J. Cent. South Univ. (2012) 19: 1202-1205
DOI: 10.1007/s11771-012-1129-8
Low-temperature sintering and microwave dielectric properties of Li2MgTi3O8 ceramics doped with BaCu(B2O5)
BAO Yan(包燕)1, CHEN Guo-hua(陈国华)1, 2, HOU Mei-zhen(侯美珍)1, HAN Zuo-peng(韩作鹏)1,
DENG Kai-neng(邓开能)1,YANG Yun(杨云)1, YUAN Chang-lai(袁昌来)1, 2,
ZHOU Chang-rong(周昌荣)1, 2, LIU Xin-yu(刘心宇)1, 2
1. School of Materials Science and Engineering, Guilin University of Electronic Technology, Guilin 541004, China;
2. Guangxi Key Laboratory of Information Materials,Guilin University of Electronic Technology, Guilin 541004, China
? Central South University Press and Springer-Verlag Berlin Heidelberg 2012
Abstract: The influences of BaCu(B2O5) (BCB) addition on sintering, microstructure and microwave dielectric properties of Li2MgTi3O8 ceramics were investigated using X-ray diffractometry, scanning electron microscopy and microwave dielectric measurements. The experimental results show that a small amount of BaCu(B2O5) addition can effectively reduce the sintering temperature to 900 ℃, and induce only a limited degradation of the microwave dielectric properties. Typically, the best microwave dielectric properties of εr=24.5, Q×f =24 622 GHz, τf=4.2×10-6 ℃ -1 are obtained for 1.0% BCB-doped Li2MgTi3O8 ceramics sintered at 900 ℃ for 3 h. The BCB-doped Li2MgTi3O8 ceramics can be compatible with Ag electrode, which may be a strong candidate for low temperature co-fired ceramics applications.
Key words: ceramics; dielectrics; low-temperature co-fired ceramics; microwave dielectric properties
1 Introduction
To meet the demands of the miniaturization of microwave components for wireless communication, low-temperature co-fired ceramic (LTCC) technology becomes an important approach owing to its predominance in enabling the fabrication of three-dimensional ceramic modules with low dielectric loss and co-fired metal electrodes. As a metallic electrode, Ag has been widely used in LTCC technology because of its high conductivity and comparatively low cost. The melting temperature of Ag is low, about 961 ℃. Therefore, the microwave dielectric ceramics must have a low sintering temperature lower than 950 ℃ and chemical compatibility with Ag [1-2] in order to use the most common electrode.
Most of the known commercial dielectric materials for the high frequency applications have good microwave dielectric properties, but they cannot be co-fired with Ag electrode because of high sintering temperatures above 1 000 ℃ [3-5]. The addition of sintering aids, such as low-melting glasses and compounds, is the most often used method to lower the sintering temperatures [6-8]. Besides this, considerable attention has been paid to develope new microwave dielectrics with low cost of raw materials and low sintering temperature [9-11]. More recently, GEORGE and SEBASTIAN [12] reported that Li2MgTi3O8 (LMT) ceramics exhibited good microwave dielectric properties (εr=27.2, Q×f=42 000 GHz, τf =3.2×10-6 ℃-1) and low cost of raw materials. Unfortunately, the ceramics cannot be co-fired with Ag electrode due to high sintering temperatures (about 1 075 ℃). As far as we know, there are rarely reports focused on the low-sintered LMT ceramics [13]. In the present work, the microwave dielectric properties of Li2MgTi3O8 with BaCu(B2O5) (BCB) were investigated. It is well known that BCB addition often makes it possible to decrease the sintering temperature of many materials [14-17]. Therefore, a small amount of BCB is added to the ceramic in order to lower the sintering temperature of LMT ceramic.
2 Experimental
Li2MgTi3O8 (abbreviated as LMT) ceramic samples were prepared by the solid-state reaction method. High- purity Li2CO3, (MgCO3)4 Mg(OH)2·5H2O, and TiO2 (>99.9%, mass fraction, Sigma Aldrich, Gillingham, UK) were used as the starting materials. Stoichiometric amounts of the powder samples were mixed and ball milled using zirconia balls in isopropan-2-ol medium for 24 h. The resultant slurry was then dried and calcined at 900 ℃ for 4 h. The calcined powders were ground to form fine powders. To synthesize BaCu(B2O5) (abbreviated as BCB) ceramic powder, BaCO3, CuO and H2BO3 (>99.5%, mass fraction, Sigma Aldrich, Gillingham, UK) were milled for 4 h in a nylon jar with zirconia balls in isopropan-2-ol medium, then dried and calcined at 800 ℃ for 4 h. After subsequent ball-milling with 0.5%-4.5% (mass fraction) BCB, followed by drying, pellets, 10 mm in diameter and about 5 mm in thickness, were prepared by uniaxial pressure of about 100 MPa, and subsequently sintered for 3 h in air at 900 ℃.
The crystal structures of the samples were studied by X-ray diffraction technique using Cu Kα radiation (Philips PW1710) operating at 40 kV and 30 mA. The bulk densities of the sintered pellets were measured by the Archimedes method. The sintered samples were thermally etched for 60 min at a temperature of 90 % of the sintering temperature and the surface morphology was analyzed by using a scanning electron microscope (SEM, JEOL JSM-6400, Tokyo, Japan). The microwave dielectric property measurements were carried out using the transmission resonant cavity technique in an Au-coated brass cavity and a vector network analyzer (Advantest R3767CH, Tokyo, Japan). A Peltier device was used to heat up the cavity in order to measure the resonant frequency, f0, between 25 ℃ and 75 ℃. A linear fit to the data was used to calculate the temperature coefficient of the resonant frequency (τf). To check the chemical compatibility of LMT ceramic with the silver powder, the homogenized mixture including 20% (mass fraction) powdered silver and the ceramic powder was pressed into pellet and sintered at 900 ℃ for 3 h. In addition to the XRD analysis, micro-structural study was carried out by scanning electron microscopy.
3 Results and discussion
Figure 1 shows the XRD patterns of LMT powder calcined at 900 ℃ for 4 h, and BCB doped-LMT ceramics sintered at 900 ℃ for 3 h. All the diffraction peaks of LMT powder calcined at 900 ℃ could be indexed as a cubic structure (P4332) Li2MgTi3O8 (PDF 89-1308) without a second phase, which agrees well with the result reported by KAWAI et al [18]. It is indicated that reactions between Li2CO3, (MgCO3)4Mg(OH)2·
5H2O and TiO2 are completed when the mixed powder is calcined at 900 ℃ for 4 h. It is also confirmed that the ceramics with a small amount of BCB (≤1.5%) show a single phase Li2MgTi3O8, and no other crystal phase derived from the reaction between the LMT and the added BCB is found. However, a trace amount of unknown second phases occur when BCB content is 3%.
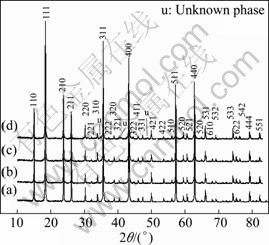
Fig. 1 XRD patterns of LMT powder calcined at 900 ℃ for 4 h (a) and LMT ceramics sintered at 900 ℃ for 3 h doped with 1.0% (b), 1.5% (c), 3.0% (d) BCB
Figure 2 shows the SEM micrographs of the polished surface of 0.5, 1.0, 1.5, and 3.0% BCB-doped LMT ceramics. It is evident that the porosity of the LMT ceramics decreases when the BCB content increases, while excessive BCB content (≥1.5%) tends to have more pores in its microstructure, which indicates the dependence of the porosity (or relative density) on BCB content. The average grain sizes for all samples are below 2 μm. At about 900 ℃, BCB improves the sintering of ceramics as a result of liquid phase sintering system (BCB has a low melting point of ~850 ℃). When BCB content increases, more liquid phase is formed during sintering. On one hand, it facilitates the array of granules as a step of sintering process and this is helpful for the sintering behavior of the samples. On the other hand, it inhibits the mass transfer during sintering because the high temperature liquid phase with more BCB has a larger viscosity and the formed liquid phase film at the grain boundary is thicker. This is not favorable for the sintering behavior of the samples. Because of the two opposite effects, there is an optimum value of the BCB content, i.e. the optimum BCB content should be 1% (mass fraction) in the present work. The 1%BCB-doped sample has more uniform and dense microstructure compared with other samples.
Figure 3 shows the dependence of BCB content on the relative density and εr values of the LMT ceramics sintered at 900 ℃ for 3 h. The theoretical density of LMT ceramic is 3.501 g/cm3 [12]. The relative density firstly increases and then decreases, which is in agreement with the variation in the microstructure. The relative permittivity versus BCB content of LMT ceramics has a trend similar to that of the relative density.
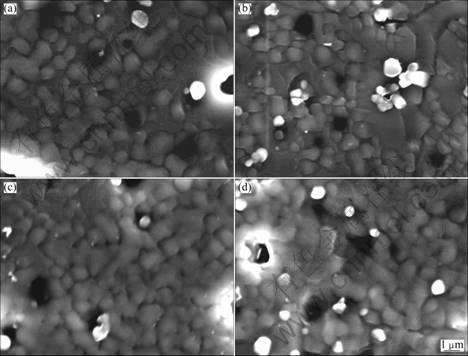
Fig. 2 SEM images of polished surface of LMT ceramics sintered at 900 ℃ for 4 h doped with different mass fractions of BCB: (a) 0.5%; (b) 1%; (c) 1.5%; (d) 3%
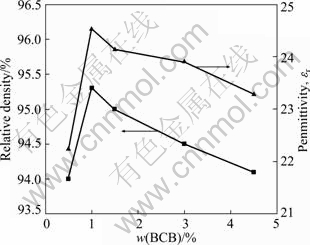
Fig. 3 Dependence of relative density and permittivity (εr) on BCB content of LMT ceramics sintered at 900 ℃ for 4 h
When BCB content is 1%, εr has a maximum value of 24.5. The first increase of εr might result from the increase of density of LMT ceramics. With further increase of BCB content, its low εr value is attributed to the decrease of overall εr value of ceramics, which indicates that the decrease of density, and the increase of BCB (low permittivity of 7.4 [14]) and secondary phase contents (see Fig. 1) result in the decrease of εr.
The dependence of Q×f and τf value on BCB content of LMT ceramics, sintered at 900 ℃ for 3 h is presented in Fig. 4. It is observed that the Q×f value of LMT ceramics firstly has a tendency to increase due to the increased density of the ceramics. A uniform and dense microstructure is in favor of improving Q×f value of LMT ceramics. Therefore, the maximum Q×f value of 24 622 GHz (at 7.3 GHz) can be obtained when BCB content is 1.0%. The Q×f value then slightly decreases when BCB content is 1.5%. It is worthy noting that Q×f value sharply decreases with the further increase of BCB content (≥3%), which may be due to the decrease of density and the formation of other secondary phases (see Fig. 3 and Fig. 1(d)). The τf values of the LMT ceramics slightly decreases with BCB content. Since BCB has negative τf value (about 32×10-6 ℃-1) [14], the addition of BCB has effect on the change of the positive τf value of the LMT ceramics. On the whole, the τf values of LMT ceramics are in the range of (2.3-4.4)×10-6 ℃-1. The XRD pattern together with SEM micrograph showing interface between Ag electrode and 1% BCB-doped LMT ceramic is presented in Fig. 5. It is seen that there are only diffraction peaks of Li2MgTi3O8 phase and the cubic silver phase (PDF 4-783) in the co-fired ceramic (Fig. 5(a)). A good contact between the ceramic and Ag is observed, as shown in Fig. 5(b). This indicates that the ceramic phase does not react with Ag powders and no other phase is formed when they are co-fired at 900 ℃ for 3 h. This result is tolerable during LTCC procedures and BCB-doped LMT ceramic can be recognized as a promising dielectric material for LTCC application.
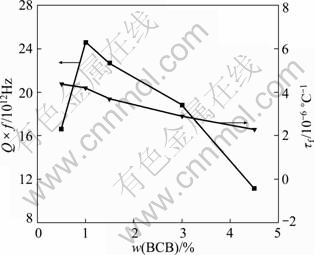
Fig. 4 Dependence of Q×f and τf values on BCB content of LMT ceramics sintered at 900℃for 4 h
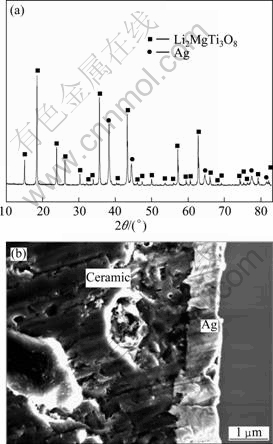
Fig. 5 XRD pattern (a) and SEM micrograph showing interface between Ag electrode and 1% BCB-doped LMT ceramic (b)
4 Conclusions
1) The effects of BCB addition on structure, microstructure and microwave dielectric properties of the LMT ceramic were investigated. LMT ceramics with addition of BCB can be well sintered at 900 ℃.
2) The 1.0% (mass fraction) BCB-added LMT ceramic material sintered at 900 ℃ has good microwave dielectric properties of εr=24.5, Q×f=24 622 GHz (at 7.3 GHz) and τf = 4.2×10-6 ℃-1.
3) The XRD analysis and SEM observation show that LMT ceramic can co-fire with the silver electrode at 900 ℃. The LMT-based ceramics may be promising candidates for LTCC applications at microwave frequencies.
References
[1] SebastianM T, Jantunen H. Low loss dielectric materials for LTCC applications: A review [J]. Int Mater Rev, 2008, 53(2): 57-90.
[2] Sebastian M T. Dielectric materials for wireless communications [M]. Oxford, UK: Elsevier Publishers, 2008: 445-448.
[3] Surendran K P, Sebastian M T. Low loss dielectrics in Ba[(Mg1/3Ta2/3)1-xTix]O3 and Ba[(Mg1-xZnx)1/3Ta2/3]O3 systems [J]. J Mater Res, 2005, 20(11): 2919–2926.
[4] Hughes H, Iddles D M, Reaney I M. Niobate-based microwave dielectrics suitable for third generation mobile phone base stations [J]. Appl Phys Lett, 2001, 79(18): 2952-2954.
[5] Nenasheva E A, Mudroliubova L P, Kartenko N F. Microwave dielectric properties of ceramics based on CaTiO3-LnMO3 system (Ln–La, Nd; M–Al, Ga) [J]. J Eur Ceram Soc, 2003, 23 (14): 2443-2448.
[6] Zhang Q L, Yang H, Zou J L, Wang H P. Sintering and microwave dielectric properties of LTCC-zinc titanate multilayers [J]. Mater Lett, 2005, 59(8/9): 880-884.
[7] Li B, Yue Z X, Li L T, Zhou J, Gui Z L. Low-fired microwave dielectrics in ZnO-TiO2 ceramics doped with CuO and B2O3 [J]. J Mater Sci: Mater Electron, 2002, 13(7): 415-418.
[8] Wee S H, Kim D W, Yoo S I. Microwave dielectric properties of low-fired ZnNb2O6 ceramics with BiVO4 addition [J]. J Am Ceram Soc, 2004, 87(5): 871-874.
[9] Pang L X, Zhou D. A low-firing microwave dielectric material in Li2O–ZnO–Nb2O5 system [J]. Mater Lett, 2010, 64 (22): 2413-2415.
[10] Liang J, Lu W Z. Microwave dielectric properties of Li2TiO3 ceramics doped with ZnO–B2O3 Frit [J]. J Am Ceram Soc, 2009, 92 (4): 952-954.
[11] Feteira A, Sinclair D C. Microwave dielectric properties of low firing temperature Bi2W2O9 ceramics [J]. J Am Ceram Soc, 2008, 91(4): 1338-1341.
[12] George S, Sebastian M T. Synthesis and microwave dielectric properties of novel temperature stable high Q, Li2ATi3O8 (A=Mg, Zn) ceramics [J]. J Am Ceram Soc, 2010, 93(8): 2164-2166.
[13] George S, Sebastian M T. Low-temperature sintering and microwave dielectric properties of Li2ATi3O8 (A=Mg, Zn) ceramics [J]. IntJApplCeramTechnol, 2010, 8(6): 1400-1407.
[14] Zhou H F, Wang H, Li K C, Yang H B, Zhang M H, Yao X. Microwave dielectric properties of ZnO-2TiO2-Nb2O5 ceramics with BaCu (B2O5) addition [J]. J Electron Mater, 2009, 38(5): 711-716.
[15] Kim M H, Lim J B, Kim J C, Nahm S. Synthesis of BaCu(B2O5) ceramics and their effect on the sintering temperature and microwave dielectric properties of Ba(Zn1/3Nb2/3)O3 ceramics [J]. J Am Ceram Soc, 2006, 89 (10): 3124-3128.
[16] Zhou H F, Chen X L, Fang L, Hu C Z. Preparation and characterization of a new microwave dielectric ceramic Ba4ZnTi11O27 [J]. J Am Ceram Soc, 2010, 93 (6): 1537-1539.
[17] Lim J B, Jeong Y H, Nguyen N H, Nahm S, Paik J H, Kim J H, Lee H J. Low temperature sintering of the Ba2Ti9O20 ceramics using B2O3/CuO and BaCu(B2O5) additives [J]. J Eur Ceram Soc, 2007, 27(8/9): 2875-2879.
[18] Kawai H, Tabuchi M, Nagata M, Tukamoto H, West A R. Crystal chemistry and physical properties of complex lithium spinels Li2MM03O8 (M=Mg, Co, Ni, Zn; M0=Ti, Ge) [J]. J Mater Chem, 1998, 8: 1273-1280
(Edited by YANG Bing)
Foundation item: Project(2010GXNSFA013029) supported by the Natural Science Foundation of Guangxi Province, China; Project(101059529) supported by National Undergraduate Innovation Program of the Ministry of Education of China
Received date: 2011-03-21; Accepted date: 2011-06-15
Corresponding author: CHEN Guo-hua, Professor, PhD; Tel: +86-773-2291434; E-mail: cgh1682002@163.com, chengh@guet.edu.cn