
A new model to describe effect of plastic deformation on elastic modulus of aluminum alloy
ZANG Shun-lai(臧顺来)1, 2, GUO Cheng(郭 成)1, WEI Gong-ji(魏公际)3,
CHEN Feng(谌 峰)3, DONG Wei(董 伟)1, ZHANG Ke(张 珂)4
1. School of Mechanical Engineering, Xi’an Jiaotong University, Xi’an 710049, China;
2. State Key Laboratory of Plastic Forming Simulation and Die & Mould Technology,
Huazhong University of Science and Technology, Wuhan 430074, China;
3. Xi’an Aeronautical Polytechnic Institute, Xi’an 710049, China;
4. School of Materials Science and Engineering, Xi’an Jiaotong University, Xi’an 710049, China
Received 28 July 2006; accepted 15 September 2006
Abstract: In order to improve the prediction capability of spring-back in aluminum sheet metal forming, the influence of the plastic deformation on elastic modulus is considered when the material undergoes a large plastic deformation. The present work focused on establishing a new model to accurately describe the relation of elastic modulus and plastic deformation. The tensile tests were performed to investigate the influence of plastic deformation on elastic modulus at low strain rate. Two different aluminum sheets were used, AA2024-T3 and LY12-CZ, and the thickness of sheet metals was 1.3 mm and 2.0 mm, respectively. In order to overcome the drawback, which is directly measuring the slope of tension curve to obtain elastic modulus, an extrapolation method was adopted. The proposal macroscopic piecewise sinusoidal function can accurately model the elastic modulus variation.
Key words: plastic deformation; elastic modulus; aluminum alloy; spring-back
1 Introduction
Classically, the elastic modulus is commonly considered a constant. However, LEMS[1] revealed that the elastic modulus decreases with the plastic deformation. Due to the change of elastic modulus under plastic deformation, the spring-back is larger than that calculated with a constant value. The measurement and description of the evolution of elastic modulus are essential to improve the prediction capability of spring-back in sheet metal forming processes[2].
Recently, several investigations on the change of elastic modulus with plastic deformation have been performed. VIN et al[3] gave a simple mathematical model to describe the relationship between plastic deformation and elastic modulus based on experiment. MORESTIN et al[4-5] formulated an elasto-plastic model using kinematic hardening model for spring-back in sheet metal forming. In their calculations the change of the elastic modulus versus plastic strain was taken into account. YAN and XU[6] addressed the effect of non-linear elastic unloading on spring-back prediction of V-shape bend. LI et al[7] discussed the evolution of elastic modulus and its mechanism based on macroscopic and microscopic experimental results. YANG et al[8] analyzed the influence of plastic deformation on the changes in spring-back characteristics of sheet metal by using both macroscopic and microscopic measurement of elastic modulus.
In this study, the influence of plastic deformation on the elastic modulus of AL2024-T3 and LY12-CZ alloys is obtained by using uni-axial tensile tests. Based on the experimental results, a new mathematical model to describe the relation between elastic modulus and plastic deformation is given.
2 theory
The change of elastic modulus after plastic deformation may be caused by a lot of factors, such as microscopic debonding between the matrix and inclusions or second-phase particles[9-11], the increase of internal stresses during deformation[12], the increase of residual stress and micro cracks, the development of texture introduced by plastic deformation[10,13,14], especially, the changes in the dislocation arrangement[11].
The residual stress increases with the plastic deformation and disturbs the elastic recovery. The micro crack inside the work-piece increases with plastic deformation. As a result, the apparent elastic modulus varies. However, the reduction of the density due to plastic deformation is less than 1% and the effect on the elastic modulus must not be as large as the results[8]. Dislocation structure is another inferential factor which changes with the plastic deformation and affects elastic behavior. The dislocations released from a common source move on a slip surface and easily pile up while the front of dislocations is stopped by obstacles, such as grain boundary, and solutes. The piled-up dislocations could move backward when the shearing stress is released during unloading[8].
MOTT and FRIEDEL first explained the dependence of E on the network of dislocations in metals. Applying a prescribed stress, a dislocation line locked by nodal points or pinned by solute atoms can bow out, giving extra elastic deformation, which results in a decrease of elastic modulus. This change can be calculated from the following equation:
(1)
where ρ is dislocation density; l is the average length of dislocations between pinning points, and α is a function of l.
A dislocation strain (εdis) can be represented by
(2)
where b is the magnitude of Burgers vector and ξ is the average displacement of a dislocation line of length l, as defined in Eqn.(1). According to Eqn.(1) and Eqn.(2), a decrease in E with plastic deformation is expected. However, it is difficult to predict the extent of this decrease, since the dislocation structure depends on several factors, such as the type of deformation process, and temperature.
3 Experimental
To measure the evolution of elastic modulus, uni-axial tensile tests were performed according to GB/T228—2002 using INSTRON 10 t tensile test machine (model: 1341) at a constant crosshead-speed, 1.05 mm/min. Flat tensile test specimens were fabricated as specified by GB/T228—2002 and hydraulic grips were used to simultaneously clutch two ends of the specimen.
To verify the evolution law of elastic modulus, two different aluminum alloy sheets were considered in this work: AA2024-T3 (1.3 mm in thickness), LY12-CZ (2.0 mm in thickness).
In the polycrystalline material, only the elastic deformation reveals when the stress is less than the true elastic limit. With the increase of the stress, which is beyond the true elastic limit and less than viscous elastic limit, the viscoelastic deformation occurs. The macroscopic phenomenon is that the strain lags behind the stress, and the stress—strain relation is non-linear. While the value of true elastic limit is very little, its amount is equal to hundreds of dislocation movements, which is far less than proportional limit of metal material. In the measuring stage of elastic modulus, the viscoelastic deformation commonly occurs. The higher the sensitivity of measurement of elastic modulus is, the lower the proportion is. The initial stage of stress—strain curve is not strictly linear. Therefore, the method of direct measuring the slope of tension curve to obtain elastic modulus is not accurate. In order to overcome this drawback, an extrapolation method is used. The schematic of method is shown in Fig.1. The middle points of unloading curve are fitted by a two order multinomial as follows:
(3)
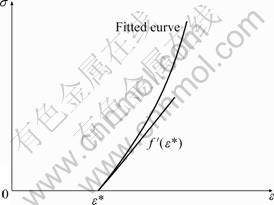
Fig.1 Schematic of method to get elastic modulus
The elastic modulus is got by computing the derivative of f(ε*) at zero stress point. Here ε* is the plastic deformation of the tensile test specimen.
In this paper, three elastic moduli are obtained from each uni-tensile stress—strain curve, which are initial elastic modulus of un-deformed material, unloading elastic modulus computed from unloading stress—strain curve, and reloading elastic modulus obtained from reloading stress—strain curve.
4 Results and discussion
The elastic modulus is calculated from the stress— strain curve at initial elastic deformation and unloading curve with a given plastic deformation using the precision extensometer, and then the reloading curve is also measured.
4.1 Variation of elastic modulus of LY12-CZ
Fig.2 shows the variation of elastic modulus with equivalent plastic strain for LY12-CZ sheets. The unloading elastic modulus decreases from the first step of deformation(at equivalent plastic strain of about 0.02), then it drops to the minimum; after this point, little recovery is observed, and the curve stabilizes in the range of 58.0-62.0 GPa. The initial elastic modulus is about 71.0 GPa, and the minimum elastic modulus is 52.1 GPa.
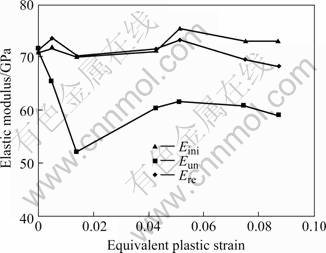
Fig.2 Change of elastic modulus of LY12-CZ with equivalent plastic strain
The aluminum alloy may not be ideal continuum caused by rolling. Hence the initial elastic modulus is various. To eliminate the influence of initial elastic modulus variation on the relationship between elastic modulus and plastic strain, the ratio of unloading elastic modulus to initial one is used. The equivalent plastic strain vs ratio of unloading elastic modulus to initial one is shown in Fig.3. In Fig.3, the ratio decreases from 100% to the minimum of 75.5%, and the decrease is about 24.5%. In Fig.2, the elastic modulus decreases from 71.0 GPa to the minimum of 52.1 GPa, and the decrease is about 26.6%. Although the difference is slight, the function of elastic modulus and plastic strain established from Fig.3 is more accurate.
The variation of initial elastic modulus, unloading one, and reloading one, with equivalent plastic strain for LY12-CZ is also shown in Fig.2. The unloading elastic modulus is lower than initial one, while the elastic modulus recovery is observed at the reloading stage. The difference between the initial elastic modulus and the reloading one of the same specimen is slight. In Fig.3, the ratio of reloading elastic modulus to initial one is approximately a constant at different equivalent plastic strains.

Fig.3 Equivalent plastic strain vs variation in elastic modulus of LY12-CZ
4.2 Variation of elastic modulus of AA2024-T3
The variation of elastic modulus with tensile equivalent plastic strain for AA2024-T3 is shown in Fig.4. The unloading elastic modulus decreases at the first step of deformation(at equivalent plastic strain of about 0.04), then it reaches the minimum; after this point, a very little recovery which is not distinct as that of LY12-CZ is observed, and the curve stabilizes with the elastic modulus in the range of 55.0-56.6 GPa. The initial elastic modulus is about 70.0 GPa, the minimum elastic modulus is 54.96 GPa, and the decrease is about 21.5%.
The effect of initial elastic modulus variation on the relationship between elastic modulus and plastic strain is eliminated by using the ratio of unloading elastic modulus to initial one. The equivalent plastic strain vs ratio of unloading elastic modulus to initial one and ratio of reloading elastic modulus to initial one are shown in Fig.5. In Fig.5, the ratio of unloading elastic modulus to initial one decreases from 100% to the minimum of 79.9%, and the decrease is about 20.1%.

Fig.4 Change of elastic modulus of AA2024-T3 with equivalent plastic strain

Fig.5 Equivalent plastic strain vs variation in elastic modulus of AA2024-T3
As shown in Fig.4, the unloading elastic modulus is lower than initial one, while the elastic modulus recovery is observed at the reloading stage. The difference between the initial elastic modulus and the reloading one is slight. In Fig.5, the ratio of reloading elastic modulus to initial one is still about a constant at different equivalent plastic strains.
4.3 Discussion
In all tests, the same phenomenon is observed. The unloading elastic modulus decreases from the first step of deformation at a certain equivalent plastic strain. The drop of unloading elastic modulus reaches a minimum. After this point, a recovery occurs. And then the curve stabilizes with the elastic modulus values in certain range. The unloading elastic modulus is lower than initial one, and the elastic modulus recovery is observed in the reloading stage. The difference between the initial elastic modulus and the reloading one of the same specimen is slight.
This can be explained by the Mott and Friedel Theory. In Eqn.(1), E is the elastic modulus of virgin materials. The dislocation density increases with the plastic deformation, then the right items of Eqn.(1) are negative, the change of elastic modulus is
(4)
Eqn.(4) is negative, thus, a decrease in E with plastic deformation is expected. In Eqn.(4), E1 is the elastic modulus of deformed sheet metal.
The dislocation density of un-deformed sheet metal is not zero caused by rolling, so there is a difference between initial elastic modulus, Eini and E, that is,
(5)
The difference between unloading elastic modulus Eun and E is
(6)
The difference between reloading elastic modulus Ere and E is
(7)
when Eqn.(6) subtracting Eqn.(5), the difference of initial elastic modulus and unloading elastic modulus is obtained as Eqn.(8):
(8)
when Eqn.(7) subtracts Eqn.(5), the difference of initial elastic modulus and reloading elastic modulus is obtained as Eqn.(9):
(9)
From Eqn.(8) and Eqn.(9), considering the evolution of dislocation structure, the change of elastic modulus versus equivalent plastic strain can be explained.
5 Mathematical equation
Traditionally, the elastic modulus variation is approximated by a piecewise linear function. The piecewise linear model is simple, but it can not correctly describe the decrease of the elastic modulus at the initial stage. Here, a macroscopic piecewise sinusoidal function(Eqn.(10)) is proposed to approximately model the elastic modulus variation. The schematic of identification of piecewise sinusoidal function parameters is shown in Fig.6. The vertical axis is the ratio of elastic modulus after plastic deformation to initial one, so the elastic modulus value at A, B, C points is the average elastic modulus
multiplying the ratio.
(10)
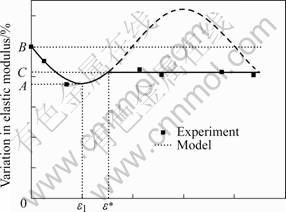
Fig.6 Approximation of elastic modulus variation versus equivalent plastic strain
Table 1 lists the piecewise sinusoidal function para- meters to describe elastic modulus variation of AA2024- T3 and LY12-CZ.
Table 1 Piecewise sinusoidal function parameters of AA2024- T3 and LY12-CZ alloys

6 Conclusions
1) In order to develop the prediction capability of spring-back in sheet metal forming processes, the elastic modulus is measured before and after plastic deformation for evaluation of the change in the elastic modulus. It is found that the unloading elastic modulus decreases from the first step of deformation at a certain equivalent plastic strain. The decrease of unloading elastic modulus reaches a minimum; after this point, a slight increase is observed, and then the curve stabilizes with the elastic modulus values in certain range.
2) The unloading elastic modulus is lower than the initial one, and the elastic modulus recovery is observed in the reloading stage.
3) The difference between the initial elastic modulus and the reloading one is slight.
4) One of the major influential factors to the variation of elastic modulus is the movable dislocation accompanying with the change of dislocation density.
5) A macroscopic piecewise sinusoidal function is proposed to approximately model the elastic modulus variation.
References
[1] LEMS W. The Change of Elastic Modulus after Deformation at Low Temperature and Its Recovery[D]. Delft: University of Delft, 1963.
[2] LI X C, YANG Y Y, WANG Y Z, BAO J, LI S P. Effect of the material-hardening mode on the springback simulation accuracy of V-free bending[J]. Journal of Materials Processing Technology, 2002, 123(2):209-211.
[3] VIN L J, STREPPL A H, SINGH U P. A process model for air bending [J]. Journal of Material Process Technology, 1996, 56(1/2): 48-54.
[4] MORESTIN F, BOIVIN M, SILVA C. Elasto-plastic formulation using a kinematic hardening model for springback analysis in sheet metal forming [J]. Journal of Material Process Technology, 1996, 56(1-4): 619-630.
[5] MORESTIN F, BOIVIN M. On the necessity of taking into account the variation in the Young modulus with plastic strain in elastic-plastic software [J]. Nuclear Engineering and Design, 1996, 162(1):107-116.
[6] YAN L C, XU B Y. The effect of non-linear elastic unloading on spring-back prediction [J]. Mechanics in Engineering, 2002, 24(3): 41-43.
[7] LI X C, YANG Y Y, BAO J, LI S P. Relationship between elastic modulus and plastic deformation [J]. Journal of Harbin Institute of Technology, 2000, 32(5): 54-56.
[8] YANG M, AKIYAMA Y, SASAKI T. Microscopic evaluation of change in spring-back characteristics due to plastic deformation [A]. Materials Processing and Design: Modeling, Simulation and Application[C]. NUMIFORM, 2004: 881-886.
[9] YAMAGUCHI K, ADACHI H, TAKAKURA N. Effects of plastic strain and strain path on elastic modulus of sheet metals [J]. Metals and Materials, 1998, 4(3): 420-25.
[10] AGNEW S R, WEERTMAN J R. The influence of texture on the elastic properties of ultrafine-grain copper [J]. Materials Science & Engineering A: Structural Materials: Properties, Microstructure and Processing, 1998, 242(1/2): 174-80.
[11] BENITO J A, MANERO J M, JORBA J, ROCA A. Change of elastic modulus of cold-deformed pure iron in a tensile test[J]. Metallurgical and Materials Transactions, 2005, 36(1): 3317-3324.
[12] BOCKER W, BUNGE H J, REINERT T. Anomalies of elastic modulus in Fe-Cu composites after high degrees of deformation [J]. Mater Sci Forum, 1993, 157-162(22): 1551-58.
[13] LEDBETTER H M, KIM S A. Low temperature elastic constants of deformed polycrystalline copper [J]. Mater Sci Eng A, 1988, 101(5): 87-92.
[14] YANG M, AKIYAMA Y, SASAKI T. Evaluation of change in material properties due to plastic deformation[J]. Journal of Materials Processing Technology, 2004, 151(1/3): 232-236.
(Edited by YANG Bing)
Foundation item: Project(06-13) supported by the Foundation of State Key Laboratory of Plastic Forming Simulation and Die & Mould Technology, China.
Corresponding author: ZANG Shun-lai; Tel: +86-29-82668607; E-mail: slzang@mailst.xjtu.edu.cn