J. Cent. South Univ. Technol. (2008) 15: 753-756
DOI: 10.1007/s11771-008-0139-z
Pyrolysis of furfural-acetone resin as matrix precursor for
new carbon materials
XIA Lun-gang(夏伦刚), ZHANG Hong-bo(张红波), XIONG Xiang(熊 翔),
ZUO Jin-lü(左劲旅), YIN Jian(尹 健)
(State Key Laboratory of Powder Metallurgy, Central South University, Changsha 410083, China)
Abstract: In order to increase the understanding of the pyrolysis mechanism, Fourier transform infrared spectroscopy (FT-IR) and thermogravimetry-mass spectrometric coupling technique (TG-MS) were used to study the pyrolysis behavior of furfural-acetone resin used for new carbon materials. The curing and carbonization mechanisms of furfural-acetone resin were mainly investigated; structural changes and volatile products evolved during pyrolysis were analyzed. The results indicate that, during pyrolysis of furfural-acetone resin adding 7% (mass fraction) phosphorous acid as curing agent, the rupture of C—O bond in the five-membered heterocycle firstly takes place to release oxygen atoms and then does the C—H bond, which enable the molecular chain to cross-link and condense, then lead to the formation of three dimensional networking structure. With the increase of pyrolyzing temperature, the scission of methyl and the opening of furan ring are generated. As a result, the recomposition of molecular chain structure is generated and a hexatomic fused ring containing double bonds is built. The main volatile products during pyrolysis of furfural- acetone resin are H2O, and a small mount of CO, CO2 and CH4. At elevated temperatures, dehydrogenation takes place and hydrogen gas is evolved.
Key words: new carbon materials; furfural-acetone resin; pyrolysis; volatile products
1 Introduction
Organic polymer is one of the most primary sources of carbon precursors for new carbon materials, such as carbon/carbon (C/C) composites and glasslike carbon materials. Currently, the main organic polymers widely used for carbon precursors of new carbon materials are phenolic resins, condensed polynuclear aromatic (COPNA) resin, polyacrylonitrile and furan resins[1]. Furan resins refer to a family of thermosetting resins
containing furan ring like
in their molecular
structure. Furan resins are commonly produced by polycondensation of furfurals or furfuryl alcohols. They have not only excellent corrosion resistance and heatproof characteristic, but also high carbon yields. So they have been widely applied in a variety of fields for a long time. Furfural-acetone resin is one kind of furan resins and is known as an excellent polymeric precursor for C/C composites and glasslike carbon materials[2-3].
The thermal degradation of matrix precursors is an important step in the manufacture of new carbon materials. The pyrolysis process converts the furan matrix to amorphous carbon. The potential for damage
during this processing step is great due to the development of stress in the materials. There are a series of complicated reactions during thermal degradation of furan resin. Generally, the thermal degradation process is divided into two stages: curing stage at lower temperatures and carbonization stage at higher temperatures. Invariably a variety of volatile compounds are released during the thermal degradation reaction, which can cause great volume expansion of the sample and some flaws in it, such as pores and cracks[4-8]. So it is quite important to investigate the thermal degradation mechanisms of furan resins for improving the producing procedure and the quality of the resulting products. Because of the differences of the raw materials and producing procedures selected by the researchers, the thermal degradation mechanisms of furan resins are more or less different. The common methods of mechanism investigation are Fourier transform infrared spectroscopy (FT-IR), thermogravimetry (TG), differential scanning calorimetry (DSC), thermal volatilization analysis (TVA), thermogravimetry-mass spectrometric coupling technique (TG-MS), etc[9-10]. In this study, the FT-IR and TG-MS techniques were used to give physical and chemical insights into the thermal decomposition of furfural-acetone resin, and the curing and carbonization mechanisms were primarily revealed.
2 Experimental
2.1 Raw materials and sample preparation
FA-2 furfural-acetone resin was provided by Changshu Duwei Chemical Plant, China. It was produced by equal mole ratio of furfural to acetone using alkali as catalyzer. The viscosity (25 ℃) was 40-150 mPa/s; water content was ≤1% and grey yield was ≤3%. The curing agent was industrial phosphorous acid with concentration of ≥85%.
The curing agent was added and the mixture was stirred for 10 min in order to yield a homogeneous mixture. The mixture held in a graphite pot was put in an oven and cured stepwise at 90 ℃ for 2 h, then at 120 ℃ for 4 h, and at 180 ℃ for 2 h in the end. The apparently compact and hard cured bulk sample was obtained.
The cured sample with the graphite pot was heated in a vacuum furnace at a programmed rate up to 850℃, then kept for 3 h. The carbonized sample was obtained and cooled down to room temperature.
2.2 FT-IR measurement
The FT-IR spectra of virgin furfural-acetone resin, cured and carbonized samples were obtained using a Nicolet AVATR360 spectrophotometer in the wave- number range of 4 000-400 cm-1. Liquid sample was tested directly or after diluted with tetrachloromethane, and solid samples were tested with potassium bromide pressed disc method.
2.3 TG-MS measurement
TG-MS apparatus consisted of a SETARAM TGA92 thermal gravimetric analyzer made in France with accuracy of 1 μg and a Balzers Omnistar mass spectrometric analyzer made in Switzerland with scanned molecular mass range of 1-300.
About 19.46 mg furfural-acetone resin with 7% (mass fraction) curing agent was held in a alumina pan, then the argon gas was flowed to expel the air for certain time until the baseline was smooth. The sample was pyrolyzed in an argon flow of 100 mL/min at a heating rate of 5 ℃/min from room temperature to 1 000 ℃.
3 Results and discussion
3.1 FT-IR analysis
The main structural unit of the furan resin molecule is furan five-membered heterocycle containing carbon, hydrogen and oxygen elements. Because in the heteroatom of furan ring, such as oxygen, unpaired electrons can participate in the six-membered conjugate system, furan resins have similar characteristic of polymers with aromatic rings and some kinds of reactions are able to take place. But they are more active than aromatic compounds because the participation of lone pair electrons in the conjugate system of five-membered heterocycles enables the lone pair electrons to flow to the carbon atoms easily, which makes them more active in electrophilic substitution reactions than aromatic compounds. That is to say, the hydrogen atoms are vulnerable to be substituted or to escape. Therefore, in the same heating condition the speeds of curing and carbonization of furan resins are always faster than those of other resins with aromatic rings[11].
The FT-IR spectrum of virgin furfural-acetone resin is shown in Fig.1. The FT-IR spectra of cured and carbonized samples are shown in Fig.2. According to Refs.[12-15], the peaks in the spectra can be assigned and listed in Table 1. Compared with the IR spectrum of virgin furfural-acetone resin, in the spectrum of cured sample the characteristic peak of —OH group at 3 121 cm-1 is obviously weakened; the characteristic peak of C—H bond in-plane deformation of the aromatic ring at 971 cm-1 and the ones of C—H bond out-of-plane deformation around 881 cm-1 and 750 cm-1 almost disappear. These results indicate that the hydroxyl groups and active hydrogen atoms in the furan molecules disappear, and that dehydration-condensation takes place.
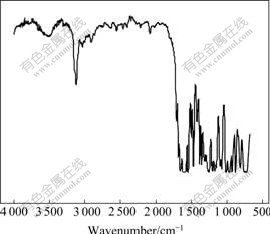
Fig.1 FT-IR spectrum of virgin furfural-acetone resin
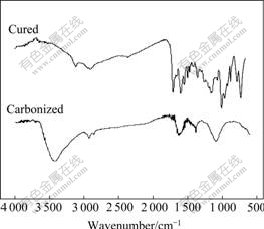
Fig.2 FT-IR spectra of cured and carbonized samples
Table 1 Peak identification of FT-IR spectra
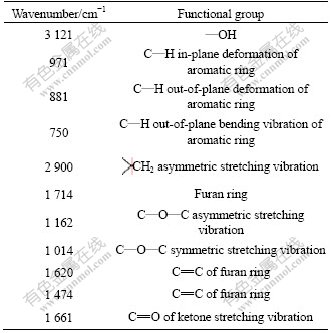
There is also characteristic peak of
CH2 group
asymmetric stretching vibration at 2 900 cm-1, which reveals that there is still characteristic group of acetone in the cured sample. Furthermore, it can be found that the intense characteristic peak related with furan rings at 1 714 cm-1 and the bands attributed to C—O—C asymmetric and symmetric stretching vibration at 1 162 and 1 014 cm-1 are all greatly weakened, which reveals the occurrence of curing reaction due to the opening of furan rings and cross-linking reaction. In addition, the bands related to C=C double bonds in furan rings at 1 620 and 1 474 cm-1 almost disappear, and the peak of C=O of ketone stretching vibration at 1 661 cm-1 is very weak, demonstrating that these groups also take part in the reaction.
In the FT-IR spectrum of carbonized sample, most of the characteristic peaks disappear or are greatly weakened, which indicates that this sample is transformed into very pristine resin carbon, and that the carbon structure is transformed into a more ordered type. Compared with the spectrum of cured sample, the bands associated with C=O stretching vibration of the ketone at 1 661 cm-1 and the bands corresponding to C—H out- of-plane bending vibration of aromatic rings at 750 cm-1 are further weakened. The cause is that most of the C=O bonds in the five-membered heterocycles are broken to release oxygen atoms, the C—H bonds are ruptured, which causes the recomposition of molecular chains. Meanwhile, it is worthy of notice that new absorption peak at around 3 432 cm-1 emerges. It can be speculated that new six-membered aromatic ring structure emerges and it is the foundation of the transformation into graphite structure. But further work is needed to confirm this statement.
3.2 TG-MS analysis
The results of TG-MS study are presented in Fig.3 (TG-DTG) and Fig.4 (MS). The TG curve of the sample shows two main mass losses in the temperature range from room temperature to 1 000 ℃. They are attributed to two stages: curing and carbonization, respectively. The curing reaction peak on the curve of DTG is high and narrow, indicating that the curing reaction is very acute and rapid and the curing time is very short. The onset and terminal temperatures of curing reaction are 111.27 ℃ and 199.8 ℃, respectively. The peak value of reactive speed is 2.332%/s at about 155 ℃. It can also be seen from Fig.4 that during curing process the main volatile products are H2O and a small amount of CO, CH4 and CO2. According to the former results of FT-IR spectra and Ref.[16], it can be concluded that when furan resin cures in the presence of phosphorous acid, the C—O bond of furan ring ruptures firstly to release oxygen atoms, then other C—H bonds rupture, and the cross-linking of molecular chains takes place to form a three-dimension networking structure. Meanwhile, water and other volatile products are evolved.
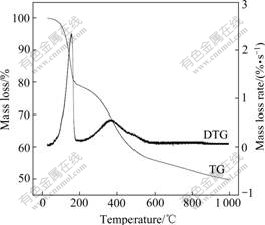
Fig.3 TG-DTG curves during pyrolysis of furfural-acetone resin
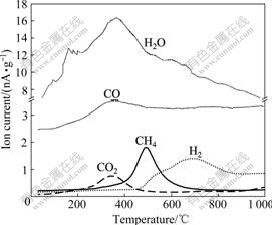
Fig.4 Evolution of volatile products during pyrolysis
With the further increase of pyrolyzing temperature from 200 ℃, cured sample undergoes a gradual decomposition and leads to carbonization. Fig.4 shows slow emissions of CO2, CO, H2O, CH4 and H2, with the peaks at around 340, 359, 367, 494 and 699 ℃, respectively. The carbonization is nearly over till 850 ℃, obtaining 51.8% carbon yields. According to Refs.[16-18], it can be concluded that the main reaction during pyrolysis of furfural-acetone resin is thermal condensation. With the rupture of methyl and the opening of furan ring, by-products like methane, carbon dioxide and carbon monoxide are generated; meanwhile, residual oxygen atoms are released in the form of water. At the end of thermal degradation a six-membered aromatic ring structure with double bonds emerges after the recomposition of furan molecules. At the same time dehydrogenation takes place, which will lead to the conversion into graphite-structure consulted by the previous FT-IR spectrum of carbonized sample.
4 Conclusions
1) The pyrolysis process of furfural-acetone resin mainly consists of two types of reaction: cross-linking with the opening of furan rings and thermal-condensation. During pyrolysis of furfural-acetone resin, the C—O bonds in the furan rings firstly rupture to release oxygen atoms, then other C—H bonds rupture, and cross-linking of molecular chains takes place to form a three-dimensional networking structure. With the rupture of methyl the opening of furan rings occurs; a six-membered aromatic ring structure with double bonds appears after the recomposition of furan molecules.
2) The pyrolysis process is divided into two stages: curing and carbonization. Curing reaction is obviously very acute and rapid, and its time is very short. Onset and terminal temperatures of curing reaction are 111.27 and 199.8 ℃, respectively. The peak value of reactive speed is 2.332%/s at around 155 ℃. The speed of carbonization reaction is slower than that of curing reaction with a wider temperature range. During the whole thermal degradation, H2O is a predominant volatile product followed by CO, CO2 and CH4. With the further increase of pyrolyzing temperature, dehydrogenation takes place to release H2.
References
[1] FU Dong-sheng, ZHANG Kang-zhu, SUN Fu-lin, YAO Dong-mei. Research progress in matrix precursors for carbon-carbon composites [J]. New Chemical Materials, 2003, 31(6): 19-21. (in Chinese)
[2] FU Xue. Resin and plastic [M]. Beijing: Chemical Industry Press, 2005. (in Chinese)
[3] BURKET C L, RAJAGOPALAN R, MARENCIC A P, DRONVAJJALA K, FOLEY H C. Genesis of porosity in polyfurfuryl alcohol derived nanoporous carbon [J]. Carbon, 2006, 44(14): 2957-2963.
[4] GUO Hua-jun, LI Xin-hai, ZHANG Xin-min, WANG Zhi-xing, PENG Wen-jie, ZHANG Bao. Optimizing pyrolysis of resin carbon for anode of lithium ion batteries [J]. J Cent South Univ Technol, 2006, 13(1): 58-62.
[5] TANABE Y, UTSUNOMIYA M, ISHIBASHI M, KYOTANI T, KABURAGI Y, YASUDA E. Oxidation behavior of furan-resin-derived carbon alloyed with Ta or Ti [J]. Carbon, 2002, 40(11): 1949-1955.
[6] ALAKHRAS F, HOLZE R. In situ UV–vis- and FT-IR-spectroscopy of electrochemically synthesized furan–thiophene copolymers [J]. Synthetic Metals, 2007, 157(2/3): 109-119.
[7] LI Zhi-hua, ZHENG Zi-qiao, REN Dong-yan, HUANG Yao-peng. Curing mechanism of TDE-85/MeTHPA epoxy resin modified by polyurethane [J]. J Cent South Univ Technol, 2007, 14(3): 296-300.
[8] XIONG Xiang, HUANG Bai-yun, XIAO Peng. Microstructures of unidirectional fibre-reinforced C/C composites fabricated by liquid method [J]. The Chinese Journal of Nonferrous Metals, 2003, 13(6): 1430-1434. (in Chinese)
[9] FIZER E, SCHAEFER W. The effect of cross-linking on the formation of glasslike carbon from thermosetting resin [J]. Carbon, 1970, 8(3): 353-364.
[10] WAITKUS P A, KORB L L. Process for preparing a vitreous carbon: US 4624811 [P]. 1986-11-25.
[11] WANG Shu-jun, ZHAO Fei-min. Study on the carbonized product of furfuralcohol resin as electrode materials of lithium ion batteries [J]. New Carbon Materials, 2000, 15 (3): 47-51. (in Chinese)
[12] HERNANDEZ V, RAMIREZ F J, ZOTTI G, NAVARRETE J T L. Resonance Raman and FT-IR spectra of pristine and doped polyconjugated polyfuran [J]. Chem Phys, 1992, 191(5): 419-422.
[13] SOCRATES G. Infrared characteristic group frequencies [M]. Chichester: John Wiley & Sons, 1980.
[14] ROBERT M, SILVERSTEIN, FRANCIS X, WEBSTER, KIEMLE D. Spectrometric identification of organic compounds [M]. Hoboken, NJ: John Wiley & Sons, 2005.
[15] LORENZ U J, LEMAIRE J, MAITRE P, CRESTONI M E, FORNARINI S, DOPFER O. Protonation of heterocyclic aromatic molecules: IR signature of the protonation site of furan and pyrrole [J]. International Journal of Mass Spectrometry, 2007, 267(1/3): 43-53.
[16] XIA Lun-gang, ZHANG Hong-bo, XIONG Xiang, ZUO Jin-lü, YIN Jian. Curing reaction of furfural acetone resin used for new carbon materials [J]. The Chinese Journal of Nonferrous Metals, 2008, 18(6): 953-958. (in Chinese)
[17] OZAKI J, OHIZUMI W, OYA A. A TG-MS study of poly(vinylbutyral)/phenol-formaldehyde resin blend fiber [J]. Carbon, 2000, 38(10): 1515-1519.
[18] BISWAS B, KANDOLA B K, HORROCKS A R, PRICE D. A quantitative study of carbon monoxide and carbon dioxide evolution during thermal degradation of flame retarded epoxy resins J]. Polymer Degradation and Stability, 2007, 92(5): 765-776.
Foundation item: Project(2006CB600902) supported by the Major State Basic Research and Development Program of China
Received date: 2008-03-13; Accepted date: 2008-05-27
Corresponding author: ZHANG Hong-bo, Professor; Tel: +86-731-8877393; E-mail: zhanghb@hnu.cn
(Edited by ZHAO Jun)