Fabrication and mechanical properties of FeAl/TiC composites
LIU Feng-xiao(刘峰晓), LIU Yong(刘 咏), HUANG Bai-yun(黄伯云),ZHOU Ke-chao(周科朝), HE Yue-hui(贺跃辉)
(State Key Laboratory of Powder Metallurgy, Central South University, Changsha 410083, China)
Abstract: FeAl/TiC composites were fabricated by reactive hot pressing blended elemental powders. The effects of TiC content, composition of the binder phase and Ni alloying on the densification process and mechanical properties of the composites were studied. The results show that the densities of the composites decrease with the increase of TiC content. Closely related with their porosities and flaw densities, the hardness and bend strength of the composites show peak values with the increase of TiC content. Higher content of Al in the binder phase was beneficial to densification, however it deteriorates the mechanical properties of the composites. The addition of Ni significantly improves the densities of the composites by enhancing matter transfer in the binder phase. By alloying with Ni, the mechanical properties of the composites are greatly improved due to the increase of the density, together with solid solution-strengthening the binder phase and promoting ductile fracture of FeAl.
Key words: FeAl/TiC composites; TiC content; binder composition; Ni alloying; densification process CLC number: TG148
Document code: A
1 INTRODUCTION
Over the past few decades, considerable investigations have been carried out to identify alternative binders for cermets in order to improve their mechanical properties and also to overcome certain shortcomings, such as high cost and density, low oxidation and corrosion resistance, and environmental toxicity[1, 2]. Iron aluminides are of particular interest due to their low cost and density, high specific strength, environmental-friendliness and excellent oxidation and corrosion resistance[3]. Preliminary results show that iron aluminides are thermodynamically compatible with such ceramics as carbides and borides in both solid and molten states, with favorable wettability and chemical stability[4]. Thus the fabrication of iron aluminide-ceramic composite is expected to provide a unique combination of high strength and toughness, coupled with high wear, corrosion and oxidation resistance.
When wettability and chemical stability are considered, FeAl/TiC is an ideal composites system. FeAl/TiC composites can be processed by liquid phase sintering[5], melt infiltration[6, 7] and hot pressing[8-10]. Because of the limited solubility of TiC in FeAl, it is hard to realize full densification when TiC content is high. This can be improved by exerting external pressure or adding alloy elements. So reactive hot pressing is utilized as the fabrication method in this work. And the effects of composite composition and Ni alloying on the densification process and mechanical properties are studied.
2 EXPERIMENTAL
Gas reduced Fe powder, N2 atomized Al powder, TiC powder and Ni powder with mean particle sizes of 54.57μm, 23.21μm, 12.84μm and 12.44μm respectively, were blended according to the nominal compositions listed in Table 1. The mixtures were cold pressed at 500MPa into compacts with dimensions of d25mm×35mm. Stearic acid(1%-3%) was used as binder in order to improve the compressibility of the mixed powders with high content of TiC. The compacts were then hot pressed in graphite die at 1300℃, 30MPa for 1h under the protection of Ar atmosphere. The hot pressed samples were cut, polished and examined with scanning electron microscope(SEM). The densities of the composites were measured by the Archimedes immersion technique and Rockwell hardness(HRA) of the composites was also tested. The phase constitution of the composites was determined by XRD. Specimens for bend test were machined and ground into bars of 6mm×6mm×25mm and the fracture surfaces were observed with SEM.
Table 1 Compositions of FeAl/TiC composites(volume fraction, %)
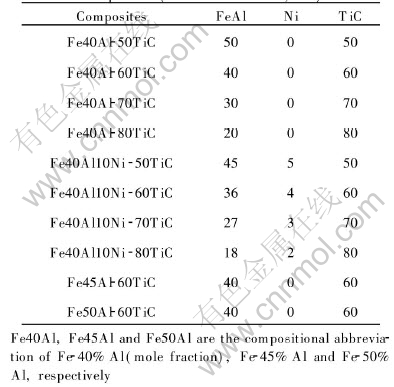
3 RESULTS AND DISCUSSION
3.1 Effect of TiC content on properties of FeAl/TiC composites The curves of the density and relative density versus the TiC content are shown in Fig.1. It can be seen that the densities and relative densities of the composites drop with the increase of TiC content. This indicates that the densification process is slowed by increasing the TiC volume fraction.
Fig.2 shows the SEM images of Fe40Al-50%TiC and Fe40Al-60%TiC. It can be seen that the microstructures of the composites are mainly composed of grey irregular-shaped TiC, white FeAl and black porosities.
When heated to the melting point of Al, the blended elemental Fe, Al powders react intensively to form intermetallics, resulting in crack of the compact, which can be solved by hot pressing. During hot pressing, the densification of the powder compacts can be divided into two parts: one is the densification of FeAl phase by viscous flow, the other is the reorientation of TiC particles to be closely packed with the flow of FeAl phase[11]. When the TiC content is low, it is easy to achieve densification by large amount of FeAl filling into the pores around TiC particles. However, with the increase of TiC content, the solid-solid contacts of TiC particles increase and the kinetics of rear-
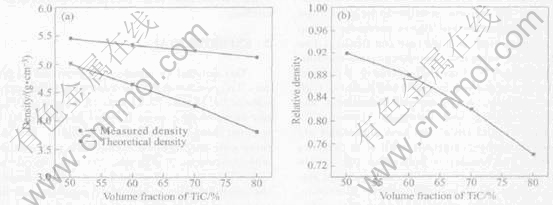
Fig.1 Density(a) and relative density(b) of composites vs TiC volume fraction
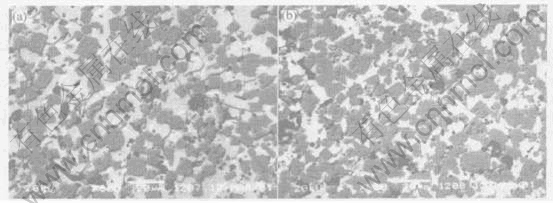
Fig.2 SEM images of Fe40Al-50%TiC(a) and Fe40Al-60%TiC(b)
rangement is slowed by the increasing contacts. And the strength of the TiC skeleton is high enough to resist further deformation. So high density can only be obtained upon rearrangement of the particles aided by solution-reprecipitation reaction. Significant solution-reprecipitation reaction depends on large solubility of TiC in molten FeAl. Due to the limited solubility of TiC in liquid FeAl compared with that of TiC in molten Ni[6], it is hard for considerable solution-reprecipitation reaction to take place. So the densities of the composites decrease with the increase of TiC content.
Fig.3 shows the hardness and bend strength of FeAl/TiC composites versus TiC volume fraction. It is clear that the hardness rises with the increase of TiC content at first, and then drops. A peak value shows at 70%TiC(volume fraction). The bend strength presents the similar trend and a peak value appears at 60%TiC. As hard phase, the increase of TiC content enhances the hardness of the composites. However, the increase of the TiC content can also cause a drop of density. With the further increase of TiC content, the hardness drops quickly due to a more porous microstructure. And with the increase of TiC content, flaws such as pores increase. They deteriorate the mechanical properties of the composites. Fig.4 shows the fracture surfaces of some FeAl/TiC composites after the bend test. There is a mixed fracture mode, typical cleavage fracture or debonding of FeAl/TiC interface, together with ductile fracture of the fine FeAl ligament.
3.2 Effect of binder composition on properties of FeAl/TiC composites
With Al content in the binder phase increasing from 40% (mole fraction) to 45% and 50%, the relative density of the FeAl-60%TiC composite increases from 88% to 92%, and then drops to 89%. According to the FeAl phase diagram, the melting point of FeAl decreases with the increase of Al content[10]. So when hot pressing at the same temperature, the degree of superheat increases with higher Al content. And this is beneficial to the homogenization and densification process. The microstructures of FeAl/TiC composites with different binder composition are shown in Fig.5. It can be seen that the microstructure becomes homogenous with more Al in the binder phase. At the same time, pores increase with the increase of
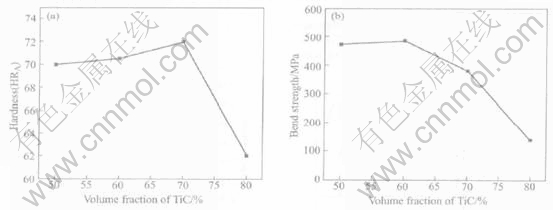
Fig.3 Hardness(a) and bend strength(b) of composites vs TiC volume fraction
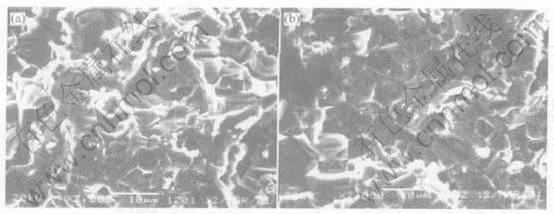
Fig.4 Fractographs of Fe40Al-50%TiC(a) and Fe40Al-60%TiC(b) after bend test
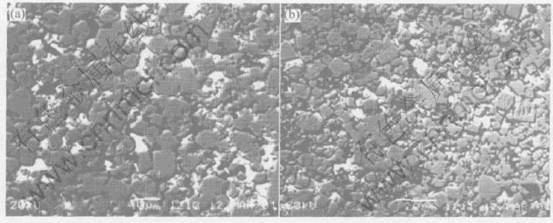
Fig.5 SEM images of Fe45Al-60%TiC(a) and Fe50Al-60%TiC(b)
Al content. Also more thermal vacancies are prone to form in Al-rich FeAl[12, 13]. These degrade the mechanical properties of the composites. The bend strength drops from 486MPa to 457MPa and then to 346MPa, with Al content increasing from 40%(mole fraction) to 45%, and to 50%.
3.3 Effect of Ni alloying on properties of FeAl/TiC composites
Some of the phase compositions of the composites are shown in Fig.6. No new phases are present except for FeAl and TiC in all the composites. This is consistent with the thermodynamic compatibility between FeAl and TiC. And the existence of Ni is mainly in the form of solid solution.
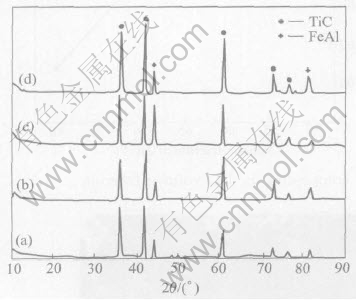
Fig.6 Phase compositions of FeAl-50%TiC(a), FeAl-70%TiC(b), FeAl10Ni-50%TiC(c), FeAl10Ni-70%TiC(d)
Fig.7 shows the density and relative density of FeAl/TiC composites with and without Ni addition. It is obvious that the density and relative density of the composites are greatly improved, es-pecially when the TiC content is high. In Ni-
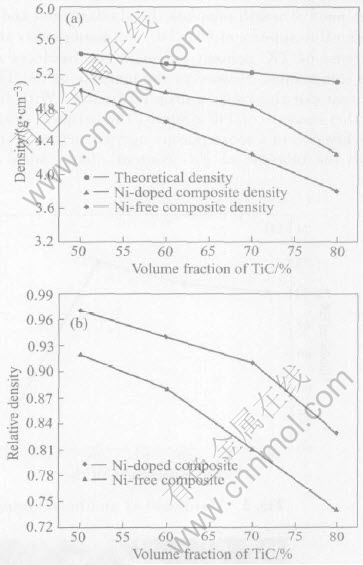
Fig.7 Density(a) and relative density(b) of Ni-doped and Ni-free composites vs TiC volume fraction
doped FeAl, the solubility of Ti can be increased from 2%(mole fraction) to 6%, compared with that in pure FeAl. It is unclear why this happens. The possible reason is that the addition of Ni phase enhances the formation of the β(B2: (Ni, Fe)(Al, Ti)) phase (hard to take apart from FeAl by XRD)[14]. And the diffusivity of elements in FeAl at 1300℃ is very high. The increased solubility and diffusivity of Ti in FeAl promote the matter transfer during the densification process. So the addition of Ni improves the composite density.
The hardness and bend strength of FeAl/TiC composite with and without Ni versus TiC volume fraction are shown in Fig.8. It is clear that the addition of Ni greatly improves these two properties. This is mainly due to the increase of density with the addition of Ni. Furthermore, by occupying Fe sites, Ni atoms change the interaction between dislocation and solid solution atoms through electric and magnetic effect[15]. This results in remarkable solid solution strengthening. Savage et al[15] studied the influence of adding Ni on hardness and yield strength of FeAl. It was found that the hardness of FeAl could be increased from HV273 to HV370 and the solid solution strengthening effect could even reach 55MPa by adding 1%Ni(mole fraction). Also, alloying elements enhance ductile fracture in FeAl phase. Subramanian et al[7] found that sufficiently thin(〈2μm) FeAl ligaments tend to fracture in a ductile manner, which is attributed to the limited dislocation pile-up distance available for very thin ligaments. And the brittle-ductile transition size is controlled by alloying and/or heat
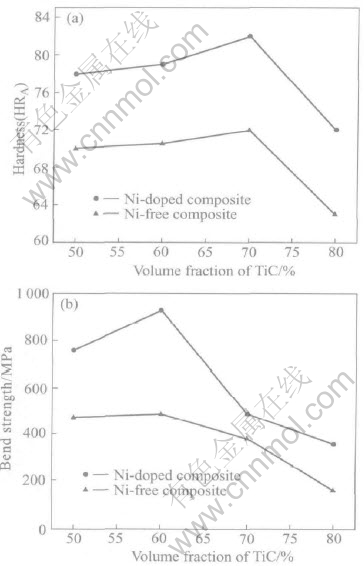
Fig.8 Hardness(a) and bend strength(b) of Ni-doped and Ni-free composites vs TiC volume fraction
treatment. So the addition of third alloy elements such as Ni increases the critical ligament thickness due to the interaction of dislocations with solute atoms and thus improves the mechanical properties. Fratograph of the FeAl10Ni-60%TiC composite is shown in Fig.9. Compared with the fracture surface of the FeAl-60%TiC, the ductile fracture seems more obvious.
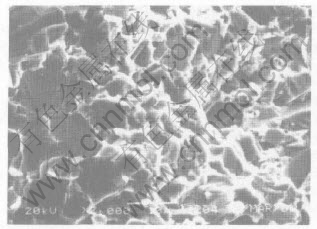
Fig.9 Fractograph of Fe40Al10Ni-60%TiC after bend test
4 CONCLUSIONS
1) FeAl/TiC composite can be successfully fabricated through reactive hot pressing at 1300℃, 30MPa under the protection of Ar atmosphere.
2) The density and relative density of the composites decrease with the increase of TiC content. The mechanical properties of the composites are closely related with their porosities. Both hardness and bend strength exhibit peak values with the increase of TiC volume fraction. Higher content of Al in FeAl improves the densities of the composites, but lowers the hardness and bend strength of the composites.
3) The addition of Ni improves the densities of FeAl/TiC composites by promoting mass transfer during densification process. The hardness and bend strength of the composites are greatly improved due to the increase of the density, together with some effects including solid solution-strengthening the binder phase and promoting ductile fracture of FeAl by alloying with Ni.
REFERENCES
[1]Stoloff N S. Iron aluminides: present status and future prospects [J]. Mater Sci Eng A, 1998, 258(1/2): 1-14.
[2]Deevi S C, Sikka V K. Nickel and iron aluminides: an overview on properties, processing and applications [J]. Intermetallics, 1996, 4(5): 357-375.
[3]Liu C T, George E P, Maziasz P J, et al. Recent advances in B2 iron aluminide alloys: deformation, fracture and alloy design [J]. Mater Sci Eng A, 1998, 258(1/2): 84-98.
[4]Misra A K. Identification of thermodynamically stable ceramic reinforcement materials for iron aluminide matrices [J]. Metall Trans, 1990, 21A(2): 441-448.
[5]Schneibel J H, Carmichael C A, Subramanian R. Liquid-phase sintered iron aluminide composites [J]. Intermetallics, 1997, 5(1): 61-67.
[6]Subramanian R, Schneibel J H. FeAl-TiC and FeAl-WC composites-melt infiltration processing, microstructure and mechanical properties [J]. Mater Sci Eng A, 1998, 244(1): 103-112.
[7]Subramanian R, Schneibel J H. The ductile-brittle size transition of iron aluminide ligaments in an FeAl/TiC composite [J]. Acta Mater, 1998, 46(13): 4733-4741.
[8]Inoue M, Suganuma K, Niihara K. Fracture properties at ambient temperatures of iron aluminides fabricated by reactive hot-pressing [J]. Scripta Mater, 1998, 39(10): 1477-1482.
[9]Subramanian R,Schneibel J H. Processing iron-aluminide composite containing carbides or borides [J]. JOM, 1997, 49(8): 50-54.
[10]Inoue M, Suganuma K, Niihara K. Mechanical properties of aluminide matrix composite fabricated by reactive hot-pressing in several environments [J]. Intermetallics, 2000, 8(11): 1035-1042.
[11]LIU Yong, LIU Feng-xiao, HUANG Bai-yun, et al. Improving densification and mechanical properties of FeAl/TiC composites by addition of Ni [J]. J Mater Sci Tech, 2003, 19(1): 73-76.
[12]Skoglund H, Knutson M, Karlsson B. The role of oxygen in powder processing of FeAl [J]. Intermetallics, 2003, 11(5): 475-482.
[13]Morris M A, George O, Merris D G. Vacancies, vacancy aggregates and hardening in FeAl [J]. Mater Sci Eng A, 1998, 258(1/2): 99-107.
[14]Kainuma R, Urushiyama K, Ishikawa K, et al. Ordering and phase separation in b.c.c. aluminides of the Ni-Fe-Al-Ti system [J]. Mater Sci Eng A, 1997, 239-240: 235-244.
[15]Savage M F, Srinivasan R, Daw M S, et al. Dislocation processes and deformation behavior in (Fe,Ni)/Al single crystals [J]. Mater Sci Eng A, 1998, 258:20-25.
(Edited by YUAN Sai-qian)
Foundation item: Project(96JJY2009) supported by the Natural Science Foundation of Hunan Province
Received date: 2004-04-12; Accepted date: 2004-11-15
Correspondence: LIU Feng-xiao, PhD candidate; Tel: +86-731-8830406; E-mail: fxliucsu@yahoo.com