
Cycle stability of La0.7Mg0.3Ni2.55-xCo0.45Cux (x=0-0.4) electrode alloys
ZHANG Yang-huan(张羊换)1, 2, ZHAO Dong-liang(赵栋梁)1, LI Bao-wei(李保卫)2,
REN Hui-ping(任慧平)2, DONG Xiao-ping(董小平)1, 3, WANG Xin-lin(王新林)1
1. Department of Functional Material Research, Central Iron and Steel Research Institute, Beijing 100081, China;
2. School of Material and Metallurgy, Inner Mongolia University of Science and Technology, Baotou 014010, China;
3. School of Materials Science and Engineering, University of Science and Technology Beijing, Beijing 100083, China
Received 17 October 2006; accepted 18 June 2007
Abstract: The La0.7Mg0.3Ni2.55-xCo0.45Cux (x=0, 0.1, 0.2, 0.3, 0.4) electrode alloys were prepared by casting and rapid quenching. Ni in the alloy was partially substituted by Cu in order to improve the cycle stability of La-Mg-Ni system (PuNi3-type) hydrogen storage alloy. The effects of substituting Ni with Cu on the microstructures and cycle stability of the alloys were investigated in detail. The results obtained by XRD, SEM and TEM show that the substitution of Cu for Ni is favourable for the formation of an amorphous in the as-quenched alloy, and this leads to an obvious refinement of the as-quenched alloy grains and a growth of the lattice constants and cell volumes of the as-cast and quenched alloys. The results obtained by the electrochemical measurement indicate that the cycle stability of the alloys significantly rises with the incremental variety of Cu content. When Cu content changes from 0 to 0.4, the cycle lives of the as-cast and quenched (30 m/s) alloys are enhanced from 72 to 88 cycles and from 100 to 121 cycles, respectively.
Key words: La-Mg-Ni alloy; La0.7Mg0.3Ni2.55-x alloy; Ni; microstructures; cycle stability
1 Introduction
Intermetallic compounds for reversible hydrogen absorption/desorption have been the subject of extensive research for about 30 years. A series of metal hydride electrode materials have been discovered, such as the rare-earth-based AB5-type alloys[1], the AB2-type Laves phase alloys[2], the V-based solid solution alloys[3], and the Mg-based alloys[4]. Especially, the AB5-type hydrogen storage alloy has realized large-scale industrialization in many countries, such as Japan and China[5-6] and the small size Ni-MH cells have rapidly grown and gained a good share in the rechargeable battery market since the commercialization of small size Ni-MH cells was found in 1990. However, the rechargeable Ni-MH cells are encountering serious competition from Li-ion cells since the Li-ion cells show higher energy density than the Ni-MH cells per unit mass or volume. The discharge capacity of the currently advanced AB5-type materials has reached 320-340 mA?h/g at 0.2-0.3C rate and room temperature. It seems to be difficult to further improve the capacity of the AB5-type alloys since the theoretical capacity of LaNi5 is about 372 mA?h/g. Therefore, the investigations of the new type electrode alloys with higher capacity and longer cycle life are extremely important to exalt the competition ability of the Ni-MH batteries in the rechargeable battery field. Recently, several new and good hydrogen storage alloys were reported. The most promising candidates are the La-Mg-Ni system alloys in view of their higher discharge capacities (360-410 mA?h/g) and low production costs. However, for commercial application the rather poor cycle stability of the La-Mg-Ni system alloys has to be further improved. For this purpose, the worldwide researchers have carried out a lot of investigations and have obtained some extremely important results[7-9]. PAN et al[10] investigated the structures and electrochemical characteristics of the La0.7Mg0.3(Ni0.85Co0.15)x (x=3.15- 3.80) alloy system and obtained a maximum discharge capacity of 398.4 mA?h/g, but the cycle stability of the alloy needs to be improved further. KOHNO et al[11] found that the La5Mg2Ni23-type electrode alloy La0.7Mg0.3Ni2.8Co0.5 has a capacity of 410 mA?h/g, and good cycle stability during 30 charge-discharge cycles. It is well known that the element substitution is one of the effective methods for improving the overall properties of the hydrogen storage alloys[12-13]. Beyond all doubts, the preparation technology is extremely important for improving the performances of the alloys. Therefore, it is expected that an optimized amount of substituting Ni with Cu in the La-Mg-Ni system alloy and a selected rapid quenching technique may lead to an alloy with good cycle stability. Therefore, the effects of substituting Ni with Cu on the microstructure and the cycle stabilities of the La0.7Mg0.3Ni2.55-xCo0.45Cux (x=0-0.4) alloys were systematically investigated.
2 Experimental
2.1 Preparation of alloys
The nominal composition of the investigated alloys is La0.7Mg0.3Ni2.55-xCo0.45Cux (x=0, 0.1, 0.2, 0.3, 0.4). The alloys are represented by Cu0, Cu1, Cu2, Cu3 and Cu4, respectively. The experimental alloys were melted in an argon atmosphere using a vacuum induction furnace. The purity of all the component metals (La, Ni, Co, Mg and Cu) is at least 99.8%. In order to prevent the volatilization of magnesium during melting, a binary La-Mg intermediate alloy (30%Mg+70%La) was beforehand prepared by electrolytic synthesis and a positive argon pressure of 0.1 MPa was applied. After induction melting, the melt was poured into a copper mould cooled by water, and a cast ingot was obtained. Part of the as-cast alloys was re-melted and quenched by melt-spinning with a rotating copper wheel. Flakes of the as-quenched alloys were obtained with different quenching rates. The quenching rate is expressed by the linear velocity of the copper wheel and the quenching rates used in the experiment are 15, 20, 25 and 30 m/s.
2.2 Microstructure determination and morphology observation
The phase structures and compositions of the alloys were determined by XRD diffractometer of D/max/2400. The diffraction was performed with Cu Kα1 radiation filtered by graphite. The experimental parameters for determining phase structure are 160 mA, 40 kV and 10 (?)/min, respectively. The morphologies of the as-cast and quenched alloys were examined by SEM. The powder samples were dispersed in anhydrous alcohol for observing the grain morphology with TEM, and the crystalline state of the specimen was determined by selected area electron diffraction (SAD).
2.3 Electrode preparation and electrochemical measurement
A round electrode pellet with 15 mm in diameter was prepared by mixing 1g alloy powder with fine nickel powder in a mass ratio of 1?1 together with a small amount of polyvinyl alcohol(PVA) solution as binder, and then compressed under a pressure of 35 MPa. After drying for 4 h, the electrode pellets were immersed in 6 mol/L KOH solution for 24 h in order that the electrode is fully wet before the electrochemical measurement.
The experimental electrodes were tested in a tri-electrode open cell, consisting of a metal hydride working electrode, a NiOOH/Ni(OH)2 counter electrode and a Hg/HgO reference electrode. In order to reduce the ohmic drop between the working electrode and the reference electrode, a Luggin capillary was located close to the hydride electrode in the working electrode apartment. The electrolyte is a 6 mol/L KOH solution. The voltage between the negative electrode and the reference electrode is defined as the discharge voltage. In every cycle, the electrode was charged with a constant current of 100 mA/g for 5 h, after resting 15 min, it was then discharged at 100 mA/g to a -0.500 V cut-off voltage. The environment temperature of the measurement was kept at 30 ℃.
3 Results and discussion
3.1 Effect of substituting Ni with Cu on micro- structure
The XRD patterns of the as-cast and quenched alloys are shown in Fig.1. All of the alloys have a multiphase structure, composing of the (La, Mg)Ni3 phase, the LaNi5 phase and the LaNi2 phase. The substitution of Cu inflicted an inappreciable influence on the phase compositions of the as-cast and quenched alloys, but it changed the phase abundances of the alloys. The amount of the LaNi2 phase in the as-cast alloys grows with the increase of the Cu content, and the substitution of Cu results in broadening of the diffraction peaks. The lattice parameters of the LaNi5 and (La,Mg)Ni3 main phases in the Cu0 and Cu2 alloys, which were calculated from the XRD data by the software of Jade 5, are listed in Table 1. The results in Table 1 indicates that the substitution of Cu for Ni obviously enlarges the lattice parameters and cell volumes of the LaNi5 and (La, Mg)Ni3 main phases in the as-cast and quenched alloys, which is attributed to the atom radius of Cu being larger than that of Ni. The rapid quenching leads to an growth of c axis and a slight shortening of a axis and cell volume of the LaNi5 and (La, Mg)Ni3 main phases.
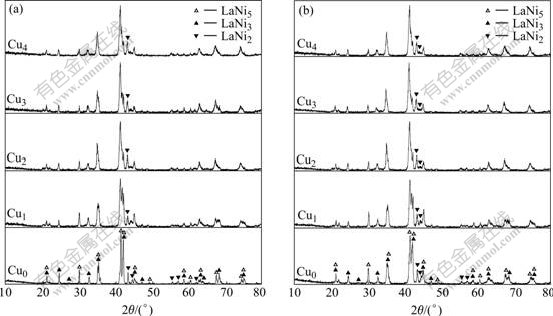
Fig.1 XRD patterns of as-cast and quenched alloys:(a) As-cast; (b) As-quenched(20 m/s)
Table 1 Lattice constants and cell volumes of (La, Mg)Ni3 and LaNi5 main phases
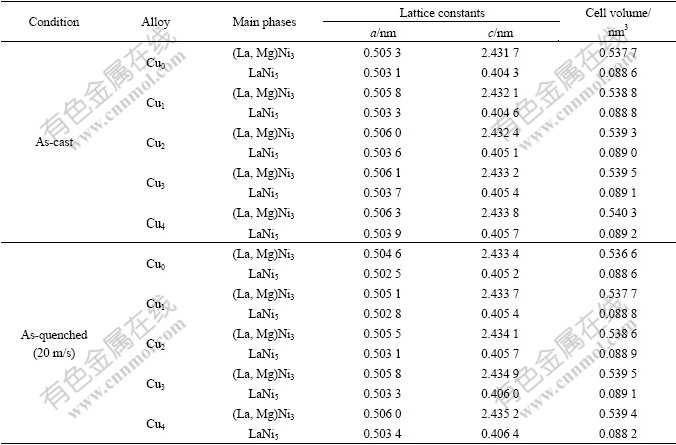
The morphologies of the as-cast and quenched alloys were inspected by SEM. The results by energy spectrum analysis indicate that all the experimental alloys are of multiphase structure, containing both the (La, Mg)Ni3 and the LaNi5 phases. Because the amount of the LaNi2 phase is small and it attaches to the (La, Mg)Ni3 phase in the process of growing, it is difficult to see the morphology of the LaNi2 phase. The grains of the as-cast alloys are very coarse and the composition homogeneity is very poor, as shown in Fig.2. Compared with the morphologies of the as-cast alloys, the rapid quenching markedly refined the grains and significantly improved the composition homogeneity of the alloys. For convenience, the plane of flake, which touches the wheel, is known as touch wheel plane, and another one is known as free plane. It can be seen from Fig.2 that the grain sizes of the quenched flake have an obvious change from the touch wheel plane to the free plane, i.e. along the thickness direction of the as-quenched flake. The further from touch wheel plane, the larger the grain size. And the morphologies of the grains change from columnar crystal to dendritic one. The substitution of Cu for Ni leads to an obvious refinement of the grains of the as-quenched alloys, suggesting that the substitution of Cu for Ni boosts the nucleation velocity and lowers the growth velocity of no-equilibrium crystallization.
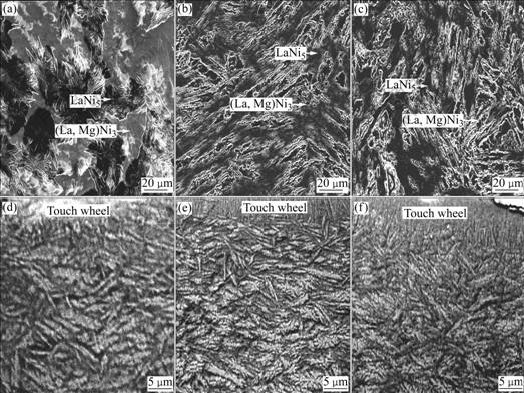
Fig.2 SEM morphologies of as-cast and quenched (20 m/s) alloys: (a), (b), (c) As-cast Cu0, Cu2 and Cu4 alloys; (d), (e), (f) As-quenched Cu0, Cu2 and Cu4 alloys
The morphologies and the crystalline state of the as-quenched alloys were examined by TEM. As shown in Fig.3, some amount of amorphous phase exists in Cu0 and Cu4 alloys when the quenching rate is 30 m/s. The SAD of the Cu0 alloy displays an obvious crystal characteristic, but it exhibits a typical amorphous structure in Cu4 alloy. This implies that the substitution of Cu is favourable for the formation of an amorphous phase.
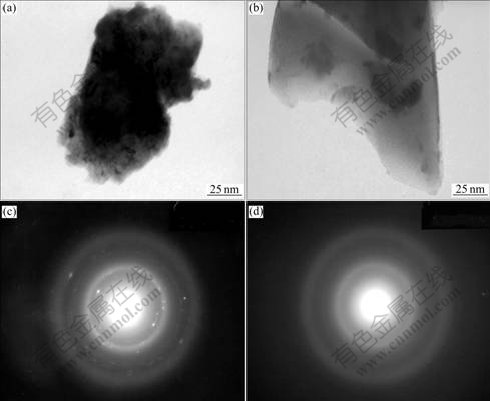
Fig.3 SEM morphologies and SAED of as-quenched (30 m/s) alloys: (a), (b) Morphologies of Cu0 and Cu4 alloys; (c) (d) SAD of Cu0 and Cu4 alloys
3.2 Effect of substituting Ni with Cu on cycle stability
The cycle life, indicated by N, is characterized by the cycle number after which the discharge capacity of the alloy obtained with a current density of 100 mA/g is reduced to 60% of the maximum capacity. The cycle number dependence of the discharge capacity of the as-cast and quenched alloys is illustrated in Fig.4. As shown in Fig.4, the substitution of Cu smoothes the slopes of the curves of the alloys, and the slopes of the curves of the alloys descend with the increase of the quenching rate, indicating that both the substitution of Cu and the rapid quenching can improve the cycle stability of the alloys. In order to present the effect of the Cu content on the cycle life of the alloys, the curves of cycle life vs Cu content of the as-cast and quenched alloys are shown in Fig.5. It turns out that a growth of Cu content involves a significant enlargement in the cycle life of the as-cast and quenched alloys. When the Cu content grows from 0 to 0.4, the cycle lives of the as-cast and quenched (30 m/s) alloys enhanced from 72 to 88 cycles and from 100 to 122 cycles, respectively. It is noteworthy that the substitution of Cu for Ni as well as rapid quenching leads to an obvious decrease of the discharge capacity of the alloys, and a similar result was obtained by LIAO et al[14].
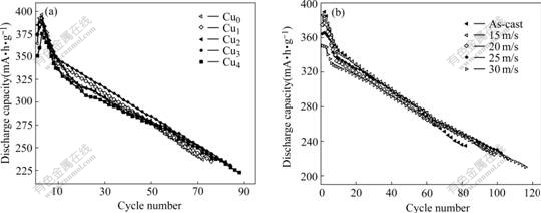
Fig.4 Evolution of discharge capacity of alloys with cycle number: (a) As-cast alloys; (b) Cu2 alloy
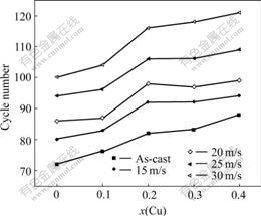
Fig.5 Curves of cycle life vs Cu content as-cast and quenched alloys
The failure of the battery is characterized by the decay of the discharge capacity and the decrease of the discharge voltage[15]. The cycle stability of the electrode alloy is an overwhelming factor of the life of a Ni-MH battery because the root cause leading to battery lose efficacy is on the negative electrode rather than on the positive electrode. In order to understand correctly the mechanism of the efficacy loss of the electrode alloy, the morphologies of the as-cast and quenched alloy particles before and after the electrochemical cycle observed by SEM are shown in Fig.6. The result in Fig.6 shows that the mechanism of the efficacy loss of the La-Mg-Ni system electrode alloy is different from that of the AB5-type alloy electrode. The particle sizes and surface morphologies of the alloys have some changes after the electrochemical cycle, leading to a disappearance of the pointedness of the particle and to a slight decrease of the particle sizes. This confirms that the pulverization of alloy particles takes place in process of the electro- chemical cycle, but the pulverization degree of the alloy is much smaller than that of the AB5-type alloy[16]. It is worthy to be noticed that a rough and porous layer can be found on the surface of the alloy particles after electrochemical cycling. The results analyzed by XRD as shown in Fig.7 confirm that the magnesium and lanthanum hydroxides are formed on the surface of the alloy particles in strong alkaline solution. Obviously, two factors are responsible for the capacity degradation of the alloy electrode. One of them is the formation of passive layers of La(OH)3 and Mg(OH)2 on the alloy surface because such a layer not only weakens the surface electrocatalytic activity and prevents the diffusion of hydrogen into or from the alloy bulk, but also decreases the content of hydrogen absorption elements La and Mg in the alloys. Consequently, the discharge capacity of the alloy significantly reduces. On the other hand, the pulverization of the alloy particles is also an important cause of the capacity degradation, owing to the pulverization enlarged the superficial area of the alloy, which accelerates the formation of La and Mg hydroxides and leads to the rapid degradation of the alloy’s capacity. Therefore, it can be concluded that an effective approach of enhancing the cycle life of the La-Mg-Ni system hydrogen storage electrode alloy is to improve the anti-corrosion and anti-oxidation capabilities of the alloys in the alkaline electrolyte.
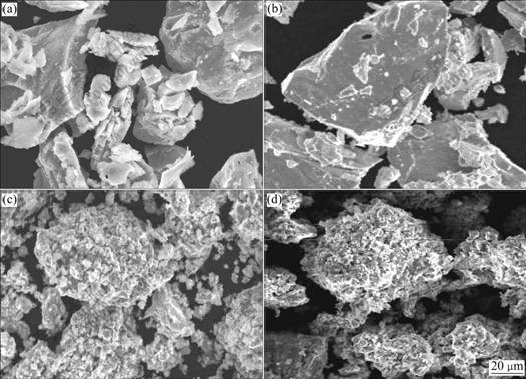
Fig.6 SEM morphologies of as-cast alloys before and after electrochemical cycle: (a), (b) Before cycle, Cu0 and Cu4 alloys; (c), (d) After cycle, Cu0 and Cu4 alloys
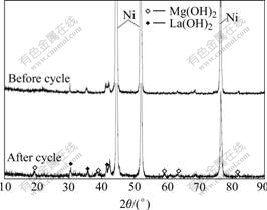
Fig.7 XRD patterns of alloy (x=1.0) before and after electrochemical cycle
The fact that the substitution Cu raises the cycle stability of as-cast alloys is due to the formation of a dense oxide film on the alloy surface that can effectively prevent alloy electrode erosion in alkaline solution. The main cause that the substitution of Cu prolongs the cycle life of the as-quenched alloys is that Cu promotes the formation of an amorphous phase in the alloys. In addition, the substitution of Cu enlarges the lattice parameters and cell volumes of the alloys, which minifies the ratio of expansion/contraction of the alloy in process of the hydrogen absorption/desorption and strengthens the anti-pulverization capability of the alloys. Therefore, the cycle stability of the alloys is improved further.
4 Conclusions
1) The substitution of Cu for Ni has little influence on the phase compositions of the as-cast and quenched La0.7Mg0.3Ni2.55-xCo0.45Cux (x=0, 0.1, 0.2, 0.3, 0.4) alloys. But it increases the abundance of the LaNi2 phase in the as-cast alloys and boosts the formation of an amorphous phase in the as-quenched alloys. In addition, the substitution of Cu leads to an increase of the lattice constants and cell volumes of the as-cast and quenched alloys and an obvious refinement of the as-quenched alloy grains.
2) The substitution of Cu for Ni significantly improves the cycle stability of the as-cast and quenched alloys, but its influence on the cycle life is stronger on the as-quenched alloys than on the as-cast one. This mainly attributes to the formation of an amorphous phase and the grain refinement of the alloy.
3) The main reason of leading to the efficacy loss of the La-Mg-Ni system alloy electrode is the oxidation and corrosion of the electrode surface in the alkaline electrolyte. An effective approach of enhancing the cycle life of the La-Mg-Ni system electrode alloys is to intensify their anti-corrosion and anti-oxidation capabilities in alkaline electrolyte.
References
[1] WILLEMS J J G, BUSCHOW K H J. A nickel metal hydride battery for electric vehicles [J]. J Less-Common Met, 1987, 129: 13-30.
[2] OVSHINSKY S R, FETCENKO M A, ROSS J. From permanent magnets to rechargeable hydride electrodes [J]. Science, 1993, 260: 176-181.
[3] TSUKAHARA M, KAMIYA T, TAKAHASHI K, KAWABATA A, SAKURAI S, SHI J, TAKESHITA H T, KURIYAMA N, SAKAI T. Hydrogen storage and electrode properties of V-based solid solution type alloys prepared by a thermic process [J]. J Electrochem Soc, 2000, 147: 2941-2944.
[4] SUN D L, ENOKI H, GINGL F, AKIBA E. New approach for synthesizing Mg-based alloys [J]. J Alloys Comp, 1999, 285: 279-283.
[5] UEHARA I, SAKAI T, ISHIKAWA H. The state of research and development for applications of metal hydrides in Japan [J]. J Alloys Comp, 1997, 253/254: 635-641.
[6] WANG Q D, CHEN C P, LEI Y Q. The recent research, development and industrial applications of metal hydrides in the People’s Republic of China [J]. J Alloys Comp, 1997, 253/254: 629-634.
[7] KADIR K, KURIYAMA N, SAKAI T, UEHARA I, ERIKSSON L. Structural investigation and hydrogen capacity of CaMg2Ni9: A new phase in the AB2C9 system isostructural with LaMg2Ni9 [J]. J Alloys Comp, 1999, 284: 145-154.
[8] CHEN J, KURIYAMA N, TAKESHITA H T, TANAKA H, SAKAI T, HARUTA M. Hydrogen storage alloys with PuNi3-type structure as metal hydride electrode [J]. Electrochem Solid-State Lett, 2000, 3(6): 249-252.
[9] LIAO B, LEI Y Q, LU G L, CHEN L X, PAN H G, WANG Q D. The electrochemical properties of LaxMg3-xNi9 (x=1.0-2.0) hydrogen storage alloys [J]. J Alloys Comp, 2003, 356/357: 746-749.
[10] PAN H G., LIU Y F, GAO M X, ZHU Y F, LEI Y Q, WANG Q D. An investigation on the structural and electrochemical properties of La0.7Mg0.3(Ni0.85Co0.15)x (x=3.15-3.80) hydrogen storage electrode alloys [J]. J Alloys Comp, 2003, 351: 228-234.
[11] KOHNO T, YOSHIDA H, KAWASHIMA F, INABA T, SAKAI I, YAMAMOTO M, KANDA M. Hydrogen storage properties of new ternary system alloys: La2MgNi9, La5Mg2Ni23, La3MgNi14 [J]. J Alloys Comp, 2000, 311: L5-L7.
[12] TAKASAKI A, SASAO K. Hydrogen absorption and desorption by Mg67-xCaxNi33 powders prepared by mechanical alloying [J]. J Alloys Comp, 2005, 404/406: 431-434.
[13] PAN H G, LIU Y F, GAO M X, LI R, LEI YQ. Function of cobalt in the new type rare-earth Mg-based hydrogen storage electrode alloys [J]. Intermetallics, 2005, 13: 770-775.
[14] LIAO B, LEI Y Q, CHEN L X, LU G L, PAN H G, WANG Q D, A study on the structure and electrochemical properties of La2Mg(Ni0.95M0.05)9 (M=Co, Mn, Fe, Al, Cu, Sn) hydrogen storage electrode alloys [J]. J Alloys Comp, 2004, 376: 186-195.
[15] CHARTOUNI D, MELI F, Z?TTEL A, GROSS K, SCHLAPBACH L. The influence of cobalt on the electrochemical cycling stability of LaNi5-based hydride forming alloys [J]. J Alloys Comp, 1996, 241: 160-166.
[16] ZHANG Y H, DONG X P, WANG G Q, GUO S H, REN J Y, WANG X L. Cycling stability of La-Mg-Ni system (PuNi3-type) hydrogen storage alloy prepared by casting and rapid quenching [J]. The Chinese Journal of Nonferrous Metals, 2005, 15(5): 705-710.(in Chinese)
Foundation item: Project(50642033) supported by the National Natural Science Foundation of China; Project(20050205) supported by the Key Technologies Research and Development Program of Inner Mongolia; Project(NJ05064) supported by the Higher Education Science Research Program of Inner Mongolia, China
Corresponding author: ZHANG Yang-huan; Tel: +86-10-62187570; E-mail: zyh59@yahoo.com.cn
(Edited by HE Xue-feng)