
Effects of whisker surface treatment on microstructure and properties of Al18B4O33w/6061Al composites
GENG Lin(耿 林), GUAN Li-na(关丽娜), L? Kui-ming(吕奎明)
School of Materials Science and Engineering, Harbin Institute of Technology, Harbin 150001, China
Received 3 February 2009; accepted 26 May 2009
Abstract: 6061Al matrix composites reinforced by ZnO-coated Al18B4O33 whiskers were fabricated by a semi-solid mechanical stirring technique. The effects of ZnO coating on interfacial reaction between whiskers and matrix and the tensile properties of the composites were investigated. Tensile tests on composites were performed at room temperature, and microstructures were observed by scanning electron microscopy (SEM). The results show that the surface treatment of whiskers could reduce interfacial reaction effectively, improve the wettability between whiskers and matrix and enhance the tensile properties of the composites obviously. In addition, semi-solid stirring parameters were also under preliminary study. The stirring parameters were determined by the distribution of whiskers in the composites. The composites with homogeneously distributed whiskers were fabricated by semi-solid stirring at 610 ℃ for 30 min.
Key words: 6061Al matrix composites; aluminum borate whisker; semi-solid stirring; wettability; interface
1 Introduction
Aluminum borate whisker reinforced aluminum matrix composites (Al18B4O33w/Al) have been extensively investigated on account of their low density, improved mechanical properties and low cost[1-2]. Thus, aluminum borate whiskers have been paid many attentions. Because the interface between the matrix and reinforcement plays a critical role in determining the properties of metal matrix composites (MMCs), many researches on the interface reaction and its effect on the mechanical properties of Al18B4O33w/Al composite have been done[3-4]. The poor interfacial wettability between aluminum borate whisker and aluminum matrix affects the properties of the Al18B4O33w/Al matrix composites. Unfortunately, few studies have been concerned with the improving of wettability between Al18B4O33 whisker and aluminum matrix. Reinforcement coating is one of the most effective technique to improve interfacial properties of MMCs[5]. The coating of whiskers was prepared commonly by sol-gel method and electroless plating[6-7]. Electroless plating can only achieve a relatively uniform metallic layer effectively, while sol-gel method is an advanced technique to synthesize high quality ceramic materials including fine powders and oxide thin films[8-9]. YUE et al[10] have successfully prepared ZnO coating on Al18B4O33w surface by means of sol-gel method. ZnO coating can improve the Al18B4O33w/Al wettability effectively. However, the sol-gel method has the disadvantages of complicated technology, high cost and severe pollution. The precipitation process is very effective for the preparation of whisker coating and it has advantages such as simple production equipment, low cost and suitability for industrial manufacture.
In addition, the application of Al18B4O33w reinforced aluminum matrix composites is affected by the preparation methods. The process of powder metallurgy is complex and squeeze casting technique is not suitable for industrial manufacture. Semi-solid stirring and forming are very effective molding method for metals and metal matrix composites because of low cost and easy handling[11-12]. The semi-solid technique also can solve the problems such as floating, segregation and unwettability of nonmetal materials[13-15]. Although semi-solid stirring technique is very useful for the application of the composites, study on this technique is limited.
In the present work, ZnO coating is coated on the surface of Al18B4O33 whisker using precipitation process in order to improve the interface wettability and reduce the interfacial reaction between Al18B4O33 whisker and matrix. The composites are fabricated by semi-solid mechanical stirring technique. Subsequently, the coating characteristics, the stirring parameters, microstructure and mechanical properties of composites are investigated and discussed.
2 Experimental
The reinforcement of the composites used in this study was Al18B4O33 whisker with 0.5-1 μm in diameter and 10-30 μm in length. The composition of the selected matrix 6061 alloy was as follows: 0.6% Si, 0.7% Fe, 0.3% Cu, 0.15% Mn, 0.8% Mg, 0.25% Zn and balance Al (mass fraction).
The Al18B4O33 whiskers were coated with ZnO layer using a precipitation process. Firstly, Al18B4O33 whisker and ZnCl2 at a mass ratio of 10?1 were put in distilled water. Secondly, the NH3·H2O solution was put into the slurry slowly and mixed by ultrasonic vibration and electric stirring to prevent whisker from agglomeration. Finally, the treated whiskers were dried at 90 ℃, followed by calcination at 500 ℃. For simplification, the coated whiskers were marked as Al18B4O33w/ZnO, and the composites reinforced by the coated and uncoated Al18B4O33 whiskers were marked as Al18B4O33w/ ZnO/6061Al and Al18B4O33w/6061Al, respectively.
The Al18B4O33w/6061Al and Al18B4O33w/ZnO/ 6061Al composites containing 5% volume fraction of whiskers were fabricated using semi-solid mechanical stirring technique in a protective atmosphere of argon to avoid oxidation. The process was as follows: 1) 6061Al alloy was melted at 800 ℃ in stainless steel crucible and then cooled to a semi-solid temperature. In order to investigate the effects of stirring temperature on the whiskers distribution, the semi-solid temperatures were selected as 650, 630 and 610 ℃, respectively; 2) Al18B4O33 whiskers were preheated to 600 ℃ and added quickly into the semi-solid alloy, and the melt was stirred at 300 r/min for 15 and 30 min respectively at the determined semi-solid temperature; 3) the semi-solid slurry was then poured into a preheated extrusion container (480 ℃) and allowed to solidify under a 200 MPa pressure to obtain billet with high density; 4) The billet was extruded with an extrusion ratio of 25?1 and a constant ram speed of 15 mm/s and then cooled in the air.
The phase composition of coated whiskers was analyzed using a Philips X'Pert X-ray diffractometer (XRD). The morphologies of the whiskers before and after surface treatment and the whisker distribution in the composites were examined by a Hitachi S-3000N scanning electron microscope (SEM). The tensile tests were carried out using an Instron-1186 universal testing machine at a constant crosshead speed of 0.5 mm/min.
3 Results and discussion
3.1 Characterization of coated Al18B4O33 whisker
The SEM micrographs of the whiskers before and after coating treatment are shown in Fig.1. From the figure it can be seen that there is no evident change in length and diameter of the whiskers before and after the coating treatment. The surface of the Al18B4O33 whisker is coated by a layer of relatively uniform particulates after coating treatment and the coated surface is rougher than that before coating treatment, indicating that certain material is coated on the surface of the Al18B4O33 whisker.
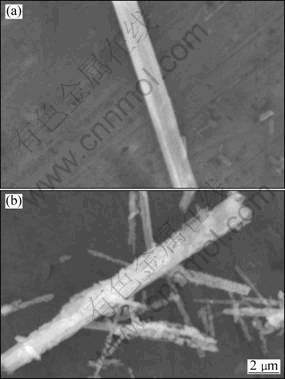
Fig.1 SEM micrographs of Al18B4O33 whiskers: (a) Al18B4O33w; (b) Al18B4O33w/ZnO
To determine the phase composition of the Al18B4O33 whisker after coating treatment, XRD analysis was carried out for the coated Al18B4O33 whiskers. The XRD result shown in Fig.2 for the coated Al18B4O33 whiskers demonstrates that the surface of the Al18B4O33 whisker is coated with ZnO. The total reaction during coating treatment and high temperature calcining stage is as follows:
ZnCl2+2NH3·H2O=2NH4Cl+ZnO+H2O (1)
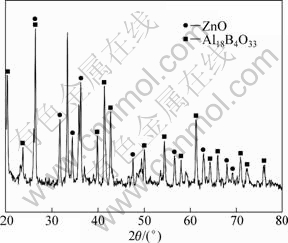
Fig.2 XRD pattern of coated Al18B4O33 whiskers
3.2 Effect of ZnO coating on wettability between molten 6061Al and Al18B4O33 whisker
In order to evaluate the effect of ZnO coating on the wettability between molten 6061Al and Al18B4O33 whisker, the infiltration pressure of molten 6061 aluminum alloy into the Al18B4O33 whisker preform was measured and analyzed. The preforms with the coated and uncoated whiskers were prepared with the same process. Colloidal silica as a binder was added during perform fabrication. The mixture of the whiskers and the binder was stirred and ultrasonic oscillated simultaneously, then it was poured into a cylindrical mold and pressed into a required size. The preform was subsequently baked at 80 ℃ for 8 h followed by sintering at 700 ℃ for 2 h. Fig.3 shows the variations of the infiltration pressure with the ram displacement during the infiltration of molten 6061Al into the uncoated and coated Al18B4O33 whisker preforms. The collected data suggest that the infiltration pressure increases with the increase of the ram displacement. It is also found that the pressure for the coated whisker preform is lower than that for the uncoated one during infiltration process. This may be attributed to the improvement of the wettability between Al18B4O33 whisker and molten 6061 aluminum alloy owing to ZnO coating, which is analyzed as follows.
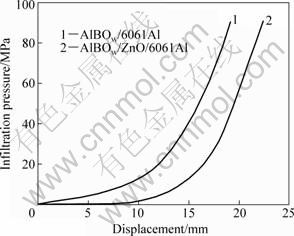
Fig.3 Variation of infiltration pressure with displacement
For squeeze casting process, the critical infiltration pressure p can be expressed as[16]
(2)
where p is the critical infiltration pressure, ρ is the density of liquid, u is the average velocity of liquid, η is the dynamics viscosity of liquid metal, L is the infiltration depth, de is the equivalent aperture of the porous perform, σlv is the surface tension force of liquid metal, ε is the porosity and θ is the contact angle.
The combination of ZnO particulates with high activity and large specific surface area and molten 6061 aluminum alloy facilitates the decrease of the critical infiltration pressure p, which leads to the decrease of the contact angle θ. This indicates that the coating of whiskers can improve the interface wettability. It is attributed to the reaction between ZnO and molten aluminum during squeeze casting. The interface reaction equation can be written as:
3ZnO+2Al=Al2O3+3Zn (3)
The increase of wettability can improve the interface bonding strength in Al18B4O33w/ZnO/6061Al composites.
3.3 Microstructure of Al18B4O33w/6061Al composites and Al18B4O33w/ZnO/6061Al
SEM images of the distribution of whiskers in Al18B4O33w/6061Al and Al18B4O33w/ZnO/6061Al composites are shown in Fig.4. The composites were prepared using semi-solid mechanical stirring technique at stirring temperature of 610 ℃ for 30 min and at a stirring rate of 300 r/min. It is seen from Fig.4(a) that the Al18B4O33w/6061Al composite has experienced a severe interfacial reaction during high temperature stirring, resulting in the formation of fragile spinelle (MgAl2O4) phase at the interface[17]. The reaction equations can be concluded as follows:
Al18B4O33+4Al=11γ-Al2O3+4B (4)
γ-Al2O3+Mg+[O]=MgAl2O4 (5)
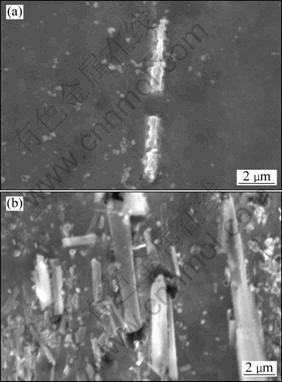
Fig.4 SEM images showing distribution of whiskers in composites: (a) Al18B4O33w/6061Al; (b) Al18B4O33w/ZnO/ 6061Al
It has been proved that the interfacial reaction product in a Al18B4O33w/ZL109Al composite is MgAl2O4[17], which is a fragile phase and harmful to aging strengthening and mechanical properties of the composites. With the appearance of the reaction, the structure of the whiskers is damaged, such as the uniformity of surface flatness and elastic modulus[18], so the composition at the interface no longer distributes homogenously and the properties of the composite are decreased. At the same time, it can be seen from the Fig.4(a) that little whisker is observed in the composite, indicating that only part of the whiskers have been stirred into the molten 6061Al due to the poor wettability between the uncoated whisker and molten 6061Al. On the contrary, no evident interfacial reaction is found at the Al18B4O33w/ZnO/6061Al composite, as shown in Fig.4(b). The whiskers have been stirred into the composite completely and uniformly distribute in the composite compared with the A18B4O33w/6061Al composite. Based on the discussion mentioned above, it can be concluded that the coating treatment of whisker can improve the wettability between whisker and matrix and reduce the interfacial reaction effectively.
The properties of the whisker reinforced aluminum matrix composites fabricated by semi-solid stirring technique are generally determined by stirring parameters such as stirring temperature, stirring time and stirring rate. In this work, the effects of stirring temperature and stirring time on the distribution of whiskers and the amount of whiskers stirred into the composites were studied. The SEM images of the whiskers distribution at different stirring temperatures (stirring time is 30 min, stirring rate is 300 r/min ) and different stirring time(stirring temperature is 610 ℃, stirring rate is 300 r/min) are shown in Fig.5 and Fig.6, respectively.
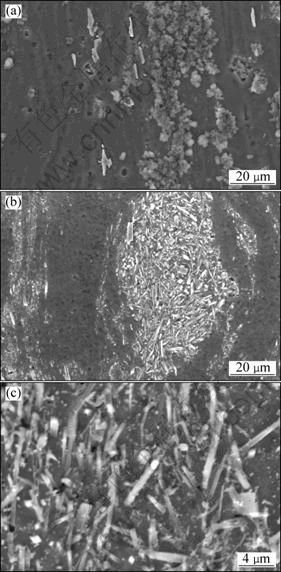
Fig.5 SEM images of distribution of whiskers in composites at different stirring temperatures: (a) 650 ℃; (b) 630 ℃; (c) 610 ℃
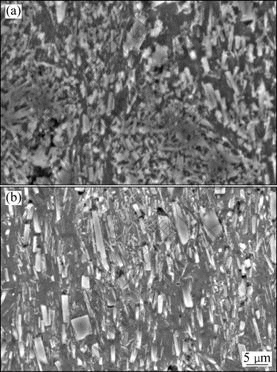
Fig.6 SEM images of distribution of whiskers in composites for different stirring time: (a) 15 min; (b) 30 min
Fig.5 reveals that the amount of whiskers stirred into the composites increases with the decrease of stirring temperature. Only a few whiskers are found in the composite at the stirring temperature of 650 ℃, meanwhile, the amount of whiskers in the composite at stirring temperature of 630 ℃ is more than that at stirring temperature of 610 ℃, but the whiskers agglomerate in the composite at stirring temperature of 630 ℃. When the temperature decreases to 610 ℃, the whiskers distribute uniformly in the composite. It is known that the viscosity of the semi-solid slurry decreases with the decrease of temperature. When the stirring temperature is 610 ℃, the semi-solid slurry has a lower viscosity and can provide a higher driving force for the movement of the whiskers, which results in a uniform distribution of the whiskers in the composite.
Fig.6 shows the distribution of the whiskers in the composites with different stirring time. It is seen that prolonging time is beneficial to the distribution of the whiskers, but the properties of the composites will be deceased because of the oxidation of the matrix in a longer time stirring. So it is very important to choose an appropriate stirring time.
3.4 Tensile properties of Al18B4O33w/6061Al composites
The detailed mechanical properties, such as ultimate strength and elastic modulus are shown in Table 1.
Table 1 Tensile properties of 6061 aluminum alloy and composites
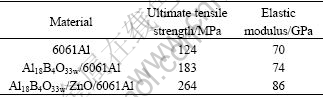
In Table 1, no evident changes in elastic modulus can be found between 6061Al and Al18B4O33w/6061Al composite because the amount of the whisker in the Al18B4O33w/6061Al composite is very low (less than 2%), as shown in Fig.4(a). The elastic modulus of the Al18B4O33w/ZnO/6061Al composite is improved obviously due to the larger amount of the whisker (about 5%) in the Al18B4O33w/ZnO/6061Al composite. The ultimate tensile strength of the Al18B4O33w/6061Al composite is higher than that of 6061Al alloy, and the ultimate tensile strength of the Al18B4O33w/ZnO/6061Al composite is increased obviously compared with that of the Al18B4O33w/6061Al composite. These results show that the surface treatment of whisker can improve the properties of aluminum borate whisker reinforced aluminum matrix composite, because coating treatment of whiskers not only enhances the wettability between whisker and matrix but also decreases the damage of the whisker caused by the interfacial reaction between whisker and matrix.
It should be specially mentioned that there are many factors influencing the mechanical properties of the composites, such as the fracture of whiskers during stirring and extrusion, uniformity of whiskers in the composite and the oxidation of matrix during stirring. These problems will be studied in the future study.
4 Conclusions
1) The surface of Al18B4O33w can be coated with ZnO by precipitation process. Coating treatment of whiskers can reduce interfacial reaction effectively and improve the wettability between whisker and matrix.
2) The Al18B4O33w/ZnO/6061Al composites can be fabricated successfully by semi-solid mechanical stirring technique, in which the stirring time is 30 min, the stirring temperature is 610 ℃ and the stirring rate is 300 r/min. The Al18B4O33 whiskers distribute uniformly in the composite.
3) ZnO coating on the surface of the Al18B4O33 whiskers can obviously enhance the properties of Al18B4O33w/ZnO/6061Al composites.
References
[1] HU J, WU P L, KONG L C, LIU G. The effect YAG laser surface treatment on corrosion resistance of Al18B4O33w/2024Al composite [J]. Mater Lett, 2007, 61: 5181-5183.
[2] SUGANAMA K, FUJITA N, SUZUKI N, NIIHARA K. Aluminum composites reinforced with a new aluminum borate whisker [J]. J Mater Sci Lett, 1990, 9: 633-635.
[3] FEI W D, LI Y B. Effect of NiO coating of whisker on tensile strength of aluminum borate whisker-reinforced aluminum composite [J]. Mater Sci Eng A, 2004, 379: 27-32.
[4] YAO L J, FUKUNAGA H. TEM study on the interfacial reaction of Al18B4O33/Al composites [J]. Scripta Mater, 1997, 37: 1267-1271.
[5] YUE H Y, FEI W D, WANG L D, LI Z J. An aluminum borate whisker-reinforced aluminum matrix composite with high plasticity [J]. Mater Sci Eng A, 2006, 430: 260-265.
[6] PENG L M, LI X K, LI H. Synthesis and microstrutural characterization of aluminum borate whiskers [J]. Ceram Int, 2006, 32: 365-368.
[7] TU J P, PAN J, MATSUMURA M, FUKUNAGA H. The solid particle erosion behavior of Al18B4O33w whisker-reinforced AC4C Al alloy matrix composites [J]. Wear, 1998, 223: 22-30.
[8] DING D Y, RAO J C, WANG D Z, MA Y Z, GENG L, YAO C K. Sol-gel alumina coatings for whisker reinforced metal matrix composites [J]. Mater Sci Eng A, 2000, 297: 138-141.
[9] SASAKI G, WANG W G, HASEGAWA Y. Surface treatment of Al18B4O33 whisker and development of Al18B4O33w/ZK60 magnesium alloy matrix composite [J]. J Mater Process Tech, 2007, 287: 429-432.
[10] YUE H Y, FEI W D, LI Z J, WANG D L. Effects of ZnO coating on the wettability and tensile properties of aluminum borate whisker-reinforced aluminum composite [J]. Mater Sci Eng A, 2006, 441: 197-201.
[11] GUAN R G, WEN J L, WANG S C, LIU X H. Microstructure behavior and metal flow during continuously extending-extrusion forming of semisolid A2017 [J]. Transactions of Nonferrous Metals Society of China, 2006, 16: 382-386.
[12] LOU S J, SHAN W W. Steady state rheological behavior of semi-solid ZK60-RE magnesium alloy during compression [J]. Transactions of Nonferrous Metals Society of China, 2007, 17: 974-980.
[13] VIEIRA E A, FERRANTE M. Prediction of rheological behavior and segregation susceptibility of semi-solid aluminum-silicon alloys by a simple back extrusion test [J]. Acta Mater, 2005, 53: 5378-5386.
[14] GEN S, MAKOTO Y, NOBUYUKI F, TOSHIO F. Modeling of compocasting process and fabrication of AZ91D magnesium alloy matrix composites [J]. J Mater Process Tech, 2002, 130: 151-155.
[15] BALASIVANANDHA P S, KARUNAMOORTHY L, KATHIRESAN S. Influence of stirring speed and stirring time on distribution of particles in cast metal matrix composite [J]. J Mater Process Tech, 2006: 268-273.
[16] YANG H L, ZHANG Z L, OHNAKA I. Structure evolution and compressive behavior of semi-solid Al-Si hypoeutectic alloy with re-melting heat treatment[J]. J Mater Process Tech, 2004, 151: 155-164.
[17] BI G, WANG H W, WU R J. Interfacial reaction of ABOw/ZL109Al composites [J]. Mater Eng, 2000(1): 27-30. (in Chinese)
[18] DING D Y, ZHANG W L, WANG D Z. Study on interfacial modification of ABOw/6061Al composites [J]. J Comp Mater, 2000, 17(2): 34-37. (in Chinese)
Foundation item: Project(2006CB605203-3) supported by the National Basic Research Program of China
Corresponding author: GENG Lin; Tel: +86-451-86413907; E-mail: genglin@hit.edu.cn
DOI: 10.1016/S1003-6326(09)60145-X
(Edited by FANG Jing-hua)