
Preparation of silver nanoparticle via active template under ultrasonic
ZHENG Min(郑 敏)1, WANG Zuo-shan(王作山)2, ZHU Ya-wei(朱亚伟)1
1. College of Material Engineering, Soochow University, Suzhou 215021, China;
2. Powder Engineering Research Center, North China University, Taiyuan 030051, China
Received 16 February 2006; accepted 13 June 2006
Abstract: A novel method was described for the production of silver nanoparticle by using nano-carbon as active template. Special ultrasonic condition was used to assure the active effect of the template and achieve an even and stable micro-reactor system, therefore yield uniform silver nanoparticle without obvious agglomeration. By laser granularity instrument measurement, the silver nanoparticles show a mean diameter of 20.4 nm and narrow distribution between 18.7 nm and 23.0 nm according to the optimum technology. Regular spherical morphology can be observed by transmission electron microscopy(TEM). X-ray diffraction analysis indicates that Ag+ is deoxidized to form metal Ag during producing precursor, subsequent calcinations promote phase transformation from nonholonomic crystal to complete cubic crystal, which is consistent with the standard JCPDS card of silver. The results reveal that the nano-carbon in active template system not only exerts micro-reactor and steric stabilization effect, but also acts as reducing agent during the reaction.
Key words: silver nanoparticle; active template; nano-carbon; ultrasonic; agglomeration
1 Introduction
During the past several years, there has been a growing interest in the novel materials called nanomaterials that have a very high surface or interfacial area and exhibit dramatic changes in properties. Among them, metal nanoparticles have been extensively investigated because of their unique physical and chemical properties and wide potential applications, especially silver nanoparticle, which can be used as catalyst, refrigeration dilution agent, immunity sensor and antimicrobial[1,2].
At present, there are lots of techniques available for the synthesis of metal nanoparticles, which includes gas reduction process[3,4], precursor pyrolysis[5,6], microwave plasma synthesis , hydrodynamic cavitations and liquid chemical reduction[7-10] and laser ablation [11]. A key issue among these techniques is the control of particle size and agglomeration, which is very important in applications. While the use of gas reduction process can produce very small particles with size of less than 10 nm and narrow distribution, the expensive raw gas material and equipment results in high cost. Therefore, many researchers pay more attention to the solution chemical reduction method because of its low cost. Presently, small metal nanoparticles can be readily synthesized by chemical reduction in a liquid medium through choosing proper surfactants and protect agents, but invariably form hard agglomerates. What’s more, the negative effect on the purity of the final production and environment has also become inevitable. In this paper, a novel method is put forward for the production of silver nanoparticle by using nano-carbon as active template, which is on the base of our past research [12,13]. One of the advantages is that the active template nano-carbon exerts multifunction such as micro-reactor, reducing agent, protector and steric stabilization agent, which has not been reported in the past references.
2 Experimental
2.1 Materials
The metal salt was silver nitrate(AgNO3), analytic purity, purchased from Shanghai Chemistry Reagent Company. Polyvinyl alcohol(PVA) and other surfactants, chemical purity, were purchased from Shanghai Chemistry Reagent Company. The nano-carbon wasprepared through burning inadequately candle method according to Ref.[12] and has a mean diameter of 9.2 nm. The deionized water and alcohol was used in all preparation.
2.2 Preparation of active of template system
The stability of active template system is very important for attaining perfect nanoparticles. Therefore, the uniform nano-carbon without obvious agglomeration should be selected through deposition method before preparing active template system. Then a certain amount of nano-carbon was dispersed under special surfactant in 100 mL solvent including water and alcohol (70?30 in volume) in an ultrasonic bath (AS10200ADT, Tianjin Automatic Science Instrument Co, Ltd) for 10 min to form into even and stable active template disperse system.
2.3 Synthesis of silver nanoparticles
Firstly, AgNO3 was dissolved in medium including water and alcohol under environment temperature to attain certain molar concentration solutions of 0.1, 0.5, and 1.0 mol/L. The volume ratio of water to alcohol was 70?30, which was constant for all solutions.
Then, the AgNO3 solution was slowly dropped into the above stock active template system containing PVA slowly. In order to promote the reaction and control the agglomeration, ultrasonic action with certain frequency and power was necessary at intervals of 5 min until completing dropping. After that, ultrasonic was replaced by mechanical mixing for other 30 min to come into being complete crystal. The above perform was carried out at a constant temperature.
The above reaction system was placed without disturbing for 5-10 h and was then filtered, the filter cake was washed sufficiently using alcohol to remove the remnant anion
and water molecule to attain silver nanoparticle covered by nano-carbon template, which was also called precursors. After drying in air environment, the precursors were calcined in a resistance furnace under 350-500 ℃ temperature for 1-2 h to remove the nano-carbon black. The leftover was silver nanoparticles with gray color without milling.
2.4 Characterization
The crystalline phase of nanoparticles was determined by X-ray diffractometry (Shimadzu XRD- 6000, Cu Kα radiation), morphology of nanoparticles was observed via transmission electron microscope (JEM- 200CX), laser granularity instrument (America BROOKHAVEN. 90PLUS) was required to analyze the nominal crystallite size and distribution.
3 Results and discussion
3.1 Effect of ultrasonic frequency
Fig.1 shows the TEM images of the as-synthesized silver nanoparticles under different frequencies.
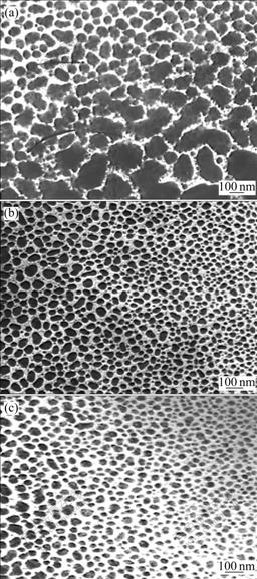
Fig.1 TEM images of as-synthesized silver nanoparticle under different ultrasonic frequencies (content of active template 0.5% (mass fraction, %), concentration of AgNO3 0.5 mol/L, calcined at 400 ℃ for 1 h): (a) 20 kHz; (b) 40 kHz; (c) 60 kHz
The micrographs demonstrate that the particle (circular dark spots) size decreases with increasing frequency. Lower frequency results in larger particle size (70nm) and obvious agglomeration (Fig.1(a)), higher frequency produces small particle size and uniform distribution (Figs.1(b) and (c)). Under frequency of 60 kHz, the silver nanoparticle has a mean diameter of 10 nm, which agrees well with the estimation from the surface area measurement (122 m2/g). Furthermore, the silver nanoparticles in Fig.1(c) have regular spherical morphology, while in Fig.1(a), we can obviously see some rod-like or triangle shaped particles. The above appearances attribute to different cavitations and disperse actions under ultrasonic frequencies, which will be explained in the following action mechanism discussion concretely.
3.2 Effect of active template concentration
Three groups of synthesis experiments were carried out with different active template concentrations. The different particle sizes and distributions of as-synthesized silver nanoparticles are shown in Fig.2.
According to Fig.2, 0.5% template concentration causes the smallest particle size, 1% has slightly larger value and 0.1% is the largest. It seems that different active template concentrations yield different mean particle sizes and distributions. A smaller mean particle size and narrower particle size distribution can be attained when the active template concentration reaches 0.5%. Further increasing the concentration results in bigger particle size. Therefore, neither too low template concentration (0.1%) nor too high template concentration (1%) is in favor of yielding small particle size, although without losing the advantage of narrow distribution. The difference between particles size and distribution is most likely due to the special function of the active template. Too low concentration cannot provide enough micro- reactor units and even strong steric stabilization function, while the active template in higher concentration is not easy to be dispersed under the present ultrasonic condition, so certain agglomerations are inevitable.
Furthermore, it should be noted that the disagreement between Fig.2(b) and Fig.1(c) is due to the different measure object. By transmission electron microscopy, the primary particle size is observed, while laser granularity instrument gives the granule size, which also indicates the formation of certain degree soft agglomeration in liquid medium.
3.3 Effect of calcining temperature
XRD patterns and relative data are shown in Fig.3 and Table 1 for the silver nanoparticles including the as- synthesized precursor and those calcined at different temperature from 350 to 500 ℃ for 1 h.
From the as-synthesized precursor (Fig.3(a)), we can see that there exist some relative weak diffraction peaks like hackle beside the typical Ag cubic crystal diffraction peaks, which were presumed to be the co-existence of crystallite Ag, amorphous Ag and amorphous carbon template. The results indicate that Ag+ is deoxidized to form metal Ag during producing precursor, with very small mean particle size estimated, using Scherrer’s equation of 11.12 nm (sample a in Table 1). The subsequent calcination promotes the transforma- tion from amorphous or nonholonomic crystal to complete of the crystal (Figs.3(b) and (3c)). Further increasing calcining temperature leads to hard agglome-meration and formation of a big crystal size of 79.77 nm (sampled in Table 1).
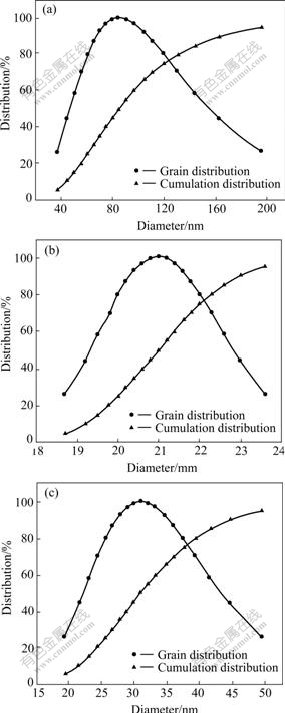
Fig.2 Granularity size and distribution of silver particles prepared by using different active template concentrations (frequency 60 kHz, concentration of AgNO3 0.5 mol/L, calcining temperature 400 ℃ for 1 h): (a) 0.1%; (b) 0.5%; (c) 1.0%
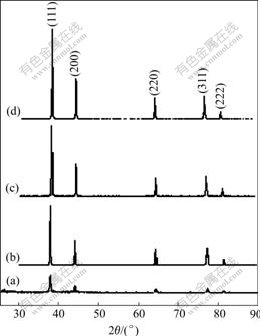
Fig.3 XRD patterns of silver nanoparticle calcined under different conditions: (a) Before calcining; (b) 350 ℃, 1 h; (c) 400 ℃, 1 h; (d) 500 ℃, 1h
Table 1 XRD patterns of silver nanoparticles calcined under different conditions
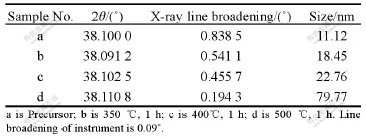
The XRD patterns also show that the crystal structure of the as-synthesized nanosilver is face-center cubic and the presence of the diffraction peaks are corresponding to the (111), (200), (220), (311) planes. All the peaks in the XRD pattern can be indexed as a standard Ag crystal (JCPDS, No.4-0783), which also indicates a high purity of as-synthesized nanosilver crystal.
3.4 Action mechanism of active template
From the experimental results and discussion described above, the action mechanism of active template under ultrasonic can be concluded according to the following several aspects: micro-reactor unit, steric stabilization function and reducing effect.
3.4.1 Micro-reactor unit of active template
The active template nano-carbon is distributed evenly in the liquid environment because of the strong disperse action of ultrasonic. The collapses of the cavitated bubbles, mainly occurring in interface between solid amounts of free hydroxyl with reducing action and “hot spots” with high temperature and high press, which are mostly adsorbed on the tiny pores or surfaces of the active template mediums and form a kind of dynamic micro-reactor units. Ag+ was deoxidized to form metal Ag in micro-reactor units; the produced metal Ag was adsorbed on the template medium rapidly. The adsorption ability of template decreases following increasing adsorption content of Ag, which is in favor of preventing the agglomeration of products. The amount of micro-reactor units and its anti-agglomeration effect mostly depend on the frequency of the ultrasonic. High frequency can yield amounts of activation bubbles and promote the diffusion of particles in liquid system and control agglomerations effectively. The results are shown in Fig.1.
3.4.2 Steric stabilization function of active template
Steric stabilization function, a kind of function for preventing the agglomerations of nanoparticles, is very important during synthesizing and heat treating, which will assure the as-synthesized nanoparticle with small size and uniform distribution. In our research, active template exerts its steric stabilization function through its “tiny-pore” effect and “bridge-bind” effect. The dynamic “tiny-pore” is in favor of forming even crystal cores and controlling the crystal growing to form uniform precursor. The “bridge-bind” effect produces lots of pore spaces, whose impalement action for crystal interface restrains the reaction between pore space and crystal interface and controls the crystal growing during calcining. Moreover, the strong adsorption of template binds up the transplant of crystal interface and the gaseity tiny pores also promote the disperse effect during calcining.
3.4.3 Reducing function of active template
The reducing function of active template nano-carbon is recognized from the XRD patterns of the as-synthesized precursor (Fig.3(a)). In micro-reactor unit, Ag+ was deoxidized to form metal Ag without adding other reducing agent besides nano-carbon, which indicates the special reducing function of active template. Reducing function of nano-carbon can be contributed to the peculiar structure of nano-carbon: a large number of atoms congregate on the surface and induce gigantic surface energy, which results in remarkable difference between surface atoms and inner ones. Most of the surface atoms are in “nudity” and have high activation than common materials; moreover, the existence of active nano-carbon promotes the cavitations and the subsequent collapse because of its peculiar structure, therefore, producing amounts of free hydroxyl with reducing action. Some research has reported the reducing function of simple ultrasonic[14], however in this experiment, metal Ag could not be attained under simple ultrasonic or common carbon under ultrasonic, which further proves the reducing function of nano-carbon active template. An interesting appearance is found that the nano-carbon can not exert reducing function until under ultrasonic environment, which indicates the strengthening action of the ultrasonic for nano-carbon, and agrees with the results in Ref.[15].
4 Conclusions
1) The high ultrasonic frequency is in favor of producing nanoparticle with small particle and narrow distribution, low ultrasonic frequency results in a considerable degree of agglomeration. The presence of proper concentration template is suitable for synthesis of perfect silver nanoparticle, while the active template in higher concentration is not easy to be dispersed under present ultrasonic condition, so certain agglomerations are inevitable.
2) Ag+ is deoxidized to form metal Ag during producing precursor. Furthermore, the typical XRD pattern of the as-prepared silver nanoparticle shows the presence of the diffraction peaks corresponding to the standard structure (JCPDS, No.4-0783). The multifunction of active template such as micro-reactor, reducing agent, protector and steric stabilization agent, can be enhanced under special ultrasonic field. This method provides a promising route to prepare metal nanoparticle without obvious agglomeration.
References
[1] KIZUKA T, ICHINOSE H, ISHIDA H. Structure and hardness of nanocrystalline silver [J]. J Mater Sci, 1997, 32(6): 1501-1507.
[2] LIANG Hai-chun, RONG Min-zhi, ZHANG Ming-qiu. Studies on silver nanoparticles synthesized by microemusion and their fluorescence [J]. Acta Physica Sinica, 2002, 51(1): 50-54.
[3] SAITO Y, MIHAMA K, UYEDA R. Formation of ultrafine metal particles by gas-evagaration [J]. Japan J Appl Phys, 1980, 19(9): 1603-1610.
[4] LIU Hua-rong, GE Xue-wu, NI Yong-hong. Synthesis and characterization of polyacrylonitrile-silver nanocomposites by irradiation [J]. Radiation Physics and Chemistry, 2001, 61(1): 89-91.
[5] ZHOU Quan-fa, XU Zheng. The research of silver nanoparticle synthesized via reduction-protection [J]. Journal of Fine Chemical Engineering, 2001, 18(1): 39-42.
[6] NIKIL J R, GEARHEART L, MURPHY C J. Wet chemical synthesis of silver nanorods and nanowires of controllable aspect ratio [J]. Chem Commun, 2001, 5: 617-622.
[7] POONDI D, DOBBINS T. A novel laser solid interaction for synthesis of silver, nickel, and immiscible silver nickel alloys from liquid precursors [J]. Journal of Materials Science, 2000, 35(24): 6237-6243.
[8] VIJAYA K, MASTAI Y, DIAMMNT Y. Sonoehemieal synthesis of amorphous Cu and nanocrystalline Cu2O embedded in a polyaniline matrix [J]. J Mater Chem, 2001, 11: 1209-1213.
[9] RODRIGUEZ SANCHEZ L, BLANCO M C. Electrochemical synthesis of silver nanoparticles [J]. Journal of Physical Chemistry B, 2000, 104(41): 9638-9688.
[10] ZHAO Bin, YAO Ming-yi, WEN Dong. Preparation and electric conductivity of ultrafine silver particles with polymer-protected colloidal dispersions [J]. Journal of East China University of Science and Technology, 1995, 21(4): 428-434.
[11] GUO Guang-sheng, GU Fu-bo, WANG Zhi-hua. Preparation of Zn nanocrystals with different morphologies by laser ablation [J]. The Chinese Journal of Nonferrous Metals, 2004, 14(10): 1749-1751. (in Chinese)
[12] WANG Zuo-shan. Preparation of Nano-sizes Alpha Alumina via Template-intervening Process and its Application [D]. Shanxi:North University of China, 2004.
[13] ZHENG Min. A kind of method for synthesizing rutile phase nano-titanium oxide [P]. CN1546384A, 2003.
[14] LIAO Xue-hong, ZHU Jun-jie, QIU Xiao-feng. Preparation of like-spheres and dendrites silver nanoparticles by soloelectron- chemical method [J]. Journal of Nanjing University, 2002, 38(1): 119-123.
[15] LI Yan, YU Hong-ying, SUN Dong-bai. Nano copper powder produced by chemical reduction under ultrasonic field and its influence facts [J]. The Chinese Journal of Nonferrous Metals, 2004, 14(11): 1947-1951. (in Chinese)
(Edited by LONG Huai-zhong)
Corresponding author: ZHENG Min; Tel: +86-512-68998646; E-mail: zhengmin@suda.edu.cn