Trans. Nonferrous Met. Soc. China 20(2010) s873-s877

Effects of annular electromagnetic stirring processing parameters on semi-solid slurry production
CHEN Xing-run(陈兴润), ZHANG Zhi-feng(张志峰), XU Jun(徐 骏)
National Engineering & Technology Research Center for Non-ferrous Metal Matrix Composites,
General Research Institute for Non-ferrous Metals, Beijing 100088, China
Received 13 May 2010; accepted 25 June 2010
Abstract: A computational model coupling an electromagnetic model with a macroscopic heat and fluid flow model in semi-solid aluminum alloy slurry preparation by annular electromagnetic stirring (A-EMS) was developed. Effects of A-EMS processing parameters, such as stirring current, stirring frequency and stirring gap width, on macroscopic transport phenomena during the solidification were analyzed by commercial software ANSYS 10.0 with corresponding experimental verification. The results show that the magnetic flux density and the melt velocity increase and the temperature difference decreases as stirring gap width and stirring frequency decrease or the stirring current increases. The slurry with the fine and uniform globular grain structure can be gained by adjusting gap width, electromagnetic frequency and current, such as under the conditions of 10 mm of gap width,10 Hz of electromagnetic frequency and 50 A of current. The calculated results are in reasonably good agreement with the measured ones.
Key words: electromagnetic stirring; semi-solid slurry; numerical simulation; microstructure
1 Introduction
To obtain Al alloys semi-solid slurry or billet with high quality, an annular electromagnetic stirring (A-EMS) process has been developed, where intensively forced shearing could be achieved under higher shear rate inside the annular chamber at the commercial frequency by means of innovatively combining non-contact electromagnetic stirring and an annular chamber with specially designed profiles, and thereby more uniformly fine microstructures of Al alloys slurry were produced in comparison with normal EMS[1-4]. Although a computational model coupling an electromagnetic model with a macroscopic heat and fluid flow model in semi-solid Al alloy slurry preparation by A-EMS has been developed[5-6], much research work is needed to disclose effects of A-EMS processing parameters on macroscopic transport phenomena in slurry-making process, which is important to optimize processing variables. In this study, based on the developed models, effects of A-EMS processing parameters, such as stirring current, stirring frequency and stirring gap width, on macroscopic transport phenomena during the solidification were investigated with corresponding experimental verification.
2 Experimental
A schematic diagram of semi-solid Al alloys slurry preparation by A-EMS is illustrated in Fig.1, which contains melt, air, cooler, crucible and electromagnetic stirrer consisting of yokes, cores and coils. The stirrer design entails the placement of the coils around the crucible to generate a rotational motion along the horizontal direction[7]. The stirring intensity and rate are changed by the adjustment of the AC voltage input employed in a range of 0-200 V, and frequency input employed in a range of 0-50 Hz, respectively. An annular chamber is designed by controlling the gap space between the crucible and the cooler, and thus an intensively forced shearing could be achieved.
In the experiments, as A357 melt was poured into the austenitic stainless steel crucible preheated to a given temperature, a cooler was inserted in the center of the crucible, and then EMS started. The lids are made of insulation kaowool, ensuring that thermal exchange during solidification mainly occurs in the radial direction. The crucible filled with semi-solid slurry was quenched into the room-temperature water immediately when the slurry temperature was cooled to a given temperature. The specimens were observed with the Zeiss-type optical microscope after grinding, polishing and etching with 0.5% HF.
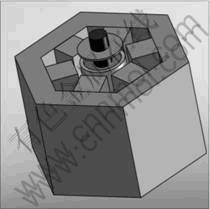
Fig.1 Schematic view of semi-solid metal slurry produced by A-EMS apparatus
3 Simulation procedure
Fig.2 shows the physical model in simulation, which is from the central cross-section of the system as shown in Fig.1. As mentioned above, a computational model coupling an electromagnetic model with a macroscopic heat and fluid flow model in semi-solid Al alloy slurry preparation by A-EMS was developed, where the influence of a three-pair-pole electromagnetic stirring on macroscopic transport phenomena during the solidification was included. The commercial software ANSYS 10.0 was used for the numerical simulation. This code allows solving the transient two-dimensional electromagnetic field, flow field and temperature field with a sequence couple. The specific modeling, solution information and relevant thermal-physical properties in simulation were provided elsewhere[6, 8].
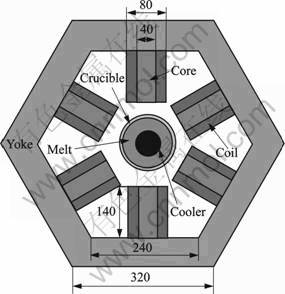
Fig.2 Physical model in simulation (unit: mm)
4 Results and discussion
4.1 Effects of stirring gap width
Fig.3 shows the distribution of electromagnetic field, velocity field and temperature field during the semisolid slurry preparation by A-EMS when stirring gap width is 20 mm, current is 50 A and frequency is 10 Hz, respectively. It is noted from Fig.3 that effects of A-EMS on electromagnetic field, flow field and temperature field can be presented apparently. Both electromagnetic field and velocity field are uniformly intensive in this narrow gap, and hence smaller temperature difference across gap is obtained. Fig.4 shows effects of stirring gap width on distribution of electromagnetic field, velocity field and temperature field. As stirring gap width decreases, electromagnetic field and velocity field mainly distribute in the narrow gap, and become more uniform and intensive; also temperature difference in the narrow gap becomes smaller and smaller. When stirring gap width arrives 10 mm, magnetic flux density and stirring velocity are very uniform and intensive, and the temperature difference in the stirring gap is only 2 ?C, which benefits for realization of uniform solidification.
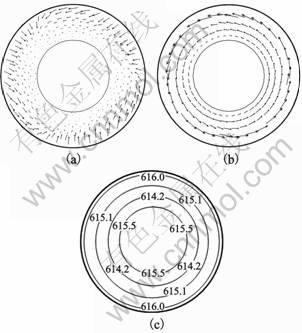
Fig.3 Distribution of electromagnetic field (a), flow field (b) and temperature field (c) in A-EMS apparatus at stirring gap width of 20 mm
4.2 Effects of stirring current
Fig.5 shows effects of stirring current on electromagnetic field, velocity field and temperature field in the radial direction at the stirring gap of 10 mm. It is found that the magnetic flux density and flow velocity in the stirring gap increase with increasing stirring current, but temperature difference in the stirring gap decreases. When stirring current is increased to 50 A, a temperature difference less than 2 ?C can be achieved.
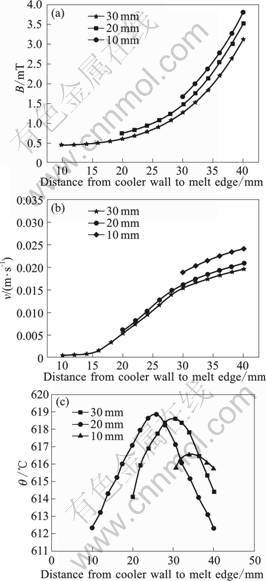
Fig.4 Effects of stirring gap width on electromagnetic field (a), velocity field (b) and temperature field (c) at frequency of 50 Hz and current of 10 A
4.3 Effects of stirring frequency
Fig.6 shows effects of stirring frequency on electromagnetic field, velocity field and temperature field in the radial direction at the stirring gap of 10 mm. It is noted that the magnetic flux density and flow velocity in the stirring gap decrease with increasing stirring frequency, but temperature difference in the stirring gap increases. It can also be figured out that the difference of the average magnetic flux density between 50 and 40 Hz is about three times that between 40 and 30 Hz, meaning that the effect of stirring frequency on the magnetic flux density in the aluminum melt is nonlinear. The velocity along the path decreases with the increase in stirring frequency in the range of 10–50 Hz. At the same frequency, the velocity decreases from the edge to center of melt.
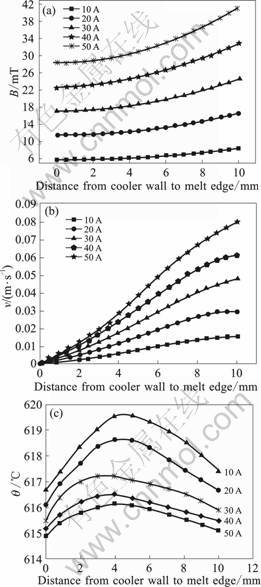
Fig.5 Effects of stirring current on electromagnetic field (a), velocity field (b) and temperature field (c) in radial direction at stirring gap of 10 mm and frequency of 10 Hz
4.4 Experimental verification
Microstructures of A357 alloy by normal EMS and A-EMS are compared in Fig.7 at frequency of 50 Hz, current of 10 A, pouring temperature of 650 ℃, crucible temperature of 300 ℃ and stirring gap width of 10 mm. It is noted that microstructure morphology is rosette-like and coarse for alloy by normal EMS, but uniformly fine and globular for alloy by A-EMS. These results are identical with other experimental ones[3-4]. Although several mechanisms had been proposed to explain the microstructure evolution in the semi-solid metal slurry preparation, it seems that the increase in nucleation density is important in this study[9-10]. In the case of normal EMS, stirring force mainly distributes at outer part of melt at the commercial frequency, and becomes weak at inner part of melt, thus a large temperature difference in the liquid is inclined to form the coarse solidification structures. However, in the case of A-EMS, strong stirring flow in the annular chamber quickly dissipates the latent heat released from the solidification front to the bulk liquid, and thus a nearly uniform temperature distribution in the liquid will be formed instantaneously, which is considered to be necessary for the simultaneous nucleation.
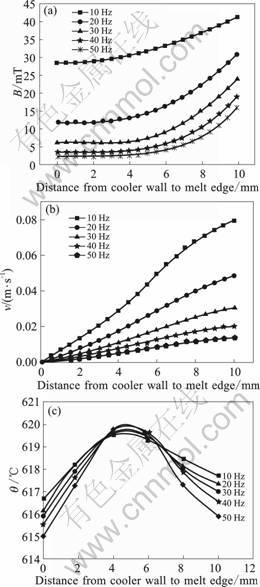
Fig.6 Effects of stirring frequency on electromagnetic field (a), velocity field (b) and temperature field (c) in radial direction at stirring gap holding of 10 mm and current of 50 A
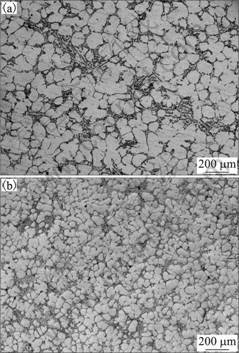
Fig.7 Microstructures of A357 alloys by normal EMS (a) and A-EMS at frequency of 50 Hz and current of 10 A (b)
5 Conclusions
1) The magnetic flux density increases, the melt velocity increases and the temperature difference decreases when stirring gap width and stirring frequency decrease or the stirring current increases.
2) The slurry with the fine and uniform globular grain structure can be gained by adjusting gap width, electromagnetic frequency and current, such as under 10 mm of gap width, electromagnetic frequeng of conditions of 10 Hz and current of 50 A. The calculated results are in reasonably good agreement with the measured ones.
References
[1] XU Jun, ZHANG Zhi-feng, BAI Yue-long, SHI Li-kai. The method and apparatus for preparing the semi-solid rheo-slurry or billets: CN200810116181.9 [P]. 2008. (in Chinese)
[2] ZHANG Zhi-feng, XU Jun, BAI Yue-long,SHI Li-kai. Development of rheo-diecasting of Al-Si alloys based on a modified DSCP process [J]. Solid State Phenomena, 2008, 141/142/143: 185-190.
[3] BAI Yue-long, XU Jun, ZHANG Zhi-feng, SHI Li-kai. Annulus electromagnetic stirring for preparing semisolid A357 aluminum alloy slurry [J]. Transactions of Nonferrous Metals Society of China, 2009, 19(5): 1104-1109
[4] ZHU Guang-lei, XU Jun, ZHANG Zhi-feng, SHI Li-kai. Annular electromagnetic stirring—A new method for the production of semi-solid A357 aluminum alloy slurry [J]. Acta Metallurgica Sinica, 2009, 22(6): 408-414.
[5] CHEN Xing-run, ZHANG Zhi-feng, XU Jun, SHI Li-kai. Numerical simulation of electromagnetic field in semi-solid slurry preparation by A-EMS [J]. Journal of University of Science and Technology Beijing, 2009,31(10): 1305-1310. (in Chinese)
[6] CHEN Xing-run, ZHANG Zhi-feng, XU Jun, SHI Li-kai. Numerical simulation of electromagnetic field, flow field and temperature field in semi-solid slurry preparation by electromagnetic stirring [J]. The Chinese Journal of Nonferrous Metals, 2010, 20(5): 937-945. (in Chinese)
[7] KANG C G, BAE J W, KIM B M. The grain size control of A356 aluminum alloy by horizontal electromagnetic stirring for rheology forging [J]. Journal of Materials Processing Technology, 2007, 187/188: 344.
[8] ZHANG Z F, KIM J M, HONG C P. Numerical simulation of grain structure evolution in solidification of an Al–5.0wt%Cu alloy under electromagnetic stirring and its experimental verification [J]. ISIJ International, 2005, 45(2): 183-191.
[9] LIU Zheng, MAO Wei-min, ZHAO Zhen-duo. Semi-solid A357 alloy slurry prepared by a new process [J]. Acta Metallurgica Sinica, 2009, 45(4): 507-512. (in Chinese)
[10] FAN Z, WANG Y, XIA M, ARUMUGANATHAR S. Enhanced heterogeneous nucleation in AZ91D alloy by intensive melt shearing [J]. Acta Materialia, 2009, 57(16): 4891-4901.
(Edited by YANG Hua)
Foundation item: Project(2006CB605203) supported by National Basic Research Program of China; Project(2009AA03Z534) supported by the National Hi-tech Research and Development Program of China
Corresponding author: ZHANG Zhi-feng; Tel: +86-10-82241229; E-mail: zhangzf@grinm.com