Trans. Nonferrous Met. Soc. China 24(2014) 690-696
Effect of wet shot peening on Ti-6Al-4V alloy treated by ceramic beads
Guo-qing CHEN1, Yan JIAO1, Tang-yong TIAN1, Xin-hua ZHANG2, Zhi-qiang LI2, Wen-long ZHOU1
1. School of Materials Science and Engineering, Dalian University of Technology, Dalian 116085, China;
2. Beijing Aeronautical Manufacturing Technology Research Institute, Beijing 100024, China
Received 5 March 2013; accepted 5 July 2013
Abstract: Ti-6Al-4V alloy was processed by wet shot peening with ceramic beads. The effects of the shot peened intensity on the microstructure, surface morphology, and residual stress were investigated. A tensile-tensile fatigue test was performed and the fracture mechanism was proposed. The results demonstrate that the surface roughness after wet shot peening is obviously lower than that after dry shot peening. With the increase of the shot peened intensity, the depth of the residual stress layer increases to 250 μm, and the maximum stress in this layer increases to -895 MPa. The fatigue strength also increases by 12.4% because of the wet shot peening treatment. The dislocation density of the surface layer is significantly enhanced after the wet shot peening with ceramic beads. The microstructure of the surface layer is obviously refined into ultra-fine grains.
Key words: Ti-6Al-4V alloy; wet shot peening; microstructure; residual stress; fatigue property
1 Introduction
Titanium and titanium alloys are widely used in the aerospace and marine industries because of their excellent properties, such as high specific strength, stability at mid-temperature, non-magnetism, and excellent corrosion resistance. However, the further development of titanium alloys is limited by their low hardness, poor abrasion resistance, and low fatigue strength [1]. Ti-6Al-4V alloy is one of the most widely used alloys and accounts for approximately 60% of all titanium alloy products. The fracture of titanium alloy components is mainly caused by fatigue, so improving their fatigue strength is important.
As a conventional strengthening process, dry shot peening has favorable effects on improving fatigue strength [2], hardness [3], fretting fatigue resistance [4,5], and abrasion resistance [6,7]. With the development of science and technology, some new methods have made progress, such as laser shot peening [8], ultrasonic shot peening [9], and high-pressure water shot peening [10]. The wet shot peening with ceramics is a newly developed surface-strengthening technology. Compared with dry shot peening, wet shot peening ensures the use of ceramic beads placed in liquids containing a certain amount of corrosion inhibitors. A liquid film is formed on the component surface, which effectively reduces friction and cools the surface. Ceramic beads are widely considered to be conducive to energy conservation and environmental protection because of their high intensity, toughness, hardness, good surface finish, and high productivity. SAKODA and TOSHA [11] reported that the fatigue strength of the medium carbon steel was improved by 20% after wet shot peening. But the wet shot peening of Ti-6Al-4V alloy using ceramic beads has not yet been reported. In the present work, the emphasis is given on the effects of different shot peened intensities on the microstructure and properties of Ti-6Al-4V alloy.
2 Experimental
The shot peening processes were performed on a JY-120WB blasting machine using a compound of Al2O3 ceramic beads and water. The main parameters of wet shot peening are given in Table 1. The material used in this study was Ti-6Al-4V alloy, which was received in an annealed condition and consisted of equiaxed grains with an average grain size of 10 μm (Fig. 1).
Table 1 Different parameters of wet shot peening
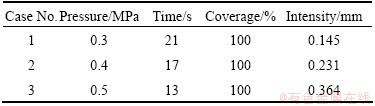
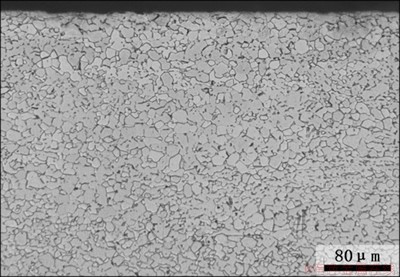
Fig. 1 SEM image of initial Ti-6Al-4V alloy
Transmission electron microscope (TEM; PHILIPS CM200) was used to observe the grain shape and microstructural anisotropy. Samples for TEM were cut into slices and mechanically polished to a thickness of 50 μm. The samples were subjected to twin-jet electropolishing with a liquor containing 5% perchloric acid+95% alcohol, and then thinned by LGB-1 ion milling.
The surface roughness was measured by a three-dimensional non-contact optical profilometer (ZYGO Newview 5022). For each sample, the surface roughness was measured at three different locations in the center. Afterwards, the surface roughness values at different locations were averaged to represent the arithmetic-mean value (Ra) of the surface roughness.
The residual stress was analyzed using an X-ray diffraction stress analyzer (X-350A) in conjunction with material removal layer-by-layer by electro-chemical polishing. A Cu Kα X-ray source was used at a tube voltage of 22 kV and current of 6 mA, within a scan range of 136°-146°. The diffraction lattice plane (213) was examined to investigate the residual stress. The stress constant is -277 MPa.
Fatigue tests were conducted under constant load control using a servo-hydraulic testing machine operated at a stress ratio of 0.1 and a frequency of 20 Hz in the laboratory air at ambient temperature. The fatigue cycle limit of the testing was set to be 107 cycles. The configuration and dimension of specimens for fatigue testing are shown in Fig. 2.
3 Results and discussion
3.1 XRD analysis
The XRD patterns of Ti-6Al-4V alloys before and after shot peening under different pressures are shown in Fig. 3. The diffraction peaks of the samples widen after shot peening because of the grain refinement on the surface layer. The peaks shift to a slightly lower angle, which indicates the existence of residual compressive stress induced by micro-strain. The widening and shifting of the diffraction peaks become more obvious with increasing the shot peened intensity. After shot peening, the peak intensity ratio of (100) to (101) remarkably changes, which represents the grain orientation changing from (100) to (101).
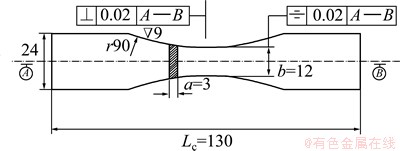
Fig. 2 Dimension of Ti-6Al-4V alloy specimens used for fatigue testing (unit: mm)
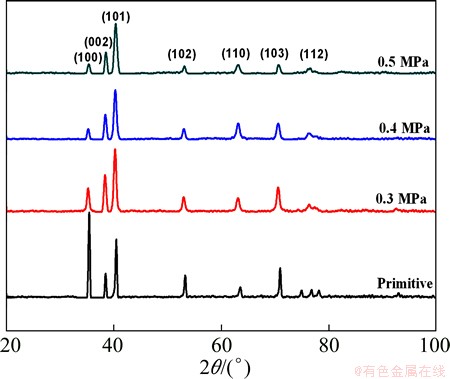
Fig. 3 XRD patterns of samples before and after shot peening under different pressures
3.2 TEM analysis
Figure 4 shows the TEM images beneath 25 μm of the treated surface under different pressures. Figure 4(a) illustrates that the intense elastic-plastic deformation occurs on the surface after repeatedly striking with the wet ceramic beads. A large number of dislocations also generate. As the dislocation glide proceeds, the dislocations tend to run into one another, pile up in front of obstacles, form a dislocation tangle, and then some irregular dislocation cells/sub-grains form (arrows in Fig. 4(a)). These dislocation cells/sub-grains consist of relatively dislocation-free regions surrounded by walls composed of dense tangles of dislocations.
Figure 4(b) shows significant grain refinement obtained after shot peening under 0.3 MPa. The average size of equiaxed grains is less than 100 nm. The diffraction pattern changes into a ring, which reveals that some grains and sub-grains with random orientation disparity coexist in the selected area. The grain refinement is attributed to the dislocation slipping as well as the formation of twins and twin-twin intersections. As plastic deformation continues, dislocations increase, slip, and accumulate, which leads to internal stress. When the stress reaches the critical resolved shear stress for mechanical twins, mono-system twins are formed. With increasing deformation, a twin-twin intersection of multi-systems gives rise to grain refinement [12,13]. The degree of plastic deformation and lattice distortion increases according to the increase in shot peened intensity. Consequently, the refined degree of grains increases and the diffraction ring becomes more intense (Figs. 4(c) and (d)). The sample surface is inclined to form ultra-fine grains after wet shot peening by ceramic beads. The interfacial bonding between the fine-grained layer and substrate is also fairly tight and difficult to separate. Therefore, wet shot peening is beneficial to the enhancement of the wear resistance and fatigue strength of Ti-6Al-4V alloy.
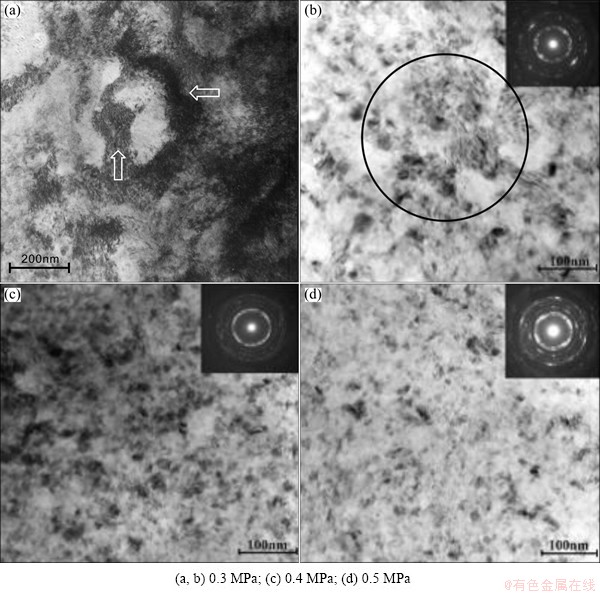
Fig. 4 TEM images of shot peened samples under different pressures
3.3 EBSD analysis
The misorientation of the low-angle boundary is characterized by values of 0°-15°. The length and density of the low-angle boundary calculated by EBSD analysis technology can quantitatively reflect the microcosmic deformation [14]. Figure 5(a) shows that the interface characteristics of samples are mainly high- angle boundaries. After shot peening under 0.3 MPa, the low-angle boundary length on the surface layer increases relatively to the matrix area, which indicates that microcosmic deformation occurs in surface structure. With increasing the shot peening intensity, the length and density of the low-angle boundary increase; the same phenomenon occurs in the matrix area (Figs. 5(b)-(d)). The increasing low-angle boundary (banded structure, dislocation tangle, etc.) prevents dislocation from slipping and thus improves the fatigue strength of materials [15].
3.4 Surface roughness analysis
The shot peened surface is more uneven than the untreated surface, and the surface roughness increases with increasing shot peening intensity. The arithmetic- mean values (Ra) of the un-peened and shot peened samples under different intensities are about 0.35, 0.48, 0.64, and 0.8 μm, which are all lower than those obtained by JIANG et al [16] and TSUJI et al [1] using dry shot peening (1.3 and 1.75 μm, respectively). By contrast, wet shot peening can yield preferable surface quality.
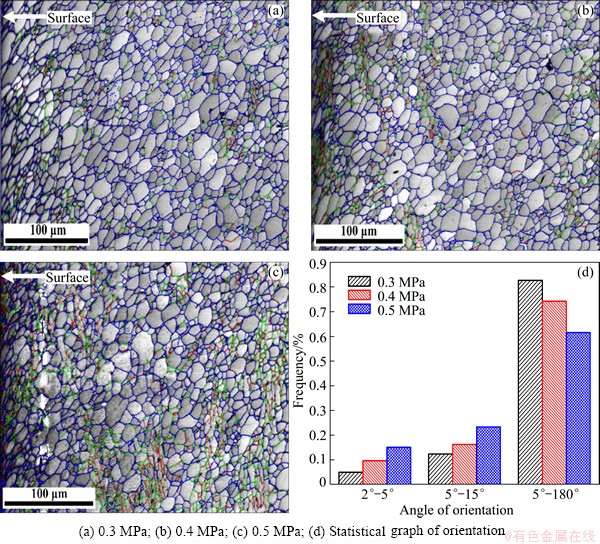
Fig. 5 Grain orientation maps of shot peened samples under different pressures
The increased surface roughness can make the compression stress layer thinner. It can also lead to the generation of tension stress on the sample surface, which hinders the improvement of fatigue resistance. Therefore, the surface roughness of the shot peened target should be as low as possible [16]. In this study, wet shot peening inflicted minor damage but exerted protective effects on the surface because of the lubrication and buffering of water, low breaking rate, and high roundness of the ceramic beads. Consequently, the stress concentration induced by low surface roughness decreases relatively to the dry shot peening, which is beneficial to the enhancement of the fatigue strength.
3.5 Residual stress analysis
The results indicate that the residual compressive stress fields exist on the surface of un-peened and shot peened specimens. Figure 6 shows the distribution of residual stresses beneath the surface under different conditions. Compared with the un-peened sample, the shot peened samples have much deeper compressive residual stress fields. The value of residual stress is higher than that of an untreated sample, and the maximum appears in the surface layer. The residual stress and the depth of stress field increase with increasing shot peened intensity. The maximum compressive residual stress is -895 MPa, and the maximum depth of the residual stress field is approximately 250 μm beneath the shot peened surface.
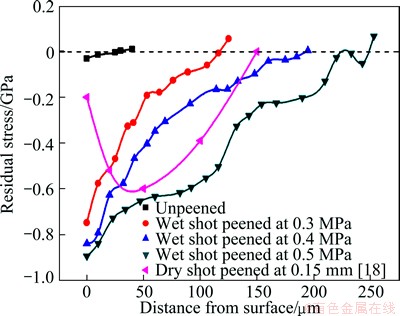
Fig. 6 Curves of residual stress distribution in wet shot peened samples
The surface residual stress is induced by the non- uniform elastic-plastic deformation and lattice distortion caused by the bombardment of ceramic balls against the component surface. The actual distribution of residual stress results from the competition of two processes, namely, hertz dynamic pressure and direct plastic extension [17,18]. For dry shot peening with a cast steel shot [17], the hertz dynamic pressure is dominant and plastic deformation is weak on the material surface when the steel shots bombard relatively hard materials. However, high shear stress appears in the sub-surface and plastic deformation also occurs in this region. Therefore, the maximum residual compressive stress is in the sub-surface layer. However, the ceramic bead (HV860) used in this experiment is sufficiently harder than Ti-6Al-4V alloy (HV330) to induce plastic deformation. The kinetic energy of the ceramic bead is less than that of the steel shot at the same speed, along with the lubrication and buffering of water. For these reasons, the maximum residual stress occurs in the surface layer where a large amount of plastic deformation exists. This attributes the greatest advantage of wet shot peening in improving fatigue strength because the fatigue crack source often initiates in the feeblest position, namely, the surface layer. Therefore, the critical stress of crack initiation significantly increases.
3.6 Fatigue strength analysis
The fatigue strength is affected by the surface hardness, roughness, compressive stress, and microstructure. The formation of residual compressive stress, increased hardness, and refinement of surface microstructure positively affect the fatigue strength, whereas increased roughness has an opposite effect. However, the effect of slightly increased surface roughness induced by wet shot peening is less than that of the residual compressive stress. A comparison of the stress-cycle number fatigue behavior of Ti-6Al-4V specimen before and after shot peening is shown in Fig. 7. The tensile fatigue limit improves from 605 MPa to 680 MPa by 12.4% after treatment. Therefore, wet shot peening with ceramic beads is an effective method of improving the fatigue strength of Ti-6Al-4V alloy.
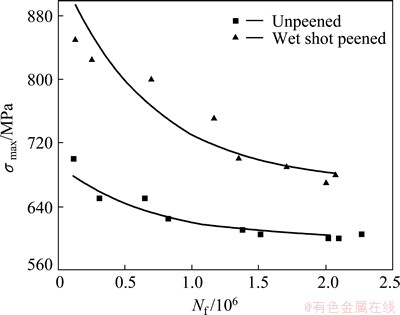
Fig. 7 Stress-cycle number (Nf) curves for Ti-6Al-4V alloy before and after shot peening
Figure 8(a) shows the SEM image showing fatigue fracture surface of the sample without shot peening, which consists of a fatigue crack source, a fatigue crack propagation region, and a fatigue fracture region. Fatigue cracks always initiate (or nucleate) on the surface of a component where dislocations slip more easily than on the sub-surface. Some microcracks (such as mechanical scratches) or metallurgical defects produced during processing also lead to crack initiation on the material surface. Two independent crack initiation sites are shown in Fig. 8(a). The crack source is related to the state and stress. On the other hand, the crack source of the shot peened sample (Fig. 8(b)) is located in the interior region beneath the surface and exhibits obvious radial striations. GAO [19] demonstrated that shot peening can lead to the formation of compressive stress and effectively reduce the tensile stress in the surface layer. Accordingly, the initiation site of fatigue crack shifts from the surface to the sub-surface and changes from multiple to single. The residual compressive stress can effectively reduce the tensile stress of an alternating load on the surface layer. Thus, the engineering stress of crack nucleation is heightened, which means that the fatigue strength can be enhanced by the residual compression stress. Evidently, wet shot peening is very effective in enhancing the fatigue strength of Ti-6Al-4V alloy.
The crack propagation region of the fatigue fracture surface in Fig. 8(c) presents parallel groove pattern- fatigue striation. As the most typical microscopic characteristic, each striation perpendicular to the direction of crack propagation is believed to represent the advanced distance of the crack front during a single load cycle. Generally, the crack more rapidly propagates and the fatigue striation widens with reduced material strength. Many microcracks and secondary cracks also exist in the propagation region. The fatigue microcracks caused by uneven local slipping and microscopic cracking grow into macrocracks. The structure of numerous spherical dimples in the rapid fracture region (Fig. 8(d)) is characteristic of a microvoid aggregation fracture.
4 Conclusions
Severe plastic deformation is induced on the material surface by the wet shot peening using ceramic beads. The deformation results in high dislocation density, grain refinement, increased low-angle boundary, and formation of compressive stress. The residual stress and depth of stress field also increase with increasing shot peened intensity. The maximum compressive residual stress is -895 MPa, and the maximum depth of the residual stress field is about 250 μm. The surface roughness of the wet shot peened sample is an order of magnitude lower than that of the dry shot peened sample. A tensile-tensile fatigue test reveals that the fatigue strength increases by 12.4% from 605 MPa to 680 MPa. These results indicate that wet shot peening with ceramic beads has favorable effects on the improvement of the fatigue property of Ti-6Al-4V alloy.
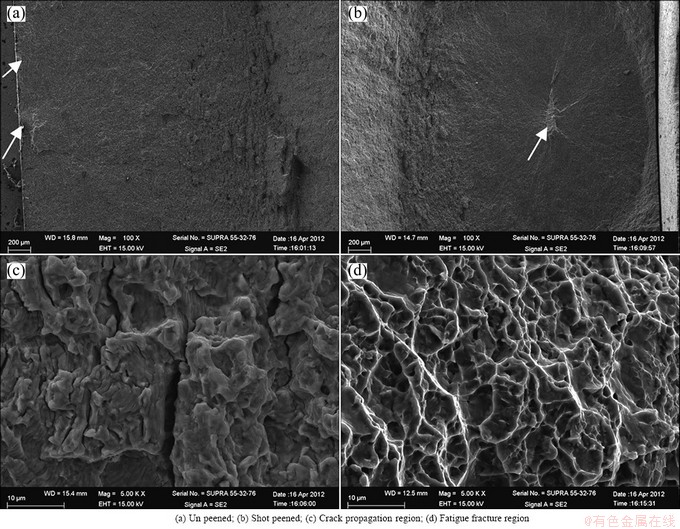
Fig. 8 SEM images of fatigue fracture surface before and after shot peening
References
[1] TSUJI N, TANAKA S, TAKASUGI T. Effects of combined plasma-carburizing and shot-peening on fatigue and wear properties of Ti-6Al-4V alloy [J]. Surface and Coatings Technology, 2009, 203(10-11): 1400-1405.
[2] GAO Yu-kui, WU Xue-ren. Experimental investigation and fatigue life prediction for 7475-T7351 aluminum alloy with and without shot peening [J]. Acta Materialia, 2011, 59(9): 3737-3747.
[3] ZHAN K, JIANG C H, JI V. Surface mechanical properties of S30432 austenitic steel after shot peening [J]. Applied Surface Science, 2012, 258(24): 9559-9563.
[4] LEE W B, CHO K T, KIM K H, MOON K I , LEE Y. The effect of the cementite phase on the surface hardening of carbon steels by shot peening [J]. Materials Science and Engineering A, 2010, 527(21-22): 5852-5857.
[5] ZHANG Xiao-hua, LIU Dao-xin. Surface mechanical properties of S30432 austenitic steel after shot peening [J]. International Journal of Fatigue, 2009, 31(5): 889-893.
[6] FRIDRICI V, FOUVRY S, KAPSA P. Effect of shot peening on the fretting wear of Ti-6Al-4V [J]. Wear, 2001, 250(1-12): 642-649.
[7] FRIDRICI V, FOUVRY S, KAPSA P, PERRUCHAUT P. Prediction of cracking in Ti-6Al-4V alloy under fretting-wear: Use of the SWT criterion [J]. Wear, 2005, 259(1-6): 300-308.
[8] LIU K K, HILL M R. The effects of laser peening and shot peening on fretting fatigue in Ti-6Al-4V coupons [J]. Tribology International, 2009, 42(9): 1250-1262.
[9] MORDYUK B N, IEFIMOV M O, PROKOPENKO G I, GOLUB T V, DANYLENKO M I. Structure, microhardness and damping characteristics of Al matrix composite reinforced with AlCuFe or Ti using ultrasonic impact peening [J]. Surface and Coatings Technology, 2010, 204(9-10): 1590-1598.
[10] TONSHOFF H K, KROOS F, MARZENELL C. High-pressure water peening—A new mechanical surface-strengthening process [J]. CIRP Annals-Manufacturing Technology, 1997, 46(1): 113-116.
[11] SAKODA S, TOSHA K. Shot peening using wet blasting machine with a wide nozzle [J]. Advanced Materials Science and Technology, 2009, 614: 163-168.
[12] WEN Ming, LIU Gang, GU Jian-feng, GUAN Wei-ming, LU Jian. Dislocation evolution in titanium during surface severe plastic deformation [J]. Applied Surface Science, 2009, 255(12): 6097-6102.
[13] GAO Yu-kui. Effect of shot peening on organization structure of TC4 titanium alloy [J]. Rare Metal Materials and Engineering, 2010, 39(9): 1536-1539.
[14] GODFREY A, CAO W Q, HANSEN N, LIU Q. Stored energy, microstructure, and flow stress of deformed metals [J]. Metallurgical and Materials Transactions A, 2005, 36(9): 2371-2378.
[15] KUNZ L, LUKAS P, SVOBODA M. Fatigue strength, microstructural stability and strain localization in ultrafine-grained copper [J]. Materials Science and Engineering A, 2006, 424(1-2): 97-104.
[16] JIANG X P, MAN C S, SHEPARD M J, ZHAI T. Effects of shot-peening and re-shot-peening on four-point bend fatigue behavior of Ti-6Al-4V [J]. Materials Science and Engineering A, 2007, 468-470: 137-143.
[17] YAN Wu-zhu, ZHANG Gang, WEN Shi-feng, LIU Jun, YUE Zhu-feng. Effect of surface roughness on evolution of residual stress field induced by shot peening [J]. Materials Science and Technology, 2010, 18(4): 523-527.
[18] FENG B X, MAO X N, YANG G J, YU L L, WU X D. Residual stress field and thermal relaxation behavior of shot-peened TC4-DT titanium alloy [J]. Materials Science and Engineering A, 2009, 512(1-2): 105-108.
[19] GAO Yu-kui. Influence of shot peening on tension-tension fatigue properties in Ti-10V-2Fe-3Al titanium alloy [J]. The Chinese Journal of Nonferrous Metals, 2004, 14(1): 60-63. (in Chinese).
Ti-6Al-4V合金的陶瓷湿喷丸表面强化工艺
陈国清1,焦 岩1,田唐永1,张新华2,李志强2,周文龙1
1. 大连理工大学 材料科学与工程学院,大连 116085;
2. 北京航空制造工程研究所,北京 100024
摘 要:采用新型陶瓷湿喷丸强化工艺对Ti-6Al-4V合金进行表面处理,研究不同喷丸强度对Ti-6Al-4V合金微观组织、形貌及残余应力的影响,并通过拉-拉疲劳试验验证陶瓷湿喷丸的强化效果,分析喷丸前后的断裂机理。结果表明:湿喷丸后的表面粗糙度较干喷丸的低,表面粗糙度、残余应力和应力场深度均随着喷丸强度的增加而增加,最大残余应力达-895 MPa,压应力层深度约为250 μm;拉-拉疲劳极限比初始的提高了12.4%。微观组织分析表明,喷丸处理后合金的表层位错密度显著增大,晶粒细化,表面形成超细晶。
关键词:Ti-6Al-4V合金;湿喷丸;微观组织;残余应力;疲劳性能
(Edited by Xiang-qun LI)
Foundation item: Project (NCET-10-0278) supported by Program for New Century Excellent Talents in University, China
Corresponding author: Guo-qing CHEN; Tel: +86-411-84707970; Fax: +86-411-84709967; E-mail: gqchen@dlut.edu.cn
DOI: 10.1016/S1003-6326(14)63112-5