Trans. Nonferrous Met. Soc. China 20(2010) s1037-s1041

Structure of miniature components from steel produced by forming in semi-solid state
b. Masek1, D. Aisman1, M. Behulova2, H. Jirkova1
1. The Research Centre of Forming Technology, University of West Bohemia,
Univerzitni 22, P. O. Box 314, 306 14 Pilsen, Czech Republic;
2. Faculty of Materials Science and Technology in Trnava, Slovak University of Technology in Bratislava,
Paulinska 16, 917 24 Trnava, Slovak Republic
Received 13 May 2010; accepted 25 June 2010
Abstract: To obtain new unconventional structures with specific mechanical and physical properties is possible not only by the development of new types of materials but also by treatment of conventional materials using unconventional innovative technological procedures. One of these technologies is the forming in semi-solid state involving rapid solidification of miniature components from steels. Production of such components is complicated by a number of technical problems. To explain phenomena of the process and structure development, the production of miniature components from the tool steel X210Cr12 difficult to form was experimentally tested. The structure of this originally ledeburite steel consisted of 95 % of metastable austenite after the treatment. Metastable austenite was located particularly in globular and polygonal grains while the remaining interspaces were filled by lamellar network. The detected high stability of extremely high fraction of metastable austenite was tested under different conditions of thermal exposition and mechanical loading.
Key words: semi-solid state; semi-solid forming; rapid cooling; metastable austenite; mini-thixoforming
1 Introduction
Thixoforming as a novel forming technology has been known since 1970s. Many working groups around the world have been dealing with the research and following industrial exploitation of low-melted alloys forming in semi-solid state[1-4]. The presented research is focused on the materials with high melting point, specially on steels. With these materials (even altogether commonly used), it is possible not only to simplify the technological procedure of components production, minimize chip machining, but also to obtain products with complex shapes, unconventional structures and physical properties.
Due to the high temperature of material treatment, intensive deformation, rapid solidification and cooling under high pressure, considerable structural changes occur during mini-thixoforming which cannot be attained by conventional material treatment.
Final microstructure after forming in semi-solid state is in contrast to as-cast dendritic microstructure, characterized by the globular and polyedric grains surrounded by the fine lamellar eutectic net. The structure of steels with proper alloying consists of metastable austenite which cannot be developed in conditions of conventional cooling or quenching[5-6]. These structures are attractive particularly by their mechanical and physical properties. The thermal and mechanical stability of developed structures depends on the chemical and energetic state of exploited material. The degree of stability under the different conditions of thermal and mechanical loading will predestinate their possible practical application.
The development of a technology for production of very small demonstrators from steels by thixoforming and particularly the stability of developed metastable structures are the main objects of this research.
2 Experimental equipment and methods
For production of small components in semi-solid state by so-called mini-thixoforming from steels, it was necessary to develop not only the suitable technology but also the needed experimental equipment. The rapid heating of semiproducts and manipulation with material in semi-solid state represent the basic problems. Material heating to the semi-solid state must be carried out with the high accuracy in order to provide required temperature field in the heated semiproduct.
After the analysis of possible variants of material treatment and experimental definition of key parameters, the equipment applying the principle of cross extrusion was designed (Fig.1).
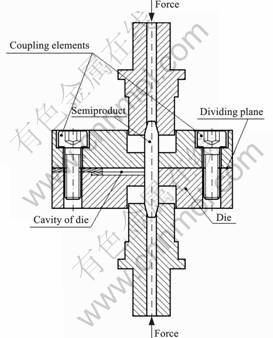
Fig.1 Schematic of cross-extrusion eqipment
For material heating, the unique system of heating was developed[7]. This system of semiproduct heating enables a very accurate regulation of semiproduct temperatures in the wide range. The designed heating method can be also used for the technological variants of material heating directly in a die cavity. In this case, the complicated manipulation with material in semi-solid state is not needed.
The main body of a die is produced from a titanium alloy best satisfying requirements for the developed technology, including particularly non-magnetic properties, corrosion resistance, sufficient toughness, low density, etc. Deformation and heating are performed through copper electrodes. The movement of electrodes is assured by a hydraulic driver. The final product shape depends on a die cavity with changeable shape insert.
Characteristic dimensions with the length of 20 mm and the thickness of several millimeters are achieved. If necessary, it is possible to work in inert atmosphere.
The obtained demonstrators were analyzed by microscopic methods. The austenite proportion in the structure was determined by X-ray phase analysis and mechanical properties were established by hardness test.
3 FEM simulation of die heating
For determination of the heat balance and thermal exposition of a die during the semiproduct heating to the temperature between solidus and liquidus, FEM simulation was performed. The heat transfer between the heated semiproduct and the die cavity was considered by mechanisms of natural convection in an argon cavity and radiation. The temperature of the heated semiproduct was supposed to be 1 350 ?C and the emissivity of the sample and the die e =0.9. The influence of the thickness of the gap between the heated semiproduct and the die on the maximum die temperature was investigated for the semiproducts with the diameter from 3 mm to 8 mm considering the gap thickness from 0.1 mm to 0.8 mm.
Fig.2 illustrates the time history of the maximum die temperature for the semiproduct with 5 mm in diameter and different gap thicknesses. The increase of the gap thickness from 0.1 mm to 0.2 mm leads to the considerable drop of the surface die temperature. The effect of the further gap enlargement on the maximum die temperatures is not so significant. The maximum die temperatures are plotted vs diameter for chosen gap thicknesses after the thermal exposition time of 120 (Fig.3). The die temperatures enhance with increasing semiproduct diameter and reducing gap thickness. Based on the results of numerical simulation, the gap thickness was designed to be at least 0.25 mm.
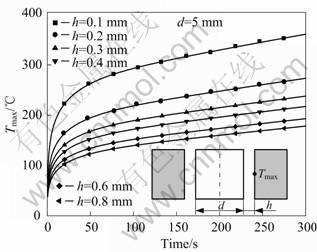
Fig.2 Influence of gap thickness between heated semiproduct (d =5 mm) and die on maximum die temperature
4 Experimental program 4.1 Material of semiproduct
As an experimental material, X210Cr12 steel was chosen (Table.1). It is the steel of ledeburite type with a high content of chromium dedicated for tools used in forming. It is characterized by its difficult formability and machinability by conventional technologies.
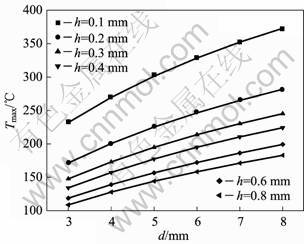
Fig.3 Dependence of maximum die temperature after thermal exposition time of 120 s on semiproduct diameter and gap thickness
Table 1 Chemical composition of X210Cr12 steel (mass fraction, %)

Thanks to the high content of carbon and chromium, this material is distinguished by a wide temperature range between solidus and liquidus, making it suitable for the processing in semi-solid state[8]. The initial material for experiment was in as-formed annealed state (Fig.4).
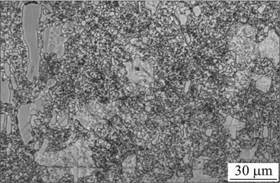
Fig.4 Microstructure of X210Cr12 steel in initial state
4.2 Mini-thixoforming
In initial experimental forming in semi-solid state, the die cavity with the shape of elongated groove with rectangular cross-section was chosen (Fig.5). The experiment with simple-shaped demonstrator enables to understand some principal phenomena and processes occurring during the forming and rapid solidification. The process parameters were successively optimized on these demonstrators, particularly heating conditions and applied deformation load. To fill the die cavity completely, it is necessary to heat the material at least to the temperature of 1 290 ?C. At this temperature the volume fraction of liquid phase in material is 40%.
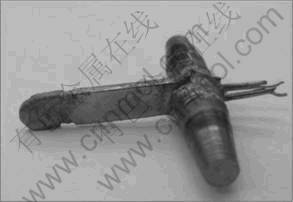
Fig.5 Example of demonstrator in initial stage of mini thixo-forming development with incomplete filling of die cavity
In the next procedures, the shape of the die cavity was modified to the form of an arm with circular ending (Fig.6). After the process optimization, complex-shaped semiproducts were obtained.
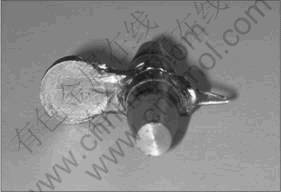
Fig.6 Demonstrator with circular arm
4.3 Microstructure obtained after mini-thixoforming
Metallographic analysis revealed that the structure after thixoforming consisted of polyedric grains of austenite surrounded by fine carbide mesh (Fig.7). By repeated X-ray diffraction phase analyses, the fraction of austenite in structure was found to be 96%.
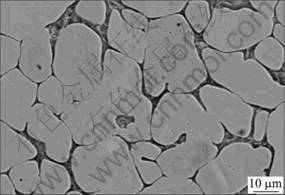
Fig.7 Structure of X210Cr12 steel after thixoforming
The fraction of ferrite and carbides reached 4%. The development of microstructure with such a high fraction of austenite resulted not only from the contribution of chemical composition but also from high heating temperature, rapid solidification, rapid cooling and structure development under high applied pressure.
The structure of obtained semiproduct was homogenous. Only near the contact surface with the die, a thin layer formed by fine dendrites was developed due to the melt segregation and rapid solidification.
4.4 Stability of metastable austenite
For evaluation of stability of metastable austenite, experimental samples were subjected to the thermal and mechanical loading (Table 2).
Table 2 Strategies of heat treatment with final fraction of single phases

The initial assumption of austenite decomposition at 200 ?C was not confirmed. After 1 h holding at this temperature, no structural changes were identified by metallography. X-ray diffraction analysis affirmed the retention of initial content of metastable austenite. A slight increase in hardness can be assigned to the precipitation of secondary carbides in the network surrounding austenite.
Based on this result, further experiments were suggested, namely in the temperature range from the temperature of liquid nitrogen up to 600 ?C[11]. The increase of tempering temperature to 350 ?C for 1 h did not cause any visible changes of microstructure and the percentage of metastable austenite remained approximately the same. Only the growth of hardness value to 461 (HV10) was recorded, which means more than 20 % increase in comparison with the hardness after tempering at 200 ?C. In this case, the increase in hardness can be attached with the precipitation of secondary carbides.
The first visible changes of microstructure were observable at the temperature of 500 ?C (Fig. 8(a)). The growth of fine troostit occurred at grain boundaries. As the amount of troostit was small, the portion of metastable austenite remained almost 90 %. The hardness was not markedly changed in comparison with its value after exposition at previous temperature.
During the exposition at 550 ?C, the troostit development was more expressive. The nucleation of troostit rosettes occurred at the boundaries of polyedric austenitic grains. In the light central areas, the micro- hardness at the level of 790 (HV0.05) was measured, predicting the presence of martensite (Fig.8(b)). The decomposition of metastable austenite in the structure was confirmed by the results of X-ray analysis according to which only 5% of austenite was determined. The austenite decomposition was probably caused by the changes of carbon content. During the thermal exposition, carbon diffused to the grain boundaries and contributed to troostit development. After further increasing temperature to 600 ?C, the total decomposition of metastable austenite occurred during the heating and subsequent 1 h holding (Fig.8(c)). In this case, the hardness drops to the value of 597 (HV10).
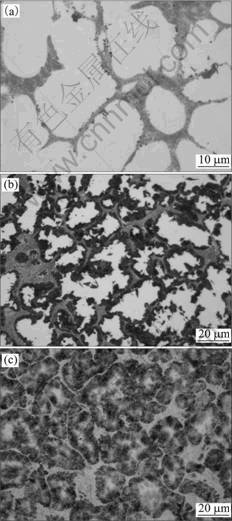
Fig.8 Microstructures of thixoformed X210Cr12 steel subjected to annealing at different temperatures for 1 h: (a) 500 ?C; (b) 550 ?C; (c) 600 ?C
To test austenite stability at cryogenic temperatures, the liquid nitrogen was used as a cooling medium. Metallographic observations after this treatment revealed martensitic needles in austenitic grains (Fig.9). The temperature did not decrease significantly below the Ms temperature due to the high carbon content. Consequently, almost 90 % of metastable austenite remained in the structure. At cryogenic temperature, the precipitation of secondary carbides in network did not occur. This fact along with a high content of metastable austenite can explain relatively low final hardness.
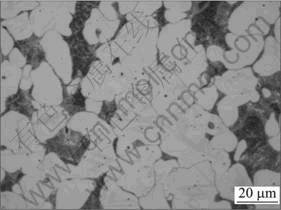
Fig.9 Morphology of martensite after treatment in liquidnitrogen
The stability of metastable austenite against plastic deformation was investigated at the room temperature. The deformation near the ultimate strength of material was applied. No changes in microstructure were noticeable using metallographic observations. By X-ray diffraction analysis, the decrease in percentage of metastable austenite to 85% was detected. It can be supposed that it was caused by deformation induced martensitic transformation. The phase transformation and deformation hardening are probably the reasons of hardness increase to the 421 (HV10). This value is 89 (HV10) higher in comparison with material hardness in the initial state after thixotropic processing.
5 Conclusions
1) Very small parts with different final shapes can be produced from conventional X210Cr12 steel by semi-solid forming process.
2) Thixoforming was performed in titanium die cavity. The shapes of demonstrator were varied. Very fine but otherwise typical thixoforming microstructures were obtained as a result of the combination of rapid solidification, deformation and suitable chemical composition of steel. The microstructure was composed of polyedric metastable austenitic grains surrounded by ledeburite network. Austenite fraction was over 95 % and the hardness reached 332 (HV10).
3) A high stability of austenite up to 500 ?C was observed. During the heating at temperatures above 500 ?C and subsequent cooling to room temperature, metastable austenite decomposed and a special structure occurred which possessed high hardness of 757 (HV10) in contrast to the initial state after thixoforming with the hardness of 332 (HV10).
4) After thermal expositions above 500 ?C, the final microstructure depended strongly on the level of heating temperature. After expositions at about 550 ?C, the microstructure consisted of martensite matrix, troostit formed along original austenite grain boundaries and carbides network. An increase of exposition temperature to 600 ?C resulted in intensive diffusion process of austenite decomposition.
5) Martensite transformation temperature was reached during expositions at cryogenic temperatures and therefore martensite needles appeared in austenite.
Acknowledgements
The paper includes results obtained within the project 1M06032 Research Centre of Forming Technology and Slovak and Czech Project SK-CZ-0180-09.
References
[1] P?TTGEN W, BLECK W, HIRT G, SHIMARA H. Thixoforming of steels-A status report [J]. Advanced Engineering Materials, 2007, 9(4): 231-245.
[2] RASSILI A, ROBELET M, FISCHER D. Thixoforming of steels and industrial applications [C]//Proceedings of the 9th ESAFORM Conference. Glasgow, 2006: 819-822.
[3] HIRT G, KOPP R. Thixoforming: Semi-solid metal processing [M]. Weinheim: WILEY-VCH Verlag GmbH & Co. KGaA, 2009.
[4] ERZ H P. Thixocasting-ein gie?verfahren zur near-net-shape- production [J]. 1999, 77(19/17): 613-617.
[5] CEZERD P, SOURMAIL T. Thixoforming of steel: A state of the art from an industrial point of view [C]// HURT G. The 10th International Conference on Semi-Solid Processing of Alloys and Components Aachen, Trans Tech Publications LTD, Zurich, 2008: 25-35.
[6] B?HRIG-POLACZEK A, HIRT G, BLECK G, K?THE F, SHIMAHARA H, PUTTGEN W, AFRATH C. Thixoforming von stahl–ein überblick (thixoforming of steels-An overview) [C]// Proceeding of 22. Aachener Stahlkolloquium, 2007: 89-99.
[7] RONESOVA A, MASEK B Digital generator of phase shift modulation. USA Patent No. 7,480,155 [P]. 2009-01-20.
[8] FRAIPOINT C, LECOMTE-BECKERS J. Alloy characterization to adept steel to thixoforming: study of a high chromium high carbon steel [C]//HIRT G. The 10th International Conference on Semi-Solid Processing of Alloys and Components. Aachen, Trans Tech Publications LTD, Zurich. 2008: 523-527.
[9] JIRKOVA H, AISMAN D, MASEK B. Unconventional structure of X210Cr12 steel obtained by thixoforming [J]. Journal of Alloys and Compounds, 2010, 504(Suppl.1): S500-S503.
[10] HALLSTED B. Use of Calphad thermodynamics to simulate phase formation during semi-solid processing [C]//HIRT G. The 10th International Conference on Semi-Solid Processing of Alloys and Components. Aachen, Trans Tech Publications LTD, Zurich. 2008: 641-646.
[11] DZIALLACH S, P?TTGEN W, BLECK W. Development of adapter heat treatments for steel out of the semi-solid state after thixoforming [J]. Solid State Phenomena, 12008, 141/142/143: 695-700.
(Edited by YANG Bing)
Corresponding author: D. AISMAN; Tel: +420-377638057, E-mail: daisman@vctt.zcu.cz