
Influence of microstructure stability on creep properties of single crystal nickel base superalloys
TIAN Su-gui (田素贵)1, MENG Fan-lai (孟凡来)1, DU Hong-qiang (杜洪强)1,
WANG Chun-tao(王春涛)1, SHUI Li (水 丽)1, HU Zhuang-qi (胡壮麒)2
1. Department of Materials Science, Shenyang University of Technology, Shenyang 110023, China;
2. Institute of Metal Research, Chinese Academy of Sciences, Shenyang 110016, China
Received 28 July 2006; accepted 15 September 2006
Abstract: The influence of microstructure stability on the creep properties of single crystal nickel-based superalloys was investigated by means of the measurement of the creep curves and microstructure observation. Results show that the superalloy with 4%(mass fraction)W in Ni-Al-Cr-Ta-Co-5.5%Mo-x%W systems displays a better microstructure stability, but the m phase is precipitated in the superalloy with 6% W during aging. The strip-like m phase is precipitated to be parallel or perpendicular to each other along the <110> orientation, and grown into the slice-like morphology along the {111} planes. The superalloy with 4%W displays a better creep rupture lifetime under the applied stress of 200 MPa at 982 oC, but the creep lifetime of alloy is obviously decreased with the increase of the element W content up to 6%. The fact that the m phase is precipitated in the superalloy with 6% W during applied stress and unstress aging results in the appearance of the poor regions for the refractory elements. This is one of the main reasons for reducing the creep rupture lifetime of the superalloy.
Key words: single crystal nickel-based superalloy; microstructure stability; creep; aging; topologically-closed-packed phase
1 Introduction
Single crystal nickel based superalloy is one of the used materials as the blade parts of aircraft engines, and the refractory elements W, Mo and Ta are the key strengthening elements[1-3]. Thereinto, the element Ta may promote the formation of g? phase, the element Mo promotes the formation of g matrix phase[4], and the element W may improve the strengthening level of both g? and g phases at high temperature. The enduring lifetimes of the single crystal nickel base superalloys are obviously enhanced with the increase of the element W content[5]. But it may promote the formation of the topologically-closed-packed (TCP) phase in nickel base superalloy with the increase of the element W concentration[6,7]. The applied stress has been shown to enhance the formation of TCP phase[8], while in another case, the applied stress has been shown to delay the formation of TCP phase[9,10]. And the presence of TCP phases has been found to be detrimental to properties of alloys such as rupture strength, tensile ductility at room temperature, impact toughness and corrosion resistance [11]. Therefore, it is very important for avoiding the precipitation of TCP phase to optimize the composition design of nickel base superalloys.
Thought the excess element W additions may increase the precipitation tendency of TCP phases in superalloys, the limit of the element W addition in Ni-Cr-Mo-Ta-Al alloy systems is still not clear. Therefore, the influence of the element W content on microstructure stability of single crystal nickel base superalloys was investigated, which may provide a criterion in theory to design the composition of alloys.
2 Experimental
Two kinds of Ni-Cr-Co-Al-Ta-5.5%Mo-x%W (mass fraction) single-crystal nickel base superalloys systems of [001] orientation, in which the same chemical composition is chosen besides the element W content to be 4% and 6%, respectively, were produced by means of the crystal selection method in a directional solidification vacuum furnace under a high thermal gradient. The bars of the single crystal superalloys were machined into the cylindrical specimens with a cross-section of 5 mm in diameter and 25 mm in gauge length according to ASTMB557M. The specimens of the alloys were aged at 1 040 ℃ for 200 h, so that the microstructure of the alloys was observed to understand the influence of the element W content on microstructure stability and the features of the TCP phase precipitated in the superalloys. In order to compare the influence of microstructure stability on the creep properties of superalloys, the uniaxial constant load tensile creep test was conducted, using a GTW504 model creep testing machine, with applying different temperatures and stresses up to fracture. The microstructure observation of the aged and creep specimens was conduced by means of SEM and TEM.
3 Results and analysis
3.1 Feature of TCP phase precipitated
After the superalloy with 4% W is aged at 1 040 ℃ for 200 h, no TCP phase is detected in the alloy, but after the superalloy with 6% W is aged for 200 h at same temperature, the morphologies of TCP phase detected are shown in Fig.1. The normal line direction of the specimens is about [001] orientation. It is seen from Fig.1(a) that the g? phase in the superalloy is diffused and grown into the bunch morphology along the directions of [100] and [010]. Significant amount of the strip-like TCP phases are precipitated in the alloy along the direction parallel or vertical to each other, and arranged at an angle about 45? relative to the g? phase coarsening direction. This shows that the orientation of the strip-like TCP phase is parallel to <110> directions. The composition analysis of SEM/EDS shows that the TCP phase is rich in the elements Mo, W and Ta.
The morphology after the specimen is etched deeply is shown in Fig.1(b). It is clearly displayed that the g? phase is grown into the bunch structure along the parallel or vertical direction. When etched deeply, the g? phase in the alloy surface is dissolved into the holes, and the g matrix or m phase is still reserved. It may be seen from Fig.1(b) that the strip-like TCP phase displays a slice-like structure along the depth direction of specimen as marked with arrow in Fig.1(b). If it is thought that the prism edge of the A and B slice-like TCP phase is about parallel to each other, the growing direction of the two slice-like TCP phase are not in the same plane in depth, and presents a definite angle with each other. The normal line of the specimen is [001] orientation, because the angles between {111} planes and [001] orientation are about 35?. This is approximately in agreement with the incline angle between two slice-like TCP phases and the normal direction of the specimen. Therefore, it may be deducted that the wider plane of the slice-like TCP phase is parallel to the {111} plane. The analysis above stated is very well in agreement with Refs.[6,7]. It still be understood from Fig.1(b) that the interface between the TCP and g phases displays the feature of the etching hole, which shows that a large number of the TCP phases are contacted with the g? phase.
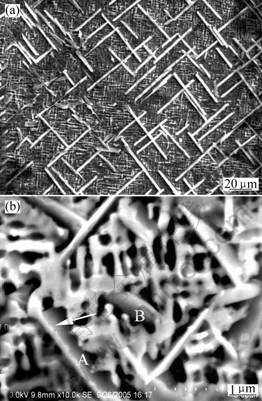
Fig.1 Microstructures of 6%W alloy aged at 1 040 ℃ for 200 h: (a) Precipitated strip-like m phase being parallel or perpendicular with each other along <110> orientation; (b) Slice-like m phase precipitated on {111} planes as marked with A and B
TEM morphology and the labeled exponent of the strip-like TCP phase are shown in Fig.2. TCP phase of the strip-like morphology is parallel to each other as marked by arrow in Fig.2(a). Fig.2(b) shows the diffraction spots of TCP phase, and the labeled exponent of the one is shown in Fig.2(c), indicating that the TCP phase is identified as the m phase with a hexagonal structure.
3.2 Influence of precipitated phase on creep features
The creep curves of alloys with 4% and 6% W content, under the applied stress of 200 MPa at 982 ℃, are shown in Fig.3. It can be seen that the alloy with 6% W displays a shorter time and a bigger strain rate during the steady state creep, and obtains only the creep lifetime of 123 h. But the creep lifetime of 266 h is displayed in the alloy with 4% W under the same conditions. Compared with 6%W alloy, the strain rate of the alloy decreases and creep lifetime increases to a bigger extent.
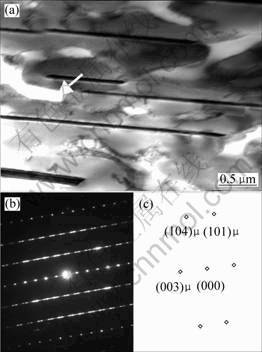
Fig.2 Morphology and labeled exponent of strip-like m phase: (a) Morphology of m phase; (b) Diffraction spots; (c) Labeled exponent
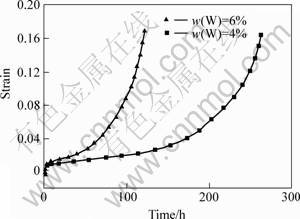
Fig.3 Creep curves of alloys with 4% and 6% W under applied stress of 200 MPa at 982 ℃
3.3 Deformation features of different alloys during creep
After two kinds of the superalloys are full treated, microstructure consists of the cubic g? phase embedded in g matrix[3]. Fig.4 shows the morphologies after two kinds of superalloys are crept up to fracture under the applied stress of 200 MPa at 982 ℃. Fig.4(a) shows a morphology after 4% W alloy is crept for 266 h. It may be understood from the image that the g? phase is transformed into the rafted structure along the direction vertical to the stress axis. The straight-like structure of the g? phase is displayed in the superalloy, and no dislocation is detected within the g? phase. After the superalloy is aged for long time under the applied or no applied stress at high temperature, no phase is detected in it. But after the superalloy with 6% W is crept for 123 h up to fracture under the applied stress of 200 MPa at 982 ℃, the rafted g? phase twisted occurs. Significant amount of dislocations are activated in the rafted g? phase, and there are some of the strip-like μ phase precipitated in the superalloy as marked with arrow in Fig.4(b).
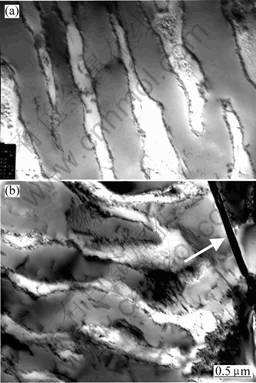
Fig.4 Microstructures after alloys crept for different time under applied stress of 200 MPa at 982 ℃: (a) 4% W alloy crept for 266 h; (b) 6% W alloy crept for 123 h (precipitated TCP phase marked with arrow)
Fig.5 shows TEM morphology after the superalloy with 6% W is crept for 123 h under the applied stress of 200 MPa at 982 ℃. It can be seen that the strip-like m phase displays a bigger size as marked with arrow. The g? phase is located in the upside of the m phase, and some of dislocations are sheared into the g? phase. And the denser dislocation tangles are piled up near m phase as marked with arrow in Fig.5, indicating that the moving dislocations may be hindered by m phase, which may bring about the stress concentration, and promote the occurrence and expending of the micro-crack in the further, so that accelerates the creep rupture of alloy. This analysis is well in agreement with the result in Fig.3.
In Ni-Cr-Co-Al-Ta-5.5%Mo-x%W alloys systems, the superalloy with 4% W displays a longer rupture lifetime due to no strip-like m phase precipitated, but some of the strip-like m phase are precipitated in the superalloy with 6% W which displays a shorter rupture lifetime. This shows that the strip-like m phase precipitated in the superalloy is one of the main reasons for reducing creep rupture lifetime.
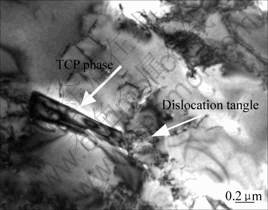
Fig.5 Dislocation tangles accumulated near m phase in 6% W alloy crept for 123 h
4 Conclusions
1) The strip-like m phase is precipitated on (001) parallel or perpendicular to each other along the <110> directions, and grown into the slice-like morphology along the {111} planes.
2) In Ni-Al-Cr-Ta-Co-5.5%Mo-x%W alloys systems, the superalloy with 4% W displays a longer creep rupture lifetime under the applied stress of 200 MPa at 982 ℃, and the creep lifetime of it are obviously decreased as the element W content is increased up to 6%.
3) During high temperature creep and aging of the superalloy with 6% W, much more elements Mo, W and Ta are dissolved into the precipitated m phase, which brings about the depleted regions for refractory elements, and reduces the strength of the g? and g phases. This is the main reason for reducing the creep lifetime of the superalloy.
References
[1] MACKAY R A, NATHAL M V, PEARSON D D. Influence of molybdenum on the creep properties of nickel-base superalloy single crystals [J]. Metall Trans A, 1990, 21A: 381-388.
[2] YU X H, YAMABE-MITARAL Y, RO Y, HARADA H. Design of quaternary Ir-Nb-Ni-Al refractory superalloys [J]. Metall Mater Trans A, 2000, 31A: 173-178.
[3] NYSTROM J D, POLLCK T M, MURPHY W H, GARG A. Discontinuous cellular precipitation in a high-refractory nickel-base superalloys [J]. Metall Mater Trans A, 1997, 28A: 2443-2452.
[4] TIAN S G, ZHANG J H, WU X, YANG H C, XU Y B, HU Z Q. Features and effect factors of creep of single crystal nickel base superalloys [J]. Metall Mater Trans A, 2001, 32A: 2947-2957.
[5] NATHAl M V, EBERT J. Influence of cobalt, tungsten on the elevated temperature mechanical properties of single crystal nickel base superalloys [J]. Metall Trans A, 1985, 16A: 1863-1245.
[6] ZHAO K, MA Y H, LOU L H, HU Z Q. Phase in a nickel base directionally solidified alloy [J]. Mater Trans, 2005, 46(1): 54-58.
[7] ZHU J, YE H Q. On the microstructure and its diffraction anomaly of the m phase in superalloys [J]. Scripta Metall Mater, 1990, 24: 1861-1866.
[8] PYCZAK F,BIERMANN H,MUGHRABI H, VOLEK A, SINGER RF. CBED-measurement of residual internal strains in the neighbourhood of TCP-phase in Ni-base superalloys[C]//POLLOCK T M, KISSINGER R D, BOWMAN R R. Superalloys. Warrendale, PA: TMS, 2000: 367-376.
[9] PESSAH M, CARON P, KHAN T. Effect of m phase on mechanical properties of a nickel base single crystal superalloy[C]// ANTOLOVICH S D, STRUSRUD R W, MACKAY R A, ANTON D L, KHAN T, KISSINGER R D, KLARSTROM D L. Superalloys. Warrendale, PA: TMS, 1992: 567-576.
[10] SIMONETTI M, CARON P. Role and behaviour of μ? phase during deformation of a nickel based single crystal superalloy [J]. Mater Sci Eng A, 1998, A254: 1-12.
[11] DAROLIA R, LAHRMAN D F, FIELD R D. Formation of topologically closed packed phases in nickel base single crystal superalloy[C]//DUHL D N, ANTOLOVICH M, LUND C, REICHMAN S. Superalloys. Warrendale, PA: TMS, 1988: 255-264.
(Edited by YANG You-ping)
Foundation item: Project (50571070) supported by the National Natural Science Foundation of China; project(2004C004) supported by Education Foundation of Liaoning Province, China
Corresponding author: TIAN Su-gui; Tel: +86-24-25691315; E-mail: tiansugui2003@163.com