
Thermal property and microstructure of Al nanopowders produced by two evaporation routes
CHEN Liang(陈 亮)1, SONG Wu-lin(宋武林)1, 2, GUO Lian-gui(郭连贵)1, XIE Chang-sheng(谢长生)1
1. State Key Laboratory of Material Processing and Die and Mould Technology,
Huazhong University of Science and Technology, Wuhan 430074, China;
2. Analytical and Testing Center, Huazhong University of Science and Technology, Wuhan 430074, China
Received 16 September 2008; accepted 16 October 2008
Abstract: Al nanopowders with diameters ranging from 20 to 50 nm passivated by Al2O3 coatings were produced by two different evaporation routes: induction heating evaporation (IHE) and laser-induction complex heating evaporation (LCHE). Thermal property of the nanopowders was investigated by differential thermal analysis (DTA) in dry oxygen environment. The results show that Al nanopowders produced by LCHE have the oxidation enthalpy change (?H) of 3.54 kJ/g, while the ΔH of Al produced by IHE is 1.18 kJ/g. The phase constitution and microstructures of these nanopowders were revealed using X-ray diffraction (XRD) analysis, transmission electronic microscopy (TEM) and high-resolution transmission electronic microscopy (HRTEM). The results show that the two powders have the same composition and mean particle size, as well as the thickness of Al2O3 coatings (3-5 nm). Defects were observed on the surfaces of the particles by LCHE. However, the defects were not detected by HRTEM on the surfaces of the particles by IHE. The results prove that there exists excessive stored energy in Al nanopowders by LCHE because of the nonequilibrium condition brought by laser and the defects are the storage area of the excessive stored energy. Propellants composed of Al nanopowders by LCHE show higher energy level and specific impulse.
Key words: energetic materials; aluminum; nanopowders; laser ablation; excessive stored energy
1 Introduction
Al powders have been broadly used as an important ingredient in energetic materials because of their high energy release, high density and low cost. Conventionally used Al powders are typically micron- sized, however, the usual insuperability problems are agglomeration, uncompleted degree of oxidation and two-phase losses[1]. Today, great attention is paid to Al nanopowders, because of the significant increase of burning rate, lower ignition time and temperature[2-4], which have the capability of solving the problems their micron-sized counterparts meet.
Besides the excellent combustion properties mentioned above, the Al nanopowders exhibit unusual thermal behavior that is originally associated with excessive stored energy due to defects in the crystal lattice or direct energy conversion when preparing[1, 5]. The excessive stored energy could be very beneficial to explosives performance and show high energy level and specific impulse. The concept of stored energy has created high expectations for these powders in energetic materials. Subsequent research, however, demonstrated the absence of stored energy in the Al nanopowders[6-7]. The liberation of energy at low temperatures is rather caused by an oxidation of the particles. Additionally, there has been no direct evidence of the defects in Al particles to date. Therefore, much work is needed to understand the energy storage phenomena inside the powders.
A variety of techniques can be performed to prepare Al nanopowders, including electro-exploded wire[8-9], plasma explosion[10], plasma synthesized process[11], sol-gel[12] and heating evaporation[13]. Among them, the heating evaporation methods based on vaporization of metals followed by condensation and particle formation are being developed. These evaporation methods distinguish themselves from others by the heating apparatus, such as electric cooker, high-frequency induction and laser. A high-frequency power equipped with induction coil and graphite crucible in its center could provide enough heat for melting and evaporating many metals. The beam generated by laser could be focused to a point and then reaches a very high temperature, which is widely used in cutting, welding and surface treatment of metals. Both of the two heating apparatus have an advantage of not disturbing the vacuum system that is vital to the evaporation methods. In this work, two evaporation routes (high-frequency induction and laser as heater respectively) were designed to produce Al nanopowders and the thermal properties especially the excessive stored energy and microstructure of both powders were investigated.
2 Experimental
2.1 Materials preparation
Al nanopowders were prepared using two different evaporation routes: induction heating evaporation (IHE) and laser-induction complex heating evaporation (LCHE). As illustrated in Fig.1, a graphite crucible with an alumina crucible in its center was charged into the induction coil. The bulk Al with a purity of 99.6% was put into the alumina crucible. The chamber was evacuated below 10 Pa and maintained at argon atmosphere pressure of 2 kPa. Then the high-frequency induction power of 5 kW was initiated, and several minutes later, the bulk pure Al was melted.
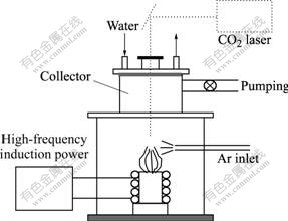
Fig.1 Schematic diagram of equipment applied in LCHE (Equipment of IHE is same as this just without CO2 laser)
Induction current of the induction power was turned up, and then the melted liquid vaporized rapidly. These evaporated Al atoms were quickly cooled through their collision with Ar gas and then Al nanopowders prepared by IHE were formed.
The Al nanopowders prepared by LCHE followed the following routes. When the bulk Al melted by high-frequency induction power mentioned above, continuous wave CO2 laser irradiation (maximum output of 2 kW) with a power of 1.6 kW was incorporated into the system, which resulted in a rapid vaporization of Al. The following processes of condensation and particle formation were the same as those by IHE.
The reactions lasted for about 15 min, and then the powers were turned off. At the same time, gas mixture of argon and air (volume ratio of 20?1) was added into the chamber maintaining a pressure of about 320 Pa to passivate Al nanoparticles. After passivating for about 10 h, the resulting dark gray, air passivated Al nanopowders were collected for further testing and analysis.
2.2 Microstructure observation and thermal property tests
The morphology and internal structure of Al nanopowders were investigated using TEM on a Tecnai G2 20 and HRTEM on a JEM-2100FEL. The phases and crystal structures of the powders were analyzed with XRD (PANalytical B.V. X’Pert PRO) using Cu Kα radiation. The thermal properties of the powders were tested by DTA and TGA. The DTA was tested on a NETZSCH STA 449C thermal analysis system. All the samples of about 2.0 mg charged into alumina crucible were heated at a heating rate of 10 ℃/min from room temperature to 800 ℃ and the experiments were carried out in dry oxygen at 20 mL/min. The TGA was tested on a Pyris1 TGA (PerkinElmer Instrument) with a heating rate of 10 ℃/min from room temperature to 1 000 ℃ and the experiments were carried out in gas mixture of Ar and O2.
3 Results
3.1 Microstructure
The general morphologies and structures of Al nanopowders prepared by the two routes are shown in Fig.2. It can be seen from Fig.2 that the produced nanopowders are well dispersed in a uniform sphere shape and a diameter range from 20 nm to 50 nm. Fig.3 shows that both kinds of particles have a structure of core-shell and the shell Al2O3 coats the core Al tightly. The shell Al2O3 with a thickness of 3-4 nm was formed in the air passivation process to protect the core Al from intensive oxidation or even spontaneous combustion[14].
The XRD patterns of air-passivated Al nanopowders are shown in Fig.4. The strong diffraction peaks can be indexed to metallic Al and the weak ones correspond to Al2O3, which means the sample mainly contains metallic Al and a small quantity of Al2O3. The XRD results are in good agreement with the HRTEM result of the core-shell structure. No diffraction peak from other impurities is detected in the sample, which means the Al nanopowders have high purity.
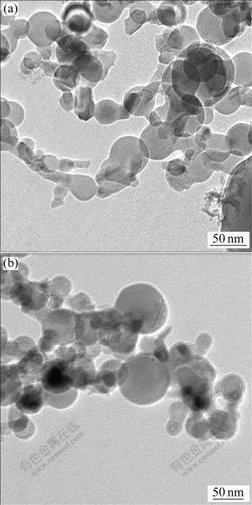
Fig.2 TEM images of Al nanopowders prepared by two routes: (a) IHE; (b) LCHE
3.2 Thermal property
From DTA and TGA curves, different thermal properties of the samples are observed, as shown in Fig.5. Both onset temperatures of the two powders are about 530 ℃, however, the peak temperatures of the powders are 560 ℃ by IHE and 565 ℃ by LCHE. There is an exothermic peak on each DTA curve due to the heat release of the reaction between Al and oxygen (O2), though the peak of the powders by LCHE is sharper than those by IHE. Enthalpy change (?H) determined by the exothermic peak area was calculated by the DTA thermal analysis system. As listed in Table 1, ?H of the
Table 1 DTA and TGA results of Al nanopowders
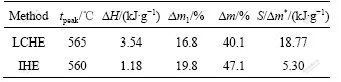
Al nanopowders prepared by LCHE is 3.54 kJ/g, while ?H of the Al nanopowders prepared by IHE is 1.18 kJ/g. There are two mass gains in each TG curve, and the first mass gain corresponds to the exothermic peak of the DTA curve due to the oxidation of Al. The specific heat release is given by the following formula, which is a parameter to determine the ability of energy release:S/?m* =?Hmi/(1.125?m1mi)=?H/(1.125?m1)where S is the heat release of the sample, mi is the initial mass of the tested sample.
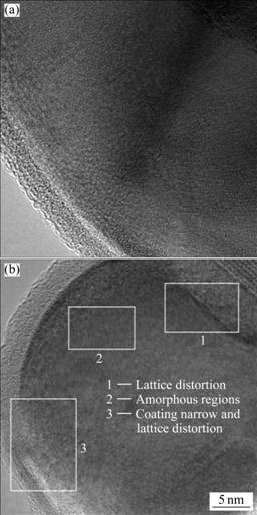
Fig.3 HRTEM images of Al particles: (a) IHE (Regular crystal planes and uniform coating); (b) LCHE
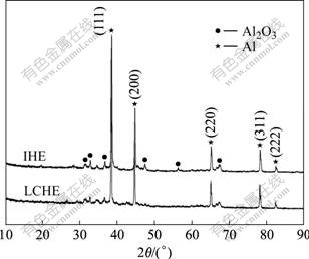
Fig.4 XRD patterns of Al nanopowders prepared by IHE and LCHE
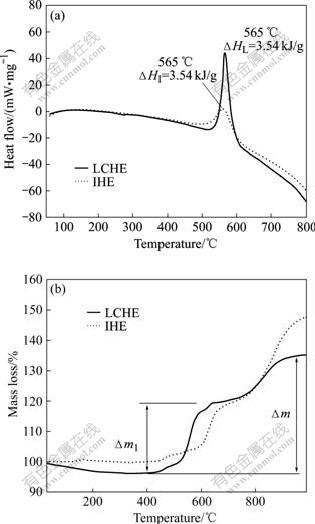
Fig.5 DTA and TGA curves of Al nanopowders prepared by two routes: (a) DTA; (b) TGA
Seen from Table 1, the ability of energy release of the Al nanopowders prepared by LCHE is more than three times of the ones prepared by IHE.
4 Discussion
Many reasons can be contributed to the different thermal properties especially the DTA ones. DTA is an effective analysis method to measure the thermal properties of energetic materials. A lot of factors may influence the DTA results, among them the reaction/carrying gas, heating rates, crucible and mass of the samples are the main influence factors. In this work, the parameters applied in this DTA instrument were fixed: 99.995% purity of O2 was as the reaction gas with a fixed flux of 20 mL/min, heating rates were set at 10 ℃/min, the alumina crucibles were annealed at 1 000 ℃ to exclude the influence of the substance attached to the crucible reacting with carrying gas, the mass of the samples was (2.0±0.1) mg. There were also differences in the DTA results when the conditions of the DTA for the two powders were kept the same and the systematic errors were excluded. Thus, the reasons for differences of the thermal properties exist in the nanopowders themselves.
From Fig.2, it can be seen that there is no obvious difference in the diameter distribution of the two powders. Furthermore, the mean particle diameter estimated by Scherrer formula (D=0.89λ/(Bcosθ), from XRD results) is about 40 nm. Seen from Fig.3, however, the internal structures revealed by HRTEM differ from each other. In Fig.3(a), the crystal planes are of orderliness and the thickness of the alumina coating is uniform. Defects of amorphous regions and lattice distortions as indicated by rectangles in Fig.3(b) are detected. Another difference in Fig.3(b) is that a part of the alumina coating turns narrow (from 4 nm to 2 nm). Evidently, difference of the thermal property is caused by the difference of the internal structure and surface morphology of the powders. However, the different technologies employed in the producing of the powders essentially result in the difference of the structure and morphology of the powders.
As for the technologies applied in the two methods, the IHE follows the conventional evaporation- condensation model[13] (illustrated in Fig.6(a)). The metal (bulk Al) is heated by the inductive resource to its melting point. As the temperature rises to the boiling point of the metal, the atoms of the Al escape from the liquid and collide to form clusters with the help of inert gas (Ar) and the proper atmosphere pressure in the chamber. Then the nanocrystalline particles deposit on the water-cooled wall. In the process of LCHE (illustrated in Fig.6(b)), the bulk Al was heated into liquid state by induction to improve the absorptivity of the target Al to laser. The incorporation of continuous CO2 laser plays a role of laser ablation to the target Al. In this laser ablation process, the energy of the laser beam is transferred to the target metal by the way of photothermal
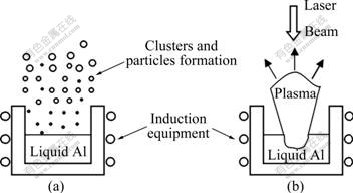
Fig.6 Schematic representation of Al particles formation: (a) Evaporation in IHE; (b) Laser ablation in LCHE
and plasma-assisted ablation[15]. After the focused laser beam (4 mm in diameter) was radiated on the Al liquid for about 1 min, a plasma arc was ignited and rapidly propagated in the reverse direction to the laser beam and in the transverse direction. The plasma expands, cools and condenses into clusters, which continues to migrate away from target Al surface until they are collected on the water-cooled wall of the chamber. The plasma is an ionized gas formed by Al atoms, which absorbs energy of the laser pulse. Due to the large amount of energy transferred to the plasma in the very short pulse time, the energy is restricted from transferring to the interior of Al particles by thermal diffusion of the plasma and stored in the defects (shown in Fig.3(b)). This energy is the excessive stored energy compared with the conventional Al micropowders and nanopowders produced by equilibrium conditions such as IHE.
5 Conclusions
1) Crystalline Al nanopowders were synthesized by two heating-evaporation processes, IHE and LCHE. Both the powders have a uniform spherical shape, the same fine size dispersion (20-50 nm) and mean diameter size. Under the same testing conditions of DTA and TGA, the ability of energy release of the Al nanopowders prepared by LCHE is more than three times of the ones prepared by IHE. The direct reason for the difference of the thermal properties is the different microstructures of the two nanoparticles.
2) Defects of amorphous regions and lattice distortions in internal structure are observed in the particles produced by LCHE, as well as the asymmetry thickness of the alumina coatings. The particles produced by IHE have regular crystal planes and uniform coating, that is, no defects are observed in the particles. The different microstructures of the powders result from the different producing processes.
3) The formation of nanopowders by IHE process that employs induction as its heating resource follows the conventional evaporation-condensation model. Laser ablation is involved in the synthesis of nanoparticles by LCHE, which has the ability of triggering the plasma arc that can absorb energy of the laser pulse. Due to the large amount of energy transferred to the plasma in the very short pulse time, the excessive energy is restricted from transferring to the interior of Al particles by thermal diffusion of the plasma and stored in the defects. Propellants composed of Al nanopowders by LCHE would show higher energy level and specific impulse.
Acknowledgments
We would like to thank Analytical and Testing Center, Huazhong University of Science and Technology for the measurements and analysis.
References
[1] IVANOV Y F, OSMONOLIEV M N, VOROZHTSOV A B. Productions of ultra-fine powders and their use in high energetic compositions [J]. Propellants, Explosives, Pyrotechnics, 2003, 28: 319-333.
[2] MENCH M M, KUO K K, YEH C L, LU Y C. Comparison of the thermal behavior of regular and ultra-fine aluminum [J]. Combustion Science and Technology, 1998, 135: 269-292.
[3] JONES D E G, BROUSSEAU P, FOUCHARD R C, TURCOTTE A M, KWOK Q S M. Thermal characterization of passivated nanometer size aluminum powders [J]. Journal of Thermal Analysis and Calorimetry, 2000, 61: 805-818.
[4] PRANDA P, PRANDOVA K, HLAVACEK V. Particle size and reactivity of aluminum powders [J]. Combustion Science and Technology, 2000, 156: 81-96.
[5] DONG S, ZOU G, YANG H. Thermal characteristic of ultrafine- grained aluminum produced by wire electrical explosion [J]. Scripta Materialia, 2001, 44: 17-23.
[6] MENCH M M, KUO K K, YEH C L, LU Y C. Comparison of the thermal behavior of regular and ultra-fine aluminum [J]. Combustion Science and Technology, 1998, 135: 269-292.
[7] DESENA J T, KUO K K. Evaluation of stored energy in ultrafine aluminum powder produced by plasma explosion [J]. Journal of Propulsion and Power, 1999, 15: 795-800.
[8] KOTOV Y A. Electric explosion of wires as a method for preparation of nanopowders [J]. Journal of Nanoparticle Research, 2003, 5: 539-550.
[9] KWON Y S, JUNG Y H, YAVOROVSKY N A, ILLYN A P, KIM J S. Ultra-fine powder by wire explosion method [J]. Scripta Materialia, 2001, 44: 2247-2251.
[10] KUO K K, BRILL T B, RESCE-RODRIGUEZ R A, MITCHELL A R, COVINO J. Challenges in propellants and combustion 100 years after Nobel [M]. New York: Begell House, 1997: 636-645.
[11] PICKINA A, IVANOV D, FROLOV Y, MUDRETSOVA S, NICHOLSKAYA A, SCHOONMAN J. Plasma synthesized nano-aluminum powders structure, thermal properties and combustion behavior [J]. Journal of Thermal Analysis and Calorimetry, 2006, 86(3): 733-738.
[12] TILLOTSON T M, GASH A E, SIMPSON R L, HRUBESH L W, SATCHER J H, POCO J F. Nanostructured energetic materials using sol-gel methodologies [J]. Journal of Non-crystalline Solids, 2001, 285: 338-345.
[13] PANDA S, PRATSINIS S E. Modeling the synthesis of aluminum particles by evaporation-condensation in an aerosol flow reactor [J]. NanoStructured Materials, 1995, 5(7/8): 755-767.
[14] KWON Y S, GROMOV A A, STROKOVA J I. Passivation of the surface of aluminum nanopowders by protective coatings of the different chemical origin [J]. Applied Surface Science, 2007, 253: 5558-5564.
[15] WANG Z L, LIU Y, ZANG Z. Handbook of nanophase and nanostructured materials: Synthesis [M]. Volume 1. Beijing: Tsinghua University Press, 2002: 216-245.
(in Chinese)
Foundation item: Project(50471061) supported by the National Natural Science Foundation of China
Corresponding author: SONG Wu-lin; Tel/Fax: +86-27-87557453; E-mail: wulins@126.com
DOI: 10.1016/S1003-6326(08)60250-2
(Edited by LI Xiang-qun)