Article ID: 1003-6326(2005)05-1026-05
Effect of Cu on microstructure and mechanical properties of 2519 aluminum alloy
LI Hui-zhong(李慧中), ZHANG Xin-ming(张新明),
CHEN Ming-an(陈明安), LIU Ying(刘 瑛), ZHOU Zhuo-ping(周卓平)
(School of Materials Science and Engineering, Central South University, Changsha 410083, China)
Abstract: The effect of Cu on the microstructure and mechanical properties of 2519 aluminum alloy was investigated by means of tensile test, microhardness test, transmission electron microscopy, and scanning electron microscopy. The results show that when the content of Cu is less than 6.0%, the strength of 2519 aluminum alloy increases with the increase of Cu content; when the content of Cu is more than 6.0%, the strength of the alloy decreases. The hardening effect of the aged alloy is accelerated at 180℃ and the time to peak age is reduced, but the plasticity of the alloy gradually decreases with the increase of Cu content. However, the hardening effect of the aged alloy decreases with the increase of Cu as the content of Cu is over 6.0%. The optimal content of Cu of 2519 aluminum alloy is 6.0%, at which the alloy has best tensile strength and plasticity.
Key words: 2519 aluminum alloy; copper; ageing; microstructures; mechanical properties CLC number: TG146
Document code: A
1 INTRODUCTION
As the third generation of armor alloy developed by USA in the 1980s, 2519 aluminum alloy has some advantages such as light-mass, high strength as well as high corrosion resistance. Up to today, most work done on this alloy mainly focuses on the welding and stress corrosion cracking. The most important aspect in this alloy is the existence of precipitated phase θ which affects its mechanical properties. Subsequently, the precipitated phase θ′ is the main hardening phase of which Cu is one of the key hardening elements. Therefore,both of them make 2519 aluminum alloy exhibit age-hardening behavior. During aging, the appropriate content of Cu in this alloy is considered the most prevalent way. Carter et al[3] mentioned that the values of KISCC in 2519 aluminum alloy were decreased with the increase of Cu content while Gutscher and Gross[10] favored that the mass fraction of Cu has no effects on the welding properties of this alloy. However, there have been no investigations on the effect of Cu content on mechanical properties in 2519 aluminum alloy till now.
In this research, new alloys were designed through changing the content of Cu in 2519 aluminum alloy, and the effect of Cu on the microstructure and mechanical properties of 2519 aluminum alloy was analyzed by micro-hardness test, tensile test and microstructure observation.
2 EXPERIMENTAL
The compositions of 2519 aluminum alloy tested are given in Table 1. The alloys were melted in a graphite crucible at 780℃, and then cast into ingots at 730℃ with a size of 100mm×100mm×25mm. The ingots were homogenized at 520℃ for 18h, and then hot rolled into sheet with thickness of 7mm. Before cold rolling into 2.4mm, the sheets were annealed at 430℃ for 2h. After solution heat treatment at 530℃ for 2h, the sheets were quenched in water to room temperature. Consequently, they were cold rolled into 2.2mm with total reduction of 7.0%, and finally aged at 180℃.
Table 1 Chemical composition of experimental alloys(mass fraction, %)
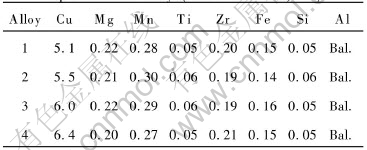
The microhardness was performed on HV-10B, and the Vickers hardness was obtained by averaging five measurements for each state. Tensile tests were performed on CSS-44100 machine. Every datum was an average value of three same samples. The microstructure was characterized by H-800 transmission electron microscopy(TEM) analysis. TEM samples were electro-polished in a 70% methanol and 30% nitric acid solution at -35℃ by using a twin-jet equipment operated at 30V. Optical microscopy analysis was carried out by Polyvar-Met.
3 RESULTS
3.1 Age-hardening behavior
Fig.1 shows the age-hardening curves of the alloys at 180℃. It is found that all the curves of the alloys exhibit age-hardening behavior apparently. With time prolonging, the microhardness of the alloy increases until the age-hardening curves appear a peak (a maximum of micro-hardness), and then the micro-hardness decreases with time increasing. It indicates that 2519 aluminum alloy possesses strong age-strengthening behavior (three stages of under-aging peak-aging and over-aging). When Cu content is less than 6.0%, the microhardness of the peak increases with the increasing content of Cu. However, the microhardness of the peak has an exception as the content of Cu is over 6.0%, which means the microhardness of the peak is not proportional to the content of Cu. When the content of Cu is 6.0%, the microhardness reaches a maximum of 146 HV while the time reaching the peak of the microhardness is shortened with the increasing content of Cu. When the content of Cu is 5.1% and 6.4%, the time of peak-aging is 24h and 18h, respectively, as seen in Fig.1.
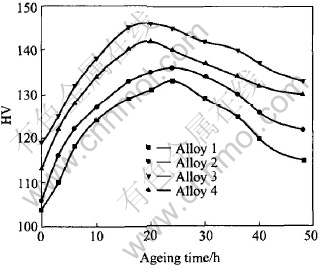
Fig.1 Age-hardening curves of alloys at 180℃
3.2 Tensile tests
Table 2 shows the mechanical properties of the alloys at room temperature. It can be seen that tensile strength (TS) and yield strength (YS) of the alloys are improved with the increase of Cu content. Conversely, the elongation decreases with increasing Cu. When Cu content was 6.0%, the TS and YS are highest with a value of 481MPa and 425MPa respectively. Furthermore, the strength decreases at room temperature with the content of Cu over 6.0%. For all of the alloys elongation decreases from 13.4% to 8% with the increase of Cu content.
Table 2 Mechanical properties of alloy at room temperature

3.3 Microstructure observations
Fig.2 shows the microstructure of the alloys under the condition of peak-aging. It is found that the microstructure reveals a characteristic of recrystallized microstructure after peak-aging. When Cu content is less than 6.0%, the microstructure exhibits no change with the varying content of Cu. When Cu content is more than 6.0%, finer recrystallized grain are found (Fig.2(d)) with a characteristics of remnant phase CuAl2 appearing. This can be attributed to phase CuAl2 which is not dissolved along grain boundaries so that growth of recrystallized grains were inhibited by those undissolved phases. Furthermore, some areas of the alloys appear fibrous microstructure. This is because the alloys are cold rolled again with a reduction of 7% after quenching (called T87 treatment).
Fig.3 shows the microstructure of alloy 1 and alloy 3 under the condition of peak-aging. It is found that the thickness of phase is about 10nm and 20nm in alloy 3 and alloy 1, respectively. However, the density of the phase in alloy 3 is larger. It is considered that the size of the phase becomes smaller, and the density of the phase becomes larger with increasing Cu content.
3.4 SEM micrographs of fracture surfaces
Fig.4 shows the SEM micrographs of fracture surfaces of the alloys under the condition of peak-aging. It is found that the fracture modes of all the alloys are integrated crack. With less content of Cu, there are many large and deep dimples on the fracture surfaces, which are called ductile fracture. As the content of Cu increases, dimples become smaller and shallower meanwhile the ratio of brittle fracture increases. From the above it is concluded that the increasing content of Cu will lessen the ductility of 2519 aluminum alloy, which is in agreement with the decrease of elongation.
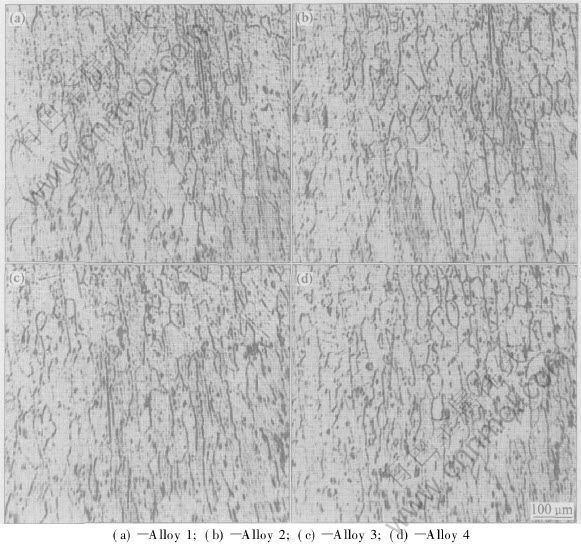
Fig.2 Morphologies of peak aged alloys
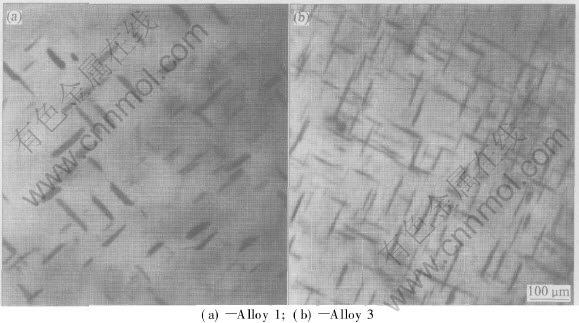
Fig.3 TEM images of peak aged alloys
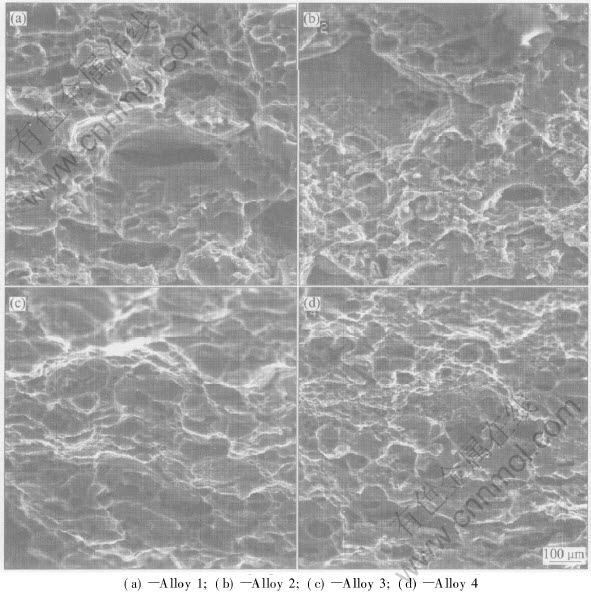
Fig.4 SEM micrographs of tensile fracture of alloys
4 DISCUSSION
2519 aluminum alloy is one kind of Al-Cu-Mg series alloys with a characteristic of high Cu/Mg ratio and age-strengthening. After solution treatment, coherent phase θ′ or semi-coherent phase θ′ is precipitated from the matrix of the alloy during artificial aging processing, which makes the alloys strengthen. The precipitation sequence is α (supersaturated solid solution)→ G.P. (Ⅰ) zone→θ″ phase→θ′ phase→θ (CuAl2) phase. It is known that the size, distribution and volume fraction of those precipitated phases determine alloys strength among Al-Cu-Mg series alloys. However, the volume fraction of precipitated phase relied on the composition of 2519 aluminum alloy and heat treatment process. In this research, different alloys were subjected to the same heat treatment process. Therefore, the chemical composition of the alloys was the key point. From Fig.3, it can be seen that the size of θ′ phase becomes smaller and the fraction value of it increases with the increase of Cu content. As Cu solves in the matrix of the alloy with high content, the supersaturated solubility of Cu will be advanced, and subsequently the kinetics of precipitation will be enhanced[12]. Therefore, supersaturated Cu precipitates in the form of θ′-precipitated phase during ageing and distributes homogeneously in Al matrix, which improved the strength of the alloys highly as much as possible (see Fig.1 and Table 2). Thus, more and more θ′ phases precipitate with the increasing content of Cu in the alloys. It is the right phase that improves the strength and hardness. The higher the content of Cu in 2519 aluminum alloy is, the more free vacancy appears. Meanwhile the diffusion rate of Cu atoms increases so that the time to nucleate and precipitate response of θ′ phase will be accelerated.
LIU et al[13] gave hypothesis that only the effect of age hardening was taken into account and ignored other hardening mechanisms. Therefore, the relation of σ with intrinsic yield strength (σi) and the increment of strength of θ′ (Δσ) are expressed as follows:
σ=σi+Δσ
The σi is a constant with respect to certain composition. Thus, the effect of ageing on Δσ is equivalent to the effect on σi. According to the research of Zhu et al[14, 15], relationship between increment of yield strength by θ′ precipitated phase and its size, volume is
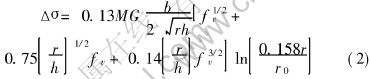
where Δσ denotes the increment of yield strength, G is the shear modulus, M is the Taylor coefficient, b is the Burgers vector of Al matrix and r0 is the inner radius of dislocations rounded those strengthening phase θ′; r, h and fv are the radius, half thickness and the volume fraction of θ′ phases respectively. The formula (2) indicates that the strengthening of θ′ phase is obvious in relation to its value fraction, and its thickness under a certain radius. Furthermore, the larger volume fraction of θ′ phase with thinner thickness is, the more strengthening is. This is in agreement with the results in this research.
When the content of Cu is more than 6.0%, the strength of 2519 aluminum alloy decreases. According to the phase diagram of aluminum and copper, the solute limit of Cu in Al is 5.7%. On one hand, when Cu content is beyond the solute limit, the volume fraction of aged precipitated θ′ phase increases with the increase of Cu content, the hardness and strength are improved; on the other hand, the quantity of the phases undissolved into the matrix increases with the increase of Cu content (Fig.2(d)). Those coarse remnant phases will rend the Al matrix so as to decrease the strength and hardness (called two mechanisms). Therefore, whether the properties of 2519 aluminum alloy are improved or not depends mainly on the competition between the two mechanisms. In this research, the second mechanism prevails with the increasing Cu content, and then strength of 2519 alloy decreases.
5 CONCLUSIONS
1) The content of Cu greatly determines the ageing behavior of 2519 aluminum alloy. When the content of Cu is less than 6.0%, the strength of 2519 aluminum alloy increases with the increasing content of Cu accordingly; as the content of Cu is more than 6%, the strength of the alloy decreases.
2) The hardening effect of the aged alloy is accelerated at 180℃ and the time to peak ageing is reduced, but the plasticity of the alloy gradually decreases with the increasing content of Cu as the content of Cu is less than 6.0%.
3) The optimal content of Cu of 2519 aluminum alloy is 6.0% which has best tensile strength and plasticity.
REFERENCES
[1]Fisher James J Jr. Aluminum alloy 2519 in military vehicles [J]. Advanced Materials and Processes, 2002, 160(9): 43-46.
[2]Carter H B, David H E, Ashok S, et al. Transient crack growth behavior in aluminum alloys C415-T8 and 2519-T87 [J]. Engineering Fracture Mechanics, 1999, 62(1): 1-22.
[3]Carter H B, David H E, Ashok S, et al. Creep crack growth behavior of aluminum alloy 2519 (Part Ⅰ)—experimental analysis [J]. ASTM Special Technical Publication, 1997, 1297(1): 3-18.
[4]Kramer L S, Blair T P, Blough S D, et al. Stress-corrosion cracking susceptibility of various product forms of aluminum alloy 2519 [J]. Journal of Materials Engineering and Performance, 2002, 11(6): 645-650.
[5]CHEN Xian-feng, PENG Da-shu, ZHANG hui, et al. Influence of heat treatment on mechanical properties and stress corrosion sensitivity of 2519 aluminum alloy plate [J]. The Chinese Journal of Nonferrous Metals, 2003, 13(4): 934-938.(in Chinese)
[6]Dymek S, Dollar M. TEM investigation of age-hardenable Al 2519 alloy subjected to stress corrosion cracking tests [J]. Materials Chemistry and Physics, 2003, 81(2-3): 286-288.
[7]LI Hui-zhong, ZHANG Xin-ming, CHEN Ming-an, et al. Microstructures and properties of welded joint of 2519 aluminum alloy [J]. The Chinese Journal of Nonferrous Metals, 2004, 14(6): 956-960.(in Chinese)
[8]ZHANG Xin-ming, GONG Min-ru, LI Hui-zhong, et al. Effect of ageing tempers of aluminum alloy 2519 sheet on intergranular corrosion [J]. Journal of Central South University(Science and Technology), 2004, 35(3): 349-352.
[9]WANG Zhu-tang, TIAN Rong-zhang. Manual for Aluminium Alloy and Its Processing [M]. Changsha: Central South University Press, 2000.
[10]Gutscher D J, Cross C E. Effect of Cu and Fe on the weldability of aluminum 2519 [A]. ASM Proceedings of the International conference: Trends in Welding Reseach [C]. Phoenix A Z, USA: ASM Int, 2002. 638-641.
[11]Mondolfo L F. Aluminum Alloys: Structure and Properties [M]. London: Butterworths, 1976. 497.
[12]LI Wei, SHEN Bao-luo, JING Shan, et al. Effect of copper content on age-hardening behavior of short mullite fibre reinforced Al-Cu composites [J]. The Chinese Journal of Nonferrous Metals, 2001, 11(2): 253-257.(in Chinese)
[13]LIU Gang, DING Xiang-dong, SUN Jun, et al. A model for age strengthening of plate like precipitate containing Al alloys [J]. The Chinese Journal of Nonferrous Metals, 2001, 11(3): 337-347.(in Chinese)
[14]Zhu A W, Strarke E A Jr. Strenthening effect of unshearable particles of finite size:a computer experimental study [J]. Acta Mater, 1999, 47(11): 3263-3269.
[15]Zhu A W, Csontos A, Strarke E A Jr. Computer experiment on superposition of strengthening effect of different particles [J]. Acta Mater, 1999, 47(6): 1713-1721.
Foundation item: Project(2005CB623706) supported by the State Key Fundamental Research Program of China
Received date: 2004-10-21; Accepted date: 2005-02-02
Correspondence: LI Hui-zhong, PhD; Tel: +86-731-8830265; E-mail: lhz606@mail.csu.edu.cn
(Edited by LI Xiang-qun)