
Modeling of severe deformation and mechanical properties in
Mg-3Al-1Zn alloy through asymmetric hot-extrusion
CHANG Li-li(常丽丽)1, WANG Yi-nong(王轶农)1, ZHAO Xiang(赵 镶)2
1. Department of Materials Science and Engineering, Dalian University of Technology,
Dalian 116024, China;
2. Key Laboratory for Anisotropy and Texture of Materials, Ministry of Education,
Northeastern University, Shenyang 110005, China
Received 12 June 2008; accepted 5 September 2008
Abstract: One-pass asymmetric hot extrusion performed at 673 K was applied to fabricate an AZ31 magnesium alloy sheet. Finite element method (FEM) was used to model the process of asymmetric hot-extrusion. Simulation results indicate that strain rate gradient through the thickness introduced a grain size gradient along the thickness direction and shear deformation during the asymmetric hot-extrusion results in weakened and tilted (0002) basal texture. The asymmetric hot extrusion effectively weakens the basal texture and improves the ductility at room temperature.
Key words: magnesium alloy; asymmetric extrusion; rigid-plastic FEM; texture; mechanical properties
1 Introduction
Room temperature ductility of magnesium alloys in the second processing strongly depends on the orientation of basal plane, because critical resolved shear stress (CRSS) of basal slip system is much lower than that of non-basal slip systems on prismatic and pyramidal planes at room temperature[1-3]. Primary processing, such as hot rolling and hot extrusion usually leads to a strong basal texture, which results in poor ductility at room temperature[4-7]. Thus, it is important to control the texture during primary processing for improvement of ductility at room temperature during the second processing. MUKAI et al[8] used ECAE method to enhance the room temperature ductility of AZ31 magnesium alloy. Significant improvement in tensile elongation about 50% was achieved. Recently, other methods, such as single roller drive rolling (SRDR) and differential speed rolling (DSR) were also used to introduce shear strain. SRDR and DSR effectively weakened basal texture and improved the ductility and formability of AZ31 magnesium alloy[9-13]. According to the precious studies, DSR and SRDR are potential methods used to improve the ductility of magnesium alloy at room temperature. A very promising application of asymmetric hot extrusion might be the first de- formation step in combination with asymmetric rolling. In the present study, one-pass asymmetric hot-extrusion was performed to fabricate the AZ31 magnesium alloy sheet and the resulting microstructure was examined. Finite element method (FEM) was applied to model the process of asymmetric and normal hot-extrusion. Variations of strain rate during asymmetric hot-extrusion were tracked.
2 Simulation models and experimental methods
The procedure of one-pass asymmetric extrusion, proposed in this study, is schematically shown in Fig.1. One-pass asymmetric extrusion can be easily conducted by an extrusion die with a chamfer (45? in this study) on one side. By one-pass asymmetric extrusion, a large amount of shear deformation can be introduced through the thickness of the extruded sheet by the die with a chamfer on one side.
The chemical composition of the as-received AZ31
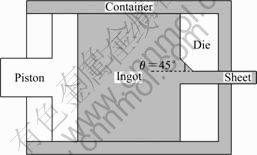
Fig.1 Schematic diagram of asymmetric extruding in present study
billet used in this study is Mg-3.02%Al-1.01%Zn- 0.30%Mn (mass fraction). This alloy is a solution hardened alloy with minimum precipitation. The as-received billet possesses nearly equiaxed grains around 75 μm and the diameter of the ingot is 50 mm. One-pass asymmetric extrusion was conducted by a die with 45? chamfer on one side at a container temperature of 673 K with the extrusion speed of 10 mm/s, resulting in a sheet of 10 mm in width, 5 mm in thickness, as shown in Fig.1. The microstructures of the samples were examined under optical microscope and average grain sizes were determined using intercept method. Four pole figures, {0002}, {
}, {
} and {
} were measured by X-ray diffraction with Co Ka radiation up to a tilt angle of 70? using the Schultz reflection method. The orientation distribution function (ODF) was calculated from the experimental pole figures data by using the series expansion method.
In order to examine the distribution characteristics of textures and microstructures along the through- thickness direction in the asymmetrically extruded sheet, the extrusion-transverse direction (ED-TD) planes on the top surface (denoted as the asymmetrically extruded sheet on chamfer side), 1/4 surface (1/4S), 1/2 surface (1/2S), 3/4 surface (3/4S) and bottom surface, respectively, were used for texture and microstructure examination, as shown in Fig.2.
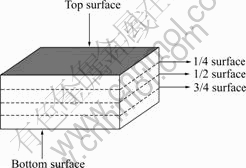
Fig.2 Samples for microstructure and texture examination
Samples labeled by A, B and C for tensile test are presented as top, center and bottom regions in the sheet, respectively, as shown in Fig.3, where ND means normal direction; and TD means transverse direction. Tensile tests were carried out along the extrusion direction (ED). The gauge length, width and thickness of the tensile specimens were 6, 3 and 1.5 mm, respectively. Tensile specimens were prepared using electrical-discharge machining from the extruded sheet. Tensile tests were conducted using WD-3010 universal testing machine with an initial rate of 1×10-3 s-1 at room temperature. All tests were repeated three times at least.
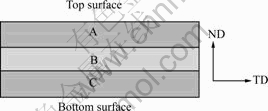
Fig.3 Samples for tensile test in present AZ31 sheet
The commercial code DEFORM was used to model the asymmetric hot-extrusion process. Hot compression tests were performed on a Gleeble 1500 thermal simulation machine at temperatures ranging from 473 to 723 K with different strain rates from 1×10-3 to 1 s-1. The flow stress curves of the AZ31 alloy for different strain rates at 673 K can be fitted into the form of power law as follows:
, where
is effective stress, k is strength coefficient, ε is the effective strain, n is strain-hardening exponent,
is effective strain rate, and m is exponent of strain rate sensitivity. The flow stress data of AZ31 alloy were imported into DEFORM. In the simulation, the billet was defined as a plastic body, while the top and bottom dies were rigid ones. There is no heat transfer between the extruded billet and walls of the container or surface of the die. Friction between the billet and dies was considered as the constant shear friction and a friction coefficient of 0.3 was applied to the extruding model. The dies and billet temperature was 673 K, and the velocity of the top die was 0.2 mm/s. In order to obtain higher precision, the billet was divided into 75 839 tetrahedral elements and 16 759 nodes, as shown in Fig.4(a). Point tracking was used to analyze variations of strain rate during procession and point position for point tracking is shown in Fig.4(b). For comparison, normal extrusion was simulated and simulation conditions were the same as asymmetric hot-extrusion, except the die had no chamfer.
3 Results and discussion
In Fig.5, point positions at different steps during asymmetric hot-extrusion were marked. Fig.6 shows variations of strain rate at different steps during the extrusion and 1, 2, 4, 5 in the figure were used to label Step 1, 2, 4, 5, respectively.
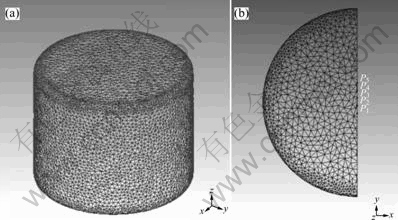
Fig.4 Finite element model of asymmetric hot-extrusion(a) and point position for point tracking during the extrusion(b)
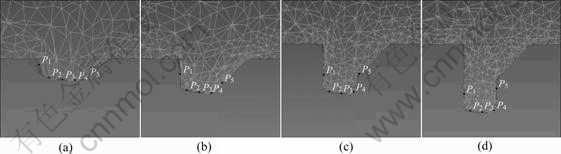
Fig.5 Point position of different steps during asymmetric hot-extrusion: (a) Step 1; (b) Step 2; (c) Step 4; (d) Step 5
As seen in Figs.5(a) and (c), point P1 and P5 pass the entrance and exit of the die with a chamfer at Steps 1 and 4, respectively. While extrusion starts, material around the entrance is crushed into the die. The fact is that stress and strain rate peak values appear where large deformation happens. When P1 and P5 pass
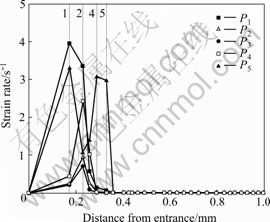
Fig 6 Strain rates of point P1, P2, P3, P4 and P5
the entrance of the die, large deformation happens, therefore, an apparent peak value in strain rate curve of points P1 and P5 appears at Step 1 as shown in Fig.6. In Fig.6, strain rate curves of P1, P2, P3 and P4 almost have the same shape while those of P1 and P5 are dramatically different. Strain rates of P1 P2, P3 and P4 increase with the deformation and have only one peak value at Step 1 for P1 and Step 2 for P2, P3, P4, respectively. However, strain rates of P5 reach the first peak value at Step 1 and another peak strain rate at Step 4. The reason is that P5 suffers severe deformation at the beginning of extrusion and reaches a strain rate peak value at Step 1, afterwards, P5 passes the exit of the asymmetric die, and significant deformation is given to P5, therefore, the second peak strain rate emerges. Through calculating the area below the strain rate curves of P1—5 from Fig.6 to evaluate the average strain rate during the asymmetric hot-extrusion process, it can be seen that strain rate of P5 during the whole deformation is higher than that of P1. Strain rates of P2 and P3 are all the same, while strain rate of P4 is higher than that of P2 and P3. The relationship between the average recrystallization grain size (d) and the Zener-Hollomon parameter (Z) during dynamic recrystallization is given by
. The temperature corrected strain rate Z is given by
, where
is strain rate, Q is activation energy for the deformation, T is temperature and R is gas constant[14-15]. Based on the present asymmetric extrusion process modeling, the strain rate throughout the thickness in the asymmetric hot-extruded sheet is not uniform. According to the above equations, simulation results suggest that the top layer is imposed gtearter strain rate than that of middle and bottom layer, resulting in the smaller grain size in the top layer and larger grain size in middle and bottom layer.
Optical microstructures of the ED-TD plane for different layers in asymmetrically extruded AZ31 alloy sheet are shown in Fig.7. After hot-extrusion, grains are refined to smaller than 4 μm in all layers. Asymmetrically hot-extruded sheet has equiaxed grains, indicating that intensively dynamic recrystallization takes place during extrusion process. However, unlike normal extrusion, due to different strain rates existing in the different layers, there is a light grain size gradient throughout the thickness in the sheet. The average grain sizes of the AZ31 specimens in different layers are listed in Table 1. Through analyzing model and experiment results, it can be seen that the experiment results confirm the variations of strain rate of P1—5 in the modeling.
Table 1 Summary of average grain size in varied positions of present AZ31 sheet
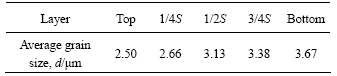
The grid distortions during normal hot-extrusion and asymmetric hot-extrusion are obtained from the FEM analysis and compared to each other in Fig.8.
In normal hot-extrusion, the grids maintain the symmetry with respect to the middle layer during hot-extrusion, and the horizantal lines of the grids become convex toward the extruding direction. In asymmetric hot-extrusion, however, the horizantal lines of the grids are asymmetric with respect to the middle layer, and the layer without shear deformation is close to the sheet surface extruded without an chamfer. It is noted that during the asymmetric hot-extrusion, shear deformation of the bottom layer increases from the entrance while that of top layer increases from a certain distance from the entrance.
Fig.9 shows (0002) pole figures at different positions in the asymmetrically hot-extruded AZ31 sheet. It can be clearly seen from Fig.9(a) that the texture in top surface is characterized by pronounced tilted (0002) basal plane towards the extrusion direction by around 15?. The (0002) pole figures in 1/4S, 1/2S and 3/4S present the similar texture characteristic, namely exhibit weak and scattered (0002) plane toward extrusion direction, especially toward transverse direction, as shown in Figs.9(b), (c) and (d), respectively. As seen in Fig.8, grids distortion in the bottom layer is almost the same as that in surface layer of normal hot-extrusion, therefore, the pole figure in bottom surface is characterized by pronounced (0002) basal texture, which is similar with conventional hot extrusion or hot rolling. This also reveals that (0002) texture intensity in the top surface (max 21) is remarkably lower than that in bottom surface (max 85). The texture intensities from 1/4S, 1/2S and 3/4S are similarly weak to each other.
The differences of textures in different positions should be attributed to the characteristics of the asymmetric extrusion processing. According to the grids distoration of asymmetric hot-extrusion, it is suggested that the top layer is imposed with the maximum asymmetric shear deformation in comparison by the bottom layer during asymmetric extrusion, which results in the tilt of basal texture towards the extrusion direction. From the experimental result of texture evolution, it can also be found that (0002) basal textures will be weakened and scattered along the thickness direction by asymmetric extrusion except for the bottom surface. However, the mechanisms of texture evolution in the present alloy sheet need further investigation.
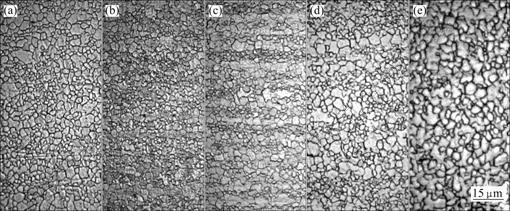
Fig.7 Optical microstructures of ED-TD plane of asymmetrically hot-extruded AZ31 square bar: (a) top surface; (b) 1/4 surface; (c) 1/2 surface; (d) 3/4 surface; (e) bottom surface
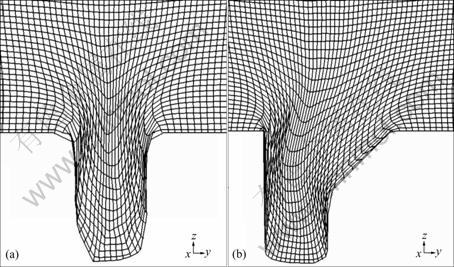
Fig.8 Comparation of grid distortion: (a) Normal hot-extrusion; (b) Asymmetric hot-extrusion
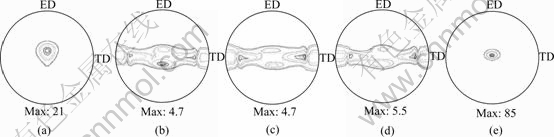
Fig.9 (0002) pole figures in asymmetrically hot-extruded AZ31 sheet: (a) Top surface; (b) 1/4S; (c) 1/2S; (d) 3/4S; (e) Bottom surface
The typical engineering stress—strain relationship at room temperature obtained from top, center and bottom regions A, B and C in the asymmetrically hot-extruded AZ 31 alloy sheet are shown in Fig.10. The results indicate that ductility of sample A (top region) and sample B (center region) is greatly improved compared with sample C (bottom region). The yield stress of sample A exhibits near half value compared with that of sample C, although the average grain size of sample A is slightly smaller than that of sample C, indicating that the grain size is not the dominant factor for yield stress (from the perspective of the Hall-Petch relation). Therefore, the low value of yield stress in sample A compared with sample C is owing to the difference of texture in the two samples. The ultimate tensile stress of sample A exhibits almost the same value as the sample C. The mechanical properties of sample B are between those of sample A and sample C. It is noticed that sample A exhibits a remarkable strain hardening and a large uniform elongation compared with samples C and B, as shown in Fig.10. The remarkable strain hardening and improved uniform elongation can be related to the modified crystal orientation. Therefore, it is suggested that the high Schmid factor for basal slip will easily lead to the operation of basal slip systems, which results in the low yield stress. Meanwhile, the easy operation of basal slip would bring out a high additional shear stress at grain boundaries (compatibility stresses) for the fine-grained polycrystalline magnesium alloys[1],
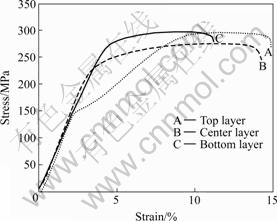
Fig.10 Engineering stress—strain curves of sample A, B and C
which will induce the non-basal a and a+c slips as accommodation of slip deformation. When flow stress increases to some degree, twinning occurs as an additional deformation mechanism even in a fine-grained alloy. Therefore, the intense interactions of multiple deformation models will then bring about a rapid work hardening and a large uniform elongation in sample A. Further microstructural investigation of deformed structure is underway to clarify the deformation mechanism of the present ductile magnesium alloy.
4 Conclusions
1) Strain rate in different layers of the sheet accumulated during asymmetric extrusion is not uniform. Different stain rates in different layers during the process result in a grain size gradient throughout the thickness.
2) Shear deformation during the asymmetric hot-extrusion leads to weakened and scattered (0002) basal texture.
3) Ductility of AZ31 magnesium alloy produced by asymmetric hot-extrusion can be improved by inclined and weakened basal texture, while yielding stress is brought down.
References
[1] KOIKE J, KOBAYASHI T, MUKAI T, WATANABE H, SUZUKI M, MARUYAMA K, HIGASHI K. The activity of non-basal slip systems and dynamic recovery at room temperature in fine-grained AZ31B magnesium alloys [J]. Acta Materialia, 2003, 51(7): 2055-2065.
[2] CHEN Y J, WANG Q D, LIN J B, ZHANG L J, ZHAI C Q. Microstructure and mechanical properties of AZ31 Mg alloy processed by high ratio extrusion [J]. Trans Nonferrous Met Soc China, 2006, 16(S3): S1875-S1878.
[3] PEREZ-PRADO M T, DEL VALLE J A, RUANO O A. Achieving high strength in commercial Mg cast alloys through large strain rolling [J]. Mater Lett, 2005, 59(26): 3299-3303.
[4] PEREZ-PRADO M T, RUANO O A. Texture evolution during annealing of magnesium AZ31 alloy [J]. Scripta Materialia, 2002, 46(2): 149-155.
[5] SRINIVASAN A, CHOWDHURY S G, SRIVASTAVA V C, SWAMINATHAN J, PODDAR P,DE P K. Microstructural and textural evolution during large strain hot rolling (LSR) of Mg-Al (AZ31) alloy [J]. Materials Science and Technology, 2007, 23(11): 1313-1320.
[6] WALDE T, RIEDEL H. Modeling texture evolution during hot rolling of magnesium alloy AZ31 [J]. Materials Science and Engineering: A, 2007, 443(1/2): 277-284.
[7] WANG Y N,HUANG J C. Texture characteristics and anisotropic superplasticity of AZ61 magnesium alloy [J]. Mater Trans, 2003, 44(11): 2276-2281.
[8] MUKAI T, YAMANOI M, WATANABE A, HIGASHI K. Ductility enhancement in AZ31 magnesium alloy by controlling its grain structure [J]. Scripta Mater, 2001, 45(1): 89-94.
[9] JEONG H G, JEONG Y G, YOON D J, CHOI S,KIM W J. The effect of differential speed rolling on microstructure and mechanical properties of an AZ31 alloy sheet [J]. Diffusion and Defect Data Part B (Solid State Phenomena), 2006, 116/117: 235-238.
[10] KIM S H, YOU B S, DONG YIM C, SEO Y M. Texture and microstructure changes in asymmetrically hot rolled AZ31 magnesium alloy sheets [J]. Materials Letters, 2005, 59(29/30): 3876-3880.
[11] JI Y H, PARK J J, KIM W J. Finite element analysis of severe deformation in Mg-3Al-1Zn sheets through differential-speed rolling with a high speed ratio [J]. Materials Science and Engineering A, 2007, 454/455: 570-574.
[12] WATANABE H, MUKAI T, ISHIKAWA K. Differential speed rolling of an AZ31 magnesium alloy and the resulting mechanical properties [J]. Journal of Materials Science, 2004, 39(4): 1477-1480.
[13] WATANABE H, MUKAI T, ISHIKAWA K. Effect of temperature of differential speed rolling on room temperature mechanical properties and texture in an AZ31 magnesium alloy [J]. Journal of Materials Processing Technology, 2006, 182(1/3): 644-647.
[14] BARNETT M R, NAVE M D, BETTLES C J. Deformation microstructures and textures of some cold rolled Mg alloys [J]. Materials Science and Engineering A, 2004, 386(1/2): 205-211.
[15] WANG Y, HUANG J C. Texture analysis in hexagonal materials [J]. Materials Chemistry and Physics, 2003, 81(1): 11-26.
(Edited by CHEN Can-hua)
Foundation item: Project (50471069) supported by the National Natural Science Foundation of China
Corresponding author: WANG Yi-nong; Tel: +86-411-84708441; Fax: +86-411-84709284; E-mail: wynmm@dlut.edu.cn