
Effect of ultrasonic power on wedge bonding strength and
interface microstructure
WANG Fu-liang(王福亮), LI Jun-hui(李军辉), HAN Lei(韩 雷), ZHONG Jue(钟 掘)
School of Mechanical and Electrical Engineering, Central South University, Changsha 410083, China
Received 25 July 2006; accepted 28 March 2007
Abstract: During the aluminum wire wedge bonding, the ultrasonic power and bonding strength were obtained. Based on those data, the relationship between ultrasonic power and bonding strength was studied. The results show that: 1) ultrasonic power is affected by ultrasonic power ratio and other uncontrolled factors such as asymmetric substrate quality, unstable restriction on the interface between wedge tool and aluminum wire; 2) when ultrasonic power is less than 1.0 W, increasing ultrasonic power leads to increasing bonding strength and decreasing failure bonding; on the contrary, when ultrasonic power is greater than 1.6 W, increasing power leads to decreasing bonding strength and increasing failure bonding; 3) only when ultrasonic power is between 1.0 W and 1.6 W, can stable and high yield bonding be reached. Finally, the microstructure of bonding interface was observed, and a ring-shaped bond pattern is founded in the center and friction scrape besides the ring area.
Key words: bonding strength; ultrasoninc power; wedge bonding; microstructure
1 Introduction
Microelectronic package has been the key factor of modern microelectronic manufacture. Ultrasonic wire bonding is an important microelectronic package technology, and up to 90% chips were packaged by this technique. It is a technology that bonds fine aluminum wire or golden wire to the pads of chip and the lead frames of substrate with ultrasonic vibration and tool force at room temperature or lower temperature[1-5]. Although it has been applied in integrated circuit(IC) industry for decades, its mechanism has not been understood very well. People only know that the bonding strength is affected by many factors. Research shows that bonding strength is affected by ball size, ball surface contamination and cleaning methods[6-8]. To investigate the relationship between bonding parameters and bonding strength, the bonding parameters such as interface stress, temperature, and ultrasonic vibration during bonding process were monitored and friction models of bonding interface were established[9-13]. Those studies show that the bonding process includes 2 stages: surface breakage and atom diffusion. The studies
about aluminum wire bonding are much less, and different failures (such as heal crack) and causes were observed[14-16]. In this study, the effect of ultrasonic power on aluminum wire bonding strength and interface microstructure was studied.
2 Experimental
According to the bonding tool or fine wire, ultrasonic bonding technologies are of two types: thermo-sonic golden wire ball bonding and ultrasonic wedge bonding. The former is used to bond golden wire(diameters range from 25 to 50 μm) by capillary tool with force, heat and ultrasonic vibration; and the later is mostly used to bond large aluminum wire(diameters range from 75 to 500 μm) at room temperature with wedge tool. This study was focused on the later.
2.1 Experiment equipment
The experiment was carried out on a self- restructured large aluminum wire wedge bonder, which has adjustable ultrasonic power, bonding force and bonding time. LW300 wedge tool, aluminum wire (300 μm in diameter) and substrate with Ni-coated pads were used in this study.
Corresponding author: WANG Fu-liang; Tel: +86-13975145436; E-mail: wangfuliang@mail.csu.edu.cn
Transducer system is the most important part of the bonder, which consists of Pr(Zr0.53Ti0.47)O3 (PZT), horn, bonding tool and so on, as shown in Fig.1.
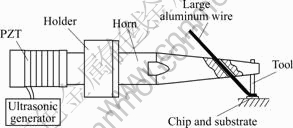
Fig.1 Structure of transducer system
Ultrasonic power is one of the most important factors that influence the bonding strength[3]. During the bonding process, the ultrasonic power may be different because of the change of wire bonding interface that consists of wire, bonding tool, chip pad or substrate pad.
2.2 Data acquisition
In order to study the effect of ultrasonic power on wedge bonding strength, the ultrasonic power signal and shear strength of each bonding were acquired. The later partly indicates the bonding strength.
The ultrasonic power signal acquisition method is shown as follows: firstly, the current and voltage signals of the PZT were acquired by a data acquisition(DAQ) system, the ultrasonic frequency was 60 kHz, and the data acquisition frequency was set as 1.2 MHz; and then ultrasonic power was calculated by multiplying current and voltage.
Fig.2 shows the ultrasonic power signal. It shows the bonding process: ultrasonic power starts at 0 ms and ends at 101.15 ms, which is defined as the ultrasonic bonding phase. Fig.2 also shows that the ultrasonic power does not always keep constant during bonding. At the beginning, the ultrasonic power increases to a peak, and then decreases to a plat until the end of bonding; after the ultrasonic is switched off, the ultrasonic power decreases to zero slowly. The average virtual value of the whole bonding phase was calculated as the indicator of ultrasonic power in this study.

Fig.2 Ultrasonic power signal during bonding
3 Results and discussion
The bonding experiments were carried out with the bonding parameters listed in Table 1.
Table 1 Bonding parameters of experiment
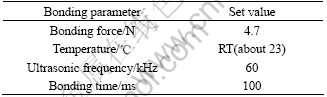
The ultrasonic power was changed by adjusting ultrasonic power ratio (the ultrasonic power ratio is defined as the ratio of the used power to the biggest power). And the ultrasonic power ratio in the experiment process is shown in Table 2.
Table 2 Ultrasonic power ratio(UPR) in experiment
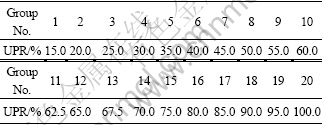
20 groups of experiments were carried out, and 50 times for each group in order to decrease the error caused by experiments and accidental factors. The ultrasonic power and shear strength of each bonding were recorded.
3.1 Distribution of ultrasonic power
The experiment data show that the ultrasonic power of each bonding is different even in the same bonding parameters, and different power may cause different distributions of power.
Fig.3 shows the distribution of ultrasonic power, which indicates that the average ultrasonic power and standard error increase with increasing ultrasonic power ratio. It may be caused by some factors: 1) different substrates cause different restriction on bonding interface and make the final ultrasonic power varied; 2) the restriction between bonding tool and aluminum wire is not certain because the wire is not always in the middle of tool groove, which causes the difference of ultrasonic power. So, wedge bonding is a sensitive process. The ultrasonic power is affected by ultrasonic power ratio and other factors that are removed in this study by repeated experiments.

Fig.3 Distribution of ultrasonic power: (a) Ultrasonic power;(b) Standard error of ultrasonic power
3.2 Ultrasonic power versus bonding strength
Fig.4 shows the relationship between ultrasonic power and wedge bonding shear strength. It contains 1 000 experiments data.
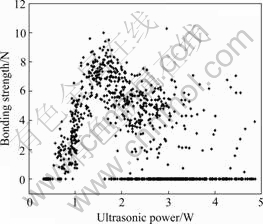
Fig.4 Ultrasonic power vs bonding strength
Fig.4 shows that: 1) even under the same ultrasonic power condition, the bonding strengths are different. When the ultrasonic power is small (less than 1.0 W), the difference is little and stable; when the ultrasonic power is large (larger than 1.6 W), the difference increases with increasing ultrasonic power, and the reason is still under research; 2) the relationship between bonding strength and ultrasonic power can be described with a parabola curve: when ultrasonic power is less than about 1.0 W, the bonding strength increases with the ultrasonic power; when ultrasonic power is greater than about 1.6 W, the bonding strength and its dispersancy decrease with increasing ultrasonic power; 3) when ultrasonic power is in the range of 1.0-1.6 W, no zero bonding strength occurs, which indicates that high yielding can be reached under such a bonding parameter condition, and zero bonding strength occurs out of this range. The possible reasons are: 1) too small ultrasonic power cannot supply energy to remove the oxide and contamination layer on bonding interface surfaces, resulting in under-bonding. On such situations, the bonding strength is small, and it can be improved by increasing the ultrasonic power; 2)too great ultrasonic power will damage the formed bonding area, making the bonding strength lower and causing over bonding. In such situation, increasing ultrasonic power will decrease the bonding strength.
3.3 Bonding states statistics
In order to understand the relationship between ultrasonic power and bonding strength more deeply, the bonding states statistics was performed.
According to the bonding states, all bonding results are of four types: 1) good, 2) peeled off, 3) broken and 4) non-stick. To some extend, these states reflect the bonding strength: state 1) is the perfect result, which has enough bonding strength and no over distortion on bonding heel; state 2) is caused by weak bonding strength, and the bonding point is peeled off in the wire loop formation process; state 3) shows that the bonding strength is formed, but wire in the bonding area is distorted heavily, and crack appears on bonding heel, which decreases shear strength and makes bonding point heel broken during wire loop formation process; and state 4) indicates that bonding strength is not formed or is too tiny.
Among the four types of bonding states mentioned above, states 1) and 3) have shear strength and can be classified into the same type. So, actually all bonding states are of three types. The statistic results of these types under different ultrasonic power conditions are shown in Fig.5.
Fig.5 shows that the statistic results of bonding states are obvious when ultrasonic power is less than 3.5 W. When ultrasonic power is in the range from 0.3 to 1.0 W, the low ultrasonic power cannot produce enough bonding strength, causing peeled off and non-stick; when ultrasonic power is in the range from 1.0 to 1.6 W, appropriate ultrasonic power can produce enough bonding strength, and avoid peeling off and non-sticking; when ultrasonic power is in the range from 1.6 to 3.5 W, the high ultrasonic power will make the formed bonding strength broken, and peeling off or non-sticking appear again; when the ultrasonic power is high than 3.5 W, the trend is the same, but not so regular. The reason is still under research.

Fig.5 Statistic results of all kinds of bonding states: (a) States 1) and 3); (b) State 2); (c) State 4)
To draw a conclusion, the reasons for peeling off and non-sticking are as the following: 1) too small ultrasonic power cannot form enough bonding strength; 2) too big ultrasonic power can make the formed bonding strength broken. So, in the large aluminum wire wedge bonding, both too small and too big ultrasonic power cause failure bonding, only moderate ultrasonic power can form stable and reliable bonding.
3.4 Bonding interface
The bonding interface was studied by observing its appearance and microstructure.
Fig.6 shows the good bonding point. No crack is observed on the heel of bonding, and wire is partly deformed.
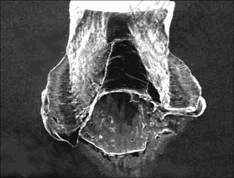
Fig.6 Good bonding point
Fig.7 shows the bad bonding point. Crack is observed on the heel of bonding, and the wire is seriously badly deformed.
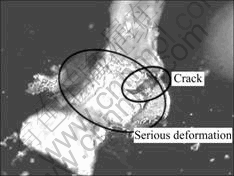
Fig.7 Broken bonding point of aluminum wire wedge bonding
Peel the wire off the substrate pad, and the microstructure of the bonding interface can be observed. Fig.8 shows the SEM images of a good bonding interface. Fig.8(a) shows the whole interface, a ring-shaped bond pattern is observed at the center and the friction scrape can be seen besides the ring area. With the EDAX spectrum test, it can be understood that the ring is made up of aluminum, which indicates that the bonding interface has higher strength than aluminum wire. Figs.8(b) and (c) show the details of areas A and B in Fig.8(a), respectively. Obviously, less aluminum is observed out of the ring-shaped area.
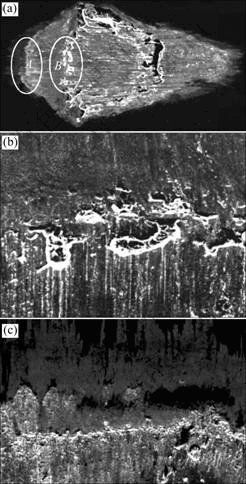
Fig.8 SEM images of good bonding interface: (a) Whole interface; (b) Details of area A; (c) Details of area B
Fig.9 shows a bonding interface of a much better bonding. A great number of aluminum is left on the substrate after the bonding point is lift-off, which indicates that the weak area of bonding exists on the aluminum wire. Fig.9(b) shows the details of the bonding interface of area A in Fig.9(a), and dimples are found in the ring area, which indicates that the ring area has high bonding strength.
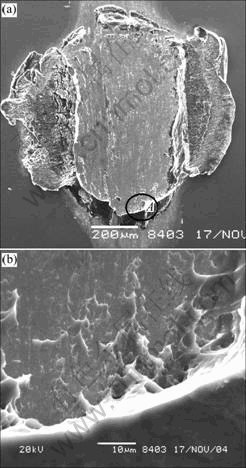
Fig.9 SEM images of much better bonding interface: (a) Whole interface; (b) Details of area A
4 Conclusions
1) Ultrasonic power is affected by many factors, such as substrate quality, constrain of wedge tool, aluminum wire, and so on. It shows that the aluminum wire wedge bonding is a sensitive process.
2) When ultrasonic power is less than 3.5 W, the effect of ultrasonic power on bonding strength is obvious;when ultrasonic power is in the range from 1.0 to 1.6 W, it can produce enough bonding strength and avoid peeling off and non-sticking; however, out of this range, too small or too high ultrasonic power will cause peeling off and non-sticking; when ultrasonic power is higher than 3.5 W, the trend is the same, but not so regular.
3) A ring-shaped bonding pattern is observed at the center of bonding interface and the friction scrape can be seen inside the ring area.
References
[1] LOPEZ C, CHAI L, SHAIKH A, STYGAR V. Wire bonding characteristics of gold conductors for low temperature co-fired ceramic applications [J]. Microelectronics Reliability, 2004, 44(3): 287-294.
[2] CHIU S S, CHAN H L W, OR S W, CHEUNG Y M, LIU P C K. Effect of electrode pattern on the outputs of piezosensors for wire bonding process control [J]. Mater Sci Eng B: Solid-state Materials for Advanced Technology, 2003, 99(1/3): 121-126.
[3] OR S W, CHAN H L W, LO V C, YUEN C W. Ultrasonic wire-bond quality monitoring using piezoelectric sensor [J]. Sensors and Actuators A: Physical, 1998, 65(1): 69-75.
[4] RODWELL R, WORRALL D A. Quality control in ultrasonic wire bonding [J]. Hybrid Circuits, 1985, 34(7): 67-72.
[5] CARRASS A, JAECKLIN V P. Analytical methods to characterize the interconnection quality of gold ball bonds [C]//Proc 2nd Euro Conf Elect Packag Technol (EuPac’96). Dusseldorf: Deutscher Verlag fur Schweisstechnik, 1996: 52-58.
[6] WEINER J A, CLATTERBAUGH G V, CHARLES H K Jr, ROMENESKO B M. Gold ball bond shear strength—Effects of cleaning, metallization and bonding parameters [C]//Proc 33rd Elect Comp Conf (ECC’83). New York: IEEE Press, 1983: 208-220.
[7] AGUILA M T, FELIPE R C, VELARD A F, EDPAN J B. Ball bond characterization: An intensive analysis on ball size and shear experiment results and applicability to existing standards [C]//Proc 1st Elect Packag Technol Conf (EPTC’97). New York: IEEE Press, 1997. 46-51.
[8] TUMMALA R R, RYMASZEWSKI E H, KLOPFENSTEIN G A. Microelectronics Packaging Handbook [M]. New York: Chapman & Hall, 1997: 121-128.
[9] CHEN Y S, FATEMI H. Au wire bonding evaluation by fractional factorial designed experiment [J]. J Hybrid Microelectron, 1987, 10(3): 1-7.
[10] MAYER M. Microelectronic Bonding Process Monitoring by Integrated Sensors [M]. Konstanz: Hartung-Gorre, 2000: 77-92.
[11] MAYER M, PAUL O, BOLLIGER D, BALTES H. Integrated temperature microsensors for characterization and optimization of thermosonic ball bonding process [J]. IEEE Trans Comp Packaging Technol, 2000, 23(2): 393-398.
[12] MAYER M, SCHWIZER J, PAUL O, BOLLIGER D. In-situ ultrasonic stress measurements during ball bonding using integrated piozoresistive microsensors [C]//Proc 1999 Intersociety Electron Pack Conf (InterPACK99). New York: IEEE Press, 1999: 1413- 1422.
[13] SCHWIZER J, MAYER M, BOLLIGER D. Thermosonic ball bonding: friction model based on integrated microsensor measurements [C]//Proc 24th IEEE/CPMT Intl Electronic Manufacturing Technology Symposium (IEMT’99). New York: IEEE Press, 1999: 108-114.
[14] RAMMINGER S, SELIGER N, WACHUTKA G. Reliability model for Al wire bonds subjected to heel crack failures [J]. Microelectronics Reliability, 2000, 40(9): 1521-1525.
[15] WANG Fu-liang, HAN Lei, ZHONG Jue. Effect of ultrasonic power on the heavy aluminum wire wedge bonding strength [J]. China Mechanical Engineering, 2005, 16 (10): 919-923. (in Chinese)
[16] LI Jan-hui, HAN Lei, ZHONG Jue. Interface structure of ultrasonic wedge bonding joints of Ni/Al [J]. Trans Nonferrous Met Soc China, 2005, 15(4): 846-850.
Foundation item: Projects(50390064, 50675227) supported by the National Natural Science Foundation of China; Project(2003CB716202) supported by the National Basic Research Program of China
(Edited by CHEN Wei-ping)