
Corrosion resistance of electrodeposited RE-Ni-W-P-SiC-PTFE composite coating in phosphoric and ferric chloride
XU Rui-dong(徐瑞东), GUO Zhong-cheng(郭忠诚), PAN Jun-yi(潘君益)
Faculty of Materials and Metallurgical Engineering, Kunming University of Science and Technology, Kunming 650093, China
Received 9 August 2005; accepted 9 December 2005
Abstract: Corrosion rate and anode polarization curves of electrodeposited RE-Ni-W-P-SiC-PTFE composite coating in various concentrations of phosphoric and ferric chloride were researched. The results show that corrosion rate of the composite coatings increases with the increasing concentrations of phosphoric and ferric chloride, and reaches the maximum value when phosphoric concentration is 40% and ferric chloride concentration is 20% (mass fraction, the same below if not mentioned). Anode polarization curves of the composite coatings show that anode polarization current density of the composite coatings heat-treated at 200 ℃ or 500 ℃ is lower than that of other coatings heat-treated at 300 ℃ or 400 ℃, which displays that the composite coatings heat-treated at 200 ℃ or 500 ℃ have better corrosion resistance. Besides, corrosion resistance of the composite coating heat-treated at 500 ℃ is better than that as deposited and RE-Ni-W-P-SiC composite coating heat-treated at 400 ℃, and is also better than that of 316L stainless steel.
Key words: electrodeposition; RE-Ni-W-P-SiC-PTFE composite coating; corrosion rate; phosphoric solution; ferric chloride
1 Introduction
During process, store and use in various kinds of environment, corrosion, wear, fatigue and rupture may happen in all materials and products. These kinds of failure and damages widely occur in industries, causing enormous losses to national economy. Therefore, people look for the way to solve this problem actively. Composite electrodepositon technology can meet the needs to a certain extent and has developed speedily in the recent decade, a series of composite coatings have been obtained, such as Ni-SiC, Ni-Al2O3, Ni-Fe-Al2O3, Ni-W-P-SiC, RE-Ni-W-P-SiC, RE-Ni-W-P-B4C-MoS2, RE-Ni-Mo-P-B4C-PTFE and Cu-SiC [1-8], which can effectively protect the machine parts from wear, corrosion and friction.
Because rare earth elements have special physical properties and just a little content in the coating can play a remarkable effect, its application in the material field becomes more and more extensive. There are references on friction, wear and oxidation performance of the composite coatings[9-13], but the reports on corrosion resistance are few[14,15], so the corrosion resistance of RE- Ni-W-P-SiC-PTFE composite coating in various concentrations of phosphoric and ferric chloride was studied in this paper.
2 Experimental
2.1 Bath composition and process conditions
The bath composition consisted of nickel sulfate (50-100 g/L), sodium hypophosphite (10-30 g/L), sodium tungstate (80-190 g/L), complex reagent (90-210 g/L), surfactant (trace), silicon carbide (30-100 g/L), rare earth oxidation (CeO 10-20 g/L) and polytetrafluoroethylene (PTFE 10-50 ml/L). The process conditions were: cathode current density 5-8 A/dm2, pH value 5-6, bath temperature 40-50 ℃, plating time 50-180 min and agitation time 1-4 min.
2.2 Material
45# steel with dimensions of 40 mm×30 mm×2 mm was used as substrate material.
2.3 Corrosion resistance
1) Corrosion specimen
Composite coatings obtained from the above process conditions were called as-deposited coating. Composite coatings heat-treated at 200, 300, 400 and 500 ℃ were called heat-treated coating. Meanwhile, 316L stainless steel was used as contrast material.
2) Anode polarization curve
Anode polarization curve was plotted by DHZ-1 electrochemical combination tester or HDV-7 transistor potentiostat with Pt electrode as auxiliary electrode and saturated calomel electrode as reference electrode. Experimental temperature was ambient temperature. Corrosive media and its concentrations are shown in Table 1.
Table 1 Corrosive media and their concentration(mass fraction, %)

3) Assessment method of corrosion degree
Corrosion rate can be described as
K1=(m0-m1)/(S0×t) (1)
where K1 is the corrosion rate(mg/cm2·h), m0 is the mass of metal before corrosion, m1 is the mass of metal after corrosion, S0 is the surface area of corroded metal, and t is the corrosion time.
3 Results and discussion
3.1 Corrosion resistance of composite coatings in phosphoric solution
Corrosion rate and anode polarization curves of RE-Ni-W-P-SiC-PTFE composite coatings heat-treated at different temperatures in various phosphoric concentrations are shown in Fig.1 and Fig.2, respectively. X-ray diffraction pattern of the composite coating heat-treated at 400 ℃ is shown in Fig.3.
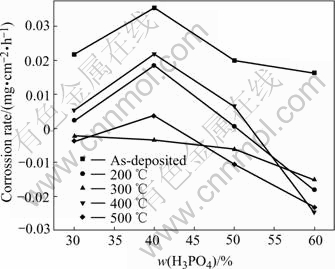
Fig.1 Corrosion rate of composite coatings in various phosphoric concentrations
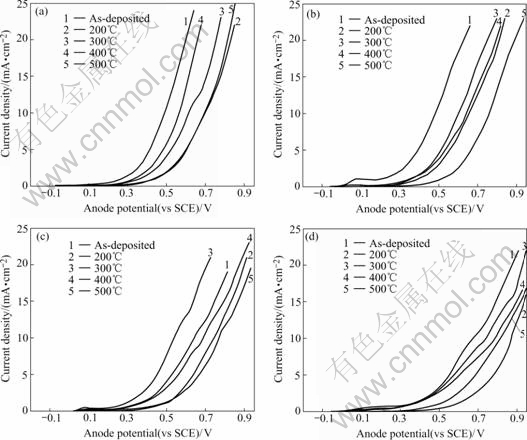
Fig.2 Anode polarization curves of composite coatings in various phosphoric concentrations (heat-treated for 2 h): (a) 30% phosphoric; (b) 40% phosphoric; (c) 50% phosphoric; (d) 60% phosphoric
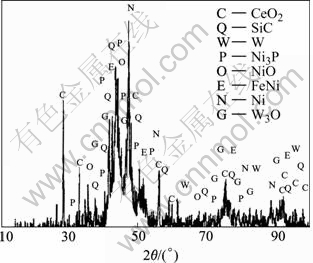
Fig.3 X-ray diffraction pattern of RE-Ni-W-P-SiC-PTFE composite coating heat-treated at 400 ℃
Fig.1 shows that corrosion rate of the composite coatings increases with the increasing phosphoric concentration, and reaches the maximum value when the phosphoric concentration is 40%. Thereafter, corrosion rate will decrease. Besides, corrosion rate of the composite coatings as-deposited and heat-treated at 400℃ is higher, while corrosion rate of composite coatings heat-treated at 200, 300 and 500 ℃ is lower, the reason is that for the as-deposited composite coating, PTFE and SiC particles embedded into the coating make it become more loose and porous in comparison with alloy coating. Moreover, because PTFE, being a soft polymer, isn’t tightly combined with the substrate, when the composite coating is heat-treated at 400 ℃, Ni3P phase occurs and PTFE has been gasified(shown in Fig.3), which leads to higher internal stress in the coating and more microcrackes on the surface of the composite coatings, corrosive media easily go to substrate through these pores and microcrackes, resulting in corrosion.
On the contrary, heat treatment at 200 ℃ avails to remove hydrogen atoms left over in the alloy, release internal stress and improve adhesion of the coating and substrate, all of these improve corrosion resistance of the coating. After heat treatment at 500 ℃, the internal stress of the coating is the lowest or has been eliminated, Ni3P grows continually, so the corrosion resistance is better.
It can be seen from Fig.2 that at the same polarization potential, corrosion current density of RE-Ni-W-P-SiC-PTFE composite coatings heat-treated at 200, 300 and 500 ℃ is less than that at 400 ℃ and as-deposited, showing better corrosion resistance, which agrees with the conclusion from Fig.1.
3.2 Corrosion resistance of composite coatings in ferric chloride solution
When heat treatment temperature and ferric chloride concentration are different, corrosion rate of RE-Ni-W-P- SiC-PTFE composite coating is shown in Fig.4, and its anode polarization curves are shown in Fig.5.
Fig.4 indicates that corrosion rate of RE-Ni-W-P- SiC-PTFE composite coatings increases with the increasing ferric chloride concentration. And besides, the corrosion rate of the composite coatings increases slowly at 200, 300 and 500 ℃. Furthermore, The corrosion resistance of the composite coating heat-treated at 500℃ is the best under all conditions and the corrosion resistance of the composite coating as-deposited and at 400℃ is poorer.
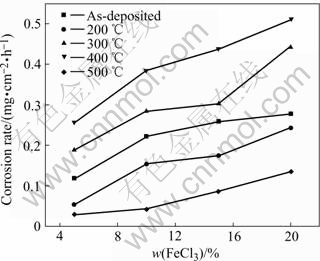
Fig.4 Corrosion rate of composite coatings in various ferric chloride concentrations
Fig.5 also presents that corrosion resistance of the composite coatings heat-treated at 200 ℃ and 500 ℃ is clearly superior to that as-deposited and heat-treated at 400 ℃.
3.3 Comparison of corrosion rate of samples in different corrosive media
Corrosion rates of the composite coatings in phosphoric and ferric chloride are shown in Tables 2 and 3 respectively.
It can be seen from Table 2 and Table 3 that the corrosion rate of RE-Ni-W-P-SiC-PTFE composite coating is higher than those of RE-Ni-W-P-SiC composite coating as-deposited, while the corrosion rate of RE-Ni-W-P-SiC-PTFE composite coating heat-treated at 500 ℃ in ferric chloride solution is lower than those of RE-Ni-W-P-SiC composite coating heat-treated at 400 ℃. In phosphoric solutions, some phosphorous compounds form on the surface of the composite coating, but the change of corrosion rate does not follow the rule obviously.
On the whole, corrosion resistance of RE-Ni-W-P- SiC-PTFE composite coating heat-treated at 500 ℃ is better than that of RE-Ni-W-P-SiC-PTFE composite coating as deposited and RE-Ni-W-P-SiC composite coating heat-treated at 400 ℃, and also better than that of 316L stainless steel. 4 Conclusions
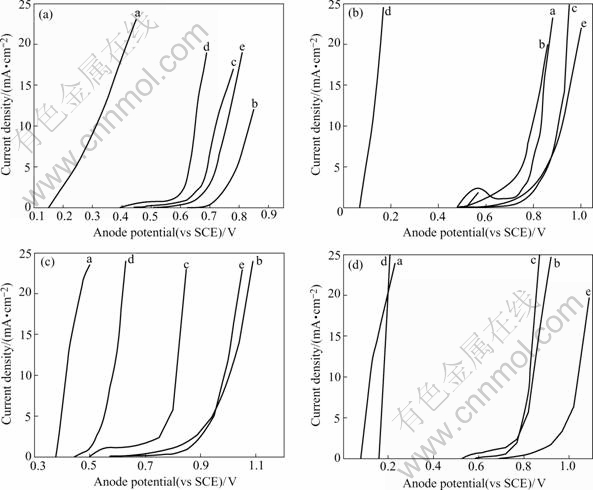
Fig.5 Anode polarization curves of composite coating in various ferric chloride concentrations (heat-treated for 2 h): (a) 5% ferric chloride; (b) 10% ferric chloride; (c)15% ferric chloride; (d) 20% ferric chloride; a As-deposited; b 200 ℃; c 300 ℃; d 400 ℃; e 500 ℃
Table 2 Corrosion rates of samples in various phosphoric concentrations (mg?cm-2?h-1)
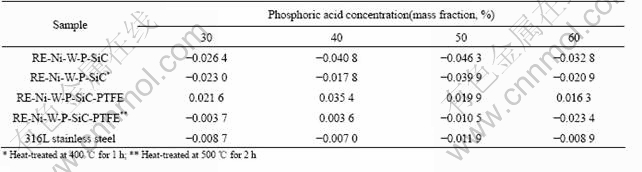
Table 3 Corrosion rates of samples in various ferric chloride concentrations (mg?cm-2?h-1)
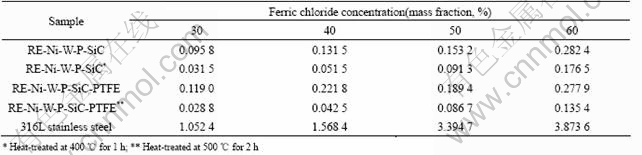
1) The corrosion rate of RE-Ni-W-P-SiC-PTFE composite coating increases with the increasing concentrations of ferric chloride and phosphoric, and reaches the maximum value when the phosphoric concentration is 40% and the ferric chloride concentration is 20%.
2) Anode polarization current density of the compo- site coatings heat-treated at 200 ℃ or 500 ℃ is lower than that of the other coatings heat-treated at 300 ℃ or 400 ℃. The composite coatings heat-treated at 200 ℃ or 500 ℃ have better corrosion resistance.
3) The corrosion resistance of RE-Ni-W-P-SiC- PTFE composite coating heat-treated at 500 ℃ is better than that of the as-deposited and RE-Ni-W-P-SiC composite coating heat-treated at 400 ℃, and is also better than that of the 316L stainless steel.
References
[1] TAN Q X. A study on composite electrodeposition process of WC with Ni [J]. Materials Protection, 1993, 26(7): 4-7.(in Chinese)
[2] SHI G H. Study on the electrodeposition of Fe-Ni-Al2O3 composite coating and its friction and wear performance [J]. Plating & Finishing, 1994, 16(5): 8-11. (in Chinese)
[3] XU R D, GUO Z C, XUE F Q, WANG J L. Electrodeposited RE-Ni-W-P-SiC composite ceramic coating on cast aluminum containing high silicon [J]. New Technique and New Process, 2002, 35(11): 1-5. (in Chinese)
[4] YAO G X. Study on preparation of (Fe-Ni-MoS2) self-lubricating composite coating and its properties [J]. Plating & Finishing, 1995, 17(2): 33-37. (in Chinese)
[5] GUO Z C, YANG X W. Theory and Practice of Electrodeposition RE-Ni-W-P-SiC Multifunctional Composite Materials [M]. Beijing: Metallurgical Industry Press, 2002. (in Chinese)
[6] GUO Z C, ZHU X Y, ZHAI D, XU R D. Cathodic process of electrodeposited RE-Ni-W-P-SiC composite coating [J]. Materials Protection, 2001,34(7): 6-9.(in Chinese)
[7] GUO Z C, ZHU X Y, XU R D. Microstructure and wear resistance of electrodeposited RE-Ni-Mo-P-B4C-PTFE composite coating [J]. Materials Science And Technology, 2004, 20(2): 257-260.
[8] GUO Z C, ZHU X Y. Studies on properties and structure of electrodeposited RE-Ni-W-B-SiC composite coating [J]. Materials Science And Engineering A, 2003, 363: 325-329.
[9] MA K Y, GUO Z C, ZHU X Y, XU R D. Characteristics of electrodeposited RE-Ni-W-B-B4C-MoS2 composite coating [J]. Trans Nonferrous Met Soc China, 2003, 13(5): 1220-1225.
[10] GUO Z C, DENG L H, YANG X W. Wear resistance of electrodeposited RE-Ni-W-P-SiC-PTFE composite coating [J]. Materials Protection, 2001, 34(1): 4-6.(in Chinese)
[11] GUO Z C, DENG L H, YANG X W. Oxidation resistance of electrodeposited RE-Ni-W-P-SiC composite coating [J]. Materials for Mechanical Engineering, 2001, 25(4): 26-36. (in Chinese)
[12] GUO Z C, ZHU X Y, XU R D. Cathodic process and wear resistance of electrodeposited RE-Ni-W-P-SiC composite coating [J]. Acta Metallurgica Sinica, 2002, 15(4): 369-373.
[13] GUO Z C, ZHU X Y, YANG X W. Corrosion resistance of electro- deposited RE-Ni-W-P-SiC composite coating [J]. Trans Nonferrous Met Soc China, 2001, 11(3): 413-415.
[14] GUO Z C, ZHU X Y, XU R D, et al. Corrosion mechanism of electrodeposited RE-Ni-W-P-SiC composite coating [J]. Materials Protection, 2003, 36(7): 38-41. (in Chinese)
[15] ZHU X Y, GUO Z C. Corrosion resistance of electrodeposited RE-Ni-W-P-SiC composite coating [J]. Materials For Mechanical Engineering, 2003, 27(2): 43-46.(in Chinese)
Foundation item: Project([2002]24) supported by the National Development and Reform Commission of China
Corresponding author: XU Rui-dong; Tel: +86-871-5154062; +86-871-5112962; E-mail: rdxukm@126.com
(Edited by LI Xiang-qun)