J. Cent. South Univ. (2016) 23: 1312-1317
DOI: 10.1007/s11771-016-3181-2

Coordination leaching of tungsten from scheelite concentrate with phosphorus in nitric acid
ZHANG Wen-juan(张文娟)1, YANG Jin-hong(杨金洪)1, ZHAO Zhong-wei(赵中伟)1, 2,
WANG Wen-qiang(王文强)1, LI Jiang-tao(李江涛)1, 2
1. School of Metallurgy and Environment, Central South University, Changsha 410083, China;
2. Key Laboratory of Hunan Province for Metallurgy and Material Processing of Rare Metals, Changsha 410083, China
Central South University Press and Springer-Verlag Berlin Heidelberg 2016
Abstract: A hydrometallurgical process for tungsten extraction and recovery from scheelite is reported. The technology includes leaching scheelite using phosphoric acid as chelating agent in nitric acid solutions, extracting tungsten by solvent extraction and reusing leaching agent. In the leaching process, affecting factors, such as temperature, leaching time, nitric acid and dosage of phosphoric acid, were examined on recovery of tungsten. Results show that more than 97% of tungsten could be extracted under conditions of leaching temperature of 80-90 °C, HNO3 concentration of 3.0-4.0 mol/L, liquild-to-soild ratio of 10:1, H3PO4 dosage of 3 stoichiometric ratio and leaching time of 3 h. Solvent extraction was then employed for the W recovery from the leachate with a organic system of 40% (v/v) N235, 30% (v/v) TBP, and 30% sulfonated kerosene. Approximately 99.93% of W was extracted and ammonium tungstate solution containing 193 g/L W was obtained with a stripping rate of 98.10% under the optimized conditions.
Key words: scheelite; nitric acid; phosphoric acid; coordination leaching
1 Introduction
Tungsten primarily exists in the form of wolframite and scheelite in nature [1]. Over the years, wolframite is the chief raw material for the production of tungsten due to the characteristics of less impurity, easy beneficiation and decomposition. However, with progressive exhaustion of wolframite, it is imperative to utilize scheelite which accounts for about 68.54% of China’s confirmed industrial reserves of tungsten [2].
The current process for recovering tungsten from scheelite is to decompose the scheelite with solutions of caustic soda or sodium carbonate at elevated temperatures and pressures to produce sodium tungstate [3-7]. Both methods, being widely applied on commercial scale, possessed a strong adaptability to raw materials and could effectively decompose scheelite concentrates and low grade ores, even the scheelite-wolframite blend concentrates. However, these two leaching processes have the disadvantages that it is necessary to conduct at high temperatures and high pressures; they require relatively large amounts of reagents [8-9], with a corresponding increase in energy consumption and reagent cost. Furthermore, the subsequent ion exchange process will produce a large amount of wastewater which can be discharged in aqueous effluents and in consequence it is environmentally harmful.
In the conventional process, scheelite is decomposed with hydrochloric acid to produce tungstic acid [10]. Unfortunately, the process suffers from the disadvantage that tungstic acid in the form of a yellow gel will be generated and cover the surface of the unreacted particle. The product layer behaves as barriers for the scheelite leaching and decrease the direct contact between the fluid reactants and the unreacted scheelite particles [11]. Consequently, one alternative method that does not form insoluble H2WO4 has been presented. This method is based on the complex effect between W and a reagent, such as oxalic, tartaric, citric, or phosphoric acid [12-14]. G
RMEN et al [13] proposed a process to recovery tungsten from scheelite concentrates. According to this process, the tungsten ores are dissolved in hydrochloric acid in the presence of phosphoric acid as complexing agent. Leach solution was then treated by ammonium salt compound addition to precipitate the tungsten. However, corrosion and volatilization problems associated with the hydrochloric acid still exist, which limits its application in industry. Additionally, the lixivium after tungstate salt precipitation contained residual ammonia. Thus, it is difficult to reuse the solution for ore leaching due to the generation and wrapping of solid hetero-poly-tungstate salt. And few effective ways have been found to deal with large quantity of residual hydrochloric acid, in consequence resulting in serious environmental problem and a waste of resource. So, there is an increasing need to develop proper leaching system.
Compared with hydrochloric acid, nitric acid has advantage that it is less corrosive to equipment. Moreover, the use of nitric acid is constructive to the removal of flotation reagent on mineral surfaces due to its strong oxidation ability. Consequently, nitric acid utilized as leachant media could be appropriate for treating scheelite concentrate. The purpose of this work is to investigate and develop a hydrometallurgical process to extract tungsten from scheelite ores. In the process, the scheelite concentrate was decomposed with nitric acid and phosphoric acid to produce a phosphotungstic acid solution. After extraction of tungsten from the solution, such as by solvent extraction, the raffinate was returned to ore leaching stage with supplementing the acid to an initial level. The acid circulation greatly decreases the leaching cost and discharge of waste water. The experimental results demonstrated that the process was environment-friendly with a high recovery of tungsten and a low cost.
2 Materials and methods
2.1 Materials
The chemical composition of the scheelite concentrates used in experiment is presented in Table 1. Scheelite 1 was used as main material taken from Jiangxi province of China and the XRD pattern is shown in Fig. 1. Material 1 was used in experiment if it is not pointed out.
The organic phase consisted of trialkylamine (N235, industrial grade) and tributyl phosphate (TBP, analytical grade) with commercial sulfonated kerosene as the solvent for extraction.
The other reagents used in this work were of analytical grade.
2.2 Methods
Leaching experiments were carried out by placing 100 mL leaching solution into round-bottom flask and heating to desired temperature in a water bath with constant stirring. 10 g sample was added to the solution when the operating temperature had stabilized. After completion of the leaching, the mixture in the reactor was filtered to separate the solid and solution. Tungsten concentration of the solutions was analyzed with ICP-AES instrument. The leaching rate of tungsten was calculated based on mass fraction of soluble tungsten in solution.
Table 1 Chemical composition of materials used in experiments

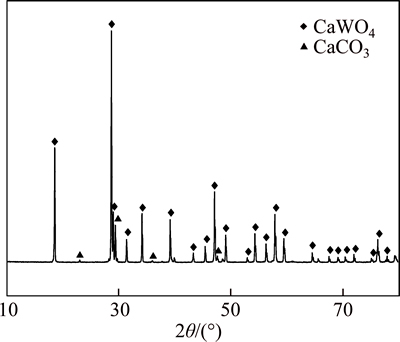
Fig. 1 XRD pattern of scheelite concentrate 1
After the leaching process, the W in solution was extracted and enriched using solvent extraction. The experiments were carried out by mixing a certain volume of the organic phase and the aqueous solution in separatory funnels. When the extraction process stopped, the loaded organic phase was stripped using a NH3·H2O solution. The concentration of WO3 in solution was determined with ICP-AES instrument.
The proposed experimental flow sheet is shown in Fig. 2.
3 Results and discussion
3.1 Leaching experiments
Tungsten can complex with phosphorus to form a soluble heteropoly compound having n(P):n(W) of 2:5-1:12, depending on the pH value. The existing literature shows that
was the only species present below pH 1.5 [15]. Thus the leaching process for scheelite in HNO3-H3PO4 solutions can be described as follows:
12CaWO4+24HNO3+H3PO4=H3PW12O40+12Ca(NO3)2+12H2O (1)
As seen from reaction (1), both products (phosphotungstic acid and Ca(NO3)2) are soluble, which fundamentally avoid the tungstic acid precipitation and wrapping. In contrast to the classic leaching by hydrochloric acid, this method has a greater reaction rate without the influence of the solid H2WO4 coating layer. As shown in Fig. 3, the use of phosphoric acid noticeably increased the reaction rate and improved the dissolution of scheelite. The leaching efficiency was increased from 75.2% to 97.4% at 80 °C for 3 h with the addition of phosphorus.
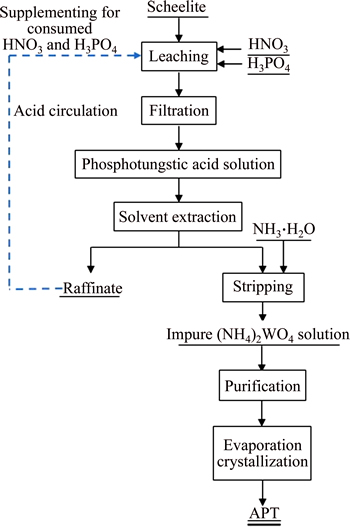
Fig. 2 Proposed flow sheet for recovery of W from scheelite
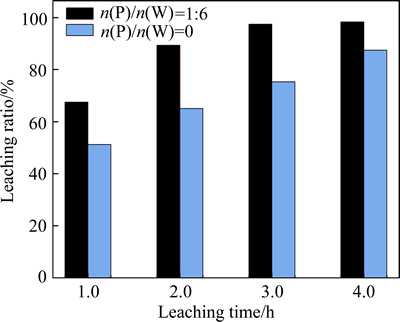
Fig. 3 Results of nitric acid leaching with and without phosphorus addition ([HNO3]=3.5 mol/L, 80 °C, liquild to soild ratio 10/1)
3.1.1 Effect of leaching conditions on tungsten extraction
Some leaching parameters, such as temperature, HNO3 concentration, leaching time and H3PO4 dosage, were investigated with a constant liquid-to-solid ratio (L:S) of 10:1 and stirring speed of 300 r/min. The result was presented in Fig. 4. The effect of temperature was evaluated for three concentrations of HNO3, namely 2.5 mol/L, 3.5 mol/L and 4 mol/L. The experimental data revealed that the extraction of tungsten was significantly sensitive to temperature and increased continuously with increase in temperature while this effect was much more at lower than at higher temperatures above 80 °C (Fig. 4(a)). The attained tungsten recovery was very satisfactory (up to 97%) at high acid concentrations (above 3.5 mol/L). By contrast, the leaching ratio was always below 90% at lower acid concentration (2.5 mol/L), even at relatively high temperature (90 °C).
A series of leaching tests was implemented with different HNO3 concentrations to determine the effect of HNO3 concentration at 70 °C and 80 °C. It was observed that the leaching of W is strongly dependent on the increase in the HNO3 concentration (Fig. 4(b)). At 80 °C the attained tungsten leaching ratio for 0.75 mol/L HNO3 was only 4.8%, but this value increased to 98.81% at 4.0 mol/L HNO3. Although the increase of HNO3 concentration could improve tungsten recovery, the maximum value was still below 90% even with HNO3 concentration of 4.0 mol/L at lower temperature (70 °C).
As results shown in Fig. 4(c), the leaching ratio of tungsten had a positive correlation with leaching time, and it was 97.39% when leached for 3 h. There was a marginal improvement with prolonging to 4 h. Figure 4(d) presents the relationship between the dosage of H3PO4 and leaching results, showing that the increase of H3PO4 dosage has only limited effect on the decomposition when it is over the stoichiometric ratio of 2. However, the recovery of W decreased at the stoichiometric quantity caused by the formation of insoluble tungstic acid. Therefore, requirement of 3 times the stoichiometric H3PO4 is considered optimal to keep a stable leaching efficiency without the formation of solid tungstic acid. By some measures, H3PO4 as a chelating agent was consumed little and the imputed mass ratio of H3PO4-to-scheelite was just 0.08.
After a series of leaching tests, temperature and HNO3 concentration were proved to be the key factors for the leaching of scheelite. This agreed with the results reported in the kinetics study by our team [16]. In order to investigate more detail of the interaction between the two factors, a more extensive study on leaching experiments was conducted where scheelite concentrate was decomposed with liquild to soild ratio of 10:1, H3PO4 dosage of 3 stoichiometric ratio and leaching time of 3 h. The results in Fig. 5 show that the tungsten recovery can be stabilized over 97% under the conditions of 80-90°C, HNO3 concentration 3.0-4.0 mol/L. In summary, the conditions for the leaching of scheelite concentrate, as determined from the leaching experiments, are obtained as follows: leaching temperature of 80-90 °C, HNO3 concentration of 3.0-4.0 mol/L, leaching time of 3 h, H3PO4 dosage of 3 stoichiometric ratio and Liquild to Soild ratio of 10:1.
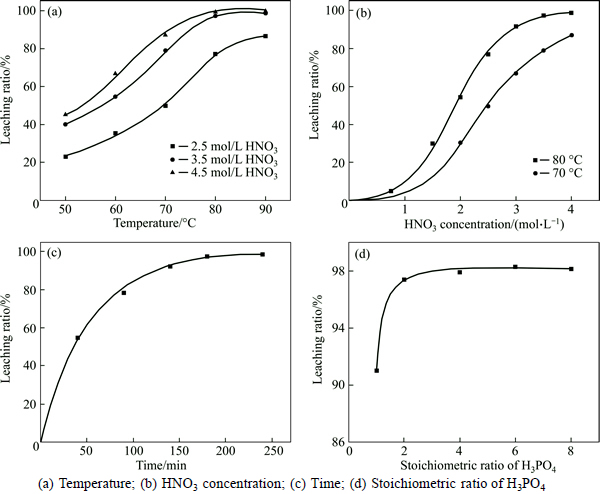
Fig. 4 Effect of leaching conditions on tungsten extraction:
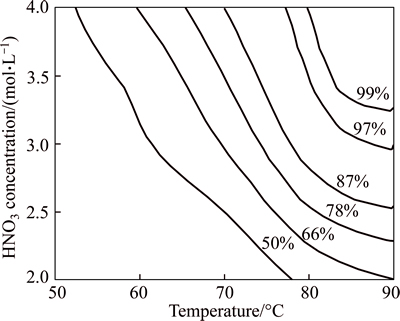
Fig. 5 Effect of temperature and HNO3 concentration on tungsten extraction
3.1.2 Adaptability
The resource of the scheelite in China is characterized with complicated components, low grade and high content of impurity [17]. For instance, the scheelite is usually accompanied with calcic minerals, such as fluorite, apatite and calcite in China’s Shizhuyuan W-Sn-Bi-Mo deposit. These minerals have similar floatability and usually mix into scheelite concentrate during beneficiation process. Therefore, various grades of scheelite, such as concentrate with grade of 60%, tungsten middlings with grade of 40%-50% and low grade scheelite, were produced. Moreover, scheelite concentrates produced form different mineral deposits have different compositions and features. Therefore, it will be necessary to investigate the leaching efficiency of various materials in this system. The results is illustrated in Table 2. It was observed that these four scheelite concentrates have been decomposed with high decomposition of tungsten and can be steadily more than 96% under the conditions of 80-90 °C, HNO3 concentration 3.0-3.5 mol/L. The maximum value of tungsten extraction reached 99.53%. It was also shown that this method has wide adaptability and is suitable to treat various scheelite concentrates.
3.2 Recovery of tungsten from leachate
The scheelite concentrate was decomposed with leaching temperature of 80 °C, an liquild to soild ratio of 10:1, an HNO3 concentration of 3.5 mol/L, an H3PO4 dosage of 3 stoichiometric ratio and a leaching time of 3 h. The WO3 in the filtrated liquor (65.9 g/L) needs to transform from phosphotungstic acid into the ammonium salt. Thus, a step may be required to extract and enrich tungsten from the solution. Such steps usually involve ion exchange or solvent extraction. As we know, N235 is a widely used extractant in acid system, especially in the extraction of W and Mo. In this study, the organic system of 40% (v/v) N235, 30% (v/v) TBP, and 30% (v/v) sulfonated kerosene was used to extract W from the solution. The phosphotungstic acid was extracted according to the following reaction.
Table 2 Result of experiments with various materials
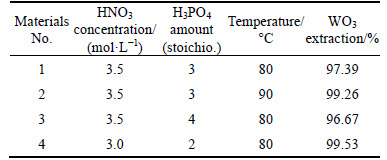

(2)
The conditions for the solvent extraction were a contact time of 10 min, a temperature of 20 °C, and an O:A ratio of 1:1.5. Approximately 99.93% of W can be extracted. After stripping by ammonia (7 mol/L) for 10 min at a temperature of 40 °C and an O:A ratio of 2:1, a stripping liquor containing approximately 193 g/L WO3 was obtained, while the stripping of W was 98.10%.
3.3 Recycling of leaching reagent
The lixivium was treated by solvent extraction and the raffinate containing residual acid. The direct discharge of this acid solution would result in serious environmental problem and a waste of resource. As considered from environment protection and energy save, it is advisable to study the reuse of leaching agent. Therefore, the cycle leaching step was designed. In lab-scale tests, the raffinate is returned for a new round of scheelite leaching by supplementing the consumed HNO3 and H3PO4 to initial level under optimal conditions verified in the first leaching experiment.Table 2 illustrates the leaching efficiency of four leaching cycles. It was assumed that the leaching efficiency was not affected during the process of four cycles, in which the extraction of W kept approximately 97%. The acid circulation greatly decreases the leaching cost and discharge of waste water.
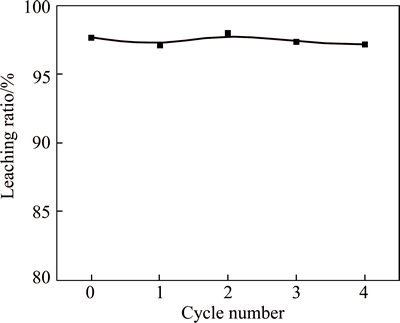
Fig. 6 Extraction of tungsten during cycle leaching process
4 Conclusions
1) Using HNO3 as leaching reagent overcomes the serious problems associated with corrosion in contrast to the classic leaching with HCl. And using H3PO4 as chelating agent fundamentally avoids the tungstic acid precipitation and wrapping.
2) More than 97% W could be extracted from scheelite with leaching temperature of 80-90 °C, HNO3 concentration of 3.0-4.0 mol/L, liquild to soild ratio of 10:1, H3PO4 dosage of 3 times stoichiometric ratio and leaching time of 3 h. Solvent extraction technology was employed for the W recovery from the leachate with the organic system of 40% (v/v) N235, 30% (v/v) TBP, and 30% sulfonated kerosene. Approximately 99.93% of W was extracted and ammonium tungstate solution containing 193 g/L W was obtained with a stripping rate of 98.10%.
3) This method has wide adaptability and is suitable for treating various scheelite concentrates with different grade and source.
4) The leaching efficiency remained unaffected and stabilized around 97% during 4 leaching cycles. The recycling of nitric acid was realized in the process. The consumption of HNO3 roughly equal to the theoretical amount. H3PO4 was consumed very little and the imputed mass ratio of H3PO4 to scheelite was just 0.08. All demonstrate that the process has low leaching cost and waste water discharge.
References
[1] LASSNER E, SCHUBERT W D. Tungsten properties, chemistry, technology of the element, alloys, and chemical compounds [M]. New York: Kluwer Academic/ Plenum Publishers, 1999.
[2] LIU Liang-xian. China’s tungsten resources and mining status [J]. China Tungsten Industry, 2012, 27(5): 4-8. (in Chinese)
[3] ZHAO Zhong-wei, LI Jiang-tao, WANG Shi-bo, LI Hong-gui, LIU Mao-sheng. Extracting tungsten from scheelite concentrate with caustic soda by autoclaving process [J]. Hydrometallurgy, 2011, 108: 152-156.
[4] ZHAO Zhong-wei, LIANG Yong, LIU Xu-heng, CHEN Ai-liang, LI Hong-gui. Sodium hydroxide digestion of scheelite by reactive extrusion [J]. Int. Journal of Refractory Metals and Hard Materials, 2011, 29: 739-742.
[5] LI Hong-gui. The progress of tungsten concentrate decomposition technique in China and future direction [J]. China Tungsten Industry, 1996, 12: 46-49. (in Chinese)
[6] QUENEAU P B, BECHSTEAD L W, HUGGINS D K. Autoclave soda digestion of scheelite concentrates with feedback control: US, 4325919 [P]. 1982-04-20.
[7] QUENEAU P B, BECHSTEAD L W, HUGGINS D K, BECHSTEAD L W. Autoclave soda digestion of refractory scheelite concentrates: US, 4320095 [P]. 1982-03-16.
[8] LI Hong-gui, YANG Jian-gao, LI Kun. Tungsten metallurgy [M]. Changsha: Central South University Press, 2010. (in Chinese)
[9] FANG Qi. Decomposition of scheelite with NaOH in autoclaving [J]. China Tungsten Industry, 2001, 16(6): 80-81. (in Chinese)
[10] FORWARD F A, VIZSOLYI A I. Process for the production of tungstic acid: US, 3193347 [P]. 1965-07-06.
[11] MO Si-hao. Tungsten metallugical principle & process [M]. Beijing: Light Industry Press, 1984: 63-79. (in Chinese)
[12] XUIN G H, YU D Y, SU Y F. Leaching of scheelite by hydrochloric acid in the presence of phosphate [J]. Hydrometallurgy, 1986, 16: 27-40.
[13] G
RMEN S, TIMUR S, ARSHN C, DUMAN I. Acid leaching of scheelite concentrate and production of heteropoly-tungstate salt [J]. Hydrometallurgy, 1999, 51: 227-238.
[14] KAHRUMAN C, YUSUFOGLU I. Leaching kinetics of synthetic CaWO4 in HCl solutions containing H3PO4 as chelating agent [J]. Hydrometallurgy, 2006, 81: 182-189.
[15] SMITH B J, PATRICK V A. Quantitative of aqueous dodecatung stophosphoric acid speciation by NMR spectroscopy [J]. Australian Journal of Chemistry, 2004, 57: 261-268.
[16] ZHANG Wen-juan, LI Jiang-tao, ZHAO Zhong-wei. Leaching kinetics of scheelite with nitric acid and phosphoric acid [J]. International Journal of Refractory Metals and Hard Materials, 2015, 52: 78-84.
[17] LV Ying, LI Hong-gui. Utilize tungsten concentrates of high molybdenum rationally [J]. China Tungsten Industry, 2005, 20(5): 15-16. (in Chinese)
(Edited by YANG Hua)
Foundation item: Project(51334008) supported by the National Natural Science Foundation of China
Received date: 2015-12-06; Accepted date: 2016-03-22
Corresponding author: ZHAO Zhong-wei, PhD, Professor; Tel: +86-731-88830476; E-mail: zhaozw@csu.edu.cn