (SEM) 和XPL-15型偏光显微镜 (PM) 观察。
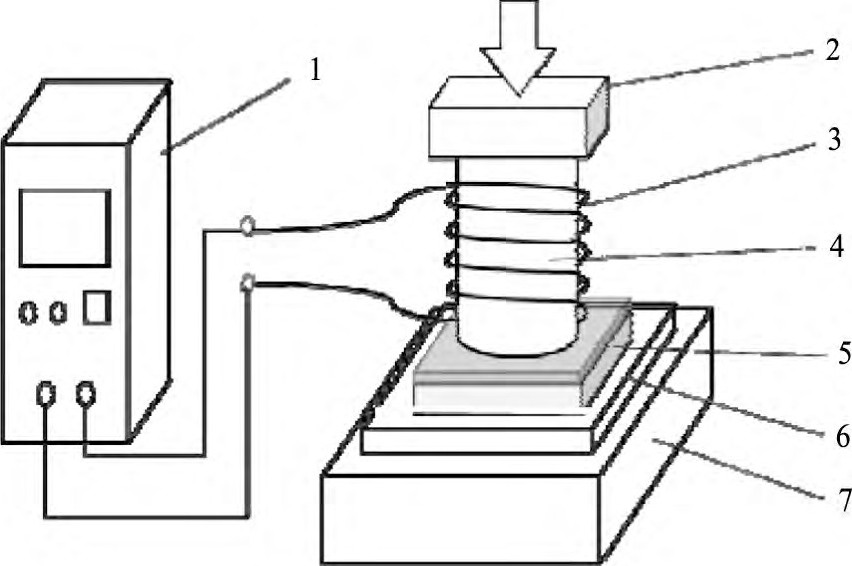
图1 感应焊接工艺示意图Fig.1 Schematic diagram of induction welding process
1-High-power high-frequency induction heater;2-Fixture;3-Induction coil;4-Magnet;5-Copper and aluminum welding parts;6-Welding mold;7-Basement
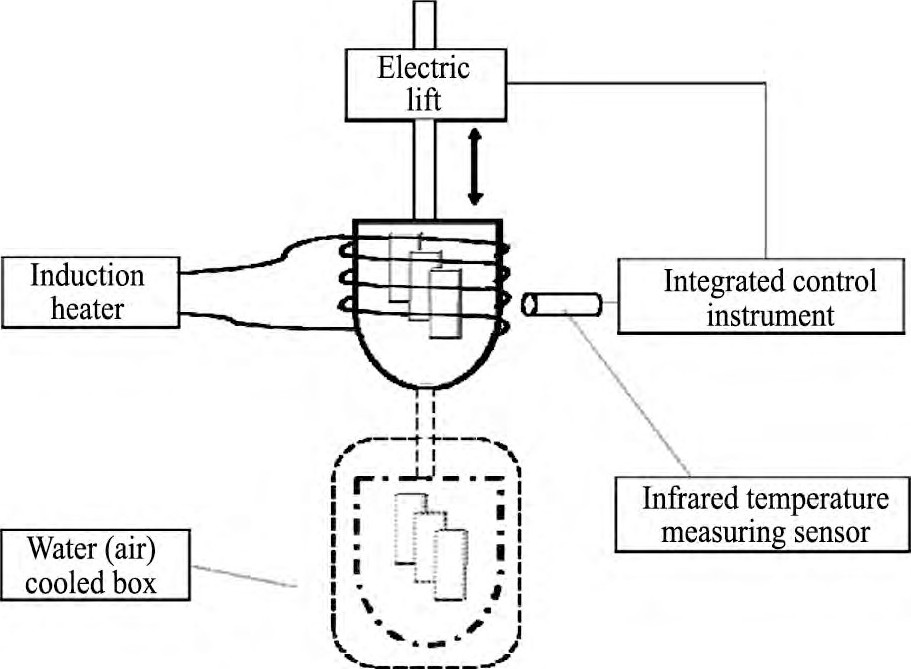
图2 循环试验台装置示意图Fig.2 Schematic diagram of circulating test bench
1.2.1 硬度测定
Cu/Al复合材料不同成分结合层硬度采用HXD-1000TMC显微硬度计测量, 载荷1.96 N, 加载时间10 s。
1.2.2 线膨胀系数测定
Cu/Al复合材料结合层线膨胀系数采用美国TAQ400型静态热机械分析仪测定, 结合层规格为6 mm×10 mm×0.86mm, 实验为压缩模式, 温度范围0~300℃, 升温速率10℃·min-1, 载荷50 m N, 采样时间0.1 s。
2 结果与讨论
实验中通过改变功率、加热温度、加热时间、施加的压力等参数, 制得不同厚度结合层的铜铝复合材料。图3为不同厚度的铜铝复合材料结合层, 图3 (a) 为微观结合层厚度, 图3 (b) 为宏观结合层厚度。
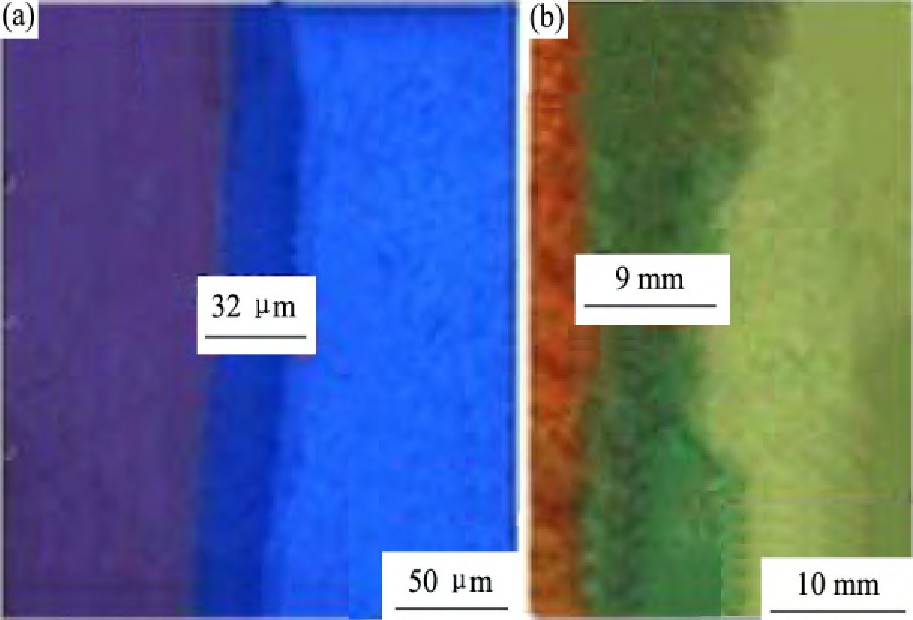
图3 铜/铝材料不同厚度的结合层Fig.3 Cu/Al bonding layers with different thicknesses
2.1 Cu/Al复合材料界面显微组织观察及成分分析
Cu/Al复合材料结合层的形成, 是因为铜铝固-液复合时发生互扩散, 形成铜铝金属间化合物过渡层。从图2中可以看出铜铝界面的结合层共分为4层。对不同扩散层进行电子探针能谱点扫描分析, 进而确定扩散界面的生成相。从图4中4个扩散层的能谱分析可得出Spectrum 1, Spectrum 2, Spectrum 3, Spectrum 4 (分别为图2 (b~e) ) 各层中铜铝原子的比分别为58∶42, 9∶4, 1∶1, 1∶2。由此可以确定, 4个扩散层中的金属间化合物分别为Cu9Al4, Al Cu和Cu Al2。其中Spectrum 1中铜铝原子比为58∶42, 由此推断其可能为Al4Cu9与Cu固溶体的混合。
为进一步确定扩散界面的生成相, 对铜铝复合材料侧表面进行X射线衍射 (XRD) 分析, 结果如图5所示。从图5中可以判断出, 在铜铝结合面上存在的铜铝金属间化合物主要有Al2Cu, Al4Cu9和Al Cu。
2.2 Cu/Al复合材料结合层硬度测试
用错位打点法, 从Cu侧到Al侧的方向进行硬度测试, 图6为Cu/Al复合材料不同区域的显微硬度分布图。由图6可知, Cu基体的显微硬度约为HV 87.1, Al基体的显微硬度约为HV 46.5。结合层的硬度明显高于两侧基体的硬度, 且在铜铝两侧靠近界面中心处硬度较高, 由Cu, Al基体到金属间化合物层的区域内均呈现梯度递增的分布规律。靠近铜侧的结合层界面处硬度猛增高又降低, 可能是因为铜与结合层起始界面处为铜基固溶体区, 其塑性变形最严重, 加工硬化程度最大。可以明显看到复合材料从Cu经结合层到Al有5个的不同硬度区间, 这与显微组织观察结果一致, 即该结合层区域中存在结合层的3个确定的金属间化合物区。由2.1节对铜铝复合材料的形貌观察及成分分析知, 铜铝复合材料从Cu侧到Al侧其成分依次为:Cu与Cu9Al4混合、Cu9Al4、Al Cu和Cu Al2。故可得知:Cu的硬度为HV 87.1;Cu9Al4层的硬度为HV 204.5;Al Cu层的硬度为HV 271.5;Cu Al2层的硬度为HV 233.9;Al的硬度为HV46.5。
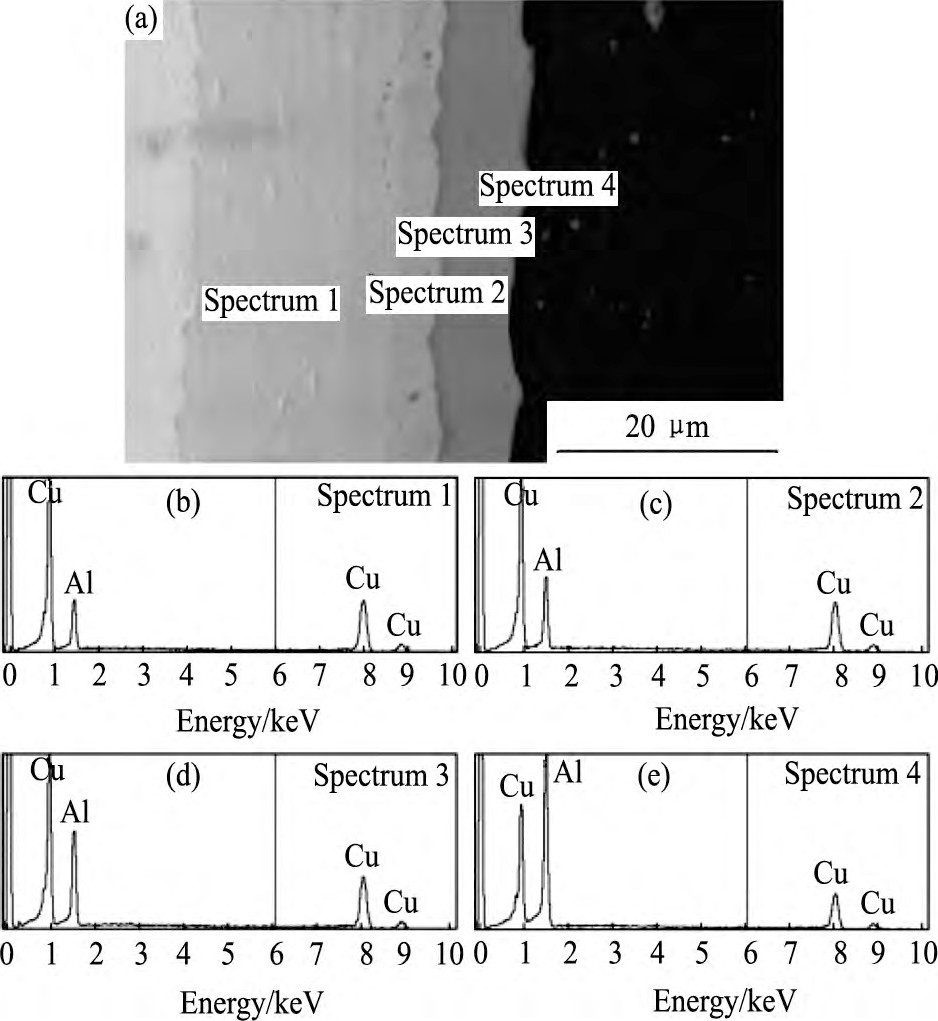
图4 Cu/Al结合层的电子探针能谱分析Fig.4 Electron energy spectrum analysis of Cu/Al bonding layer
(a) SEM image; (b) Spectrum 1; (c) Spectrum 2; (d) Spectrum 3; (e) Spectrum 4
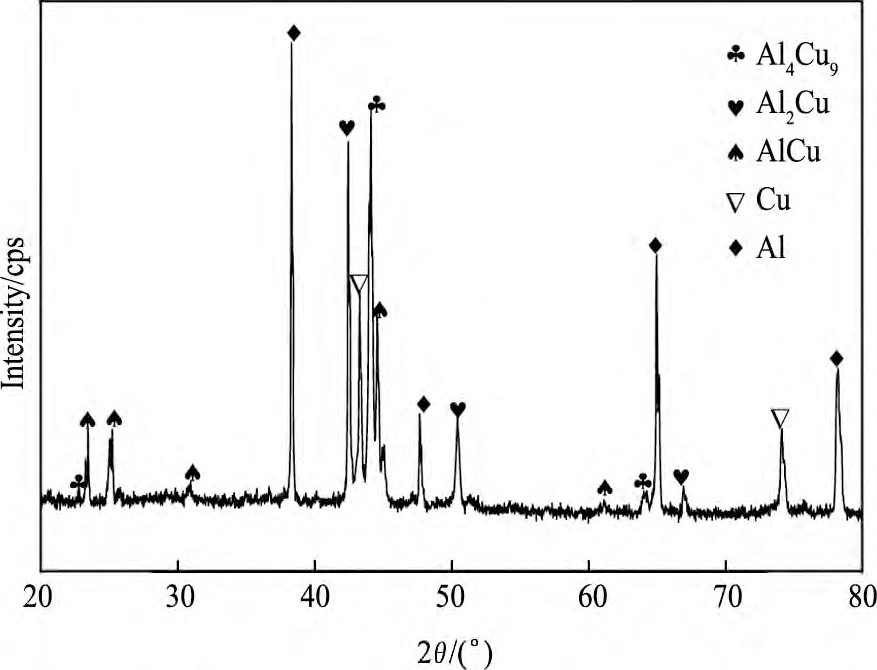
图5 铜铝复合材料XRD图谱Fig.5 XRD pattern of Cu/Al composite
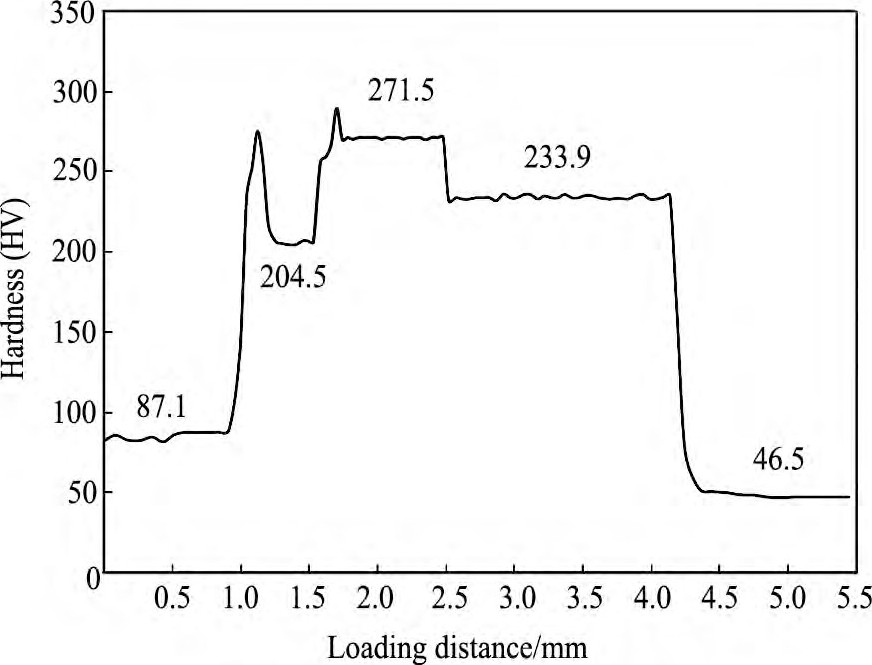
图6 Cu/Al复合材料硬度分布图Fig.6 Micro-hardness of Cu/Al composite
2.3 Cu/Al复合材料结合层性能分析
热膨胀系数, 指温度升高1℃, 沿试样某一方向上的相对伸长或收缩量。热机械分析是在程序温度控制下, 测量试样在一定负荷下产生的形变随温度变化。在热膨胀系数测试仪 (TMA) 压缩模式下测得Cu/Al复合材料结合层的形变-温度关系, 知Cu/Al复合材料结合层的热膨胀系数为28.7×10-6℃-1。
铜、铝两种金属的线膨胀系数分别为:16.5×10-6℃-1, 23.6×10-6℃-1, 两者线膨胀系数相差6.5×10-6℃-1。这种较大的线膨胀系数差使铜铝焊接时结合层两侧的金属处在不同的应力状态下, 容易使铜铝复合材料在结合层处产生裂纹。通过本实验的研究可以看到铜与结合层的线膨胀系数之差为12.2×10-6℃-1, 铝与结合层的线膨胀系数之差为5.1×10-6℃-1。对Cu/Al复合材料而言, 3种材料两两之间线膨胀系数之差的顺序从大到小依次为:铜-结合层>铜-铝>铝-结合层。
通过热循环实验的研究可以看到, 在温度骤升或降的情况下, 由于结合层与铜基材间的膨胀或收缩不一致导致铜铝复合材料的热应力的产生。当温度迅速升高或降低时, 结合层与铜基材同时发生热膨胀或收缩, 材料的导热性越差, 其加热或冷却时表面与内部的温度差越大, 由此产生的内应力就越大, 也就更容易产生裂纹[16]。当温度迅速升高时, 复合材料表面产生热膨胀, 结合层由于自身热导率差产生较强的热应力, 该热应力在界面处会产生应力突变, 致使结合层与铜基材间的界面结合强度大幅降低[17]。随着热循环试验的激热激冷, 结合层与铜基材间的界面需承受循环交变应力的作用, 而结合层与铜基材的热膨胀系数相差很大, 使得界面交变循环应力作用加强, 复合材料在结合层与铜基材作用界面的薄弱处产生裂纹, 加剧了铜与结合层在结合处的开裂[17]。
用偏光显微镜 (PM) 对经热循环试验的铜铝复合材料结合层进行组织形貌观察, 图7为200℃热循环100次, 400次, 2000次的结合层组织形貌图, 从图7中可以看出, 200℃时, 随着循环次数的增加, 结合层与铜基材结合处的开裂越来越明显。图8为250℃热循环50次, 100次, 600次的结合层组织形貌图。图9为300℃热循环60次, 90次, 200次的结合层组织形貌图。可以看出在同一循环次数下, 热循环温度越高, 铜与结合层结合处的开裂越明显。这是由于热循环温度越高, 铜在铝中的扩散系数以及铝在铜中的扩散系数越大, 在扩散时间相同的情况下, 扩散速度越大越易生成结合层, 此时结合层与铜基材的之间较大的热膨胀系数差加剧了铜与结合层的结合处的开裂。
铝铜中间化合物过渡层由中间化合物区和固溶体区组成, 固溶体区即为铝固溶体区和共晶相区, 中间化合物区即为Al2Cu, Al4Cu9和Al Cu所组成的区域。当循环温度较低时, 过渡层由铜铝中间化合物和富铜的铝固溶体两部分组成。当温度较高时, 铜向铝中扩散剧烈, 结合层厚度增加, 在铝与结合层之间形成枝晶状的铝固溶体层, 交界呈波浪状, 呈现液相界面作用的特征, 而Cu区界面交界线呈直线, 为固相界面作用的特征。且随温度升高固溶到基体中的铜增加, 使得网状分布的Al2Cu[18]相增加, 由于金属间化合物抗裂纹扩展能力较低, 裂纹最先起源于金属间化合物较多的区域, 并沿化合物层扩展、断裂[19]。铜铝复合材料经热疲劳后, 靠近铜侧界面容易出现断裂现象, 生成的脆性相Al2Cu是造成材料在结合层断裂的主要原因之一[20]。
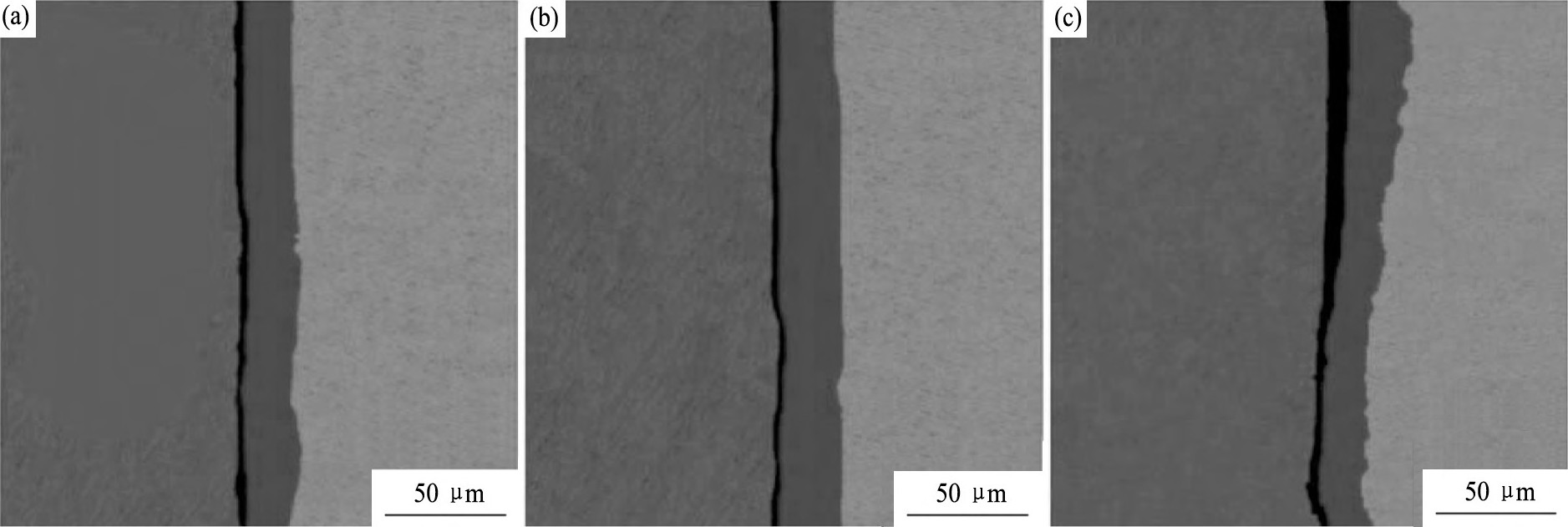
图7 200℃下热循环不同次数的结合层组织形貌Fig.7 Microstructures of interfaces with different cycle times at 200℃ (a) 100 times; (b) 400 times; (c) 2000 times
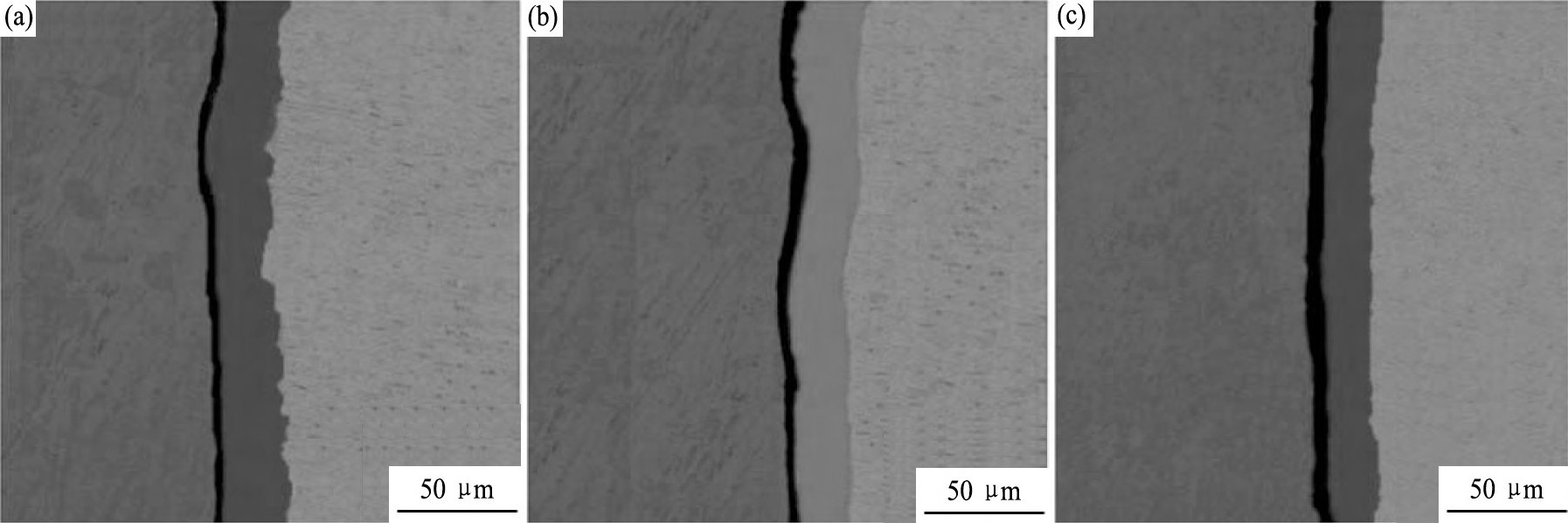
图8 250℃下热循环不同次数的结合层组织形貌Fig.8 Microstructures of interfaces with different cycle times at 250℃ (a) 50 times; (b) 100 times; (c) 600 times
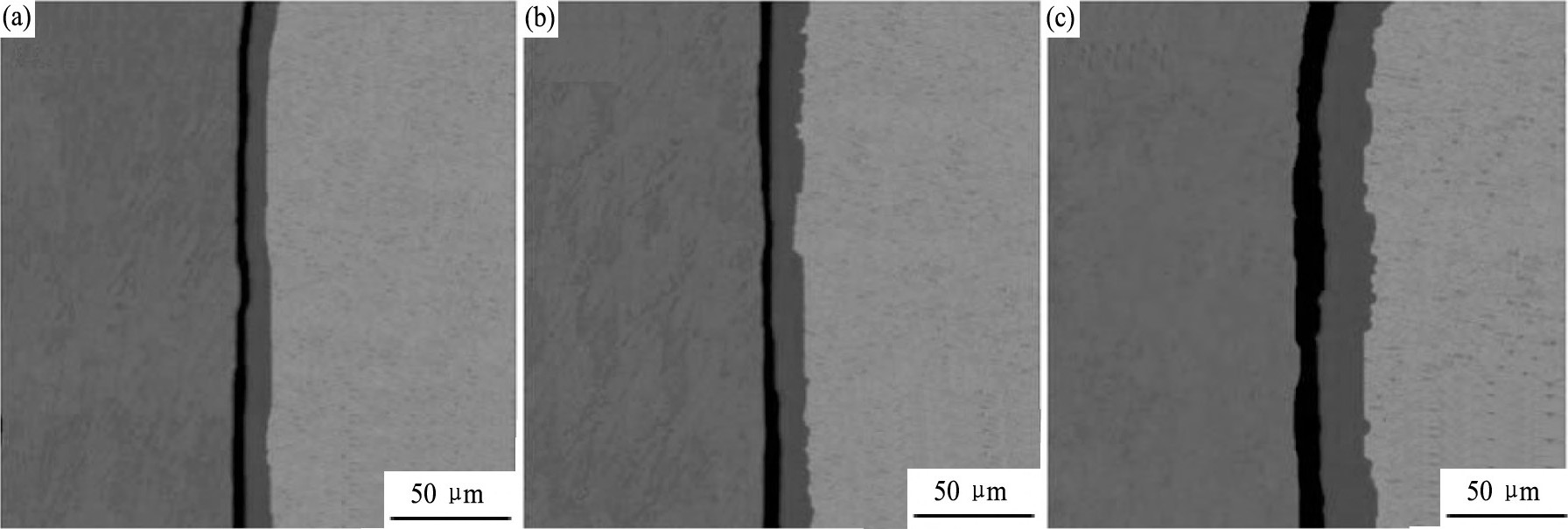
图9 300℃下热循环不同次数的结合层组织形貌Fig.9 Microstructures of interfaces with different cycle times at 300℃ (a) 60 times; (b) 90 times; (c) 200 times
结果表明, 经过较高热循环温度及循环次数的铜铝复合材料, 在结合层与铜基材结合处出现了不同程度的开裂, 而在结合层与铝基材结合处完好无损。且经热循环温度越高, 循环次数越多, 铜铝复合材料在铜与结合层结合处的开裂越明显。
3 结论
1.复合材料从Cu经结合层到Al的有5个的不同硬度区间, 结合层区域中存在结合层的3个确定的金属间化合物区。铜铝复合材料从Cu侧到Al侧, Cu的硬度为HV 87.1;Cu9Al4层的硬度为HV204.5;Al Cu层的硬度为HV 271.5;Cu Al2层的硬度为HV 233.9;Al的硬度为HV 46.5。
2.Cu/Al复合材料结合层的热膨胀系数为28.7×10-6℃-1。对Cu/Al复合材料而言, 3种材料两两之间线膨胀系数之差的顺序从大到小依次为:铜-结合层>铜-铝>铝-结合层。
3.经过较高热循环温度及循环次数的铜铝复合材料, 在结合层与铜基材结合处出现了不同程度的开裂, 而在结合层与铝基材结合处完好无损。且经热循环温度越高, 次数越多, 铜与结合层结合处的开裂越明显。
参考文献
[1] Zhao H J, Wang D, Qin J, Zhang Y H.Research progress on bonding mechanism and interface reaction of Cu/A1 laminated composite[J].Heat Working Technology, 2011, 40 (10) :84. (赵鸿金, 王达, 秦镜, 张迎晖.铜/铝层状复合材料结合机理与界面反应研究进展[J].热加工工艺, 2011, 40 (10) :84.)
[2] Li Q Y, Wang M G.Intermetallic of compound interface of aluminum/copper[J].Journal of Jiamusi University (Natural Science Edition) , 2009, 27 (4) :556. (李青云, 王明光.铝/铜复合界面金属间化合物[J].佳木斯大学学报 (自然科学版) , 2009, 27 (4) :556.)
[3] Berski S, Dyja H, Maranda A.Analysis of quality of bimetallic rod after extrusion process[J].Material Processing Technology, 2006, 177:582.
[4] Duboury L, Pelletier H, Vaissiere D.Mechanical characterization of laser surface alloyed aluminum-copper systems[J].Wear, 2002, 253:1077.
[5] Ding Z M, Song J M, Guan J S, Shen C B, Yan Y, Gao H.Influence of diffusion-treatment temperature on phase, morphology and properties of aluminum-plating coating on the steel[J].Journal of Functional Materials, 2010, 41 (8) :1321. (丁志敏, 宋建敏, 关君实, 沈长斌, 阎颖, 高宏.扩散处理对钢基铝镀层的相、形貌和性能的影响[J].功能材料, 2010, 41 (8) :1321.)
[6] Boessenkool H W, Durst G, Siegel S.Solid-phase bonding of metals[P].US Patent:US 2860409, 1958.
[7] Yu B Y, Qiao G, Chen Y, Su B, Liu C Y.Investigation on the Cu/Al liquid-solid bonding bimetallic composite with process of hot-dipping[J].Special Casting and Nonferrous Alloys, 2010, 30 (6) :581. (于宝义, 乔刚, 陈岩, 苏薄, 刘春雨.热浸镀法Cu/Al液固复合的研究[J].特种铸造及有色合金, 2010, 30 (6) :581.)
[8] Wen K Y.Improvement and application of copper and aluminum products of terminal connector[J].New Technology&New Process, 2011, (7) :100. (温开元.铜铝设备线夹产品的改进与应用—基于爆炸焊接新技术新工艺的应用[J].新技术新工艺, 2011, (7) :100.
[9] Wang Z, Liu P, Liu X K, Chen X H, He D H, Ma F C.Microstructure and performance of hot-dip aluminizing coating of copper[J].Chinese Journal of Rare Metals, 2015, 39 (10) :955. (王征, 刘平, 刘新宽, 陈小红, 何代华, 马凤仓.铜热浸镀铝的组织与性能[J].稀有金属, 2015, 39 (10) :955.)
[10] Wei M K, Duan M C, Wang Z.The investigation of aluminum oxide film with continuous beds of passage[J].Journal of Functional Materials, 1996, 27 (3) :279. (魏明坤, 段明诚, 王柱.含过渡层氧化铝膜的制备[J].功能材料, 1996, 27 (3) :279.)
[11] Guo Y J, Liu G W, Jin H Y, Shi Z Q, Qiao G J.Investigation on the interracial structure and phase formation mechanism of the diffusion-bonded Cu/Al laminates[J].Rare Metal Materials and Engineering, 2011, 40 (S2) :215. (郭亚杰, 刘桂武, 金海云, 史忠旗, 乔冠军.扩散结合Cu/Al叠层复合材料的界面结构与相生成机制[J].稀有金属材料与工程, 2011, 40 (S2) :215.)
[12] Hoseini Athar M M, Behzad Tolaminejad.Weld-ability window and the effect of interface morphology on the properties of Al/Cu/Al laminated composites fabricated by explosive welding[J].Materials&Design, 2015, 12 (86) :516.
[13] Tanaka Y, Kajihara M, Watanabe Y.Growth behavior of compound layers during reactive diffusion between solid Cu and liquid Al[J].Materials Science and Engineering A, 2007, 445-446:355.
[14] Zhang S H, Guo Z J.Study on aluminum-copper composites[J].The Chinese Journal of Nonferrous Metals, 1995, 5 (4) :128. (张胜华, 郭祖军.铜-铝复合材料的研究[J].中国有色金属学报, 1995, 5 (4) :128.)
[15] Xie J, Wu W D, Du K, Zheng F C, Ye C G, Huang L Z, Yuan G H.Process and microstructure analysis in vacuum diffusion bonding of aluminum and copper films[J].Atomic Energy Science and Technology, 2004, 38 (7) :120. (谢军, 吴卫东, 杜凯, 郑凤成, 叶成钢, 黄丽珍, 袁光辉.Al/Cu微米级厚度薄膜扩散连接工艺及显微组织分析[J].原子能科学技术, 2004, 38 (7) :120.)
[16] Wu J H, Li B S, Guo J K.Investigation on thermophysical properties of Si O2-Al N composites[J].Journal of Aeronautical Materials, 1999, 19 (3) :27. (吴洁华, 李包顺, 郭景坤.Si O2-Al N复合材料的物理性质[J].航空材料学报, 1999, 19 (3) :27.)
[17] Li Z L, Jiang Y H, Zhou R, Yang H, Zhang D P.Process of thermal fatigue crack formation and expansion of WC/iron matrix surface composites[J].Acta Materi-ae Compositae Sinica, 2008, 25 (2) :23. (李祖来, 蒋业华, 周荣, 羊浩, 张冬平.WC/铁基表面复合材料的热疲劳裂纹形成过程[J].复合材料学报, 2008, 25 (2) :23.)
[18] Zhu Z H.Study on Cu Al2/Al composites'synthetic technology of solid phase reaction and contact reaction with aluminium melt[J].Journal of Nanjing University of Aeronautics&Astronautics, 1997, 29 (5) :564. (朱正吼.Cu Al2/Al复合材料的固相反应合成技术及与Al液的接触反应研究[J].南京航空航天大学学报, 1997, 29 (5) :564.)
[19] Guo Y J, Jian W Z, Zhi X H.Microstructure and tensile behavior of Cu-Al multilayered composites prepared by plasma activated sintering[J].Materials Science and Engineering, 2010, A527 (20) :5234.
[20] Zhang Y, Song K X, Liu Y M, Zhao P F, Zhang Y M.Fabrication of Cu/Al composites by solid-liquid Bonding Method under pressure[J].Special Casting and Nonferrous Alloys, 2014, 34 (1) :101. (张亚, 宋克兴, 刘亚民, 赵培峰, 张彦敏.加压条件下固-液复合法制备Cu/Al复合材料[J].特种铸造及有色合金, 2014, 34 (1) :101.)