文章编号:1004-0609(2011)05-1192-07
从废旧锂离子电池中分离回收钴镍锰
陈 亮1, 唐新村1, 2, 张 阳1, 瞿 毅1, 王志敏1
(1. 中南大学 化学化工学院, 长沙 410083;2. 中南大学 粉末冶金国家重点实验室, 长沙 410083)
摘 要:提出一种新型的从废旧锂离子电池中分离回收钴镍锰的工艺。该工艺采用物理擦洗-稀酸搅拌浸出的方法分离集流体与活性物质,采用H2SO4+H2O2为浸出剂对活性物质进行浸出,然后采用黄钠铁矾法去除浸出液中的铁,再采用N902萃取分离铜,通过水解沉淀法除铝,最后采用碳酸盐共沉淀法制备镍钴锰碳酸盐前躯体。结果表明:最优浸出条件为液固比10:1、H2SO4浓度2.5 mol/L、H2O2加入量2.0 mL/g(粉料)、温度85 ℃、浸出时间120 min;在此条件下,钴、镍和锰的浸出率分别达到97%、98%和96%;除去浸出液中的铁、铜和铝后,钴、镍和锰的损失率分别为1.5%、0.57%和4.56%;总体来说,废旧锂离子电池中钴、镍和锰的回收率均可以达到95%。
关键词:废旧锂离子电池;浸出;萃取;N902;回收
中图分类号:TM 912.9;X 705 文献标志码:A
Separation and recovery of Ni,
Co and Mn from spent lithium-ion batteries
CHEN Liang1, TANG Xin-cun 1, 2, ZHANG Yang1, QU Yi1, WANG Zhi-min1
(1. School of Chemistry and Chemical Engineering, Central South University, Changsha 410083, China;
2. State Key Laboratory of Powder Metallurgy, Central South University, Changsha 410083, China)
Abstract: A novel process was developed for the separation and recovery of nickel, cobalt and manganese from the lithium-ion secondary batteries. In this process, stirring-scrubbing and dilute acid leaching are used to separate the active materials from current collectors. The Fe3+ ion in the leach liquor was removed using sodium jarosite method, then the copper was extracted by N902, and the aluminum was selectively precipitated as aluminum hydroxide. Finally, the pure NixCoyMnz ternary system precursor was prepared using carbonate co-precipitation method. The results show that the optimum conditions include liquid/solid ratio of 10:1, H2SO4 concentration of 2.5 mol/ L, H2O2 addition of 2.0 mL/g(powder), leaching time of 120 min and leaching temperature of 85 ℃, under which the leaching rates of Ni, Co and Mn are 97%, 98% and 96%, respectively. After the removal of iron, copper and aluminum in the leach liquor, the loss rates of Ni, Co and Mn are 1.5%, 0.57% and 4.56%, respectively. Overall, 95% of Ni, Co and Mn can be recovered from the spent lithium-ion batteries.
Key words: spent lithium-ion batteries; leaching; extraction; N902; recovery
锂离子电池自1990年实现商业化以来,以其具有能量密度大、质量轻、寿命长且无记忆性等诸多优点,被广泛应用于移动电话、笔记本电脑和照相机等便携式电子设备中。据统计,2000年全球锂离子电池生产量达到5亿只,预计2010年产量将超过46亿只[1]。由于技术和经济等方面的原因,目前锂电池回收率很低,大量废旧锂电池被遗弃,给环境造成巨大威胁和污染,同时对资源也是一种浪费,分析表明:锂离子电池中含钴5%~20%、锂5%~7%、镍5%~10%[2-3]。因此,如何在治理“电池污染”的同时,实现废旧电池有色金属资源尤其是钴的综合循环回收,已成为社会关注的热点难题。
目前,世界各国对锂离子电池中有价金属钴的回收与电池材料的再生工艺研究很多,LI等[4]先用超声清洗分离集流体与活性物质,并使用高浓度盐酸浸出,沉淀回收钴;LIU等[5]采用有机溶剂浸泡极片,使集流体与活性材料分离,通过高温固相法重新合成LiCoO2;LEE等[6]使用两级热处理两级过筛后高温煅烧的方法预选活性物质,分别采用HNO3和HNO3-H2O2体系对筛后活性物质浸出;WANG等[7]采用盐酸浸出,高锰酸钾氧化沉锰,丁二酮肟萃取镍,氢氧化钠沉淀回收钴。由于以上研究实际应用效果欠佳,一般不具备经济可行性。造成这一局面的原因一方面是废旧锂离子电池拆分过程效率低,集流体与活性物质分离过程能耗大,成本较高,环境污染严重;另外一方面是LiNiO2、LiMnxNiyCo1-x-yO2和LiMn2O4等替代品也逐渐进入市场[8-9],使回收锂电池中钴的同时不得不进行多种金属如锰和镍的分离。
针对废旧锂离子电池回收工艺中所面对的上述问题,本文作者试图寻求一条回收效率高、经济合理、且环境友好的废旧锂离子电池的回收工艺。
1 实验
1.1 实验材料
实验所用的粉料来自湖南某废旧锂电池拆解厂。对回收的大量废旧锂电池进行手工拆壳和电池芯粉碎,经过预处理后获得活性粉料,其主要化学成分如表1所列,其XRD谱如图1所示。
表1 粉料金属成分含量
Table 1 Metal composition of powder (mass fraction, %)

1.2 实验原理与方法
锂离子电池中,正极活性物质或负极活性物质通常是与溶于NMP的有机粘结剂(如PVDF)调浆后涂覆在金属集流体上制成薄膜电极。将活性物质和集流体进行分离主要有以下3条途径:1) 高温分解或溶解粘结剂[10];2) 溶解集流体[11-12];3)破坏接触界面[13]。本文作者采用手工除去塑料及金属外壳,取出电芯,将电芯机械破碎至1~5 mm,破碎后的电芯置于热水中搅拌擦洗,过滤烘干后过筛,分出大部分活性物质。
通过稀酸局部溶蚀集流体表面和活性物质,造成表面缺陷,再通过搅拌擦洗作用使残留的活性物质从电极集流体上脱落,二次过筛后实现其与正负极集流体分离。铝箔、铜箔经洗涤、干燥后可直接作为产品回收,两次筛分的活性粉体合并经进一步处理回收有价组分。
2Al+3H2SO4→Al2(SO4)3+3H2↑ (1)
4LiCoO2+6H2SO4→2Li2SO4+4CoSO4+6H2O+O2↑ (2)

图1 粉料的XRD谱
Fig.1 XRD pattern of powdered materials
本实验采用H2SO4+ H2O2浸出废旧锂电池中的活性物质,浸出过程中发生的反应为
2LiCoO2+3H2SO4+H2O2→2CoSO4+O2↑+
Li2SO4+4H2O (3)
浸出后的滤液中含有Fe3+、Cu2+、Al3+等杂质,本实验采用黄钠铁矾法除铁[14],其反应式为
Fe2(SO4)3 + 12H2O + Na2SO4 → Na2Fe6(SO4)4(OH) 12↓+
6H2SO4 (4)
目前市场上流行多种铜的特效萃取剂,如LIX 系列、Cyanex系列等。由实验选用的萃取剂为N902。相对于这些萃取剂而言,虽然N902萃取铜的pH值范围和萃取容量相对较小,但其价格相对便宜,适合大规模的工业化生产[15]。实验结果表明:N902对铜具有很强的选择性,且反萃性能优良,有利于实现产业化。萃余液经水解沉淀除铝后,通过碳酸盐共沉淀法制备三元锂离子电池正极材料前躯体。综上所述,实验工艺流程如图2所示。
1.3 分析方法
试样中钴以及其余元素的液相分析采用PS-6等离子原子发射光谱ICP-AES,pH值测定使用PHS-3C型pH计,物相分析采用日本RigakuD型X射线衍射仪。
2 结果讨论
2.1 活性物质与集流体的分离
将破碎后的电芯碎片加入热水中机械搅拌,过滤烘干后进行第一次振动筛分,分离出的粉体材料留作他用。取一定量筛上碎料,置于一定浓度的稀硫酸溶液中机械搅拌浸泡,控制试验温度为25 ℃,转速为400 r/min,液固比为10:1,搅拌时间为60 min,考察硫酸浓度对活性物质与集流体分离的影响。反应结束后过滤溶液,用热水多次淋洗渣相,滤液和洗液合并送入下段浸出工序;渣相用孔径为180 μm(80目)筛子进行筛分,筛上产物为铝箔和铜箔;筛下产物经过滤、干燥得到活性粉料。不同硫酸浓度对试样溶解性的影响如表2所列。
由表2可知,筛上碎料中活性物质与铝箔、铜箔得到有效分离时的最佳硫酸浓度为0.5 mol/L。在筛上碎料的浸出过程中,除了有少量铝浸出外,还有少量的铜浸出。这可能是由于铜箔上的石墨化碳很容易脱落,铜箔表面被氧化生成氧化铜而溶于稀硫酸。
表2 不同硫酸浓度对试样溶解性的影响
Table 2 Effects of different H2SO4 concentration on solubility of sample
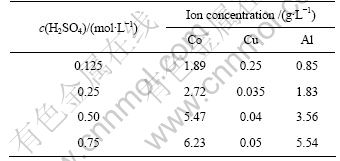
2.2 还原酸浸
每次试验使用10 g活性粉料,粉末平均粒径为0.178 mm,固定搅拌速度为400 r/min,分别考察反应温度和时间、硫酸浓度、双氧水加入量、液固比对浸出率的影响。
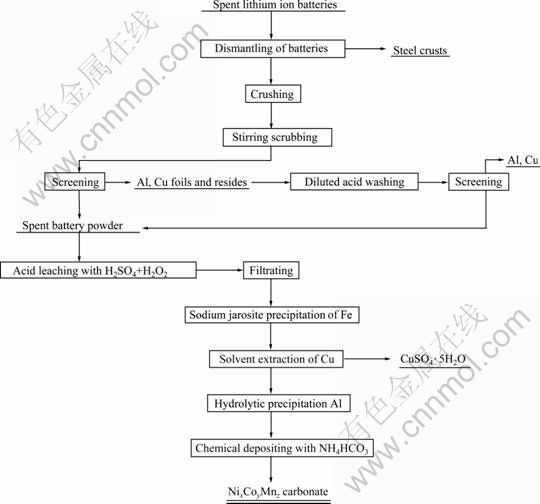
图2 废旧锂电池有价金属回收流程图
Fig.2 Flowsheet for recovery of valuable metals from spent lithium-ion batteries
2.2.1反应温度和时间对浸出过程的影响
在硫酸浓度2.5 mol/L、加入H2O21.0 mL/g(粉料)、液固比10:1的条件下进行试验,考察温度和时间对活性粉料浸出效果的影响,结果如图3~5所示。
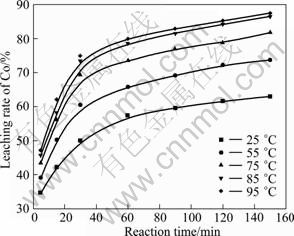
图3 浸出温度和时间对钴浸出率的影响
Fig.3 Effects of temperature and time on leaching rate of Co
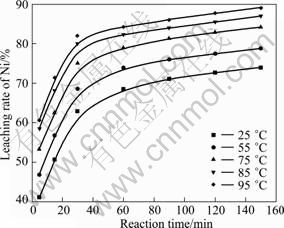
图4 浸出温度和时间对镍浸出率的影响
Fig.4 Effects of temperature and time on leaching rate of Ni
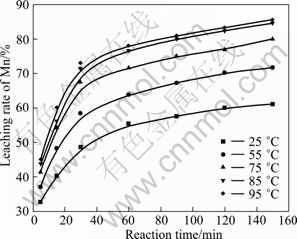
图5 浸出温度和时间对锰浸出率的影响
Fig.5 Effects of temperature and time on leaching rate of Mn
从图3~5中可以看出,粉末中钴、镍和锰的浸出速率随反应温度的升高和反应时间的延长而提高。酸浸过程中,粉末的溶解为固-液非均相反应,温度的升高对浸出过程的化学反应速率和扩散速率都有促进作用。25 ℃时,钴、镍和锰的浸出率都不高;当温度升至85 ℃后,随着温度的增加,浸出率的变化较小。反应60 min时,钴、镍和锰浸出率急剧增加;反应120 min后,钴、镍和锰浸出率增加趋势变缓。因此,综合考虑三者的浸出效果和能耗的损失,选择浸出反应温度为85 ℃,反应时间为120 min。
2.2.2硫酸浓度对浸出过程的影响
在温度85 ℃、时间120 min、加入H2O21.0 mL/g(粉料)、液固比10:1的条件下进行试验,考察硫酸浓度对活性粉料浸出效果的影响,结果如图6所示。
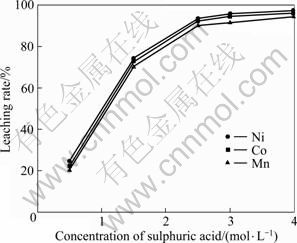
图6 硫酸浓度对浸出率的影响
Fig.6 Effect of sulfuric acid concentration on leaching rate
从图6中可以看出,粉末的钴、镍和锰浸出率随硫酸浓度的增加而升高,当硫酸浓度为2.5 mol/L时,钴、镍和锰浸出率趋于平缓,钴、镍和锰浸出率分别为92.3%、93.5%和90.1%;继续增加硫酸浓度,浸出率增加不大,故选择硫酸浓度为2.5 mol/L。
2.2.3双氧水加入量对浸出过程的影响
在硫酸浓度2.5 mol/L、温度85 ℃、时间120 min、液固比10:1的条件下进行试验,考察双氧水加入量对活性粉料浸出率的影响,结果如图7 所示。
从图7中可以看出,粉末中钴、镍和锰的浸出率随双氧水加入量的增加而增大。当不加双氧水时,浸出率始终低于60%,此时LiCoO2发生的是自身氧化还原反应,反应方程如式(3)所示。加入双氧水后,反应方程如式(4)所示,双氧水的加入大大促进了LiCoO2的溶解,提高了活性粉料的浸出率和溶解速率。当双氧水加入量大于2.0 mL/g(粉料)后,继续增加其用量,对钴、镍和锰浸出率的影响都非常小,此时钴、镍和锰的浸出率分别为95.6%、96.1%和93.5%。
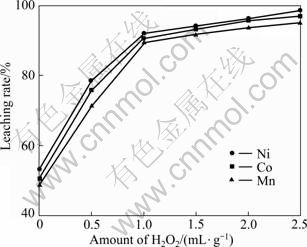
图7 双氧水加入量对浸出率的影响
Fig.7 Effect of H2O2 amount on leaching rate
2.2.4液固比加入量对浸出过程的影响
在硫酸浓度2.5 mol/L、温度85 ℃、时间120 min、加入H2O2 2.0 mL/g(粉料)的条件下进行试验,考察液固比对活性粉料浸出效果的影响,结果如图8所示。
从图8中可以看出,粉末中钴、镍和锰的浸出率随液-固比的增加而增大。当液-固比增加时,溶解一定量固体的溶液体积增大,主体溶液中反应生成物的浓度也随之降低。反应生成物浓度梯度减小可提高溶液中新生成产物的扩散速率,从而有利于粉末的溶解;但液-固比过高时,则要求反应容器较大,增加了浸出工序的负担,同时又必然降低了浸出液的溶度,对回收工艺不利。因此,选择合适的液-固比为10:1。
通过对影响浸出各因素的考察,综合考虑经济、能耗及反应容器体积等原因,选择最佳浸出条件如下:2.5 mol/L硫酸、2.0 mL H2O2/g粉料、120 min、85 ℃、液固比10:1。在最佳浸出条件下,钴、镍和锰的浸出率分别为97%、98%和96%,终点pH值为0.5~0.8,各元素在浸出液中的质量浓度见表3。
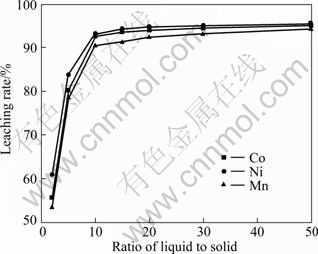
图8 液固比对浸出率的影响
Fig.8 Effect of ratio of liquid to solid on leaching rate
表3 浸出液中各离子的质量浓度
Table 3 Mass concentrations of ions in leaching solution (g/L)

2.3 浸出液的净化
2.3.1 黄钠铁矾法除铁
将浸出液预中和调节pH值至1.0后,加热至95 ℃,再缓慢加入质量分数为10%的NaOH溶液调节pH值至1.7~1.9,反应2 h后调节终点pH至3.0~3.5,除铁后溶液中铁离子含量为0.006 g/L。结果表明,采用黄钠铁矾法除铁时,钴的回收率较高, 铁的除去率为99.9%,而钴、镍和锰的损失率均小于1%。
2.3.2 N902 萃取除铜
1) 水相pH值对N902萃取铜的影响
萃取剂N902为酸性萃取剂,在萃取过程中会产生大量的H+,且浸出过程是在硫酸过量的条件下进行的,因此浸出液也具有一定的酸度。为了达到最优的分离效果,需将水相的pH调节至最适合萃取的范围。在固定萃取剂组成(体积分数)为10%N902+90%璜化煤油、O/A为1:1的条件下进行试验,考察水相不同pH值对N902萃取性的影响,结果如图9所示。
由图9可知,水相pH值对N902萃取铜的影响较大,随着水相pH值的增加,铜萃取率上升明显;pH值大于1.25后,铜萃取率的增加趋于缓慢,此时铜的萃取率为97.72%,钴、镍、锰和铝的萃取率分别为0.82%、0.31%、1.9%和0.53%;继续增加pH值时,铜萃取率缓慢上升,同时大量的钴、镍、锰和铝将进入有机相,达不到萃取分离的目的,故选择萃取水相pH值为1.25。
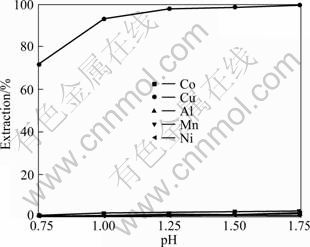
图9 pH值对N902萃取性的影响
Fig.9 Effect of pH value on extraction property of N902
2) N902体积分数对萃取铜的影响
在料液初始pH值为1.25、O/A为1:1的条件下进行试验,考察N902浓度对萃取铜的影响,结果如图10所示。
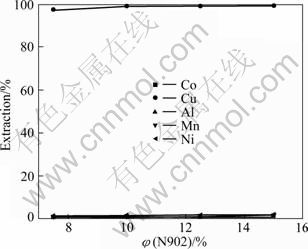
图10 N902含量对萃取率的影响
Fig.10 Effect of N902 content on extraction
由图10可知,铜萃取率随N902用量的增加而提高,N902体积分数达到10%后,铜萃取率几乎不变,而钴、镍、锰和铝的萃取率缓慢增加,此时铜萃取率为99.29%,钴、镍、锰和铝的萃取率分别为0.15%、1.34%、0.54%和0.46%;继续增加N902的体积分数,铜萃取率上升缓慢,同时萃取剂的密度和黏度随N902用量的增加而急剧增大,不利于分相,故选择N902体积分数达到10%。
选择有机相组成(体积分数)为10%N902+90%磺化煤油,调节水相料液pH为1.25,O/A为1:1,一级萃取后料液中各金属离子浓度为Cu 0.005 g/L、Fe 0.005 g/L、Al 2.86 g/L、Co 19.68 g/L、Ni 0.45 g/L和Mn 1.58 g/L。由实验结果发现,在最优条件下铜、钴、镍、锰和铝分离效果明显,料液中99.5%的铜进入有机相,钴、镍、锰和铝的萃取率仅为0.15%、1.34%、0.54%和0.46%,达到了分离铜的目的。
2.3.3硫酸反萃除铜
1) 硫酸浓度对铜反萃效率的影响
在温度为25 ℃、O/A为1:1的条件下,改变硫酸浓度进行试验,考察反萃剂硫酸浓度对铜反萃率的影响,结果如表4所列。
表4 硫酸浓度对反萃铜的影响
Table 4 Effect of concentration of H2SO4 on stripping of copper

由表4可以看出,随着硫酸浓度的增加,铜的反萃率显著上升,当硫酸浓度达到4 mol/L时,铜的反萃率达到了94.8%,此时反萃基本达到平衡。当硫酸浓度继续增大时,溶液会出现3种相,即有机相、水相和乳化相。综合铜的反萃率,以及成本考虑,选取反萃硫酸浓度为4 mol/L。
2) 反萃等温线及逆流萃取理论级数
在温度为25 ℃、负载有机相中铜离子浓度为2 g/L,硫酸浓度为4 mol/L的条件下,根据相比的不同混合,测定水相中铜的浓度以及有机相中铜的浓度,绘制出铜萃取平衡等温线,并根据McCabe-Thiele图解法求出逆流萃取所需理论级数,结果如图11所示。
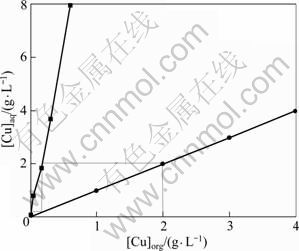
图11 反萃平衡等温线及McCabe-Thiele图
Fig.11 Stripping isotherm and McCabe-Thiele diagram
由图11可见,在O/A为1?1、硫酸浓度为2 mol/L的条件下,经过2级逆流反萃能洗出富铜有机相中99.9%的铜,反萃酸耗和反萃液残酸浓度均较低,有利于铜的后续回收。
2.3.4 水解沉淀除铝
根据金属离子水解所需的pH值要求,控制pH值在5.5以下,此时钴、镍和锰基本不水解,而铝水解而形成沉淀。控制反应温度为95 ℃,反应时间为2 h,考查溶液终点pH值对沉淀率的影响。结果表明,在3.5≤pH≤4.3的区间里,溶液的酸度对铝的去除效果影响很大。当pH>4.3时,沉淀趋势变缓,但钴、镍和锰的损失率随酸度的减小而上升明显。在保证杂质去除效果较好的基础上,尽量降低钴、镍和锰的损失率,故选取反应中溶液的pH为4.3。此时料液中各金属离子的质量浓度为Cu 0.002 g/L、Fe 0.004 g/L、Al 0.03 g/L、Co 19.22 g/L、Ni 0.42 g/L和Mn 1.50 g/L。
2.4 三元锂离子电池正极材料前躯体的制备
经过上述纯化过程后,溶液中主要是含钴、镍和锰金属离子,而铜、铁和铝的质量浓度分别降至0.002、0.004和0.03 g/L。根据料液中钴镍锰的摩尔比,配入适当的硫酸镍、硫酸锰或硫酸钴,随后往溶液中添加碳酸氢铵,采用共沉淀法制备镍钴锰碳酸盐前躯体。
3 结论
1) 采用物理擦洗-稀酸搅拌浸出的方法可以实现电极活性物质与集流体的高效分离,铝箔和铜箔可直接作为产品回收。
2) 采用H2SO4+H2O2为浸出剂对活性物质浸出,最优条件如下:液固比10:1,H2SO4 2.5mol/L,2.0 mL双氧水/g粉料,温度85 ℃,浸出时间120 min。此时钴、镍和锰的浸出率分别达到97%、98%和96%。
3) 采用黄钠铁矾法能有效地除去溶液中的铁,除铁率为99. 9 %;以N902为萃取剂,硫酸为反萃剂回收溶液中的铜,铜回收率可达到99.9%;采用水解沉淀法除铝,调节pH为4.3,能有效去除铝离子。
4) 经过上述工艺过程,采用共沉淀法制备镍钴锰碳酸盐前躯体,可以回收废旧锂离子电池中95%的钴、镍和锰。
REFERENCES
[1] KANAMURA K, HOSHIKAWA W, UMEGAKI T. Electrochemical characteristics of LiNi0.5Mn1.5O4 cathodes with Ti or Al current collectors[J]. Journal of The Electrochemical Society, 2002, 149(3): 339-345.
[2] SHIN S M, KIM N H, SOHN J S, YANG D H, KIM Y H. Development of a metal recovery process from Li-ion battery wastes[J]. Hydrometallurgy, 2005, 79(3/4): 172-181.
[3] LEE C K, RHEE K I. Preparation of LiCoO2 from spent lithium- ion batteries[J]. Journal of Power Sources, 2002, 109(1): 17-21.
[4] LI Jin-hui, SHI Pi-xing, WANG Ze-feng, CHEN Yao, CHANG Chein-chi. A combined recovery process of metals in spent lithium-ion batteries[J]. Chemosphere, 2009, 77(8): 1132-1136.
[5] LIU Yun-jia, HU Qi-yang, LI Xin-hai, WANG Zhi-xing, GUO Hua-jun. Recycle and synthesis of LiCo02 from incisors bound of Li-ion batteries[J]. Transactions of Nonferrous Metals Society of China, 2006, 16(4): 956-959.
[6] LEE C K, RHEE K I. Reductive leaching of cathodic active materials from lithium ion battery wastes[J]. Hydrometallurgy, 2003, 68(1/3): 5-10.
[7] WANG Rong-chi, LIN Yu-chuan, WU She-huang. A novel recovery process of metal values from the cathode active materials of the lithium-ion secondary batteries[J]. Hydrometallurgy, 2009, 99(3/4): 194-201.
[8] CASTILLO S, ANSART F, LABERTY-ROBERT C, PORTAL J. Advances in the recovering of spent lithium battery compounds[J]. Journal of Power Sources, 2002, 112(1): 247-254.
[9] WANG Rong-chi, LIN Yu-chuan, WU She-huang. A novel recovery process of metal values from the cathode active materials of the lithium-ion secondary batteries[J]. Hydrometallurgy, 2009, 99(3/4): 194-201.
[10] CONTESTABILE M, PANERO S, SCROSATI B. A laboratory-scale lithium-ion battery recycling process[J]. Journal of Power Sources, 2001, 92(1/2): 65-69.
[11] 吴 芳. 从废旧锂离子二次电池中回收钴和锂[J]. 中国有色金属学报, 2004, 14(4): 697-701.
WU Fang. Recovery of cobalt and lithium from spent lithium-ion secondary batteries[J]. The Chinese Journal of Nonferrous Metals, 2004, 14(4): 697-701.
[12] NAN Jun-min, HAN Dong-mei, ZUO Xiao-xi. Recovery of metal values from spent lithium-ion batteries with chemical deposition and solvent extraction[J]. Journal of Power Sources, 2005, 152: 278-284.
[13] 卢毅屏, 夏自发, 冯其明, 龙 涛, 欧乐明, 张国范. 废锂离子电池中集流体与活性物质的分离[J]. 中国有色金属学报, 2007, 17(6): 997-1001.
LU Yi-ping, XIA Zi-fa, FENG Qi-ming, LONG Tao, OU Le-ming, ZHANG Guo-fan. Separation of current collectors and active materials from spent lithium-ion secondary batteries[J]. The Chinese Journal of Nonferrous Metals, 2007, 17(6): 997-1001.
[14] VU H, JANDOVA J, HRON T. Recovery of pigment-quality magnetite from jarosite precipitates[J]. Hydrometallurgy, 2010,101(1/2): 1-6.
[15] 徐源来, 徐盛明, 徐 刚, 池汝安. 白铜合金废料综合回收工艺[J]. 中国有色金属学报, 2009, 19(4): 760-765.
XU Yuan-lai, XU Sheng-ming, XU Gang, CHI Ru-an. Comprehensive recovery of copper-nickel alloy scrap[J]. The Chinese Journal of Nonferrous Metals, 2009, 19(4): 760-765.
(编辑 何学锋)
基金项目:国家自然科学基金资助项目(20876178);中南大学粉末冶金国家重点实验室开放课题
收稿日期:2010-08-25; 修订日期:2010-11-22
通信作者:唐新村,副教授,博士;电话:0731-88836961; E-mail: tangxincun@163.com