
Electrochemical deposition of hydroxyapatite coatings on titanium
ZHANG Yuan-yuan(章媛媛), TAO Jie(陶 杰), PANG Ying-chun(庞迎春),
WANG Wei(王 炜), WANG Tao(汪 涛)
College of Material Science and Technology, Nanjing University of Aeronautics and Astronautics,
Nanjing 210016, China
Received 14 June 2005; accepted 13 February 2006
Abstract: Hydroxyapatite coatings were prepared on titanium substrate by electrochemical deposition technology, in which the electrolyte was 0.042 mol/L Ca(NO3)2 and 0.025 mol/L (NH4)2HPO4 with pH 4.4 adjusted by dilute HNO3 and NH4OH. The morphology and phase composition of the coatings were investigated by scanning electron microscopy(SEM) and X-ray diffractometry(XRD). The effect of the deposition voltage and electrolyte concentration on the morphology and the structure of the coating was also discussed. The results show that coating thickness increases and the morphology changes from porous form to actionomprphic-assembled form with increasing deposition voltage(from 1 V to 3 V). In addition, it is found that the anodic oxidation of the titanium is effective in improving the tear strength between the HA coatings and the Ti substrate.
Key words: titanium; hydroxyapatite; anodic oxidation; electrodeposition
1 Introduction
Titanium implants have been used widely for various types of bone-anchored reconstructions due to their excellent corrosion resistance and mechanical properties. However, titanium exhibits poor osteoinductive properties, fortunately, which has been resolved recently by coating the metal with a layer of bioceramic, especially hydroxyapatite (Ca10(PO4)6(OH)2, hereafter HA), which is the major inorganic component of natural bone and able to accelerate bone ingrowth onto the surface of implant during the early stages after implantation[1].
In the past decades, several coating methods have been developed to deposit HA onto titanium surface, including plasma spraying, ion beam sputtering, sol-gel, electrophoretic deposition, and electrochemical deposition, etc[2-7]. Among these methods, plasma spraying is the most popular method for coating on titanium implant surfaces. However, the high temperature of the plasma spray usually generates the decomposition of the HA. Moreover, plasma spray coating technique is not capable of producing a uniform HA coating on implant with a complex shape.
Compared with plasma spray, electrochemical deposition has unique advantages due to its capability of forming uniform coating and simple setup. In addition, the deposition processing can be conducted at room temperature and the morphology of coating can be controlled easily by varying the electrochemical potential and electrolyte concentration[8]. However, the tear strength of HA coating produced by electrochemical deposition is much lower than that by the plasma spray. Some researchers have demonstrated that the addition of ethanol[9] or H2O2[10] to the electrolyte solutions could improve the mechanical properties of HA coating. HU et al[11] prepared hybrid bioceramic coatings of HA/poly (vinyl acetate) on Ti-6Al-4V alloy, which exhibited a better tear strength. Recently, the pretreatment of Ti substrate has been introduced. HE et al[12] deposited a thin Al film on Ti substrate and then applied anodization and hydrothermal treatment, the calcium phosphate grows from the holes of anodized aluminum oxide during the coating process. CHENG et al[13] fabricated thin HA layer on the Ti substrate, covered with the compact anodic oxidation film using the pre-treating method of anodic oxidation. YANG et al[14] prepared the bioactive titanium metal via anodic oxidation treatment. Although, the electrochemical HA coating and pre-treating routes become more and more important, the investigation on electrochemical deposited HA coating on the porous anodized Ti substrate has not been reported up to date.
Therefore, this study is aimed at discussing the characteristics of the electrochemically deposited HA coatings on porous anodized titanium and improving the mechanical properties of HA coating by pre-treating titanium with anodic oxidation method.
2 Experimental
2.1 Anodic oxidation of titanium
Commercial pure titanium sheets from Nanjing Bao Se Titanium Industry Co, Ltd were cut into specimens with dimensions of 40 mm×25 mm×1 mm. Then the specimens were cleaned with acetone in an ultrasonic bath and rinsed with distilled water. Before anodic oxidation, the specimens were polished chemically in a mixture of 50%HF+50% (volume fraction) HNO3 (1∶1 in volume ratio) for about 10 s and rinsed with distilled water, and then dried with a hair dryer.
0.5 mol/L H2SO4 solution was used as electrolyte for anodic oxidation. The copper sheet worked as a cathode and the titanium sheet worked as an anode. The distance between the two sheets was 4.0 cm. The power(KDA/50A/250V)supplied 120 V voltage for 10 min. During the treatment, the electrolyte was stirred to maintain the homogeneity of the temperature and composition. After anodic oxidation, the titanium was rinsed with distilled water and dried by hair dryer.
2.2 Electrochemical deposition of HA
The electrolyte used in this study contained 0.042 mol/L Ca(NO3)2 and 0.025 mol/L (NH4)2HPO4 and its pH value was adjusted to 4.4 by dilute HNO3 and NH4OH. Titanium sheet was used as a cathode and a larger surface titanium plate as the counter-electrode. The deposition was carried out with WYJ-3A direct current power and the time was kept for 2 h. After deposition, the specimens were rinsed in distilled water and dried in air, then soaked in 1 mol/L NaOH solution at 80 ℃ for 2 h.
The formation process of HA may be a combination of several reactions[15]. Firstly, the electrolyte undergoes an equilibrium reaction as
(1)
Secondly, with the aid of the electric field, the water at the cathode surface is decomposed into hydrogen gas and hydroxide ions:
(2)
The formation of OH- can enhance the reaction in Eqn.(1) to produce
.
Finally, the
combines with Ca2+ to produce a CaHPO4?2H2O precipitation and deposits on the surface of the substrate:
(3)
When the alkaline treatment is applied to the coated samples, OH- in the solution causes the following reaction to take place:
(4)
2.3 Characterization and test
Field emission scanning electron microscopy(SEM) measurements were performed with an LEO-1530VP microscope operated at 10 kV. The phase composition of the coatings was identified by X-ray diffractometry(XRD, BRUKER D8 ADVANCE, Cu Kα). The tear strength of the HA coating was tested by universal material testing machine(CMI5105) according to ASTM F 1044.
3 Results and discussion
3.1 XRD analysis of coatings
Fig.1 shows the XRD pattern of the specimen after electrochemical deposition and treatment in 1 mol/L NaOH solution. It shows that all reflections can be indexed readily to the standard HA patterns and Ti. The appearance of Ti reflections indicates that the coating deposited on the Ti substrate should be quite thin.
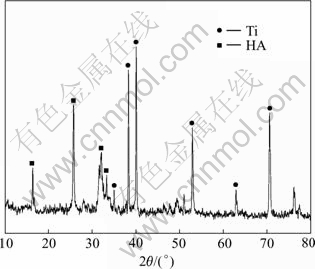
Fig.1 XRD pattern of HA coating deposited at 3 V for 2 h followed by alkaline treatment
3.2 SEM observation of HA coating
SEM images clearly show the morphologies of the resulting coatings and indicate that deposition voltage and electrolyte concentration play key roles in the morphology control of the products.
The typical morphology of HA coatings at the depo- sition voltage of 2 V with macroporous feature is shown in Fig.2. The coating consists of thin flakes and its thick- ness is estimated to be approximately 3 ?m (Fig.2(b)). It can be seen from this photo that these flakes develope perpendicularly to the substrate, adjacent curled flakes fuse together on one joint to construct the macroporous structure. The diameter of the pores is about 5 ?m.
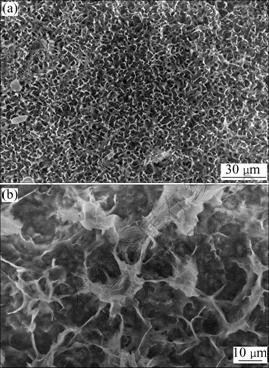
Fig.2 Morphologies of HA coating by electrochemical deposition at 2 V
Increasing the deposition voltage to 3 V results in the formation of HA layered particles that constitutes the coatings deposited on the substrate. A typical SEM image of the unique crystals is presented in Fig.3(a), and this suggests that the coating consists of actinomorphic- assembled lamellar crystals. A high-magnification SEM image shows the rough surfaces of the lamellar particles (Fig.3(b)), and shows the appearance of the oriented- developed needle-like primary crystals. Interestingly, a few double-layered structures are also observed. Fig.3(c) clearly shows the underlayer with porous structures similar to the sample obtained under the deposition voltage of 2 V, and it reveals that the upper-layer consists of large flakes, which also roughly shows the appearance of oriented-developed acicular crystals. The above results suggest that the variation of deposition voltage drastically changes the morphology of the HA coatings.
In order to investigate the influence of the electrolyte concentration on HA coating, another set of experiment was carried out, where the deposition voltage was kept at 3 V, the Ca(NO3)2 was increased to 0.25 mol/L and (NH4)2HPO4 to 0.15 mol/L, and the other experimental conditions were kept the same. As shown in Fig.4, the coating composed of actinomorphic-assembled lamellar crystals was also obtained. The lamellar particles are also perpendicular to the substrate. Com- pared with the coating deposited in lower electrolyte concentration, the coating seems to be more compact and possesses a flower-like primary structure owing to the higher reactant concentration providing more com- ponents to the development of the crystals, which also suggests that the electrolyte concentration has no obvious effect on the crystal morphology.
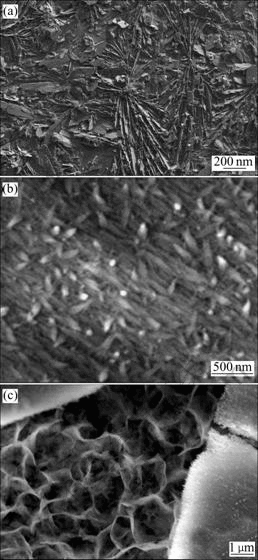
Fig.3 Morphologies of coating by electrochemical deposition in 3 V
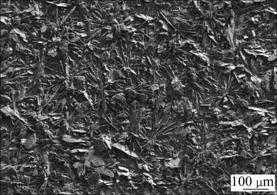
Fig.4 Morphology of coating deposit in high concentration electrolyte at 3 V for 2 h
3.3 Tear strength test
The tear strength of HA coating films was tested according to ASTM F 1044. They were glued to equal sized titanium plates with epoxy resin. The tear strength was carried out with a universal testing machine using a 10 kN load cell and a crosshead speed of 1.0 mm/min [16].
For comparison, two groups of samples were chosen that one group was treated with anodic oxidation, while the other without anodic oxidation. All HA coatings were deposited at voltage of 3 V. For each group, at least five samples were tested. The data in Table 1 are the tear force(F) and tear strength(σb) of HA coatings on titanium with or without anodic oxidation. The average tear strength of the coatings deposited on the titanium without anodic oxidation is about 5.0 MPa, while the average tear strength of the one with anodic oxidation is about 7.3 MPa.
Table 1 Tear strengths of HA coatings on titanium

The improvement of the tear strength may be mainly contributed to the porous TiO2 structure on Ti substrate. Fig.5 shows the typical morphology of Ti substrate after anodic oxidation. The oxide films exhibit porous microstructure with rounded pores. The ambient region around these pores was protuberant. Thus the surface of the Ti substrate is much rougher, which may be helpful in forming mechanical interlock between the Ti substrate and the HA coating. In addition, the pores are approximately 100-200 nm in diameter, in which the nucleation of calcium phosphate crystal may occur at the
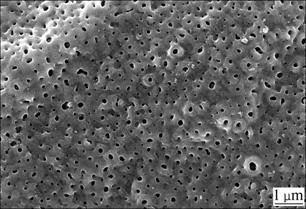
Fig.5 Morphology of Ti substrate with anodic oxidation at 120 V after 10 min
beginning of the reaction leading to the HA crystals embedded in the substrates and the improvement in the tear strength of HA coating. Furthermore, the chemical interactivity between HA and TiO2 has been found at the temperature beyond 900℃[17,18]. Although the temperature was much lower than 900 ℃ during the electrochemical coating process, the effect of chemical interaction between HA and TiO2 on the improvement of tear strength could not fully excluded, which needs to be investigated further via TEM observation of the interface between both layers.
4 Conclusions
HA coatings, with both porous and actinomorphic-assembled lamellar structures, on Ti substrates can be conveniently fabricated through an electrochemical deposition route with the increasing voltage. Different to deposition voltage, the electrolyte concentration has no obvious effect in changing the morphology of HA coatings. Additionally, the anodic oxidation, a substrate pre-treating process, prior to electrochemical deposition can improve the tear strength of the HA coatings on Ti substrate.
References
[1] Hench L L. Bioceramics: from concept to clinic [J]. J Am Ceram Soc, 1991, 74(7): 1487-1510.
[2] Lü Y P, Li M S, Wang J H, Sun R X, Li S T, Zhu R F. Cross-sectional analysis on microstructure of plasma-sprayed HA+TiO2 composite coatings on titanium substrate [J]. Trans Nonferrous Met Soc China, 2004, 14(6): 1139-1144.
[3] Khor K A, Gu Y W, Cheng P. Plasma spraying of functionally graded hydroxyapatite/Ti-6Al-4V coatings [J]. Surf Coat Tech, 2003, 168: 195-201.
[4] Wang C X, Chen Z Q, Guan L M, Liu Z, Wang P, Zheng S, Liao X. Structural characterization of ion beam sputter deposited calcium phosphate coatings [J]. Surf Coat Tech, 2002, 130(1): 39-45.
[5] Metikos-Hukovic M, Tkalcec E, Kwokal A, Piljac J. An in vitro study of Ti and Ti-alloys coated with sol-gel derived hydroxyapatite coatings [J]. Surf Coat Tech, 2003, 165: 40-50.
[6] Wei M, Ruys A J, Swain M V, Kim S H, Milthorpe B K, Sorrell C C. Interfacial bond strength of electrophoretically deposited hydroxyapatite coatings on metals [J]. J Mater Sci Mater Med, 1999, 10(7): 401-409.
[7] Han Y, Fu T, Lu J, Xu K. Characterization and stability of hydroxyapatite coatings prepared by electrodeposition and alkaline-treatment process[J]. J Biomed Mater Res, 2001, 54(1): 96-101.
[8] Kuo M C, Yen S K. The process of electrochemical deposited hydroxyapatite coatings on biomedical titanium at room temperature [J]. Mater Sci Eng C, 2002, 20: 153-160.
[9] Wang F, Wu X Q, Sheng C, Xu X Y, Wu X H, Zhang Z R. Effect of ethyl alcohol on calcium phosphate coating by electrodeposition [J]. Journal of Shanghai Normal University (Nature Science), 2003, 32(2): 52-56.
[10] Zhao Z W, Li H G, Sun P M, Li Y J, Huo G S, Masazumi O, Ryoichi I. New method for electro-chemical deposition of bioceramic coatings [J]. Rare Metals and Cemented Carbides, 2002, 30(1): 6-8.
[11] Hu H B, Lin C J, Hu R, Leng Y. A study on hybrid bioceramic coatings of HA/poly (vinyl acetate) co-deposited electrochemically on Ti-6Al-4V alloy surface [J]. Mater Sci Eng C, 2002, 20(1-2): 209-214.
[12] He L P, Wu Z J, Chen Z Z. In-situ growth of nanometric network calcium phosphate/porous Al2O3 biocomposite coating on Al-Ti substrate [J]. The Chinese Journal of Nonferrous Metals, 2004, 14(3): 460-464.(in Chinese)
[13] Cheng X R, Wang J W, Wang Y N, Wang G, Zhao L Q. Preparation of thin hudroxyapatite layers on cp titanium through anodic oxidation followed with hydrothermal treatment [J]. J Biomed Eng, 2002, 19: 378-380.
[14] Yang B C, Uchida M, Kim H M, Zhang X D, Kokubo T. Preparation of bioactive titanium metal via anodic oxidation treatment [J]. Biomaterials, 2004, 25(6): 1003-1010.
[15] Huang L Y, Xu K W, Lu J. A study of the process and kinetics of electrochemical deposition and hydrothermal synthesis of hydroxyapatite coatings [J]. Materials in Medicine, 2000, 11(11): 667-673.
[16] Wei M, Ruys A J, Milthorpe B K, Sorrell C C. Electrophoretic deposition of hydroxyapatite coatings on metal subtrates: A nanoparticulate dual-coating approach [J]. Journal of Sol-Gel Science and Technology, 2001, 21: 39-48.
[17] Weng J, Liu X, Zhang X, Ji X. Thermal decomposition of hydroxyapatite structure induced by titanmium and its dioxide [J]. Mater Lett, 1994, 13: 159-161.
[18] Schoes S, Dorner-Reisel A, Wang T, Brendler e, Mueller e. Investigation of hydroxyapatite/titania composites by means of infrared and 31P MAS NMR spectroscopy [J]. Biomed Techn, 2004, 49(2): 586-597.
Corresponding author: TAO Jie; Tel: +86-25-52112900; Fax: +86-25-84895378; E-mail: taojie@nuaa.edu.cn
(Edited by LONG Huai-zhong)