J. Cent. South Univ. (2017) 24: 2932-2939
DOI: https://doi.org/10.1007/s11771-017-3707-2

Hydration properties and thermal analysis of cement-based materials containing limestone powder
ZHOU Wei(周伟)1, 2, LI Liang(李梁)2, 3, LIU Shu-hua(刘数华)1, 2, VINH T. N. Dao3, LIU Xing-hong(刘杏红)4
1. State Key Laboratory of Water Resources and Hydropower Engineering Science,Wuhan University, Wuhan 430072, China;
2. School of Water Resources and Hydropower Engineering, Wuhan University, Wuhan 430072, China;
3. School of Civil Engineering, The University of Queensland, Brisbane 4072, Australia;
4. School of Civil Engineering and Architecture, Wuhan University, Wuhan 430072, China
Central South University Press and Springer-Verlag GmbH Germany, part of Springer Nature 2017
Abstract: The hydration and thermal properties of cement-based materials containing various proportions of limestone powder as a partial replacement for ordinary Portland cement, were investigated and reported. Both compressive and flexural strengths of cement mortar with various contents of limestone powder were tested to study the influence of limestone powder on the strength development of resulting mixtures. The hydration heat and its rate of evolution were also tested, which clearly showed that the replacement percentage of limestone powder had significant effects on the total hydration heat but only a modest influence on the rate of heat evolution of cement-limestone binder. Importantly, the reduction coefficient of limestone powder on the hydration heat, needed for estimation of adiabatic temperature rise of cement-limestone binder, was found to be approximately 0.51. Fundamental thermal properties of these concrete mixtures containing limestone powder were also studied. Increasing the percentage of limestone powder resulted in a significant reduction in the adiabatic temperature rise but only a slight increase in other thermal properties such as thermal conductivity, thermal diffusivity and specific heat. In addition, thermal analysis using finite-element modelling indicated that inclusion of limestone powder did not significantly affect the rate of temperature rise nor the occurrence time of the highest temperature at early ages.
Key words: limestone powder; cement mortar; hydration properties; thermal properties
1 Introduction
Limestone powder (LP) has been increasingly used in blended cements as a partial replacement for ordinary Portland cement (OPC), with typical replacement level ranging between 6% and 20% by mass of OPC [1]. LP is beneficial in not only reducing the cost of concrete and carbon footprint of concrete production, but also improving the workability and durability performance of resulting concrete and concrete structures [2–4]. As a filler material, LP has been reported to reduce the total porosity and delay the initial and final setting time of cement pastes [5–7]. In addition to the filler effects, LP could also affect the hydration reaction of blended binders: the calcium carbonate of LP could interact with the aluminate hydrates formed by the hydration reactions of OPC [1, 8]. Recently, researches on composite limestone cements have been carried out, with a significant focus on self-compacting concrete (SCC) [9–12]. Overall, the main objective of these previous researches was to explore the optimum percentage of LP in blend cements, with the aim of designing a concrete with good mechanical and durability performance as well as low environmental impact. Besides, many researchers studied cementitious hydration reactions and products of complex binders containing LP based on X-ray powder diffraction (XRD) analyses [13, 14]. Especially, cement- low quality limestone powder binary binder [15, 16] and cement-limestone powder-fly ash ternary binder [17, 18] were widely tested and analyzed. Through these researches, it had been reported that LP could speed up the hydration process of complex binder and react with OPC to produce calcium hydrates [19, 20].
With the current trend of increasing use of LP, the changes of thermal properties of concrete containing various contents of LP have become a new concern in engineering, but inadequate attention has been paid to the influence of LP on the thermal performance of concrete. YOSHITAKE et al [21] did some experiments on thermal and mechanical properties of high volume fly ash concrete and presented a method to estimate the adiabatic temperature rise. ZHU [22] studied thermal properties of concrete containing limestone aggregate, but with the focus on the effects of LP as a filler rather than as a supplementary cementitious material. In this work, several concrete mixtures with different replacement proportions of LP for OPC were designed. Some basic thermal characteristics, such as adiabatic temperature rise, thermal conductivity and average specific heat, were tested and obtained. In addition, thermal fields of concrete specimens were simulated using finite element modelling to cast more light onto the influence of LP on the thermal performance of concrete at early ages.
2 Main materials
The OPC used in the study meets the Chinese National Standard (GB 175–2007) [23] that requires:
1) Loss on ignition (LOI) is controlled within 5.0% by mass;
2) Content of SO3 is less than 3.5% by mass;
3) Content of MgO is less than 5.0% by mass.
According to the Chinese National Standard (GB/T 30190–2013) [24], LP used in mix deign conforms to the following three requirements:
1) Content of CaCO3 is larger than 75% by mass;
2) Fineness modulus is less than 15%;
3) Content of water is controlled within 1.0% by mass.
The chemical compositions and physical properties of OPC and LP used are presented in Table 1. Figure 1 shows two images of LP (5 μm and 10 μm) as observed by scanning electron microscope (SEM). The particle size distribution of both OPC and LP, as obtained by laser grain size analyzer, are also given in Fig. 2. It can be seen that LP was approximately one order of magnitude finer than OPC: while LP had particle size of mainly between 0.7 μm and 10.0 μm, OPC’s particles were mostly between 1.0 μm and 100 μm.
3 Experiments
3.1 Mix design
In order to study the hydration properties of CLP binder, a series of mixes with direct replacement level of OPC by LP ranging between 0 and 50% by mass, while keeping the total binder content constant, were designed (Table 2). The content of water and sand were set as 225 g and 1350 g, respectively for all mixes. The water- to-binder ratio (w/b) was thus identical for every mix at 1:2 by mass.
3.2 Test methods
For each mix, mortar specimens with dimensions of 40 mm×40 mm×160 mm were prepared and used to test both compressive strength and flexural strength at different ages. All specimens were cured in environmentally-controlled room with relative humidity of above 90% and temperature of (20±1) °C. Compressive and flexural strengths were tested in accordance with GB/T17671–2005. Besides, the fluidity test was also performed to determine the performance of fresh mortar in accordance with GB/T2149–2005. To investigate hydration properties of CLP binder, hydration heat and the rate of heat evolution were studied. Hydration reaction at very early ages was tested in a 20 mL ampere bottle with the initial hydration temperature of about 20 °C.
Table 1 Chemical compositions (mass fraction) and physical properties of OPC and LP

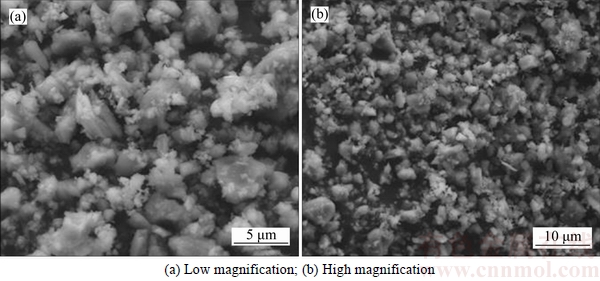
Fig. 1 SEM images of limestone powder:
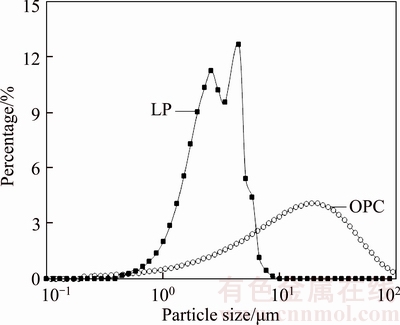
Fig. 2 Particle size distribution of LP and OPC
Table 2 Mix proportion of CLP mortar
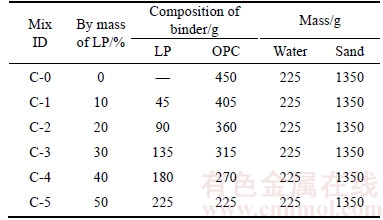
4 Results and discussion
4.1 Physical properties
Scanning electron microscope (SEM) was used to observe the microstructure of CLP mortar before initial setting. In Fig. 3, three SEM images of C-0, C-3 and C-5 (with LP proportion by mass of OPC of 0%, 30% and 50%, respectively) are shown. It can be observed that the higher the proportion of LP, the lower the porosity of fresh mortar, which clearly highlights the pore-filling effect of LP particles.
The test results of fluidity, flexural strength and compressive strength are shown in Fig. 4. Fluidity of fresh CLP mortar increased from 161.2 mm to 193.1 mm as the percentage of LP rose from 0 to 50% by mass of OPC, indicating that LP could be seen as a water reducer in cement-based mix. Figures 4(b) and (c) show that changing the mixtures proportion of LP has a strong influence on the rate of strength development. As shown in the figure, both compressive and flexural strengths decreased gradually with the proportion of LP increasing.
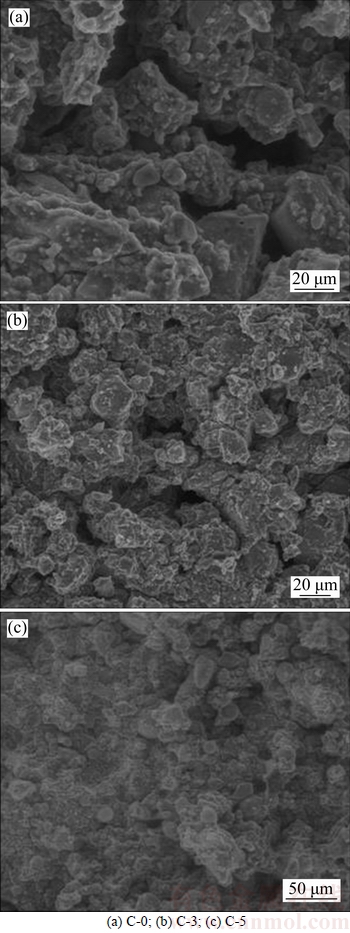
Fig. 3 Scanning electron microscope images of CLP mortar at very early ages:
This suggests the negative influence of increasing replacement level of OPC by LP (on an equal-weight basis) on flexural and compressive strengths of resulting concrete.
Brittleness index, defined as the ratio of compressive strength to flexural strength [25], is an important parameter to evaluate crack resistance capacity of cement materials. Generally, the smaller the brittleness index, the better the crack resistance capacity. Brittleness index of CLP mortar at different ages were calculated and plotted in Fig. 5. It was found that the brittleness index increased over time. Also, increased percentage of LP corresponded to a reduction in the average brittleness index, indicating that LP was beneficial for improving crack resistance capacity of cement-based materials: at the age of 28 d, an increase in percentage of LP from 0 to 50% caused a half reduction in brittleness index from 5.75 to 2.93.
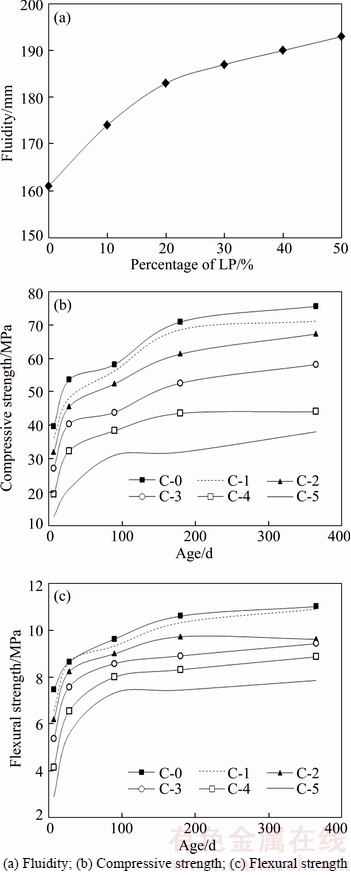
Fig. 4 Physical and mechanical properties of CLP mortar:
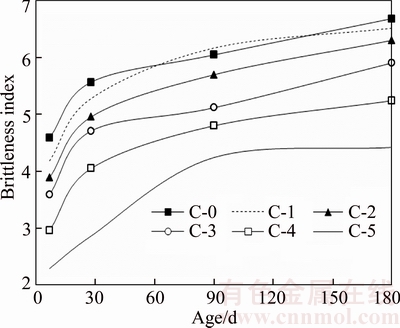
Fig. 5 Brittleness index of CLP mortar
4.2 Contribution rate on strength
To quantitatively analyze the effect of LP and OPC on the strength development of cement-based materials and to assess hydration activity of LP in CLP binder, the concept of specific strength Rsa [26], as defined below, was used:
(1)
where Ra is the absolute value of strength of CLP mortar and q0 is the mass fraction of OPC in CLP binder.
Because the CLP mortar mix C-0 had zero content of LP, it was selected as the reference specimen in the study. The specific strength Rsc of C-0 can be written as
(2)
where Rc is the absolute value of the strength of C-0.
The contribution rate of OPC on strength of CLP mortar is defined as
(3)
Consequently, the contribution rate of LP can be expressed as
(4)
Based on Eqs. (3) and (4), the contribution rates of OPC and LP at different ages were calculated and presented in Fig. 6. Generally, Ph exceeding 100% and Pa becoming negative, indicate that hydration activity of OPC at that moment is stronger than that in the reference specimen C-0. For C-1, C-2 and C-3 specimens (Figs. 6(a), (b) and (c)), the value of Pa were relatively high of between 4.30% and 11.15% after the age of 90 d. For C-4 and C-5 specimens (Figs. 6(d) and (e)), the values of Pa both were negative, while the values of Ph exceeded 100% at the age of 7 d, implying that LP could have promoted the contribution rate of OPC on the strength at early ages.
4.3 Hydration heat and rate of heat evolution
The measured data of hydration heat of C-0, C-3 and C-5, are presented in Fig. 7. It can be observed that the higher the percentage of LP, the lower the recorded heat of hydration: At the age of 72 h, the hydration heat of C-0 was 68.12 J/g higher than that of C-5. Regarding the rate of heat evolution, it decreased rapidly initially before increasing again to peak at the age of around 12 h. After the age of 48 h, the rate of heat evolution tended to stabilize at approximately 1.6 J/(g·h).

Fig. 6 Contribution rates of OPC and LP:
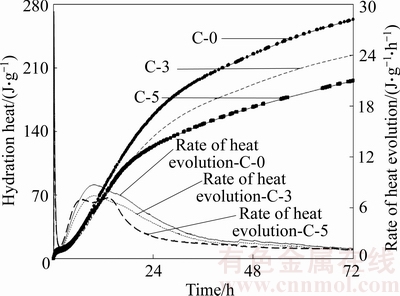
Fig. 7 Hydration heat and rate of heat evolution
Using collected data on hydration heat of mortars with varied contents of OPC and LP, the reduction coefficient k for estimation of the adiabatic temperature rise of CLP mortar can be determined. The adiabatic temperature rise of CLP mortar can be approximately computed by Eq. (5)
(5)
where Q(τ) is the hydration heat of OPC; W is the content of OPC; k is the reduction coefficient; F is the content of LP; c is the average specific heat; Qb(τ) is the hydration heat of CLP binder; Wb is the content of CLP binder.
Based on Eq. (5), the reduction coefficient k can be expressed as Eq. (6). Using the equation and the collected test data of hydration heat of C-0, C-3 and C-5, the reduction coefficient k was estimated at 0.507 and 0.521 for C-3 and C-5, respectively.
(6)
4.4 Thermal analysis
Concrete specimens with different replacement levels of LP for OPC (0, 30% and 50%), were designed and used to test thermal properties of CLP concrete (Table 3). To correspond with CLP mortar tests, the ratio of water to binder (w/b) was still kept at 1:2 by mass. The contents of sand and aggregate were set as 612 kg/m3 and 1268 kg/m3 respectively for all mixes.
Table 3 Mixture compositions of CLP concrete
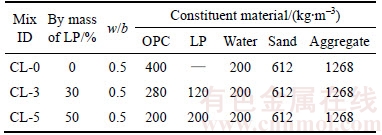
A number of important thermal parameters of concrete were tested and reported in Table 4, including adiabatic temperature rise, which is one of the key parameters, since it directly and significantly affects the thermal field in concrete structures. It is clear from Table 4 that the adiabatic temperature rise of CLP concrete increases rapidly initially, reaching a near-peak value at the age of around 3 d, and subsequently petering out. The adiabatic temperature rise at 3 and 7 d was averaged at 91.4% and 96.7% of that at 28 d. It was also observed that an increase in percentage of LP resulted in a significant decrease in recorded adiabatic temperature rise.
Different from its influence on the adiabatic temperature rise, an increase in percentage of LP brought about only a relatively modest gain in the thermal conductivity, thermal diffusivity and average specific heat.
In order to investigate the influence of these thermal parameters on temperature rise of concrete, a finite element model using ANSYS was developed to simulate the temperature field of a 6 m×4 m×4 m concrete block [22, 27]. The casting temperature was assumed at round 12 °C, the block was assumed to be perfectly insulated. The node P at the center of the block was chosen as the feature node to assess the temperature history of the concrete block. The governing equation of heat conduction can be expressed as [22]:
(7)
where T is the temperature of concrete; τ is the age of concrete; a is the thermal diffusivity; c is the average specific heat; ρ is the density and Q is the hydration heat.
The equation used to simulate the adiabatic temperature rise can be expressed as [22]:
(8)
where θ0 is the final adiabatic temperature rise; both i and j are model constants (see Table 5).
Figure 9 shows the temperature history of the feature node of P at the block’s center. It is clear that the temperature at the center location P of all three concrete blocks made of CL-0, CL-3 and CL-5 rises rapidly to near-peak values at around two to three days, after which the temperature increase becomes very modest.
The temperature fields over the cross-sections through the centre P of the concrete blocks (Fig. 8) at the age of 2.5 d were captured and illustrated in Fig. 10. Due to the insulated nature of the blocks and the modest temperature rise after the first two to three days, the temperature fields were quite uniformed, with the difference between the highest and lowest temperatures of less than 0.5%. Again, the peak temperature was the lowest for the case of CL-5, followed by that of CL-3 block, which was in turn lower than corresponding value of CL-0 block.
Table 4 Thermal properties of CLP concrete

Table 5 Parameters of adiabatic temperature rise
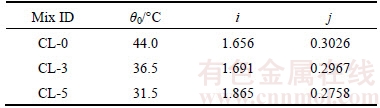
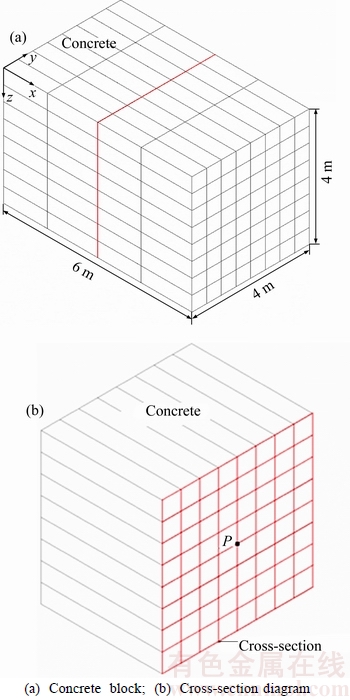
Fig. 8 FEM model:
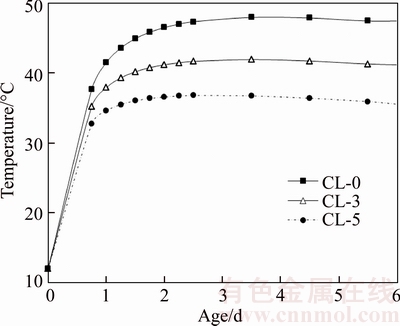
Fig. 9 Temperature history of concrete block at node P
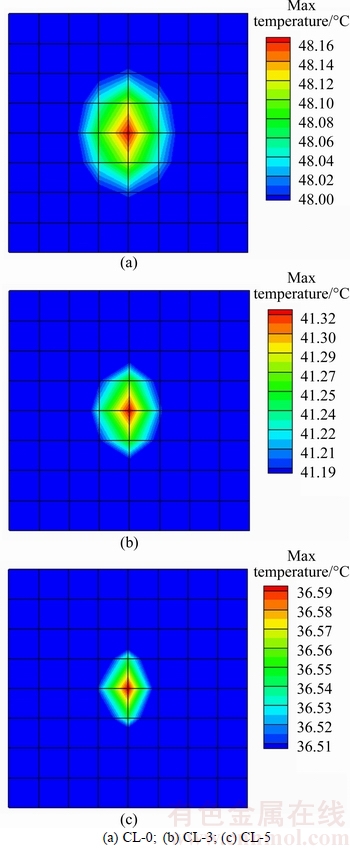
Fig. 10 Simulated temperature fields at about 2.5 day:
5 Conclusions
1) An increased replacement level of limestone powder, while leading to improved flowability and crack resistance capacity, caused a reduction in the compressive strength and flexural strength. If the replacement level was lower than 30%, limestone powder contributed to the strength development of mortar after the age of 90 d. Once the level exceeded 40% or 50%, it had negative influence on the strength development.
2) The total hydration heat was found to decrease rapidly with increasing percentage of limestone powder. However, the influence of limestone powder on the rate of heat evolution was small at very early ages. For engineering applications, adiabatic temperature rise of cement limestone powder concrete could be estimated using Eq. (5). The reduction coefficient (k) of limestone powder on the hydration heat was determined at approximate 0.51.
3) As the percentage of limestone powder increases from 0 to 50% by mass of ordinary Portland cement, the adiabatic temperature rise of cement-limestone powder concrete reduced significantly, while other thermal properties (including thermal conductivity, thermal diffusivity and average specific heat) experienced only a relatively modest gain.
4) Simulation results from thermal analysis based on finite element method indicated that inclusion of limestone powder did not significantly affect the rate of temperature rise nor the occurrence time at the highest temperature at early ages. For the binary binder (w/b= 0.5) containing ordinary Portland cement and limestone powder, the highest temperature may drop by about 2.3 °C as the replacement percentage of limestone powder increases by 10%.
References
[1] MEDDAH M S, LMBACHIYA M C, DHIR R K. Potential use of binary and composite limestone cements in concrete production [J]. Construction and Building Materials, 2014, 58: 193–205.
[2] BENTZ D P, ARDANI A, BARRETT T, JONES S Z, LOOTENS D, PELTZ M A, SATO T, STUTZMAN P E, TANESI J, WEISS W J. Multi-scale investigation of the performance of limestone in concrete [J].Construction and Building Materials,2015, 75: 1–10.
[3] YE G, LIU, X, DE SCHUTTER G, POPPE AM, TAERWE L. Influence of limestone powder used as filler in SCC on hydration and microstructure of cement pastes [J]. Cement and Concrete Composites, 2007, 29(2): 94–102.
[4] RAMEZANIANPOUR A A, GHIASVAND E, NICKSERESHT I, MAHDIKHANI M, MOODI F. Influence of various amounts of limestone powder on performance of Portland limestone cement concretes [J].Cement and Concrete Composites,2009, 31(10): 715720.
[5] CELIK K, JACKSON M D, MANCIO M, MERAL C, EMWAS A H, MEHTA P K, MONTEIRO P J M. High-volume natural volcanic pozzolan and limestone powder as partial replacements for portland cement in self-compacting and sustainable concrete [J].Cement and Concrete Composites,2014, 45: 136–147.
[6] CELIK K, MERAL C, GURSEL A P, MEHTA P K, HORVATH A, MONTEIRO P J. Mechanical properties, durability, and life-cycle assessment of self-consolidating concrete mixtures made with blended Portland cements containing fly ash and limestone powder [J].Cement and Concrete Composites, 2015, 56: 59–72.
[7] DE WEERDT K, KJELLSEN K O, SELLEVOLD E, JUSTNES H. Synergy between fly ash and limestone powder in ternary cements [J].Cement and Concrete Composites,2011, 33(1): 30–38.
[8] MARTIN L H, WINNEFELD F, M
LLER C J, LOTHENBACH B. Contribution of limestone to the hydration of calcium sulfoaluminate cement [J].Cement and Concrete Composites,2015, 62: 204–211.
[9] SCH
LER A, LOTHENBACH B, WINNEFELD F, ZAJAC M. Hydration of quaternary Portland cement blends containing blast-furnace slag, siliceous fly ash and limestone powder [J].Cement and Concrete Composites,2015, 55: 374–382.
[10] DE WEERDT K, HAHA M B, LE SAOUT G, KJELLSEN K O, JUSTNES H, LOTHENBACH B. Hydration mechanisms of ternary Portland cements containing limestone powder and fly ash [J].Cement and Concrete Research,2011, 41(3): 279–291.
[11] LOTHENBACH B, LE SAOUT G, GALLUCCI E, SCRIVENER, K. Influence of limestone on the hydration of Portland cements [J].Cement and Concrete Research,2008, 38(6): 848–860.
[12] YOSHITAKE I, WONG H, ISHIDA T, NASSIF A Y. Thermal stress of high volume fly-ash (HVFA) concrete made with limestone aggregate [J].Construction and Building Materials,2014, 71: 216–225.
[13] DE WEERDT K, KJELLSEN K O, SELLEVOLD E, JUSTNES H. Synergy between fly ash and limestone powder in ternary cements [J].Cement and concrete composites,2011, 33(1): 30–38.
[14] MARTIN L H, WINNEFELD F, M
LLER C J, LOTHENBACH B. Contribution of limestone to the hydration of calcium sulfoaluminate cement [J].Cement and Concrete Composites,2015, 62: 204–211.
[15] JAAFAR M S, BAYAGOOB K H, NOORZAEI J, THANOON W A. Development of finite element computer code for thermal analysis of roller compacted concrete dams [J].Advances in Engineering Software,2007, 38(11): 886–895.
[16] YAN Pei-yu, MI Gui-dong, WANG Qiang. A comparison of early hydration properties of cement-steel slag binder and cement-limestone powder binder [J]. Journal of Thermal Analysis and Calorimetry, 2014, 115(1): 193–200.
[17] SCHOLER A, LOTHENBACH B, WINNEFELD F, ZAJAC M. Hydration of quaternary Portland cement blends containing blast-furnace slag, siliceous fly ash and limestone powder [J]. Cement & Concrete Composites, 2015, 55: 374–382.
[18] DE WEERDT K, HAHA M B, LE SAOUT G, KJELLSEN K O, JUSTNES H. Hydration mechanisms of ternary Portland cements containing limestone powder and fly ash [J]. Cement and Concrete Research, 2011, 41(3): 279–291.
[19] LIU Shu-hua, WANG Lu. Influence of limestone powder on hydration properties of complex binders [J]. Materials Research Innovations, 2014, 18 (S2): 186–190.
[20] LOTHENBACH B, SAOUT L G, GALLUCCI E, SCRIVENER K. Influence of limestone on the hydration of Portland cements [J]. Cement and Concrete Research, 2008, 38(6): 848–860.
[21] YOSHITAKE I, WONG H, ISHIDA T, NASSIF A Y. Thermal stress of high volume fly-ash (HVFA) concrete made with limestone aggregate [J]. Construction and Building Materials, 2014, 71: 216–225.
[22] ZHU Bo-fang. Thermal stress and temperature control in mass concrete [M]. Beijing: China Water & Power Press, 1999. (in Chinese)
[23] GB 175–2007. Common Portland cement [S]. (in Chinese)
[24] GB/T 30190–2013. Concrete with ground limestone [S]. (in Chinese)
[25] RINGOT E, BASCOUL A. About the analysis of micro-cracking in concrete [J]. Cement and Concrete Composites, 2001, 23(2): 261–266.
[26] PU Xin-cheng. Super-high strength high performance concrete [M]. USA, Taylor & Francis: CRC Press, 2012.
[27] JAAFAR M S, BAYGOOB K H, NOORZAEI J, THANOON W A. Development of finite computer code for thermal analysis of roller compacted concrete dams [J]. Advances in Engineering Software, 2007, 38(11): 886–895.
(Edited by HE Yun-bin)
Cite this article as: ZHOU Wei, LI Liang, LIU Shu-hua, VINH T.N. Dao, LIU Xing-hong. Hydration properties and thermal analysis of cement-based materials containing limestone powder [J]. Journal of Central South University, 2017, 24(12): 2932–2939. DOI:https://doi.org/10.1007/s11771-017-3707-2.
Foundation item: Project(51579192) supported by the National Natural Science Foundation of China; Project(2013BC0359001) supported by the National Basic Research Program of China; Project(201506270058) supported by China Scholarship Council
Received date: 2016-03-08; Accepted date: 2016-05-12
Corresponding author: LI Liang, PhD candidate; Tel: +61–0452566516; E-mail: liliangrun@whu.edu.cn