
Corrosion behavior on aluminum alloy LY12 in simulated atmospheric corrosion process
WANG Zhen-yao(王振尧), MA Teng(马 腾), HAN Wei(韩 薇), YU Guo-cai(于国才)
Environmental Corrosion Center, Institute of Metal Research, Chinese Academy of Sciences,
Shenyang 110016, China
Received 17 April 2006; accepted 22 January 2007
Abstract: The corrosion behavior of typical high-strength aluminum alloy LY12 was studied by accelerated corrosion tests of cyclic wet-dry-immersion containing media of NaHSO3 and NaCl to simulate the corrosion process in different atmosphere environment, and the corrosion mechanism was also discussed. The main experimental techniques include mass loss, morphological check, analysis of corrosion products and electrochemical measurement. The result shows that the mass loss of LY12, with or without cladding, has linear relationship with test time in the three kinds of chemical media, 0.02 mol/L NaHSO3, 0.006 mol/L NaCl and 0.02 mol/L NaHSO3+0.006 mol/L NaCl, respectively. A layer of cladding on high-strength aluminum alloy can raise evidently the resistance of atmospheric corrosion. Cl- can promote pitting generation on the oxide film of LY12 when
exists, LY12 can react much intensely with
derived from anions.
Key words: aluminum alloy; atmospheric corrosion; accelerated corrosion test; surface analysis; electrochemical measure
1 Introduction
Aluminum alloys are generally considered to have good resistance to corrosion in atmosphere[1]. Uncoated aluminum alloys are used extensively in many fields, including structural materials, electrical conductor and thermal conductor. A number of atmospheric corrosion tests of aluminum alloys were performed[2-5]. But there are the shortages of long test period, high cost, difficult control for surrounding factors in atmospheric corrosion. Therefore, the development and application of simulated accelerated test methods in laboratory were important more and more. The influence of different pollutants and ions on corrosion of aluminum alloys was studied by means of accelerated test[6-8]. A lot of study on corrosion behaviour of aluminum alloys in simple environment system, especially in solutions containing Cl-[9-11], was carried out. Less study was performed in complex environment system, for example, the effect of
cooperating with Cl- in corrosion of aluminum alloys in dry-wet cycle condition. In this paper, the corrosion behavior of typical high-strength aluminum alloy LY12 was studied by accelerated corrosion test of cyclic wet-dry-immersion containing media of NaHSO3 and NaCl.
2 Experimental
2.1 Experimental material
Typical high-strength aluminum alloy LY12 samples of 100 mm?50 mm?0.9 mm were made, and its heat treatment state is T3. The chemical compositions of the samples were (mass fraction, %): Cu 3.8-4.9, Mg 1.2-1.8, Mn 0.3-0.9, Al balanced. The alloy was clad with a layer of industrial pure aluminum. The layer was wiped off using 5% NaOH solution at 75 ℃[12]. The thickness of the samples without cladding was 0.7 mm. All samples were washed with acetone for removing oil on the surface, then dried and weighted (exactness 0.1 mg). A group of samples consisting of three pieces of sample in a desired test period were taken off, and the samples were washed by 50 mL H3PO4+20 g CrO3+1 L distilled water, and then by HNO3 for 5 min to remove corrosion product and weighted for calculation of mass losses[13].
2.2 Accelerated corrosion test
A DW-UD-3 type equipment of cyclic wet-dry- immersion was used. 0.02 mol/L NaHSO3, 0.02 mol/L NaHSO3+0.006 mol/L NaCl, 0.006 mol/L NaCl, was used as immersion agents to simulate the corrosion process in different atmosphere environments, respectively. The test parameters are listed in Table 1. The test was performed for 240 h, and the samples in every desired period of 48 h were taken off for measurements.
Table 1 Parameters of wet-dry-immersion cycle test
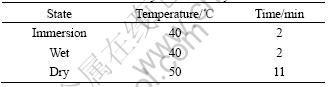
2.3 Surface analysis
The corrosion products on aluminum alloy LY12 without cladding corroded for different time were analyzed by scanning electron microscopy(SEM) and X-ray photoelectron spectroscopy ((XPS).
2.4 Electrochemical measurement
The dimension of electrochemical sample was 10 mm×10 mm. The surface of the samples without cladding was polished by abrasive papers from No.400 to No.1000. The electrochemical impedance spectroscopy (EIS) and polarization curve of the samples corroded for different time we ermeasured by EG&G PARC M398 and M352 electrochemical system at a room temperature. The electrolyte came from immersion solution was used to accelerated corrosion test without charging gas. A platinum sheet was served as assistant electrode, a saturated sulfite hydrargyrum (HgSO3) was used as reference electrode. CView2.3 and ZView2.3 software for electrochemical analysis were used.
3 Results and discussion
3.1 Behavior of mass loss
The relationship between test time and mass losses of LY12 aluminum alloys with cladding and without cladding, in the three kinds of media, 0.02 mol/L NaHSO3, 0.02 mol/L NaHSO3+0.006 mol/L NaCl, 0.006 mol/L NaCl is shown in Fig.1. It can be seen that the mass loss of LY12 aluminum alloy with cladding in 0.02 mol/L NaHSO3+0.006 mol/L NaCl is greater than that in 0.02 mol/L NaHSO3, and the mass loss in 0.006 mol/L NaCl is the least in the three kinds of media. The law for corrosion of LY12 aluminum alloy without cladding is similar to that with cladding mentioned above. The corrosion of LY12 aluminum alloy without cladding is more severe than that with cladding.
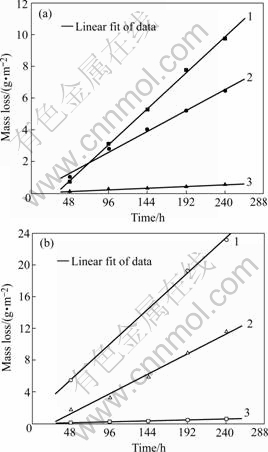
Fig.1 Mass loss of LY12 vs test time in different solutions: 1—0.02 mol/L NaHSO3+0.006 mol/L NaCl; 2—0.02 mol/L NaHSO3; 3—0.006 mol/L NaCl; (a) With cladding; (b) Without cladding
Average mass losses of LY12 aluminum alloy samples exposed to simulated environments for different periods are plotted in the linear form in Fig.1. Reasonable straight line is analytically described by the equation m=C+Vt, where m represents the average mass loss, g/m2; t is the test time, h; V is the average corrosion rate in test process, g/(m2·h); C is a constant, g/m2. Fitting results and relative coefficients R are listed in Table 2. The results show that average corrosion rate of the samples with cladding in 0.02 mol/L NaHSO3 is 0.027 63 g/(m2·h); and in 0.006 mol/L NaCl is 0.002 14 g/(m2·h), in 0.02 mol/L NaHSO3+ 0.006 mol/L NaCl is 0.047 29 g/(m2·h), being 1.7 times higher than that in 0.02 mol/L NaHSO3 (0.047 29/0.027 63= 1.711 5) and 22 times higher than that in 0.006 mol/L NaCl (0.047 29/0.002 14=22.098 1). It can also be obtained that average corrosion rate of the samples without cladding in 0.02 mol/L NaHSO3 is 1.9 times higher than that with cladding (0.052 29/0.027 63=1.892 5); in 0.006 mol/L NaCl, 1.2 times higher than that with cladding (0.002 68/ 0.002 14); in 0.02 mol/L NaHSO3+0.006 mol/L NaCl, 2 times higher than that with cladding (0.092 85/0.047 29=1.963 4). This shows that the effect of
cooperating with Cl- on the accelerated corrosion of samples is remarkable, and the layer of cladding can raise effectively corrosion resistance of LY12 aluminum alloy.
3.2 Micrograph and corrosion product of LY12 aluminum alloy without cladding
SEM images of sample exposed to 0.02 mol/L NaHSO3 for different time are shown in Fig.2. The results show that pitting corrosion can be seen easily after test for 96 h in Fig.2(b), its number and size increase gradually with the increase of test time, and most appearance looks shallow and circle. Corrosion products on surface of samples corroded for 240 h are hardly observed, and the region beside pits becomes rough gradually, indicating that new pitting corrosion is formed (Figs.2(c) and (d)).
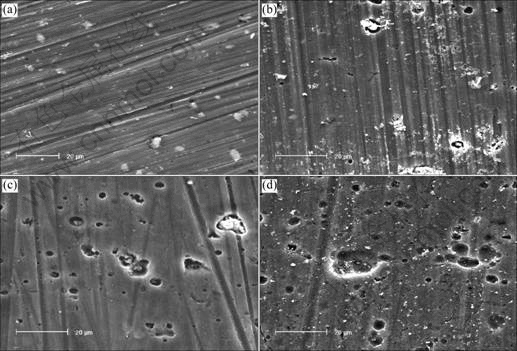
Fig.2 SEM images of samples exposed to 0.02 mol/L NaHSO3 for different test time: (a) 0, uncorroded; (b) 96 h; (c) 144 h; (d) 240 h
XPS analysis on surface of samples exposed to 0.02 mol/L NaHSO3 for 240 h is shown in Fig.3. It can be seen that the intension peak of aluminum element at binding energy 74.9 eV is corresponded to three-valued aluminum ions, which come from Al2(SO4)3, Al(OH)3, AlOOH etc[14]; the intension peak of sulfur element at 168.8 eV is corresponded to
[15]; and the intension peak of copper element at 933.2 eV and 953.7 eV come from the enrichment of alloy’s copper on the surface. This shows that sulphate aluminum exists really on surface of sample exposed to 0.02 mol/L NaHSO3 for 240 h, and the selective dissolution of LY12 aluminum alloy results in copper enrichment on the surface.
SEM images of surface of sample exposed to 0.02 mol/L NaHSO3+0.006 mol/L NaCl for different times are shown in Fig.4. It can be seen that small corrosion pits on surface of sample appear after 48 h (Fig.4(a)), white corrosion products around corrosion pits appear after 96 h and look like cirques (Fig.4(b)), rupturing into several parts. The corrosion products include mainly three kinds of element, aluminum, oxygen and sulfur, and the proportions of their atoms are approximately 31.25, 62.44, 6.31 (XPS result). The cirques corrosion products disappear after 192 h. The number of corrosion pits increases with the increase of test time. A thin layer of corrosion products derived from pits forms after 240 h, and the layers cracks because of dehydration.
Table 2 Mass loss of aluminum alloy LY12 vs test time in different media
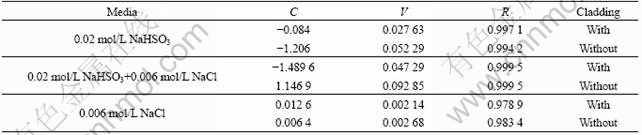
Fig.3 XPS spectra collected from samples exposed to 0.02 mol/L NaHSO3 for 240 h: (a) Al 2p; (b) S 2p; (c) Cu 2p3/2
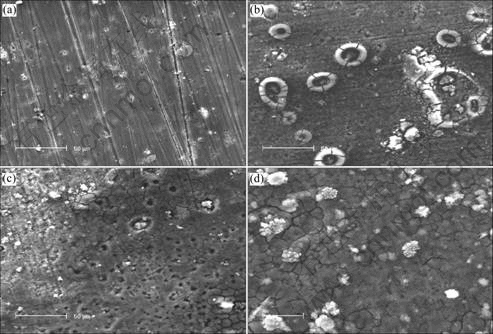
Fig.4 SEM images of samples exposed to 0.02 mol/L NaHSO3+0.006 mol/L NaCl for different test time: (a) 48 h; (b) 96 h; (c) 192 h; (d) 240 h
XPS analysis on surface of samples exposed to 0.02 mol/L NaHSO3+0.006 mol/L for 240 h is shown in Fig.5. It can be seen that, the intension peaks of aluminum and sulfur element appear at 74.7 eV and 169.2 eV respectively; the weak peaks of copper element appear at 953.9eV and 933.7eV, respectively; no chlorine element peak is found, which shows that sulphate aluminum is main corrosion product on surface of sample exposed to 0.02 mol/L NaHSO3+0.006 mol/L for 240 h.
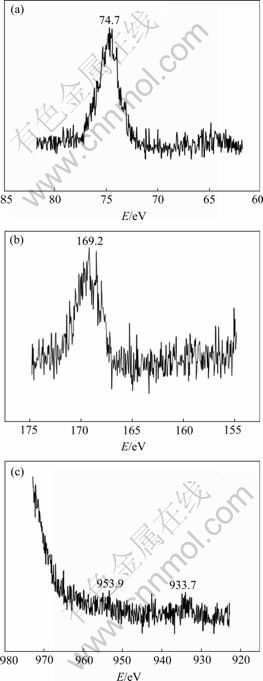
Fig.5 XPS spectra collected from samples exposed to 0.02 mol/L NaHSO3+0.006 mol/L NaCl for 240 h: (a) Al 2p; (b) S 2p; (c) Cu 2p3/2
SEM images of surface of sample exposed to 0.006 mol/L NaCl for 96 h and 192 h are shown in Fig.6. The result shows that the corrosion is not serious, and pitting corrosion is still main feature. Some small corrosion pits on surface of sample appear after 96 h (Fig.6(a)), and the number of corrosion pits increases slowly with the increase of test time.
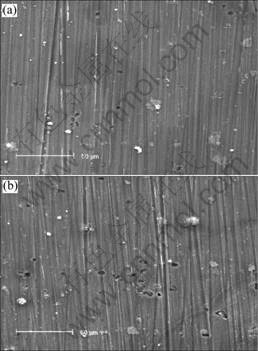
Fig.6 SEM images of samples exposed to 0.006 mol/L NaCl for different test time: (a) 96 h; (b) 192 h
Remarkable difference on the corrosion process of LY12 samples exposed to three kinds of environments mentioned above can be observed, while main common character is pitting corrosion. In the environment of 0.02 mol/L NaHSO3+0.006 mol/L NaCl, pitting corrosion starts strongly in early test period, and the number and the size do not increase quickly with the increase of test time until a layer of corrosion product of sulphate aluminum forms on the whole surface of the samples. Cl- can produce effectively pitting fountain while
exists, resulting in oxide film wrecking and accelerating corrosion.
3.3 Electrochemical behavior of aluminum alloy LY12 without cladding
3.3.1 Polarization curve
The polarization curves of the electrochemical samples exposed to 0.02 mol/L NaHSO3 for 144, 192 and 240 h are given in Fig.7. As for the uncorroded samples, its anode Tafel slop is relatively high, so the whole corrosion process is controlled by anode polarization. As for the samples corroded for different time in accelerated corrosion test, the trend that their anode Tafel slops decrease with the increase of accelerated corrosion time can be observed, so the whole corrosion process is controlled by cathode polarization gradually instead of anode polarization. The resistance for Al3+ reaching to the interface of oxide film and solution decreases as acidic media are propitious for oxide film dissolving. The concentration of H+ is limited by the concentration of
Cathode process is mainly hydrogenous deoxidizing reaction. The trend of corrosion potential moving positively is evident. Corrosion current is high in early test period, and decreases with the increase of time and reaches the smallest value at 144 h. The fact indicates that the corrosion products on the sample suppress anodic reaction.
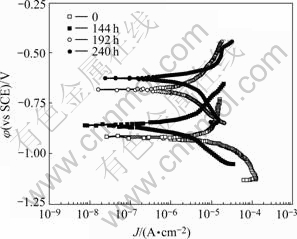
Fig.7 Polarization curves of samples exposed to 0.02 mol/L NaHSO3
The polarization curves of the samples exposed to 0.02 mol/L NaHSO3 +0.006 mol/L NaCl for 48, 96, 192 and 240 h are shown in Fig.8. For the samples tested for 96 h, its anode Tafel slop is relatively big. The whole corrosion process is controlled by anode polarization, the conversion point of passivation and activation appears because of happening of pitting corrosion on the surface. Anode Tafel slops of the polarization curves decrease and cathode Tafel slops increase with the increase of time of accelerated corrosion test. It is thought that controlling steps of electrode reaction change from anode polarization to both cathode and anode polarization or cathode polarization, only cathode polarization in the last period of accelerated corrosion test. The corrosion current is larger in early period and does not change largely.
There are
,
and Cl- in the mixed media for accelerated corrosion test. When comparing Fig.8 with Fig.7, it can be seen that the behavior of anode process alters evidently because of Cl- existing. Cl- can adsorb on the surface of oxide film, especially local site with defection, and then results in dissolution of oxide film in acidic media. The sulphate aluminum film forms on surface of sample exposed to 0.02 mol/L NaHSO3+ 0.006 mol/L NaCl under the action of H+,
and Cl- together, which makes polarization passivate. The oxide film and the sulphate aluminum film also dissolve gradually. Cathode process becomes the controlling step in the whole electrode reaction.
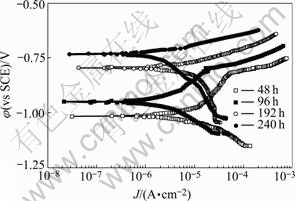
Fig.8 Polarization curves of samples exposed to 0.02 mol/L NaHSO3+0.006 mol/L NaCl
The polarization curves of the samples exposed to 0.006 mol/L NaCl for 48, 96, 144 and 240 h are shown in Fig.9. The results show that the corrosion potentials of the samples do not change and corrosion currents decrease with the increase of time of accelerated corrosion test. The cathode pervasion process, that is oxygen pervasion, is the controlling step in the whole process of corrosion test. It is hard to find the status of oxygen pervasion in real atmospheric corrosion due to thin liquid film. The corrosion of samples exposed to 0.006 mol/L NaCl is not serious because low Cl- concentration can not produce pitting origin enough. From comparison between mixed media and single medium, it can be obtained that corrosion current of former is higher than that of latter, the influence of Cl-concentration in test is quite small, and
plays a main role in accelerated corrosion. The law of corrosion current variation is consistent to that of mass loss changing.
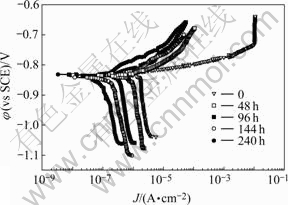
Fig.9 Polarization curves of samples exposed to 0.006 mol/L NaCl
3.3.2 Electrochemical impedance spectroscopy (EIS)
The relative information on corrosion mechanism of aluminum LY12 alloy can be obtained from the characters of EIS of the tested electrodes in media, the corrosion of aluminum alloy is related to the quality of its oxidation film, and EIS of aluminum alloy electrode in electrolyte can reflect the quality and changing process of oxidation film[16-17].
It can be seen from Fig.10 that EIS of the electrodes tested in 0.02 mol/L NaHSO3 medium consists of both parts of inductive arc at low frequency and capacitive arc at high frequency. It is known that capacitive arc at high frequency is related with the state of surface film of electrodes, which is corresponded to SEM results. Inductive arc at low frequency results mainly from pitting corrosion, wrecking and shaping of part film.
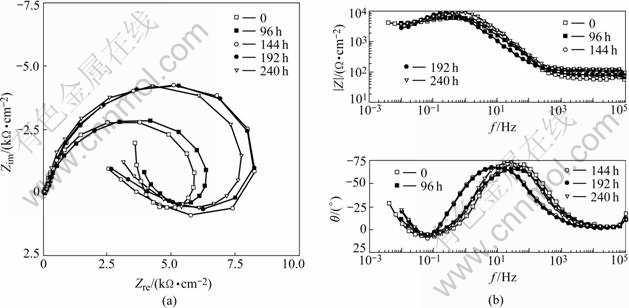
Fig.10 EIS of samples exposed to 0.02 mol/LNaHSO3: (a) Nyquist; (b) Bode
EIS of the electrodes tested in 0.006 mol/L NaCl only appears in capacitive arc character as shown in Fig.11. There is inductive arc at low frequency in early test period, which shows that the film on surface of sample does not experience the process of pitting corrosion, destroying its integrality. Formation and dissolution of oxidation film arrives a dynamic balance in distilled water, which decides the thickness of oxidation film.
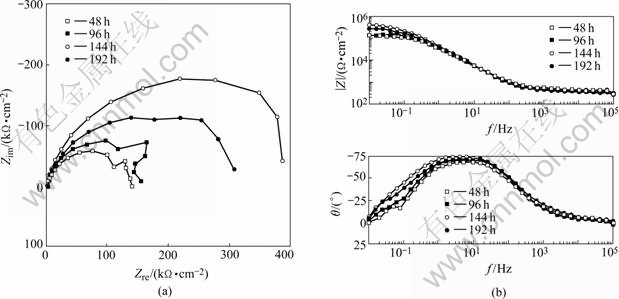
Fig.11 EIS of samples exposed to 0.006 mol/L NaCl for different test time: (a) Nyquist; (b) Bode
2Al+3H2O→Al2O3+6H++6e-
Al2O3+6H+→2Al3++3H2O
Cl- existing in solution plays a role in accelerating dissolution, resulting in breaking and pitting of oxidation film. Dissolution rate of oxidation film in 0-0.15 mol/L NaCl increases as the concentration of Cl- increases, which can be explained by adsorption balance of Cl- on interface of oxidation film and solution and by reaction model of forming AlClx net substance escaping from surface[11].
In the character of the electrodes exposed to 0.02 mol/L NaHSO3+0.006 mol/L NaCl, weak inductive arc at low frequency and strong capacitive arc at high frequency, can be seen in Fig.12, which is different from that exposed to 0.02 mol/L NaHSO3 or 0.006 mol/L NaCl. Results show that the corrosion mechanism of aluminum alloy LY12 in mixed media is different from that in single medium. The impedance of electrodes corroded for 48 h decreases obviously and capacitive arc appears. There is two capacitive arcs in the EIS. New capacitive arc in Fig.12(b) is in left of old capacitive arc. EIS of the electrodes corroded for 96 h has a main character of new capacitive arc, and old capacitive arc becomes unobvious. The impedance of electrodes uncorroded is the biggest.
The capacitive arc of EIS mainly represents the performance of oxidation film on the surface of untested electrodes with good integrality and quality. Oxidation films in mixed media reduce quickly due to the cooperating action of H+ and Cl-, resulting in baring metal in local region and accelerating corrosion. Meanwhile, new oxidation film is formed by H2O reacting with LY12 metal, which is loose, not as well as old oxidation film. New capacitive arc of the electrodes tested for 48 h appears because of new oxidation film forming on the surface. The oxidation film on the surface of the electrodes formed in air is destroyed when the electrodes is tested for 96 h.
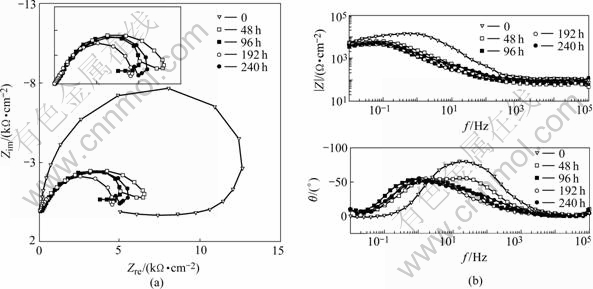
Fig.12 EIS of samples exposed to 0.02 mol/L NaHSO3+0.006 mol/L NaCl for different test time: (a) Nyquist; (b) Bode
4 Conclusions
1) The relationship between test time and average mass losses of aluminum alloy LY12 samples with cladding and without cladding, exposed to three kinds of simulated atmosphere environments containing respectively 0.02 mol/L NaHSO3, 0.02 mol/L NaHSO3+ 0.006 mol/L NaCl, 0.006 mol/L NaCl, can be described by the linear equation m=C+Vt.
2) There is quite difference in the corrosion on surface of sample without cladding, exposed to three kinds of simulated atmosphere containing 0.02 mol/L NaHSO3, 0.02 mol/L NaHSO3+0.006 mol/L NaCl, 0.006 mol/L NaCl. Pitting corrosion is their common character. Sulphate aluminum forms on the surface of sample exposed to 0.02 mol/L NaHSO3. The selective dissolution of LY12 results in copper enrichment on the surface. The large number of corrosion pits on surface of sample exposed to 0.02 mol/L NaHSO3+0.006 mol/L NaCl in earlier period appear, and a layer of corrosion product, sulphate aluminum, corrosion pits, is formed gradually and cracks because of dehydration.
3) The electrochemical behaviors of aluminum alloy LY12 without cladding in above three media are different. It is also different in different period in a same medium. The corrosion current in 0.02 mol/L NaHSO3+0.006 mol/L NaCl is bigger than that in 0.02 mol/L NaHSO3 or 0.006 mol/L NaCl; corrosion controlling step has a conversion from anode to cathode in accelerated corrosion process, and new time constant of EIS appears because of new oxidation film forming.
4) 0.02 mol/L NaHSO3 and 0.006 mol/L NaCl have a cooperating action to aluminum alloy LY12 in accelerated corrosion process. The corrosion behavior and mechanism of aluminum alloy LY12 in mixed media is different from that in single medium. Cl- can produce effectively pitting fountain while
exists, resulting in oxidation film wrecking and accelerating corrosion.
References
[1] LEYGRAF C, GRAEDEL T. Atmospheric Corrosion [M]. New York: John Wiley and Sons, 2000.
[2] SOWINSKI G, SPROWLS D O. Weathering of Aluminum and Its Alloys[A]. Ailor W H. Atmospheric Corrosion [M]. New York: John Wiley and Sons, 1982: 297-328.
[3] LASHERMES M, GULHAUDIS A, REBOUL M, TRENTELIVRES G. Thirty-Year Atmospheric Corrosion of Aluminum Alloys in France[A]. Ailor W H. Atmospheric Corrosion [M]. New York: John Wiley and Sons, 1982: 353-364.
[4] GATTO F, PERRONE A. Atmospheric Corrosion of Aluminum in Italy[A]. Ailor W H. Atmospheric Corrosion [M]. New York: John Wiley and Sons, 1982: 827-840.
[5] CAO C N. Material Natural Environmental Corrosion of China [M]: Beijing: Chemical Industry Press, 2005. (in Chinese)
[6] MENDOZA A R, CORVO F. Outdoor and indoor atmospheric corrosion of non-ferrous metals [J]. Corrosion Science, 2000, 42(7): 1123-1147.
[7] BLUCHER D B, LINDSTROM R, SVENSSON J E, JOHANSSON L G. The effect of CO2 on the NaCl-induced atmospheric corrosion of aluminum [J]. Journal of the Electrochemical Society, 2001, 148(4): B127-131.
[8] OESCH S, FALLER M. Environmental effects on materials: The effect of the air pollutants SO2, NO2, NO and O3 on the corrosion of copper, zinc and aluminium, a short literature survey and results of laboratory exposures [J]. Corrosion Science, 1997, 39(9): 1505-1530.
[9] GUILLAUMIN V, SCHMUTZ P, FRANKEL G S. Characterization of corrosion interfaces by the scanning Kelvin probe force microscopy technique [J]. Journal of the Electrochemical Society, 2001, 148(5): B163-173.
[10] RAMGOPAL T, GOUMA P I, FRANKEL G S. Role of grain-boundary precipitates and solute-depleted zone on the intergranular corrosion of aluminum alloy 7150 [J]. Corrosion, 2002, 58(8): 687-698.
[11] BOXLEY C J, WATKINS J J, WHITE H S. Al2O3 film dissolution in aqueous chloride solutions [J]. Electrochemical and Solid State Letters, 2003, 6(10): B38-B41.
[12] WOOD W G. Aluminum, Cleaning and Finishing, Metal Handbook [M]. (v 5). 9.Metals Part: American Society for Metals, 1982: 582-585.
[13] FERRER K S, KELLY R G. Comparison of methods of removal of corrosion products from AA20424-T3 [J]. Corrosion, 2001, 57(2): 110-117.
[14] KOLICS A, POLKINGHORNE J C, WIECKOWSKI A. Adsorption of sulfate and chloride ions on aluminum [J]. Electrochimica Acta, 1998, 43(18): 2605-2618.
[15] XIE G Y, LIU Z Y, ZHU Z P. Reductive regeneration of sulfated CuO/Al2O3 catalyst-sorbent in ammonia [J]. Applied Catalysis B—Environmental, 2003, 45(3): 213-221.
[16] AN B G, ZHANG X Y, SONG S, LI H X, HAN E H. A study of electrochemical impedance spectrum for corrosion behavior of LY12 aluminum alloy in simulated acid rain [J]. Journal of Chinese Society for Corrosion and Protection, 2003, 167-170.
[17] CARBONINI P, MONETTA T, MITTON D B, BELLUCCI F. Degradation behaviour of 6013-T6, 2024-T3 alloys and pure aluminium in different aqueous media [J]. Journal of Applied Electrochemistry, 1997, 27(10): 1135-1142.
Foundation item: Project(50499331) supported by the National Natural Science Foundation of China
Corresponding author: WANG Zhen-yao; Tel: +86-24-23893544; E-mail: zhywang@imr.ac.cn
(Edited by YANG Hua)