文章编号:1004-0609(2007)07-1207-06
高炉尘泥化学除锌
黄志华, 伍喜庆, 彭冠兰
(中南大学 资源加工与生物工程学院,长沙 410083)
摘 要:为了降低经物理分选后的高炉精泥中锌的含量,对高炉精泥进行化学浸出除锌研究,考察浸出剂、浸出时间、温度、液固比和搅拌速度等对浸出的影响,并进行理论分析。结果表明:硫酸对锌的浸出率最高,氯化铁次之,氨水最低;在合适的浸出条件下:液固比8?1,温度20 ℃,硫酸浓度125 g/L,浸出时间35 min和搅拌速度150 r/min,锌浸出率为73.9%,高炉精泥中的锌含量从1.46%降低到0.38%。对硫酸浸出脱锌的动力学和反应机制的研究表明,浸出过程遵从1-2α/3-(1-α)2/3=kt,浸出反应的活化能为8.89 kJ/mol,属于扩散控制过程。
关键词:高炉尘泥;除锌;循环利用;动力学;浸出
中图分类号: 文献标识码:A
Removal of zinc from blast furnace dust by chemical leaching
HUANG Zhi-hua, WU Xi-qing, PENG Guan-lan
(School of Resources Processing and Bioengineering, Central South University, Changsha 410083, China)
Abstract: Chemical leaching zinc from blast furnace dust concentrate (BFDC) treated by physical separation was investigated in order to reduce the content of zinc, and all common operating factors, such as leaching duration, temperature, ratio of liquid to solid and stirring rate, have tested. The results show that among the three leaching chemicals tested (sulfuric acid, ferric chloride and amine) sulfuric acid is the best one for leaching zinc. A zinc leaching rate of 73.9% is achieved and resultantly the content of zinc in the product is reduced from 1.46% to 0.38% under the following proper leaching conditions: ratio of liquid to solid 8?1, room temperature (about 20 ℃), acid concentration of 125 g/L, leaching time 35 min and stirring rate 150 r/min. The kinetics and reaction mechanism of zinc acid leaching indicate that the leaching reaction conforms to the equation: 1-2α/3-(1-α)2/3=kt, the activation energy for the sulfuric acid leaching is 8.89 kJ/mol, and the leaching process is controlled by diffusion.
Key words: blast furnace dust; zinc removal; recycling; kinetics; leaching
高炉冶金尘泥(又称瓦斯尘(灰)和瓦斯泥),主要源于钢铁工业的高炉炼铁过程[1]。高炉瓦斯尘泥中主要成分为铁、碳以及硅和钙镁等,且数量较大,最方便的再利用莫过于将其循环用做高炉原料。就循环利用尘泥做炼铁原料(如送至烧结厂)而言,最大问题是其中的重金属(Zn、Pb等)等有害元素的存在,这些元素主要来源于原料和燃料。
锌等重金属元素的存在对尘泥循环利用做炼铁原料的危害性主要表现在于:锌与高炉炉衬内的元素结合形成低熔点的化合物而软化炉衬,使炉衬腐蚀速度加快而影响高炉寿命;锌在高炉内以及烧结-高炉间的不断循环累积,富集到一定程度时,促使炉瘤生成,高炉内粘结严重,使炉身中上部风量加不上,影响稳产高产;此外,锌的循环存在会增大高炉焦比以及影响产品质量[2-4]。
目前,各钢铁厂对高炉瓦斯尘泥有以下处理方法:
直接外排堆存(未利用);厂内直接循环使用或部分使用(使用多少取决于烧结矿中锌的测定);综合回收利用。而要循环利用好尘泥,一方面要考虑有用元素铁和碳的富集再利用,另一方面还要考虑除去锌等重金属元素。
一般回收铁用弱磁选[5-7]、摇床[8]或反浮选[9]等方法;回收碳采用烃油类捕收剂(煤油或柴油)浮选的方法[7-9]。去锌等重金属元素是指降低上述回收利用的铁和碳精矿中锌等重金属元素的含量。物理方法回收铁和碳,通常也可使锌等重金属元素的含量降低,如水力旋流器[10-12]、磁选[13]和浮选[14-15]等。但是,这些物理方法去锌不太理想。
尘泥粒子表面多孔,大的尘泥粒子往往是小粒子的团聚体;对尘泥粒子(40 μm)的剖面分析,发现尘泥粒子的结构为:内核为金属铁芯,其外层为团聚的氧化亚铁层,再外层为团聚的锌铁尖晶石微粒子层。化学分析也进一步佐证,在尘泥粒子的表面有一富含锌的薄层,而铁作为主要元素以不同的形式分布于整个粒子中,氧的分布与铁相似,只是在中核含金属铁[15]。
从锌在尘泥粒子中的分布来看,用单一的物理分离方法将锌降至很低不现实。化学除锌是另一个值得研究的方向。许多国家(如伊朗[18]、芬兰[19]、法国[22]等)采用湿法冶金技术,选用适当的浸出剂(如NTA3-、FeCl3[17]、酸、碱、氨基乙酸),将有用金属锌从尘泥中选择性地浸取出来,之后对浸出液提纯、分离,从而回收。
本文作者用化学浸出的方法对高炉尘泥经物理分选后的精泥进一步除锌,降低锌金属在精泥中的含量,使得这种精泥便于高炉回收利用。
1 实验
1.1 试样和试剂
所用试样源于某钢铁厂的高炉尘泥经物理分选后的精泥,含铁60.11%(全铁),含锌1.46%;粒度组成为29.5%小于74 μm。所用试剂:硫酸和氯化铁为工业纯;五水硫酸铜和氨水为分析纯;铜氨络离子溶液为实验室配制,采用0.2 g五水硫酸铜和8 mL氨水配制成200 mL铜氨络离子的稀溶液。
1.2 方法
每次称取10 g精泥试样放入200 mL的带刻度的烧杯中,加水调整至一定刻度获得合适液固比(一般为4?1),之后加入浸出剂,于20 ℃以150 r/min搅拌浸出20 min,然后过滤,测出溶液中Zn2+的浓度,从而计算浸出率。
2 结果和讨论
2.1 浸出剂的选择
浸出剂的种类很多,选择一种浸出率高、选择性好的浸出剂是实现化学脱锌的关键。常用浸出剂大致有酸类、盐类和碱类等,为此,这里采用具代表性且常用的硫酸、氯化铁和氨水等浸出剂,比较它们的浸出性能。
硫酸、氯化铁和氨水等浸出剂浸出锌和铁的结果如图1所示。从图中可以看出,在浸出剂同样用量的条件下,硫酸对锌的浸出效果最好,浸出率最高,氯化铁次之,氨水最低,浸出率最大分别为71.3%、50.8%和21.9%;为考查浸出的选择性,铁的浸出率也一并示于图上。从铁的浸出率看,硫酸和氯化铁接近,均在10%左右,氨水基本不浸出铁,所以未在图中标出。硫酸可以很好地浸出锌,分别比用氯化铁和氨水浸出多20.5%和49.3%,浸出铁少,有比较高的选择性,且硫酸价格低廉。所以,选用硫酸为浸出剂进行后面的实验。
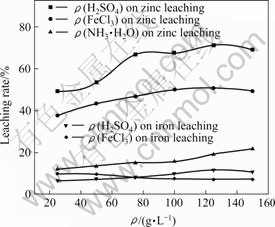
图1 浸出剂的浓度对浸出率的影响
Fig.1 Effect of ρ(H2SO4, FeCl3, NH3?H2O) on leaching rate
混合浸出剂(硫酸+氯化铁)或添加铜氨络离子对锌的浸出率的影响如图2和图3所示。由图可以看出,随着氯化铁配比的增加,锌的浸出率呈下降的趋势,浸出率介于纯硫酸和氯化铁的浸出率之间,未出现协同增大的效应。这可能是在总用量一定的情况下,加入氯化铁,减少了硫酸的用量,造成对锌的浸出率的降低;加入铜氨络合离子后,锌的浸出率维持在49%
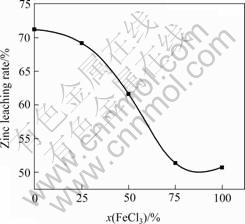
图 2 硫酸与氯化铁配比对锌的浸出率的影响
Fig.2 Effect of ratio of H2SO4 to FeCl3 on zinc leaching rate

图3 铜氨络离子对锌的浸出率的影响
Fig.3 Effect of addition of cupric-ammonium complex ion on zinc leaching rate
左右,基本不影响硫酸浸出锌。可见,使用混合浸出剂(硫酸+氯化铁)或添加铜氨络离子都不能达到促进硫酸浸出锌的目的。
高炉尘泥中的元素锌和铁等基本是以氧化物的形式存在, 且锌等重金属倾向于分布在尘泥的细粒级部分, 含铁物相主要为金属铁、磁铁矿和(假象)赤铁矿,含锌矿物为氧化锌,含铅矿物为氧化铅,但氧化锌(铅)难以单相存在,而以极细颗粒附着在硅酸盐和焦碳末粒子上[6, 10, 15-16]。因此,硫酸浸出剂参与的浸出反应实质是金属氧化物与酸反应的非氧化-还原反应,根据反应类型可以判断此反应与pH值有关。反应的通式如下:

式中 αM为Mm+离子的活度,pH0为某一温度下标准反应所需pH值。25 ℃时溶解ZnO、Fe2O3和Fe3O4反应的pH0分别为5.8、-0.24和0.891[23]。由此,比铁的氧化物,锌可以在较高的pH值条件下被浸出;只要控制溶液的pH值在适当范围,就可加强对锌的浸出,削弱对铁矿物的浸出,从而实现ZnO与Fe2O3、Fe3O4的选择性浸出。
2.2 浸出的影响因素
影响浸出的因素有很多,一般的动力学研究表明,较重要的影响因素有:颗粒的大小、浸出的温度、溶剂的浓度、液固比和搅拌速度等。由于样品的粒度偏细,这里不考察粒度的影响,其它如浸出时间、浸出温度、液固比和搅拌速度等对浸出的影响,分别如图4~7所示。
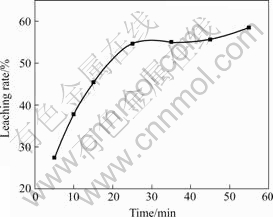
图4 浸出时间对浸出率的影响
Fig.4 Effect of reaction time on leaching rate
从图4可以看出,其他条件(硫酸用量25 g/L,液固比4/1,温度为20 ℃,搅拌速度150 r/min)相同时,浸出率随浸出时间的延长而逐渐增大。在25 min之前,浸出率迅速增大;此后,浸出率增长的速率变缓慢;在55 min时,浸出率为58.4%,比25 min时高3.8%。这表明浸出25 min可以使锌浸出比较充分。
图5所示为浸出温度对浸出率的影响。在80 ℃以下,呈现有规律的增长,之后达到稳定,浸出率也从20 ℃时的45.3%增长到80 ℃时的57.8%,高于80 ℃时,浸出温度对浸出率影响不大。在一定条件下,扩散系数D(后面证实为扩散控制)与温度T的关系[23]为:

式中 r为扩散物质粒子直径;μ为扩散介质粘度。其它条件不变时,随着温度的升高,扩散系数也会升高,浸出率随之增大。
浸出矿浆液固比的大小既影响浸出剂用量又影响矿浆的粘度。如图6所示,在液固比3?1到8?1范围
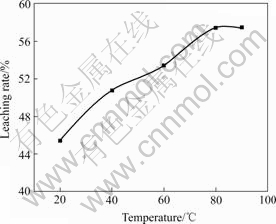
图5 浸出温度对浸出率的影响
Fig.5 Effect of reaction temperature on leaching rate

图6 液固比对浸出率的影响
Fig.6 Effect of ratio of liquid to solid on leaching rate
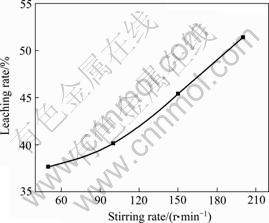
图7 搅拌速度对浸出率的影响
Fig.7 Effect of stirring rate on leaching rate
内,提高矿浆液固比,得到较高的浸出率。 当液固比达到8?1时,再增大液固比对浸出率的影响不大,因此确定最佳液固比为8?1。
搅拌对于一个以扩散过程为控制的反应是很重要的。搅拌可以防止矿粒沉降,还可以减小扩散阻力、增大扩散系数,减小颗粒扩散层的厚度。从图7可以看出,在实验范围内,浸出时间相同时,随着搅拌速度的增大,锌浸出率有较大幅度的提升,说明搅拌对锌的浸出有利。
2.3 最终浸出结果
在上述实验的基础上,选择以下合适的条件:液固比8?1、浸出温度20 ℃、硫酸用量125 g/L、浸出时间35 min、搅拌速度150 r/min,可浸出高炉精泥中的锌,得到73.9%的锌浸出率,将高炉精泥中的锌含量降到0.38%。
3 浸出动力学
3.1 浸出动力学方程
液固浸出反应一般可概括为以下几个步骤:反应物在溶液中向固体表面扩散、反应物向固体内部扩散、反应物在表面起化学作用、生成物从固体内部向外表扩散和生成物离开固体表面向溶液扩散。因此,其反应控制步骤可分为外扩散控制、内扩散控制、化学反应控制以及混合控制。如果是受内扩散控制的反应,其动力学方程[20-21]符合:
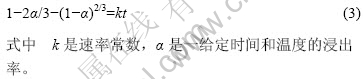
为了验证此浸出反应符合扩散控制的观点,将1-2α/3- (1-α)2/3 对反应时间t作图。如图8所示,在温度为20 ℃、40 ℃和60 ℃的情况下,动力学曲线均为一直线,证明此浸出反应满足此动力学方程,浸出反应受扩散控制,此时K分别为:1.78×10-3、2.44×10-3和2.75×10-3。
3.2 浸出反应的活化能
应用阿仑尼乌斯公式,并进行适当处理,可得如下方程:

将图8中的所得温度下(T)的速度常数(K)作lgK—1/T图,如图9所示。从图可以看出,lgK—1/T关系基本为一直线,该浸出反

图8 硫酸浸出锌的动力学曲线
Fig.8 Leaching kinetics
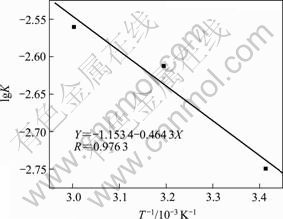
图9 Arrhenius图
Fig.9 Arrhenius diagram
应符合阿仑尼乌斯方程,进而可以算出反应的表观活化能为8.89 kJ/mol。表观活化能低,浸出反应属于扩散控制范围(化学动力学研究表明,一般表观活化能小于13 kJ/mol,即可认定为扩散控制过程[20]),与前述动力学方程研究的结果一致。
4 结论
1) 硫酸、氯化铁和氨水等常用浸出剂对高炉精泥的浸出表明,硫酸对锌的浸出率最高,氯化铁次之,氨水最低;硫酸不但可以很好的浸出锌,而且有比较好的选择性;混合使用浸出剂(硫酸+氯化铁)或添加铜氨络离子都不能达到促进硫酸浸出锌的目的。
2) 温度升高可提高硫酸浸锌的浸出率。在室温20 ℃下,硫酸浸出锌的合适条件为:液固比8?1、硫酸用量125 g/L、浸出时间35 min、搅拌速度150 r/min;所得锌的浸出率为73.9%,可将高炉精泥中的锌含量从1.46%降到0.38%,从而作为一种原料供高炉炼铁用。
3) 硫酸浸出锌的动力学和反应机制的研究则发现,过程遵从1-2α/3- (1-α)2/3方程,浸出反应的活化能为8.89 kJ/mol,属于扩散控制过程。
REFERENCES
[1] 邱显冰. 冶金含铁尘泥的基本特征与在资源化[J]. 安徽冶金科技职业学院学报, 2004(3): 54-56.
QIU Xian-bin. Basic character of iron containing metallurgical dust and resource regeneration[J]. Journal of Anhui Vocational College of Metallurgy and Technology, 2004(3): 54-56.
[2] 中南矿冶学院. 铁矿粉造块[M]. 北京: 冶金出版社, 1978: 10.
Institute of Central South Mining and Metallurgy. Iron ore Powder Agglomeration[M]. Beijing: Metallurgy Press, 1978: 10.
[3] Makkonen H T. Optimization of steel plant recycling in Finland: dusts, scales and sludge[J]. Resources Conservation and Recycling, 2002, 35: 77-84.
[4] 李肇毅. 宝钢高炉的锌危害及其抑制[J]. 宝钢技术, 2002(6): 18-21.
LI Zhao-yi. Damage of element of zinc to blast furnace and its inhibition[J]. Bao Steel Technology, 2002(6): 18-21.
[5] 石振明. 高炉瓦斯泥中铁的回收[J]. 金属矿山, 1995(8): 34-37.
SHI Zhen-ming. Recovery of iron from gas slime of blast furnace[J]. Metal Mine, 1995(8): 34-37.
[6] 唐晓莲, 宫中桂. 某钢铁厂高炉瓦斯泥综合利用试验研究[J]. 矿产综合利用, 1996(1): 44-47.
TANG Xiao-lian, GONG Zhong-gui. Research on comprehensive utilization of BF sludge of iron and steel company[J]. Multipurpose Utilization of Mineral Resources, 1996(1): 44-47.
[7] 李嘉智, 李 峰. 合理利用高炉烟尘[J]. 成都科技大学学报(自然科学版), 1994, 13(2): 13-17.
LI Jia-zhi, LI Feng. Pational utilization of blast-furnace flue dust department of metallurgy[J]. Journal of Chengdu University (Natural Science), 1994, 13(2): 13-17.
[8] 孙体昌, 胡永平. 济钢高炉瓦斯泥的可选性研究[J]. 矿产综合利用, 1997(5): 4-8.
SUN Ti-chang, HU Yong-ping. Beneficiability study of the blast furnace dust from Ji’nan iron and steel company[J]. Multipurpose Utilization of Mineral Resources, 1997(5): 4-8.
[9] 丁忠浩, 翁 达. 高炉瓦斯泥微泡浮选柱浮选工艺研究[J]. 武汉科技大学学报(自然科学版), 2001, 24(4): 353-354.
DING Zhong-hao, WENG Da. Study on flotation process to treat the blast-furnace soot by fine-bubble flotation column[J]. Journal of Wuhan Yejin University of Science and Technology, 2001, 24(4): 353-354.
[10] Callenfels S, Van J E. 高炉污泥处理用的水力旋流设备[J]. 钢铁, 2004, 39(1): 59-64.
Callenfels S, Van J E. Hydrocyclone installation for blast furnace sludge treatment[J]. Iron and Steel, 2004, 39(1): 59-64.
[11] 林高平, 邹 宽. 高炉瓦斯泥回收利用新技术[J]. 矿产综合利用, 2002(3): 42-45.
LIN Gao-ping, ZOU Kuan. Recovery of blast furnace sludge by hydrocyclone[J]. Multipurpose Utilization of Mineral Resources, 2002(3): 42-45.
[12] 邹 宽, 林高平. 使用水力旋流器回收高炉瓦斯泥[J]. 中国冶金, 2003(9): 29-34.
ZOU Kuan, LIN Gao-ping. Recovery of BF sludge by hydrocyclone[J]. China Metallurgy, 2003(9): 29-34.
[13] 于留春. 梅山高炉瓦斯泥综合利用的研究[J]. 宝钢技术, 2003(6): 22-25.
YU Liu-chun. Study on comprehensive utilization of BF gas slime at meishan[J]. Bao Steel Technology, 2003(6): 22-25.
[14] Smith S M. A novel process for recycling steel-making dust[J]. Iron and Steel Maker, 2000, 27(2): 69-76.
[15] Kelebek S. Characterization of basic oxygen furnace dust and zinc removal by acid leaching[J]. Minerals Engineering, 2004, 17: 285-291.
[16] 王东彦, 王文忠. 转炉和含锌铅高炉尘泥的物性和物相分析[J]. 中国有色金属学报, 1998, 8(1): 135-139.
WANG Dong-yan, WANG Wen-zhong. Analysis of intrinsic properties and phase condition on converter sludge and bearing Zn Pb blast furnace sludge[J]. The Chinese Journal of Nonferrous Metals, 1998, 8(1): 135-139.
[17] Leclerc N, Meux E, Lecuire J M. Hydrometallurgical recovery of zinc and lead from electric arc furnace dust using mononitrilotriacetate anion and hexahydrated ferric chloride[J]. Journal of Hazardous Materials, 2002, B91: 257-270.
[18] Asadi Z B, Mowla D, Shariat M H, Fathi K J. Zinc recovery from blast furnace flue dust[J]. Hydrometallurgy, 1997, 47: 113-125.
[19] Makkonen H T, Heino J, Laitila L. Optimisation of steel plant recycling in Finland: dusts, scales and sludge[J]. Resources, Conservation and Recycling, 2002, 35: 77-84.
[20] 陆九芳, 李总成, 包铁竹. 分离过程化学[M]. 北京: 清华大学出版社, 1993.
LU Jiu-fang, LI Zong-cheng, BAO Tie-zhu. Separation chemistry[M]. Beijing: Tsinghua University Press, 1993.
[21] 戈 芳, 池汝安. 用盐酸从矿泥中浸出稀土的动力学控制分析[J]. 稀土, 2003, 24(6): 16-19.
GE Fang, CHI Ru-an. Analysis of kinetics control on leaching rare earth from weathered with hydrochloric acid[J]. Rare Earth, 2003, 24(6): 16-19.
[22] Rodriguez-Torres I, Valentin G, Chanel S, Lapicque F. Recovery of zinc and nickel from electrogalvanisation sludge using glycine solutions[J]. Electrochimica Acta, 2000, 46: 279-287.
[23] 黄礼煌. 化学选矿[M]. 北京: 冶金工业出版社, 1990.
HUANG Li-huang. Chemical beneficiation[M]. Beijing: Metallurgy Industry Press, 1999.
(编辑 李向群)
收稿日期:2006-11-08;修订日期:2007-03-08
通讯作者:伍喜庆,博士,副教授;电话:0731-8830548(O);E-mail: xiqingwu@hotmail.com