J. Cent. South Univ. (2017) 24: 303-310
DOI: 10.1007/s11171-017-3431-6

Friction properties of groove texture on Cr12MoV surface
WANG Jing(王敬)1, 2, ZHOU Jie(周杰)1, ZHU Shan-shan(朱姗姗)1, ZHANG Jian-sheng(张建生)1
1. School of Materials Science and Engineering, Chongqing University, Chongqing 400044, China;
2. Department of Automotive Engineering, Chongqing Technology and Business Institute, Chongqing 400052, China
Central South University Press and Springer-Verlag Berlin Heidelberg 2017
Abstract: To analyze the influence of surface texture on friction properties of Cr12MoV’, ordinary grinder and spinning technology were adopted to obtain the grooved surface morphology of samples, and then the impact of spindle speed and feed in z-direction on surface morphology in the process of spinning was studied. In addition, the corresponding friction coefficient of sample was obtained through friction and wear tests. The results show that the peak clipping and the valley filling were conducted on the grinding surface, which could improve the surface roughness effectively and make the grinding trench-type wear scar more uniform. Both the area ratio of groove and groove spacing increased initially and then decreased with the increase of the spindle speed or the feed in z-direction. As a kind of micro-process, the groove could influence the friction coefficient of sample surface, whose distribution was beneficial to the reduction of friction coefficient. Compared with the surface obtained through ordinary grinding, grooved surface morphology through spinning technology was more conductive to reduce the friction coefficient, which could be reduced by 25%. When the friction coefficient of sample was reduced to the minimum, the texture of groove corresponded had an optimal area ratio and an optimal groove spacing, 37.5% and 27.5 μm, respectively.
Key words: groove texture; spinning; friction coefficient; area ratio; groove spacing
1 Introduction
As the foundation of industrial development, the quality of mold is indispensable for realizing mass production and the development of new products. To a great extent, die decides the quality, efficiency, and developing ability of a new product. Therefore, the level of mold production has become an important factor to measure the level of a country’s manufacturing. In order to lower the production cost, to improve the quality and efficiency of production, to improve the utilization ratio of material, and to save energy, various new molding processes are substituted for the traditional machining technology worldwide, such as precision stamping, precision forging, pressure casting, cold extrusion, hot extrusion, and isothermal superplastic forming. 60%–80% of the parts are produced by molding in the area of electronics, automobile, motor, electrical appliance, instrument, and communications products. Those products have high accuracy requirements, high complexity, high consistency, high productivity, and low consumption, which precede the manufacturing method of other processing [1].
Cold forming mold plays an important role in modern industrial applications, which is mainly used for pressing, cold drawing, stamping molding under cold state. Cold stamping technology is the mature forming technology, and its output accounts for 1/3 of mold production. Compared with other molding technology, cold stamping technology is widely applied in various industrial production and manufacturing because of its low production cost, simple production process, improved product quality, overall appearance of environment and enterprise and so on [2]. As a kind of die steel, cold working die steel, is mainly used for cold forming, such as cold stamping die, cold drawing die, cold heading die, and cold extrusion die [3]. The friction properties of cold stamping die have great influence on the product quality of cold stamping, cold drawing, and cold extrusion. Unreasonable friction coefficient can cause various defects, such as wrinkling, failure and underfilling. Therefore, it is quite important to study the friction properties of die surface. Surface texture refers to micro-dimple or micro-grooves with certain size and order on the surface of friction pair.
Surface texture can cause hydrodynamic pressure to reduce friction and improve the surface bearing capacity by storing lubricating oil, which has been proved to be an effective way to improve the surface tribological performance [4–6]. In recent years, with the development of laser machining and electro-chemical machining,
precise machining of surface texture can be realized. The research on the influence of surface texture on friction performance has become a world focus. HUA et al [7] used laser texturing to study the wet friction and wear behavior of DF2 tool steel under different loading conditions. VILHENA et al [8] compared the performance of samples with non-textured surface and laser surface texturing discs with different dimple depths, and found that tribological behavior depended on the depth of the micro-dimples as well as on the lubrication mode. DING et al [9] studied the surface texture to improve the friction performance of DLC films in water-lubricated condition, which reduced the friction coefficient.
For the friction properties of surface texture, published researches mostly focus on sliding bearing, piston, and cylinder liner [10-13], whereas studies on cold forming die are rare. Moreover, studies on friction properties of grooved surface morphology are fewer [14-16], while the shapes of texture are mostly regular- shaped pits or salient. AMANOV et al [14] investigated the influence of bulges around the dimples rim on the sliding friction and wear behavior [14]. YAN et al [15] studied the effect of dimple parameters on the friction properties of specimen surface through orthogonal method. WANG and HAN [16] studied drag reduction by dimples on surfaces in plane-plane contact lubrication. GANGOPADHYAY et al [17] compared the effect of friction performance between wear patterns on cam lobes tested against production shims and shims with parallel line V-grooves. In order to improve the friction performance of cold forming die, this work studied the influence of groove type topography on friction performance of Cr12MoV cold die steel that was treated through grinding process and spinning technology under oil lubrication.
2 Friction and wear tests
2.1 Materials and specification
Cold die steel, Cr12MoV, was adopted in this work as experimental material and its hardness could reach about HV700 after quenching. The samples’ surfaces were ground on ordinary grinder. The axial speed of grinding was 5 mm/s. The rotating speed of grinding wheel was 1000 r/min and the surface roughness after grinding was about 5.5. Then, spinning processing was applied to the part of grinding surface using NC machine tool, and the samples were cut to dimensions of 30 mm× 10 mm×5 mm finally.
2.2 Sample preparation methods
Samples for friction and wear tests were prepared by two kinds of surface treatments. First group was just treated through ordinary grinding (No.0), and the second group was treated through spinning processing after ordinary grinding treatment (No.1–No.9). Therefore, two groups of samples with different surface morphologies were obtained and the process of surface treatment is shown in Fig. 1. During the process of cold pressing, oil lubrication was applied. The ball diameter of machining tool was 10 mm, the spindle speed and the feed in z-direction were different for each group; nevertheless, the feed speeds in x-direction and y- direction were invariant, 800 mm/min and 0.1 mm/s, respectively. The relationship between sample numbers and parameter information is listed in Table 1.
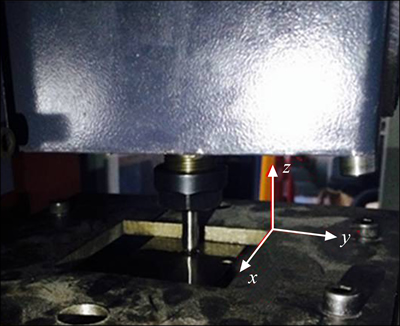
Fig. 1 Surface treatment of samples
Table 1 Sample number and parameter information
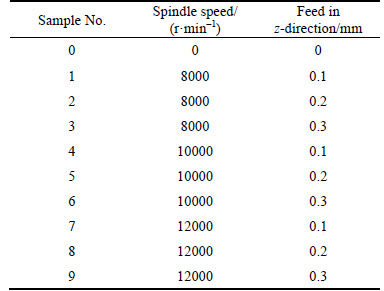
2.3 Friction and wear tests
The friction and wear tests were conducted on machine, as shown in Fig. 2. Two samples were needed: the upper sample was cylindrical pin made of GCr15 (d=6 mm) and its hardness was HRC 65; the lower one with the same parameters was self-made sample which has the mechanical properties just as mentioned in part 2.1. In the process of tests, the contacting way of two samples was surface contacting. The two samples moved rectilinearly twice during one circle of motor rotation. The friction direction followed the groove direction of sample surface. The friction test had a friction frequency of 5 Hz, a load of 60 N and a friction time of 300 s. Rich oil lubrication was used between the upper and lower samples, which meant that abundant lubricating oil was dropped on the friction surface of the lower sample and Hasta 5# oil (made in Shanghai of China) was selected as the lubricating oil.
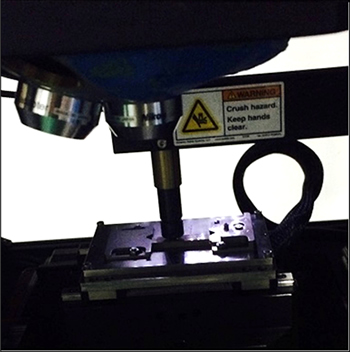
Fig. 2 Friction and wear test
3 Results and discussion
3.1 Influence of spinning technology on surface of sample
3.1.1 Influence of spinning technology on surface roughness
Figure 3(a) shows the schematic diagram of spinning process; Figure 3(b) shows the relationship among the surface roughness and the spindle speed and the feed in z-direction. Sample No. 0 had no feed in z-direction. The surface roughnesses of samples No. 0– No. 9 decreased significantly and presented a downward trend with the increase of spindle speed and the feed in z-direction in spinning processing. This is because the ball-end cutter makes residual wear scar more uniform during the process of rotation and feed, which are the peaking clipping and the valley filling, just as shown in Fig. 3(a). After spinning, the wear scar had a certain degree of reduction and the sample surface was smoother. Moreover, higher speed and greater amount of feed made the peaking clipping and valley filling further intensive. However, an excessive spindle speed would increase the friction heat between the ball and sample dramatically, which led to pitting corrosion and quality reduction of die surface. Meanwhile, an excessive incline of feeding in z-direction would increase the residual stress of surface remarkably, which was also detrimental to surface quality. Therefore, a rational control speed and the feed in z-direction are significance to improve the surface quality of samples effectively.
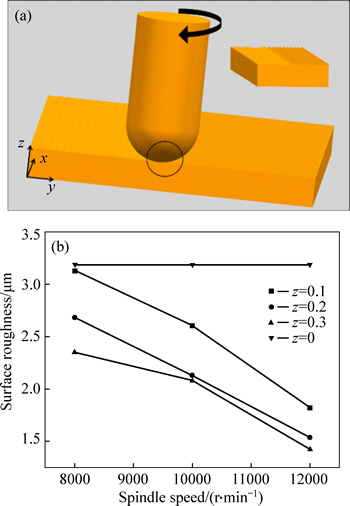
Fig. 3 Schematic diagram of spinning process (a) and relationship among surface roughness and spindle speed and feed in z-direction (b)
3.1.2 Influence of spinning technology on surface morphology
After ordinary grinding, the grinding wheel made the sample surface become grooved wear scars. Also, due to the effect of ball-end cutter, those wear scars showed plastic deformation, which made some degree of peak clipping and valley filling. The groove treated by spinning technology was better distributed than at untreated. The surface morphology of samples and the height curve of profile were obtained on Olympus confocal laser scanning microscope (LEXT-OLS410), and the surface morphologies of samples are shown in Table 2.
In order to make research on the friction properties of samples, the surface morphology of samples should be quantified. In order to further research the friction properties of the specimen, this work adopted the area ratio of groove, f, and the spacing of groove, d, to quantify the surface morphology of sample, and they could be described as Eqs. (1) and (2). The quantitative method was: selecting the five largest peaks and five lowest valleys in the height curve of the profile, and using the five highest peaks and the five deepest valleys as limits to determine the depth of groove; then intercept the section curve in the half depth of groove and
calculate the intercept of peaks and the intercept of valleys, respectively. S was the sum of intercepts of each valley; the length of line was 1200 mm; f was the area ratio of groove; D was the sum of intercepts of each peak; n was the number of peaks; d was the spacing in groove.
The area ratio of groove is


(1)
The spacing of groove is

=48.5 μm (2)
Using the same method to characterize other samples, the area ratio of groove and the groove spacing are obtained, just as shown in Table 3. The samples were ordinary grind and its height curve of profile is shown in Fig. 4.
Table 2 Surface morphology of each sample (unit: μm)
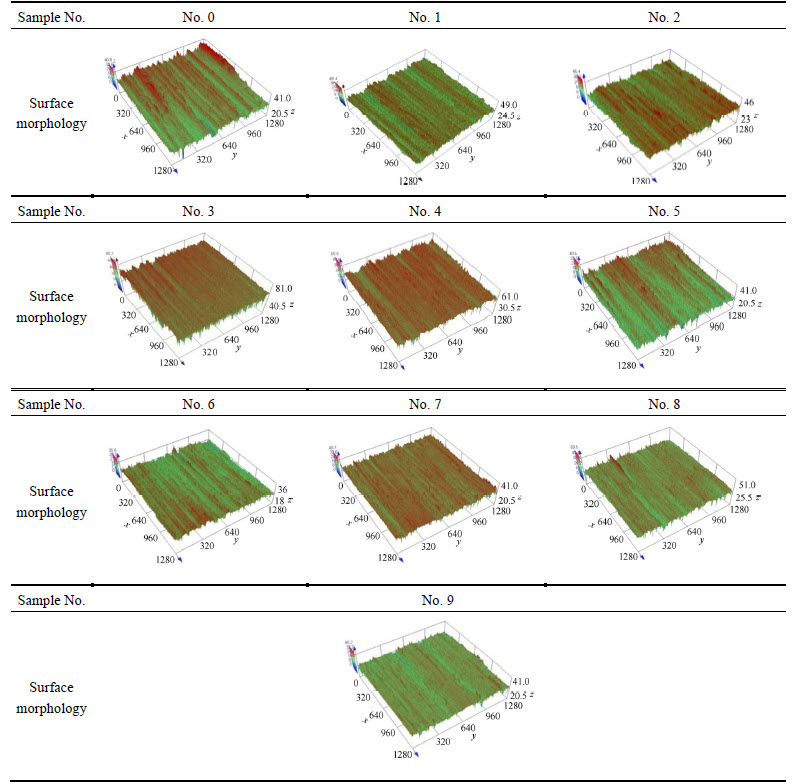
Figure 5(a) shows the relationship among the area ratio of groove, the spindle speed, and the feed in z-direction. Figure 5(b) shows the relationship among the spacing in groove, the spindle speed,and the feed in z-direction. Figure 5 shows that both area ratio and groove spacing of samples No. 0–No. 9 treated with spinning are lower than those of sample No. 0, which indicates that the spinning technology could make the sample surface well-distribute. Both the area ratio of groove and groove spacing increase firstly, then decrease with the increase of spindle speed, but they decrease with the increasing feed in z-direction. After spinning treatment, the shallow wear scar will disappear and the deep wear scar also will weaken in depth and width. Therefore, the area ratio of sample surface and the spacing in groove are lower than before, and related to the rotation and feed of ball-end cutter.
Table 3 Area ratio of groove and spacing in groove
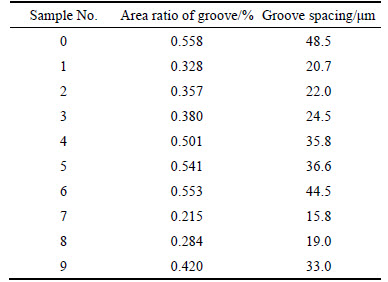
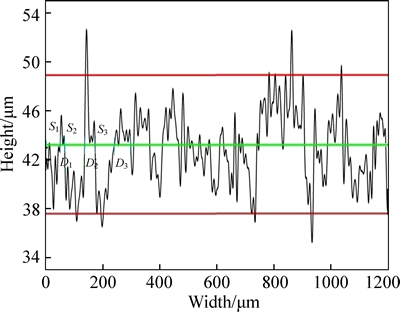
Fig. 4 Characterization of ordinary grind samples and height curve of its profile
Figure 6 shows the mechanism diagram of spinning processing. h is the feed of ball-end cutters in z-direction. H is the feed of grinding in z-direction. A and B are the simultaneous areas of extrusion and rolling, respectively, namely pressure area. B and C are the areas of plastic deformation. The plastic deformation occurs with elastic deformation, which is also known as the elastic recovery area. Due to the high-speed rotation of ball-end cutters, the samples cause extrusion deformation as well as rolling in the areas of A and B. Rolling can refine the microstructure of surface and produce surface residual stress, which can improve surface hardness of the workpiece, carrying capacity, abrasion resistance, fatigue strength, and corrosion resistance; and make the surface more superior performance [18–20]. The feed of ball-end cutters in z-direction (i.e. the pushing amount of plane) isdirectly related to the spinning effect during the process of high speed spinning. The surface roughness will decrease with its increase usually. While it reaches a minimum value, the greater pushing amount of plane will produce larger plastic deformation, which leads to increasing surface roughness: a large area, deep grooves, and poor surface quality [21–23]. At the same time, the rotating speed of ball-end cutters will influence the surface planeness and surface quality of samples near the ball-end cutters, and the wear scar will be polished fleetly with the high rotation of ball-end cutter.
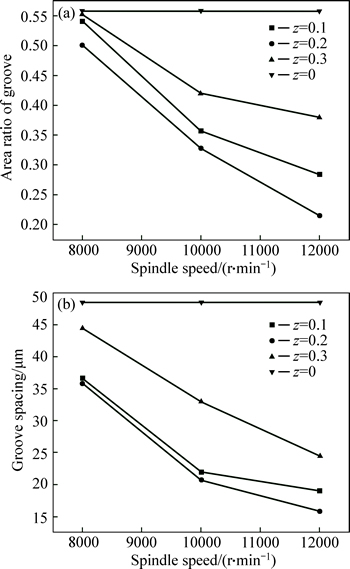
Fig. 5 Relationship among area ratio of groove (a) and groove spacing (b) and spindle speed and feed in z-direction
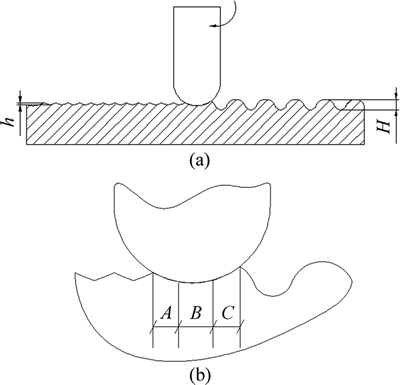
Fig. 6 Mechanism schematic diagram of spinning processing (a) and areas (b)
3.2 Influence of grooves on surface friction properties
Figure 7 shows the friction coefficient curves of each sample under the load of 60 N. As the curves shown in Fig. 7, instantaneous friction coefficient is far larger than that after being stable. Because instantaneous friction between upper and lower samples tends to static friction at the beginning of friction test, the coefficient of static friction is much larger than kinetic friction. The friction coefficients of samples No. 1 and No. 3 are greater, which are similar to that of sample No. 0 while the friction coefficients of No. 2 and No. 9 are slightly lower. Moreover, the friction coefficients of the rest samples are significantly lower than that of sample No. 0. The surface texture of artificial micro- processing is able to store lubricating oil and gather micro-wear particle, which can effectively reduce the abrasive wear and furrow. At the same time, in the case of lubricating oil, the surface texture contributes to the formation of hydrodynamic lubrication, which improves the carrying capacity and the tribological properties of surface effectively [24–26]. As one kind of micro- processings, groove also affects the friction coefficient of the sample surface. Figure 7 illustrates that the reasonable area ratio of groove and the groove spacing can reduce the friction coefficient of the sample.
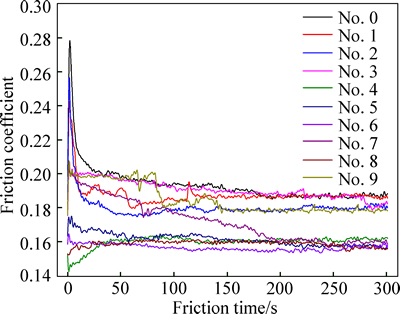
Fig. 7 Friction coefficient of each sample
3.2.1 Influence of groove area ratio on surface friction properties
Figure 8 shows the relationship between friction coefficient and area ratio of groove. The curve shows that the area ratio has a large impact on the friction coefficient under the same conditions of friction coefficient. The reasonable area ratio can reduce the friction coefficient of the sample, even up to 25%. With the increase of the area ratio (20%–60%), the friction coefficient of samples firstly decreases, and then gradually increases. Friction coefficient has an optimal value of 0.1575, and the corresponded optimal area ratio is 37.5%. When the area ratio of groove gradually increases from 20% to 40%, the main function of groove is used as storage of lubricating oil. In this case, the surface texture contributes to the formation of hydrodynamic lubrication, which improves the carrying capacity and the tribological properties of surface effectively. However, the mobility of lubricating oil will get better with the continuous increase of the area ratio (40%–60%), which leads to increase in difficulty in forming hydrodynamic lubrication and decline of bearing capacity of oil film [27–28]. Meanwhile, increasing occupancy rate of area will make the friction coefficient increase.
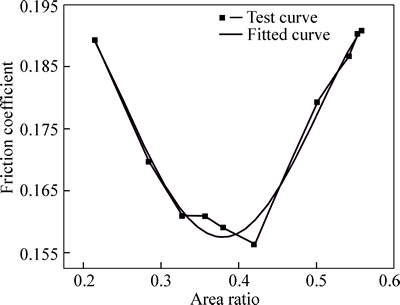
Fig. 8 Relationship between friction coefficient and area ratio of groove
3.2.2 Influence of groove spacing on surface friction properties
Figure 9 shows the relationship between friction coefficient and groove spacing. As the curve shown, the friction coefficient has greater influence on groove spacing under the same condition. The friction coefficient of the sample decreases before increasing gradually with the increase of groove spacing (15–50 μm). A minimum value of 0.155 corresponds to the optimal groove spacing of 27.5 μm. There is a corresponding relation that the greater groove spacing results in a smaller area ratio of the groove, and vice versa. According to the influence of the area ratio on friction coefficient, the groove spacing increases gradually from 15 μm to 30 μm (the area ratio of groove decreases from the maximum value to the optimal value gradually). Also, the fluidity of lubricating oil weakens gradually under the effect of groove, which is conductive to the formation of dynamic pressure oil film bearing oil film, the improvement of the carrying capacity of oil film, and the decrease of friction coefficient. As groove spacing (30–50 μm) increases, area ratio sustainedly reduces. Groove texture which can be used for storing lubricating oil will become less and less, and the friction coefficient will increase.
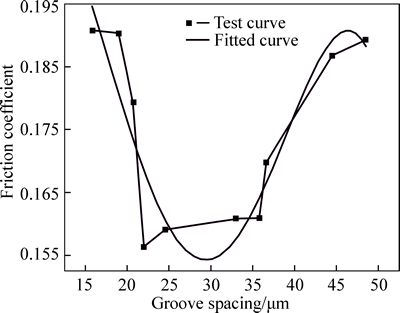
Fig. 9 Relationship between friction coefficient and groove spacing
4 Conclusions
1) In spinning process, the peaking clipping and the valley filling were conducted on wear scar by rotation and fed by ball-end cutter, which could effectively improve the surface roughness.
2) Spinning technology can produce a grooved distribution of sample surface. Both the area ratio of groove and groove spacing increase firstly, and then decrease with the increase of spindle speed. Also, they have the same change trend with the increase of feed in z-direction.
3) Compared with the surface obtained through ordinary grinding, grooved surface morphology obtained through spinning technology is more conductive to reduce the friction coefficient.
4) Under the effects of rich lubrication and surface contact, groove texture can reduce the friction coefficient of samples. The texture of groove has an optimal area ratio and an optimal distance, 37.5% and 27.5, respectively, at the friction load of 60 N and the frequency of 5 Hz.
References
[1] LI Shao-hong. Research of microstructure design and control on high strength high toughness cold work die steel [D]. Shanghai: Shanghai University, 2011. (in Chinese)
[2] OHKAWA Y. Cryogenic treatment of die [J]. TAO Wei-lin, trsl. Die and Mould Technology, 1990(1): 82–86. (in Chinese)
[3] LI Chen-hui, WU Xiao-chun, XIE Chen, WANG Hong-bin. Investigation on wear resistance of Cr8 tool steels [J]. Tribology, 2013, 33(1): 36–43. (in Chinese)
[4] LEI Shu-ting, DEVARAJAN S, CHANG Z. A study of micropool lubricated cutting tool in machining of mild steel [J]. Journal of Materials Processing Technology, 2009, 209(3): 1612–1620.
[5] RAEYMAEKERS B, ETSION I, TALKE F E. Enhancing tribological performance of the magnetic tape/guide interface by laser surface texturing [J]. Tribology Letters, 2007, 27(1): 89–95.
[6] PODGORNIK B, VILHENA L M, SEDLACEK M, REK Z,
I. Effectiveness and design of surface texturing for different lubrication regimes [J]. Mecanica, 2012, 47: 1613–1622.
[7] HUA Meng, DONG Guang-neng, ZHANG Hui, HO J K L, CHOW F. The wet tribological behaviors of doughnut patterns laser- textured on DF2 tool steel under different loading conditions [J]. Applied Physics A, 2013, 111(4): 997–1011.
[8] VILHENA L M, PODGORNIK B,
J, MOZINA J. Influence of texturing parameters and contact conditions on tribologicalbehaviour of laser textured surfaces [J]. Meccanica, 2011, 46(3): 567–575.
[9] DING Qi, WANG Li-ping, WANG Yong-xin. Improved tribological behavior of DLC films under water lubrication by surface texturing [J]. Tribology Letters, 2011, 41(2): 439–449.
[10] LOPEZ-CERVANTES A, DOMINGUEZ-LOPEZ I, BARCEINAS-SANCHEZ J D O, LUISGARCIA-GARCIAN A. Effects of surface texturing on the performance of biocompatible UHMWPE as a bearing material during in vitro lubricated sliding/rolling motion [J]. Journal of the Mechanical Behavior of Biomedical Materials, 2013, 20(4): 45–53.
[11] TALA-IGHIL N, FILLON M, MASPEYROT P. Effect of textured area on the performances of a hydrodynamic journal bearing [J]. Tribology International, 2011, 4(3): 211–219.
[12] TOMANIK E. Modelling the hydrodynamic support of cylinder bore and piston rings with laser textured surfaces [J]. Tribology International, 2013, 59: 90–96.
[13] GRABON W, KOSZELA W, PAWLUS P, OCHWAT S. Improving tribological behaviour of piston ring–cylinder liner frictional pair by liner surface texturing [J]. Tribology International, 2013, 61: 102–108.
[14] AMANOV A, TSUBOI R, OE H, SASAKI S. The influence of bulges produced by laser surface texturing on the sliding friction and wear behavior [J]. Tribology International, 2013, 60(7): 216–223.
[15] YAN Dong-sheng,QU Ning-song, LI Han-song. Significance of dimple parameters on the friction of sliding surfaces investigated by orthogonal experiments [J]. Tribology Transactions, 2010, 53(5): 703–712.
[16] WANG Jia-dao, HAN Zhong-ling. Drag reduction by dimples on surfaces in plane–plane contact lubrication [J]. Tribology Letters, 2008, 31(3): 159–166.,
[17] GANGOPADHYAY A, McWATT D G. The effect of novel surface textures on tappet shims on valvetrain friction and wear [J]. Tribology Transactions, 2008, 51(2): 221–230.
[18] LI Feng-lei, XIA Wei, ZHOU Zhao-yao. Auralization differences between individualized and non-individualized binaural room impulse responses [J]. Journal of South China University of Technology, 2008, 36(8): 98–103. (in Chinese)
[19] AKKURT A. Comparison of roller burnishing and other methods of finishing treatment of the surface of opening in parts from toll steel D3 for cold forming [J]. Metal Science and Heat Treatment, 2011, 53: 145–150.
[20] BABU P R, ANKAMMA K, PRASAD T S, RAJU A PRASAD N. Optimization of burnishing parameters and determination of select surface characteristics in engineering materials [J].
2012, 37(4): 503–520.
[21] TADIC B, TODOROVIC P M, LUZANIN O, NILJANI D, JEREMIC B M, BOGDANOVIC B, VUKELIC D. Using specially designed high-stiffness burnishing tool to achieve high-quality surface finish [J]. Int J Adv Manuf Technol, 2012, 67: 601–611.
[22] LUO Hong-yun, LIU Jian-ying, WANG Li-jiang, ZHONG Qun-peng. The effect of burnishing parameters on burnishing force and surface microhardness [J]. Int J Adv Manuf Techno, 2006, 28: 707–713.
[23] LACALLE L N L D,
, ARANA J L. The effect of ball burnishing on heat-treated steel and Inconel 718 milled surfaces [J]. International Journal of Advanced Manufacturing Technology, 2007, 32(10): 958–968.
[24] LI Yang, LIU Xiao-jun, WANG Qing-sheng, LIU Kun. Effect of laser textured surfaces on the frictional property in line contact [J]. Tribology, 2013, 33(4): 349–355. (in Chinese)
[25] YU Hai-wu, WANG Xiao-lei, SUN Zao, YUAN Si-huan..Theoretical analysis on hydrodynamic lubrication of cylinder micro-dimple surface texture [J]. Journal of Nanjing University of Aeronautics & Astronautics, 2010, 42(4): 209–213. (in Chinese)
[26] CORDIER ROBERT C, CRAMPON J, FOCT J. Surface alloying of iron by laser melting: Micro structure and mechanical properties [J]. Surface Engineering, 1998, 14(5): 381–385.
[27] YIN Bi-feng, QIAN Yan-qiang, DONG Fei-lu, LU Zhen-tao. Simulative and experimental research on tribological property of micro-groove typed textures [J]. Lubrication Engineering, 2012, 37(12): 9–13. (in Chinese)
[28] CHEN Hao-sheng, LI Yong-jian, CHEN Da-rong. Numerical analysis on effect of regular surface topography in non-newtonian fluid lubrication [J]. Chinese Journal of Mechanical Engineering, 2007, 43(8): 48–52. (in Chinese)
(Edited by YANG Hua)
Cite this article as: WANG Jing, ZHOU Jie, ZHU Shan-shan, ZHANG Jian-sheng. Friction properties of groove texture on Cr12MoV surface [J]. Journal of Central South University, 2017, 24(2): 303-310. DOI: 10.1007/s11171-017- 3431-6.
Foundation item: Project(51275543) supported by the National Natural Science Foundation, China; Project(KJ1603804) supported by the Research Projects of Chongqing Commission of Science and Technology, China
Received date: 2015-10-08; Accepted date: 2016-05-11
Corresponding author: ZHOU Jie, Professor; Tel: +86-13983198835; E-mail: zhoujie@cqu.edu.cn