
Influence of process parameters on electrochemical and physical properties of sputtered iron-doped nickel oxide thin films
HUANG Jin-zhao(黄金昭)1, XU Zheng(徐 征)1, LI Hai-ling(李海玲)2,
KANG Guo-hu(亢国虎)2, WANG Wen-jing(王文静)2
1. Key Laboratory of Luminescence and Optical Information, Ministry of Education,
Institute of Optoelectronic Technology, Beijing Jiaotong University, Beijing 100044, China;
2. Beijing Solar Energy Research Institute, Beijing 100083, China
Received 19 November 2005; accepted 2 March 2006
Abstract: The iron-doped nickel oxide films used as oxygen evolution catalysts in the photoelectrochemical production of hydrogen from solar energy were deposited by means of RF reactive magnetron sputtering from a Ni-Fe alloy target in oxygen and argon atmosphere. The effects of processing parameters on the film properties, such as overpotential, composition, surface morphology and preferred orientation, were investigated. The electrochemical experiment, structural and compositional measurements indicate that the relative lower substrate temperature, higher RF power, higher working pressure and oxygen content are necessary to gain lower overpotential. The lowest overpotential of 251 mV is obtained at a current density of 80 mA/cm2. The existence of iron, which acts as activity site, and Ni3+ ion is responsible for lowering overpotential. By analyzing SEM and XRD data, it is also noticed that an improvement in crystallinity, appropriate grain size and less crystalline phase contribute to an increased electrocatalytic activity in oxygen evolution reaction. These results mentioned above indicate that iron-doped nickel oxide is promising as an oxygen catalyst.
Key words: iron-doped nickel oxide; films; overpotential; photoelectrochemical
1 Introduction
A principal focus of modern research in electrocatalysis is to discover electrode materials that exhibit excellent electrochemical stability and show interesting activity towards typical electrochemical reaction[1-10]. It is desirable that these materials are inexpensive, and abundantly available.
Nickel is considered the most suitable anode material for the oxygen evolution reaction(OER) in concentrated alkaline solution, because of its catalytic properties and corrosion resistance in concentrated alkaline solutions, and it is relatively cheap[11-13]. So the electrochemistry of oxygen evolution from nickel electrodes during alkaline electrolysis has been studied extensively.
In general, when oxygen evolution takes place on nickel electrode, the surface is already covered with an oxide layer[14]. Nickel oxide (NaCl-type structure with a lattice parameter of 0.419 5 nm[15-17]) has widely vary- ing electronic, electrochemical and optical properties depending on the synthesis process and the resulting defect structure[18]. It has been used as functional layer materials for chemical sensor, p-type transparent conducting film and materials for electrochromic display[19].
Several studies have reported an increased activity for the evolution of oxygen on nickel oxide electrode when iron is present[12,14,20,21]. MILLER et al[14] and CORRIGON[20] obtained the lowest overpotential of 285 mV and 230 mV at 8 mA/cm2, respectively. This composite oxide shows promise as the anodic electrocatalyst for alkaline electrolysis to produce hydrogen. Iron-doped nickel oxide film can be fabricated by various physical and chemical ways, such as reactive magnetron sputtering[14], electron beam evaporation and cathodic electrodeposition[20]. Among these methods, reactive magnetron sputtering has been widely used to prepare this film, due to the increased adhesion of the film to substrate.
In this paper, we describe the development of sputtered iron-doped nickel oxide films used as oxygen evolution catalysts. The effects of processing parameters including oxygen content, working pressure, RF power and substrate temperature on the electrochemical and physical properties of iron-doped nickel oxide film are studied with the goal of lowering the overpotential.
2 Experimental
The iron-doped nickel oxide films were deposited by RF reactive magnetron sputtering from a Ni-Fe alloy target which was 76.4 mm in diameter, 3 mm in thickness and 99.99% in purity. The mole fractions of Fe and Ni are 21% and 79%, respectively. The deposition was conducted in an oxygen and argon atmosphere. Before deposition, the chamber was pumped to a pressure of less than 4.5?10-3 Pa by a diffusion pump, and a pre-sputtering process followed for 10 min to clean the target surface and to remove any possible contamination. The films were deposited under different substrate temperature, RF power, working pressure and oxygen content.
Both oxygen and argon of various ratios were controlled by mass flow controller. The relative oxygen pressure defined as p(O2)/p(O2+Ar) was varied from 10% to 40%. The working pressure was from 1 Pa to 4 Pa. The applied RF powers were from 100 W to 400 W. The range of substrate temperatures was from 50 ℃ to 200 ℃.
The electrochemical properties (overpotential) of thin films during oxygen evolution were characterized by a series of steady-state polarization curves. The electrochemical measurements were carried out in a conventional three-electrode cylindrical electrochemical cell which had a standard calomel reference electrode (SCE) and a Pt counter electrode. The reference electrode was brought into contact with the working electrode through a Luggin capillary (KCl agar-agar salt bridge) in order to minimize the IR drop of the solution resistance. All tests were conducted with a well-defined electrode area of 1 cm2 in 1 mol/L potassium hydroxide (KOH) prepared using deionized water.
A conventional stylus surface-roughness detector (Alpha-step 200) was used to measure the film thickness. The crystalline and orientation were studied by the X-ray diffraction (XRD, Rigaku, D/max-RB) technique. Scanning electron microscope (SEM, JEM-6301F) was used to examine the surface feature and morphology, and the ratio of composition was measured by energy dispersive spectrum(EDS) affiliated to SEM. Before X-ray photoelectron spectra (XPS, PHI5300) experiment, the films were etched for 3 min to remove the effect of contamination. The XPS spectra obtained were calibrated using the C 1s line (284.6 eV).
3 Result and discussion
3.1 Influence of substrate temperature
Fig.1 compares the steady-state polarization plots of the films deposited under different substrate temperatures. The influence of substrate temperature on the overpotential is not very obvious. The lowest overpotentials are found in the films deposited under 50 ℃ and 150 ℃.
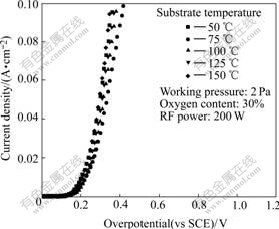
Fig.1 Steady-state polarization plots of films deposited under different substrate temperatures
At higher substrate temperature, atoms have enough energy to diffuse to the preferred nucleation site and may help to eliminate the internal defect of target and obtain grains with good crystallinity, and decrease the overpotential for the OER[22]. But higher substrate temperature may reduce the adhesion between the substrate and film. Now that the higher or lower temperatures have no obvious influence on overpotential, the lower substrate temperature is suitable for industrialization.
The non-stoichiometric NiO is known as a p-type semiconductor. The defects, which are the cause of hole conductivity, are the Ni2+ ion vacancies. Each vacancy is replaced by two Ni3+ ions which act as electron acceptors. The mechanism of electrical conductance for the film can be attributed to the existence of localized Ni3+ ion in the lattice[23].
It is reported that Ni3+ ion is the key function in reducing resistivity, and it is useful to reduce the overpotential. Ni3+ ions existing at localized lattice sites act as point defects, which are responsible for the variation in resistivity. The existence of localized Ni3+ ion was conformed by the XPS data. Fig.2 shows the spectrum of Ni 2p. The peak at 854.5 eV is due to both NiO (853.8 eV) and Ni2O3 (855.8 eV). The XPS spectrum is deconvolted by Gaussian curves corresponding to peaks of nickel oxides. As we can see in Fig.2, it contains not only Ni2+ ion but also Ni3+ ion.
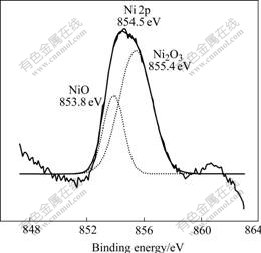
Fig.2 Deconvoltion spectrum of Ni 2p in film
3.2 Effects of RF power
Fig.3 shows the influence of RF power on the overpotential. With the increasing of RF power, the grain size may be fine and increased (The later SEM results will give the evidence). Large grains mean less grain boundaries and thus less scatterings at the grain boundary, then lead to a lower overpotential. The oxygen content in the film increases with decreasing RF power. This implies that more vacancies exist in the film, which results in lower resistivity. The resistivity of the film can be lowered by increasing the Ni3+ ion concentration as a result of nickel vacancies and interstitial oxygen in the nickel oxide crystallites.
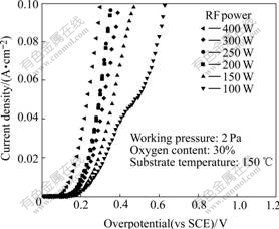
Fig.3 Steady-state polarization plots of films deposited under different RF power
3.3 Effects of working pressure
The polarization curves obtained on films deposited under different working pressures are shown in Fig.4. With the increasing of working pressure, the over- potential decreases.
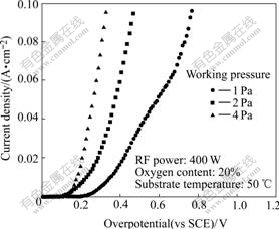
Fig.4 Steady-state polarization plots of films deposited under different working pressures
Fig.5 shows the X-ray diffraction patterns for samples deposited under different working pressures. The diffraction peak is observed, which indicates a strong preferred orientation and good quality of crystallinity. As the working pressure is increased, the intensity of diffraction peak increases. From the XRD patterns and polarization plots of the films, it is indicated that the lower overpotential of the films is obtained with higher working pressure. In the films, only peak assigned to cubic NiO is observed. We interpret this as evidence that the iron is dispersed throughout the matrix, possibly incorporated into the NiO lattice.
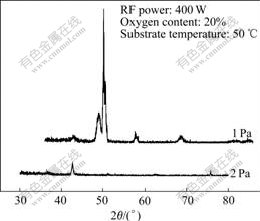
Fig.5 XRD patterns of FeNi:Ox thin films obtained under different working pressures
We believe that the differences of morphology and crystalline structure between higher and lower working pressure are responsible for the differences in overpotential, and the absence of, or lack of access to the active site in these films is the cause of the higher overpotential for the OER in these films. Under higher working pressures (Fig.6), the larger grain size and better oriented crystallites which provide an aboundance of chemically active site for the OH- ion reactants, both at microcrystalline faces on the surface and within grain boundaries are found. In contrast, smaller grain size and poorly oriented crystallites restrict access to active sites and increase overpotential.
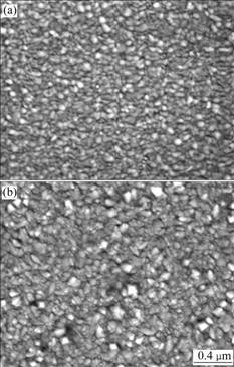
Fig.6 SEM micrographs of Fe:NiOx thin films deposited under different working pressures: (a) 1 Pa; (b) 2 Pa
3.4 Influence of oxygen content
Fig.7 shows the steady-state polarization plots of the films deposited under different oxygen contents. It is obvious that higher oxygen content helps to reduce over- potential.

Fig.7 Steady-state polarization plots of films deposited under different oxygen contents
It is found that there is higher overpotential in those films with the poorer crystallinity and more random orientation. We attribute this to reduced access to reaction sites located on microcrystallite faces along the surface and intergrain boundaries of the crystallite structure. From Fig.8, although crystallites become better with the decreasing of oxygen content, the overpotential becomes higher. It is because that the lower oxygen content gives rise to crystalline phase in the films.
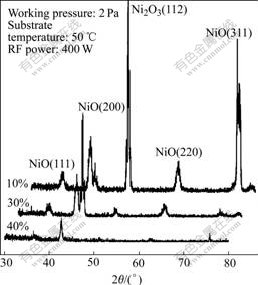
Fig.8 XRD patterns of FeNi:Ox thin films deposited under different oxygen contents
Just as what we said the larger grain size is beneficial for the lowering of overpotential, the grain size of sample deposited at 30% oxygen content is larger than that of sample deposited at 10% oxygen content (Fig.9), so the overpotential of sample deposited at 30% oxygen content is lower.
The addition of iron makes the overpotential lower. Such a change is consistent with iron’s higher electrochemical activity compared with nickel. From Fig.10, the Fe3+ ion is found in the films (Fe2O3:710.9 eV). Fe3+ ion provides a more favorable active reaction sites for the absorption of OH-. In fact, the addition of iron can not be attributed to decrease of the resistivity of the films, but the mechanistic change resulted from the incorporation of iron into the film reduces the overpotential sufficiently to overcome the shortcoming due to higher resistivity.
The Fe, Ni and O contents of the films were measured by EDS (Fig.11). The results show that, with the increasing Fe content, the overpotential becomes lower. The Fe content is 14.00%, 14.59% and 15.00% for samples deposited at 10%, 30% and 40% oxygen con-tent, respectively.
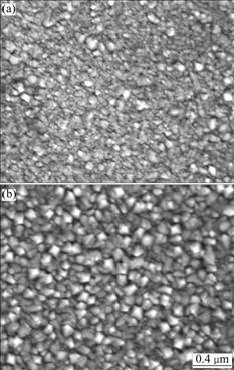
Fig.9 SEM micrographs of Fe:NiOx thin films deposited under different oxygen contents: (a) 10%; (b) 30%
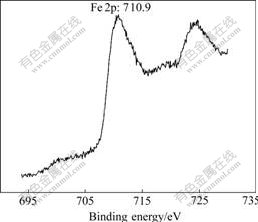
Fig.10 XPS spectrum of Fe 2p in Fe:NiOx thin film
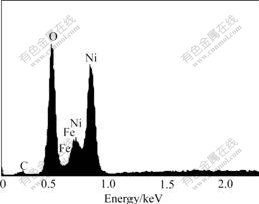
Fig.11 EDS spectrum of FeNi:Ox thin film
4 Conclusions
1) The iron-doped nickel oxide thin films were deposited by RF reactive magnetron sputtering using a Fe-Ni alloy target at different process parameters. The substrate temperature, RF power, working pressure and oxygen content are the main factors affecting the physical and electrochemical properties of the films.
2) The higher oxygen content, higher working pressure, higher RF power and lower substrate temperature are necessary to gain the full benefit of the films. A minimal overpotential of 251 mV is obtained at a current dentisity of 80 mA/cm2. The variation in overpotential is strongly related to changes in microstructure and composition.
3) The conduction in nickel oxide is due to the presence of Ni3+ ions, which are formed due to nickel vacancies in the films. The higher electrochemical activity of iron attributes to the lowering of overpotential. In general reactively sputtered iron-doped nickel oxide is a promising oxygen evolution reaction catalyst.
References
[1] WEI Zhi-qiang, QIAO Hong-xia, DAI Jian-feng, FENG Wang-jun, WANG Qing, LI Wei-xue. Preparation and characterization of Ni nanopowders prepared by anodic arc plasma [J]. Trans Nonferrous Met Soc China, 2005, 15(1): 51-56.
[2] BAK T, NOWOTNY J, REKAS M, SORRELL C C. Photo- electrochemical hydrogen generation from water using solar energy [J]. Int J Hydrogen Energy, 2002, 27: 991-1022.
[3] NAVARRO-FLORES E, CHONG Z W, Omanovic S. Characterization of Ni, NiMo, NiW and NiFe electroactive coatings as electrocatalysts for hydrogen evolution in an acidic medium [J]. J Mol Catal A: Chem, 2005, 226: 179-197.
[4] HITZ C, LASIA A. Experimental study and modeling of impedance of the HER on porous Ni electrodes [J]. J Electroanal Chem, 2001, 500: 213-222.
[5] CONWAY B E, JERKIEWICZ G. Relation of energies and coverages of underpotential and overpotential deposited H at Pt and other metals to the ‘volcano curve’ for cathodic H2 evolution kinetics [J]. Electrochim Acta, 2000, 45: 4075-4083.
[6] METIKOS-HUKOVIC M, JUKIC A. Correlation of electronic structure and catalytic activity of Zr-Ni amorphous alloys for the hydrogen evolution reaction [J]. Electrochim Acta, 2000, 45: 4159-4170.
[7] TANAKA S, HIROSE N, TANAKI T. Evaluation of Raney-nickel cathodes prepared with aluminum powder and tin powder [J]. Int J Hydrogen Energy, 2000, 254: 81-485.
[8] LOSIEWICZ B, BUDNIOK A, ROOWIONSKI E, LAGIEWKA E, LASIA A. The structure, morphology and electrochemical impedance study of the hydrogen evolution reaction on the modified nickel electrodes [J]. Int J Hydrogen Energy, 2004, 29: 145-157.
[9] HUANG L, YANG F Z, SUN S G, XU S K, ZHOU S M. Studies on structure and electrocatalytic hydrogen elvolution of nanocrystalline Ni-Mo-Fe alloy electrodeposit electrodes [J]. Chin J Chem, 2003, 21: 382-386.
[10] YANG F Z, GUO Y F, HUANG L, et al. Ectrodeposition, structure and corrosion resistance of nanocrystalline Ni-W alloy [J]. Chin J Chem, 2004, 22: 228-231.
[11] MILLER E L, ROCHELEAU R E. Electrochemical and electrochromic behavior of reactive sputtered nickel oxide [J]. J Electrochem Soc, 1997, 144: 1995-2003.
[12] BROSSARD L. Oxygen discharge on nickel and cobalt anodes in 30% KOH at 70℃ in the presence of dissolved iron and vanadium [J]. Int J Hydrogen Energy, 1991, 16: 87-92.
[13] GRAS J M, SPITERI P. Corrosion of stainless steels and nickel-based alloys for alkaline water electrolysis [J]. Int J Hydrogen Energy, 1993, 18: 561-566.
[14] MILLER E L, ROCHELEAU R E. Electrochemical behavior of reactively sputtered iron-doped nickel oxide [J]. J Electrochem Soc, 1997, 144: 3072-3077.
[15] SATO H, MINAMI T, TAKATA S, YAMADA T. Transparent conducting p-type NiO thin films prepared by magnetron sputtering [J]. Thin Solid Films, 1993, 236: 27-31.
[16] HOTOVY I, B?C D, HASC?K S, NENNEWITZ O. Characterization of NiO thin films deposited by reactive sputtering [J]. Vacuum, 1998, 50: 41-44.
[17] HOTOVY I, HURAN J, SPIESS L, et al. The influence of process parameters and annealing temperature on the physical properties of sputtered NiO thin film [J]. Vacuum, 2003, 69: 237-242.
[18] FERREIRA F F, TABACNIKS M H, FANTINI M C A, FARIA I C, GORENSTEIN A. Electrochromic nickel oxide thin films deposited under different sputtering conditions [J]. Solid State Ionics, 1996, 86-88: 971-976.
[19] HOTOVY I, HURAN J, JAN?K J, KOBZEV A P. Deposition and properties of nickel oxide films produced by DC reactive magnetron sputteing [J]. Vacuum, 1998, 51: 157-160.
[20] CORRIGAN D A. The catalysis of the oxygen evolution reaction by iron impurities in thin film nickel oxide electrode [J]. J Electrochem Soc, 1987, 134: 377-384.
[21] KAMNEV A A, EZHOV B B. Electron spectroscopy of soluble anodic oxidation products of iron in alkaline solutions [J]. Soviet Electrochemistry, 1989, 24: 1027-1029.
[22] LU Y M, HWANG W S, YANG J S, CHUANG H C. Properties of nickel oxide thin films deposited by RF reactive magnetron sputtering [J]. Thin Solid Films, 2002, 420/421: 54-61.
[23] LU Y M, HWANG W S, YANG J S. Effect of substrate temperature on the resistivity of non-stoichiometric sputtered NiOx films [J]. Thin Solid Films, 2002, 155: 231-235.
(Edited by YUAN Sai-qian)
Foundation item: Project(2003CB214501) supported by the National Basic Research Program of China; Project(48010) supported by the Excellent Doctor’s Science and Technology Innovation Foundation of Beijing Jiaotong Univsersity, China
Corresponding author: HUANG Jin-zhao; Tel: +86-10-51688605; Fax: +86-10-51683933; E-mail: zhengxu@center.njtu.edu.cn