
Grain refinement and plastic formability of Mg-14Li-1Al alloy
JIANG Bin(蒋 斌)1, 2, YIN Heng-mei(殷恒梅)2, LI Rui-hong(李瑞红)1, 2, GAO Liang(高 亮)1, 2
1. National Engineering Research Center for Magnesium Alloys, Chongqing University, Chongqing 400030, China;
2. College of Materials Science and Engineering, Chongqing University, Chongqing 400030, China
Received 23 September 2009; accepted 30 January 2010
Abstract: Al-5Ti-1B master alloy was added into Mg-14Li-1Al (LA141) alloy and then LA141 sheets were prepared by extrusion and cold rolling. The effect of the addition level of Al-5Ti-1B master alloy on the grain size of LA141 alloy was investigated as well as the effects of the total reduction of cold rolling and the annealing temperature on microstructure, mechanical properties and plastic formability of the LA141 sheets. The results show that the optimal addition level of Al-5Ti-1B master alloy into LA141 alloy is 1.25% (mass fraction) and LA141 alloy has the finest grains. With the increase of the total reduction of cold rolling, the grains of the as-rolled LA141 sheets were flattened gradually. A proper anneal temperature of 200 ?C is obtained for the cold rolled LA141 sheets. Under this condition, microstructure of the LA141 sheets consists of fine and uniform equiaxed grains and has higher Erichsen cupping index (IE).
Key words: Mg-14Li-1Al alloy; sheet; grain refinement; plasticity formability
1 Introduction
Mg-14Li-1Al (LA141) alloy has low density of 1.35 g/cm3, which is much lower than that of general magnesium alloys like AZ31 and ZK60. Meanwhile, this alloy is a single phase alloy and its main phase is β(Li) phase with a BCC crystal structure and good plasticity. Therefore, it has been used in many products for aeronautic and astronautic equipment in order to reduce mass[1].
However, Mg-Li alloy is chemically active, and its cast ingot is generally prepared by common mould casting because of no usable semi-continuous casting technique and equipment. So, Mg-Li alloy ingot has larger grain size and its strength is obviously lower than those of general magnesium alloys. To improve its strength and then extend its application, many new processes have been reported. Increasing the content of Al and Zn[2], reducing the content of Li[3], multi- element alloying[4] and composite reinforcement[5] will enhance the strength of Mg-Li alloy, but to some degree decrease good plasticity of Mg-Li alloy which is known as the most important features of this alloy. Rapid solidification[6] and equal channel angle process[7] will refine the grains of Mg-Li alloy, but these processes are costly.
Through a grain refiner, Mg-Li cast alloy with fine grains would be obtained. Thus, it is easy to carry out cold rolling with large reduction and to improve the mechanical properties and meanwhile keep low density. On this background, LA141 alloy was selected to prepare the sheet by cold rolling and Al-5Ti-1B master alloy was used as a potential grain refiner for LA141 alloy. The addition level of Al-5Ti-1B was optimized to get a better microstructures. Meanwhile, the microstructure during cold rolling and annealing of the LA141 sheets were investigated as well as the plastic formability, which would be used for reference in the future research and applications.
2 Experimental
The used alloy is commercial LA141 alloy and its main composition (mass fraction) is 13.5% Li, 1.2% Al and balance Mg. Al-5Ti-1B master alloy is also commercial alloy with main composition of 4.9% Ti, 1.1% B and balance Al.
The mass fractions of Al-5Ti-1B master alloy in the LA141 alloy is 0.5%, 1.0%, 1.25% and 1.75%,respectively. The LA141 alloy with the various additions of Al-5Ti-1B master alloy was respectively put into different mild steel crucibles (20 mm in diameter, and 100 mm in height). In order to ensure the same melting and solidification history, all the crucibles were placed into an induction furnace and were heated to 730 ?C in argon atmosphere. After isothermal holding for 10 min all the crucibles with the melt were cooled in the furnace under argon atmosphere until the melt solidified completely. Then, the LA141 ingots were gotten. The samples were cut for microstructure observation from the center of these LA141 ingots.
The optimized addition of Al-5Ti-1B was used to prepare the LA141 ingot with a larger size applied for extrusion of LA141 sheets. The mixture of LA141 with the optimized addition of Al-5Ti-1B was melted in the mild steel crucible under argon atmosphere by using the induction furnace at 730 ?C. After being held for 10 min, the melt was put out from the crucible by means of argon drive and was poured into a ferrous mould with the size of d85 mm×400 mm. Meanwhile, in order to obtain a good ingot, the bottom of the mould was sprayed by cooling compressed air until the solidification completed. The milled LA141 ingot containing Al-5Ti-1B was gotten with the size of d80 mm×300 mm.
In order to obtain the 2 mm thick and 100 mm wide LA141 sheet, d80 mm LA141 ingot was extruded at 200 ?C by a porthole die because this die can bring more uniform microstructure to the extrusion product[8].
During cold rolling of the LA141 alloy sheet, the reduction per pass was 15%-20%. When the total reduction was 50%, 64%, 70% and 75%, respectively, corresponding to the 1.00, 0.72, 0.60 and 0.50 mm thick LA141 sheets, microstructure of the as-cold rolled LA141 sheets was observed by optical microscopy. In order to optimize microstructure and mechanical properties, the as-cold rolled LA141 sheets were annealed under different temperatures. The standard Erichsen cupping test was also used to evaluate the plastic formability at room temperature of the annealed LA141 sheets, with the punch speed of 5 mm/min.
3 Results and discussion
3.1 Grain refinement of LA141 alloy by adding Al-5Ti-1B master alloy
The microstructures of LA141 without and with different additions of Al-5Ti-1B master alloy are shown in Fig.1. Because of the low cooling rate during solidification, the microstructures of all the LA141 ingots consist of equiaxed grains and no columnar grains are seen.
Fig.1 Microstructures of LA141 ingot with different additions of Al-5Ti-1B: (a) 0; (b) 0.50%, (c) 1.00%, (d) 1.25%; (e) 1.75%
The grain size of the LA141 alloy ingots containing Al-5Ti-1B master alloy was reduced obviously. When the addition content of Al-5Ti-1B is 1.25%, the mean grain size is reduced to 500 μm and the smallest grain size is gotten. Further increasing the content of Al-5Ti-1B would cause the grain size to increase to some degree, which is the same as the effect of ZnO particles on the grain refinement of Mg-Zn alloy[9]. It is shown that an optimal addition level of Al-5Ti-1B exists and efficiency of the grain refinement of Al-5Ti-1B is limited, which agrees with the grain refinement of aluminium alloys using the inoculation[10-12] and may be related to the release of latent heat during solidification[12-13].
3.2 Microstructure evolution of as-cold rolled LA141 sheets with different reductions
LA141 ingot containing 1.25% Al-5Ti-1B, which has the finest grains, was used to prepare the as-extruded LA141 sheets for the following cold rolling. The microstructure of the 2.00 mm thick as-extruded LA141 sheet is shown in Fig.2(a). The microstructure in this sheet consists of uniform and equiaxed grains because of both dynamical recrystallization during extrusion and uniform deformation resulted by the porthole die. The mean grain size is about 80 μm, much finer than that of the LA141 ingot shown in Fig.1(d). These fine and uniform equiaxed grains will be beneficial to the following cold rolling.
From Fig.2(b) to (e), with the increase of the total reduction of cold rolling, the grains of the as-cold rolled LA141 sheets are gradually elongated along rolling direction and their optical topography evolves from equiaxed (shown in Fig. 2(b)), to flat (shown in Fig.2(c)-(e)). Meanwhile, the ratio of length of the grains along rolling direction, to thickness of the grains along the thickness direction of the as-cold rolled LA141 sheets increases gradually. When the thickness of the as-cold rolled LA141 sheets is more than 0.6 mm and the total reduction is lower than 70%, the substructures in the grains are hardly observed in the microstructure, which

Fig.2 Microstructures of 2.00 mm thick as-extruded LA141 sheet (a) and as-cold rolled LA141 sheets with different reductions: (b) 50%, (c) 64%, (d) 70%; (e) 75%
shows that in the as-cold rolled LA141 sheets with lower than 70% reduction, the density of crystal defects is lower. LA141 maybe has a body center cubic structure and lower tensile strength[1], and plastic deformation occurs easily. It is possible that dislocations are easy to slip out of the sheet during cold rolling.
However, when the thickness of the as-cold rolled LA141 sheets is 0.50 mm and the total reduction is 75%, lots of substructures in the grains appear (shown in Fig.2(e)), which shows that lots of crystal defects will be formed in the as-cold rolled LA141 sheets with the larger total reduction. These defects will benefit the following annealing.
3.3 Microstructure and plastic formability of 0.50 mm thick as-annealed LA141 sheets
The 0.50 mm thick as-rolled LA141 sheets were respectively annealed at 150, 200 and 250 ?C for 1 h. The microstructures of the as-annealed LA141 sheets are shown in Fig.3. In the microstructure of the as-annealed LA141 sheet shown in Fig.3(a), some flat grains exist still. It is obvious that just partial recrystallization occurs in the as-cold rolled LA141 sheet and larger residual stress exists, although this sheet is annealed at 150 ?C for 1 h. At a higher temperature the recrystallization is easier[14]. With the increase of the annealing temperature, the microstructure of the as-annealed LA141 sheet is changed to the fine and uniform equiaxed grains (shown in Fig.3(b)), which shows that the recrystallization is enough. Further increasing the anneal temperature causes the local coarse grains (shown in Fig.3(c)). Therefore, the better annealing parameter for the as-cold rolled LA141 sheet is 200 ?C, 1 h.
The mechanical properties of the as-annealed LA141 sheets were tested and the results are shown in Table 1. It is shown that the LA141 sheet annealed at 150 ?C for 1 h has low strength and obvious anisotropy because of the partial recrystallization (shown in Fig.3(a)). The increase of the annealing temperature enhances the tensile strength and improves the anisotropy of strength and plasticity, due to the improvement of microstructure. The local coarse grains in the microstructure, resulting from higher annealing temperature, decreases both strength and plasticity and even increases their anisotropy.
Based on the above result, the plastic formability at room temperature of the as-annealed LA141 sheets was evaluated by Erichsen cupping test[15]. In this test, Erichsen cupping index (IE) is thought about as a criterion for the plastic formability at room temperature of the as-annealed LA141 sheets. The larger the IE value, the better the plastic formability at room temperature. The test results are listed in Table 2. The LA141 sheet annealed at 200 ?C has the largest IE value which shows
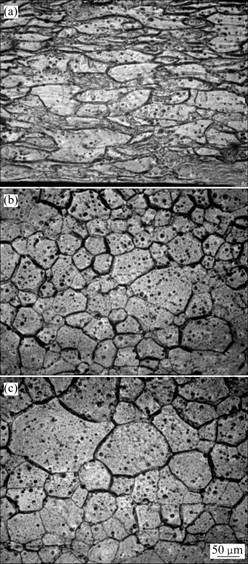
Fig.3 Microstructures of 0.50 mm thick LA141 sheet annealed at different temperatures for 1 h: (a) 150 ?C, (b) 200 ?C; (c) 250 ?C
Table 1 Mechanical properties of 0.50 mm thick LA141 sheets annealed at different temperatures for 1 h
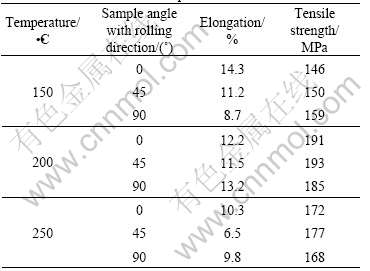
Table 2 IE of 0.50 mm thick LA141 sheets annealed at different anneal temperatures for 1 h
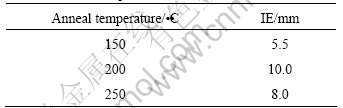
the best plastic formability at room temperature, because it has better microstructure and mechanical properties.
4 Conclusions
1) The Al-5Ti-1B master alloy can remarkably refine the grains of LA141 alloy. When the addition level is 1.25%, the mean grain size of the LA141 alloy is reduced to the largest degree.
2) With the increase of total reduction of cold rolling, the grains of the as-cold rolled LA141 sheets are flattened gradually. Meanwhile, crystal defects are not observed in the microstructure of the cold rolled LA141 sheets when the total reduction is no more than 70%. When the total reduction is 75%, lots of crystal defects are observed in the grains of the as-cold rolled LA141 sheet.
3) After being annealed at 200 ?C for 1 h, the cold rolled LA141 sheet has fine and uniform equiaxed microstructure, and therefore has the better mechanical properties and lower anisotropy. Meanwhile, the higher Erichsen cupping index is obtained and this annealing parameter will provide a better plastic formability at room temperature to the as-cold rolled LA141 sheet.
References
[1] HAFERKAMP H, NIEMEYER M, BOEHM R, HOLZKAMP U, JASCHIK C, KAESE V. Development, processing and applications range of magnesium lithium alloys [J]. Materials Science Forum, 2000, 350/351: 31-41.
[2] SANSCHAGRIN A, TREMBLAY R, ANGERS R, DUBE D. Mechanical properties and microstructure of new magnesium-lithium base alloys [J]. Materials Science and Engineering A, 1996, 220: 69-77.
[3] CAO F R, CUI J Z, WEN J L, LEI F. Mechanical behaviour and microstructure evolution of superplastic Mg-8.4wt pct Li alloy and effect of grain size and phase ratio on its elongation [J]. Journal of Materials Science and Technology, 2000, 16(1): 55-58.
[4] LE Q C, CUI J Z, LIU H W. Quenching and ageing behaviours of Mg-Li-Zn alloy [J]. Transactions of Nonferrous Metals Society of China, 1997, 7(3): 40-44.
[5] WOLFENSTINE J, GONZALEZ-DONCEL G, SHERBY O D. Elevated temperature properties of Mg-14Li-B particulate composites [J]. Journal of Materials Research, 1996, 5(7): 1359-1362.
[6] MATSUDA A, WAN C C, YANG J M, KAO W H. Rapid solidification processing of a Mg-Li-Si-Ag alloy [J]. Metallurgical and Materials Transactions A, 1996, 27A: 1363-1370.
[7] LIU T, ZHANG W, WU S D, JIANG C B, LI S X, XU Y B. Equal channel angular pressing of a two-phase alloy Mg-8Li-1Al. II. Room temperature tensile properties of the alloy processed by ECAP [J]. Acta Metallurgica Sinica, 2003, 39(8): 795-798.
[8] JIANG B, GAO L, HUANG G J, DING P D, WANG J. Effect of extrusion processing parameters on microstructure and mechanical properties of as-extruded AZ31 sheets [J]. Transactions of Nonferrous Metals Society of China, 2008, 18(S1): 160-164.
[9] FU H M, QIU D, ZHANG M X, WANG H, KELLY P M, TAYLOR J A. The development of a new grain refiner for magnesium alloys using the edge-to-edge model [J]. Journal of Alloys and Compounds, 2008, 456: 390-394.
[10] GREER A L, COOPER P S, MEREDITH M W, SCHNERDER W, SCHUMACHER P, SPITTLE J A, THRONCHE A. Grain refinement of aluminium alloys by inoculation [J]. Advanced Engineering Materials, 2003, 5(1/2): 81-91.
[11] IQBAL N, VAN DIJK N H, HANSEN T, KATGERMAN L, KEARLEY G J. The role of solute titanium and TiB2 particles in the liquid-solid phase transformation of aluminium alloys [J]. Materials Science and Engineering A, 2004, 386: 20-26.
[12] GREER A L, BUNN A M, THRONCHE A, EVANS P V, BRISTOW D J. Modelling of inoculation of metallic melts: Application to grain refinement of aluminium by Al-Ti-B [J]. Acta Materialia, 2000, 48: 2823-2835.
[13] MAXWELL I, HELLAWELL A. A simple model for grain refinement during solidification [J]. Acta Materialia, 1975, 23: 229-237.
[14] SU C W, LU L, LAI M O. Recrystallization and grain growth of deformed magnesium alloy [J]. Philosophical Magazine, 2008, 88(2): 181-200.
[15] KANG D H, KIM D W, KIM S, BAE G T, KIM K H, KIM N J. Room temperature formability of Mg alloys [J]. Materials Science Forum, 2009, 618/619: 463-466.
(Edited by CHEN Can-hua)
Foundation item: Project(50604020) supported by the National Natural Science Foundation of China; Project(2007CB613706) supported by the National Basic Research Program of China; Project(2009AA03Z507) supported by the National High-tech Research and Development Program of China
Corresponding author: JIANG Bin; Tel: +86-23-65111140; E-mail: jiangbinrong@cqu.edu.cn