Calculation of cooling rate of amorphous aluminum alloy melt-spun ribbons
HE Shi-wen (何世文), LIU Yong(刘 咏), LIU Zu-ming(刘祖铭), HUANG Bai-yun(黄伯云)
State Key Laboratory of Powder Metallurgy, Central South University, Changsha 410083, China
Received 20 April 2006; accepted 30 June 2006
Abstract: Based on the heat transfer theory and liquid solidification theory, the heat transfer during the rapid solidification process of amorphous ribbons prepared by melt spinning was approximately modeled by one-dimensional heat conduction equation. Besides, integration with the temperature gradient, the relationship between the ribbon thickness and solidification time was derived according to the boundary conditions of ribbon-copper wheel. A simply theoretical model was obtained to calculate the cooling rates of aluminum amorphous ribbons. According to the above theoretical model, the critical cooling rate of aluminum amorphous ribbons by melt spinning is above 106 K/s, which proves that the aluminum based alloys belong to the marginal glass forming ability of alloys. The calculated results are in good agreement with other estimated values reported previously.
Key words: aluminum amorphous ribbon; rapid solidification; cooling rate; melt spinning; heat transfer
1 Introduction
Aluminum based amorphous alloys have attracted great interest of materials researchers due to their extremely high strength, high corrosion resistance and other extraordinary properties[1]. So far, preparation of bulk amorphous aluminum alloys is still very difficult due to the marginal glass forming ability of alloys. The preparation of amorphous aluminum alloys can be obtained only by melt-quenching or solid phase reaction. At the present time, the melt spinning of single wheel is the most effective method to prepare aluminum based amorphous alloys. Generally, the average cooling rate of amorphous alloys by melt spinning must range from 105 K/s to 106 K/s[2,3]. Glass forming ability is best described by the critical cooling rate, Rc, of the material. In general, three main methods have been devised to determine the cooling rate[4,5]. The first method involves the construction of the time-temperature- transformation(TTT) curve, which is calculated indirectly by suppression nucleation theory. The second method considers continuous-cooling-transformation(CCT) curve. The third method involves the measurement of the offset temperature for fusion and the onset temperature of solidification upon cooling at different rates using differential thermal analysis (DTA). This three methods all depend on some experiments, which is tedious and time-consuming.
The thickness of amorphous ribbons depends strongly on the heat transfer between the ribbon and the cooling wheel. Several papers are devoted to theoretical investigation of the problem[6-8]. The results of investigation are very useful for more deep understanding of influence of heat transfer on service properties of amorphous metallic alloy ribbons. But in the same time they are complicated for engineers and practical use. The next series of the investigation uses analytical approach based on the well-known solutions of heat conductivity equation. In this work, based on the heat transfer theory and he temperature gradient, we derive the relationship between the ribbon thickness and the solidification time. The aim of the present work is to develop a heat transfer model more appropriate for melt spinning and to get a simple calculation the cooling rates of amorphous ribbons.
2 Theoretical model
The ribbon and the cooling wheel during melt spinning can be considered semi-infinite bodies[9].The temperature transfer between the ribbon and the cooling wheel is governed by Fourier’s equation of heat conduction in a one-dimensional.
Fourier’s equation of heat conduction with no internal energy generation is given as[10]
(1)
where x, t, r, c, λ and a(a=λ/cr) are the distance from the interface (m), the cooling time (s), the density (kg/m3), the specific heat capacity (J/(kg?K)), the thermal conductivity (W/(m?K)) and the thermal diffusivity (m2/s), respectively.
Fig.1 shows the sketch of the thermal profile within the ribbon and the cooling wheel[10]. The initial temperature within the ribbon and the cooling wheel is uniform at T1,0 and T2,0, respectively, where the subscripts 0, 1 and 2 denote initial conditions, the ribbon and the cooling wheel, respectively. The temperature of the ribbon-wheel interface is suddenly changed to Ti.
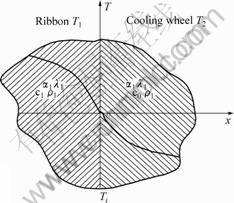
Fig.1 Schematic diagram of thermal profile within ribbon and cooling wheel
According to relevant mathematics knowledge, the general solution[10] of Eqn.(1) is
(2)
where A and B are the indefinite integration constants,
is the error function.
For the aluminum ribbon (x<0), the boundary condition and initial condition are of the form:
T1=Ti(x=0(t>0)) and T1=T10(t=0(x<0)).
T1=Ti(x=0(t>0)),
we have
T1=C1+D1erf(0)=C1=Ti, so C1=Ti.
T1=T10(t=0(x<0)),
Then we have
T1=C1+D1erf(-∞) =C1-D1=T10,
so D1=C1-T10=Ti-T10.
According to Eqn.(2), the general solution for the temperature distribution (T1) is
(3)
If we substitute the values of C1 and D1 into Eqn.(3), then
(4)
Similarly, for the cooling wheel(x>0), the general solution for the temperature distribution(T2) is
(5)
At the distance x=0, the heat flux is the same on both sides of the ribbon and wheel interface according to Fourier’s law. The relevant equation is
(6)
The differential coefficients of Eqns.(4) and (5) in the x=0 are Eqns.(7) and (8), respectively.
(7)
(8)
If we substitute Eqns.(7) and (8) into Eqn.(6) and simplify, then
(9)
Table 1 shows the initial temperatures and thermophysical properties of aluminum ribbon and copper wheel[11].
Table 1 Initial temperature and thermophysical properties of materials
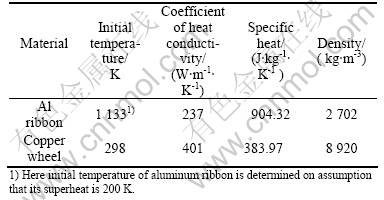
If we substitute the thermophysical properties in Table 1 into Eqn.(9), then Ti=626.74 K.
And we substitute Ti=626.74 K into Eqn.(4), then the temperature field of aluminum alloy ribbon is
(10)
To simplify Eqn.(10), then
(11)
According to
, we can get the cooling rate of aluminum alloy ribbon
(12)
The key factor of calculation cooling rate according to Eqn.(12) is the solidification time.
Suppose cooling rate of the ribbon is constant, then the temperature of copper wheel, namely, T2(x,t) can be expressed as
(13)
The temperature gradient of the ribbon-wheel contact can be expressed as[12]
(14)
Now the boundary conditions at the ribbon-wheel interface are of the formas:
T1(0,t)=T2(0,t)=T(0,t)
(15)
where d is the ribbon thickness, subscript 1 relates to the ribbon, and subscript 2 relates to the wheel.
From Eqn.(13), the following equation can be get
(16)
From Eqns.(14), (15) and (16), we can get
(17)
From Eqn.(17), then
(18)
The value of δ1 in Eqn.(18) is equal to the value of δ in Eqn.(12), i.e. the ribbon thickness. Thus we can determine directly solidification time according to ribbon thickness.
From Eqns.(18) and (12), we can calculate the cooling rates of aluminum alloy amorphous ribbons.
3 Results and discussion
The solidification time of the magnesium alloy ribbon was calculated with the following formula based on the square root law of casting solidification theory[13]
(19)
where ξ is the thickness of ribbon, m; and
is Chvorinov’s constant, which depends on the material properties and casting conditions. L and Tm1 are the latent heat of crystallization, kJ/kg and the melting temperature of the ribbon, K, respectively.
As can be seen the theoretical Eqns.(17) and (19) all give the same function δ=A
. The theoretical value of coefficient A of Eqn.(17) is
(20)
where A was estimated easily for cooling of the melt on a copper wheel for the following parameters c1 , r1 and (λ2c2r2)1/2, which are invariable .
While the theoretical value of coefficient A of Eqn.(19) is:
A=
(21)
One can see that coefficient A can be calculated more easily according to Eqn.(20) than according to Eqn.(21).
The solidification time of magnesium based amorphous ribbon (50 μm) is 1.782×10-5 s and 1.708×10-5 s according to Eqns.(18) and (19), respectively. The difference between them is less than 5%. It means the theoretical analysis of Eqn.(18) reflects right the main features of the heat transfer between the ribbon and the copper wheel. The calculation of solidification time according to Eqn.(18) only depends on the thermophysi-cal properties of two materials. That is to say, the calculation of solidification time according to Eqn.(19) is more complex than according to Eqn.(18). We calculate the solidification time according to Eqn.(18) in the study.
Suppose that the ribbon thickness is 50 μm, then the calculated cooling rate is -2.356×106 K/s. Fig.2 shows the relationship between the cooling rates and the ribbon thickness by theoretical calculation. From Fig.2, we know that the bigger the cooling rate the lower is the ribbon thickness. By far, the thickest aluminum amorphous ribbon by melt spinning is 140 μm[14], the cooling rate of which is up to 106 K/s according to above theoretical analysis. This result agrees very well with other estimated values reported previously[15,16]. It also makes sure that aluminum is the marginal glass forming ability of alloys.
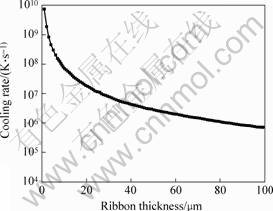
Fig.2 Relationship between cooling rates and ribbon thickness
4 Conclusions
1) Based on heat transfer theory and temperature gradient theory, the relationship between amorphous alloy ribbon thickness and solidification time is derived according to the boundary conditions of ribbon-copper wheel. The cooling rate of amorphous alloy ribbons can be calculated more simply than according to suppression nucleation theory.
2) The cooling rates of aluminum based amorphous ribbons are calculated based on the relationship between the ribbon thickness and solidification time. The higher the cooling rate is the lower the aluminum ribbonthickness. The critical cooling rate is larger than 106 K/s to obtain aluminum amorphous ribbon. The calculated results agree very well with other values reported previously.
3) The results of heat transfer investigation will contribute to preparation bulk amorphous alloys.
4) Eqn.(17) can be recommended for engineering estimations of heat transfer conditions between melt and cooling wheel.
References
[1] INOUE A. Amorphous, nanoquasicrystalline and nanocrystalline alloys in Al-based systems[J]. Progress in Materials Science, 1998, 43(5): 365-520.
[2] TAKAYAMA S. Amorphous structures and their formation stability[J]. Journal of Materials Science, 1976, 11(1): 164-185.
[3] HE Sheng-jing, GAO Li-ru. Amorphous Materials and its Use[M]. Beijing: China Machine Press, 1987. (in Chinese)
[4] HNG H H, LI Y, NG S C, et al. Critical cooling rates for glass formation in Zr-Al-Cu-Ni alloys[J]. Journal of Non-Crystalline Solids, 1996, 208( ): 127-138.
[5] KIM Y J, JOHN W L, RULISON A J. Metallic glass formation in highly undercooled Zr41.2Ti13.8Cu12.5Be22.5 during containerless electrostatic levitation processing[J]. Appl Phys Lett, 1994, 65(17): 2136-2138.
[6] KUBICAR L. Analysis of heat transfer in the splat cooling technique[J]. Mat Sci Eng A, 1991, A133 (1): 755-757.
[7] WANG G X, MATTHYS E F. Modelling of rapid solidification by melt spinning:Effect of heat transfer in the cooling substrate[J]. Mater Sci Eng A, 1991, A136(2): 85-97.
[8] GRANASY L, LUDWIG A. Heat transfer in the single roller quenching methods[J]. Mater Sci Eng A, 1991, A133(1): 751-754
[9] WANG Xiao-jun, CHENG Xue-ding, YU Wei-yuan, et al. Estimation of cooling rate of magnesium based amorphous ribbons prepared by melt spinning method[J]. Journal of Lanzhou University of Technology, 2004, 30(3): 11-13.(in Chinese)
[10] ZHANG Hong-ji. Heat Transfer[M]. Beijing: Higher Education Press, 1992. (in Chinese)
[11] Compile Group. Handbook of Applied Chemistry[M]. Beijing: Science Press, 2001. (in Chinese)
[12] HOLMAN J P. Heat Transfer[M]. New York: McGraw-Hill Book Company, 1989.
[13] CHEN Ping-chang, ZHU Lu-mei, LI Zan. The Principle of Material Forming[M]. Beijing: China Machine Press, 2002. (in Chinese)
[14] WANG Seng-hai, BIAN Xiu-fang and JIA Yu-bao. Formation of aluminum based ultra-thick amorphous ribbon[J]. Scientific Bulletin, 2003, 48(14): 1521-1523. (in Chinese)
[15] DONALD I W, DAVIES H A. Prediction of glass-forming ability for metallic systems[J]. Journal of Non-Crystalline Solids, 1978, 30(1): 77-85.
[16] MARINGER R E, MOBLEY C E. Rapidly quenched metals 3 [A]. Proceedings of the Third International Conference on Rapidly Quenched Metals[C]. Brighton, 1978. 44-49.
(Edited by LONG Huai-zhong)
Foundation item: Project (2003AA302520) supported by the Hi-tech Research and Development Program of China
Corresponding author: HE Shi-wen; Tel: +86-731-8830406; E-mail: hswcsu@126.com