J. Cent. South Univ. (2012) 19: 380-383
DOI: 10.1007/s11771-012-1015-4
Ultrasonic plastification speed of polymer and its influencing factors
JIANG Bing-yan(蒋炳炎)1, 2, HU Jian-liang(胡建良)1, LI Jun(李俊)1, LIU Xiao-chao(刘小超)1
1. State Key Laboratory of High Performance Complex Manufacturing,Central South University, Changsha 410083, China;
2. School of Aeronautics and Astronautics, Central South University, Changsha 410083, China
? Central South University Press and Springer-Verlag Berlin Heidelberg 2012
Abstract: The melt filling difficulty in micro cavity is one of the main challenges for micro-injection molding (MIM). An approach employing ultrasound in MIM was proposed. The approach was extensively studied through experiments with a home-made experimental ultrasonic plastification device. The results of the experiments show that polymer ultrasonic plastification speed increases with ultrasonic supply voltage and plastification pressure. When the ultrasonic supply voltage is 200 V and the plastification pressure is 2.0 MPa, the polymer ultrasonic plastification speed reaches the maximum value of 0.111 1 g/s. The results also indicate that the ultrasonic cavitation effect is the most significant effect of all the three effects during polymer ultrasonic plastification process.
Key words: ultrasonic plastification; plastification speed; ultrasonic cavitation; micro-injection molding
1 Introduction
Developed in 1980s, micro-injection molding (MIM), which produces small parts with milligram scale mass and/or micron scale dimension, has made great advances and gradually establishes itself as one of the key technologies which drives the development of micro-electro-mechanical systems (MEMS) technology due to its many advantages including low-cost mass production and processing polymers [1-3]. However, as an emerging technology, micro-injection molding is facing with many challenges such as difficulties in micro-cavity filling [4-5] and inhomogeneity in microstructure of micro products. It has been reported that the ultrasonic power can significantly decrease the viscosity of polymer melt in extrusion process of polymer [6-12].
Polymer plastification way has a significant effect on the melt flow properties. MICHAELI et al studied ultrasonic plastification way as a new concept plastification way in MIM. The result showed that the melt obtained by ultrasonic plastification can be more homogeneous and very applicable for MIM [13-14]. BRETTHAUER and KAUZLARIC analyzed the potential of ultrasound for low temperature plastification of PMMA both theoretically and experimentally in ultrasonic welding. The results indicated that the yielding due to high shear rates is responsible for the decrease in the necessary temperature for ultrasonic plastification compared with conventional plastification [15]. However, the mechanism of the interaction between polymer and ultrasonic is not concerned.
In the previous research, a new approach, which employs ultrasound in MIM, was proposed, and through experiments it was found that applying ultrasound to polymer plasticization resulted in a more uniform microstructure in polymer melt [16]. In this work, in order to analyze the relationship between ultrasonic and polymer plastification speed as well as the internal mechanisms, the major factors of applying ultrasound in MIM, including polymer ultrasonic plastification speed and its influencing factors, were analyzed.
2 Experimental
2.1 Ultrasonic plastification equipment
The experiments were carried out on the ultrasonic plastification equipment, as shown in Fig. 1. Its parameters are listed in Table 1.
2.2 Material
The material used in experiment is high density polyethylene (HDPE) (Grade: 8008), produced by Lanzhou Chemical Industry Co., Ltd., and its parameters are listed in Table 2.
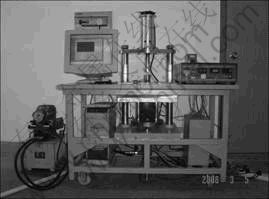
Fig. 1 Ultrasonic plastification equipment
Table 1 Parameters of ultrasonic plastification equipment
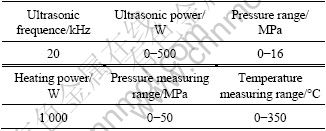
Table 2 Parameters of high density polyethylene (HDPE)
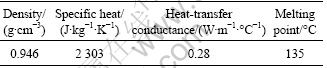
2.3 Experimental method
As shown in Fig. 2(a), at the beginning of ultrasonic plastification process, there were two heat effects among polymer pellets: friction heat effect and viscoelastic heat effect. Polymer pallets were melted because of the acute friction among them induced by the ultrasonic vibration of horn. As a result, the polymer pellets beneath the ultrasonic horn started to become melted, as shown in Fig. 2(b). Meanwhile, the ultrasonic cavitation took place in the polymer melt, which eventually got all the polymer pellets melted. A sensor (PT133-50) which can gage both temperature and pressure, was assembled in
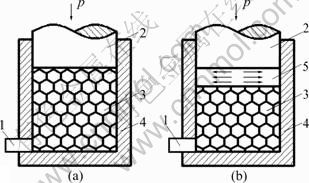
Fig. 2 Ultrasonic plastification process: 1—Sensor; 2—Ultrasonic horn; 3—Polymer pellets; 4—Barrel; 5—Polymer melt
this device to measure the ultrasonic plastification speed of ploymer.
Heat ratio of friction heat effect can be described as [17]
(1)
where q is the heat ratio, p is the average ultrasonic pressure, μ is the friction coefficient between polymer pellets, ω is the ultrasonic rotational frequency, and S is the surface areas of polymer pellet. Equation (1) indicates that the heat ratio of friction heat effect increases with the average ultrasonic pressure.
Visco-elasticity of polymer causes the stress state to fall behind the strain state, as shown in Fig. 3.

Fig. 3 Visco-elasticity of polymer
The delayed energy consumption of polymer is established as [18]
(2)
where σ0 is the critical stress, ε0 is the critical strain, and δ is the phase angle.
In Eq. (2), the delayed energy consumption of polymer increases with stress, strain and phase angle between stress and strain.
The ultrasonic cavitation effect formula is shown as [19]

(3)
where R is the real bubble radius (m), R0 is the initial bubble radius (m),
is the velocity of bubble (m/s),
is the bubble acceleration (m/s2), p0 is the initial pressure (Pa), which is provided by hydraulic system, pv is the gas pressure in the bubble (Pa), pa is the ultrasonic amplitude (Pa), σ is the surface tension of polymer melt (N/m), υ is the kinematic viscosity of polymer melt (m2/s), k is the polytropic index, and ω is the ultrasonic rotational frequency.
The relationship between pressure and ultrasonic cavitation effect is shown in Fig. 4, which is simulated by MATLAB. When the pressure is smaller, the bubble is under less resistance as it grows bigger, so the ultrasonic cavitation effect is more intensive.
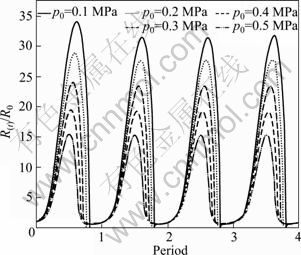
Fig. 4 Relationship between pressure and ultrasonic cavitation effect
3 Results and discussion
3.1 Measurement of ultrasonic plastification speed
The ultrasonic plastification experiments were carried out under different combinations of ultrasonic supply voltage (150, 200 and 250 V) and pressure (1.00, 1.25, 1.50, 1.75 and 2.00 MPa). When the output of sensor reached the maximum value, as shown in Fig. 5, the plastification time was recorded. So, the ultrasonic plastification speed can be measured as the ratio of polymer mass to plastification time. The results are shown in Table 3.
As can be seen in Table 3, when the ultrasonic supply voltage is 150 V and the pressure is 1.00 MPa, the pressure sensor cannot get the pressure of polymer melt, indicating that the ultrasonic cannot make the polymer pellets melted under these parameters. When the ultrasonic supply voltage is 250 V, and pressure is over 1.75 MPa, the real ultrasonic power is over the rated power, so the ultrasonic system cannot work. In order to analyze the relationship among plastification speed, pressure and ultrasonic supply voltage, data from Table 3 are expressed by a curve, as shown in Fig. 6.
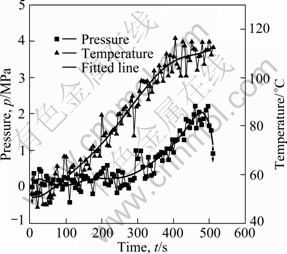
Fig. 5 Measured pressure and temperature during plastification process
Table 3 Ultrasonic plastification speed (g/s)
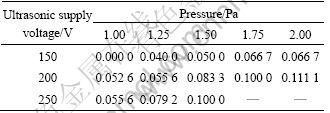

Fig. 6 Relationship among ultrasonic supply voltage, pressure and plastification speed
3.2 Effect of ultrasonic power on ultrasonic plastification speed
As shown in Table 3 and Fig. 6, the plastification speed of polymer increases with the ultrasonic supply voltage. Because the ultrasonic supply voltage determines the ultrasonic energy supply, the stronger the ultrasonic energy supply is, the higher the plastification speed of polymer is.
3.3 Effect of pressure on ultrasonic plastification speed
The plastification speed of polymer increases with the pressure, but the influence tends to be weakened, as shown in Table 3 and Fig. 6. As mentioned before, In the process of ultrasonic plastification, there are three kinds of heat effects, that is, friction heat effect, viscoelastic heat effect and ultrasonic cavitation effect. As discussed above, the friction heat effect and viscoelastic heat effect are increased with pressure, while ultrasonic cavitation effect is reduced with pressure. So this effect is the main cause of the ultrasonic plastification needed to be analyzed.
3.4 Analysis of ultrasonic plastification process
The ultrasonic power changes with ultrasonic supply voltage and pressure during the ultrasonic plastification process. When ultrasonic supply voltage is 200 V, the curves of ultrasonic power under different pressures (1.00, 1.25, 1.50, 1.75 and 2.00 MPa) are obtained in Fig. 7.

Fig. 7 Curve of ultrasonic power under different pressures
As can be seen in Fig. 7, the ultrasonic power increases with the pressure at the first two minutes. The theoretical analysis shows that the friction heat effect and viscoelastic pressure are proportional to pressure, while ultrasonic cavitation is inversely proportional to pressure. At the beginning of the ultrasonic plastification process, the friction heat effect and viscoelastic heat effect increase as the pressure increases. In the later process, the main effect is ultrasonic cavitation, so the ultrasonic cavitation is the most significant effect during the ultrasonic plastification process.
4 Conclusions
1) The experimental results of ultrasonic plastification of polymer show that the ultrasonic plastification speed of polymer increases with ultrasonic supply voltage and plastification pressure.
2) When the ultrasonic supply voltage is 200 V and the plastification pressure is 2.0 MPa, the polymer ultrasonic plastification speed reaches a maximum, 0.111 1 g/s.
3) The results also indicate that the ultrasonic cavitation effect is the most powerful effect of the three effects during the ultrasonic plastification process of polymer.
References
[1] SHA B, DIMOV S, GRIFFITHS C, PACKIANATHER M S. Investigation of micro-injection moulding: Factors affecting the replication quality [J]. Journal of Materials Processing Technology, 2007, 183(2/3): 284-296.
[2] YU Ming-ching, YOUNG Wen-bin, HSU Pe-ming. Micro-injection molding with the infrared assisted mold heating system [J]. Materials Science and Engineering A, 2007, 460/461: 288-295.
[3] LAMERS T, DAVID M, GOODSON K. MEMS industry finding success one step at a time [J]. Microwave Journal, 2004, 47(8): 55-58.
[4] SHA B, DIMOV S, GRIFFITHS C, PACKIANATHER S M. Micro-injection moulding: Factors affecting the replication quality of micro features [C]// The Second International Conference on Multi-Material Micro Manufacture. Grenoble, France, 2006: 269-272.
[5] LIN Huang-ya, YOUNG Wen-bin. Analysis of the filling capability to the microstructures in micro-injection molding [J]. Applied Mathematical Modelling, 2008, 37(4): 1-10.
[6] PENG Bo, WU Hong, GUO Shao-yun, LAI Shih-yaw, JOW Jinder. Static ultrasonic oscillations induced degradation and its effect on the linear rheological behavior of novel propylene based plastomer melts [J]. Polymer Degradation and Stability, 2007, 92(8): 1632-1639.
[7] WU Hong, GUO Shao-yun. Improved properties of metallocene- catalyzed linear low-density polyethylene/polypropylene blends during ultrasonic extrusion [J]. Chinese Journal of Polymer Science, 2007, 25(4): 357-364. (in Chinese)
[8] YU Xiao-feng, LU Chang, WU Hong, GUO Shao-yun. Effect of ultrasonic oscillations on weld line strength of PS, PMMA, and their blends [J]. Journal of Applied Polymer Science, 2006, 102(3): 2990-2997.
[9] ZHAO Li-juan, LI Jiang, GUO Shao-yun, DU Qin. Ultrasonic oscillations induced morphology and property development of polypropylene/montmorillonite nanocomposites[J]. Polymer, 2006, 47(7): 2460-2469.
[10] FENG W, ISAYEV A I. In situ ultrasonic compatibilization of unvulcanized and dynamically vulcanized PP/EPDM blends [J]. Polymer Engineering and Science, 2004, 44(11): 2019-2028.
[11] ISAYEV A I, KUMAR R, LEWIS T M. Ultrasound assisted twin screw extrusion of polymer-nanocomposites containing carbon nanotubes [J]. Polymer, 2009, 91(1): 250-260.
[12] KIM H, YANG H, LEE J W. Effect of viscosity ratio and AN content on the compatibilization of PC-SAN blends during ultrasound-assisted melt mixing [J]. Korea-Australia Rheology Journal, 2005, 17(4): 165-170.
[13] MICHAELI W, SPENNEMANN A, GARTNER R. New plastification concepts for micro injection molding [J]. Microsyst Technol, 2002, 8: 55-57.
[14] MICHAELI W, OPFERMANN D. Ultrasonic plasticising for micro injection moulding [C]// The Second International Conference on Multi-Material Micro Manufacture. Grenoble, France, 2006: 345-348.
[15] BRETTHAUER C, KAUZLARIC D. Particle based modeling of ultrasonic plastification with a yield-stress fluid (simulation and experiments) [C]// Proceeding of Multiscale Materials Modeling Third International Conference. Freigurg, Germany, 2006: 917-920.
[16] HU Jiang-liang, JIANG Bing-yan, LI Jun, LIN Ming-run, WANG Ren-quan. Experimental study of polymer ultrasonic plastification [J]. Journal of Central South Unversity: Science and Technology, 2010, 41(4): 1369-1373. (in Chinese)
[17] QIN Xiang-pei, LI Jian, MENG Hua, LIU Hong-tao. Effects of friction geat on tribological properties of UHMWPE [J]. Tribology, 2005, 125(6): 550-554. (in Chinese)
[18] LU Song, MENG Hui-rong. Thermal analysis of plastic gears [J]. Plastics, 2003, 32(5): 58-60. (in Chinese)
[19] NEPPIRAS E A. Acoustic cavitation[J]. Physics Reports: Review Section of Physics Letters, 1980, 61(3): 159-251.
(Edited by YANG Bing)
Foundation item: Project(107086) supported by the Key Program of Chinese Ministry of Education; Project(2009) supported by the Graduate Degree Thesis Innovation Foundation of Central South University, China
Received date: 2010-11-25; Accepted date: 2011-03-09
Corresponding author: JIANG Bing-yan, Professor, PhD; Tel: +86-731-88836035; E-mail: jby@csu.edu.cn