
Influence of phosphorus on oxidation behavior of
low thermal expansion superalloy IN909 at 650 ℃
SUN Ya-ru(孙雅茹)1, 2, SUN Wen-ru(孙文儒)2, HOU Gui-chen(侯桂臣)2, GUO Shou-ren(郭守仁)2,
LIU Zheng (刘 正)1, HU Zhuang-qi(胡壮麒)2, N. K. PARK3
1. School of Sciences, Shenyang University of Technology, Shenyang 110023, China;
2. Institute of Metal Research, Chinese Academy of Sciences, Shenyang 110016, China;
3. Korea Institute of Machinery and Materials 66, Sangnam-dong, Changwan 641-010, S. Korea
Received 28 July 2006; accepted 15 September 2006
Abstract: The effect of phosphorus on the oxidation resistance of low thermal expansion alloy IN909 was studied. The composition and structure of the oxidation layer were analyzed. It is found that the oxidation initiates at the grain boundaries. During the oxidation, Fe atoms diffuse toward the surface and form the outside oxidation layer as the oxide of iron. The transition oxidation layer lies between the oxidation layer and the matrix which is enriched with Nb, Ti and Si, forming FeTiO5, Nb2O5, Fe2SiO4 and TiO2. Phosphorus hardly influences the thermal expansion coefficient of IN909 alloy. However, it increases the formation of ε phase at the boundary of the transition oxidation layer and matrix. As a result, the oxidation rate is decreased efficiently because the ε phase inhibits the diffusion of the element such as iron from the matrix to the oxidation layer.
Key words: IN909 alloy; low thermal expansion superalloy; oxidation; phosphorus
1 Introduction
Low thermal expansion superalloys are helpful to improve the efficiencies of aero engines because they supply a ease of controlling the clearance between the rotating and static parts[1-2]. However, they suffered from the stress accelerated grain boundaries oxygen (SAGBO) attack because Cr greatly increases the thermal expansion coefficient and is limited in the low thermal expansion superalloys. The reason for SAGBO is the oxygen diffusion along grain boundaries and Fe toward the oxidation layer. It has been revealed that phosphorus noticeably inhibits the diffusion of oxygen along the grain boundary of some wrought superalloys[3-4]. More attentions have been paid on the behavior of phosphorus at grain boundaries because phosphorus is a surface-active element and tends to be segregated at the grain boundaries, and the stress rupture specimens are generally failed by intergranular fracture. The beneficial effect has been attributed to the grain boundary strengthening by phosphorus[5-10]. So in this study, the effect of phosphorus on the oxidation behavior of IN909 alloy was investigated.
2 Experimental
The alloys were melted in a vacuum induction furnace using high purity raw materials, and the chemical composition (mass fraction, %) of the ingots was Ni 38.5, Co 13.5, Nb 4.7, Ti 1.5, Si 0.35, B 0.007, C 0.010, the other was Fe. The chemical composition of alloy 1 was controlled within the specification of IN909 alloy. For alloy 2, the phosphorus addition was increased to 0.013%, and other elements were kept the same as those in alloy 1. The two ingots were homogenized at 1 120 ℃ for 10 h, hot forged into bars of 35 mm square section at 1 100℃, and rolled into bars with 16 mm diameter within 950-1 110 ℃. The bars were then given a heat-treatment: 980 ℃, 1 h, AC; 780 ℃, 8 h, furnace cooled at 55 ℃, 1 h to 620 ℃, 620 ℃, 8 h, AC. The thermal expansion coefficient was measured. The oxidation samples with a dimension of 10 mm× 10 mm×10 mm were exposed in air at 650 ℃ for 5, 20, 40, 60, 80 and 100 h, respectively. The mass of the samples after oxidation were measured by using electron analytical scales. The microstructures of oxidation layers were characterized by using optical and scanning electron microscopy (SEM) with EDX.
3 Results
3.1 Thermal expansion coefficient
As shown in Fig.1, the phosphorus addition up to 0.013% hardly influences the thermal expansion coefficient of IN909 alloy.
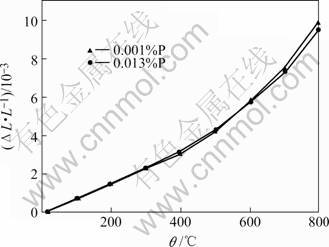
Fig.1 Effect of phosphorus on thermal expansion coefficient of IN909 alloy
3.2 Oxidation properties
The oxidation properties of the two alloys at 650 ℃ for up to 100 h are shown in Fig.2. Both of the two curves basically follow the parabolic law. The rate of mass gain at initial stage of oxidation within 5 h is higher, and it drops noticeably and remains constant from 5 to 100 h. The mass gain and oxidation rate of IN909 alloy are apparently decreased by 0.013% phosphorus addition.
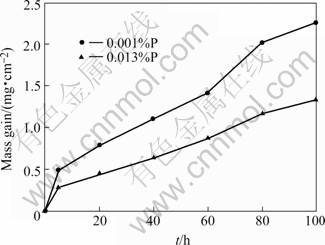
Fig.2 Effect of phosphorus on mass gain of IN909 alloy oxidized at 650 ℃
3.3 Microstructure of oxidation layers
The microstructure of the oxidation layer is shown in Fig.3, from which three zones are observed, outer oxidation layer, intermediate transition layer and matrix. Fig.4 shows the EDXS of the transition layer in Fig.3, the main compositions of the outer oxidation layer are Fe and O (Fig.4(a)), no other element is found in this region. The elemental distribution in the light gray zone of the transition layer is shown in Fig.4(b), the dark-gray channels in the transition layer corresponding to oxidation along boundaries are enriched with Nb, O, Fe and Si (Fig.4(c)). Combining the results of X-ray diffraction, it is determined that the outer oxidation layer is made up of Fe2O3, and the transition layer is made up of FeTiO5, Fe2SiO4 and TiO2.
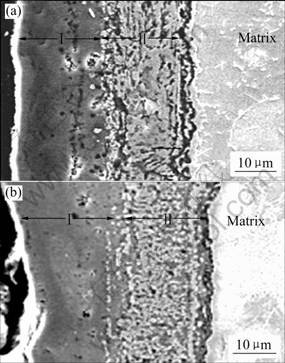
Fig.3 Cross sectional morphologies of oxidation layer of IN909 alloys oxidized at 650 ℃ for 20 h: (a) 0.001%P; (b) 0.013%P(I—Outer layer; Ⅱ—Transition layer)
Large amount of ε phase is precipitated in the matrix neighboring to the oxidation transition layer (Fig.5), 0.013%P addition greatly increases the precipitation of ε phase which parallels to each other. The ε phase is rich in Nb,Ti,Ni and Co.
4 Discussion
The external oxidation layer is made up of Fe and O, and the formation of Fe2O3 is obviously the main process of the oxidation of IN909 alloy. However, the oxidation process could not be so simple because the IN909 alloy contains many other elements.
From the results shown in Figs.3 and 4, more kinds of oxides are formed in the transition layer, including FeTiO5, Fe2SiO4 and TiO2. However, the outer oxidation layer only contains Fe2O3, other phases disappear. This implies that the complicated reaction takes place during the oxidation. It is apparently that O diffuses from air into the matrix, Fe from the matrix towards the oxidation layer during the oxidation. Other elements, such as Ti, Si and Nb, concentrate highly at the boundaries between the transition layer and matrix, forming FeTiO5, Fe2SiO4 and TiO2. The stability of these phases must be lower than that of the Fe2O3, and they will decompose, sending out O atoms and forming Fe2O3 when enough Fe atoms diffuse from the matrix to the boundary of the outer oxidation layer and transition layer. This may be the growing process of the oxidation scale.
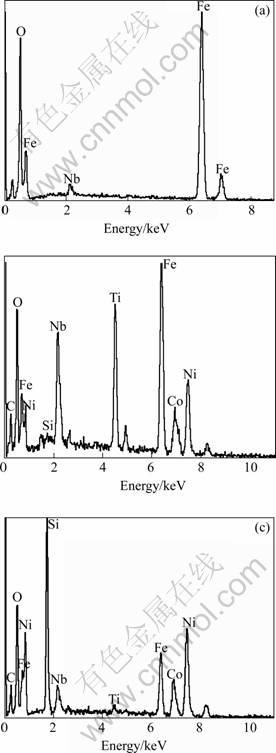
Fig.4 Elemental distribution in oxidation structure in Fig.3: (a) Outer layer; (b) Light gray zone in transition layer; (c) Dark gray zone in transition layer
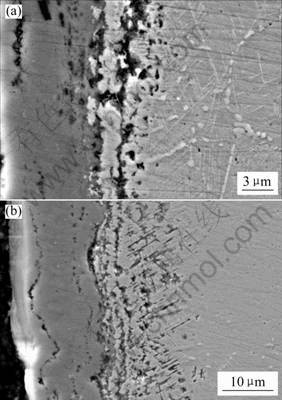
Fig.5 Precipitation of ε-phase in matrix neighboring to oxidation layer of IN909 alloys with 0.001%P (a) and 0.013%P (b)
Because the diffusion rate at the grain boundaries is naturally higher than that at the matrix, O atoms are easy to diffuse from the air into the substrate along the grain boundaries of IN909 alloy and Fe from matrix to the outside, and the oxides are firstly nucleated and grown at the grain boundaries, as is observed in Figs.3 and 4. With the growth of the oxides at the grain boundaries, the whole grain is turned from the alloy matrix into the oxide, forming the oxidation layer. Apparently, the grain boundary diffusion controls the oxidation rate of the IN909 alloy.
No phosphide or phosphorus-bearing phase is found in any phase of the IN909 alloy, so phosphorus must exist in the alloy as free atoms. Phosphorus is the surface-active element and naturally tends to be segregated at the grain boundaries. The phosphorus atoms at the grain boundaries occupy the defects there and would surely lower the grain boundary diffusion rate. As a result, the oxidation rate of the IN909 alloy is decreased.
As shown in Fig.5, phosphorus increases the precipitation of the ε-phase. The ε-phase is rich in Nb, Ti Ni and Co, whereas poor in Fe, so it will act as the barriers to inhibit Fe atoms to diffuse from the matrix towards the oxidation layer. The ε-phase appears as long bands parallel to each other between which the γ matrix exists, this structure will form a zigzag passage for the diffusion of O and Fe atoms. As a result, the diffusion distance is largely prolonged and the oxidation rate is decreased noticeably.
5 Conclusions
1) Phosphorus addition does not influence the thermal expansion coefficient of IN909 alloy.
2) The oxidation layer is constituted by Fe2O3 at the outside, and FeTiO5, Fe2SiO4 and TiO2 under the Fe2O3 scale.
3) The oxidation of the IN909 alloy is controlled by the grain boundary diffusion of the atoms such as Fe and O, the addition of phosphorus decreases the oxidation rate of IN909 alloy by inhibiting the grain boundary diffusion and increasing the precipitation of ε-phase.
References
[1] DENG B, HANG G W, FENG D. Development of low thermal expansion superalloys and their application in aerospace[J]. Journal of Aeronautical Material, 2003, 23: 244-246.
[2] SMITH J S, SMITH D F. Controlled Expansion Alloy[P]. US 4487743. 1984.
[3] HU Z Q, SUN W R, GUO S Y, LU D Z. Effect of trace P on Fe-Ni based wrought superalloys[J]. Chinese Journal of Nonferrous Metals, 2001, 11(6): 953-954.(in Chinese)
[4] GUO S R, SONG H W, LU D Z. The effect of phosphorous on superalloys[J]. Acta Metall Sinica, 2000, 35(10): 18-23.
[5] SUN W R, GUO S R. Effect of phosphorus on the δ-Ni3Nb phase precipitation and the stress rupture properties in alloy 718[J]. Mater Sci Eng A, 1998, A247: 173-179.
[6] GUO S R, SUN W R, LU D Z, et al. Effect of minor elements on microstructure and mechanical properties of IN718 alloy [A]. LORIA E A. Proceedings of Superalloys 718, 625, 706 and Various Derivatives[C]. Warrendale, PA: TMS-AIME, 1997: 521-530.
[7] SUN W R, GUO S R, LU D Z, et al. Effect of phosphorus on the microstructure and stress rupture properties in an Fe-Ni-Cr base superalloy[J]. Metall Mater Trans, 1997, 28A: 649-654.
[8] ZHU L Y. A new way to improve superalloys[A]. ANTOLOVICH S D. Superalloys 1992[C]. Warrendale, PA: TMS-AIME, 1992: 145-154.
[9] SONG H W, GUO S R, HU Z Q. Beneficial effect of phosphorus on the creep behavior of Inconel 718[J]. Scripta Mater, 1999, 41: 215-220.
[10] BRAINT C L. Grain boundary segregation in the Ni-base alloy 182[J]. Surf Interface Anal,1990, 16: 552-558.
(Edited by CHEN Wei-ping)
Foundation item: Projects(50271072, 504710831) supported by the National Natural Science Foundation of China
Corresponding author: SUN Ya-ru; Tel: +86-24-25691515; E-mail: yarusun@yahoo.com.cn