文章编号:1004-0609(2010)03-0565-07
钠化还原法处理高铝褐铁矿新工艺
姜 涛,刘牡丹,李光辉,孙 娜,曾精华,邱冠周
(中南大学 资源加工与生物工程学院,长沙 410083)
摘 要:开发一种处理高铝褐铁矿的新工艺。采用钠化还原?磁选法对一种铁品位为48.92%(质量分数)、Al2O3含量为8.16%(质量分数)的高铝褐铁矿进行铝铁分离研究。结果表明:当硫酸钠添加量为12%(质量分数),还原焙烧温度为1 050 ℃,焙烧时间为60 min时,焙烧产物磨至粒度小于0.074 mm的占98%;在磁场强度为0.675 T的条件下,可获得铁品位91.00%,Al2O3含量1.36%的金属铁粉,铁的回收率为91.58%,铝的脱除率为90.47%。XRD研究结果表明,在钠盐焙烧过程中,铁氧化物被还原成金属铁,大部分铝、硅矿物与硫酸钠反应生成非磁性物质铝硅酸钠,经磁选后进入非磁性物,从而实现铝铁的高效分离。
关键词:褐铁矿;钠盐;铝;还原焙烧;磁选
中图分类号:TD982 文献标识码:A
Novel process for treatment of high-aluminum limonite ore by reduction roasting with addition of sodium salts
JIANG Tao, LIU Mu-dan, LI Guang-hui, SUN Na, ZENG Jing-hua, QIU Guan-zhou
(School of Minerals Processing and Bioengineering, Central South University, Changsha 410083, China)
Abstract: A novel process was developed to treat the high-aluminum limonite ores. Al-Fe separation from a high-aluminum limonite ore with total iron grade of 48.92% and Al2O3 content of 8.16% (mass fraction) was studied by reduction roasting with addition of sodium salt followed by magnetic-separation. The results show that metallic iron powder with total iron grade of 91.00% and Al2O3 content of 1.36% is obtained when the sodium sulfate dosage is 12% (mass fraction), the roasting temperature is 1 050 ℃ and time is 60 min, and the grinding fineness is 98% ores less than 0.074 mm and the magnetic field intensity is 675 mT, then the iron recovery is 91.58%, and the removal of Al2O3 is 90.35%. The XRD results indicate that the iron oxides are transformed into metallic iron, most of the aluminiferous mineral and silicic mineral reacts with the sodium sulfate during the reduction roasting and forms sodium aluminosilicates, which enter into the nonmagnetic materials during the magnetic separation, then Al-Fe separation is realized.
Key words: limonite ores; sodium salt; aluminum; reduction roasting; magnetic separation
在我国安徽、广西、贵州等地以及毗邻的东南亚国家储有丰富的含铝褐铁矿。由于褐铁矿磁性弱,可浮性差,矿石中铁矿物与铝矿物嵌布紧密,在磨矿过程中极易泥化,而且存在大量Al3+取代Fe3+形成类质同像的结构,导致单体解离度低,难以选别,是一种典型的难选铁矿石资源[1?2]。Al2O3是高熔点酸性脉石, 当高炉炉渣中Al2O3含量超过15%,将引起炉渣熔点升高、粘度增大,使得渣铁分离困难,高炉利用系数降低[3]。因此,高炉一般要求入炉原料Al2O3含量小于2%,这就要求铁矿石Al2O3含量在2%~3%左右[4]。由于高铝褐铁矿石Al2O3含量高(>8%),而且铝铁分离困难,至今尚未得到利用,基本属于呆滞矿产资源。另一方面,我国进口铁矿中高铝矿石越来越多,如澳大利亚粉矿、印度粉矿、智利Romeral粉矿等[4?5]虽然铁品位高,但由于矿石中Al2O3含量偏高使得其应用受到限制。余永富等[6?7]提出以铁、铝和硅3种元素的含量来评价铁矿粉的质量,把降低铝、硅含量与提高铁品位放到同等重要的位置上来考虑。可见,开发高效的铝铁分离技术,实现这类高铝铁矿的综合利用,对缓解我国铁矿资源严重短缺的压力具有重要的现实意义。
目前,国内外针对铝铁分离的研究主要有选矿法和冶炼法,其中选矿法主要包括物理选矿法和化学选矿法。含铝铁矿石的物理选矿研究较多,也取得了一定的进展,主要工艺有磁化焙烧、强磁选、重选、浮选及其联合工艺等[8?10]。但是物理法只适用于结构简单的矿石,对于铝铁嵌布关系复杂的矿石铝铁分离效率低。含铝铁矿石的化学选矿以盐酸浸出法及氯化焙烧法研究最多,对于铝铁嵌布关系复杂的矿石铝铁分离效果较好[11]。本文作者[12]曾采用强磁选和磁化焙烧工艺对高铝褐铁矿进行铝铁分离研究,结果表明矿石中以类质同像形式与铁矿物共存的铝无法采用常规方法从铁矿物中分离;并研究了钠化焙烧—浸出工艺[1]对高铝铁矿石铝铁分离的影响,获得铁品位大于60%,Al2O3含量低于3%的铁精矿,但作为炼铁原料,这种铁精矿的Al2O3含量仍然偏高,只能作为配矿使用。
冶炼法是目前各国研究最多的方法,主要包括还原烧结法、熔炼法和直接还原法。美国、日本均开展了含铝铁矿还原烧结回收铁的研究,在铁的回收上取得了一定的效果,但是整体来说,流程较长,能耗大,而且铁的回收率较低[13?14]。熔炼法是将含铝铁矿石在高炉或电炉中熔炼出生铁,该方法的优点是铁的回收率高,矿石中的部分有价金属元素如钒、锰、镓也可得到综合回收利用。然而,熔炼温度需要保持在1 800 ℃左右,能耗大大增加,对设备的要求非常严格,操作也更加困难,因此,虽然熔炼法能制得生铁,但是其应用仍然受到很大的局限[15?16]。直接还原法用气体或固体还原剂在低于铁矿石软化温度下,将含铝铁矿石中的铁氧化物还原成金属铁,然后通过磁选实现铁的回收。从目前的研究现状来看,该方法存在的主要问题是铁与铝、硅的分离效果差,产品铁品位低,而且还原条件苛刻,能耗较大,难以实现工业化,因而限制了其应用,如果能进一步改善还原条件,降低焙烧能耗,提高铁与铝、硅的分离效率,无疑将为难处理铁矿的铝铁分离提供新的思路[17?18]。
综上所述,由于高铝铁矿石内部铝铁赋存关系复杂,现有的处理工艺存在铝铁分离效率低、能耗高、流程长等问题,因而这部分资源尚未得到合理有效的利用,基本属于呆滞矿产资源。本文作者采用钠化还原方法,通过添加钠盐与酸性脉石成分Al2O3和SiO2反应,破坏矿石结构,促进还原焙烧过程中铁氧化物的还原和铁晶粒长大,为铝铁分离创造条件。实现由难处理含铝铁矿石直接制备高品位金属铁粉,开发出高效的铝铁分离新工艺。
1 实验
1.1 原料性质
试验所用原料为印度尼西亚高铝褐铁矿,其主要化学成分见表1。详细物化性能见文献[1]和[12]。该矿石铁品位较低,仅为48.92%,脉石成分主要是Al2O3和SiO2,其含量分别为8.16%和4.24%,其它有害杂质硫和磷等含量均较低。
表1 原矿的主要化学成分
Table 1 Main chemical composition of raw ore (mass fraction, %)

为得到良好的还原效果,试验所用还原剂为广西烟煤,该煤固定碳含量为48.47%,挥发分含量为43.08%,灰分含量为8.45%,是一种良好的还原剂。试验中还原煤均破碎到粒度小于5 mm。硫酸钠为化学分析纯。
1.2 研究方法
试验流程包括造块、还原焙烧和磨矿磁选3个环节。原矿磨矿至粒度小于0.074 mm的粒径含量占80%,将矿与粘结剂(占原矿质量的1%)、辅助添加剂BS(占原矿质量的2.5%)及一定比例(占原矿的质量分数)的钠盐添加剂混匀、造块、干燥,然后称取一定量的干团块与还原煤混合,置于已达到预设温度的竖炉高温区内进行还原,待还原结束后取出反应罐隔绝空气冷却至室温。将已还原的团块磨矿至一定细度,采用弱磁选进行分选,所得磁性物质即为金属铁粉,非磁性物质用于回收有价元素。以铁粉全铁品位、Al2O3含量、铁的回收率和铝的脱除率作为评价指标。新工艺原则流程如图1所示。
2 结果与分析
高铝铁矿中铝的化学物相研究结果表明[1],40.44%的铝以类质同像的形式存在于铁矿物中,构成铝铁同晶替代的嵌布关系,导致单体解离困难。在铁矿石的还原过程中,碱金属能使铁氧化物的晶格点阵发生畸变,提高还原速率,促进铁原子的扩散与铁晶粒的长大。钠盐和焙烧参数是影响还原的关键,因此,本实验研究了钠盐用量、焙烧温度、焙烧时间对铝铁分离的影响。为强化还原焙烧过程中金属铁颗粒的长大,加入了一种辅助添加剂BS,其用量固定为2.5%。
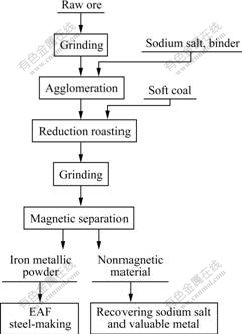
图1 钠还原法处理高铝褐铁矿新工艺原则流程图
Fig.1 Flowsheet in principle of novel process
2.1 钠盐用量的影响
本研究所用钠盐为硫酸钠,在焙烧温度1 100 ℃,焙烧时间60 min,焙烧产物磨至粒度小于0.074 mm的占98%、磁场强度0.675 T的条件下,研究了硫酸钠用量对铝铁分离的影响,结果如图2和3所示。
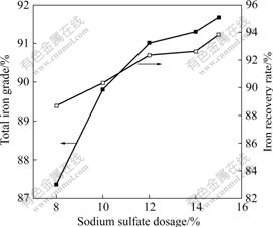
图2 硫酸钠用量对金属铁粉铁品位和铁回收率的影响
Fig.2 Effects of sodium sulfate dosage on total iron grade of metallic iron powder and recovery rate of iron
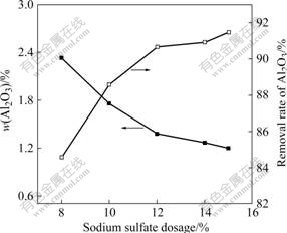
图3 硫酸钠用量对金属铁粉Al2O3含量和Al2O3脱除率的影响
Fig.3 Effects of sodium sulfate dosage on Al2O3 content of metallic iron powder and removal rate of Al2O3
由图2和3可知,随着硫酸钠用量从8%增加到15%,金属铁粉铁品位从87.36%升高到91.68%,铁的回收率从88.69%升高到93.85%;Al2O3含量从2.33%逐渐降低到1.2%,铝的脱除率则呈上升趋势。可见,硫酸钠用量增加,有利于铝铁分离。当硫酸钠用量低于10%时,金属铁粉的各项指标都不理想,而硫酸钠用量超过12%后,金属铁粉各项指标改善的幅度不大。综合考虑,硫酸钠用量选择12%为宜,此时,金属铁粉中铁品位为91.02%,铁的回收率为92.35%,Al2O3含量为1.38%,铝的脱除率为90.98%。
2.2 还原焙烧温度的影响
在硫酸钠用量12%、焙烧时间60 min、焙烧产物磨至粒度小于0.074 mm的占98%、磁场强度0.675 T的条件下,研究了还原焙烧温度对铝铁分离的影响,结果如图4和5所示。

图4 还原焙烧温度对金属铁粉铁品位和回收率的影响
Fig.4 Effects of reduction roasting temperature on total iron grade of metallic iron powder and recovery rate of iron
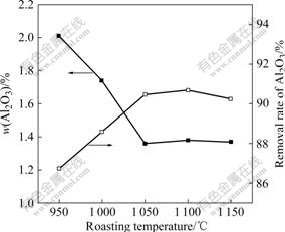
图5 还原焙烧温度对金属铁粉Al2O3含量和Al2O3脱除率的影响
Fig.5 Effects of reduction roasting temperature on Al2O3 content of metallic iron powder and removal rate of Al2O3
从图4和5可知,随着还原焙烧温度从950 ℃升高到1 100 ℃,金属铁粉铁品位从88.94%升高到91.02%,铁的回收率从89.65%升高到92.35%,当还原焙烧温度继续升高,金属铁粉铁品位和回收率均稍有降低,这是因为温度太高,铁氧化物的还原历程发生变化,FeO与脉石矿物铝、硅反应生成难还原的铁橄榄石和铁尖晶石,一定程度上阻碍了铁的还原。金属铁粉中Al2O3含量首先随温度升高从2.01%降低到1.36%,铝的脱除率从86.74%升高到90.68%,当温度超过1 100 ℃后,其值稍有降低。总体来说,当还原焙烧温度超过1 050 ℃后,金属铁粉的各项指标变化幅度均很小,因此还原焙烧温度以1 050 ℃为宜。
2.3 还原焙烧时间的影响
在硫酸钠用量12%、焙烧温度1 050 ℃、焙烧产物磨至粒度小于0.074 mm的占98%、磁场强度0.675 T的条件下,研究了还原焙烧时间对铝铁分离的影响,结果如图6和7所示。
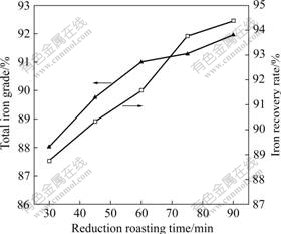
图6 焙烧时间对金属铁粉铁品位和回收率的影响
Fig.6 Effects of reduction roasting time on total iron grade of metallic iron powder and recovery rate of iron
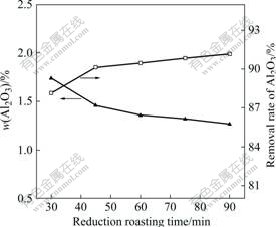
图7 还原焙烧时间对金属铁粉Al2O3含量和Al2O3脱除率的影响
Fig.7 Effects of reduction roasting time on Al2O3 content of metallic iron powder and removal rate of Al2O3
从图6和7可知,随着还原焙烧时间延长,磁性产品中铁品位和回收率均呈上升趋势,当时间为90 min时,金属铁粉中铁品位接近92%,铁的回收率达到94.37%;金属铁粉中Al2O3含量随焙烧时间延长变化幅度不大,在1.3%左右;铝的脱除率随还原焙烧时间增加呈上升趋势,当时间超过45 min后升高幅度 不大。综上所述,还原焙烧时间在60 min为宜,此时金属铁粉铁品位为91.00%,铁的回收率为91.58%,Al2O3含量为1.36%,铝的脱除率为90.47%。
高铝铁矿石钠化还原试验研究结果表明,在硫酸钠用量12%、焙烧温度1 050 ℃、焙烧时间60 min、焙烧产物磨至粒度小于0.074 mm的占98%、磁场强度0.675 T的条件下,可获得铁品位91.00%,Al2O3含量1.36%的金属铁粉,铁的回收率为91.58%,铝的脱除率为90.35%。全流程各产品的主要化学成分如表2所示。
表2 铝铁分离过程中各产品的主要化学成分
Table 2 Main chemical compositions of samples obtained during separation of aluminium and iron
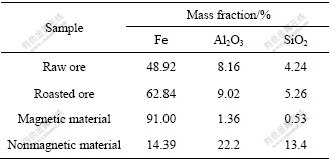
3 钠化还原过程中铝铁物相变化
为了解钠化还原焙烧—磨选过程中铝、铁的物相变化,对焙烧温度1 050 ℃,焙烧时间60 min,硫酸钠用量12%,焙烧产物磨至粒度小于0.074 mm的占98%,磁场强度0.675 T的条件下获得的焙烧矿、金属铁粉及非磁性物进行XRD分析,结果如图8~10所示。为便于比较,同时将原矿的XRD谱列出,如图11所示。

图8 焙烧矿的XRD谱
Fig.8 XRD pattern of roasted ore
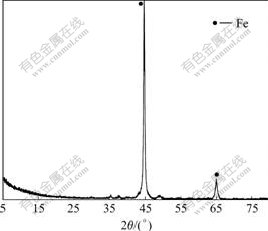
图9 金属铁粉的XRD谱
Fig.9 XRD pattern of iron metallic powder
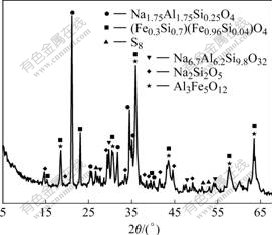
图10 非磁性物的XRD谱
Fig.10 XRD pattern of nonmagnetic material

图11 高铝褐铁矿原矿的XRD谱
Fig.11 XRD pattern of raw ore
图8所示为焙烧矿的XRD谱。由图8可知,原矿经钠盐还原焙烧后,铁氧化物针铁矿、磁铁矿、赤铁矿被还原为金属铁,其它物相主要是铝硅酸钠,这是铝、硅矿物与硫酸钠的反应产物,其余脉石矿物还有铁橄榄石、Al3Fe5O12、FeS及S。这是由于当还原温度较低时(<700 ℃),铁氧化物主要停留在FeO的稳定阶段,此时部分铝、硅矿物与FeO反应分别生成了铁橄榄石和Al3Fe5O12;另一方面,硫酸钠在低温下能被还原成单质硫和Na2S,在Na2S、FeO同时存在的条件下,Al2O3、SiO2均能与它们自发反应生成FeS。焙烧矿经弱磁选分选后,金属铁进入磁性物,而其余物相均进入非磁性物,从而成功实现了铝铁的分离,如图9~10所示。金属铁粉铁品位得到了大幅度提升,从62.84%升高到91.00%,Al2O3含量从9.02%降到1.36%;而铝、硅矿物均在非磁性物中富集。氧化铝在非磁性物中的富集为Al2O3的综合回收提供了有利条件。
4 结论
1) 开发了钠化还原法处理高铝褐铁矿的新工艺。还原分选试验结果表明,在硫酸钠用量12%、焙烧温度1 050 ℃、焙烧时间60 min、焙烧产物磨至粒度小于0.074 mm的占98%、磁场强度0.675 T的条件下,可获得铁品位91.00%,Al2O3含量1.36%的金属铁粉,铁的回收率为91.58%,铝的脱除率为90.47%。
2) 在钠盐焙烧过程中,铁氧化物被还原成金属铁,经弱磁选后进入磁性物,大部分铝、硅矿物与硫酸钠反应生成不溶于水的非磁性物质铝硅酸钠,少量铝、硅矿物与FeO反应分别生成铁橄榄石和Al3Fe5O12,经磁选后进入非磁性物。
REFERENCES
[1] 李光辉, 周太华, 刘牡丹, 姜 涛, 范晓慧. 难处理褐铁矿铝铁分离新工艺及机理研究[J]. 中国有色金属学报, 2008, 18(11): 2087?2093.
LI Guang-hui, ZHOU Tai-hua, LIU Mu-dan, JIANG Tao, FAN Xiao-hui. A novel process and mechanisms of aluminum-iron separation of refractory limonite ore[J]. The Chinese Journal of Nonferrous Metals, 2008, 18(11): 2087?2093.
[2] TROLORD F, TARDY Y. A model of Fe3+ -kaolinite, Al3+ - goethite, Al3+ - hematite equilibria in laterites[J]. Clay Minerals, 1989, 24(1): 1?21.
[3] 陈培敦, 孙守建, 赵树民. 高Al2O3炉渣对高炉生产的影响[J]. 山东冶金, 2005, 27(1): 12?13.
CHEN Pei-dun, SUN Shou-jian, ZHAO Shu-min. Influence of slag with high content of Al2O3 on blast furnace production [J].Shangdong Metallurgy, 2005, 27(1): 12?13.
[4] 刘南松. 关于铁矿石优化利用的探讨[J]. 冶金矿山设计与建设, 1996(2): 36?41.
LIU Nan-song. Study on optimization of iron ore utilization[J]. Metallurgy Mine Design and Construction, 1996(2): 36?41.
[5] 焦玉书, 周 伟. 世界铁矿资源开发利用和我国进口铁矿石的发展态势[J]. 中国冶金, 2004(11): 13?18.
JIAO Yu-shu, ZHOU Wei. Utilization of world iron resources and the development status of import iron ore in China[J]. Chinese Metallurgy, 2004(11): 13?18.
[6] 余永富, 张汉泉. 我国钢铁发展对铁矿石选矿科技发展的影响[J]. 武汉理工大学学报, 2007, 29(1): 1?7.
YU Yong-fu, ZHANG Han-quan. Influence of domestic iron and steel development on iron ore processing technology[J]. Journal of Wuhan University of Technology, 2007, 29(1): 1?7.
[7] 余永富. 我国铁矿山发展动向、选矿发展现状及存在的问题[J]. 矿冶工程, 2006, 26(1): 21?25.
YU Yong-fu. Development trends of iron mines and status and problems of beneficiation technology in China[J]. Mining and Metallurgical Engineering, 2006, 26(1): 21?25.
[8] 孙炳泉. 近年我国复杂难选铁矿石选矿技术进展[J]. 金属矿山, 2006(3): 11?13.
SUN Bing-quan. Beneficiation technology of refractory iron ore in china in recent years[J]. Metal Mine, 2006(3): 11?13.
[9] 袁致涛, 高 太, 印万忠, 韩跃新. 我国难选铁矿石资源利用的现状及发展方向[J]. 金属矿山, 2007(1): 1?6.
YUAN Zhi-tao, GAO Tai, YIN Wan-zhong, HAN Yue-xin. Status quo and development orientation of China’s refractory ore resource utilization[J]. Metal Mine, 2007(1): 1?6.
[10] 李光辉, 董海刚, 肖春梅, 范晓慧, 郭宇峰, 姜 涛. 高铁铝土矿的工艺矿物学及铝铁分离技术[J]. 中南大学学报: 自然科学版, 2006, 37(2): 235?240.
LI Guang-hui, DONG Hai-gang, XIAO Chun-mei, FAN Xiao-hui, GUO Yu-feng, JIANG Tao. Mineralogy and separation of aluminum and iron from high ferrous bauxite[J]. Journal of Central South University: Science and Technology, 2006, 37(2): 235?240.
[11] 孙炳泉. 褐铁矿选矿技术进展[J]. 金属矿山, 2006(8): 27?29.
SUN Bing-quan. Advance in beneficiation technology of limonite ore[J]. Metal Mine, 2006(8): 27?29.
[12] 姜 涛, 刘牡丹, 李光辉, 周太华, 范晓慧. 高铝铁矿石工艺矿物学及铝铁分离技术[J]. 中南大学学报: 自然科学版, 2009, 40(5): 1165?1171.
JIANG Tao, LIU Mu-dan, LI Guang-hui, ZHOU Tai-hua, FAN Xiao-hui. Mineralogy and separation of aluminum and iron of high-aluminum iron ores[J]. Journal of Central South University: Science and Technology, 2009, 40(5): 1165?1171.
[13] 周秋生, 范旷生, 李小斌, 彭志宏, 刘桂华. 采用烧结法处理高铁赤泥回收氧化铝[J]. 中南大学学报: 自然科学版, 2008, 39(1): 92?97.
ZHOU Qiu-sheng, FAN Kuang-sheng, LI Xiao-bin, PENG Zhi-hong, LIU Gui-hua. Alumina recovery from red mud with high iron by sintering process[J]. Journal of Central South University: Science and Technology, 2008, 39(1): 92?97.
[14] 刘万超, 杨家宽, 肖 波. 拜耳法赤泥中铁的提取及残渣制备建材[J]. 中国有色金属学报, 2008, 18(1): 187?192.
LIU Wan-chao, YANG Jia-kuan, XIAO Bo. Recovering iron and preparing building material with residues from Bayer red mud [J]. The Chinese Journal of Nonferrous Metals, 2008, 18(1): 187?192.
[15] MISHILA B, 王中明, 李长根. 从赤泥中回收有价产品[J]. 国外金属矿选矿, 2003, 40(7): 38?44.
MISHILA B, WANG Zhong-ming, LI Chang-gen. Recovering value elements from Red Mud[J]. Metallic Ore Dressing Abroad, 2003, 40(7): 38?44.
[16] 逯军正, 于先进, 张丽鹏. 从赤泥中回收铁的研究现状[J]. 山东冶金, 2007, 29(4): 10?12.
LU Jun-zheng, YU Xian-jin, ZHANG Li-peng. Development condition of recovering iron from Red Mud[J]. Shandong Metallurgy, 2007, 29(4): 10?12.
[17] 刘永康, 梅贤功. 高铁赤泥煤基直接还原的研究[J]. 烧结球团, 1995(2): 5?9.
LIU Yong-kang, MEI Xian-gong. Study on coal-based direct reduction of high-iron-content Red Mud[J]. Sintering and Pelletizing, 1995(2): 5?9.
[18] WEISSBERGER S, ZIMMELS Y. Studies on concentration and direct reduction of the Ramim iron ore[J]. International Journal of Mineral Processing, 1983, 11(2): 115?130.
基金项目:国家杰出青年科学基金资助项目(50725416)
收稿日期:2009-03-09;修订日期:2009-08-25
通信作者:姜 涛,教授,博士;电话:0731-88877656;E-mail: jiangtao@mail.csu.edu.cn
(编辑 龙怀中)