
J. Cent. South Univ. (2018) 25: 534-542
DOI: https://doi.org/10.1007/s11771-018-3758-z

Effect of pre-recovery on subsequent recrystallization kinetics in moderately deformed and supersaturated Al–Mn alloys
HUANG Li(黄利), CAO Ling-fei(曹玲飞), HUANG Guang-jie(黄光杰), WU Xiao-dong(吴晓东), XIA Ming-yong(夏明勇)
College of Materials Science and Engineering, Chongqing University, Chongqing 400044, China
Central South University Press and Springer-Verlag GmbH Germany, part of Springer Nature 2018
Abstract: The effect of pre-recovery on the recrystallization kinetics of a supersaturated Al–Mn alloy annealed at 530 °C was investigated. The results show that the pre-recovery treatment can lead to faster recrystallization kinetics at the initial stage but cause sluggish recrystallization at the later stage. This different recrystallization behavior is explained by the formation of precipitates-free zones and the consumption of driving force during the pre-recovery treatment. The promoted recrystallization at the early stage can be interpreted by the promotion of recrystallization nucleation through sub-grain growth to a critical size inside precipitates-free zones. A simple model is presented to describe the nucleation of recrystallization with pre-recovery treatment in the supersaturated Al–Mn alloys.
Key words: pre-recovery; recrystallization; nucleation and growth; kinetics; precipitation
Cite this article as: HUANG Li, CAO Ling-fei, HUANG Guang-jie, WU Xiao-dong, XIA Ming-yong. Effect of pre-recovery on subsequent recrystallization kinetics in moderately deformed and supersaturated Al–Mn alloys [J]. Journal of Central South University, 2018, 25(3): 534–542. DOI: https://doi.org/10.1007/s11771-018-3758-z.
1 Introduction
In metals of high stacking fault energy (γSFE) such as aluminum and its alloys, significant recovery may occur since climb and cross-slip of dislocations can be readily activated. As recovery occurs, a series of events including dislocations annihilation and rearrangement, sub-grains formation and growth will take place within a small scale [1]. Such a process not only causes a reduction of stored energy by dislocation movement, but also involves microstructure transition, i.e., the formation of sub-grain structure. Therefore, the influence of pre-recovery on recrystallization is two-side. On one side, pre-recovery can reduce the stored energy which is subsequently available for nucleation and growth of the recrystallized grains, hence it retards recrystallization [2, 3]. On the other side, pre-recovery also occurs in the form of sub- grain growth or sub-grain coalescence and can act as nuclei of recrystallization, regardless of driving force [4–6]. In light of this fact, it is expected that pre-recovery could stimulate the nucleation of recrystallization under certain circumstances.
Although there are some studies in which low temperature pre-recovery treatment either have an effect of enhancing or reducing the recrystallization rate in precipitate-free aluminum alloys [3, 4, 7], detailed investigations of recovery, recrystallization and microstructural evolution in the presence of fine precipitates are rare. In particles-containing alloys, precipitation can strongly influence the recrystallization behavior [8–13]. The fine dispersoids precipitated in the course of annealing treatment can hinder or even suppress recrystallization. Thus the recrystallization process is very complicated when precipitation occurs concurrently during the pre-recovery stage. It is therefore of great interest to investigate the effect of pre-recovery on recrystallization behavior during the annealing of the cold-deformed particle- containing alloys.
In the current work, the effect of pre-recovery on recrystallization kinetics was explored in a cold rolled supersaturated Al–Mn alloy. For this purpose, the microstructural evolution (recrystallization and precipitation behavior) and associated theoretical analysis have been conducted to understand the inherent mechanism of recrystallization nucleation and grain growth in the samples with and without pre-recovery treatment.
2 Experimental
Commercial twin roll cast 3003 alloy (Al–1.13Mn–0.45Fe–0.1Si, mass fraction) was used in this work. The as-received sheets with 6.7 mm thickness were cold-rolled to a 28.6% reduction. It should be noted that the sheets were already deformed during casting process so the total deformation (hot and cold) reduction was supposed to be 50%. Then the cold-rolled materials were subjected to two different annealing treatments as schematically illustrated in Figure 1. Figure 1(a) shows a single-step annealing (referred hereafter to as SSA) where the cold-rolled sheets were solely annealed at 530 °C for 15 h in a pre-heated muffle furnace. For comparison, Figure 1(b) shows a two-step annealing (referred to as TSA) to investigate the effect of pre-recovery on recrystallization behavior. TSA included an initial pre-recovery treatment at low temperature(450 °C, 5 h) and a following high temperature recrystallization process (530 °C, 15 h) with a rapid heating rate. All the samples were immediately water-quenched after annealing.
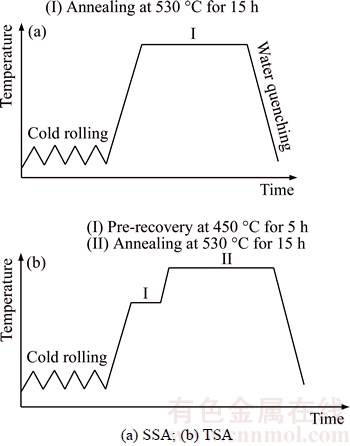
Figure 1 Schematic illustration of thermo-mechanical processing schedules:
The grain structure was revealed by optical micrographs of the cold-rolling and various annealing specimens anodized using Barkers reagent. The softening response was measured by means of Vickers hardness tests and precipitation reaction was monitored by electrical conductivity measurements at room temperature. Hardness measurements were conducted using a 4.9 N applied load and with a dwell time of 15 s, and the average hardness from eight independent measurements was reported. Electrical conductivity was measured by a digital D60K conductivity instrument. Second phase particles (constituent particles and precipitates) were examined by a combination of back-scattered electron (BSE) channeling contrast images in a focused ion beam scanning electron microscopy (FIB/SEM, ZEISS AURIGA) and transmission electron microscopy (TEM) performed by a Zeiss LIBRA 200 under 200 kV. All micrographs presented below were characterized at the quarter of thickness of the planes in the rolling direction (RD) and normal direction (ND) unless otherwise stated.
3 Results and discussion
3.1 Recrystallization kinetics
Hardness measurement was taken to track the softening behavior during the different annealing processes. Generally, hardness decreases slowly during recovery process and drops abruptly as the recrystallization starts [14]. Accordingly, the process of recrystallization is monitored by measurements of Vickers hardness as a function of annealing time, as seen in Figure 2. It can be found that the recrystallization of the cold-rolled Al–Mn sheets starts after 20 min of incubation period at 530 °C during the single-stage annealing (SSA, in Figure 2(a)); while in the case of two-step annealing (TSA, Figure 2(b)), recrystallization initiates immediately after the temperature ramps to 530 °C without any incubation period. Before the onset of recrystallization, the hardness drops slowly from 63.2 to 54.2 and 49.1 for the SSA and TSA samples, respectively, indicating that pre-recovery releases a lot of stored energy. After complete recrystallization, the hardness value reaches a plateau of about 33.5 for both cases. The recrystallization volume fraction (Xv) was estimated from the variation in hardness (H) with annealing time (t) by [15]:
(1)
where Hrv represents the hardness after recovery prior to the onset of recrystallization and Hrx the hardness after complete recrystallization. The values of Hrv and Hrx are obtained from the hardness curves combined with the microstructural observation. Hence, the values of hardness Hrv before the onset of recrystallization are determined to be 54.2 and 49.1 in the SSA and TSA samples, respectively. The value of hardness (Hrx) after complete recrystallization is 33.5 for both SSA and TSA samples.
Recrystallization volume fraction as a function of annealing time is, in general, well expressed by the Johnson-Mehl-Avrami-Kolmogorov (JMAK) model [1]:
(2)
where k is a constant which is a function of the material and the annealing temperature, and the JMAK exponent n depends on the type of nucleation and growth dimension. The data for the Xv can be presented in the form of ln [–ln (1–Xv)] vs ln t.
Figure 3 shows the recrystallization kinetics at 530 °C of the deformed Al–Mn sheets with and without pre-recovery treatment. The recrystallization fraction vs annealing time curves exhibit sigmoidal shape, as seen in Figure 3(a). The specimens with pre-recovery recrystallized much faster than that without pre-recovery at the early stage of recrystallization, while opposite trend was observed at the late stage. This is consistent with hardness measurement in TSA case where the incubation period is hardly observed. The JMAK plots of the SSA and TSA sample are shown in Figure 3(b). The plot of SSA sample is linear with a slope of 1.14; while the plot of TSA sample is linear with a slope of 1.02 at the early stage of recrystallization, and deviate from linear relation at the later stage of recrystallization.
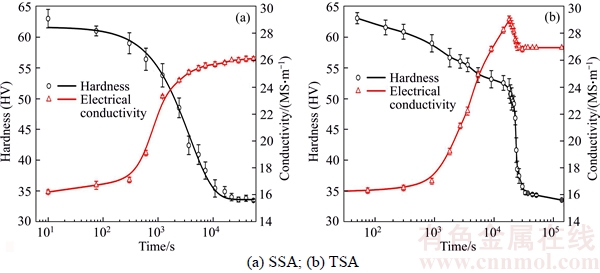
Figure 2 Changes with annealing time in hardness and electrical conductivity of Al–Mn sheets during single- and two-step annealing:
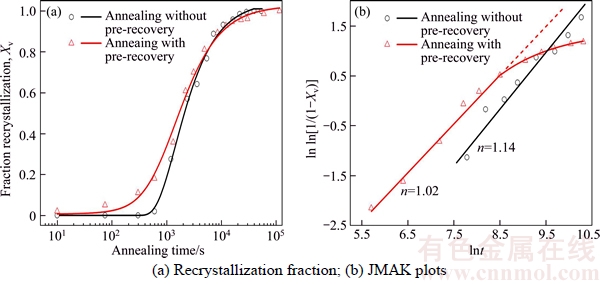
Figure 3 Recrystallization kinetics at 530 °C of cold-rolled Al–Mn alloy with and without pre-recovery treatment:
3.2 Microstructure evolution
3.2.1 Recrystallization behavior
The evolution of the microstructure during SSA and TSA is shown in Figure 4. A typical deformed structure showing elongated grains along the rolling direction is observed after cold rolling (Figure 4(a)). By the single-step annealing at 530 °C for 40 min, where the recrystallization fraction is about 40%, only a few coarse elongated recrystallized grains can be observed (Figure 4(b)). These grains had a growth advantage and invaded promptly into the deformed microstructure. Longer annealing time of 15 h leads to a complete recrystallization state and a very coarse, elongated grains structure along rolling direction (Figure 4(c)). In the TSA case, no obvious microstructure changes can be observed at the low-temperature stage (Figure 4(d)), indicating that only recovery takes place. After the second annealing at 530 °C for 40 min, where the recrystallization fraction is about 48.5%, a large number of small recrystallized grains with equiaxed shape are presented (Figure 4(e)). The grain structure after full recrystallization is different distinctly from that in the SSA case, showing much finer quasi-equiaxed grains (Figure 4(f)). From Figures 4(b) and (e), it can be observed that grain boundaries are the dominant nucleation sites for both the SSA and TSA cases. Unlike the SSA sample, the TSA sample exhibits much higher number density of nuclei, indicating that pre-recovery could result in an enhanced nucleation rate. This promotion of nucleation contributes to the faster recrystallization kinetics in the early stage. Additionally, the recrystallized grains in the TSA sample are much smaller than those in the SSA sample. Grain growth could be significantly impeded in TSA case due to the reduced stored energy and the pinning effect by the fine dispersoids which will be discussed in the following section.
3.2.2 Precipitation behavior
For TRC Al–Mn alloys, an important aspect is that the majority of Mn retains in solid solution due to a rapid solidification [16]. These supersaturated Mn will precipitate as Mn-bearing dispersoids during subsequent annealing, which has a profound influence on the softening reactions [17]. Therefore, it is necessary to examine the precipitation behaviour during the annealing process. The relationship of the electrical conductivity κ (MS/m) and the concentration of the elements in Al–Mn alloys can be described by [18, 19]:

(3)
where C is the mass fraction of the alloying elements in the matrix. According to Eq. (3), the influence of Si and Cu on the conductivity is much less than that of Mn and Fe, thus can be neglected. In addition, most of the Fe precipitates in the form of constituent particles in as-cast 3003 alloy ingots, while the majority of Mn remains in solid solution [19]. Therefore, the electrical conductivity measurements can be used to evaluate the content of Mn in the Al matrix, and thereafter give information on precipitation of Mn-bearing dispersoids. Figure 2 shows the changes of electrical conductivity (red lines) during the SSA and TSA treatments. In light of the evolution in Vickers hardness and electrical conductivity, it is found that the evolution of precipitation during SSA behaves quite differently from that in the TSA process. For the SSA, the change of Mn content in aluminium matrix is about 0.55wt% during recovery, and about 0.17wt% in the concurrent precipitation during recrystallization, as estimated by Eq.(3). However, in the case of TSA, the change of Mn content in aluminium matrix is about 0.82wt% prior to recrystallization as a result of pre-recovery and is about –0.09% during recrystallization, suggesting that Mn-bearing dispersoids precipitate mainly during pre-recovery and then marginally dissolve back into the matrix during recrystallization. After complete recrystallization, the Mn concentration in Al matrix is almost the same level for both SSA and TSA.
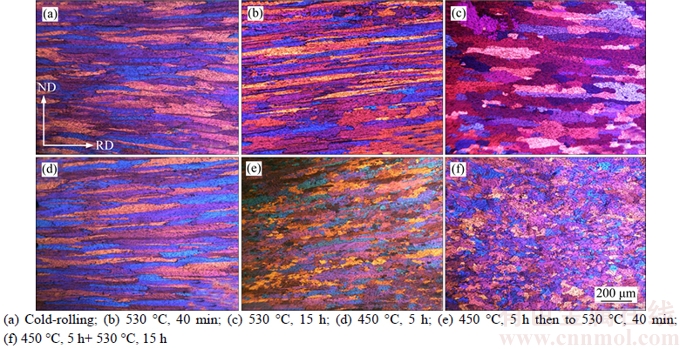
Figure 4 Optical micrographs showing evolution of recrystallization in samples after cold rolling and annealing:
To obtain more information on the precipitation behaviour during SSA and TSA, the distribution of the second-phase particles was examined by TEM on the rolling plane, as displayed in Figure 5. The microstructure exhibited typical deformed structure for all of the moderately cold-rolled alloys. The structure mainly consisted of cells with a size of approximately 0.5–1.0 μm and dislocation tangles on the cell boundaries. No precipitates can be observed in this state (Figure 5(a)). After annealing at 530 °C for 20 min in the SSA case (Figure 5(b)), i.e. the incubation period, the microstructure contains less dislocations and a well-defined sub-grain structure forms. Simultaneously, fine dispersoids are observed on the sub-grain boundaries. These particles are spherical or needle-like in shape. The chemical composition of the selected precipitates derived from EDS (Figures 5(e)–(f)) is summarized in Table 1, from which the particles can be identified to be α-AlFeMnSi and Al6(Fe, Mn), respectively. At the pre-recovery stage of TSA condition (Figure 5(c)), a well-recovered boundary structure forms and the fine particles are clearly observed on the sub-boundaries which is quite similar to that of Figure 5(b). By heating to 530 °C at the second stage (Figure 5(d)), it is clear that sub-grain coarsening occurs and some sub-grains boundary/ front have overcome the pinning effect from precipitated dispersoids,as tagged by the “crossmark 5”, which are left behind the moving sub-grain boundary. It should be noted that before the onset of recrystallization in both cases (Figures 5(b) and (d)),a substantial amount of Mn-bearing dispersoids precipitates from the solid solution which is consistent with the electrical conductivity results.
3.3 Nucleation and growth reactions
The primary purpose of the current investigation is to study the effect of pre-recovery on the subsequent recrystallization kinetics in supersaturated aluminium alloys. In this work, the results show that pre-recovery treatment actually accelerates the rate of recrystallization at the early stage, but reduces it at the later stage. It is well known that recrystallization kinetics is a function of nucleation and growth rates [2]. How the pre-recovery affects the nucleation and growth reactions which in turn affects the recrystallization kinetics, will be discussed below separately.
As mentioned above, lots of stored energy is consumed and much more precipitates are formed during pre-recovery process of the two-step annealing. The release of stored energy leads to a lower driving force for growth (PD), while precipitates result in a Zener pinning pressure (PZ).
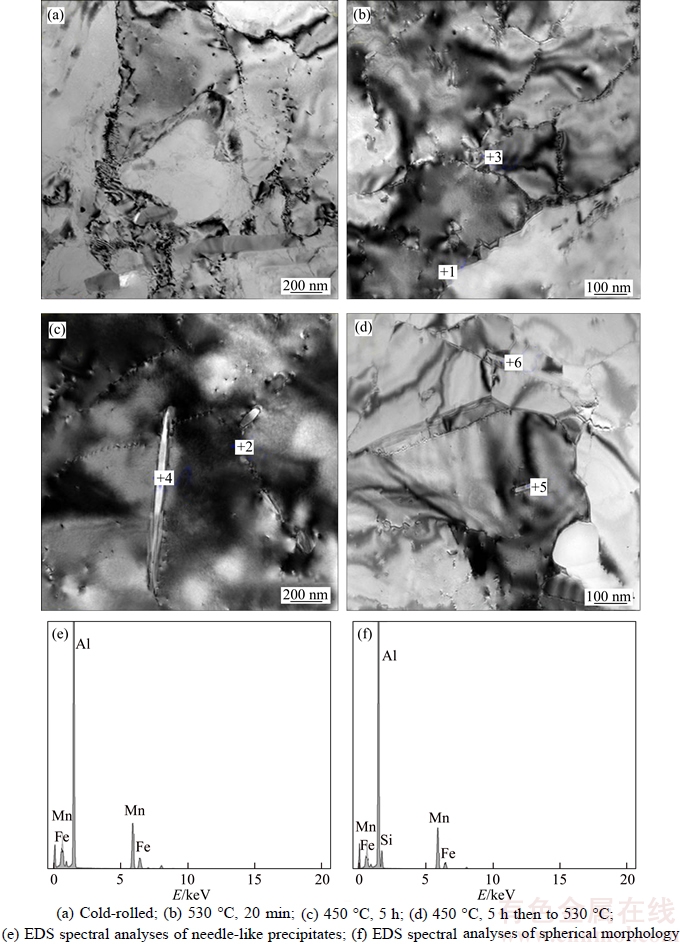
Figure 5 TEM bright field images of cold-rolled and various annealed samples:
In the initial stage of recrystallization (i.e. nucleation process), the retarding pressure originated from boundary curvature (PC) should be taken into account, and the net driving force for recrystallization (ΔP) can be thus described as [1]:
(4)
where rGB is the specific grain boundary energy; and R is the radius of a small spherical new nucleus. The nucleus will not grow to a new grain unless ΔP is positive, so the criterion for reliable nuclei will be given as:
(5)
Table 1 Chemical composition (at%) derived from related EDS results of marked precipitates in Figure 5
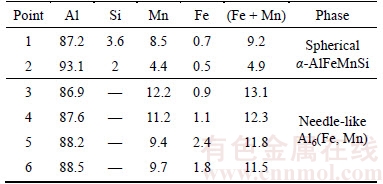
In the case of TSA, the pre-recovery brings about a lower PD and a higher PZ and hence a lower value of (PD–PZ), leading to a larger RC in accordance with Eq.(5). Since it is recognised that a larger RC is unfavourable to nucleation of recrystallization, accordingly, pre-recovery is expected to slow down recrystallization. However, in TSA case an enhancement of recrystallization kinetics at the early stage of annealing was observed, which is conflicting to the theoretical prediction. The microstructural evolution in Figure 4 demonstrates that pre-recovery favours recrystallization nucleation, and then the question is how does pre-recovery promote nucleation? Are there some local regions where the sub-grains grow faster and become reliable nuclei after pre-recovery treatment? To examine this, back scattered images with large scanning areas of cold-rolled and pre- recovered samples were captured and displayed in Figure 6. It can be seen that small primary particles distribute at the grain boundaries and along the rolling direction in the cold rolled condition (Figure 6(a)). After pre-recovery treatment, a large amount of fine precipitates emerges (Figure 6(b)). Most of them locate on the sub-grain boundaries in the interior of grains. However, some regions about 1–2 μm in thickness (marked by arrows in Figure 6(b)) are observed in the periphery of primary particles, where only few precipitates or even no precipitates exist. Inside this kind of precipitates free zones (PFZs), sub-grain growth is less affected by precipitates and thus the size of sub-grains is obviously larger than that outside these regions. These larger sub-grains within PFZs can readily become recrystallization nuclei. The corresponding nucleation step is illustrated in Figures 6(c)–(d). Figure 6(c) shows a typical microstructure of a deformed state, the cells/sub- grains structure is well developed. After pre- recovery treatment,the sub-grains within the precipitates-free zones are easier to grow, bulge into the neighbouring grain, as shown in Figure 6(d) and finally turn into recrystallized nucleus. Such nucleus will preferentially grow into the neighbouring grain because its boundaries with respect to neighbouring grains are high-angle boundaries, which are easy to move during grain growth.
Recrystallization nucleation takes place when the sub-grain size, R, reaches the critical radius, RC. Figure 7 is a schematic plot of the annealing time dependence on the sub-grain size R and the critical sub-grain size RC during the recovery stage. The shaded area represents the range of sub-grain sizes. The solid line represents the critical sub-grain size RC, which increases with time as a result of decreased stored energy (PD) and increased Zener pinning force (PZ). In the SSA case (Figure 7(a)), only a small amount of sub-grains can reach the critical size and become the recrystallization nuclei which rapidly invade into the deformed regions. In the TSA case (Figure 7(b)), the sub-grains can be divided into two regimes, in the interior of grains and inside the PFZs. Sub-grains inside the grains grow slowly and need long time to reach the critical size RC due to pinning effect by precipitates; while sub-grains inside the PFZs can readily grow over the RC. Consequently, there are more nuclei in TSA case than that in SSA case. It is thus concluded that pre-recovery promotes nucleation event and stimulates the rate of recrystallization at the early stage of annealing process.
At the later stage of annealing (growth process), the net driving force ΔP for grain growth is considered to be (PD–PZ). Therefore, pre- recovery will decrease the rate of recrystallization. This is in agreement with the experimental observations in Figure 3, where the JMAK exponent n is 1.02 for the materials with pre- recovery, somewhat lower than 1.14 for the materials without pre-recovery. The value of n is close to 1 which is very often observed in particles- containing aluminum alloys [15, 20]. Morever, the size of nuclei in the TSA sample (Figure 4(e)) is much smaller than that in the SSA sample (Figure 4(b)), this fact also reflects the suppressed growth rate in the former case. Ultimately, the samples without pre-recovery finish the recrystallization within a shorter period and exhibit a coarser grain structure compared to the pre- recovered samples.
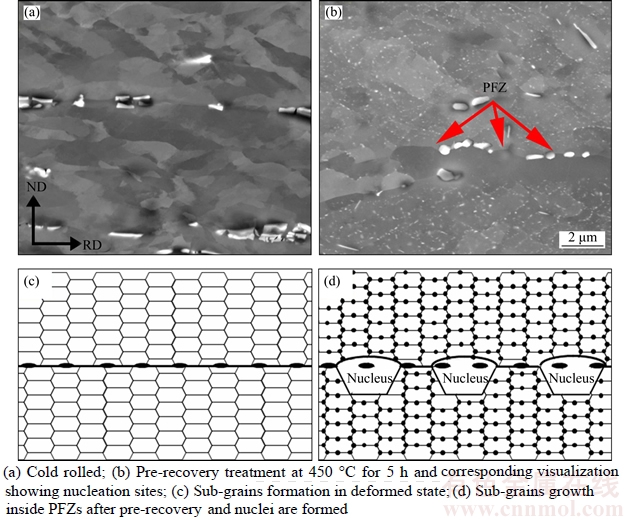
Figure 6 Back scattered images of Al–Mn sheets:

Figure 7 Schematic illustration showing evolution of subgrain size R distribution relative to critical subgrain size RC:
4 Conclusions
1) The effect of pre-recovery treatment on the recrystallization kinetics of a supersaturated Al–Mn alloy annealed at 530 °C is discussed. Pre-recovery stimulates the recrystallization kinetics at the early stage of annealing, which is attributed to the enhanced nucleation event; while opposite trend was observed at the later stage, owing to the reduced growth rate of the pre-recovered sample.
2) During pre-recovery, a large amount of Mn-bearing dispersoids precipitate from the supersaturated solid solution, and pin the movement of sub-grain boundaries. Simultaneously, precipitates-free zones form adjacent to original grain boundaries, leading to favorable recrystallization nucleation since sub-grain growth can readily take place within these zones.
3) Pre-recovery significantly decreases the net driving force for grain growth due to the reduction of stored energy and the increased Zener pining effect.
4) A simple model is presented to describe the nucleation step of recrystallization with pre- recovery treatment in the supersaturated Al–Mn alloys.
References
[1] HUMPHREYS F J, HATHERLY M. Recrystallization and related annealing phenomena [M]. Oxford: Elsevier, 2004.
[2] OYARZABAL M, MARTINEZ-DE-GUERENU A, GUTIERREZ I. Effect of stored energy and recovery on the overall recrystallization kinetics of a cold rolled low carbon steel [J]. Mater Sci Eng A, 2008, 485: 200–209.
[3] Stuwe H P, Padilha A F, Siciliano F Jr. Competition between recovery and recrystallization [J]. Mater Sci Eng A, 2002, 333: 361–367.
[4] Decreus B, Zurob H S, Dunlop J, Brechet Y. Effect of low-temperature recovery treatments on subsequent recrystallization in Al-2.5Mg [J]. Mater Sci Forum, 2007, 550: 381–386.
[5] Zurob H S, Brechet Y, Dunlop J. Quantitative criterion for recrystallization nucleation in single-phase alloys: Prediction of critical strains and incubation times [J]. Acta Mater, 2006, 54: 3983–3990.
[6] PRIMIG S, LEITNER H, KNABL W. Influence of the heating rate on the recrystallization behaviour of molybdenum [J]. Mater Sci Eng A, 2012, 535: 316–324.
[7] FURU T, MARTHINSEN K, NES E. Modeling recrystallization [J]. Mater Sci Technol, 1990, 6: 1093– 1102.
[8] Somerday M, Humphreys F J. Recrystallization behavior of supersaturated Al–Mn alloys. Part 1—Al–1.3wt% Mn [J]. Mater Sci Technol, 2003, 19: 20–29.
[9] Huang K, ENGLER O, LI Y J, MARTHINSEN K. Evolution in microstructure and properties during non-isothermal annealing of a cold-rolled Al–Mn–Fe–Si alloy with different microchemistry states [J]. Mater Sci Eng A, 2015, 628: 216–229.
[10] Daaland O, Nes E. Recrystallization texture development in commercial Al–Mn–Mg alloys [J]. Acta Mater, 1996, 14: 1413–1435.
[11] XIA S L, Ma M, ZHANG J X, WANG W X. Effect of heating rate on the microstructure, texture and tensile properties of continuous cast AA 5083 aluminum alloy [J]. Mater Sci Eng A, 2014, 609: 168–176.
[12] Liu W C, Radhakrishnan B. Recrystallization behaviour of a supersaturated Al–Mn alloy [J]. Mater Letters, 2010, 64: 1829–1832.
[13] Birol Y. Homogenization of a twin-roll cast thin Al–Mn strip [J]. J Alloys Compd, 2009, 471: 122–127.
[14] XIA S L, Ma M, ZHANG J X, WANG W X. Effect of heating rate on the microstructure, texture and tensile properties of continuous cast AA 5083 aluminum alloy [J]. Mater Sci Eng A, 2014, 609: 168–176.
[15] Liu W C, Radhakrishnan B. Recrystallization behaviour of a supersaturated Al–Mn alloy [J]. Mater Letters, 2010, 64: 1829–1832.
[16] Birol Y. Homogenization of a twin-roll cast thin Al–Mn strip [J]. J Alloys Compd, 2009, 471: 122–127.
[17] HUANG Y C, LI Q, XIAO Z B, LIU Y, ZHANG H H. Influence of precipitation on recrystallization texture of AA3104 aluminum alloy [J]. Journal of Central South University, 2015, 22: 3683–3688.
[18] Huang K, Zhao Q L, Li Y J, Marthinsen K. Two-stage annealing of a cold-rolled Al–Mn–Fe–Si alloy with different microchemistry states [J]. J Mater Process Tech, 2015, 221: 87–99.
[19] Li Y J, Arnberg L. Quantitative study on the precipitation behavior of dispersoids in DC-cast AA3003 alloy during heating and homogenization [J]. Acta Mater, 2003, 52: 3415–3428.
[20] RADKO K, JAROSLAV P. Recrystallization of previously recovered aluminium [J]. Metal Sci, 1975, 9: 104–110.
(Edited by FANG Jing-hua)
中文导读
预回复处理对过饱和Al–Mn合金再结晶动力学的影响
摘要:研究预回复处理对Al–Mn合金再结晶动力学的影响。研究结果表明,预回复过程中在初生相或晶界附近形成2–3 μm无析出带,该区域内的亚晶容易长大成为有效的再结晶核心,提高再结晶形核率;同时,预回复消耗形变储能,并在晶粒内部析出大量的细小颗粒状Al12(Fe,Mn)3Si相和针状Al6Mn相,降低晶粒长大的净驱动力,减缓了晶粒长大速度。因此,在450 °C预回复处理状态下,在530 °C退火时形核率提高导致早期的再结晶动力学相对较快,而晶粒长大速度减缓导致晚期的再结晶动力学相对较慢。
关键词:预回复处理;再结晶;形核与长大;析出;动力学行为
Foundation item: Project(2016YFB0300901) supported by National Key R&D Program of China; Project(51421001) supported by the National Natural Science Foundation of China; Project(106112015CDJXY130003) supported by the Fundamental Research Funds for the Central Universities, China
Received date: 2016-06-20; Accepted date: 2016-08-25
Corresponding author: HUANG Guang-jie, PhD, Professor; Tel: +86–23–65120787; E-mail: gjhuang@cqu.edu.cn; CAO Ling-fei, PhD, Professor; Tel: +86–23–65120781; E-mail: caolingfei@cqu.edu.cn