
Oxidation behavior of oxidation protective coatings for
C/C-SiC composites at 1 500 ℃
YAN Zhi-qiao(闫志巧)1, 2, XIONG Xiang(熊 翔)1, XIAO Peng(肖 鹏)1,
CHEN Feng(陈 峰)1, ZHANG Hong-bo(张红波)1, HUANG Bai-yun(黄伯云)1
1. State Key Laboratory of Powder Metallurgy, Central South University, Changsha 410083, China;
2. Guangzhou Research Institute of Nonferrous Metals, Quangzhou 510650, China
Received 16 January 2008; accepted 28 April 2008
Abstract: Porous carbon/carbon preforms were infiltrated with melted silicon to form C/C-SiC composites. Three-layer Si-Mo coating prepared by slurry painting and SiC/Si-Mo multilayer coating prepared by chemical vapor deposition(CVD) alternated with slurry painting were applied on C/C-SiC composites, respectively. The oxidation of three samples at 1 500 ℃ was compared. The results show that the C/C-SiC substrate is distorted quickly. Three-layer Si-Mo coating is out of service soon due to the formation of many bubbles on surface. The mass loss of coated sample is 0.76% after 1 h oxidation. The sample with SiC/Si-Mo multilayer coating gains mass even after 105 h oxidation. SiC/Si-Mo multilayer coating can provide longtime protection for C/C-SiC composites and has excellent thermal shock resistance. This is attributed to the combination of dense SiC layer and porous Si-Mo layer. Dense SiC layer plays the dual role of physical and chemical barrier, and resists the oxidation of porous Si-Mo layer. Porous Si-Mo layer improves the thermal shock resistance of the coating.
Key words: C/C-SiC composites; oxidation protective coating; slurry painting; chemical vapor deposition
1 Introduction
Molten silicon infiltration(MSI) is a major manufacturing process of C/C-SiC composites. Compared with chemical vapor infiltration(CVI) and polymer impregnation and pyrolysis(PIP), MSI has many advantages such as lower component fabrication time to reduce costs significantly[1]. It is generally thought that C/C-SiC composites exhibit better oxidation resistance than C/C composites because SiC and residual Si are contained. However, our research found that the initial oxidation temperature of C/C-SiC composites is about 100 ℃ lower than that of C/C composites. The mass loss rate below 1 000 ℃ was much higher[2]. Consequently, MSI C/C-SiC composites need oxidation protection when exposed to oxidizing environment at high temperatures.
Currently, three primary methods are used to apply oxidation protection coating on the surface of carbon materials: pack cementation, chemical vapor deposition (CVD) and slurry method[3]. Among these methods, pack cementation is widely used to form coatings on C/C composites in particular[4-7]. Unfortunately, the process has to be carried out above 1 800 ℃ and residual silicon may escape from the C/C-SiC substrate causing substrate to become loose and the mechanical strength to decrease. In this regard, pack cementation is not suitable for MSI C/C-SiC composites.
In this work, three-layer Si-Mo coating prepared by slurry painting, and SiC/Si-Mo multilayer coating prepared by CVD alternated with slurry painting, were applied on MSI C/C-SiC composites, respectively. The oxidation of substrate and two coated samples at 1 500 ℃ was investigated.
2 Experimental
2.1 Specimen preparation
The 2.5D bulk needled carbon fiber felts (bulk density of 0.56 g/cm3) from Tianniao Yixing High Technology Co., Ltd., China, were used as preforms. A CVD process was used to deposit pyrocarbon in the felts and MSI was adopted to infiltrate the porous carbon/ carbon preforms to form C/C-SiC composites. The details were reported in Ref.[2].A Si-Mo layer was prepared by painting the mixture slurry of Si and Mo powders and silica sol on the surface of substrate then drying and sintering at 1 500 ℃ for 10 min. The above process was repeated for 3 times to form three-layer Si-Mo coating. The coating was about 100 μm thick and the details were reported in Ref.[8].
For SiC/Si-Mo multilayer coating, a SiC layer was first deposited on the substrate for 6 h at 1 100 ℃ in MTS (methyltrichlorosilane)-H2-Ar system. Then, a Si-Mo layer was made by slurry painting. These processes were repeated until the coating structure, form inside to outside, was SiC→Si-Mo→SiC→Si-Mo→SiC. This coating was about 100 μm thick too, and the detail information was reported in Ref.[9].
2.2 Oxidation tests
The substrate and two coated samples were heated at 1 500 ℃ in air in a corundum tube furnace to investigate the isothermal thermal cycling behavior. The samples were put inside or taken out of the furnace directly to air within several seconds. Cumulative mass changes of the samples were measured at room temperature by an electronic balance with a sensitivity of ±0.1 mg. The mass change (Δm) of the samples is calculated by the following equation:
Δm=(m1-m0)/m0×100% (1)
where m0 and m1 are the mass of the samples before and after oxidation, respectively.
The morphologies and crystalline structures of the samples were analyzed by scanning electron microscopy (SEM, Jeol-6300LV) equipped with energy dispersive spectroscopy(EDS).
3 Results and discussion
3.1 Oxidation of C/C-SiC substrate
Morphologies of C/C-SiC composites before and after oxidation are shown in Fig.1. Pores in the original C/C porous preforms are well infiltrated by the reaction- formed SiC and residual Si. C/C-SiC composites have high density (Fig.1(a)) and the open porosity is less than 3%[2], which indicates that MSI is a rapid process to fabricate dense C/C-SiC composites, and to retain high residual Si content (about 14.2% (mass fraction) [2]).
The C/C-SiC substrate has a network structure and the fiber bundles are distributed in the continuous network framework consisting of SiC and Si (Fig.1(b)). Therefore, when being oxidized at or below 1 400 ℃, C/C-SiC composites always exhibit good shape retention though carbon in the substrate is utterly burnt out. It is found that the substrate does not distort after 10 h oxidation at 1 400 ℃. While after oxidation at 1 500 ℃ for 1 h, it is badly distorted and many lumps appear on the surface (Fig.1(c)). SEM image (Fig.1(d)) shows that the substrate becomes very loose and many microcracks emerge. By EDS analysis, these lumps contain mainly Si and O, suggesting that they should be the molten SiO2 glass agglomeration.
Above the Si melting point (1 410 ℃), residual Si in the substrate melts evaporates into Si(g) and diffuses toward the surface of sample. Si(g) is rapidly oxidized into SiO2 and deposits on the surface. It is concluded that C/C-SiC composites with residual Si cannot be directly used at 1 500 ℃.
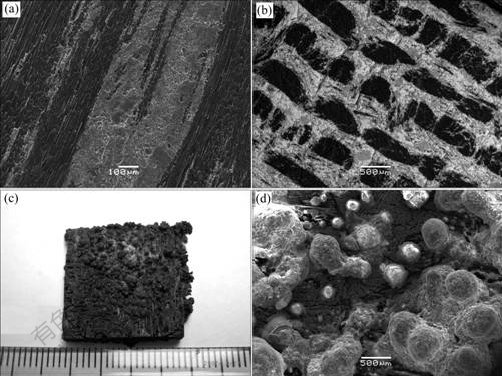
Fig.1 Morphologies of C/C-SiC composites: (a), (b) Before oxidation; (c), (d) Oxidation at 1 500 ℃ for 1 h
3.2 Oxidation of C/C-SiC substrate with three-layer Si-Mo coating
SiC, Si, MoSi2 and SiO2 are found in the three-layer Si-Mo coating. After 140 h oxidation at 1 400 ℃, the mass loss of the coated sample is 1.34%, showing that the coating can provide longtime oxidation protection for C/C-SiC composites at that temperature[8]. While after 1 h oxidation at 1 500 ℃, the mass loss reaches 0.76% (Fig.2(a)) and many bubbles appear on the surface. The surface SEM image, shown in Fig.2(b), reveals that continuous SiO2 glass has been formed accompanied with bubbles. The phase formation Mo+2Si→MoSi2 is accompanied by a volume reduction of about 27%[10]. This reduction produces certain pores and interface in the Si-Mo layer and leads to higher chemical activity. At 1 500 ℃, SiC, Si and MoSi2 are rapidly oxidized into SiO2 glass and CO. Simultaneously, residual Si in the coating melts and evaporates. Gases of Si(g) and CO gather in the coating and bubbles are formed in the SiO2 glass when the pressure exceeds the critical value. Then the coating is out of service. Therefore, three-layer Si-Mo coating cannot provide oxidation protection for C/C-SiC composites at 1 500 ℃.
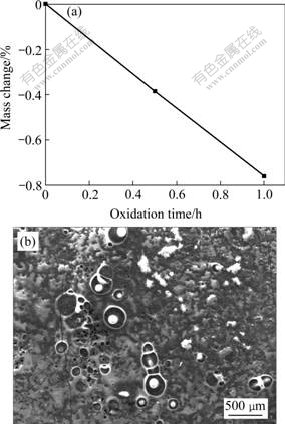
Fig.2 Oxidation of C/C-SiC composites with three-layer Si-Mo coating at 1 500 ℃: (a) Isothermal oxidation curve; (b) SEM image after 1 h oxidation
FANG[11] reported a Si-Mo slurry coating on C/C composites. The coating consisted of Si and MoSi2. It worked well at 1 370 ℃, but soon became invalid at 1 450 ℃. In a conclusion, coatings with residual Si can not be used at 1 500 ℃ directly.
3.3 Oxidation of C/C-SiC substrate with SiC/Si-Mo multilayer coating
Based on the above analysis, it can be inferred that the evaporation of residual Si and higher chemical activity of Si-Mo layer lead to the failure of the C/C-SiC substrate with and without three-layer Si-Mo coating. Our purpose is thus to develop the coating system with dense barriers. The designed SiC/Si-Mo multilayer coating, from inside to outside, was SiC→Si-Mo→SiC→Si-Mo→SiC. Even after 150 h oxidation at 1 400 ℃, the mass loss of the coated sample was 0.25%[9]. When being oxidized at 1 500 ℃, the coated sample kept mass gaining during 105 h, which suggests that the coating can protect the C/C-SiC substrate from oxidation at that temperature. Surface SEM image (Fig.3(b)) shows a glassy SiO2 layer covering the surface well except the existence of several microcracks. During the oxidation test, the sample was taken out of the furnace directly into air within several seconds for weighing. The cooling rate from 1 500 ℃ to room temperature was very quick. Owing to this quick cooling, the coating would suffer from tensile stress, which induced the formation of microcracks. These microcracks could be self-sealed quickly when the coated sample was heated to 1 500 ℃ again, such that they have little effect on the oxidation resistance of the coating. Moreover, the coating remained intact during the whole test for 21 cycles of thermal shock between 1 500 ℃ and room temperature. The oxidation curve is changed steadily. These verify that the SiC/ Si-Mo multilayer coating has excellent oxidation resistance at 1 500 ℃ with good thermal shock resistance.

Fig.3 Oxidation of C/C-SiC composites with SiC/Si-Mo multilayer coating at 1 500 ℃: (a) Isothermal oxidation curve; (b) SEM image after 105 h oxidation
Compared with the results in Ref.[12] (SiC-MoSi2- (Ti0.8Mo0.2)Si2 multi-composition coating, 2.18% mass loss at 1 500 ℃ for 49 h for C/C composites) and Ref.[13] (a dense C/SiC gradient oxidation protective coating, 2.46% mass loss at 1 500 ℃ for 35 h for C/C composites), the oxidation resistance is obviously improved, and the protective temperature is higher than that of SiC/Si-MoSi2 coating for carbon materials (reported to be 1 400 ℃[14]).
Compared with three-layer Si-Mo coating, the excellent oxidation resistance of SiC/Si-Mo multilayer coating should be attributed to the alternated structure, especially the outer SiC layer. CVD SiC coating deposited at 1 100 ℃ is usually quite dense, and even a very thin layer could play the dual role of physical and chemical barrier. On the one hand, the SiC layer hinders the diffusion of oxygen in and Si(g) out. On the other hand, it is oxidized into dense SiO2 glass and resists the oxidation of Si-Mo layer. These prolong the coating lifespan.
The excellent thermal shock resistance of the SiC/Si-Mo multilayer coating is attributed to the Si-Mo layer. The porous Si-Mo layer has lower elastic modulus, which helps reducing thermal stress and thermal expansion mismatch between the coating and the substrate[15]. These pores provide sites for volume expansion of SiO2 formation. These factors ensure the excellent thermal shock resistance of the multilayer coating.
4 Conclusions
Owing to the evaporation of Si and higher chemical activity of Si-Mo layer, the MSI C/C-SiC substrate with and without three-layer Si-Mo coating cannot be used at 1 500 ℃. For SiC/Si-Mo multilayer coating, the outer SiC layer plays the dual role of physical and chemical barrier, which hinders the diffusion of oxygen in and Si(g) out, and resists the oxidation of Si-Mo layer. The coating could provide longtime protection for C/C-SiC composites at 1 500 ℃. The porous Si-Mo inner layer ensures the coating has excellent thermal shock resistance. Coatings with residual Si should be avoided to use at 1 500 ℃ solely, but they can act as inner layers when dense outer barriers exist.
References
[1] SCHULTE-FISCHEDICK J, SCHMIDT J, TAMME R, KRONER U, ARNOLD J, ZEIFFER B. Oxidation behavior of C/C-SiC coated with SiC-B4C-SiC-cordierite oxidation protection system [J]. Mater Sci Eng A, 2004, 386(1/2): 428-434.
[2] YAN Zhi-qiao, XIONG Xiang, XIAO Peng, HUANG Bai-yun. Oxidation kinetics and mechanism of C/SiC composites fabricated by MSI process [J]. Journal of Inorganic Materials, 2007, 22(6): 1151-1158. (in Chinese)
[3] SNELL L, NELSON A, MOLIAN P. A novel laser technique for oxidation-resistant coating of carbon-carbon composites [J]. Carbon, 2001, 39(7): 991-999.
[4] ZHANG Y L, LI H J, FU Q G, LI K Z, HOU D S, FEI J. A Si-Mo oxidation protective coating for C/SiC coated carbon/carbon composites [J]. Carbon, 2007, 45(5): 1130-1133.
[5] LI H J, XUE H, WANG Y J, FU Q G, YAO D J. A MoSi2-SiC-Si oxidation protective coating for carbon/carbon composites [J]. Surf Coat Technol, 2007, 201(24): 9444-9447.
[6] FU Q G, LI H J, LI K Z, SHI X H, HU Z B, HUANG M. SiC whisker-toughened MoSi2-SiC-Si coating to protect carbon/carbon composites against oxidation [J]. Carbon, 2006, 44(9): 1866-1869.
[7] HUANG J F, ZENG X R, LI H J, LI K Z, XIONG X B. Oxidation behavior of SiC-Al2O3-mullite multi-coating coated carbon/carbon composites at high temperature [J]. Carbon, 2005, 43(7): 1580-1583.
[8] YAN Zhi-qiao, XIONG Xiang, XIAO Peng, CHEN Feng, HUANG Bai-yun. Oxidation behavior of Mo-Si coated C/SiC composites [J]. Aerospace Materials & Technology, 2007(6): 39-43. (in Chinese)
[9] YAN Z Q, XIONG X, XIAO P, CHEN F, ZHANG H B, HUANG B Y. A multilayer coating of dense SiC alternated with porous Si-Mo for the oxidation protection of carbon/carbon silicon carbide composites [J]. Carbon, 2008, 46(1):149-153.
[10] SCHUBERT T, BOHM A, KIEBACK B, ACHTERMANN M, SCHOLL R. Effects of high energy milling on densification behavior of Si-Mo powder mixtures during pressureless sintering [J]. Intermetallics, 2002, 10(9): 873-878.
[11] FANG Hai-tao. A Si-Mo fused slurry coating of C/C composites and the oxidation resistance [D]. Harbin: Harbin Institute of Technology, 2001. 81-83. (in Chinese)
[12] JIAO G S, LI H J, LI K Z, WANG C, HOU D S. SiC-MoSi2-(Ti0.8Mo0.2)Si2 multi-composition coating for carbon/ carbon composites [J]. Surf Coat Technol, 2006, 201(6): 3452-3456.
[13] ZHANG Y L, LI H J, FU Q G, LI K Z, WEI J, WANG P Y. A C/SiC gradient oxidation protective coating for carbon/carbon composites [J]. Surf Coat Technol, 2006, 201(6): 3491-3495.
[14] ZHAO J, GUO Q G, SHI J L, ZHAI G T, LIU L. SiC/Si-MoSi2 oxidation protective coatings for carbon materials [J]. Surf Coat Technol, 2006, 201(3/4): 1861-1865.
[15] DING S Q, ZENG Y P, JIANG D L. Thermal shock resistance of in situ reaction bonded porous silicon carbide ceramics [J]. Mater Sci Eng A, 2006, 425(1/2): 326-329.
Foundation item: Project(2006CB600908) supported by the National Basic Research Program of China
Corresponding author: XIONG Xiang; Tel: +86-731-8836079; E-mail: xiong228@sina.com
DOI: 10.1016/S1003-6326(08)60229-0
(Edited by YUAN Sai-qian)