文章编号:1004-0609(2009)07-1245-07
铜包铝复合扁线轧制变形行为的数值模拟与实验研究
罗奕兵,刘新华,谢建新
(北京科技大学 新材料技术研究院,北京 100083)
摘 要:采用三维刚塑性有限元法,研究铜包铝复合线材由圆断面到扁断面的平辊轧制变形行为及其对主要工艺参数的影响,并对模拟结果进行实验验证。结果表明:铜包铝圆线平辊轧制的宽展率和伸长率与压下率之间存在线性关系;当压下率为17.4%和29.4%时,摩擦因数对铜包铝扁线宽展率的影响很小;当压下率为43%时,随摩擦因数的增加宽展率增大;轧辊直径增大,扁线宽展率呈增大趋势,铜层分布的均匀性提高,但影响较小;在总压下率一定时,采用尽可能少的压下道次可使扁线获得更大的宽展率和更均匀的铜层分布;有限元计算结果与实验结果具有较好的一致性。
关键词:铜包铝;扁线;平辊轧制;数值模拟
中图分类号:TG 335.8 文献标识码:A
Numerical simulation and experimental investigation on
rolling behaviors of copper cladding aluminum flat wires
LUO Yi-bing, LIU Xin-hua, XIE Jian-xin
(Advanced Materials & Technology Institute, University of Science and Technology Beijing, Beijing 100083, China)
Abstract: The deformation behaviour of copper cladding aluminum wire in flat rolling process was investigated. The effect of main process parameters on the deformation was analyzed by 3D rigid plastic finite element model combining with experiments. The results show that there is a linear relation between the reduction rate and spread and elongation rate for the copper cladding aluminum flat wires. When the reduction rates are 17.4% and 29.4%, the friction coefficient has a very small influence on the spread rate. When the reduction ratio is 43%, the spread rate increases as the friction coefficient increases. With increasing roller diameter, the spread rate is enhanced and the distribution uniformity of copper layer is improved, but the effect is small. When the total reduction rate is invariable, it is suggested that the flat wire has more spread rate and uniformity of copper layer using possible fewer passes. The reasonable agreement of the FEM predictions and the experimental results is obtained.
Key words: copper cladding aluminum; flat wire; flat rolling; numerical simulation
金属包覆材料以单一材料所不具有的综合性能受到了广泛的重视,具有广阔的应用前景[1?2]。铜包铝导线与纯铜导线相比,具有密度低、相对成本低等优 点[1, 3],被认为是继铜、铝后的第三种理想导体材料,广泛用于同轴电缆内导体、布线、线圈和绕组导线等。若采用低密度的铜包铝扁线用作线圈或绕组导线,既可有效减轻线圈质量,还有利于提高线圈的槽满率,减小线圈尺寸。
较为常见的异形断面金属包覆材料的加工方法主要有热挤压法[4?5]和复合拉拔成形法[6?7]。热挤压法只适用于包覆层与芯材金属化学相容较好,且两种材料的屈服强度差较小[7?8]的金属包覆材料的制备。铜与铝的屈服强度之比σCu/σAl在室温下约为3.1,在500 ℃时增大到7.6[8],且铜与铝在高温下易形成脆性金属间化合物界面层[9]。因此,热挤压法难以用于铜包铝扁线的制备。复合拉拔法具有单道次变形量小、加工道次多、需通过热处理改善界面结合强度等特点,且一般只适用于断面积和宽厚比(即横断面宽度和高度之比)均较小的包覆材料的加工,难以适用于大断面异形复合材料、或宽厚比7~10以上的扁线的加工。
铜和铝均是具有良好冷加工性能的金属,而平辊轧制是高效、低成本的扁平断面材料(尤其是宽厚比10以上的扁平材料)的成形加工方法。为此,谢建新等[10?12]开发了采用平辊冷轧方法,由圆形断面的铜包铝铸坯或圆线,制备铜包铝导电扁排或扁线的工艺。迄今为止,有关单一材质圆线平辊轧制的变形行为有较多的研究报道[13?14],但关于包覆线材或棒材的平辊轧制变形未见报道。为了提高平辊轧制时包覆层厚度与扁线宽度的控制精度,本文作者采用刚塑性有限元法对铜包铝复合扁线的平辊轧制变形行为进行数值模拟,研究道次压下率、摩擦因数、轧辊直径和压下制度等工艺条件对铜包铝扁线尺寸及铜包覆层厚度均匀性的影响规律,并通过实验对有限元模拟结果进行验证。
1 有限元模拟分析
1.1 模型建立
1.1.1 几何模型
将铜包铝复合圆线进行平辊轧制成形扁线时的截面形状变化如图1所示。平辊轧制压下率εh为

式中:h0和h1分别为坯料轧前和轧后的厚度;Δh为道次压下量。
轧件宽展率
和伸长率A的定义分别为


式中:b0和b1分别为坯料轧前和轧后的宽度;l0和l1分别为坯料轧前和轧后的长度。
铜包覆层的均匀性用铜层厚度差?L来表征:
(4)
式中:L1和L2分别为断面内水平和垂直对称轴位置处的铜层厚度,如图1所示。
由图1可知,在铜包铝圆线的平辊轧制变形过程中,坯料在宽度和厚度方向具有对称性,故在有限元计算中仅取1/4圆柱体(见图2)为计算对象。ABBASI等[15]的研究表明,适当厚度的界面过渡层对铜包铝复合材料的冷成形性能影响较小,因而计算中假定铜层与铝芯直接接触,且铜层与铝芯在变形过程中的界面条件为完全结合状态,不发生分离现象。冷轧时铜与轧辊间的库仑摩擦因数[16]为 f=0.05~0.25。坯料的网格划分如图2所示,由于铜层厚度较薄,故其铜层的网格尺寸比铝芯的小,模型的网格总数为57 000。
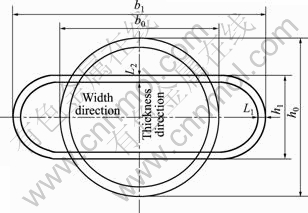
图 1 铜包铝圆线轧制前后截面形状示意图
Fig.1 Schematic diagram of cross-section shape change for CCA round wire rolling
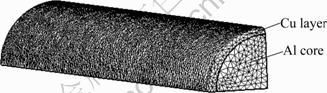
图2 圆线模型网格划分示意图
Fig.2 Schematic diagram of FE mesh for 1/4 of rod cross section
1.1.2 物理模型
为与实验保持一致,铜、铝材料分别选为T2和1060,铜、铝的本构关系方程[17]分别采用σ=245.3+ 14.72ε0.58 MPa和σ=93.2+0.98ε MPa。考虑到铜和铝流变应力的值较小,轧制时轧辊的弹性变形很小,因此在模拟中假设轧辊为刚体。本文作者采用刚体推动[18]法解决刚塑性有限元模拟轧制变形时的轧件咬入。
为与实验结果进行对比,在有限元模拟中铜包铝圆线坯料尺寸为d 10.6 mm,断面铜包覆层厚度为0.56 mm,铜包覆层面积比为20%。
在铜包铝扁线平辊轧制变形行为的研究中,道次压下率范围为17.4%~43%(厚向压下量为1.84~4.56 mm);轧辊与坯料的摩擦因数为f=0.1~0.25;轧辊直径为D=130~280 mm。
在压下制度对铜包铝扁线变形行为的影响研究中,取总压下率为41.5%(总厚向压下量为4.4 mm),坯料与轧辊间摩擦因数f=0.25,考察6种不同的压下制度(如表1所列)对宽展率和铜层厚度均匀性的影响。
表1 压下制度及变形量参数
Table 1 Deformation parameters of reduction schedule
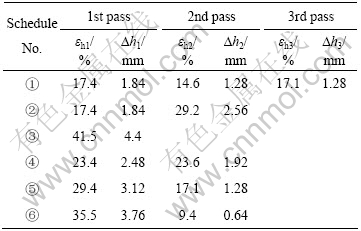
Total reduction ratio is 41.5%, and total reduction thickness is 4.4 mm.
1.2 模拟结果及分析
1.2.1 压下率对变形行为的影响
当轧辊直径D=130 mm,摩擦因数f=0.25,轧制速度v=0.13 m/s时,压下率对轧件宽展率和伸长率的影响如图3所示。从图3中可以看出,随着压下率的增大,轧件宽展率和伸长率均增加,且两者与压下率之间存在近似线性关系。当压下率为17.4%时,轧件
伸长率与宽展率基本相等;而随着压下率的增加,宽展率大于伸长率,且两者之差逐渐增大,轧制变形变为以宽展为主,也表明宽展受压下率的影响更显著。这一特点可以从厚向对称面内宽度方向的金属流动速度分布的明显变化得到解释。如图4所示,当轧制速度为0.13 m/s,轧辊直径D=130 mm,摩擦因数f=0.25,压下率从17.4%增大到35.5%时,金属在宽度方向的流动速度增加近2倍,大于压下率增加的倍数。随着压下率的增大,几何变形区长度(即坯料与轧辊接触长度的水平投影)从10.9 mm增加到15.5 mm,增加了42%,导致金属纵向流动阻力显著增加,使轧件伸长率的增大较小。
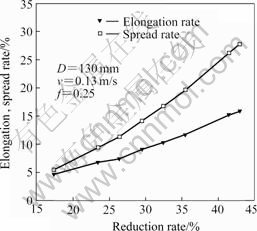
图3 压下率对轧件宽展率和伸长率的影响
Fig.3 Effect of reduction ratio on spread and elongation rate
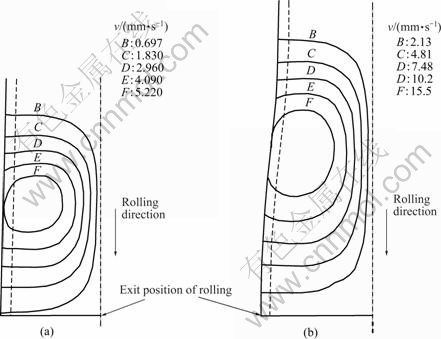
图4 厚向对称面宽度方向的金属流动速度分布图
Fig.4 Width velocity distribution of metal in thickness direction of symmetry plane: (a) εh=17.4%; (b) εh=35.5%
图5所示为压下率和宽展指数(w=Δb/εh)的关系。由图5可以看出,随着压下率的增加,宽展指数增大,但增长趋势逐渐变缓。这是因为当坯料直径一定时,压下率增加,即压下量增大,变形区长度增长,因而坯料在轧制方向的塑性流动阻力增加,使宽展指数增大。但是,压下率增加,坯料与轧辊接触面的宽度也增加,沿宽度方向流动的摩擦阻力增大,宽展增加的趋势减小。因此,随着压下率的增加,宽展指数的增长趋势逐渐减小。
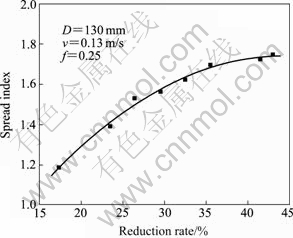
图5 压下率和宽展指数的关系
Fig.5 Relationship between reduction rate and spread index
计算结果表明,当轧辊直径D=130 mm,摩擦因数f=0.25时,不同压下率(εh=17.4%~43%)条件下轧制后扁线的铜层厚度差为ΔL=0.02~0.03 mm,其变化较小。由前面分析可知,铜包铝圆线平辊轧制时,变形以宽展为主,横断面上铜包覆层的变形以形状改变为主,因而轧制变形对铜层厚度变化的影响较小。
1.2.2 摩擦因数对变形行为的影响
当轧辊直径D=130 mm,轧制速度v=0.13 m/s时,摩擦因数对宽展率的影响如图6所示。从图6中可以看出,当压下率为17.4%和29.4%时,摩擦因数对铜包铝轧制扁线宽展率的影响很小;当压下率为43.0%时,随着摩擦因数的增加,宽展率增加。这是因为如表2所列,由圆形断面到扁形断面的平辊轧制变形中,当压下率在17.4%~29.4%的范围内时,几何变形区长度较小,摩擦因数的增加对轧制方向和宽度方向的流动阻力之比影响很小;而当压下率达到43.0%时,轧制方向几何变形区的长度为17.1 mm,大于宽度方向坯料与轧辊的平均接触宽度6 mm,即随着摩擦因数的增大,坯料在轧制方向和宽度方向的阻力之比增大,宽展增加。
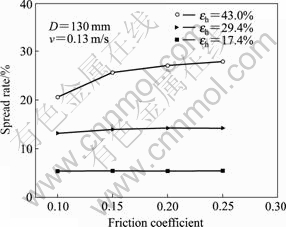
图6 摩擦因数对宽展率的影响
Fig.6 Effect of friction coefficient on spread rate
表2 不同压下率条件下轧制变形区长度和平均宽度的计算值
Table 2 Length and average breadth of deformation zone in variable reduction rate
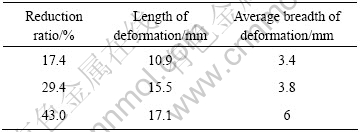
Roller diameter is 130 mm, and round wire diameter is 10.6 mm.
当压下率εh=43.0%时,摩擦因数对铜层厚度差ΔL的影响如图7所示。从图7中可见,随摩擦因数增大,铜层厚度差ΔL逐步减小。这是因为,L1位置铜层的变形以形状改变为主,而L2位置铜层的变形以延伸变形为主。当摩擦因数增大时,轧制方向阻力增大,延伸变形减小,L2位置铜层厚度减薄量变小,铜层厚度差ΔL减小,铜层分布的均匀性增加。因此,从增加扁线宽展和提高铜层分布均匀性两方面考虑,采用由平辊轧制铜包铝圆线制备扁线时宜采用无润滑(摩擦因数较大)轧制。
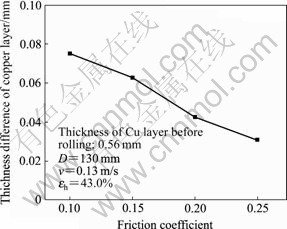
图7 摩擦因数对铜层厚度差的影响
Fig.7 Effect of friction coefficient on thickness difference of copper layer
1.2.3 轧辊直径对变形行为的影响
当压下率εh=26.4%,摩擦因数f=0.25,轧制速度v=0.13 m/s时,轧辊直径对轧件宽展率和铜层厚度差的影响如图8所示。从图8中可以看出,随着轧辊直径增大,铜包铝圆线平辊轧制的宽展率呈增加趋势,但增长量较小。在图8所示条件下,当轧辊直径从130 mm增大280 mm时,宽展率从11.4%上升到13.5%,增加量为2.1%。
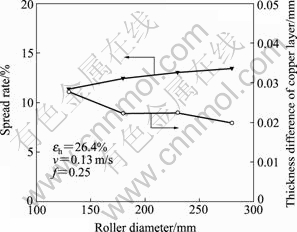
图8 轧辊直径对轧件宽展率与铜层厚度差的影响
Fig.8 Effect of roller diameter on spread rate and thickness difference of copper layer
轧辊直径增大,铜层厚度差值呈下降趋势,即铜层分布的均匀性增加,但变化量较小。这是因为,随着轧辊直径的增大,变形区长度增加,有利于轧件的宽展变形和铜层厚度差的减小。因此,从增加扁线宽展和提高铜层分布均匀性两方面考虑,采用平辊轧制制备扁线时宜采用较大直径的轧辊。
1.2.4 压下制度对变形行为的影响
轧制道次和压下率分配对宽展率和铜层厚度差的影响如图9所示,其中数字①~⑥分别对应于表1中所述6种不同压下制度。当总压下率为41.5%时,轧制道次对宽展率及铜层厚度差的影响如图9(a)所示。从图9(a)中可以看出,轧制道次越多,宽展率越小,铜层厚度差增加。这是因为总压下率一定,轧制道次越多,则每道次的变形量越小。由前述可知,在压下率较小时,铜包铝圆线轧制时延伸变形量相对增加,宽展变形相对减小,同时L2更易于变薄,因而轧制道次越多,其扁线最终的宽度越小。
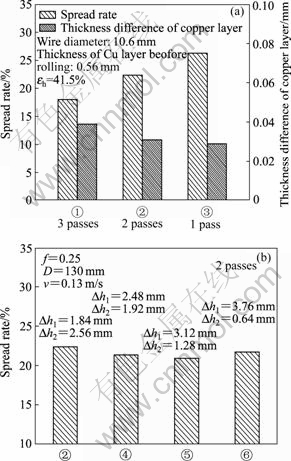
图9 轧制道次和压下制度对铜包铝圆线轧制变形的影响
Fig.9 Effect of total passes and rolling schedule on deformation of copper cladding aluminum wires (①?⑥ correspond to six rolling schedules in Table 1): (a) Total passes; (b) Reduction distribution in pass
图9(b)所示为轧制道次为2,4种不同压下量分配时的宽展率比较。从图9(b)中可以看出,采用2道次轧制时,压下量的分配对宽展率有一定的影响,第④、⑤种压下量分配时的宽展率较小。而第②种压下量分配(第一道次压下量较小、第二道次压下量较大)和第第⑥种压下量分配(第一道次采用大压下,而第二道次的压下量较小)轧制时,所获得的宽展率较大。
2 轧制实验及结果
2.1 实验方法
实验材料采用冷静液挤压法制备的铜包铝圆线,圆线直径10.6 mm,断面铜包覆层面积比为20%。轧制前铜包铝圆线在氩气保护下进行退火处理,退火温度为280 ℃,退火时间1.5 h。圆线试样头部用压力机压扁,以便轧制时能顺利咬入。轧制实验在二辊轧机上进行,轧辊直径为130 mm,轧制速度为0.13 m/s,采用无润滑轧制。
实验首先研究轧制压下率(23.0%~43.0%)和压下制度对宽展率的影响。然后在轧制总压下率为50.5%的条件下,分别采用一道次压下和两道次压下(其中εh1=26.3%)这两种压下制度分析轧制道次的影响。
采用线切割截取长10 mm的扁线试样,用树脂镶样后将试样端面磨平抛光,用数码相机拍摄截面形貌,再利用ImageTool软件测量照片中各处铜层厚度值。
2.2 结果分析
2.2.1 轧制压下率对宽展率的影响
图10所示为铜包铝圆线轧制压下率对宽展率的影响。由图10可以看出,铜包铝圆线轧制压下率和宽展率之间呈近似线性关系。无润滑轧制时坯料与轧辊间的摩擦因数f=0.25时计算结果与实验结果具有较好的一致性。
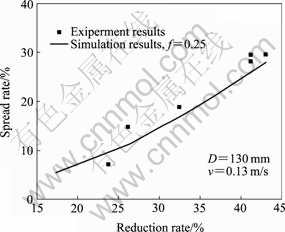
图10 铜包铝圆线轧制压下率对宽展率的影响
Fig.10 Effect of reduction ratio on spread rate for copper cladding aluminum wires
2.2.2 轧制道次对宽展率的影响
在总压下率为50.5%时,采用一道次轧制后的扁线宽展率为28.1%;采用两道次轧制(其中第一道次轧制压下率为εh1=26.3%)时,扁线宽展率为25.2%。改变总压下率和轧制道次的实验也得到相似结果,即压下率一定时,轧制道次增多,扁线的宽展减小,这与有限元计算结果一致。
2.2.3 压下率对铜层厚度差的影响
测得实验用直径10.6 mm铜包铝圆线的断面最大铜层厚度为0.59 mm,最小铜层厚度为0.49 mm。在压下率为为20.0%和41.0%时,扁线铜层最大铜层厚度与最小铜层厚度之差分别为0.11和0.14 mm。压下率对扁线轧制前后的铜层厚度均匀性影响较小。
图11所示为直径10.6 mm铜包铝圆线及其经两道次轧制(总压下率εh=62.3%)后扁线的横截面形状。从图11可以看出,扁线铜层厚度较为均匀。最大铜层厚度为0.43 mm,最小铜层厚度为0.28 mm,铜层平均厚度为0.35 mm(沿周长取40点测得的平均值),最大偏差为23%。
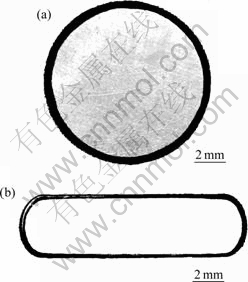
图11 铜包铝圆线和轧后扁线横截面的形状
Fig.11 Round and flat cross-section of copper cladding aluminum wire: (a) Round wire with d 10.6 mm; (b) Flat wire after 2 passes (about 4 mm×14.7 mm)
3 结论
1) 有限元计算结果表明,铜包铝圆线平辊轧制变形时宽展率分别与伸长率和压下率之间存在着线性关系。
2) 当压下率为17.4%和29.4%时,摩擦因数对铜包铝扁线宽展率的影响很小;当压下率为43%时,随摩擦因数增加,宽展率有较大增大。
3) 轧辊直径增大,扁线轧制宽展率呈增大趋势,铜层分布的均匀性提高,但影响程度均较小。
4) 在总压下率一定时,采用尽可能少的压下道次可使扁线获得更大的宽展率和更均匀的铜层分布。
5) 有限元计算结果与实验结果具有较好的一致性。
REFERENCES
[1] PERRARD W. Strategies for optimizing cable design and performance through the use of bimetallic wire[J]. Wire Journal International, 2001, 34(7): 154?159.
[2] GIBSON A. Emerging applications for copper-clad steel and aluminum wire[J]. Wire Journal International, 2008, 41(2): 42?148.
[3] XIE J X, WU C J, LIU X H, LIU X F. A novel forming process of copper cladding aluminum composite materials with core-filling continuous casting[J]. Materials Science Forum, 2007, 539/43: 956?961.
[4] 夏坚平, 薛运龙, 段文庆, 沈其峰, 贾 勇. 金属基三层微异形复合线材的新加工方法[J]. 稀有金属材料与工程, 1999, 28(6): 398?400.
XIA Jian-ping, XUE Yun-long, DUAN Wen-qing, SHEN Qi-feng, JIA Yong. A new manufacturing method for gold matrix three-ply composite microtapes[J]. Rare Metal Materials and Engineering, 1999, 28(6): 398?400.
[5] KIUCHI M, HSU R Q. Numerical stimulation of drawing of multi-cores clad bars[J]. Journal of Materials Processing Technology, 1992, 34(1/4): 397?404.
[6] GOMEZ X, ECHEBERRIA J. Microstructure and mechanical properties of carbon steel A210-superalloy sanicro 28 bimetallic tubes[J]. Mater Sci Eng A, 2003, 348(1/2): 180?191.
[7] AVIZTUR B. Metal forming: The application of limit analysis[M]. New York: Marcel Dekker, 1980.
[8] BERSKI S, DYJA H, MARANDA A, NOWACZEWSKI J, BANASZEK G. Analysis of quality of bimetallic rod after extrusion process[J]. Journal of Materials Processing Technology, 2006, 177(1/3): 582?586.
[9] KWON H C, JUNG T K, LIM S C, KIM M S. Fabrication of copper clad aluminum wire (CCAW) by indirect extrusion and drawing[J]. Materials Science Forum, 2004, 449/452: 317?320.
[10] 谢建新, 刘新华, 刘雪峰. 一种铜包铝复合扁线及其生产方法: 中国专利 200810057667.X[P]. 2008?02?04.
XIE Jian-xin, LIU Xin-hua, LIU Xue-feng. A flat cross section copper cladding aluminum composite wire and manufacturing process: CN 200810057667.X[P]. 2008?02?04.
[11] 谢建新, 刘新华, 刘雪峰, 罗奕兵. 一种高性能铜包铝矩形横断面复合导电母排及其制备工艺: 中国专利200810057668.4 [P]. 2008?02?04.
XIE Jian-xin, LIU Xin-hua, LIU Xue-feng, LUO Yi-bing. A high performance rectangle cross section copper cladding aluminum composite electric bus-bar and manufacturing process: CN 200810057668.4[P]. 2008?02?04.
[12] 谢建新, 刘新华, 刘雪峰. 一种铜包铝复合导线的短流程制备工艺: 中国专利 200810057669.8[P]. 2008?02?04.
XIE Jian-xin, LIU Xin-hua, LIU Xue-feng. A short manufacturing process of copper cladding aluminum composite electric wire: CN 200810057669.8[P]. 2008?02?04.
[13] KAZEMINEZHAD M, TAHERI A K. Deformation inhomogeneity in flattened copper wire[J]. Materials & Design, 2007, 28(7): 2047?2053.
[14] CARLSSON B. The contact pressure distribution in flat rolling of wire[J]. Journal of Materials Processing Technology, 1998, 73(1/3): 1?6.
[15] ABBASI M, KARIMI T A, SALEHI M T. Growth rate of intermetallic compounds in Al/Cu bimetal produced by cold roll welding process[J]. Journal of Alloys and Compounds, 2001, 319(1/2): 233?241.
[16] 重有色金属材料加工手册编写组. 重有色金属材料加工手册(第三分册)[M]. 北京: 冶金工业出版社, 1979.
Editorial Group of Heavy Nonferrous Processing Manual. Heavy nonferrous processing manual (3rd Fascicule)[M]. Beijing: Metallurgical Industry Press, 1979.
[17] 赵志业. 金属塑性加工力学[M]. 北京: 冶金工业出版社, 1987.
ZHAO Zhi-ye. Metal plastic working mechanics[M]. Beijing: Metallurgical Industry Press, 1987.
[18] 原思宇, 张立文, 齐 民, 甄 玉, 郭书奇. 推动模型在棒线材轧制过程模拟中的应用[J]. 钢铁, 2005, 40(5): 50?54.
YUAN Si-yu, ZHANG Li-wen, QI Min, ZHEN Yu, GUO Shu-qi. Application of pushing model in simulation of wire and rod rolling process[J]. Iron and Steel, 2005, 40(5): 50?54.
基金项目:北京市科技计划资助项目(207000300700707)
收稿日期:2008-10-10;修订日期:2009-01-08
通讯作者:谢建新,教授,博士;电话:010-62332254;E-mail: jxxie@mater.ustb.edu.cn
(编辑 李向群)