文章编号:1004-0609(2013)04-1107-07
采用HBL101萃取石煤高酸浸出液中的钒
李青刚,许 亮,齐兆树,莫兴德,廖宇龙
(中南大学 冶金科学与工程学院,长沙 410083)
摘 要:针对现行石煤提钒萃取工艺及研究现状,提出采用新型萃取剂HBL101从石煤高酸浸出料液中直接萃取钒的方案,考察料液的酸度、料液电位、萃取时间、相比以及温度对萃取率的影响,绘制HBL1010萃取等温曲线。结果表明:在料液酸度为1.458 mol/L,萃取温度为35~45 ℃,萃取时间为10min,相比O/A=1/1(油相与水相体积比)的条件下,钒的单级萃取率达到95%以上。三级逆流萃取实验结果显示,钒的萃取率达到99.7%以上。采用NaOH对负载有机相进行反萃,反萃液经调节pH后直接加入NH4Cl沉钒,得到的五氧化二钒纯度达到98.68%以上。
关键词:石煤;钒;萃取;HBL101
中图分类号:TF841.1 文献标志码:A
Extraction of vanadium from high acid leaching solution of
stone coal by HBL101
LI Qing-gang, XU Liang, QI Zhao-shu, MO Xing-de, LIAO Yu-long
(School of metallurgical Science and Engineering, Central South University, Changsha 410083, China)
Abstract: A new extractant HBL101 was used to directly extract vanadium from high acid leach solution of stone coal. The effects of acidity and potential of feed, time, phase ratio and temperature on the extraction of vanadium were investigated. The extraction distribution isotherms of vanadium were plotted. The extraction distribution isotherm was also obtained. The results show that the extraction of vanadium from the solution with 1.458 mol/L [H+] reaches 95% in single stage with A/O ratio of 1:1 (volume ratio of oil phase to aqueous phase) at 35-45 ℃ for 10 min. In three-stage counter current test, the extraction rate of vanadium is 99.7%. The loaded organic can be easily stripped using NaOH solution. After pH adjustment, the strip liquor is used to precipitate vanadium by adding NH4Cl. The final product of V2O5 with purity of 98.68% can be obtained.
Key words: stone coal; vanadium; extraction; HBL101
基金项目:国家“十二五”科技支撑计划资助项目(2012BAB07B05)
收稿日期:2011-06-20;修订日期:2012-10-31
通信作者:李青刚,副教授,博士;电话:0731-88830742;E-mail: xlshlqg@csu.edu.cn
我国石煤提钒工艺起步于20世纪70年代末期,经过30年的发展,目前在钒行业中已占据重要的地位。据统计,目前石煤提钒的产量已达到我国钒总产量的45%左右。近年来,由于钒的市场价格急剧下降,环境要求日益严格,生产成本较高,大部分石煤提钒厂处于停产状态,仍在生产的少数几家也处于亏本或持平状态,因此技术改革、降低生产成本迫在眉睫。目前石煤提钒的生产工艺主要有:钠化焙烧、钙化焙烧、酸浸萃取、碱法工艺等。钠化焙烧工艺对环境造成巨大破坏,在我国很多地方已禁止使用。钙化焙烧由于技术的原因,目前在国内还没有产业化的先例。碱法工艺对矿石适应性差,目前国内只有两家工厂采用。酸浸萃取工艺具有钒的回收率高、可自动化操作的特点,应用广泛,成为目前石煤提钒的主流工艺。
当前国内萃取钒的工业中常用的萃取剂有碱性萃取剂、中性萃取剂、酸性萃取剂等,其中应用较为成熟的是酸性磷类萃取剂P204[1]。在P204萃取石煤酸浸液的钒之前一般需要用碱中和石煤酸浸出液中的酸,再用硫代硫酸钠还原溶液中高价态的钒,由于料液的中的酸经中和后减少,很难循环使用,因此试剂消耗量大[2-8]。伯胺N1923萃取钒(Ⅴ),在pH值为2时,钒(V)萃取率能达到95%以上,而pH大于6时萃取率不到35%[9-10]。刘波等[11]采用N263从钒(Ⅴ)溶液中回收钒(Ⅴ),研究发现萃取料液的pH值控制在5~7时,萃取率达90%以上。张云等[12]在石煤酸浸液中采用三正辛胺萃取钒(Ⅴ),并以TBP为协萃剂,结果发现在pH值为2~3时萃取速度快,萃取率大于98%。伯胺N1923、N263和三正辛胺用于萃取钒(V)时,对溶液的pH要求比较苛刻,工业上一般不采用。姚宝书[13]采用TBP对偏钒酸铵进行萃取研究,发现在浓度为0.5 mol/L NH4VO3的HCl溶液中,O/A=1/1、室温下,萃取率可达98%以上,关于其工业应用未见报道。沈明伟等[14]研究了P507分离钒(Ⅳ)、钼(Ⅵ),发现在用P507+磺化煤油组成的有机相萃取石煤酸性浸出液中的钒(Ⅳ)的同时,溶液中的钼也被萃取,且常温下,O/A=1/2时,经5级逆流萃取,钼(Ⅵ)、钒(Ⅳ)的萃取率均达到98%以上。P507对钒(Ⅳ)、钼(Ⅵ)的选择性较差,因此难以应用于工业生产中。刘玉国等[15]研究了P538环己烷溶液萃取硫氰酸钒(Ⅴ)的机理,研究发现在温度为20 ℃的条件下,萃取机理为
离子与萃取剂电离出的H+交换,萃合物的组成中n(
):n(HA-)=1:1,但其萃取效果并未见详细报道。KIM等[16]报道了采用乙酰丙酮从废催化剂苏打浸出液中萃取钼(Ⅵ)、钒(Ⅴ)的研究,钒(Ⅴ)的萃取率接近100%。但没有关于该研究成果更进一步的详细报道。
综上所述,目前钒萃取的研究及工业生产上存在工艺流程长、循环利用效果差、生产成本高、萃取剂选择性差、溶液的酸碱度要求严格等不足。此外,未见从高酸浸出液中直接萃取钒的报道。为了克服上述不足,同时解决高酸条件下萃取钒的问题,本文作者首次提出了在不对石煤高酸浸液进行中和处理的情况下,用氧化剂将高酸溶液中低价态钒氧化为钒(Ⅴ),然后用肟类萃取剂HBL101直接从高浓度的硫酸浸出溶液中选择性萃取钒;其中萃余液的酸度不降低,可返回用于浸出;减少了P204萃取工艺中浸出液的中和、还原和反萃液氧化等工序,降低了试剂的消耗,节约了生产成本,提高了生产效率。肟类萃取剂常用于从水溶液中萃取铜、钴、镍等,其用于萃取钒曾有学者研究。ZENG等[17]进行了用肟类萃取剂LIX63从酸性溶液中萃取回收钼(Ⅵ)、钒(Ⅴ)的研究,结果显示,在pH值为1~2时该萃取剂可以从含Fe的溶液中选择性萃取钼(Ⅵ)、钒(Ⅴ),其研究也停留在酸度较低的条件下,未见高酸条件下萃取钒研究的报道。
1 实验
1.1 实验试剂与设备
1.1.1 实验试剂
萃取剂主要有HBL101,这是一种肟类螯合萃取剂,国内某厂提供;稀释剂为磺化煤油。
料液为国内某公司提供的高浓度的石煤硫酸浸出液,料液酸度为1.458 mol/L,在本实验中提到的酸度均为H+浓度,其单位均为mol/L,其成分见表1。
表1 料液各组分的浓度
Table 1 Chemical components of feed solution (g/L)
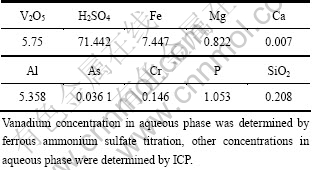
1.1.2 实验设备
125 mL/250 mL梨型分液漏斗,康氏振荡器,pH/ORP-4571酸度计/氧化还原电位计,电感耦合等离子体发射光谱仪。
1.2 实验原理
由于萃取剂是肟类螯合萃取剂,被萃取的金属阳离子与HL作用生成螯合物MLn,进入有机相生成萃合物,其反应方程如下:
→
(1)
负载有机相反萃采用NaOH溶液,其中Na+与萃合物中的
交换,Na+进入有机相发生反萃反应,其反应方程式如下:
→
(2)
1.3 实验方法
(1) 料液预处理:实验前将沉淀过滤后,向料液中加入氯酸钠进行氧化,氧化时搅拌30 min,搅拌结束后静置8~24 h。(2) 有机相的配制:按萃取剂与稀释剂体积比为1:9,量取有机相于烧杯内,充分搅拌,使其混合均匀即得所需的有机相。(3) 萃取实验:先量取一定体积有机相装入125 mL分液漏斗,再量取需要量的料液,加入装有有机相的分液漏斗,根据要求的萃取条件,将分液漏斗放入水浴恒温振荡器中匀速振荡,根据实验要求的时间等条件来控制振荡过程,振荡结束后,取出分液漏斗,置于萃取架分层。分析萃余液中各元素的浓度,计算萃取率(E)。
(3)
式中:[Me]a为萃余液中离子浓度,g/L;[Me]o为料液中离子浓度,g/L;Va为萃余液的体积,L;Vo为料液的体积,L。
2 结果与讨论
2.1 料液酸度对各元素萃取率的影响
实验料液:用NaClO3将料液氧化到电位950 mV,静置24 h以上开始实验,料液中V2O5浓度5.75 g/L。
萃取条件如下:O/A为1/2,萃取时间为10 min,分相时间3 min,温度为28 ℃,水相体积为60 mL,实验结果如图1所示。
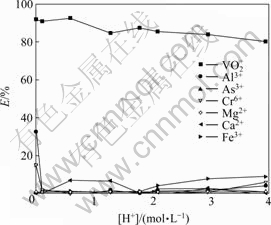
图1 酸度对各元素萃取率的影响
Fig. 1 Effect of [H+] on extraction of elements
从图1可看出,溶液酸度对钒的萃取率影响不显著。随着酸度的增加,钒的萃取率呈略微下降的趋势,在O/A=1/2、酸度为4 mol/L时钒的单级萃取率仍然 达到80%以上。从萃取原理Mn+(aq)+nHL(org)= MLn(org)+nH+(aq)看出,在高酸条件下钒与萃取剂的结合能力大于H+及其他金属杂质离子的结合能力。随着酸度的降低,从图1可以出,少量Fe、Al离子被萃取,分析认为,酸度的降低使萃取平衡反应向右移动,有利于萃取金属离子,Fe3+、Al3+与萃取剂结合能力随着酸度的降低而增强,故有少部分Fe3+、Al3+在低酸条件下被萃取。其中,Ca2+在酸度为0.5~1.5 mol/L时,也有少部分被萃取,但Ca2+的总浓度为0.007 g/L,可能是由于存在分析误差,使其萃取率接近8%。而在各酸度条件下钒的萃取率均在80%以上,而其他杂质的萃取率较低,说明该萃取剂在0~4 mol/L酸度条件下对钒(Ⅴ)具有较好的选择性,可以直接从高酸溶液中萃取钒(Ⅴ),同时达到与Fe3+、Al3+等杂质分离的 效果。
2.2 料液电位对钒、铁、钙、镁萃取率的影响
实验料液:用NaClO3将料液氧化到电位分别为445、578、605、782、884、956、1 072、1 135 mV,静置24 h后再萃取,料液酸度为1.458 mol/L。
萃取条件如下:O/A为1/1,萃取时间为10 min,分相时间3 min,温度为28 ℃,水相体积为50 mL,考察溶液电位对萃取的影响,实验结果如图2所示。
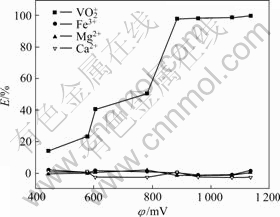
图2 料液电位与萃取率的关系
Fig. 2 Effect of potential of feed solution on extraction of metals
由图2可看出,钒的萃取率随电位的增大呈上升趋势。且当电位在850~900 mV时,钒的萃取接近100%,而高于该电位范围时,钒的萃取率基本不发生改变。根据钒水溶液φ—pH图[18]可知,在溶液酸度为1 mol/L、电位在900 mV以上钒是以
形式存在。结合图2可知,在电位低于850 mV时,钒大部分是以
和VO2+阳离子形式存在,随着电位的升高,溶液中
占的比例升高,而萃取率也随着电位的增大而升高,说明该萃取剂对
具有较好的萃取效果。随着电位的变化,溶液中Fe的价态也在变化,在低电位时,Fe以Fe2+形式存在,随着电位的升高,由Fe2+变成Fe3+,而Fe的萃取率不管电位如何变化几乎为零。溶液中的Ca2+、Mg2+的价态不随电位的变化而发生改变,其萃取率几乎都为零,实验结果表明该萃取剂对
具有较高的选择性,避免了Fe2+、Fe3+、Mg2+、Ca2+等离子给湿法冶金分离带来的困扰。
2.3 萃取时间对钒和铁萃取率的影响
实验料液:用NaClO3将料液氧化到电位880 mV,静置24 h开始实验,料液[H+]为1.458 mol/L,料液中V2O5浓度为5.75 g/L。在本文作者的后续实验的料液均与本实验的相同。
萃取条件如下:O/A为1/1,分相时间为3 min,温度为28 ℃,水相体积为50 mL,实验结果如图3所示。
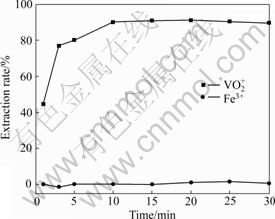
图3 萃取时间与钒萃取率的关系
Fig. 3 Effect of time on extraction of metals
从图3可看出,在10 min内,
萃取率随着时间的延长而提高,当萃取时间超过10 min时萃取率基本不变,即该萃取剂萃取钒在10 min左右达到了萃取平衡,故选择最佳萃取时间为10 min。而不管时间如何变化铁萃取率几乎为零,由于料液经过预处理,料液中的铁为Fe3+,说明该萃取剂能有效地分离
和Fe3+。
2.4 萃取相比对钒萃取率的影响
萃取条件如下:萃取时间为10 min,温度为28 ℃,分相时间为3 min,有机相体积为30 mL,实验结果如图4所示。
从图4可以看出,随着O/A的减小钒萃取率降低,对于含10%的肟类萃取剂,O/A=1/1时其单级萃取率在95%以上,相比越小,水溶液中的钒(Ⅴ)含量越高。为了保证浸出液的萃取率,应采取相比1/1。在实际生产中,采用相比1/1,通过改变水相和有机相流量来保证有机相的饱和萃取。
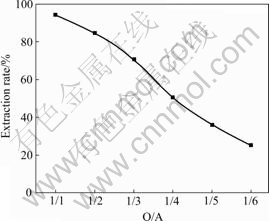
图4 相比对钒萃取率的影响
Fig. 4 Effect of O/A on extraction of vanadium
2.5 萃取温度对钒和铁萃取率的影响
萃取条件如下:O/A=1/1,萃取时间为10 min,分相时间为3 min,水相体积为50 mL,实验结果如图5所示。
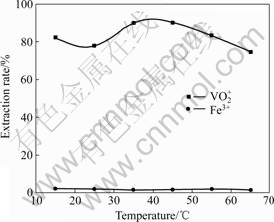
图5 温度对萃取的影响
Fig. 5 Extraction of temperature on extraction of vanadium
从图5可看出,肟类萃取剂在低温下其萃取钒(Ⅴ)的效果并没有达到最佳,这可能与温度低萃取反应的活性低有关。35~45 ℃时,萃取率达到最高,随着温度升高萃取率反而降低。因为温度过高,肟类萃取剂会发生突变[19],有机相的挥发增大,造成有机相的损失增大。同时温度越高对能源的需求也越多。故萃取钒的最佳温度应该为35~45 ℃。不管温度如何变化,Fe的萃取率几乎为0,说明温度改变不会使该萃取剂萃取铁。
2.6 钒萃取等温曲线
在相比O/A=1/1、温度为28 ℃、萃取时间为10 min时,采用相比法测定萃取饱和量,绘制萃取等温曲线如图6所示。
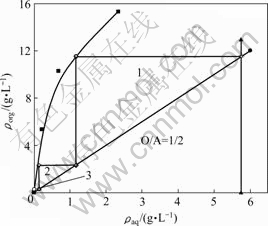
图6 钒(Ⅴ)的萃取等温曲线
Fig. 6 Isotherm extraction curves of vanadium(V)
从图6可以看出,在有机组成为10%HBL101+ 90%磺化煤油的饱和萃钒量(V2O5)为15.28 g/L左右。由图6可知,钒(Ⅴ)的萃取等温线的斜率较大,说明钒(Ⅴ)在该萃取体系中萃取性能较好。依照逆流萃取原理,绘制马克凯勒—齐利图,设萃余液中钒(Ⅴ)浓度为0.03 g/L时,按照相比O/A=1/2操作线,绘制 钒(Ⅴ)的操作曲线,从图6可以看出,通过三级逆流萃取,水相中的钒(Ⅴ)浓度可以降低至0.03 g/L。因此,该萃取体系需经过三级逆流萃取提取钒(Ⅴ)。
2.7 三级逆流实验
在本实验中,进行了6组三级逆流萃取实验,操作流程图如图7,图中A代表水相,O代表有机相,方框代表梨形分液漏斗。萃取条件如下:t=30 ℃,O/A=1/2.4,接触时间10 min,分相时间3 min,V0=30 mL。图7中,A1、A2、A3、A4、A5、A6分别表示三级迸流萃取后的萃余液,O1、O2、O3、O4、O5、O6分别表示三级迸流萃取的负载有机相。实验结束后,用硫酸亚铁铵滴定法分析A1、A2、A3、A4、A5、A6中的钒浓度,用ICP分析A6中各杂质金属离子的浓度。实验结果分别见表2和表3。由表2可知,采用三级逆流萃取,萃余液中钒浓度低于0.02 g/L,钒的萃取率达到99.7% 钒具有较高的选择性。
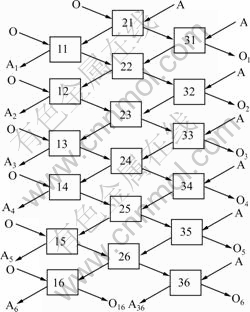
图7 三级逆流萃取模拟实验流程
Fig. 7 Flowchart of simulated three-stages counter current extraction
表2 钒的三级逆流模拟试验结果
Table 2 Vanadium of simulated three-stage counter current extraction
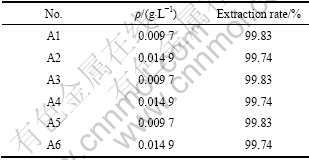
表3 A6中各种杂质金属离子的实验结果
Table 3 Metals of simulated counter current extraction in A6
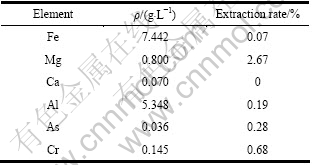
将按照图7所示操作流程图实验得到的负载有机相O1、O2、O3、O4、O5、O6混合后,用1 mol/L的NaOH按O/A=1/1,在室温下反萃30 min得到的反萃液调节pH为8.8后采用铵盐直接沉钒,得到的偏钒酸铵烘干后煅烧得到V2O5,采用ICP分析V2O5中各杂质含量,结果见表4。
表4 五氧化二钒中主要杂质元素的质量分数
Table 4 Major impurity contents in V2O5
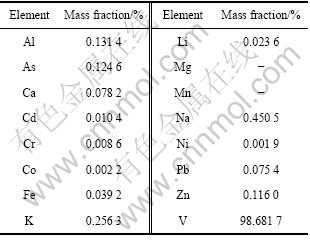
从表4可以看出,负载有机相直接反萃后得到反萃液,反萃液直接沉钒得到的产品纯度达到98.68%。该萃取剂不萃取料液中的Fe等元素,所得萃余液的钒(Ⅴ)含量均较低,且分相速度快,得到的反萃液可直接沉钒,最终得到的产品纯度达到98.68%以上。
3 结论
1) HBL101能在酸度为0~4 mol/L的范围内萃取
,且不萃取Fe3+、Al3+、Ca2+、Mg2+等杂质金属,具有较优良的选择性。
2) HBL101萃取石煤高酸溶液中V2O5的最佳萃取条件如下:温度35~45 ℃,萃取时间10 min,O/A=1/1,在该条件下钒(Ⅴ)的单级萃取率达到95%以上。
3) 通过HBL101萃取等温曲线求得逆流萃取的理论级数为3级,经3级逆流萃取,钒的萃取率达到99.68%以上。
4) HBL101不需要调节酸度,可直接萃取料液,节约了生产成本,降低了环境污染。其萃取饱和量相比P204大,达到15.28 g/L,该萃取剂应用于工业生产能有效地避免P204萃取工艺中的中和调酸、还原等步骤,且该萃取剂
具有较高的选择性,避免了湿法冶金中Fe3+的干扰。负载有机相反萃后,反萃液经调节pH值后,可直接用氯化铵沉钒,同样也避免了P204萃取工艺中反萃液氧化后沉钒。
REFERENCES
[1] 李尚勇, 谢 刚, 俞小花. 从含钒的浸出液中萃取钒的研究现状[J]. 有色金属, 2011, 63(1): 100-104.
LI Shang-yong, XIE Gang, YU Xiao-hua. Vanadium extraction with acidic medium[J]. Nonferrous Metals, 2011, 63(1): 100-104.
[2] 鲁兆伶. 用酸法从石煤中提取五氧化二钒的试验研究与工业实践[J]. 湿法冶金, 2002, 21(4): 175-183.
LU Zhao-ling. Investigation and industrial practice on extraction of V2O5 from stone coal containing vanadium by acid process[J]. Hydrometallurgy of China, 2002, 21(4): 175-183.
[3] 王晓丹, 朱 云. 制酸废催化剂回收钒[J]. 有色金属, 2010, 62(4): 62-64.
WANG Xiao-dan, ZHU Yun. Vanadium recovery from spent acid-making catalyst[J]. Nonferrous Metals, 2010, 62(4): 62-64.
[4] 胡建锋, 朱 云. P204萃取硫酸体系中钒的性能研究[J]. 稀有金属, 2007, 31(7): 367-370.
HU Jian-feng, ZHU Yun. Extraction of vanadium by P204 from sulfuric acid solution[J]. Chinese Journal of Rare Metals, 2007, 31(7): 367-370.
[5] LI Xing-bin, WEI Chang, DENG Zhi-gan, LI Min-ting, LI Cun-xiong, FAN Gang. Selective solvent extraction of vanadium over iron from a stone coal/black shale acid leach solution by D2EHPA/TBP[J]. Hydrometallurgy, 2010, 105: 359-363.
[6] 李兴彬, 魏 昶, 樊 刚, 邓志敢, 李旻廷, 李存兄. 溶剂萃取-铵盐沉钒法从石煤酸浸液中提取五氧化二钒的研究[J]. 矿冶, 2010, 19(3): 49-53.
LI Xing-bin, WEI Chang, FAN Gang, DENG Zhi-gan, LI Min-ting, LI Cun-xiong. Research of vanadium pentoxide from an acid leaching solution of stone coal using solvent extraction and ammonium precipitation[J]. Mining & Metallurgy, 2010, 19(3): 49-53.
[7] 李晓健. 酸浸-萃取工艺在石煤提钒工业中的设计与运用[J]. 湖南有色金属, 2000, 16(3): 21-23.
LI Xiao-jin. Design and application of acid leaching—Extraction processing in bone coal extracting vanadium industry[J]. Hunan Nonferrous Metals, 2000, 16(3): 21-23.
[8] 曹耀华, 高照国, 刘红召, 李 琦. 萃取法从含钒酸浸液中提取钒的研究[J]. 河南化工, 2007, 24(6): 20-23.
CAO Yao-hua, GAO Zhao-guo, LIU Hong-zhao, LI Qi. Study on vanadium extraction from vanadium acid leaching solution[J]. Henan Chemical Industry, 2007, 24(6): 20-23.
[9] WANG Yu-xing, LUO Qin-ge, LIU Shu-me. A study on extraction mechanism of vanadium(Ⅴ) by primary amine N1923[J]. Natural Science Journal of Xiangtan University, 1990, 19(3): 139-146.
[10] 刘彦华, 杨 超. 用溶剂萃取法从含钒浸出液中直接沉淀钒[J]. 湿法冶金, 2010, 29(4): 263-267.
LIU Yan-hua, YANG Chao. Research on direct precipitate of vanadium in vanadiferous leaching solution[J]. Hydrometallurgy of China, 2010, 29(4): 263-266.
[11] 刘 波, 冯光熙, 黄祥玉, 张 敏. 用N263从钒溶液中回收钒[J]. 化学研究与应用, 2003, 15(1): 54-57.
LIU Bo, FENG Guang-xi, HUANG Xiang-yu, ZHANG Min. Recovery of vanadium pentoxide from contained vanadium solution with methyltri (C9-11 alkyl) ammonium chloride[J]. Chemical Research and Application, 2003, 15(1): 54-57.
[12] 张 云, 范必威, 彭达平, 陈细发. 从石煤酸浸液中萃取钒的工艺研究[J]. 成都理工学院学报, 2001, 28(1): 107-109.
ZHANG Yun, FAN Bi-wei, PENG Da-ping, CHEN Xi-fa. Technology of extracting V2O5 from the stone coal acid-leaching solution with TOA[J]. Journal of Chengdu University of Technology, 2001, 28(1): 107-109.
[13] 姚宝书. TBP萃取偏钒酸铵的条件[J]. 化学世界, 1990, 31(1): 12-14.
YAO Bao-shu. The conditions of ammonium metavanadate extraction using TBP[J]. Chemical World, 1990, 31(1): 12-14.
[14] 沈明伟, 朱昌洛, 李华伦. P507-煤油体系在钒钼萃取分离中的试验研究[J]. 矿产综合利用, 2007(4): 14-18.
SHENG Ming-wei, ZHU Chang-luo, LI Hua-lun. P507-Kerosene system in extraction separation of vanadium and molybdenum[J]. Multipurpose Utilization of Mineral Resources, 2007(4): 14-18.
[15] 刘玉国, 安 悦, 付晓东, 杨 东. P538萃取钒(Ⅳ)的研究[J]. 光谱实验室, 1998, 15(5): 32-34.
LIU Yu-guo, AN Yue, FU Xiao-dong, YANG Dong. Study on vanadium(Ⅳ) extracted by P538[J]. Chinese Journal of Spectroscopy Laboratory, 1998, 15(5): 32-34.
[16] KIM K, CHO J W. Selective recovery of metals from spent desulphurization catalyst[J]. Korean Journal of Chemical Engineering, 1997, 14(3): 162-167.
[17] ZENG L, CHENG C Y. Recovery of molybdenum and vanadium from synthetic sulphuric acid leach solutions of spent hydrodesulphurisation catalysts using solvent extraction[J]. Hydrometallurgy, 2010, 101: 141-147.
[18] POST K, RIBINS R G. Thermodynamic diagram for the vanadium–water system at 298.15 K[J]. Electrochimica Acta, 1976, 21: 401-405.
[19] BARNARD K R, TURNER N L. The effect of temperature on hydroxyoxime stability in the LIX 63–versatic 10–tributyl phosphate synergistic solvent extraction system under synthetic nickel laterite conditions[J]. Hydrometallurgy, 2011, 109: 245-251.
(编辑 龙怀中)