J. Cent. South Univ. (2016) 23: 2165-2172
DOI: 10.1007/s11771-016-3273-z

Surface adhesive properties of continuous PBO fiber after air-plasma-grafting-epoxy treatment
JIA Cai-xia(贾彩霞)1, WANG Qian(王乾)2, CHEN Ping(陈平)1, 2, PU Yong-wei(蒲永伟)1
1. Liaoning Key Laboratory of Advanced Polymer Matrix Composites Manufacturing Technology,Shenyang Aerospace University, Shenyang 110136, China;
2. State Key Laboratory of Fine Chemicals & School of Chemical Engineering (Dalian University of Technology), Dalian 116024, China
Central South University Press and Springer-Verlag Berlin Heidelberg 2016
Abstract: It was found that air dielectric barrier discharge (DBD) plasma contributed to the grafting of epoxy resin onto continuous PBO fiber surface. This air-plasma-grafting-epoxy method yielded a noticeable enhancement in the interfacial adhesion between PBO fiber and thermoplastic matrix resin, with the interlaminar shear strength of the resulting composites increased by 66.7%. DSC and FTIR analyses were then used to study the curing behavior of epoxy coating on PBO fiber surface, deduce the possible grafting reactions and investigate the grafting mechanism. More importantly, TGA measurement showed that the grafting of epoxy onto PBO fiber had almost no effect on the composite heat resistance, and there was more thermoplastic matrix resin adhering to the fiber surface; the latter could also be clearly found in the SEM photos. Thereby, the air-plasma-grafting-epoxy treatment was proved to be an effective method for the improvement of continuous PBO fiber surface adhesive properties.
Key words: plasma grafting; continuous PBO fiber; surface adhesive properties; heat resistance
1 Introduction
As a kind of rigid-rod isotropic crystal polymer, poly(p-phenylene benzobisoxazole) (PBO) fiber can be used as reinforcements in high-performance composites in the fields of space and aviation applications, military, industry and other advanced domains [1-2]. The chemical structure of PBO fiber contains the aromatic hetero-cyclic rings, which provides the fiber with superior mechanical properties and excellent thermal resistance under a wide range of conditions [3].However, at the same time, owing to its surface smoothness and the lack of polar functional groups in its polymer repeat units, the bonding between PBO fiber and the matrix resin can not be formed effectively. Efficient stress transfer from the matrix material to the fiber is less than desirable and the applications of PBO fiber in the field of fiber/resin composites are then greatly limited [4]. Thereby, surface modification of PBO fiber is necessary, and a variety of methods have been proposed.
In recent years, plasma technique is widely applied for fiber surface treatment because it can achieve effective results without impacting the bulk properties of the fiber [5]. Notably, more attention has been paid to air dielectric barrier discharge (DBD) plasma due to the advantage of this technique which can work under atmospheric pressure without the need of expensive vacuum equipment and therefore permits the on-line processing for surface treatment of continuous fibers [6-7]. However, the disadvantage of this technique is the aging effect of the modifications on material surface. It is known that grafting technique is a traditional surface treatment method because the grafting agent could react with the fiber and then form stable chemical bonds [8]. Hence, the method combining grafting agent with plasma treatment should improve fiber surface properties effectively and, importantly, avoid the aging effects.
In this work, bisphenol A diglycidyl ether (DGEBA) type epoxy was chosen as the grafting agent and air DBD plasma was the grafting technique. This air-plasma- grafting-epoxy treatment was used to bring continuous PBO fiber better surface adhesive properties and the mechanism of DGEBA grafting onto PBO fiber surface was then investigated, which has been rarely mentioned in the literature. Effects of the air-plasma-grafting-epoxy treatment on surface adhesive properties of PBO fiber were studied by changes in interlaminar shear strength (ILSS) of PBO fiber reinforced thermoplastic poly (phthalazinone ether sulfone ketone) (PBO/PPESK) composites. Differential scanning calorimetry (DSC) was used to show the curing behavior of DGEBA coating on PBO fiber surface and then the possible chemical reactions occurring between DGEBA and PBO fiber were deduced. Fourier transform infrared spectroscopy (FTIR) confirmed that DGEBA was finally grafted onto PBO fiber surface and verified the grafting reactions. In addition, thermogravimetric analysis (TGA) measurement was used to investigate the heat resistance changes of the resulting PBO/PPESK composites. And the state of PPESK resin adhering to PBO fiber surface could be clearly observed in the scanning electron microscopy (SEM) photos.
2 Experimental
2.1 Materials
Continuous poly(p-phenylene benzobisoxazole) (PBO) fiber produced by Toyobo Co. Ltd., Japan (HM, tradename ZylonTM) was used in this work. Its tensile strength, stiffness, relatively low density and filament diameter were 5.8 GPa, 270 GPa, 1.56 g/cm3, and around 12 μm, respectively.
Commercially available bisphenol A diglycidyl ether (DGEBA) type epoxy resin, with an epoxy equivalent of about 192, was supplied by Dalian Qihua Chemical Co. Ltd., China. It is a kind of liquid epoxy resin at room temperature and has better solubility which can be dissolved in some usual solvents such as acetone, methylbenzene, cyclohexanone and glycol.
Poly (phthalazinone ether sulfone ketone) (PPESK) is a novel thermoplastic resin (characteristic viscosity, 0.48) which was received from Dalian Polymer New Material Co. Ltd., China. This resin shows superior mechanical strength as well as excellent thermal stability, and meanwhile possesses better solubility in some usual solvents such as N,N-dimethylacetamide (DMAc), N-methyl-2-pyrrolidone (NMP) and chloroform.
2.2 Air DBD plasma set-up
A stainless hollow cylinder was used as the chamber for the air DBD plasma treatment of PBO fiber, which permitted the on-line processing for surface modification of continuous fibers [9]. Two identical circular stainless electrodes (diameter, 4.7 cm) were placed within the cylinder enclosure, both covered with a quartz plate (thickness, 1 mm) as the barrier. The lower electrode was connected to a plasma generator which provided a high AC voltage (output frequency, 27 kHz) continuously, and the upper electrode to earth. The discharge gap was set at 3 mm. When proper voltage was applied in this work, the plasma discharge power density could reach 41.4 W/cm3 and a large amount of filamentary dielectric barrier discharge generated between the two electrodes [10]. Continuous PBO fiber was treated by means of going through the DBD plasma region at a constant controlled speed of 2.6 cm/s, ensuring that the fiber surface was treated for 10 s [11]. During this process, the treatment system was always exposed to atmosphere through the air hole of the DBD apparatus.
2.3 Sample preparation
During the manufacture processing of PBO fiber, “oily” finish component was always coated on the fiber in the last step. The finish could strongly decrease the surface energy of PBO fiber, weaken the interface between fiber and matrix by forming a weak boundary layer [12]. PBO fiber was therefore washed by using acetone in our study prior to the subsequent grafting and plasma treatments.
For the preparations of grafting solution and resin solution, DGEBA and PPESK resin were dissolved in acetone and DMAc solvent, respectively, forming DGEBA/acetone solution with concentration varying from 0.7% to 5% (mass fraction) and PPESK/DMAc solution with concentration of about 15% (mass fraction). Based on the priority of the treatments carried out on PBO fiber surface, there were seven composite specimens prepared in this work. Both the sample codes and their treatment conditions are described in Table 1. Note that all the PBO fiber filled PPESK composites with and without grafting epoxy treatment were prepared by wet winding technology and then compression molding technology. The chemical structures of PBO fiber, DGEBA grafting agent and PPESK resin are shown in Fig. 1.
2.4 Characterization
Interlaminar shear strength (ILSS) of PBO fiber reinforced PPESK composites was tested to characterize PBO fiber surface adhesive properties. It was measured using short-beam shear testing via Shimadzu universal testing machine according to ASTM D 2344 with a constant cross head speed of 2 mm/min and a span to thickness ratio of 5. The tests were carried out at 20 °C and 50% relative humidity. The dimensions of all samples were set at 25 mm×6 mm×2 mm. The ILSS can be calculated by
(1)
where τ is the ILSS in MPa; Pb is the maximum load in Newton; b and h are the width and the thickness of the composite specimen in mm, respectively. Each ILSS value reported was the average value of five measurements.
Table 1 Codes of PBO/PPESK samples and descriptions for treatment conditions
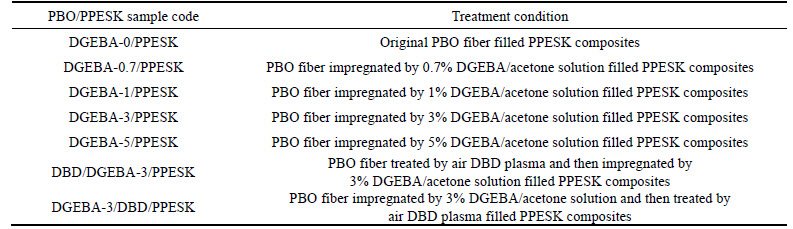
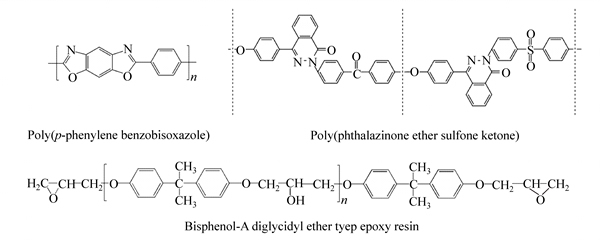
Fig. 1 Chemical structures of PBO fiber, DGEBA grafting agent and PPESK resin
Differential scanning calorimetry (DSC) measurements were conducted with an NETZSCH DSC 204 instrument. The calorimeter was calibrated with indium metal (99.99% purity) as a standard. 5-7 mg samples were used at a linear heating rate of 10 °C/min to 350 °C under a purified nitrogen gas (~99.99%) flow rate of 20 mL/min.
Fourier transform infrared spectroscope (FTIR; NEXUS EVRO, Nicolet) coupled with the attenuated total reflectance (ATR) attachment was also performed to detect the chemical bond changes of PBO fiber surface before and after the air-plasma-grafting-epoxy treatment. FTIR scans were performed in reflectance mode, applying a wavenumber range of 3000-680 cm-1 with the wavenumber resolution 2 cm-1, and the average result of 32 automatic scans was output as the test result.
A PerkinElmer TGA-7 thermal analyzer was used to obtain thermogravimetric analysis (TGA) measurements. All samples (~3 mg) were heated at a linear heating rate of 10 °C/min to 700 °C under a purified nitrogen gas (~99.99%) flow rate of 60 mL/min.
Scanning electron microscope (SEM; QUANTA 200, FEI) was selected to observe the state of PPESK resin adhering to PBO fiber surface. The pressure of the chamber for SEM measurement was less than 60 Pa and the accelerating voltage was 25 kV. The magnification was set at 1000×.
3 Results and discussion
3.1 Surface adhesive properties of PBO fiber after air-plasma-grafting-epoxy treatment
Interlaminar shear strength (ILSS) can be used to evaluate the interfacial adhesion of fibrous composites and reflect the fiber surface adhesive properties. Table 2 lists the ILSS values of PBO fiber reinforced PPESK composite samples. For the original PBO fiber reinforced PPESK composites, the DGEBA-0/PPESK sample exhibited a low ILSS of 33.24 MPa. After impregnating the epoxy grafting agent, all ILSS values were higher than those of the untreated one, increasing from 37.60 MPa to 48.77 MPa with the concentration of DGEBA/acetone solution varying from 0.7% to 3%. However, when the concentration of grafting solution increased to 5%, the ILSS of the DGEBA-5/PPESK sample showed an obvious decline to 40.78 MPa, though it was still larger than that of the untreated sample. It could be found from the above results that concentrations of the epoxy grafting solution had a great effect on the interface performance of continuous PBO fiber filled PPESK composites, and the DGEBA/acetone solution with concentration of 3% might have a better grafting effect. Therefore, the concentration of the DGEBA/ acetone solution used for air-plasma-grafting-epoxy method was set to be 3%.
Table 2 ILSS of composites before and after fiber treatment by air-plasma-grafting-epoxy method
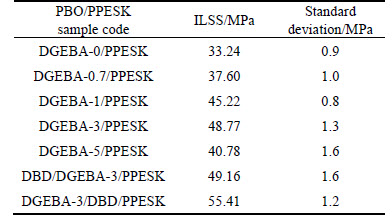
For PBO fiber treated by air DBD plasma and then impregnated by 3% DGEBA/acetone solution filled PPESK composites, the ILSS value of the DBD/ DGEBA-3/PPESK sample had hardly changed when compared to that of the DGEBA-3/PPESK sample. However, for PBO fiber impregnated by 3% DGEBA/ acetone solution and then treated by air DBD plasma filled PPESK composites, the ILSS of the DGEBA-3/ DBD/PPESK sample reached the maximum value of 55.41 MPa in this study, with the increments of 12.7% and 66.7% compared with the DBD/DGEBA-3/PPESK and DGEBA-0/PPESK samples, respectively. These results showed that carrying out air DBD modification after impregnating epoxy grafting agent proved high effect in the air-plasma-grafting-epoxy method, which could largely improve the surface adhesive properties of PBO fiber and enhance the interfacial adhesion of PBO/PPESK composites. The improving mechanism was analyzed in following sections.
3.2 Possible reactions between PBO fiber surface and epoxy grafting agent
Differential scanning calorimetry (DSC) is an important thermal analysis technique which can be used in investigating curing behavior of thermosetting resin. In this work, the DSC traces of three PBO fiber samples including DGEBA-3 (PBO fiber impregnated by 3% DGEBA/acetone solution), DBD/DGEBA-3 and DGEBA-3/DBD were obtained, as shown in Fig. 2, in order to study the curing behavior of DGEBA coating on PBO fiber surface and explain the remarkable improvement in ILSS of the DGEBA-3/DBD/PPESK sample.
There was only one exothermic transition associated with the curing of epoxy in the curve of DGEBA-3 sample; we all knew that this behavior arises from the thermosetting curing of epoxy resin. The situation was much the same for the fiber sample treated by air DBD plasma and then impregnated by 3% DGEBA/ acetone solution (DBD/DGEBA-3). The difference was that the main exothermic peaks for the above two samples appearing at 343 and 336 °C, respectively, indicating that impregnating epoxy grafting agent after the air DBD treatment changed little the subsequent curing behavior of DGEBA coating on PBO fiber surface except for making its thermosetting curing occur at a relatively low temperature. However, for the fiber sample impregnated by 3% DGEBA/acetone solution and then treated by the air DBD plasma (DGEBA-3/ DBD), another exothermic peak appeared on the moderate temperature side at about 221 °C, and the exothermic transition associated with curing of epoxy further shifted to a lower temperature (about 325 °C), indicating that some chemical reactions in the DGEBA-3/DBD fiber sample occurred after the plasma treatment and meanwhile the thermosetting curing of DGEBA coating on PBO fiber surface could take place more easily.
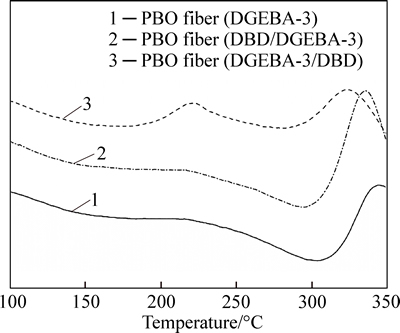
Fig. 2 DSC traces of PBO fiber before and after air-plasma- grafting-epoxy treatment
Plasma, which consists of charged and neutral species, including electrons, positive ions, negative ions, radicals, etc, is commonly called as the fourth state of matter. In a plasma, the average electron energy ranges between 1 and 10 eV, which could possibly introduce some types of chemical modifications on the fiber surface and then initiate some reactions, including polymerization or grafting [13]. For example, hydroxyl and/or carboxyl radicals might be introduced to position 2 of benzene ring in PBO molecular, forming 1,2,4-substituted benzene via substitution reaction [14] because of the bombardment of the active particles existing in the air DBD plasma. However, the radicals would annihilate during impregnating the DGEBA/ acetone solution. Therefore, the DSC and the ILSS results showed only a little change when comparing DBD/ DGEBA-3 to DGEBA-3 fiber sample.
For DGEBA-3/DBD, the plasma could introduce radicals to the DGEBA molecules coating on PBO fiber surface as well, and then graft polymerization would take place between the radicals produced on the fiber surface and in the DGEBA molecules, as illustrated in Fig. 3. The exothermic transition at about 221 °C was just caused by these radical reactions which could lead to the grafting of epoxy resin onto PBO fiber and improve the fiber surface adhesive properties. These changes were in good agreement with the results derived by ILSS measurement, showing that impregnating PBO fiber with epoxy grafting agent before carrying out air DBD plasma treatment was an effective way for the air-plasma- grafting-epoxy method.
3.3 Air-plasma-grafting-epoxy treatment studied by FTIR
Then, Fourier transform infrared spectroscopy (FTIR) in wavenumber range from 3000 to 680 cm-1 was recorded to investigate changes in surface groups of the fiber sample DGEBA-3/DBD, as shown in Fig. 4. The absorbent peak at about 700 cm-1 was used as an internal reference. In comparison with the curve of DGEBA-0 which was the fiber sample without DBD or grafting treatment, both the FTIR spectra of DGEBA-3/DBD and DGEBA-3/DBD/extraction (this fiber sample was prepared by extracting DGEBA-3/DBD with acetone, used for proving the grafting reaction occurring between PBO fiber and DGEBA) showed several remarkable differences.
After the air-plasma-grafting-epoxy treatment, new absorption band at 2960 cm-1 appeared in the FTIR spectra of both DGEBA-3/DBD and DGEBA-3/DBD/ extraction samples, which was associated with the methyl group in DGEBA [15]. At the same time, the intensity of absorbent peak at 913 cm-1, the infrared absorption characteristic peaks of DGEBA [16], increased obviously for the two samples. Moreover, it could be found that the infrared absorption characteristic peaks of benzene ring at 1610, 1580, 1510 and 1450 cm-1, as well as C—O—C group at 1248, 1185 and 1040 cm-1 enhanced evidently [17].
For the DGEBA-3/DBD/extraction sample, the DGEBA un-grafted onto PBO fiber was removed from PBO fiber surface after the extraction by acetone, so the intensities of absorbent peak in relation to DGEBA clearly decreased compared with the DGEBA-3/DBD sample. This result could provide strong evidence that part of DGEBA coating on PBO fiber had been grafted onto the fiber surface after the air DBD plasma treatment.
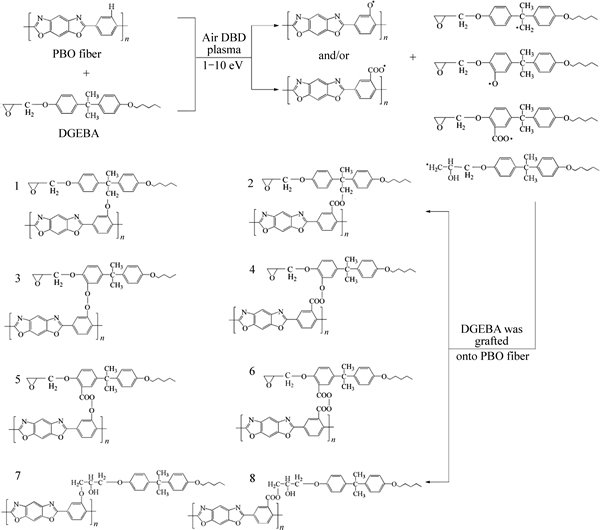
Fig. 3 Possible reactions occurring between PBO fiber and DGEBA grafting agent
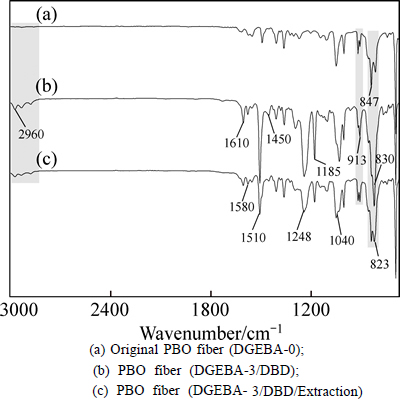
Fig. 4 FTIR spectra of PBO fiber before and after air-plasma- grafting-epoxy treatment:
Especially, for the DGEBA-3/DBD sample, there was one strong infrared absorption characteristic peak appearing at about 830 cm-1 after the air-plasma- grafting-epoxy treatment [18]. After the extraction, however, two absorption peaks at 847 and 823 cm-1 appeared respectively. By comparing the curve of DGEBA-3/DBD/extraction with that of DGEBA-0, the absorption peak at 847 cm-1 associated with benzobisoxazole structure of PBO [19] appeared clearly and the intensity of absorption peak at 823 cm-1 associated with substituted benzene [20] was greatly increased, which just arose from the 1,2,4-substituted benzene formed in the plasma grafting processing. Therefore, the radical reactions shown in Fig. 3 were reasonable.
3.4 Influence of air-plasma-grafting-epoxy treatment on composite heat resistance and interfacial adhesion
In order to investigate whether the grafting of epoxy onto PBO fiber surface affected the heat resistance of PBO/PPESK composites, thermogravimetric analysis (TGA) was used in this study. From Fig. 5(a), some changes in heat resistance of the fibrous composites before and after the air-plasma-grafting-epoxy treatment could be obtained, in terms of onset decomposition temperature (T5%) and char yield at 600 °C.
From an inspection of the TGA thermograms, the T5% values for the DGEBA-0/PPESK and the DGEBA-3/ DBD/PPESK samples were 509 and 506 °C, respectively, namely, there was almost no effect on the heat resistance of PBO fiber filled PPESK composites after the grafting epoxy treatment by the air DBD plasma. It’s important to note that the char yield at 600 °C, after the air-plasma- grafting-epoxy treatment, showed a decrease of about 2.3%, demonstrating that more PPESK resin was existing in the fiber/resin composite sample. As listed in Table 3, the residual rates of DGEBA-0/PPESK and DGEBA-3/ DBD/PPESK composites were 83.4% and 81.1% in mass fraction, respectively. Because the degradation of PBO fiber started just after 600 °C in nitrogen gas, as shown in Fig. 5(b), we can consider the mass loss at this temperature as the decomposition of PPESK resin (the amount of DGEBA was too small to be considered). Then the amounts of decomposed resin for DGEBA- 0/PPESK and DGEBA-3/DBD/PPESK composites should be 16.6% and 18.9%, respectively. And because the decomposition rate of PPESK resin at 600 °C was 36.7%, we could get that the amounts of resin coating on PBO fibers in DGEBA-0/PPESK and DGEBA-3/DBD/ PPESK composites were about 45.2% and 51.5%, respectively.
From SEM photos in Fig. 6, it can be easily find that there was a large amount of PPESK resin appearing on/among the fiber filaments and the interfacial adhesion properties between PBO fiber and PPESK resin was improved to some extent, which thereby brought the DGEBA-3/DBD/PPESK sample the high ILSS value.
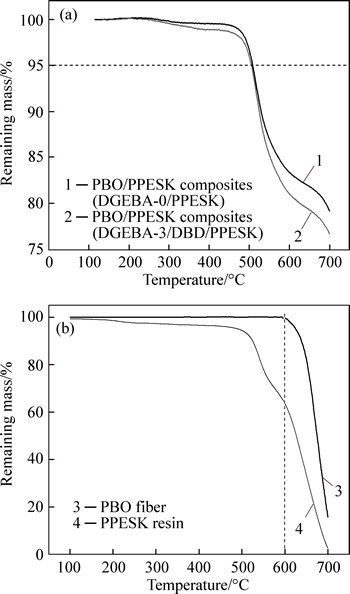
Fig. 5 TGA curves of PBO/PPESK composites (a), and PBO fiber and PPESK resin (b)
Table 3 Amounts of residues for PBO/PPESK composites, PBO fiber and PPESK resin at 600 °C
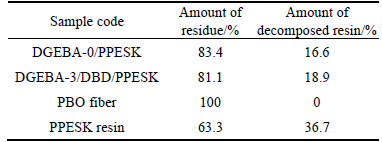
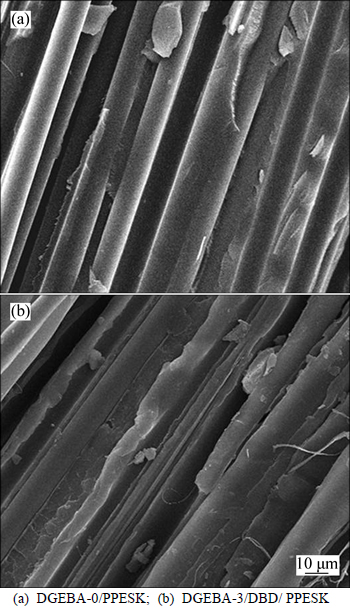
Fig. 6 SEM photos of PBO/PPESK composites before and after grafting epoxy:
4 Conclusions
Air dielectric barrier discharge (DBD) plasma contributes to the grafting of epoxy (DGEBA) onto PBO fiber surface. ILSS measurements indicate that the interface performance of PBO fiber filled PPESK composites could be improved by the air-plasma- grafting-epoxy treatment. DSC measurements show a new exothermic peak appearing in the curve of DGEBA-3/DBD fiber sample and the exothermic transition associated with thermosetting curing of epoxy shifts to a lower temperature, indicating that some chemical reactions occur between PBO fiber surface and the DGEBA grafting agent. Then, the infrared absorption characteristic peaks in FTIR spectra show some obvious changes for the sample DGEBA- 3/DBD, providing strong evidence that the DGEBA has been grafted onto PBO fiber surface by the air DBD plasma and confirming the radical reactions deduced by DSC. Finally, TGA proves that the grafting of epoxy onto PBO fiber has almost no effect on heat resistance of the resulting composites and together with SEM show that there are more PPESK resins adhering to the treated PBO fiber surface. Therefore, the air-plasma-grafting- epoxy treatment is proved to be a suitable method for improving continuous PBO fiber surface adhesive properties.
References
[1] ZHANG Tao, HU Da-yong, JIN Jun-hong, YANG Sheng-lin, LI Guang, JIANG Jian-ming. XPS study of PBO fiber surface modified by incorporation of hydroxyl polar groups in main chains [J]. Applied Surface Science, 2010, 256: 2073-2075.
[2] KITAGAWA T, YABUKI K, YOUNG R J. An investigation into the relationship between processing, structure and properties for high-modulus PBO fibres. Part 1. Raman band shifts and broadening in tension and compression [J]. Polymer, 2001, 42: 2101-2112.
[3] WU G M, SHYNG Y T. Surface modification and interfacial adhesion of rigid rod PBO fibre by methanesulfonic acid treatment [J]. Composites Part A, 2004, 35: 1291-1300.
[4]
E, MELCHER S, LIU J W, GAO S L, BIANCHI A D, ZHERLITSYN S, WOSNITZA J. Adhesion of PBO fiber in epoxy composites [J]. Journal of Material Science, 2007, 42: 8047-8052.
[5] LI R Z, YE L, MAI Y W. Application of plasma technologies in fibre-reinforced polymer composites: A review of recent developments [J]. Composites Part A, 1997, 28A: 73-86.
[6] BORCIA G, DUMITRASCU N, POPA G. Influence of helium- dielectric barrier discharge treatments on the adhesion properties of polyamide-6 surfaces [J]. Surface and Coatings Technology, 2005, 197: 316-321.
[7] LIU C Z, BROWN N M D, MEENAN B J. Statistical analysis of the effect of dielectric barrier discharge (DBD) operating parameters on the surface processing of poly(methylmethacrylate) film [J]. Surface Science, 2005, 575: 273-286.
[8] CHEN Lei, WEI Feng, LIU Li, CHENG Wei-lu, HU Zhen, WU Guang-shun, DU Yun-zhe, ZHANG Chun-hua, HUANG Yu-dong. Grafting of silane and graphene oxide onto PBO fibers: Multifunctional interphase for fiber/polymer matrix composites with simultaneously improved interfacial and atomic oxygen resistant properties [J]. Composites Science and Technology, 2015, 106: 32-38.
[9] JIA Cai-xia, CHEN Ping, LI Bin, WANG Qian, LU Chun, YU Qi. Effects of Twaron fiber surface treatment by air dielectric barrier discharge plasma on the interfacial adhesion in fiber reinforced composites [J]. Surface and Coatings Technology, 2010, 204: 3668-3675.
[10] WANG Qian, CHEN Ping, JIA Cai-xia, CHEN Ming-xin, LI Bin. Improvement of PBO fiber surface and PBO/PPESK composite interface properties with air DBD plasma treatment [J]. Surface and Interface Analysis, 2012, 44: 548-553.
[11] WANG Qian, CHEN Ping, JIA Cai-xia, CHEN Ming-xin, LI Bin. Effects of air dielectric barrier discharge plasma treatment time on surface properties of PBO fiber [J]. Applied Surface Science, 2011, 258: 513-520.
[12]
K, VILLAR-RODIL S, PAREDES J Ι,
M A. Surface characterization of PBO fibers [J]. Macromolecules, 2003, 36: 8662-8672.
[13] SHAMSI M H, LUQMAN M, BASARIR F, KIM J S, YOON T H, GECKELER K E. Plasma-modified halloysite nanocomposites: Effect of plasma modification on the structure and dynamic mechanical properties of halloysite-polystyrene nanocomposites [J]. Polymer International, 2010, 59: 1492-1498.
[14] WANG Jie-liang, LIANG Guo-zheng, ZHAO Wen, ZHANG Zeng-ping. Enzymatic surface modification of PBO fibres [J]. Surface and Coatings Technology, 2007, 201: 4800-4804.
[15] ZHANG W, BLACKBURN R S, DEHGHANI-SANIJ A. Electrical conductivity of epoxy resin-carbon black-silica nanocomposites: Effect of silica concentration and analysis of polymer curing reaction by FTIR [J]. Scripta Materialia, 2007, 57: 949-952.
[16] MEURE S, WU D Y, FURMAN S A. FTIR study of bonding between a thermoplastic healing agent and a mendable epoxy resin [J]. Vibrational Spectroscopy, 2010, 52: 10-15.
[17] WANG Xin, HU Yuan, SONG Lei, XING Wei-yi, LU Hong-dian. Thermal degradation mechanism of flame retarded epoxy resins with a DOPO-substitued organophosphorus oligomer by TG-FTIR and DP-MS [J]. Journal of Analytical and Applied Pyrolysis, 2011, 92: 164-170.
[18]
M A, ALVAREZ R. Evaluation of bituminous wastes as coal fluidity enhancers [J]. Fuel, 2012, 101: 45-52.
[19] WALSH P J, HU X B, CUNNIFF P, LESSER A J. Environmental effects on poly-p-phenylenebenzobisoxazole fibers. II. Attempts at stabilization [J]. Journal of Applied Polymer Science, 2006, 102: 3819-3829.
[20]
M A, ALVAREZ R. Influence of additives of various origins on thermoplastic properties of coal [J]. Fuel, 2009, 88: 2365-2372.
(Edited by YANG Hua)
Foundation item: Project(L2014056) supported by the Liaoning Education Department, China; Project(201501089) supported by the Dr. Start-up Fund of Liaoning Province, China
Received date: 2015-08-27; Accepted date: 2015-10-26
Corresponding author: CHEN Ping, PhD, Professor; Tel: +86-411-84986100; E-mail: chenping__898@126.com