文章编号: 1004-0609(2005)05-0813-04
铜在富FeO熔渣中的氧化溶解行为
李长荣, 洪 新, 郑少波, 蒋国昌
(上海大学 材料科学与工程学院, 上海 200072)
摘 要: 在1873K条件下对铜在富FeO熔渣中的氧化溶解行为进行了研究。 结果表明: 铜氧化物在富FeO熔渣中以Cu2O的形式存在; 熔渣中CaO的含量将对铜的氧化溶解产生影响, 随着渣中CaO含量的增加, 熔渣中的铜含量逐渐下降, 但在不同温度下, 这种影响的作用各不相同; 当温度较高时, 渣中CaO含量对铜的氧化溶解影响较大, 且随着温度的降低, 其影响作用明显变缓; 反应体系的氧分压对铜的氧化溶解影响较大, 在熔渣中γ(CuO0.5)不变的情况下, 铜氧化物的溶解与体系氧分压的四分之一次方之间呈正线性关系。
关键词: 铜氧化物; 富FeO熔渣; 溶解行为 中图分类号: TF111; X705
文献标识码: A
Oxidation dissolution behavior of copper in FeO-rich slag
LI Chang-rong, HONG Xin, ZHENG Shao-bo, JIANG Guo-chang
(School of Materials Science and Engineering, Shanghai University,Shanghai 200072, China)
Abstract: The oxidation dissolution behavior of copper in the FeO-rich slag at 1873K was investigated. The results show that the copper oxidate is Cu2O. The CaO content in slag has influence on the copper oxidation dissolution in the FeO-rich slag. The copper content in slag decreases gradually with the increase of CaO content in the slag. But the influence is different under different temperatures. The influence of CaO content on the copper content in slag at higher temperature is relative obvious and becomes plain at lower temperature. The partial oxygen pressure of reaction system has great influence on the copper oxidation dissolution in the FeO-rich slag. The curve of copper oxidation dissolution in slag and the quarter root of the partial oxygen pressure is positive linearity.
Key words: copper oxide; FeO-rich slag; dissolution behavior
由于铜被广泛地应用于各种机械以及电子产品中, 因而在金属回收利用过程中就不可避免地混入到废钢铜中, 尽管人们采用了许多分离措施, 仍然无法阻止废钢中铜含量的上升和蓄积[1-3]。 由于铜会增加钢材的热脆倾向, 恶化锻轧、 热轧性能, 因此废钢中铜含量的蓄积和上升已经成为提高废钢循环利用率的主要障碍[1, 4]。 各国学者对钢水脱铜技术进行了广泛地研究, 但到目前为止, 还没有一种令人满意的实用脱除技术。 文献[5]提出了一种先渣化再还原的利用含铜量较高的劣质废钢的新思路, 这一方法有望实现铁与多种残余元素的同时分离, 并将废钢冶炼成纯净钢。 铜在富FeO熔渣中的溶解行为对含铜铁溶液的渣化过程有着重要影响, 是研究其在渣金间分配规律的基础。
许多学者曾对铜在富FeO熔渣中的溶解行为进行过研究, 但已有的研究主要是针对铜冶金过程中的行为[6-12], 研究所涉及的温度较低, 一般为1273~1573K, 且获得的数据较分散, 也曾有学者对这些数据进行过优化[13]。 对于含铜废钢溶液的渣化过程来说, 主要温度为1873K左右[5, 14], 鲜见有铜在此温度范围内的熔渣氧化溶解行为的报道, 本文作者对铜在富FeO熔渣中的氧化溶解行为进行了研究。
1 实验
实验所用的高温实验炉加热元件选用d9mm×200mm×400mm硅钼棒6支, 串连。 硅钼棒由炉顶插入炉膛, 顶端接线, 外置防护罩。 测温采用双铂铑热电偶(B分度)2支, 炉子的控温精度为不大于±1K。 水冷腔焊于炉体底部, 设有进出水管及一个进气管, 进气管用于向炉管内通保护气体。
首先将经过预熔的渣粒10g加入到高纯氧化镁坩埚内, 坩埚外径为d22mm, 内径为20mm, 厚度为50mm, 外套石墨坩埚。 将坩埚放入高温炉的恒温区域, 随炉一起升温, 升温速率小于5K/min。 升温至石墨坩埚发红时, 通入氩气保护, 氩气流量0.1m3/h。 至1873K时, 恒温30min后, 认为坩埚内熔渣温度已均匀, 然后将10g颗粒状金属纯铜加入坩埚中, 金属铜的熔点较低, 而且金属量也较少, 很快就会熔化, 可以认为加入时间就是反应的开始时间。 恒温至预定时间4h后, 将坩埚取出, 急冷, 熔渣经过处理后, 送化验室化验。
2 结果与分析
在对熔渣成分进行成分分析前, 对其进行了显微观察, 发现有许多金属相存在于熔渣中。 这些金属相的存在会使熔渣的分析结果出现偏差。 因此, 将所获得的熔渣试样破碎后, 研磨并筛分, 仔细分离渣相与金属相, 严格处理后的熔渣成分采用ICP等离子发射光谱法进行分析, 分析结果如表1所列(分析讨论中所用的数据排除了金属相的干扰)。
表1 与金属铜溶液平衡氧化铁熔渣的化学分析结果
Table 1 Chemical analysis results of iron oxide slag equilibrium with
copper solution (Mass fraction, %)
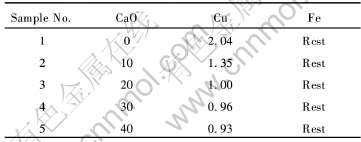
铜在其氧化物中可以表现为多价态金属离子, 且铜的氧化物有CuO和Cu2O两种。 CuO 是碱性氧化物, 小于1273K的温度下稳定存在, 大于1273K时发生分解; Cu2O 是高温下稳定的氧化物, 在大气中加热到2473K以上时, 分解成铜并析出氧。
采用日本理学电机生产的D/max-rc X射线衍射仪, 对氧化铁熔渣进行了X射线衍射分析, 扫描强度为40kV、 100mA, 扫描速度为4(°)/min。 熔渣的衍射结果表明: 熔渣中的铜是以Cu2O形式存在。
由X射线衍射分析结果可知, 铜在熔渣中的存在状态是Cu2O。 尽管铜还有可能以CuO氧化物的形态存在于熔渣中, 但许多研究表明: 体系氧分压为10-7~102Pa, 假设熔渣中的铜都以Cu+形式存在的, 熔渣中的Cu2+是可以忽略的[13]。 因此, 对于铜在熔渣中的溶解可以用下式予以讨论[16]:
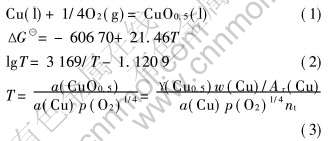
式中 nt是100g熔渣中成分的摩尔总数, 其中的氧化物均用单金属表示, 如FeO1.5或CuO0.5等; Ar(Cu)为铜的相对原子质量。
这种表示方法对于讨论体系中摩尔数的影响较为方便, 基本可以认为nt是一个常数。 比如, 在本体系的研究中, 熔渣中成分变化较大时, nt的值总为1.41~1.49。 金属铜的a(Cu)=1, Ar(Cu)=63.55, 假设本体系的nt=1.45, 则可以从上式中推导得出:
w(Cu)=92.15Tp(O2)1/4/γ(CuO0.5)(4)
从表1的实验结果可以看出, 在1873K温度条件下, 与金属铜溶液平衡的纯氧化铁熔渣中的铜含量为2.04%。 图1所示为熔渣中CaO含量与Cu含量的关系。 由图1可看出, 熔渣成分对铜在熔渣中的溶解有重要影响, 渣中铜含量随着熔渣中CaO含量的增加逐渐减小(即铜在熔渣中的溶解随着CaO含量的增加而逐渐减小)。
由式(4)可以得出:
γ(CuO0.5)=92.15Tp(O2)1/4/w(Cu)(5)
在本研究的条件下, 经测量体系的氧分压p(O2)=10-3Pa。 由式(3)计算, 得出1873K温度下, 反应的T=3.724, 将实验结果代入上式计算, 可以得出相应条件下的γ(CuO0.5)。 如图2所示为γ(CuO0.5)与熔渣中CaO含量的关系。
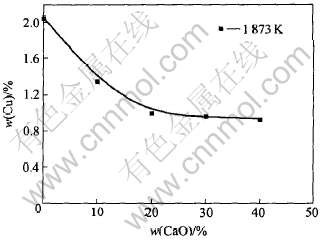
图1 熔渣中CaO含量与Cu含量的关系
Fig.1 Relation between CaO content and content of Cu in slag
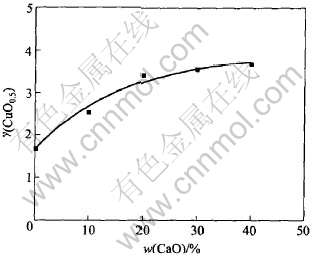
图2 γ(CuO0.5)与熔渣中CaO含量的关系
Fig.2 Relation between γ(CuO0.5) and content of CaO in slag
拟合曲线得出γ(CuO0.5)与熔渣中CaO含量之间的关系:
γ(CuO0.5)=3.95-
2.31exp(-w(CaO)/16.63)(6)
由图2和计算式可知, 氧化铁熔渣中CuO0.5的活度系数随熔渣中CaO含量的增加而逐渐变大, 但其增长趋势会随着CaO含量的增大而逐渐变缓。
由式(4)可看出, 铜在氧化铁熔渣中的溶解受温度(T), 氧分压(p)和熔渣的(γ(CuO0.5))的影响。 在温度和氧分压一定的情况下, 则取决于熔渣的成分。
如果假设熔渣中γ(CuO0.5)是一个常数, 则可知熔渣中铜的溶解与体系氧分压的四分之一次方之间呈线性关系。 假设γ(CuO0.5)是一个常数, 根据式(4)可计算出熔渣中的铜含量与体系氧分压之间的关系。 分别计算不同γ(CuO0.5)时熔渣的铜含量, 结果如图3所示。
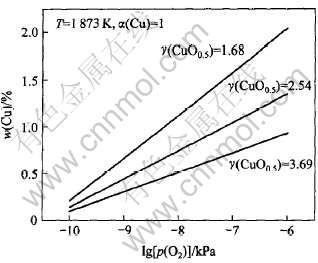
图3 1873K温度下氧分压与熔渣中Cu含量的关系
Fig.3 Relation between partial pressure of
oxygen and content of Cu in slag at 1873K
关于氧分压对铜氧化物溶解的影响, 铜冶金中的研究多数在10-7Pa量级以上, 低于该氧分压的情况较为少见。 但氧分压高于1Pa时, 由Cu-O系状态图可知[16, 17], 在铜冶炼或炼钢的温度范围内, 铜会被完全氧化成氧化物。
图4所示为不同温度条件下熔渣中CaO含量对Cu含量的影响, 其中1873K的曲线是根据本研究结果绘制的, 而1573K和1523K是根据文献[17]中数据绘制的。 由图4可见, 在不同温度下, CaO含量对Cu含量的影响有所不同, 但其影响趋势都是一致的, 随着熔渣中CaO 含量的增加, 铜的氧化溶解逐渐降低。 由图也可以看出, 温度较高时, CaO含量的影响较大, 而在温度较低时, 其影响明显变缓。
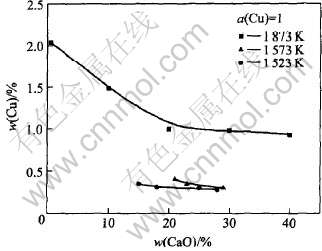
图4 不同温度下熔渣中CaO含量与Cu含量的关系
Fig.4 Relation between content of Cu and
content of CaO at different temperature
3 结论
1) 铜氧化物在富FeO熔渣中是以Cu2O的形式存在的。
2) 1873K温度条件下, γ(CuO0.5)与熔渣中CaO含量之间的关系为
γ(CuO0.5)=3.95-
2.31exp(-w(CaO)/16.63)
3) 假设熔渣中γ(CuO0.5)是一个常数, 则熔渣中铜的氧化溶解与体系氧分压的四分之一次方之间呈正线性关系。
4) 熔渣中CaO含量对铜的氧化溶解是有影响的, 随着CaO含量的增加, 熔渣中的铜含量下降, CaO含量在高温时的影响大于低温时的影响。
REFERENCES
[1]Iwase M. Removal of copper from ferrous scrap[J]. Denki-Seiko(Electric Furnace Steel), 1995, 66(1): 21-26.
[2]Savov L, Janke D. Recycling of scrap in steelmaking in view of the tramp element problem[J]. Metall, 1998, 52(6): 374-383.
[3]Marique C. Scrap recycling and production of high quality steel grades in Europe[J]. La Revue de Metallugie-CIT, 1996(11): 1377-1385.
[4]Kakudate K, Adachi Y, Suzuki T. A quantitative macro model of steel scrap recycling considering copper contamination for the sustainable society[J]. Tetsu-to Hagane, 2000, 86(12): 837-843.
[5]徐匡迪, 蒋国昌, 洪新, 等. 从废钢冶炼纯净钢新流程的讨论[J]. 金属学报, 2001, 37(4): 395-399.
XU Kuang-di, JIANG Guo-chang, HONG Xin, et al. Discussion on new process making clean steel from scrap[J]. Acta Metallurgica Sinica, 2001, 37(4): 395-399.
[6]Takeda Y. Phase diagram of CaO-FeO-Cu2O slag under copper saturation[A]. Proceedings of Yazawa International Symposium: Materials Processing Fundamentals and New Technologies, 2003, 1: 211-225.
[7]Kim H G, Sohn H Y. Effects of CaO, Al2O3 and MgO additions on the copper solubility, ferric/ferrous ratio and minor-element behavior of iron-silicate slags[J]. Metallurgical and Materials Transactions B, 1998, 29B (3): 583-590.
[8]Hino M, Yazawa A. 炉渣中氧化铜的溶解平衡[A]. 1995年铜国际会议论文集[C]. 北京: 冶金工业出版社, 1998, 2: 408-419.
Hino M, Yazawa A. The dissolve equilibrium of copper oxide in slag[A]. Proceedings of 1995 Copper International Conference[C]. Beijing: Metallurgical Industry Press, 1998, 2: 408-419.
[9]Acuna C, Zaniga J. 使用石灰溶剂吹炼高品位铜锍的试验研究[A]. 1995年铜国际会议论文集[C]. 北京: 冶金工业出版社, 1998. 335-347.
Acuna C, Zaniga J. Investigation on blowing high-grade copper matte with lime flux[A]. Proceedings of 1995 Copper International Conference[C]. Beijing: Metallurgical Industry Press, 1998. 335-347.
[10]Peddada S R, Gaskell D R. The activity of CuO0.5 along the air isobars in the systems Cu-O-SiO2 and Cu-O-Ca at 1300℃[J]. Metallurgical Transactions B, 1993, 24B(1): 59-62.
[11]Yazawa A, Takeda Y, Waseda Y. Thermodynamic properties and structure of ferrite slags and their process implications[J]. Canadian Metallurgical Quarterly, 1981, 20(2): 129-134.
[12]Toguri J M, Santander N H. The solubility of copper in fayalite slag at 1300℃[J]. Canadian Metallurgical Quarterly, 1969, 8: 168-171.
[13]Degterov S A, Pelton A D. A thermodynamic database for copper smelting and converting[J]. Metallurgical and Materials Transactions B, 1999, 30B(4): 661-669.
[14]LI Chang-rong, HONG Xin, ZHENG Shao-bo, et al. Distribution behavior of elements copper and tin between FeO-rich slag and iron solution[J]. Trans Nonferrous Met Soc China, 2004, 14(1): 194-197.
[15]万谷志郎, 著. 钢铁冶炼[M]. 李宏, 译. 北京: 冶金工业出版社, 2001. 248-265.
Ban-Ya S. Ironmaking and steelmaking[M]. LI Hong, transl. Beijing: Metallurgical Industry Press, 2001. 248-265.
[16]Yazawa A, Takeda Y. Equilibrium relations between liquid copper and calcium ferrite slag[J]. Transactions of the Japan Institute of Metals, 1982, 23(6): 328-333.
[17]刘纯鹏. 铜冶金物理化学[M]. 上海: 上海科学技术出版社, 1990. 625-629.
LIU Chun-peng. Metallurgical Physical Chemistry of Copper[M]. Shanghai: Shanghai Science and Technology Press, 1990. 625-629.
收稿日期: 2004-09-23; 修订日期: 2005-01-31
作者简介: 李长荣, (1963-), 男, 副教授, 博士.
通讯作者: 李长荣; 电话:021-28203563; E-mail: cr263@163.com
(编辑李艳红)