
Microstructures and mechanical properties of AZ80 alloy treated by pulsed ultrasonic vibration
ZHANG Zhi-qiang(张志强), LE Qi-chi(乐启炽), CUI Jian-zhong(崔建忠)
Key Laboratory of Electromagnetic Processing of Materials of Ministry of Education, Northeastern University,
Shenyang 110004, China
Received 12 June 2008; accepted 5 September 2008
Abstract: Pulsed ultrasonic field was employed in the melt of the AZ80 magnesium alloy. The effects of pulsed ultrasonic field on microstructure and mechanical properties of AZ80 magnesium alloy were investigated. The results show that the as-cast microstructure of the AZ80 alloy with pulsed ultrasonic treatment is significantly changed. Pulsed ultrasonic field significantly decreases the grain size, changes the morphologies of the β-Mg17Al12 phases and reduces their area fraction. It is found that pulse width of ultrasonic plays an important role on the microstructure formation of AZ80 alloy. With increasing pulse width, grains become finer and more uniform. In the range of experimental parameters, the optimum pulse width for melt treatment process is found to be 210 μs. The mechanical tests show that the mechanical properties of the as-cast AZ80 magnesium alloy with pulsed ultrasonic treatment are much higher than those of AZ80 alloy without ultrasonic field.
Key words: AZ80 magnesium alloy; pulsed ultrasonic vibration; microstructure; mechanical properties
1 Introduction
It is well recognized that the mechanical properties would be benefited from the microstructures with fine grains of metallic alloy including magnesium alloys. The microstructure refinement of magnesium alloys has become an important research field. In general, two different approaches to grain refinement by solidification processing have been pursued: chemical stimulation[1-3] and physical induction[4-6]. The chemical route depends primarily on the selection of a nucleating catalyst, while the physical one relies mainly on the use of an external field. The chemical route is easy to apply but it is not always possible to find or develop a potent nucleus for a given group of alloys, for example, Mg-Al alloys[7-8]. This makes the physical route a necessary option for many cast alloys.
Ultrasonic treatment is a simple and effective physical means for solidification control. In 1878, the ultrasonic vibration was firstly introduced into metallurgical application to refine grains[9]. When ultrasonic vibrations are coupled to the solidifying melts, microstructural changes occur including grain refinement, increased homogeneity and reduced segregation. Many studies on ultrasonic vibration are mainly focused on the as-cast grain refinement of low-melting alloys or aluminum alloys[10-11]. However, few experiments have been made on the application of pulsed ultrasonic vibration to the magnesium alloys. Therefore, in this work, pulsed ultrasonic field was introduced into magnesium alloy melts and the effects of pulsed ultrasonic vibration on the as-cast microstructure and mechanical properties of magnesium alloy AZ80 were investigated.
2 Experimental
Magnesium alloy AZ80 was used as the experimental material. The melting of AZ80 Mg alloy was carried out in a laboratory resistance furnace with an iron crucible and protected by CO2+0.5% SF6 atmosphere in order to prevent severe oxidation. The melt was overheated to (650±10) ℃ and controlled at this temperature for 600 s. Then the preheated ultrasonic radiator was inserted into the magnesium alloy melt and the magnesium alloy melt was treated by the pulsed ultrasonic. The treated melt was water quenched immediately after the pulsed ultrasonic treatment. For comparison reasons, samples were also made without ultrasonic vibration. For convenience, without pulsed ultrasonic treatment was defined as 0 μs pulse width ultrasonic treatment.
The experimental apparatus for ultrasonic treatment is shown in Fig.1. The ultrasonic system used for this research consisted of a metallurgic ultrasonic system, a resistant furnace and an iron crucible. The ultrasonic system consisted of a ultrasonic generator with the frequency of (20±2) kHz, a magnetostrict transducer made of high purity nickel sheets, and a acoustic radiator made of mild steel. Pulsed ultrasonic power of the unit could be adjusted from 0 to 2 kW and pulse width could
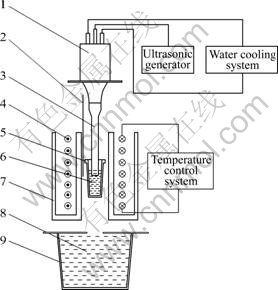
Fig.1 Schematic of experiment arrangement: (1) Ultrasonic transducer; (2) Thermocouple; (3) Ultrasonic radiator; (4) Resistance heater; (5) Iron crucible; (6) Mg-9.0Al%; (7) Ceramic tube; (8) Water; (9) Tank
also be adjusted from 0 μs to 210 μs. During the treatment procedure, the temperature of melt, the preheating temperature of the radiator and the time of applying the ultrasonic field were precisely controlled. In this experimental procedure, the melt of AZ80 alloy was treated by ultrasonic with the power of 150 W for 50 s and with the pulse width of 0, 75, 150 and 210 μs, respectively.
The microstructure of the AZ80 alloy samples was studied by optical microscope (Leica DMR), scanning electron microscope (SEM). SEM was done in an SSX-50 machine attached with an energy dispersive spectroscope (EDS). The optical microstructures were captured and their average grain diameters were measured with Leica DMR image analysis software. The area fraction of constituent phase was measured from the recorded SEM images taken using software SISCIA S8.0. Besides, the tensile specimens with a gauge length of 36 mm and a gauge diameter of 6 mm were made from the longitudinal sections of the samples. The tensile properties were measured using CMT5105 universal test machine at a constant ram velocity of 0.5 mm/min.
3 Results and discussion
3.1 Effects of pulsed ultrasonic treatment on microstructure of AZ80 alloy
Fig.2 shows the typical microstructures of AZ80 alloy without and with different pulse width ultrasonic treatment. It is clear that without pulsed ultrasonic treatment, the coarse dendrites of the primary phase (α-Mg) are present throughout the sample in Fig.2(a), demonstrating the normal dendrite growth mode. As shown in Fig.2(a), one branch of a primary dendrite is about 170 μm in length, which indicates that the grain size is about 340 μm since one equiaxed grain usually contains six primary dendrite arms. Fig.2(a) and (b) display a certain difference in terms of the dendrite size.

Fig.2 Microstructures of AZ80 alloy obtained by different ultrasonic pulse width at 650 ℃ for 50 s (pulsed ultrasonic power 150 W): (a) Without pulsed ultrasonic treatment; (b) 75 μs; (c) 150 μs; (d) 210 μs
With the application of different pulse width ultrasonic vibration, the proportion of long dendrites is less than that without pulsed ultrasonic treatment. Furthermore, with the increase of pulse width, more and more long dendrites can be broken up and spheroidized by stronger pulsed ultrasonic wave. When the pulse width of pulsed ultrasonic is 75 μs, a mixed grain structure is observed, as shown in Fig.2(b). However, when the pulsed width is increased to 150 μs, the grains are greatly refined and the average grain size is about 130 μm, as shown in Fig.2(c). With further increasing pulse width of pulsed ultrasonic, no significant effect on grain size is observed. Fig.2(d) shows the result when the pulse width is 210 μs. These are attributed to the fact that, when pulsed ultrasonic is introduced into the molten alloy, two basic phenomena of acoustic cavitation and acoustic streaming will occur. Acoustic cavitation can lead to supercooling in the local zone[11]. Thus, a mass of extrinsic nucleation is formed. The formed nucleus can be distributed throughout the melt by the acoustically induced streaming. As a result, the grain size of AZ80 magnesium alloy is improved significantly.
The SEM images of as-cast microstructure of AZ80 alloy without and with pulsed ultrasonic treatment are shown in Fig.3. The as-cast microstructures of AZ80 alloy without pulsed ultrasonic treatment consist of the coarse primary dendrites (α-Mg, see Fig.2(a)) and the continuous bulk skeletal β-Mg17Al12 compounds (see
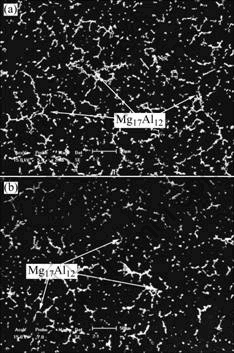
Fig.3 SEM images showing as-cast microstructure of AZ80 alloy: (a) Without pulsed ultrasonic treatment; (b) With pulsed ultrasonic treatment (P =150 W; pulse width = 150 μs)
Fig.3(a)), which are mainly distributed at grain boundaries. Fig.3(b) shows the microstructure of the AZ80 alloy with pulsed ultrasonic treatment. Compared with the microstructure of the AZ80 without pulsed ultrasonic treatment, the average grain size and area of β-Mg17Al12 compounds in AZ80 alloy are decreased from 290 μm to 130 μm and 30 131 μm2 to 21 010 μm2, respectively. The continuous skeletal β-Mg17Al12 phases become fine and uniform, and change into almost discontinuous net shape and particle, and their amounts are obviously reduced (see Fig.3(b)). In addition, the area fraction of β-Mg17Al12 phase in AZ80 alloy without and with pulsed ultrasonic treatment was also measured by software SISCIA S8.0. The statistical value of area fraction of the β-Mg17Al12 phase is 9.9% in AZ80 alloy without pulsed ultrasonic treatment. With pulsed ultrasonic treatment, the area fraction of the β-Mg17Al12 phase is reduced to 6.8% and the reduction extent is 31.6%. It is supposed that pulsed ultrasonic treatment produces evidently refining effect on AZ80 alloy. Because of cavitation and acoustic streaming, the grains of AZ80 alloy are very fine. Thus, the finer the grains are, the lower the content and the smaller the size of the β-phases is.
3.2 Effects of pulsed ultrasonic treatment on mechanical properties of AZ80
Fig.4 shows the mechanical properties of AZ80 alloy without and with different pulse width ultrasonic treatments. It is clear that the ultimate tensile strength (σb) and elongation (δ) of the AZ80 alloy without pulsed ultrasonic treatment are correspondingly lower than those of the treated ones. With increasing pulse width from 0 μs to 75 μs, the ultimate tensile strength and the elongation are increased observably from 123 MPa to 162 MPa and from 2.75% to 4.34%, respectively. When the pulse width is increased to 150 μs, the ultimate tensile
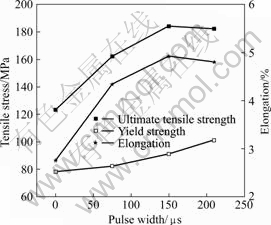
Fig.4 Mechanical properties of AZ80 alloy without and with different pulse width ultrasonic treatments
strength and the elongation are increased by 184 MPa and 4.92%, respectively. While, with increasing pulse width from 150 μs to 210 μs, the ultimate tensile strength and the elongation do not show apparent difference. When increasing pulse width from 0 μs to 75 μs and then to 150 μs, the yield strength (σ0.2) has no remarkable fluctuation. When the pulse width reaches 210 μs, a prominent ascent of yield strength appears and is increased to 101 MPa. The pulsed ultrasonic treatment refines microstructures greatly and makes grains equiaxed or nearly equiaxed, resulting in forming fewer amounts of the β-Mg17Al12, and the continuous skeletal β-Mg17Al12 phases become fine, uniform and change into almost discontinuous net shape and particle, which is helpful for improving mechanical properties. So the mechanical properties of AZ80 alloy with different pulse width ultrasonic treatments are much higher than those of AZ80 alloy without pulsed ultrasonic treatment.
4 Conclusions
1) The as-cast microstructures of A80 alloy with pulsed ultrasonic treatment are significantly refined from coarse dendrites without pulsed ultrasonic treatment to spherical equiaxed grains. The average grain size of AZ80 alloy is decreased from 290 μm without pulsed ultrasonic treatment to 130 μm with 210 μs pulse width ultrasonic treatment.
2) The β-Mg17Al12 phases of AZ80 alloy without pulsed ultrasonic treatments are coarse, continuous and non-uniform. After the pulsed ultrasonic treatment, the phases are fine, discontinuous and uniform throughout the alloy, and their amounts are obviously reduced.
3) The superior mechanical properties, such as yield strength (101 MPa), ultimate tensile strength (182 MPa) and fracture strain (4.8%) are achieved in the AZ80 alloy with 210 μs pulse width ultrasonic treatment.
References
[1] NOGITA K, DAHLE A K. Effects of boron on eutectic modification of hypoeutectic Al-Si alloys[J]. Scripta Materialia, 2003, 48(3): 307-313.
[2] LU L M, DAHLE A K, STJOHN D H. Grain refinement efficiency and mechanism of aluminium carbide in Mg-Al alloys[J]. Scripta Materialia, 2005, 53(5): 517-522.
[3] EMLEY E F. Principles of magnesium technology[M]. Oxford: Pergamon Press, 1966: 200-208.
[4] GUO Shi-jie, LE Qi-chi, ZHAO Zhi-hao, CUI Jian-zhong. Microstructural refinement of DC cast AZ80 Mg billets by low frequency electromagnetic vibration[J]. Mater Sci Eng A, 2005, 404(1/2): 323-329.
[5] ESKIN G I. Broad prospects for commercial application of the ultrasonic (cavitation) melt treatment of light alloys[J]. Ultrasonics Sonochemistry, 2001, 8: 319-325.
[6] ZHNAG Zhi-qiang, LE Qi-chi, CUI Jian-Zhong. Ultrasonic treatment of magnesium alloy melts and its effects on solidification microstructures[J]. Materials Science Forum, 2007, 546/549: 129-132.
[7] STJOHN D H, MA Q, EASTON M A. Grain refinement of magnesium alloys[J]. Metallurgical and Matertials Transactions A, 2005, 36(7): 1669-1679.
[8] LEE Y C, DAHLE A K, STJOHN D H. The role of solute in grain refinement of magnesium[J]. Metallurgical and Materials Transactions A, 2000, 31(11): 2895-2906.
[9] ESKIN G I. Ultrasonic treatment of light alloy melts[M]. Amsterdam: Gordon & Breach, 1998: 1-6.
[10] JIAN X G, THOMAS T M, HAN Q Y. Refinement of eutectic silicon phase of aluminum A356 alloy using high-intensity ultrasonic vibration[J]. Scripta Materialia, 2006, 54(5): 893-896.
[11] ABRAMOV V, ABRAMOV O, BULGAKOV V, SOMMER F. Solidification of aluminium alloys under ultrasonic irradiation using water-cooled resonator[J]. Materials Letters, 1998, 37(1/2): 27-34.
(Edited by YANG Hua)
Foundation item: Projects(2007CB613701; 2007CB613702) supported by the National Basic Research Program of China; Project(50574028) supported by the National Natural Science Foundation of China; Project(2006BAE04B01-5) supported by the National Key Technology R&D Program of China; Project(B07015) supported by the 111 Project of China
Corresponding author: ZHANG Zhi-qiang; Tel: +86-24-83687734; E-mail: zqzhang@mail.neu.edu.cn