Trans. Nonferrous Met. Soc. China 20(2010) s981-s987

Semi-solid gravity sand casting using gas induced semi-solid process
T. CHUCHEEP1, R. BURAPA3, S. JANUDOM1, S. WISUTMETHANGOON2, J. WANNASIN1
1. Department of Mining and Materials Engineering, Faculty of Engineering, Prince of Songkla University, Hat Yai, Songkhla, 90112, Thailand;
2. Department of Mechanical Engineering, Faculty of Engineering, Prince of Songkla University, Hat Yai, Songkhla, 90112, Thailand;
3. Department of Industrial Engineering, Faculty of Engineering, Rajamangala University of Technology Srivijaya, Songkhla, 90000, Thailand
Received 13 May 2010; accepted 15 July 2010
Abstract: The semi-solid metal forming using high pressures has been applied for several years. In contrast, low pressure casting, such as gravity sand casting, has not been widely studied even though it may help reduce porosity defects and offer a better casting yield. A semi-solid gravity sand casting process using the Gas Induced Semi-Solid process was investigated. The results show that the process can produce complete parts with no observable defects. The ultimate tensile strength and elongation data of semi-solid cast samples are higher than those of the liquid cast samples. In addition, the semi-solid sand casting process gives a better casting yield. It can be concluded that the semi-solid sand casting of an aluminum alloy using the GISS process is a feasible process.
Key words: gravity sand casting; semi-solid sand cast; Al7Si0.3MgFe; gas induced semi-solid
1 Introduction
The semi-solid metal forming is mostly applied with high pressures[1]. This process has a number of attractive properties, such as laminar filling of die cavities, reduced porosity and improved mechanical properties[1-3, 4]. In contrast, the gravity sand casting has not been commonly used because the lower fluidity of the slurry has generally made their gravity impossible[5] even though it has several advantages in small lots, complex parts or big parts[3, 5-6].
The major disadvantages of gravity sand casting are low casting yield and high possibility of defects, such as shrinkage and gas porosity[3,7].
In addition, the proper gating and riser design must be carefully considered in the conventional sand casting[8-9]. Therefore, the semi-solid casting has been considered in this conventional sand casting. Presently, only a small number of semi-solid gravity casting studies have been carried out.
MASAHITO et al[3] developed transition controlled semi-solid molding (TCSSM) for ductile iron in lost foam sand mold casting. In the process, the vacuum system increases the fluidity of casting. The results show that sound casting of pipe fits with no core and no riser, and turbo housing with no shrinkage and no riser, and about 25% higher casting yield than the conventional process.
WANNASIN et al[10] reported that semi-solid sand casting of Al-Cu B204 reduced hot tearing and had sufficient fluidity to fill the molds even with a low gravity pressure.
According to the literatures, it can be concluded that the semi-solid gravity sand casting is possible to be performed and can give several benefits.
Currently, no research focusing on the semi-solid gravity sand casting with Al7Si0.3MgFe has been reported even though this alloy has excellent fluidity, resistance to hot cracking, low solidification shrinkage, and good machinability after T6[8]. Therefore, this work aims to study the feasibility of the semi-solid gravity with Al7Si0.3MgFe casting in sand mold by the gas induced semi-solid (GISS) process[11].
2 Experimental
2.1 Materials
The secondary Al7Si0.3MgFe ingots (commercial grade “AC4C”) were bought from a local producer in Thailand. It was produced following the JIS H 5202-1999 standard[12]. The chemical composition of the alloy is shown in Table 1.
Table 1 Chemical composition of alloy used in experiment (mass fraction,%)

The trial casting part in this experiment is obtained from a small casting company as shown in Fig.1. The trial cast part consists of three sections: thick section(A), circular section(B) and tube section(C).
Two pieces of wood split pattern for sand mold and core box were machined following the drawing. The two pieces of the core box were made of wood with the diameter of 2.5 cm and the length of 90 cm.
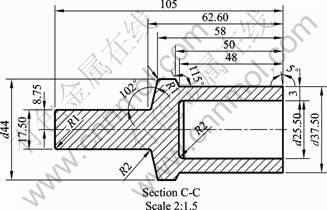
Fig.1 Drawing of trial casting part
2.2 Sand mold
Green sand molds were prepared by manual ramming. The sand for molding was recycled sand, added with bentonite 0.75% and water 1.75%. The mixing was done by a rotary sand mixer. The CO2 sand cores were pure sand and rammed in a core box. The cope and drag were made of wood with the thickness of 1.5 cm and the outer dimensions of 30 cm×26 cm×7 cm. The conventional casting used unpressurized gating system with the side gate (1 cm×1.8 cm), a tapered sprue[9,13], and a top riser (40 mm diameter). The semi-solid casting used tapered sprue and top gate[14] (diameter 2.6 cm), and no riser as shown in Fig.2.
2.3 Semi-solid slurry preparation
The alloy was melted at (730 ± 15)℃ and treated with commercial cleaning flux and degassing flux.
The slurry was prepared by immersing a porous graphite in the molten aluminum above the liquidus temperature and introduced fine inert gas bubbles in the melt. The schematic diagram of the GISS process is shown in Fig.3[11].
From preliminary studies, the solid fraction higher than 10% had a chance of unsuccessful filling of the mold cavity. In this experiment, the solid fractions were selected to be about 5% and 10%.
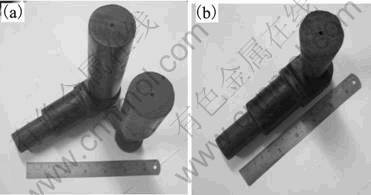
Fig.2 Gating system of conventional casting(a) and semi-solid casting(b)
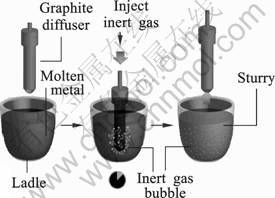
Fig.3 Schematic diagram of gas induced semi-solid process
2.4 Casting
This study consists of four experiments. The first and second experiments are conventional sand casting pouring with a high temperature of 740 ?C (CVC1), and a low pouring temperature of 690 ?C (CVC2) as shown in Table 2. The third and fourth experiments are semi-solid sand casting at the solid fractions of about 5% (SSM1) and 10% (SSM2) as in shown Table 2. The schematic diagram of the GISS sand casting is shown in Fig.4.
Table 2 Experimental conditions
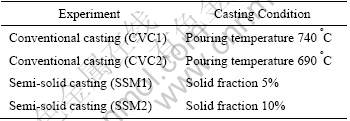
2.5 Analysis
Both of the conventional and semi-solid sand casting samples were heat treated at the T6 condition (solution treat at 540 ?C for 6 h, quenching in the water, aging at 180 ?C for 6 h)[15].
The metallographic samples were obtained by sectioning the thick position of the trial part. The tensile test specimens were selected from the thick section of the trial casting part and machined according to the ASTM B557M standard as shown in Fig.5[16]. The specimens with length of 36 mm, diameter of 6 mm, gage length of 30 mm, and fillet radius of 6 mm were used.
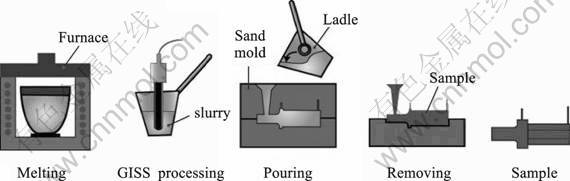
Fig.4 Schematic diagram of GISS sand casting process
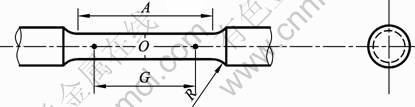
Fig.5 Schematic diagram of specimens for tensile testing[16]
3 Results and discussion
3.1 Cast sample
The casting parts of conventional and semi-solid casting are shown in Fig.6. The conventional part consists of a side gate and a top riser at the thick section. In contrast, the semi-solid part has only a top gate.
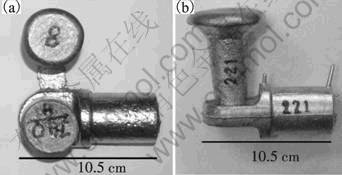
Fig.6 Casting parts prepared by conventional casting(a) and semi-solid casting(b)
All the casting conditions can produce complete filling. The semi-solid parts achieved good feeding at low solid fractions, which agrees with the results by WANNASIN et al[10], which show feasible gravity casting and by YURKO[4], which show that semi-solid slurry at low solid fractions can flow like a superheated melt. Also, KIRKWOOD et al[17] reported that the apparent viscosity for A356 at different shear rates at a low solid fraction (<10%) did not have very high viscosity[17].
3.2 Microstructure
3.2.1 As cast microstructure
The microstructures of the semi-solid castings at the solid fraction 5% and solid fraction 10% are quite similar. The microstructures of the conventional sand casting at the pouring temperatures of 740 ?C and 690 ?C are also similar.
The typical microstructures of conventional sand casting are shown in Figs.7 (a) and (b). A comparison shows that the microstructure of conventional casting has large dendritic structure. However, the semi-solid castings shown in Figs.7 (c) and (d) have finer non-dendritic structure.
The finer and non-dendritic microstructure of the semi-solid samples is achieved by the GISS process as reported elsewhere[11].
As shown in Fig.8, the microstructure of the conventional casting at a high temperature “CVC1” has coarser eutectic structure. This is because the high pouring temperature results in a low cooling rate. The results of the low pouring temperature and both of the low solid fractions show that the eutectic structures are finer.
3.2.2 Microstructure uniformity
A microstructure uniformity analysis is conducted to confirm the feasibility of semi-solid sand casting. The specimens were cut from 3 positions of the sample parts as shown in Fig.9. The results show that for both cases of conventional and semi-solid castings, the microstructure is quite uniform. The only difference is the finer size of the semi-solid structure.
3.2.3 Microstructure after heat treatment
The microstructures after T6 heat treatment of both cases are given in Fig.10. The results show that the silicon particles are rounder in the semi-solid samples[18]. This is expected since the eutectic structure in the as cast condition is also finer for the lower casting temperatures.
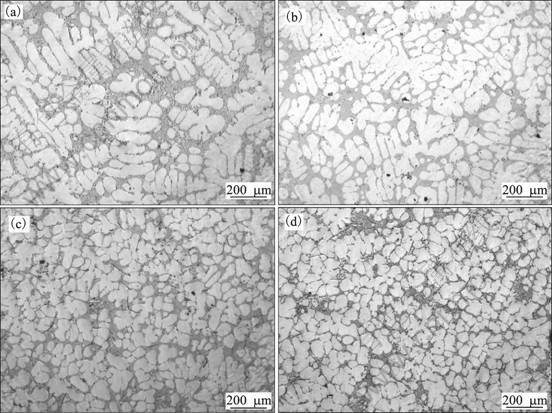
Fig.7 Typical microstructures of samples by different castings: (a) CVC1, 740 °C; (b) CVC2, 690 °C; (c) SSM1, SF5%; (d) SSM2, SF 10%
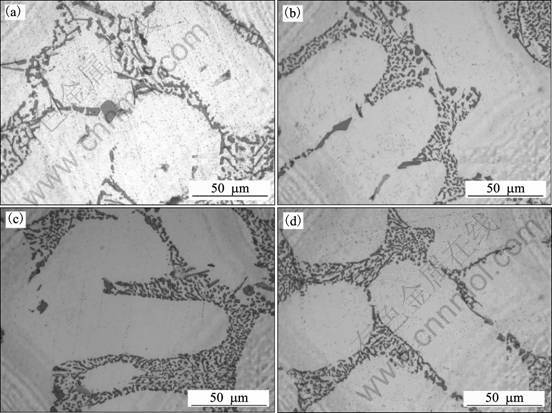
Fig.8 Typical microstructures of samples by different castings (a) CVC1, 740 °C; (b) CVC2, 690 °C; (c) SSM1, SF5%; l (d) SSM2, SF 10%
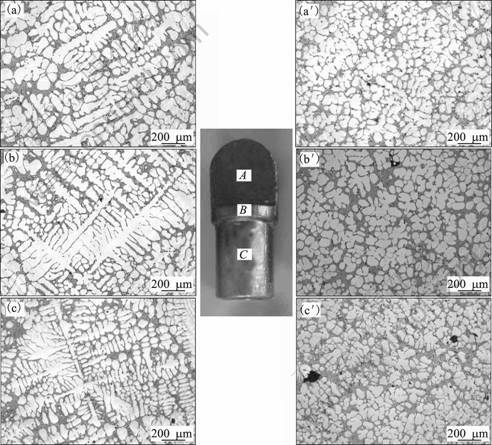
Fig.9 As-cast microstructures of different positions by different castings (a), (a') position A; (b), (b') position B; (c), (c') position C; (a), (b), (c) Conventional casting; (a'), (b'), (c') Semisdid sand casting
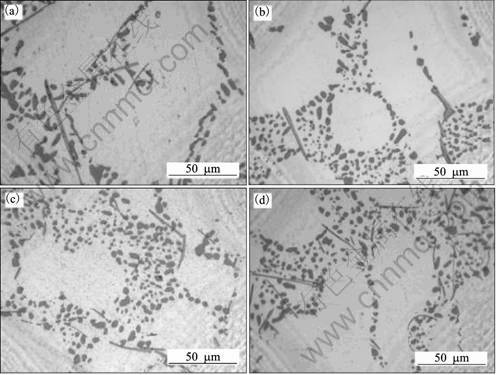
Fig.10 Microstructures of samples after heat treatment: (a) CVC1, 740?C; (b) CVC2, 690?C; (c) SSM1, SF5%; (d) SSM2, SF 10%
3.3 Mechanical properties
The ultimate tensile strength and standard error from 5-6 samples for the conventional castings CVC1 and CVC2 are (246.2+11.3) MPa and (254.1+2.1) MPa, respectively. The values are slightly lower than those of the semi-solid samples SSM1 ((268.0+6.3) MPa) and SSM2 ((262.6+9.7) MPa). The results are shown in Fig. 11.
The elongation shows the same trend in Fig.12. The semi-solid samples have slightly higher values (SSM1(5.4+0.3)% and SSM2(5.4+0.6)%) compared with the conventional casting (CVC1( 4.0+0.5)% and CVC2(5.1+0.4%)).
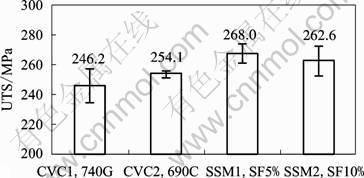
Fig.11 Tensile strength of conventional and semi-solid casting
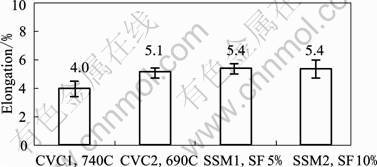
Fig.12 Elongation of each process
The finer primary phase and eutectic structure may be responsible for this slightly better properties[7].
A previous study by SHABESTARI et al[18] reported their results of A356-T6 sand cast at different thicknesses as summarized in the Table 3.
Compared with these results, it is noted that the average ultimate tensile strengths of the semi-solid
casting (268 MPa and 262 MPa) are not different when compared with A356-T6 unmodified in Table 3. The elongation of the semi-solid casting with the solid fraction of 5% and 10% is about 5.4%, which is slightly higher than all the results in Table 3[18]. The result shows that the semi-solid casting can give acceptable properties compared with other conventional sand casting processes.
3.4 Casting yield
The semi-solid casting yields of SSM1 (51.7%+1.6%), and SSM2 (52.8%+1.7%) are higher than conventional casting yields CVC1 (37.6%+0.6%) and CVC2 (38.4%+2.8%) as summarized in Fig.13.
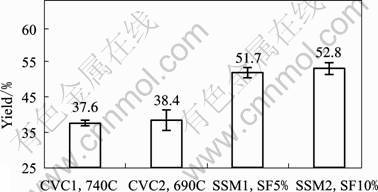
Fig.13 Casting yield of each process
The casting yield of the semi-solid casting is improved in this experiment even though the semi-solid casting needs to use a bigger gate. In this experiment, the semi-solid casting can eliminate the use of a riser, so the casting yield is increased from about 40% to 50%. The semi-solid casting without a riser can also complete the feeding of the thick part because the lower casting temperature of the semi-solid casting can decrease shrinkage[3].
The higher casting yield not only reduces the energy cost[3] but also reduces the environmental impact from the low casting temperature.
Table 3 Mechanical properties of sand cast samples after T6 heat treatment[18]
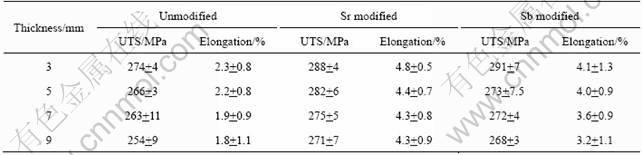
4 Conclusions
1) Gas induced semi-solid casting of Al7Si0.3MgFe at a low solid fraction can fill the casting in gravity sand casting.
2) The results of the ultimate tensile strength of semi-solid casting are similar to those of the conventional casting. However, the elongation data of the semi-solid sand castings are slightly higher than those of the conventional casting, especially when compared with the high-temperature casting.
3) The casting yield of the semi-solid process is higher than that of the conventional casting. This is due to the elimination of a big riser.
Acknowledgements
The authors gratefully thank the funding from Prince of Songkla University for Ph.D. 50% Scholarship, the Royal Golden Jubilee Ph.D. program (Grant No. PHD/0173/2550), Graduate School Scholarship, the Department of Mining and Materials Engineering, and Asst.Prof.Dr. Sakesun Suthummanon, Head of the Industrial Engineering Department for facility support.
We also thank the Innovative Metal Technology (IMT) team especially Miss R Canyook, Mr. T. Rattanochaikul, Miss N. Mahathaninwong, Mr. S. Chantaramanee and Mr. T. Junin for all the kind supports.
References
[1] GUO Hong-min, YANG Xiang-jie, WANG Jia-xuan. Pressurized solidification of semi-solid aluminium die casting alloy A356 [J]. Journal of Alloys and Compounds, 2009, 485: 812-816.
[2] FLEMINGS M C. Behavior of metal alloys in the semisolid state [J]. Metallurgical Transactions B, 1991, 22B: 269-293.
[3] MASAHITO G, TATSUHIKO K, MANABU K. Integrated development of controlled semi-solid casting technology for super-cooled ductile iron [J]. Solid State Phenomena, 2006, 116/117: 9-15.
[4] YURKO J A, MARTINEZ R A, FLEMINGS M C. SSRTM: The spheroidal growth route to semi-solid forming [C]//The 8th International Conference on Semi-Solid Processing of Alloys and Composites. Limassol: Cyprus, 2004.
[5] MIRZADEH H, NIROUMAND B. Fluidity of Al-Si semi-solid slurries during rheocasting by novel process [J]. Journal of Materials Processing Technology, 2009, 209: 4977-4982.
[6] MIRZADEH H, NIROUMAND B. Semi-Solid casting of Al-7wt%Si alloy in expendable Molds [J]. Solid State Phenomena, 2006, 116-117: 495-500.
[7] EMAMI A R, BEGUM S, CHEN D L, SKSZEK T, NIU X P, ZHANG Y, GABBIANELLI F. Cyclic deformation behavior of a cast aluminum alloy [J]. Materials Science and Engineering A, 2009, 516: 31-40.
[8] JORSTAD J L, RASMUSSEN W M. Aluminum casting technology [M]. 2nd ed. Illinois: American Foundrymen’s Society Inc, 1993: 271.
[9] TAYLOR H F, FLEMINGS M C, WULFF J. Foundry Engineering[M]. New York: John Wiley & Sons Inc, 1959: 132-199.
[10] WANNASIN J, SCHWAM D, YURKO J A, ROHLOFF C, WOYCIK G. Hot tearing susceptibility and fluidity of semi-solid gravity cast Al-Cu alloy [J]. Solid State Phenomena, 2006, 116/117: 76-79.
[11] WANNASIN J, MARTINEZ R A, FLEMINGS M C. A Novel technique to produce metal slurries for semi-solid metal processing[J]. Solid State Phenomena, 2006, 116/117: 366-369.
[12] JIS H 5202–1999. Aluminium alloy castings [M]. Tokyo: Japanese Standards Association, 1999: 1397-1413.
[13] SYLVIA J G. Cast metals technology[M]. Massachusetts: Addison-Wesley Publishing Company, 1972: 175-186.
[14] MOHAMED R, HIROYUKI N, MITSUHARU T. Semi-solid processing of thin section gray cast iron in sand mold [C]//The 8th International Conference on Semi-solid Processing of Alloys and Composites. Limassol: Cyprus, 2004.
[15] ASTM B917/B917M–01. Standard practice for heat treatment of aluminum-alloy casting from all processes [M]. Pennsylvania: ASTM International, 2001: 1-11.
[16] ASTM B557M–02a. Standard test methods of tension testing wrought and cast aluminum-and magnesium-alloy product [Metric] [M]. Pennsylvania: ASTM International, 2003: 1-15.
[17] KIRKWOOD DAVID H, SUERY MICHEL, KAPRANOS PLATO, ATKINSON HELEN V, AND YOUNG, KENNETH P. Semi-solid processing of alloys [M]. London: Springer Series in Materials Science, 2009, 124: 48-56.
[18] SHABESTARI S G, SHAHRI F. Influence of modification, solidification conditions and heat treatment on the microstructure and mechanical properties of A356 aluminum alloy [J]. Journal of Materials Science, 2004, 39: 2023-2032.
(Edited by LI Yan-hong)
Corresponding author: J. WANNASIN ; Tel: +66-74-287-312; E-mail: jessada.w@psu.ac.th; jessada@alum.mit.edu