
Effect of TiH2 on preparation of closed-cell aluminum foam and its compressive behavior
YANG Guo-jun(杨国俊), YU Hai-jun(尉海军), YAO Guang-chun(姚广春)
School of Materials and Metallurgy, Northeastern University, Shenyang 110004, China
Received 28 July 2006; accepted 15 September 2006
Abstract: The vesicant problem during the process of preparing closed-cell aluminum foam by molten body transitional foaming process was discussed and the effect of granularity and addition of TiH2 on porosity of closed-cell aluminum foam was investigated. The static compressive behavior of closed-cell aluminum foam and the influence of porosity on static compressive property of closed-cell aluminum foam were researched as well. The results show that with increasing granularity of TiH2, the porosity of closed-cell aluminum foam firstly increases and then decreases gradually, the granularity should be controlled in the range of 38-74 μm which can result in higher porosity. The porosity of closed-cell aluminum foam increases with the increasing addition of TiH2, and the addition of TiH2 should be controlled from 1.5% to 2.5% which can result in homogeneous cell and moderate strength of closed-cell aluminum foam. The compressive process of closed-cell aluminum foam obviously displays linear elastic phase, plastic collapse phase, and densification phase, and the compressive strength grows with decreasing porosity.
Key words: TiH2; closed-cell aluminum foam; granularity; porosity; mechanical behavior
1 Introduction
In 1940s, SOSNICK[1] researched on the aluminum foam and reported the first patent on aluminum foam. Owing to the difficulty to control the foaming techniques and specimen size, aluminum foam can not be developed and applied immediately. Early in 1980s, many people in the world began to develop aluminum foam material again, and found that it had properties of light mass, thermal insulation, sound absorption, sound insulation, energy absorption, anticorrosion and electromagnetic shielding[2-5], so it could be applied in metallurgy, construction, mechanism, transportation, electron, and communication and it attracted much attention from researchers internationally[6-9].
Aluminum foam can be divided into open-cell aluminum foam and closed-cell aluminum foam, which can be prepared by seepage method and molten body foaming method respectively. Aluminum foam produced by seepage method is uniform in cell size, but the size and porosity are not large and high owing to the influence of mold. Because of the simple production process, adjustable product size and easy industrialization, molten body foaming method attracts more attention the world over. Though there are some reports on choosing vesicant[10-11], the researches are not systemic. The authors produced closed-cell aluminum foams by molten body foaming method and researched the effects of granularity and addition of TiH2 on porosity of closed-cell aluminum foam[12]. The static compressive property of closed-cell aluminum foam with different porosity was also researched.
2 Experimental
2.1 Effect of amount and granularity of TiH2
The process of preparing closed-cell aluminum foam has four steps: 1) Adding 3% metal Ca to increase the viscosity of the melt at 850 ℃; 2) Adding TiH2 to the melt at 680 ℃, and stirring rate 2 000 r/min; 3) Transferring the melt to the bubbly case and keeping the melt in maintaining furnace for 6 min; 4) Post process. Added 0.5%, 1.0%, 1.5%, 2.0%, 2.5%, 3.0% of TiH2 to prepare closed-cell aluminum foam assuring other conditions being equal.
Screed TiH2 according to the granularity and prepare closed-cell aluminum foam with different granularity of TiH2. The adding amount of TiH2 is 1.5%, and the granularities of TiH2 are <38 μm, 38-47 μm, 47-61 μm, 61-74 μm, 74-112 μm, 112-147 μm respectively.
2.2 Compressive property of closed-cell aluminum foam
Select four groups of closed-cell aluminum foam with different porosity from the experiment above, and machine them into samples (diameter 30 mm, height 30 mm). The equipment utilized in this compressive testing is CMT4000 automatic compressive machine, and the compressive rate is 2.5 mm/min. Each test stops when the sample is compressed solid.
3 Results and discussion
3.1 Effect of amount and granularity of TiH2
Fig.1 shows the relationship between the content of TiH2 and the porosity of closed-cell aluminum foam, which shows that the porosity of closed-cell aluminum foam increases with the increasing amount of TiH2. The density of the closed-cell aluminum foam becomes smaller, but the increasing trend becomes tempered. This is caused by the fact that with increasing amount of TiH2, the aluminum releases more hydrogen, so the cell size becomes larger, and the cell wall thinner, consequently the porosity increases, at the same time, as more hydrogen is released, combination of cell and perforation become easier, most hydrogen goes out of cell to the environment, thus the increasing trend of porosity resulted by addition of TiH2 becomes tempered.
Fig.2 shows the macro-photograph of closed-cell aluminum foam with different amounts of TiH2. As can be seen from Fig.2, when the amount of TiH2 is 0.5%, after the foam is cut, the cells are small and not uniform. When the amount of TiH2 is 1.5%, the cells are uniform and round, the wall thickness of cell is moderate. When the amount reaches 2.5%, the cells become large and the wall thickness of cell is small. When the amount is 3%, the cells continue to grow large, the wall thickness is the smallest among the four and some cells break and crack, and some are in series. So Fig. 2 can well indicate the above explanation of the increasing porosity with the amount of TiH2 added.
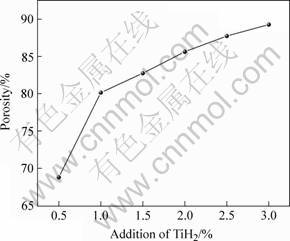
Fig.1 Relation between porosity of closed-cell aluminum foam and amount of TiH2
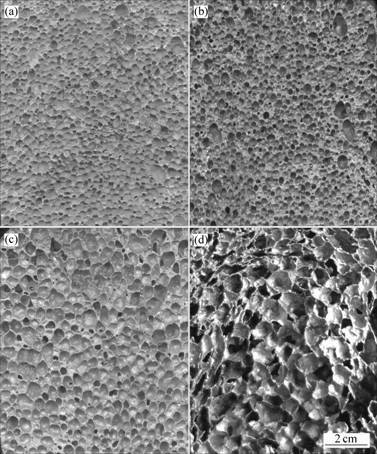
Fig.2 Closed-cell aluminum foam with different contents of TiH2: (a) 0.5%; (b) 1.5%; (c) 2.5%; (d) 3.0%
Therefore, taking practice and economy into consideration, the adding amount of TiH2 should be controlled between 1.5% and 2.5%, if the uniform cell structure and moderate strength are desired. Unless the desired closed-cell aluminum foam is small in density and low in strength, then the addition of TiH2 can be larger than 3%. If high density closed-cell aluminum foam is needed, the addition of TiH2 can be less than 1.0%.
Fig.3 shows the curve of the relationship between granularity of TiH2 and the porosity of closed-cell aluminum foam, which shows that the porosity firstly increases then decreases with the addition of granularity of TiH2. The reason is that TiH2 with larger granularity does not decompose fully within the same period of time, releasing less hydrogen. When the diameter of TiH2 is less than 38 μm, it is likely to float on the surface of the melt rather than to interfuse with the melt, and as the surface area is large, decomposing rate is high. So within the same period of time, they decomposing more fully, and as a result the porosity becomes smaller. So the granularity of TiH2 should be within a certain range, in this test, from 38 to 74 μm.
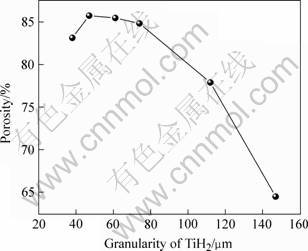
Fig.3 Relation between granularity of TiH2 and porosity of closed-cell aluminum foam
3.2 Compressive property of closed-cell aluminum foam
Fig.4 shows the compressive curve of closed-cell aluminum foam. The figure shows that the compression of closed-cell aluminum foam can be divided into 3 stages: linear elastic stage, plastic collapse stage and densification stage[13]. Linear elastic stage is within a small strain range, usually ε<0.025. Within this range, the stress—strain curve is a linear line, the slope of which is the apparent elastic modules. The largest stress that the top of the line corresponds is the compressive strength. When strain grows to a certain point, the compressive stress—strain of closed-cell aluminum foam enters plastic collapse stage which is characterized by the fact when the strain is small, the stress drops dramatically. After all the cell walls collapse, the walls contact with each other so further strain is provided by matrix of the material, as a consequence compressive stress increases markedly with growing strain. It is shown in the densification stage in Fig.4.
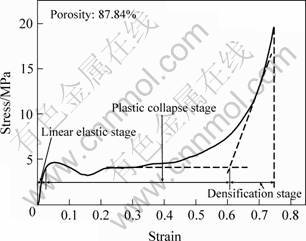
Fig.4 Quasi-static compressive curve of closed-cell aluminum foam
Fig.5 shows the relationship between the porosity and compressive strength of the closed-cell aluminum foam. The figure indicates that with the increase of porosity, the compressive strength gradually drops, from 18.96 MPa to 3.8 MPa. This is because the bigger the porosity, the smaller the relative density, so the capability to bear external force is also smaller, consequently the compressive strength decreases.
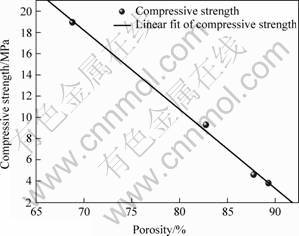
Fig.5 Relationship between the porosity and compressive strength of closed-cell aluminum foam
4 Conclusions
1) The amount and the granularity of the vesicant greatly affect the porosity of closed-cell aluminum foam. The experiment shows that if closed-cell aluminum foam with uniform cells and large porosity is desired, taking economy and property into consideration, the amount of TiH2 should be controlled from 1.5% to 2.5%, granularity from 38 to 74 μm.
2) The compression of closed-cell aluminum foam can be divided into three stages: linear elastic stage, plastic collapse stage and densification stage. Porosity influences the compressive strength obviously, with the increase of porosity, the compressive strength drops.
References
[1] SOSNICK B. Process for Making Foamlike Mass of Metal [P]. US Patent 2434775, 1948.
[2] BAZLE A G, TRAVIS A B, BRUCE K F, CHIN J Y, CLAAR T D, HARALD H E, JOHN W G. Aluminum foam integral armor: a new dimension in armor design [J]. Compos Struct, 2001, 52: 381-395.
[3] BHATTACHARYA A, CALMIDI V V, MAHAJAN R L. Thermophysical properties of high porosity metal foams [J]. Int J Heat Mass Transfer, 2002, 45: 1017-1031.
[4] ANDREWS E W, HUANG J S, GIBSON L J. Creep behavior of a closed-cell aluminum foam [J]. Acta Mater, 1999, 47(10): 2927-2935.
[5] SANDS M, SHIVKUMAR S. EPS molecular weight and foam density effects in the lost foam process [J]. J Mater Sci, 2000, 38: 2233-2239.
[6] CSILLA K, FRANTISEK C, ZSUZSANNA R. Acoustic emission measurements on metal foams [J]. J Alloy Compd, 2004, 378: 145-150.
[7] LU T J, ONG J M. Characterization of close-celled cellular aluminum alloys [J]. J Mater Sci, 2001, 36: 2773-2786.
[8] PLACIDO E, ARDUINI-SCHUSTER M, KUBN J. Thermal properties predictive model for insulating foams [J]. Infrared Phys Techn, 2005, 46: 219-231.
[9] WEN C E, MABUCHI M, YAMADA Y. Processing of fine-grained aluminum foam by spark plasma sintering [J]. J Mater Sci Lett, 2003, 22: 1407-1409.
[10] YAN Fu-xue, ZHAO Kang, GU Chen-qin. Fabrication of Foamed Aluminum by a New Vesicant-Mixed Rare Earths Hydride [J]. Journal of the Chinese Rare Earth Society, 2005, 23(2): 186-190. (in Chinese)
[11] LIU Bing, CHEN Feng. Effect of TiH2 addition on pore structures of aluminum foam prepared by power metallurgy route [J]. Journal of Southeast University (Natural Science Edition), 2005, 35(2): 257-261. (in Chinese)
[12] YAO Guang-chun, ZHANG Xiao-ming, SUN Ting. The Method of Preparing Closed-cell Foam Aluminum by Direct Foaming in Melt [P]. CN Patent 1320710, 2001. (in Chinese)
[13] ANDREWS E, SANDERS W, GIBSON L J. Compressive and tensile behaviour of aluminum foams [J]. Mater Sci Eng A, 1999, 270: 113-124.
(Edited by LONG Huai-zhong)
Foundation item: Project (2002AA334060) supported by the Hi-tech Research and Development Program of China
Corresponding author: YU Hai-jun; Tel: +86-24-83686462; E-mail: yuhaijunneu@163.com