
Key techniques of automatic gauge control and profile control for aluminium strip and foil
LI Mou-wei(李谋渭)1, LIU Hong-fei(刘鸿飞)1, WANG Xiang-li(王向丽)1,
TONG Chao-nan(童朝南)2, YIN Feng-fu(尹凤福)1, BIAN Xin-xiao(边新孝)1, ZHANG Lei(张 磊)1
1. School of Mechanical Engineering, University of Science and Technology Beijing, Beijing 100083, China;
2. School of Information Engineering, University of Science and Technology Beijing, Beijing 100083, China
Received 28 July 2006; accepted 15 September 2006
Abstract: Such characteristics of aluminium strip and foil as soft and thin gauge make tension control one of the key techniques for automation gauge control(AGC). To avoid the disadvantage of traditional mathematical control method which is unfitful for nonlinear hysteresis, the technique for tension AGC fuzzy control was developed and thickness deviation more than 3% of product thickness was achieved consequently in 1 350 mm cold rolling mill of aluminium strip and foil. Additionally, because the gauge of aluminium strip and foil is thin, stage-cooling roll method becomes a key technique for profile control. So stage-cooling roll intelligent control method is developed and pre-coated aluminum foil with good profile less than 10 I (the relative differences in elongation of 0.01%) is produced using the profile control system in 1 400 mm cold rolling mill of aluminium strip and foil.
Key words: aluminium strip and foil; control; AGC fuzzy control; stage-cooling intelligent control method
1 Introduction
Aluminium strip and foil are important fundamental materials for the development of national economy[1]. Both thickness deviation and profile are two key quality attributes. Traditional pressure automatic gauge control (AGC) is hard to take good effect because aluminium strip and foil are of soft and thin gauge, especially in negative rolling gap. In addition, velocity AGC asks for high system stability and synchronization, so tension AGC takes remarkable function. Because tension gauge control works through the tension pressure effect in the deformation zone which is difficult to be described by mathematical equation accurately, if such a system in which its non-linear hysteresis model is uncertain is worked out based on traditional linear system control theory, it is difficult to achieve our control goal[2-3]. When the thickness of the slab fluctuates severely, tension gauge control can not obtain perfect effect. That is to say, PI regulator algorithm can not work effectively on controlling both small and big thickness deviation. After studying the control idea of skilled operators, tension AGC fuzzy control technique is developed.
The gauge of aluminium strip and foil is thin, so profile control using stage-cooling method achieves remarkable effect during practical production process. Especially to solve high-order profile problems, multi-variable, time-varying, severely-nonlinear profile control is required, which urges us to develop the technique for stage-cooling intelligent control.
2 Tension AGC fuzzy control
In order to reduce the stability error of gauge control system and get zero error, fuzzy controller with integral component is selected. Fig.1 illustrates the diagram of tension AGC fuzzy controller[4-5].
In Fig.1, Hg is the given thickness, Hf is the detected thickness, δH is the thickness deviation, K1 and K2 are scale coefficients of quantifying δH based on different thickness targets and different required precisions, K3 and K4 are proportional integral coefficients regulated on the base of different target thicknesses and K5 is the coefficient of practical output voltage amplitude.

Fig.1 Diagram of tension AGC fuzzy controller
The quantification procedure is to work out the membership function table for the quantification of thickness E, the membership function table for the quantification of thickness change rate EC, and the membership function table for tension controlling variable U on the basis of product precision. Fuzzy decision is to build fuzzy rule decision table according to the requirement for negative tolerance rolling and expresses the designer’s purpose and idea brightly. Table 1 lists the tension AGC fuzzy decision table according to product thickness deviation which is controlled within ±3%.
Table 1 Fuzzy decision for tension AGC
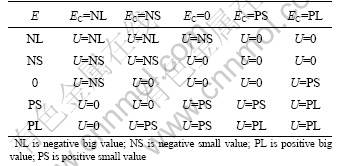
The table above will be explained well with the following example of the 1st rule:
If E=NL and EC=NL or EC=NS
then U=NL
This rule indicates that when thickness is negative big deviation, and thickness change rate shows a tendency to attenuate the thickness, the back tension control is in position of output control grade of decreasing to the fullest extent of tension.
Fuzzy control is adopted in the 1 350 mm cold rolling mill of aluminium strip and foil in Northeast Alloy Co Ltd and thickness deviation less than 3% of the product thickness has been acquired successfully.
3 Stage-cooling intelligent profile control
The cooling control mechanism is discussed and system control is studied here on the basis of 1 400 mm cold rolling mill of aluminium strip and foil in Huayi Aluminium Plant.
3.1 Temperature-controlling element effect of nozzles and their organic combination
Coolant fluid controls working roll crown through nozzles and each nozzle is a temperature-controlling element. The organic combination of temperature- controlling elements forms the basis of stage cooling profile control. The following is the results of computer simulation for the cooling control and deformation of working roll tested by experiments. Fig.2 shows the change of the crown of working rolls when closing one nozzle. Fig.3 shows the change of the crown of working rolls when three nozzles are opened, closed and opened respectively[6].
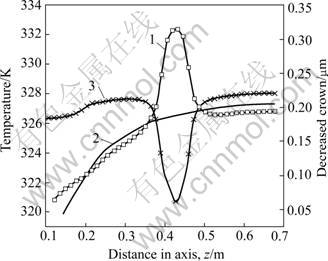
Fig.2 Change of crown of working roll when closing one nozzle: 1 Temperature of roll surface (one nuzzle off); 2 Tem- perature of roll surface (normal); 3 Decreased crown of roll
3.2 Heat transfer characteristics between working rolls and coolant fluid from nozzles and its optimization
The optimization of heat transfer characteristics is crucial for improving stage-cooling control effect. The main factors affecting heat transfer characteristics include jetting velocity, temperature, jetting angle and viscosity of the coolant fluid[7,8]. Figs.4-7 show the results of computer simulation for convection heat transfer coefficient (ordinate) which corresponds to the distance of circle direction of working roll (abscissa) when the surface temperature of working roll is 363 K and the space between nozzle and working roll is 0.1 m [2]. Fig.4 shows the computer simulation for condition: the temperature of coolant fluid is 303 K, jetting angle is 156? and the viscidity of coolant fluid is 0.001 Pa. Fig.5 shows the computer simulation for condition: the temperature of coolant fluid is 303 K, radial jetting velocity vx=27 m/s, tangent velocity vy=-12 m/s and the viscidity of coolant fluid is 0.001 Pa. Fig.6 shows the computer simulation for condition: radial jetting velocity vx=27 m/s, tangent velocity vy=-12 m/s, jetting angle is 156? and the viscidity of coolant fluid is 0.001 Pa. Fig.7 shows the computer simulation for condition: the temperature of coolant fluid is 303 K, radial jetting velocity vx=27 m/s, tangent velocity vy=-12 m/s and the jetting angle is 156?.
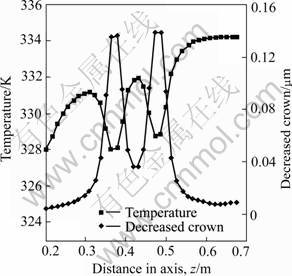
Fig.3 Change of crown of working roll when three nozzles are opened, closed and opened, respectively
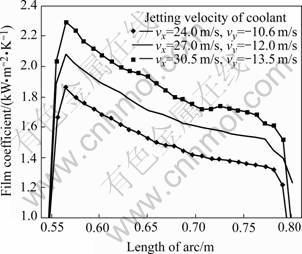
Fig.4 Convection heat transfer coefficient changing with jetting velocity of coolant
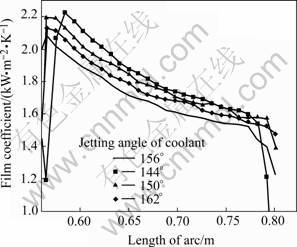
Fig.5 Convection heat transfer coefficient changing with jetting angle of coolant
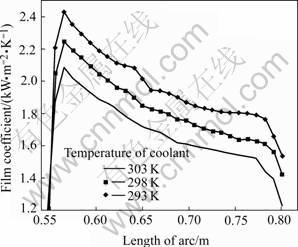
Fig.6 Convection heat transfer coefficient changing with temperature of coolant
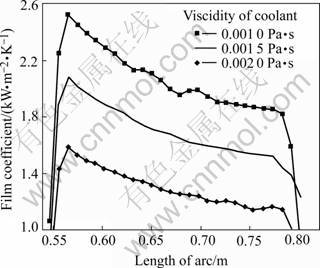
Fig.7 Convection heat transfer coefficient changing with viscidity of coolant
After studying the effect of each factor on the characteristics of convection heat transfer, orthogonal test method is introduced to decide the order of the importance of each factor affecting the characteristics of convection heat transfer in return: viscidity of coolant fluid, jetting velocity, temperature of coolant fluid, jetting angle. A set of optimum parameters are obtained finally[9,10].
3.3 Stage-cooling intelligent control
After measured profile is identified by means of the method of fuzzy clustering, one-order curve and quadric curve in the profile defect are distinguished and the profile defect which will be eliminated by stage-cooling is obtained. Nozzle cooling system which is optimized with the method above can control the transverse crown of rollers through the ratio of vacancy to occupancy. That is to say, jetting coolant fluid and the closing time of nozzles are classified into several modes in one control period (such as 7 discrete time proportional points) and improved genetic algorithm is adopted for the sum of the coolant fluid of rollers according to the requirement of various cooling segments. Then the normalized proportion of the ratio of vacancy to occupancy is optimized and the optimum control on profile is achieved.
7 modes of the ratio of vacancy to occupancy are assumed as follows:
(X1) 1?0 (all the nozzles are opened); (X2) 1?0.25; (X3) 1?0.75; (X4) 1?1; (X5) 1?5; (X6)1?10; (X7) 0?1 (all the nozzles are closed).
Fig.8 shows the target curve which will be optimized. Through applying improved genetic algorithm and optimizing the proportion of {X1, X2, X3, X4, X5, X6, X7}, the optimum cooling control effect can be achieved.
Table 2 shows the optimized cooling mode of 1-8 cooling segments corresponding to Fig.8.
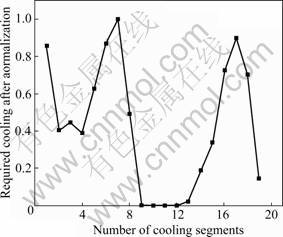
Fig.8 Target curve to be optimized
Table 2 Optimized results of 1-8 cooling segments corresponding to Fig.8
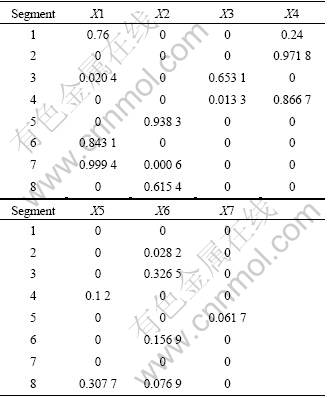
The control method above has been realized in the air supported shapemeter and its control system are developed jointly by Huayi Aluminium Plant, Angfei Company and University of Science and Technology Beijing, and installed in 1 400 mm cold rolling mill of aluminium strip and foil.
The system has been in operation for above one year and pre-coated aluminum foil whose good profile is less than 10 I (I unit is a key index for strip flatness, 10 I means relative differences in elongation of 0.01%) is produced.
4 Conclusions
1) Tension AGC fuzzy control is an effective controlling method for improving the thickness precision of aluminium strip and foil. This technique is applied in 1 350 mm cold rolling mill of aluminium strip and foil and has achieved excellent thickness accuracy.
2) Stage-cooling is one of the key profile control methods for aluminium strip and foil. The importance order of each factor which affects the characteristics of convection heat transfer is as follows: the viscidity of coolant fluid, the jetting velocity, the temperature of coolant fluid, and the jetting angle.
3) Adopting the ratio of vacancy to occupancy is a good method for roller cooling control. By applying the foregoing profile control system, pre-coated aluminium foil with excellent profile can be produced successfully in 1 400 mm cold rolling mill of aluminium strip and foil.
References
[1] LI Yun-qing. The analyses of the developmental situation of aluminium foil industry and its relative industrial policy in our country [J]. China Metal Bulletin, 2006, 23: 2-6.
[2] LI Shao-yuan, WANG Jing-cheng. Intelligent Control [M]. Beijing: China Machine Press, 2005: 1-7. (in Chinese)
[3] JANABI-SHARIFI F, NEURO-FUZZY A. System for looper tension control in rolling mill [J]. Control Engineering Practice, 2005, 13: 1-13.
[4] LI Mou-wei, TONG Chao-nan, XU Feng. Study on tension AGC fuzzy control and great accuracy overall sealed tension sensor [J]. Metallurgical Equipment, 1998(1): 26-28.
[5] TONG Chao-nan, SUN Yi-kang, CHEN Bai-hong, ZHANG Hai-bo. Intelligent control of a multi-function AGC system in hot strip mills [J]. Journal of University of Science and Technology Beijing, 2002(5): 553-555.
[6] YIN Feng-fu. The Technology of Differential Roll Cooling in the Mill of Aluminium Strip and Foil and its Intelligent Control Model [D]. Beijing: University of Science and Technology Beijing, 2003: 68-79.
[7] YIN Feng-fu, LI Mou-wei, ZHU Qi-jian, WANG Feng-li. The simulation of influence on convective heat transfer in aluminium strip mill [J]. Metallurgical Equipment, 2002(5): 26-28.
[8] YIN Feng-fu, LI Mou-wei, ZHANG Da-zhi, LIU Hong-fei, LIANG Zhi-yuan. Convective heat transfer analysis between working roll and coolant fluid of mill 1 400 F [J]. The Chinese Journal of Nonferrous Metals, 2003, 13(1): 51-55. (in Chinese)
[9] YIN Feng-fu, LI Mou-wei, ZHANG Shao-jun, LI Dong-ming. Distribution of heat production in aluminium foil mills [J]. Journal of University of Science and Technology Beijing, 2003(6): 568-571.
[10] YIN Feng-fu, LI Mou-wei, ZHANG Shao-jun. Optimum values of convection heat transfer between the working roll and coolant fluid of mill 1 400 F [J]. Journal of University of Science and Technology Beijing, 2005(4): 480-483.
(Edited by YANG Bing)
Corresponding author: LI Mou-wei; Tel: +86-10-62334249; E-mail: limow@me.ustb.edu.cn