Trans. Nonferrous Met. Soc. China 23(2013) 2605-2610
Rheological characteristics of injection molded titanium alloys powder
Jia-hui WANG1, Qing-nan SHI2, Cheng-ling WU1, Jian XI2
1. City College, Kunming University of Science and Technology, Kunming 650051, China;
2. Faculty of Materials Engineering, Kunming University of Science and Technology, Kunming 650093, China
Received 21 July 2012; accepted 20 June 2013
Abstract: Ti-6Al-4V alloy powder was taken as raw material. 60% (mass fraction) paraffin, 35% low density polyethylene and 5% stearic acid were employed as binders to prepare injection feedstocks. Capillary rheometer was adopted to determine the rheological parameters and to analyze the rheological properties of the feedstocks at different milling time, powder loading and temperature. It is indicated through the results that the viscosity increases and the value of n decreases with the increase of milling time. The more the powder loading is, the higher the viscosity is. The empirical formula on the relationship between the viscosity and the powder loading is:
. The value m is calculated as 0.33. The flow activation energy Ea decreases with the increase of shear rate.
Key words: injection molding; titanium alloy; feedstock; rheological properties
1 Introduction
Ti and its alloys have received considerable attention recently in aerospace, navigation, automotive, biological engineering, sports goods and other fields. The advantages of these materials include low density, high specific strength, excellent corrosion resistance, and biocompatibility. However, the industrialized application of Ti and its alloys, especially in the manufacturing of complex parts, is limited owing to the poor machining performance and high manufacturing cost. Therefore, there is an urgent need in the industry for an alternative method of Ti manufacture, which can reduce the cost and complexity of processing. A leading candidate is metal injection molding (MIM) [1-8].
MIM derived from plastic injection molding is an advanced net-shape powder metallurgy forming process, which is composed of the following processes: 1) mixing of the binder and the powder in a hot extruder to create uniform powder/binder mixture; 2) injection molding process to form the desired shape; 3) debinding process to remove the binder system; 4) sintering process to obtain the desired parts. Technically, the parts made by powder injection molding enjoy such good performances as no ingredient segregation, even structure and stable performance. Economically, as a new technology with little or no cutting, its utilization ratio of the material for the parts reaches 100%, which saves material as well as improves productivity [9].
In the MIM process, mold filling by the feedstock is dependent on the viscous flow of the mixture into the mould cavity. It requires special rheological properties. The most important property is the viscosity, which is extremely sensitive to temperature and shear rate. When the shear rate increases, the viscosity decreases, which is beneficial to the shape forming. This work studies the rheological properties and analyzes the influence of such factors as the powder milling time, shear rate, temperature and powder loading on the viscosity of the molding compounds.
2 Experimental
2.1 Powder
The metal powders used in the experiments are Ti (particle size < 74 μm, purity > 99.5%) and 6Al-4V pre-alloyed powder (particle size < 74 μm, purity > 99%). Mixtures of 90% Ti (mass fraction) and 10% 6Al-4V alloy powder as starting powders, along with 1% of SA, have been milled in a QX-2 planetary ball mill. The ball-to-powder mass ratio is 20:1, and the rotational speed of the sun disc and the jar is 330 r/min. The jars are evacuated and filled with Ar gas to avoid oxidation of the powder particles. The milling time is 20, 40 and 60 h, respectively. The characteristics of these powders are reported in Table 1. Figure 1 shows SEM micrographs of the particles.
Table 1 Characteristics of Ti alloy powders
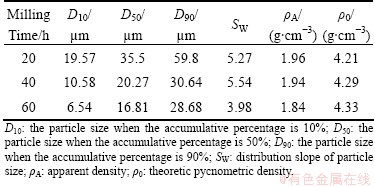
The spherical morphology of the particles was examined with an XL30SEM-TMP scanning electron microscopy (SEM) and the particle size distributions of the powders were obtained in a laser scattering particle analyzer (Rise-2002).
2.2 Binder and feedstock preparation
A wax-polymer binder was selected in this work. The binder consists of paraffin wax (PW) 60%, low density polyethylene (LDPE) 35% and stearic acid (SA) 5%. In order to analyze the influences of temperature, shear rate, powder milling time and powder loading on rheological properties, six feedstocks are prepared by mixing process, which are conducted through multi-blade mixer at 140 °C for 2 h. Table 2 shows the preparation parameters of feedstocks.
Table 2 Feedstocks preparation parameters
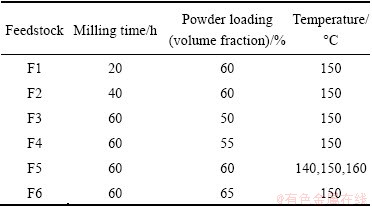
2.3 Rheological measurement
The viscosity of feedstocks was measured by an Instron 3211 capillary rheometer. A mould of 1.2 mm diameter and 51.11 mm length was used. The test temperatures were 140, 150 and 160 °C. The shear rate was in the range of 4.23 to 1412 s-1.
3 Results and discussion
3.1 Pseudo-plastic behavior of feedstocks
The flow curves of feedstocks F1, F2, F5 as a function of shear rate at 150 °C are shown in Fig. 2, based upon lgτ versus
. This fluid is named pseudo-plastic, which is the most general kind in non-Newtonian fluids. It can be described by the “power law”:
(1)
where τ is the shear stress; K is a constant;
is the shear rate; and n is the flow behavior index. It is found from the curves that the shear stress increases with increasing the shear rate.
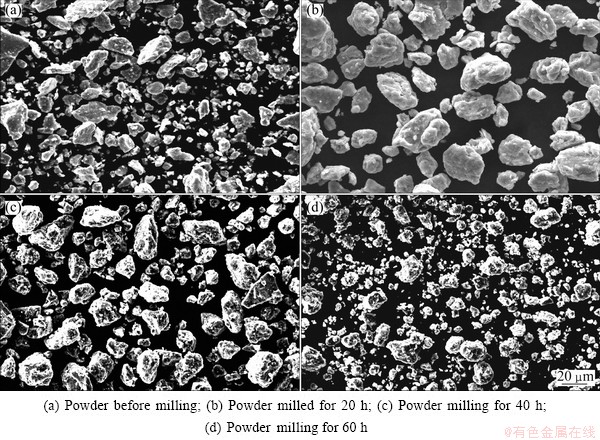
Fig. 1 SEM images of particles
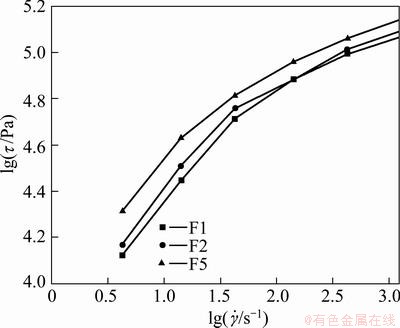
Fig. 2 Shear stress of feedstocks F1, F2, F5 as function of shear rate at 150 °C
For a pseudo-plastic fluid, the viscosity decreases with increasing the shear rate, which can be described by
(2)
where ηa is the apparent viscosity; and n is smaller than 1 [10-12]. Figure 3 shows the plot of the viscosity as a function of shear rate. The viscosity is found to decrease with the shear rate increasing. With the increase of shear rate, the change of apparent viscosity slows down due to the winding long-chain molecules of the polymer in the melt. When it is still, the particles or molecules are wound randomly; with shear stress, they gradually become directional, extending, deforming and dispersing to form organized flow. With the increase of shear rate, the melt is more organized and the viscosity decreases. When the melt is totally organized, the viscosity ceases to decrease. The reduction of the viscosity with increasing shear rate is taken the advantage of in achieving desirable and optimum viscosity for metal in processing without raising the temperature to detrimental levels, simply by raising the shear rate to as high level as economically and otherwise possible. From the slopes of the curves obtained in Fig. 2, the flow behavior index n is determined. The value of n represents the degree of sensitivity of viscosity to shear rate. The lower the value of n is, the more sensitive the viscosity to shear rate is. The measured n values of feedstocks under various shear rates are shown in Fig. 4. It is shown through analysis that the value of n decreases with the increase of shear rate.

Fig. 3 Viscosity of feedstocks F1, F2, F5 as function of shear rate at 150 °C
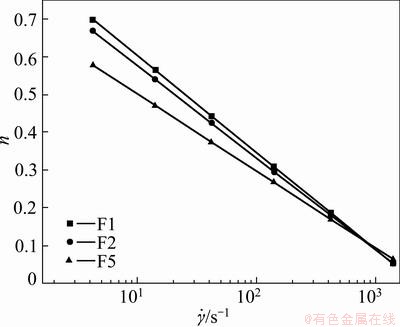
Fig. 4 n value of feedstocks F1, F2, F5 as function of shear rate at 150 °C
3.2 Influence of MA milling time on rheological behavior
The powder characteristics are important factors that determine the feedstock rheological behavior, especially the particle size, the distribution slope of particle size, and the particle shape. The characteristic data of powders after 20, 40, 60 h of milling are summarized in Table 1. It is indicated by the results that milling time changes the powder characteristics. These changes include the reduction of the average particle size, the distribution slope of particle size, and the apparent density [13,14].
In order to study the effect of milling time on the rheological properties, feedstocks after 20, 40, 60 h of milling are prepared at temperature of 150 °C, which are in the same powder loading (
=60%, volume fraction). As shown in Fig. 3, the viscosity increases with the growing of milling time. When the milling time grows, the particle size is smaller, the surface increases and the friction is reinforced. Hence, in a given volume, the viscosity is inversely proportional to the particle size. The increase of the shear rate leads to smaller difference in the viscosity at different milling time. For example, when the shear rate is 14.12976 s-1, the difference in the viscosity between 20 h and 60 h is 699.821 Pa·s; when the rate is 423.8929 s -1, the difference reduces to 10.597 Pa·s.
After analyzing the value of n in Fig. 4, it is found that n decreases with the increase of milling time, that is to say, the longer the milling time is, the more sensitive the viscosity to shear rate is. With the increase of shear rate, the difference between the value of n at different milling time decreases. When the shear rate reaches 423.8929 s-1, the values of n at 20, 40 and 60 h are approximate.
3.3 Influence of powder loading on rheological behavior
As MIM feedstock is composed of powder and binder, the rheological behavior is determined by the viscosity of the polymer. The addition of metal powder increases the viscosity of feedstock. Therefore, the content of binder and powder is vital to the success of MIM. Figure 5 shows the relationship between the powder loading and the viscosity of feedstocks F3, F4, F5 and F6 at milling time of 60 h. At low shear rates, the viscosity is very sensitive to the powder loading. Meanwhile, the viscosity increases with the increase of the powder loading [15,16]. With the increase of shear rate, the sensitivity reduces. The log-log curve of shear stress and shear rate is shown in Fig. 6. According to Fig. 6, the flow behavior index n of feedstocks F3, F4, F5 and F6 are 0.387, 0.337, 0.320 and 0.301, respectively. It means the value of n decreases when the powder loading increases.
The empirical formula on the relationship between viscosity and powder loading is
(3)
where ηb is the viscosity of the binder itself; η is the viscosity of the feedstock;
is the volume fraction of powder;
max is the maximum powder loading; A, m are the constants. Figure 7 shows the relationship between ln η and
at shear rate of 423.8929 s-1 for the feedstocks F3, F4, F5 and F6 at 150 °C. Through density experiment of powder-binder,
m is determined to be 73%. The value m is calculated as 0.33.

Fig. 5 Viscosity of feedstocks F3, F4, F5 and F6 as function of shear rate at different powder loading
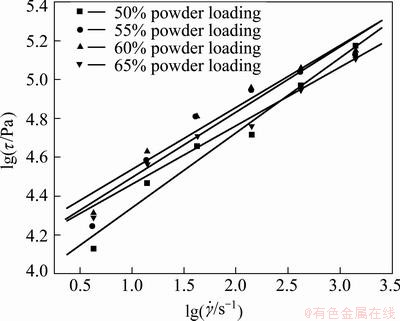
Fig. 6 Shear stress of feedstocks F3, F4, F5, F6 as function of shear rate at different powder loading
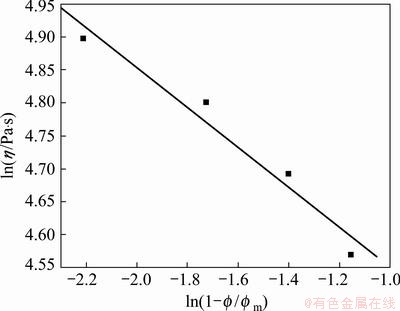
Fig. 7 Viscosity of feedstocks as a function of powder loading at shear rate of 423.8929 s-1
3.4 Influence of temperature on viscosity
The dependence of viscosity on temperature is also important in MIM process. The relationship between the viscosity and temperature can be expressed as
(4)
where η0 is the viscosity at temperature T0; Ea is the flow activation energy; R is the gas constant; T is the temperature. The value of Ea indicates the degree of sensitivity of the viscosity to temperature, and the lower Ea value is, the less sensitive viscosity to temperature variation is [13-16]. It is important for the injection process, because the dependence of the viscosity on temperature is generally higher than that on shear rate. If the viscosity is very sensitive to the temperature variation, any small fluctuation of temperature during molding results in a sudden viscosity change. This can cause undue stress concentration in the molded part, resulting in cracking and distortion. Therefore, lower Ea of feedstock is favorable for injection molding. Ea can be obtained by lg η—1/T curve, as shown in Fig. 8. The curves are drawn at the shear rate of 141.2976, 423.8929 and 1412.976 s-1, respectively. As shown in Table 3, Ea decreases with the increase of shear rate.
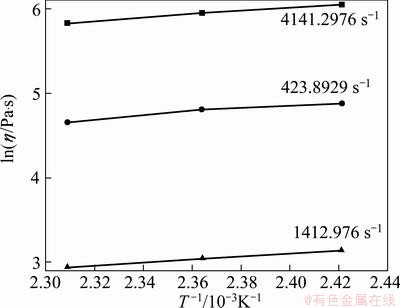
Fig. 8 Relationship between ln η and T-1 at three different shear rates
Table 3 Ea value of feedstock F5at different shear rates

What’s more, the value of n changes with the variation of temperature. The values of n of feedstock F5 at 140, 150 and 160 °C are listed in Table 4. It is found that the higher temperature is, the higher the value of n is, which means that feedstock is not sensitive to changes in shear rates. In the MIM process, the viscosity comes from the polymeric component in the binder. The dilution behavior at shear and recovery of the viscosity after the revocation of shear stress is the destruction and reconstruction of melts. When the temperature gets higher, the distance between the molecules and the kinetic energy grows, while the molecular attraction and internal friction decrease. The rise of temperature leads to the destruction of melt to some degree, which undermines the influence and the sensitivity of shear rate.
Table 4 n value of feedstock F5 at different temperatures

4 Conclusions
1) The flow of Ti-6Al-4V alloy feedstocks is pseudoplastic. The shear stress grows exponentially with shear rate increasing and the viscosity decreases with the increase of shear rate and temperature. With the increase of shear rate, the change of the viscosity slows down. The value of n represents the degree of sensitivity of the viscosity versus shear rate. It is found that the value of n decreases with increasing shear rate.
2) With the growing of milling time, the viscosity increases and the value of n decreases. On the other hand, the differences of the viscosity at different milling times and the difference between the values of n decrease with the increase of shear rate.
3) The more powder loading is, the higher viscosity is, and the lower value of n is. With the increase of shear rate, the sensitivity of the viscosity to powder loading decreases. The empirical formula on the relationship between viscosity and powder loading is:
. The value m is calculated as 0.33.
4) For Ti-6Al-4V alloy feedstocks, the value of n increases with the increase of temperature and Ea decreases with the increase of shear rate.
References
[1] OBASI G C, FERRI O M, BORMANN R, EBEL T. Influence of processing parameters on mechanical properties of Ti-6Al-4V alloy fabricated by MIM [J]. Materials Science and Engineering A, 2010, 527: 3929-3935.
[2] FERRI O M, BORMANN R, EBEL T. Influence of surface quality and porosity on fatigue behavior of Ti-6Al-4Vcomponents processed by MIM [J]. Materials Science and Engineering A, 2010, 527: 1800-1805.
[3] THIAN E S, LOH N H, KHOR K A, TOR S B. Ti-6A1-4V/HA composite feedstock for injection molding [J]. Materials Letters, 2002, 56: 522-532.
[4] SCOTT W K, ERIC N, SIMMONS K. A new binder for powder injection molding titanium and other reactive metals [J]. Journal of Materials Processing Technology, 2006, 176: 205-209.
[5] AROCKIASAMY A, RANDALL M G, HEANEY D F, WANG P T, HORSTEMEYER M F, KING R L, ADCOCK B. Effect of additives on sintering response of titanium by powder injection moulding [J]. Powder Metallurgy, 2011, 54: 420-426.
[6] ERGUL E, GULSOY H
, GUNAY V. Effect of sintering parameters on mechanical properties of injection moulded Ti-6Al-4V alloys [J]. Powder Metallurgy, 2009, 52: 65-71.
[7] GUO Shi-bo, QU Xuan-hui, XIANG Jun-huai, ZHANG Rong-fa, HE Xiaog-ming, LI Ming-sheng, DUO Shu-wang, LI Wen-kai. Effect of annealing processing on microstructure and properties of Ti-6A1-4V alloy by powder injection molding [J]. Transaction of Nonferrous Metals Society of China, 2006, 16: 701-704.
[8] MUTSUDDY B C. Injection molding research paves way to ceramic engine parts [J]. Ind Res Dev, 1983, 25: 76-80.
[9] GERMAN R M, BOOKER P. Powder injection molding [J]. Appl Mech Rev, 1991, 44(8): 134-168.
[10] HUANG Bai-yun, LIANG Shu-quan, QU Xuan-hui. The rheology of metal injection molding [J]. Journal of Materials Processing Technology, 2003, 137: 132-137.
[11] HUANG Bai-yun, FAN Jing-lian, LIANG Shu-quan, QU Xuan-hui. The rheological and sintering behavior of W-Ni-Fe nano-structured crystalline powder [J]. Journal of Materials Processing Technology, 2003, 137: 177-182.
[12] SOTOMAYOR M E, VAREZ A, LEVENFELD B. Influence of powder particle size distribution on rheological properties of 316 powder injection moulding feedstocks [J]. Powder Technology, 2010, 200: 30-36.
[13] MANNSCHATZ A, MULLER A, MORITZ T. Influence of powder morphology on properties of ceramic injection moulding feedstocks [J]. Journal of the European Ceramic Society, 2011, 31(14): 2551-2558.
[14] LI Yi-min, LI Liu-jun, KHALIL K A. Effect of powder loading on metal injection molding stainless steels [J]. Journal of Materials Processing Technology, 2007, 183: 432-439.
[15] SUPATI R, LOH N H, KHOR K A, TOR S B. Mixing and characterization of feedstock for powder injection molding [J]. Materials Letters, 2000, 46: 109-114.
[16] CONTRERAS J M, JIME’MENEZ-MORALES A, TORRALBA J M. Experimental and theoretical methods for optimal solids loading calculation in MIM feedstocks fabricated from powders with different particle characteristics [J]. Powder Metallurgy, 2010, 53: 34-40.
注射成形钛合金粉末流变特性
王家惠1,史庆南2,吴承玲1,席 健2
1. 昆明理工大学 城市学院,昆明 650051;
2. 昆明理工大学 材料科学与工程学院,昆明 650093
摘 要:以Ti-6Al-4V合金粉末为原料,选用60%(质量分数)石蜡、35%低密度聚乙烯和5%硬脂酸为粘结剂配方制备注射成型喂料。采用毛细管流变仪测定喂料的流变参数,分析不同球磨时间、粉末装载量、温度下喂料的流变学性能。结果表明:随着球磨时间的增加,喂料粘度增加,n值减小;粉末装载量越高,喂料的粘度值越大,而且粘度与粉末装载量满足经验公式:
,经计算,m的值为0.33。粘性流动激活能Ea值随剪切速率的增加而减小。
关键词:注射成形;钛合金;喂料;流变特性
(Edited by Chao WANG)
Corresponding author: Qing-nan SHI; Tel: +86-871-5916780; E-mail: shikust@vip.163.com
DOI: 10.1016/S1003-6326(13)62774-0