
Densification simulation of compacted Al powders using multi-particle finite element method
Kyung-Hun LEE, Jung-Min LEE, Byung-Min KIM
School of Mechanical Engineering, Pusan National University, Pusan, Korea
Received 2 March 2009; accepted 30 May 2009
Abstract: The powder compaction simulations were performed to demonstrate deformation behavior of particles and estimate the effect of different punch speeds and particle diameters on the relative density of powder by a multi-particle finite element model(MPFEM). Individual particle discretized with a finite element mesh allows for a full description of the contact mechanics. In order to verify the reliability of compaction simulation by MPFEM, the compaction tests of porous aluminum with average particle size of 20 μm and 3 μm were performed at different ram speeds of 5, 15, 30 and 60 mm/min by MTS servo-hydraulic tester. The results show that the slow ram speed is of great advantage for powder densification in low compaction force due to sufficient particle rearrangement and compaction force increases with decrease in average particle size of aluminum.
Key words: cold compaction; Al powder; particle size; multi-particle finite element model
1 Introduction
Conventional powder metallurgy is generally composed of compaction, where powders are compressed into desired shape at room temperature, and sintering, where compacted powder is consolidated to full density by the bonding between particles at high temperature. During sintering many residual pores in compacted powders lead to the shrinkage, warpage and inhomogeneous density distribution of the final powder products, followed by a low mechanical strength. Thus, to obtain the high quality of powder products, it is required to minimize the residual pores and to make the density distribution of powder compacts uniform[1-2].
Many experimental and theoretical studies based on continuum mechanics have been carried out to probe the densification behavior of powder compacts. But these continuum mechanics are difficult to investigate the individual particle behavior, interaction between particles and the effect of different particle diameter. To improve the observation of the physical phenomena during compaction at the particle level, the discrete element method(DEM) was used by CUNDALL and STRACK [3], and CAMBOU[4], where particle was regarded as a rigid body. Recently, particle which is mapped by a finite element mesh was a deformable body including mechanical properties[5]. However, rotational stiffness of particle and interaction between the contact points were occasionally ignored in typical DEM[6-7]. Moreover, DEM was limited to powder compacts with low relative densities[8].
Multi-particle finite element model(MPFEM) with full finite element discretization of the particles was developed by PROCOPIO and ZAVALIANGOS[9] for alternative DEM. They researched a multi-particle compaction problem with different shapes of particle and mechanical properties. The finite element discretization of individual particle in MPFEM gives discrete behavior of particle assembly for compaction of powder with high relative densities, including their large contact deformation.
In the present work, the effects of different punch speeds and average particle sizes on deformation behavior and densification of Al particles were investigated during compaction by MPFEM. Analytical results were inspected by compaction tests of aluminum powder with average particle sizes of 20 and 3 μm.
2 Conditions of finite element analysis and experiment
2.1 Conditions of MPFEM analysis
Fig.1(a) shows the representative finite element mesh of particle used in MPFEM and analysis model for aluminum powder compaction with particle diameter of 1.0 and 0.5 mm. Analysis was performed on the plain strain condition for its convenience. The ratio of the total particle area(Atp) to the container area (Ac=85 mm2) is 0.508 for particle diameter of 1.0 mm and 0.510 for particle diameter of 0.5 mm to give the periodic arrangement of particles for each particle size, as shown in Fig.1(b). Therefore, the number of particle is 56 for 1.0 mm and 221 for 0.5 mm, and the regular interval between particles is 0.2 mm for 1.0 mm and 0.1 mm for 0.5 mm, respectively.

Fig.1 FE Models of compaction processes for two particle sizes using MPFEM: (a) Initial mesh of particle; (b) Particle arrangements and FE models
The dimension of container was 5 mm in diameter and 17 mm in height. The friction coefficient between particles or between particle and container wall is 0.192 in all cases. The material used in the MPFEM was Al 1100 and the mechanical properties are shown in Table 1. The compaction simulations by MPFEM were performed for different punch speeds of 5, 15, 30 and 60 mm/min and two particle diameters using ABAQUS 6.3 Explicit which is commercial finite element program. Single action pressing method was used in the compaction simulation.
Table 1 Mechanical properties of Al 1100
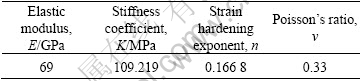
2.2 Conditions of experiment
Fig.2 shows the configurations of compaction die (AISI D2) used in the compaction test where the powder material is Al 1100. The mass of each powder compact was 0.45 g and cylindrical powder compacts were fabricated to height of 10 mm and diameter of 5.0 mm. Compaction tests were performed by universal testing machine(MTS) with punch speeds of 5, 15, 30 and 60 mm/min, like FE-simulations. Fig.3 shows SEM images of aluminum powder with average particle size of 20 and 3 μm used in this study. After compaction test, the relative density of porous samples was measured using the Archimedes method. Also, SEM observation for each compact was carried out to observe the particle deformation and behavior with different punch speed and average particle size.
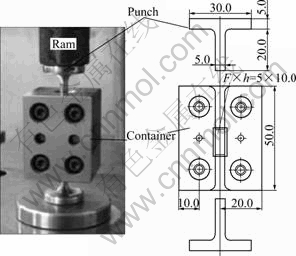
Fig.2 Configuration and dimensions of tool for compaction tests of Al 1100 powders (Unit: mm)
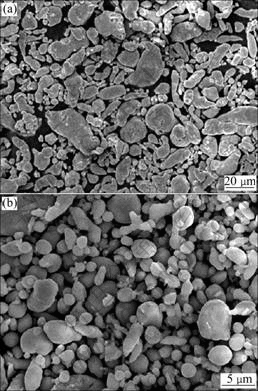
Fig.3 SEM images of Al 1100 powders with average particle size of 20 μm (a) and 3 μm (b)
3 Results of finite element analysis and experiment
3.1 Results of MPFEM analysis
Fig.4 shows the compaction load—punch stroke curves of aluminum powder with diameter of 1 mm for different punch speeds. As punch speed increased, com- compaction load increased for the same punch stroke, and punch stroke decreased for the same compaction load. The maximum load was defined at position with infinite slope of load—stroke curve and this occurred regularly regardless of punch speed. These patterns were similar to those with particle diameter of 0.5 mm.
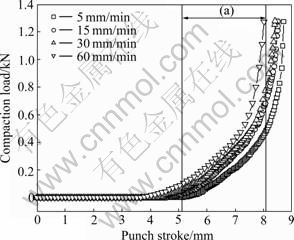
Fig.4 Compaction load—stroke curves of powders with particle diameter of 1 mm for different punch speeds
Friction force between particles by particle rearrangement and plastic deformation of particles was involved in load—stroke curve. The increase of load was dependant on local plastic deformation of particle or friction forces by elastic deformation at initial stoke, and the slope of load—stroke curve increased slowly. After that, slope of load—stroke curve increased dramatically in region with only plastic deformation and without particle sliding and rotation. Friction force between particles and plastic deformation could be presented together for punch speed of 5 mm/min in Fig.4(a).
Fig.5 shows the behavior and effective stress distribution of powders at punch speed of 5 and 60 mm/min with punch strokes in Fig.4(a). As the punch stroke increased, powders were densified by particle rearrangement (elastic deformation or local plastic deformation) and plastic deformation at a punch speed of 5 mm/min. On the contrary, at punch speed of 60 mm/min, particle rearrangement was little, and plastic deformation of particles occurred at the lower punch stroke as compacted with that at punch speed of 5 mm/min. Consequently, higher punch speed gave a shorter period of particle rearrangement due to restrictive particle movements.
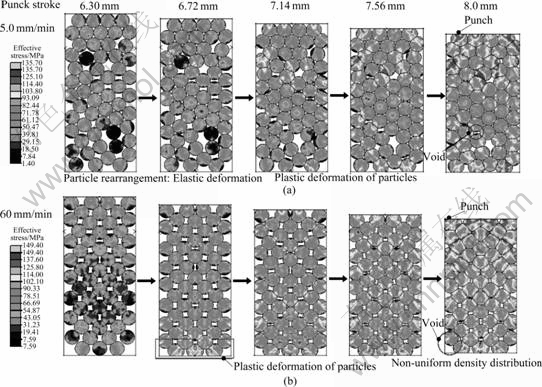
Fig.5 Behavior and effective stress distributions of powders at punch speeds of 5 mm/min (a) and 60 mm/min (b)
In general, particles of neighboring punch had high plastic deformation and effective stress distribution. Pores existed between particles at punch speed of 5 mm/min; on the other hand, pores distributed over a bottom of container at 60 mm/min. In this study, because particles are incompressible, all the powders have the same relative density at same punch stroke. Therefore, punch speed of 5 mm/min gave more uniform distributions for relative density of powders than 60 mm/min.
Fig.6 shows the effective strain and stress distributions of powders for different punch speeds at a compaction load of about 1.2 kN. As the punch speed increased, maximum equivalent stress and strain increased. Strain chains were connected to bottom of container in a crow line paralleled to a transfer direction of punch, especially contours of equivalent strain for punch speed of 60 mm/min. On the other hand, these at punch speed of 30 mm/min had obvious lozenge patterns which linked up container wall with central parts of the powder compacts in direction of 45?. These patterns trend to be slightly reduced at 15 and 5 mm/min.
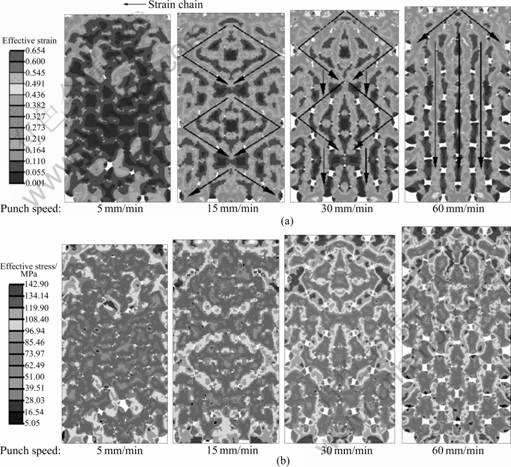
Fig.6 Effective strain and stress distributions of powders for different punch speeds at compaction load of about 1.2 kN: (a) Effective strain; (b) Effective stress
Such the strain chain means the transfer direction of compaction load between particles. Because compaction load was perpendicularly transferred to particles arranged in bottom of container at 60 mm/min, particles were restricted at short punch stroke. However, densification mode at punch speed of 30 and 15 mm/min had lozenge patterns owing to enough particle movement and rearrangement caused by slow transfer velocity of load. Consequently, as the punch speed decreased for the same ratio of Atp to Ac, relative density of powder compacts increased and density distributions were more homogeneous by transfer direction (velocity) of compaction load and particle flow behavior.
Fig.7 shows compaction load—punch stroke curves of powders with particle diameter of 1.0 and 0.5 mm at punch speed of 5 mm/min. For particle diameter of 0.5 mm the maximum compaction load was about twice as much as that for particle diameter of 1.0 mm and a slope of its load—stroke curve dramatically increased at stroke of approximately 8.0 mm. Fig.8 shows behaviors and effective stress distributions of powder with particle diameter of 0.5 mm. Due to small particle, densification of particle mainly occurred by particle rearrangement. After rearrangement, as friction area was increased by higher specific particle area, compaction loads dramatically increased. As results of small particle diameter, a long period of particle rearrangement provided a short section (Fig.7(a)), where friction force and plastic deformation coexisted. The whole value of effective stress distribution compared with particle diameter of 1.0 mm (Fig.5) is smaller, too. Patters of strain chain and stress distribution are similar.
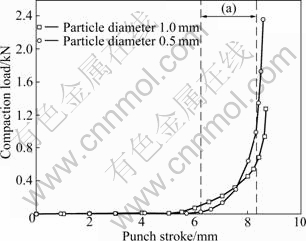
Fig.7 Compaction load—stroke curves of powders with particle diameter of 1.0 mm and 0.5 mm at punch speed of 5 mm/min
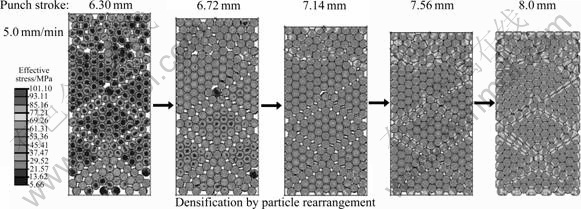
Fig.8 Behaviors and effective stress distributions of powder with particle diameter of 0.5 mm
3.2 Results of powder compaction test
Fig.9 shows compaction load—punch stroke curves of Al 1100 powders with average particle size of 20 μm for different punch speeds obtained from compaction tests. The whole patterns of compaction load—punch stroke curves are equal to analysis results. As mentioned above, these patterns were caused by improvement of particle rearrangement at lower punch speed. Same results were shown in powder compaction test with average particle size of 3 μm. However, compaction tests were performed by double action pressing which is different from finite element analysis. In this test, powder densification occurred early about twice as much as single action pressing in finite element analysis. Therefore, load for compaction test increased slightly from initial punch stroke.
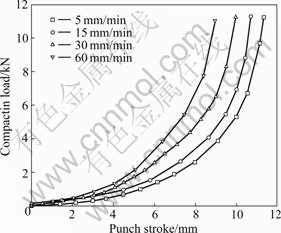
Fig.9 Load—stroke curves of Al 1100 powders with particle diameter of 20 μm for different punch speeds obtained from compaction tests
Fig.10 shows load—stroke curves of Al 1100 powders with average particle size of 20 and 3 μm for punch speed of 5 mm/min obtained from compaction force. The whole experimental results were similar to analysis results in respect of different average particle size. Due to different initial height of powder compacts for same mass, the punch stoke at average particle size of 3 μm was longer than that of 20 μm in experiment results which is different from analysis results. In the case of lower particle size, because the whole specific particle area and surface activities increase, bonding force between particles grow up. This phenomenon was responsible for decreasing the fluidity between particles and then compaction load increased.
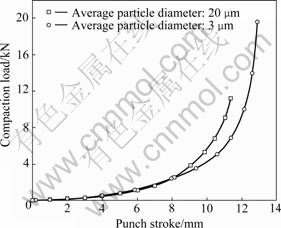
Fig.10 Load—stroke curves of Al 1100 powders with particle diameter of 20 and 3 μm at punch speed of 5 mm/min obtained from compaction tests
Fig.11 shows relative density of each powder obtained from compaction simulation and tests. Relative density was calculated by the ratio of the total particle area to container area at the maximum compaction load from finite element analysis. As the average particle size increased and compaction speed decreased, relative density increased. As mentioned above, these patterns are due to active densification of powder by particle rearrangement.
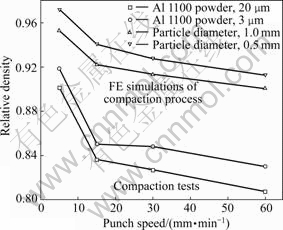
Fig.11 Relative density of each powder obtained from compaction simulations and tests
As shown in Fig.10, small particle size provided a high friction between particles. Particle rearrangement and fluidity were dependent on friction between particles. However, an increase of friction between particles did not always mean to diminution of rearrangement or fluidity, and mentioned that particle rearrangements had need of comparatively high compaction load. In the case of nano particle, extremely large specific surface area may provide full restriction of particle movement by only interparticle friction. The relative density of powder compacts with nano particle may be lower than that of micron powder.
SEM images of compacted powders with average particle size of 20 and 3 μm after compaction tests are presented in Fig.12. Microstructures of powder compact were observed in the central part and neighboring part with punch. Most of neighboring particles on punch were plastically deformed and were arranged perpendicularly in transfer direction of punch. On the other hand, particles of the central part were closed while particles comparatively maintained the initial shape. The analysis results mainly agreed with experimental results, so finite element analysis using MPFEM was estimated to have an outstanding reliability.
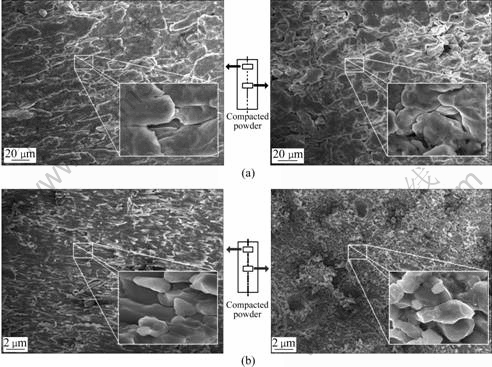
Fig.12 SEM images of compacted powders with average particle size of 20 μm (a) and 3 μm (b) after compaction tests
4 Discussion
Typical patterns of particle densification in powder compaction are presented in Fig.13. Ductile powder like aluminum is densified by interparticle contact with initial particle rearrangement, and elastic deformation and plastic deformation since then. After contact, the force between particles which is applied to the particle was mainly divided into normal force for contact point and rolling moments which is generated by tangential force. Here, normal force takes part in elasto-plastic deformation of particles and rolling moments contribute particle rearrangement.
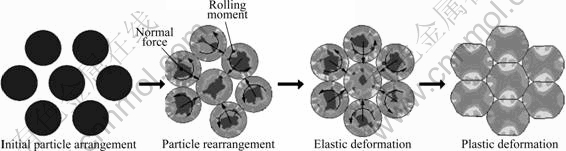
Fig.13 Typical patterns of particle densification in powder compaction
Fig.14 shows rolling moments of particles for different punch speeds in compaction simulations. Mean value of tangential load which was applied at seven particles located in central part of container divided by particle diameter was a rolling moment when compaction load was translated to particle of neighboring bottom of container. High punch speed gave low rolling moments. That pattern was difficult to explain clearly by results of this work. Rolling moments are expected to be reduced by increase of contact area between particles (plastic deformation of particle).
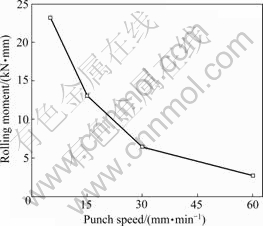
Fig.14 Rolling moments of particles for different punch speeds in compaction simulations
As previously stated, high punch speed led to the vertical strain chain within powders during compaction due to high propagation velocity of compaction load between particles. Low rolling moments of particles at high punch speed may be caused by these patterns that lead to the high normal force for a small contact area between particles or increasing the number of their contact before particle rolling. These problems will be discussed next.
5 Conclusions
To observe deformation behavior of particles and estimate the relative density for different punch speed and particle diameter, compaction simulations with Al powder using multi-particle finite element model were performed. In order to verify the reliability of finite element analysis, compaction tests for different punch speeds of 5, 15, 30 and 60 mm/min and average particle sizes of 20 and 3 μm were carried out. The results can be summarized as follows:
1) Higher compaction velocity provided higher loads for same punch stroke and lower punch stroke for specific load. Because the velocity of load transfer was fast and powder densification mode was formed perpendicularly for high compaction velocities, particles were restricted and plastically deformed at a short punch stroke.
2) Due to higher compaction velocity, a period of particle rearrangement decreased and relative density of final powder compacts decreased. On the other hand, particle movement was free and a long period of particle rearrangement and high relative density of powder compacts were given for a slow compaction velocity.
3) As the average particle size decreased, compaction load increased owing to higher interparticle friction. However, because a period of particle rearrangement was long and plastic deformation of particles occurred lately in the case of small particle size, relative density of final powder compacts was comparatively high.
4) High punch speed led to high rolling moments, followed by high particle movement and powder densification.
Acknowledgement
This work was supported by a grant-in-aid for the National Core Research Center Program from the Ministry of Education Science & Technology, Korea; and the Korea Science & Engineering Foundation (No. R15-2006-022-03003-0).
References
[1] LEWIS R W, JINKA A G K, GETHIN D T. Computer-aided simulation of metal powder die compaction processes [J]. Int J Powder Metall, 1993, 25(6): 287-293.
[2] GETHIN D T, TRAN V D, LEWIS R W, ARIFFIN A K. An investigation of powder compaction processes [J]. Int J Powder Metall, 1994, 30(4): 385-398.
[3] CUNDALL P A, STRACK O D L. A discrete numerical model for granular assemblies [J]. Geotechnique, 1979, 20: 47-65.
[4] CAMBOU B. Behavior of granular systems [M]. Springer: CISM Courses and Lectures, 1998: 385.
[5] MUNJIZA A, OWEN D R J, BICANIC N. A combined finite-discrete element method in transient dynamics of fracturing solids [J]. Eng Comput, 1995, 12: 145-174.
[6] HEYLIGER P R, McMEEKING R M. Cold plastic compaction of powders by a network model [J]. J Mech Phys Solids, 2001, 49: 2031-2054.
[7] MARTIN C L, BOUVARD D, SHIMA S. Study of particle rearrangement during powder compaction by the discrete element method [J]. J Mech Phys Solids, 2003, 51(4): 667-693.
[8] REDANZ P, FLECK N A. The compaction of a random distribution of metal cylinders by the discrete element method [J]. Acta Mater, 2001, 49: 4325.
[9] PROCOPIO A T, ZAVALIANGOS A. Simulation of multi-axial compaction of granular media from loose high relative densities [J]. J Mech Phys Solids, 2005, 53: 1523-1551.
Corresponding author: Byung-Min KIM; Tel: +82-51-581-3075; E-mail: bmkim@pusan.ac.kr
(Edited by YANG Bing)