Tribological property and wear mechanism of undercooled Ni-Pb monotectic alloys
XIE Hui(谢 辉)1, YANG Gen-cang(杨根仓)1, HAO Wei-xin(郝维新)1,
LA Pei-qing(喇培清)2, LIU Wei-min(刘维民)2, XU Li-jun(许丽君)1
(1. State Key Lab of Solidification Processing,Northwestern Polytechnical University, Xian 710072, China;
2. State Key Lab of Solid Lubrication, Lanzhou Institute of Chemical Physics,Chinese Academy of Sciences, Lanzhou 730000, China)
Abstract: The tribological properties of Ni-31.44%Pb monotectic alloys were measured by using a SRV reciprocating tribo-tester. The effects of load, sliding speed and melt undercooling on wear rate of the sample were investigated. The worn surface of Ni-31.44%Pb was examined using scanning electron microscope (SEM) and X-ray photoelectron spectroscope (XPS). The results show that the wear properties of the samples undercooled by 80K and 310K are obviously superior, which is attributed to more efficient transfer of Pb from the bulk material to the worn surface. The lubricating film is identified as a mixture of Ni2O3 and PbO by XPS analysis. At the same load and sliding speed, the predominant wear mechanisms can be identified as oxidative wear for the lower and larger undercooling, and plastic deformation and fracture for the medium undercooling.
Key words: Ni-Pb monotectic alloy; high undercooling; wear rate; wear mechanism CLC number: TG115.5
Document code: A
1 INTRODUCTION
Monotectic alloys have perfect physical and chemical properties and can be used as self-lubricating materials, electrical contact materials, superconducting materials etc[1-3]. However, it is very difficult to fabricate monotectic alloys with homogeneous structures by employing conventional casting, because the parent liquid decomposes quickly into two distinct immiscible liquids in the immiscibility gap[4-6]. The problem has delayed the utilization of monotectic alloys as industrial materials and systematic research on the solidification of monotectic alloys[7-9]. Single phase, eutectic and peritectic melts have been studied systematically by high undercooling and rapid solidification, and can solidify at a higher speed under larger undercooling and obtain more homogeneous microstructure with nearly no solution segregation[10, 11]. Up to now, there is nearly no literature to report the fabrication of homogeneous monotectic alloy and the stu- dy of the tribological property and wear mechanism by employing high undercooling technique. The main aim of the present paper is to report the tribological property and the wear mechanism of Ni-31.44%Pb (mass fraction) monotectic alloy undercooled by different undercooling, at the room temperature under the dry friction condition.
2 EXPERIMENTAL
Ni-31.44%Pb (mass fraction) monotectic alloy was fabricated by high undercooling technique, and its processing details have been reported elsewhere[12]. The sample was 2mm in thickness and 12mm in diameter. The counterpart was a GCr15 steel ball with hardness HRC62-63 and surface roughness Ra about 0.01μm with a diameter of 9.53mm. The chemical composition of the steel ball is given in Table 1.
Table 1 Chemical composition of SAE 52100 steel[13] (mass fraction, %)

Prior to tribological testing, the surfaces of the discs were polished with 1200-grit emery paper. All of the samples were cleaned in an ultrasonic bath with acetone and then ethanol for 20min, and then dried in hot air. Tribological tests were conducted using SRV reciprocating tribo-tester (see Fig.1) under reciprocating sliding at room temperature (23℃).
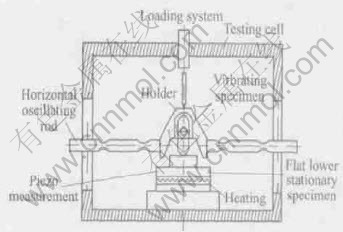
Fig.1 Schematic system of SRV reciprocating tribo-tester
The operating conditions were as follows. In all experiments, the stroke was 1mm, and the sliding time was 10min. The frequencies of oscillation ranged from 10Hz to 20Hz, which corresponds to sliding speeds of 0.02-0.04m/s. The load normally ranged from 10N to 30N with a 20Hz frequency.
The cross-section of the worn discs was measured using a surface profilometer. The wear volume of the sample was calculated by
V=SL(1)
where V is the wear volume of the sample, S is the cross-section area and L is the length of the stroke. The volumetric wear rate W was evaluated as
W=V/s(2)
where s is the total sliding distance. The test deviation was not more than 6%. After testing, the worn surface of the samples was studied using scanning electron microscope (SEM). The elements chemical states on the worn surface were determined by a PHI-5702 X-ray photoelectron spectroscopy (XPS). During XPS analysis, a 400W Mg Kα line was used, the pass energy was 29.350eV and the binding energy of C1s (284.6eV) was used as a reference, and the diameter of the spot was 400μm.
3 RESULTS AND DISCUSSION
3.1 Wear behavior
Under the dry sliding condition, the effect of load on the wear rate of Ni-Pb monotectic alloy under different undercoolings are shown in Fig.2. It can be seen that the wear rate of the alloy sharply increases with load under the same undercooling. In addition, the wear rate of the samples undercooled by 80K and 310K is obviously smaller than that of the others.
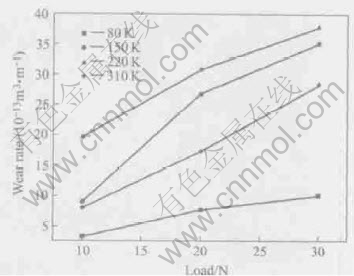
Fig.2 Wear rates of Ni-31.44%Pb monotectic alloys vs load at sliding speed of 0.04m/s
At the same sliding speed, superior performance of the materials undercooled by 80K and 310K is easy to be explained in the transfer efficiency of the Pb element. Typical microstructures of Ni-31.44%Pb monotectic alloy under the different undercooling are shown in Fig.3, where the white is nickel-rich phase and the dark lead-rich phase. When the undercooling is 80K, the microstructure is mainly composed of rough α-Ni dendrites and intradendritic massive Pb lumps (Fig.3(a)), where the Pb element can transfer continuously from the interior of material to the worn surface because of the presence of large size Pb lumps. With the increase of undercooling, the size of Pb lumps becomes smaller (Fig.3(b) and 3(c)) and the Pb transfer becomes difficult, the corresponding wear rate increases obviously. However, when the undercooling is 310K, the wear rate is obviously smaller than those of 150K and 220K, which results from the solid solubility change of Pb element in the nickel-rich phase under high undercooling conditions. It is well known that the maximum solid solubility of Pb element in α-Ni is about 1.02% (mole fraction) (or 4.1%, mass fraction) under the equilibrium solidification conditions[15]. In our previous work[14], the Pb solubility can reach 5.83% (or 17.83%, mass fraction) at the undercooling 418K because of distinct solute trapping. Therefore, the Pb element on the worn surface should be mainly transferred from the interior of α-Ni dendrites(Fig.3(d)) but not from the interdendritic regions, which is a useful way to increase the Pb transferability by the increase of relative contact area between the sample and the counterpart.
The variation of wear rate with the sliding speed at the 20N load is given in Fig.4. It can be seen that the wear rates of the samples undercooled by 80K and 150K decrease with the increase of
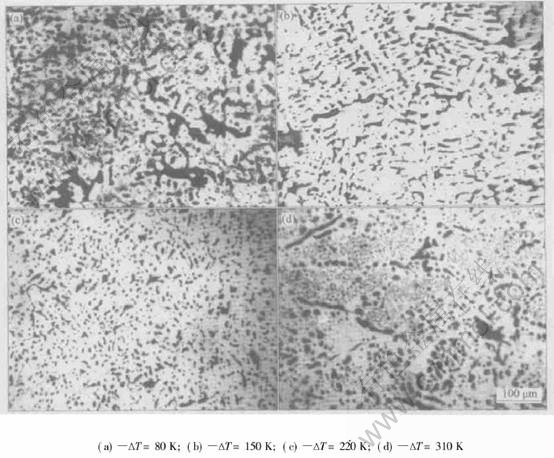
Fig.3 Microstructures of Ni-31.44%Pb monotectic alloys under different undercoolings
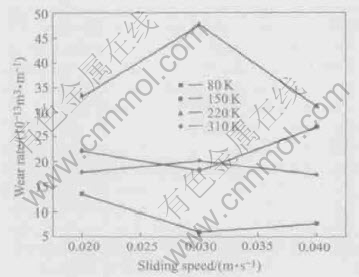
Fig.4 Wear rates of Ni-31.44%Pb monotectic alloys vs sliding speed at load 20N
sliding speed at first, and then the wear rates increase with the sliding speed increasing. Whereas, the wear rates of the samples undercooled by 220K and 310K increase with the speed increasing at first, and then decrease with the sliding speed. The experiment results above-mentioned can be explained as follows.
At the same load, for the smaller under-cooling, it is helpful for the lower sliding speed to hold the Pb element transferred from the interior of the material on the worn surface, which causes the wear rate to decrease. But the loss of Pb element to the worn surface, as transferred from the interior of the material, becomes easy with the increase of sliding speed, and finally causes the wear rate to increase. Under the larger undercooling, it is obviously useful for the larger sliding speed to help Pb element to transfer from the interior of material to the worn surface. The real reason that the wear rate of the sample undercooled by 310K is obviously lower than that of 220K is also attributed to the solid solubility difference between two different undercoolings.
In the present work, a black film was observed on almost the entire worn surface of the Ni-Pb bearing alloys and was apparent on the worn surface of specimens tested at the higher load or sliding speed. The chemical states of Ni and Pb elements on the Ni-31.44%Pb worn surface investigated using XPS analysis are shown in Fig.5. The analysis reveals that the nickel and lead exist mainly in compound states. According to Fig.4(a), the binding energy of the nickel 2p3/2 peak is 855.4eV. This is probably indicative of the presence of Ni2O3, based on literature data[16]. Fig.4(b) shows that the binding energy of the lead component is 138.5eV, midway between 136.9eV of the lead 4f7/2 peak and 141.7eV of lead 4f5/2 peak, which is approximately associated with PbO. Consequently, it can be concluded that the lubricating film on the worn surface is a mixture of Ni2O3 and PbO.
The XPS results also indicate that the lubricating film is actually the reaction products of Ni and Pb which react with oxygen in the atmosphere under high contact pressure and surface temperature. Pure Pb is not found in the film which is different from the pure Pb film that has been reported by many workers[17, 18]. The film on the interface between the Ni-Pb monotectic alloy and steel ball restricts metal-metal contact, and hence the resistance to wear and friction is improved.
3.2 Surface morphology and wear mechanism
Fig.6 shows the SEM morphologies of the worn surface, which reflects the effect of the lubricating film on the wear of Ni-Pb monotectic alloys. Under the same load and sliding speed, the worn surface of Ni-Pb monotectic alloys undercooled by 80K and 310K appears smooth and consists of small grooves, and some powder is present at the bottom of these grooves. XPS examination of the
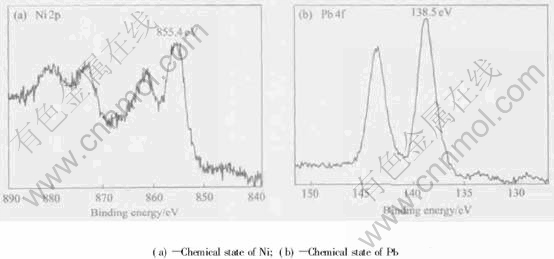
Fig.5 XPS spectra of worn debris of Ni-Pb monotectic alloy
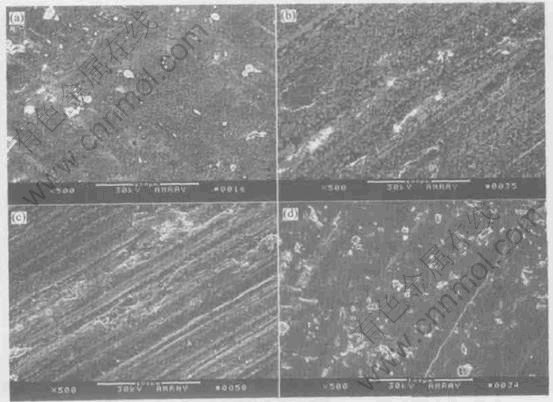
Fig.6 Morphologies of worn surfaces of Ni-Pb monotectic alloys undercooled by 80K(a), 310K(b), 150K(c) and 220K(d) at 20N, 0.04m/s
wear debris shows the existence of nickel and lead oxides, indicating that oxidative wear is the main mechanism for the samples with lower and higher degrees of undercooling. Compared with that of the samples undercooled by 80K and 310K, the worn surfaces of the samples undercooled by 150K and 220K underwent significant plastic deformation, resulting in fracture, which can lead to the ejection of large wear fragments from the testing sample. Hence, for the medium undercooling region, the predominant wear mechanism can be identified as plastic deformation and fracture.
4 CONCLUSIONS
1) The wear rate of samples undercooled by 80K and 310K is obviously smaller than that of the others, which is attributed to more efficient transfer of Pb from the bulk material to the friction surface.
2) The lubricating film is identified as a mixture of Ni2O3 and PbO by XPS analysis.
3) At the same load and sliding speed, for the lower and larger undercooled samples, the main wear mechanism is oxidative wear. For the medium undercooled samples, the predominant wear mechanism can be identified as plastic deformation and fracture.
REFERENCES
[1]Inoue A, Yano N. Microstructure and superconducting prosperities of melt quenched insoluble Al-Pb and Al-Pb-Bi alloys[J]. J Metal Sci, 1987, 22(1): 123-128.
[2]Wecker J, Helmott J R, Schultz L, et al. Giant magneto-resistance in melt spun Cu-Co alloys[J]. App Phys Let, 1993, 62(16): 1985-1987.
[3]Pratt G C. Materials for plain bearing[J]. Int Met Rev, 1973,18: 62-88.
[4]XIAN A P, ZHANG H W, LI Z Y. Preparation of homogeneity immiscible alloy by marangoni convection[J]. Acta Metall Sinica, 1996,32:113-119. (in Chinese)
[5]ZHANG H W, XIAN A P. Study of Al-Bi immiscible alloy control-casting technique[J]. Acta Metall Sinica,1999, 35:1187-1190. (in Chinese)
[6]LIU Y, GUO J J, JIA J. Liquid-liquid separation mechanism and preparation technique of homogeneous monotectic alloys[J]. Foundry, 2000, 49:11-17. (in Chinese)
[7]Mackay M L. Innovation in powder metallurgy: An engine bearing material[J]. Met Pro, 1977, 111: 32-35.
[8]Uenishi K, Kawaguchi H, Kobayashi K F. Microstructure of mechanically alloyed Al-In alloys[J]. J Mater Sci, 1994, 29(20): 4860-4865.
[9]Feder R J, Smith W E. Method of making a fine dispersion aluminum based bearing[P]. US3797084.1974.
[10]LI J F, ZHOU Y H, YANG G C. Solidification behavior of undercooled Cu70Ni30 alloy melts[J]. Mater Sci Eng, 2000, A277: 161-168.
[11]ZHANG Z Z, SONG G S, YANG G C, et al. Recalescence behavior and solidification structure of the undercooled Fe82B17Si1 eutectic alloy[J]. Prog Nat Sci, 2000, 10: 364-370.
[12]XIE H, YANG G C, HAO W X, et al. Solidification behavior of undercooled Ni-Pb hypermonotectic alloys[J]. J Mater Sci, 2004, 39: 2561-2563.
[13]LA P Q, XUE Q J, LIU W M. Tribological properties of Ni3Al-Cr7C3 composite coating under water lubrication[J]. Tribol Int, 2000, 33: 469-475.
[14]Aziz M J. Model for solute redistribution during rapid solidification[J]. J Appl Phys, 1982, 53: 1158-1168.
[15]Nash P. Phase Diagrams of Binary Nickel Alloys: Nickel-Lead[M]. OH: Materials Park, 1991. 247-251.
[16]Moulder J F, Stickle W F, Sobol P E, et al. Handbook of X-ray Photoelectron Spectroscopy[M]. MN: Perkin-Elmer Physical Electronics Division, 1992. 84-85, 188-189.
[17]Mohan S, Agarwala V, Ray S. Wear characteristics of stir-cast aluminum-lead alloys[J]. Z Metkd, 1989, 80: 904-908.
[18]Mohan S, Agarwala V, Ray S. Microstructure and wear characteristics of rheocast Al-Pb bearing alloys[J]. Trans JIM, 1992, 33: 861-869.
(Edited by YUAN Sai-qian)
Foundation item: Project (G2000067202) supported by the National Basic Research Program of China; Project (50171055) supported by the National Natural Science Foundation of China; Project (01G53046) supported by the Aviation Science Foundation of China; Project (200208) supported by the Doctorate Creation Foundation of NWPU for the Financial Support; and Project(0206) supported by the Foundation of State Key Lab. of Solid Lubrication
Received date: 2004-05-31; Accepted date: 2004-09-06
Correspondence: XIE Hui, PhD; Tel: +86-29-88491484; E-mail: xaxiehui@hotmail.com