DOI: 10.11817/j.ysxb.1004.0609.2021-36676
Ti/Ni复合中间层扩散连接钨与钢接头的断裂行为
蔡青山,段欣昀,朱文谭,王健宁,刘文胜,马运柱
(中南大学 轻质高强结构材料国家级重点实验室,长沙410083)
摘 要:复合阻隔扩散连接技术是制备高性能钨/钢异种金属结构件的有效方法。本文研究Ti/Ni复合中间层扩散连接钨与钢接头的断裂行为,分析金属间化合物和残余应力对钨/钢接头性能及断裂方式的影响。结果表明:在拉伸载荷作用下,钨/Ti/Ni/钢扩散连接接头呈现出界面断裂、反应层断裂和混合断裂等3种断裂模式;在较低的连接温度和较短的保温时间下,钨/钢接头发生W/Ti界面断裂,接头强度较低;随着连接温度升高,钨/钢接头断裂发生在钨基体和W/Ti界面的混合区域,接头强度在(950℃, 1h)时达到最高,受残余应力和界面强度共同控制;随着连接温度进一步升高,Ti/Ni界面硬脆金属间化合物Ti2Ni、TiNi和TiNi3不断长大,厚度过大造成钨/钢接头在Ti–Ni金属间化合物层断裂。最后,分析钨/钢接头发生解理断裂的微观机制。
关键词:断裂;扩散连接;钨;复合中间层;残余应力
文章编号:1004-0609(2021)-07-1726-11 中图分类号:TF841.1 文献标志码:A
引文格式:蔡青山, 段欣昀, 朱文谭, 等. Ti/Ni复合中间层扩散连接钨与钢接头的断裂行为[J]. 中国有色金属学报, 2021, 31(7): 1726-1736. DOI: 10.11817/j.ysxb.1004.0609.2021-36676
CAI Qing-shan, DUAN Xin-yun, ZHU Wen-tan, et al. Fracture characterization of W-steel joints diffusion bonded with Ti/Ni composite interlayer[J]. The Chinese Journal of Nonferrous Metals, 2021, 31(7): 1726-1736. DOI: 10.11817/j.ysxb.1004.0609.2021-36676
钨及其合金与钢的连接件是核聚变堆DEMO装置中偏滤器部件的首选复合结构件[1]。然而,钨与钢的物理性能差异较大,特别是热膨胀系数相差大(室温下钨为4.5×10–6 K–1,钢为12×10–6~ 14×10–6 K–1),在连接和部件服役过程中将产生高的热应力,选择合适的连接技术,降低连接处的热应力有利于提高偏滤器的性能和使用寿命。
近几年关于钨/钢连接技术的研究得到了广泛关注,主要的连接技术有钎焊技术和真空扩散焊技术。尽管钎焊能实现钎料与母材的良好冶金结合,但是其钎焊温度较高(1150 ℃)容易造成钢中晶粒粗大和发生相转变[2],导致材料性能下降。扩散焊技术具有低的连接温度和高的接头使用温度,是一种非常有效的钨/钢连接技术。然而,钨/钢直接扩散连接焊接应力大,且连接界面极易形成FeW等硬脆金属间化合物和金属碳化物[3],现有研究主要是通过添加Ni[4-5]、Nb[2]、Ti[6-7]或V[8-9]作中间层来改善钨/钢扩散连接接头质量。所制备的钨/钢接头质量得到一定的改善,但这种单金属中间层自身会与基体材料发生反应在接头界面形成新的金属间化合物或其他脆性相,影响接头界面性能的进一步提升。
本文作者从减少或避免界面金属间化合物等硬脆相生成和缓和接头应力两方面,基于元素互溶的Hume-Rothery准则,结合残余应力的有限元分析,优化设计出“硬质/软质”的复合阻隔中间层,如V/Ni[10]、V/Cu[11]、Ti/Ni[12]和Ti/Cu[13]。复合中间层实现了钨与钢的良好扩散连接,其连接界面结合良好,大大缓解了界面残余应力,所得钨/钢连接接头强度比现有采用单一中间层所制备的钨/钢接头提升了45%以上[14]。钨/钢扩散连接过程中,“钨/硬质层/软质层/钢”的“三明治”结构在外加力学载荷作用下,当所采用的工艺参数不同时,接头强度发生明显的波动,其接头断裂失效特征也呈现出复杂的变化。
鉴于此,本论文从钨/复合中间层/钢接头断裂失效行为研究的角度出发,以钨/Ti/Ni/钢焊接结构为对象,对在不同工艺参数下钨/钢接头的拉伸断裂失效特征进行分析,探讨其裂纹扩展路径及断裂失效的微观机制,为进一步获得高性能钨/钢扩散连接接头提供基础理论支撑。
1 实验
1.1 实验材料
实验所用的纯钨为厦门虹鹭钨钼工业有限公司提供,是通过粉末冶金方法制备而成高纯掺钾钨杆(≥99.95%,质量分数,下同)。所用的0Cr17不锈钢为太原钢铁集团有限公司提供,是分别通过热轧、剥皮、较直和研磨等工艺制备而成,其化学成分如表1所列。中间层材料为Ti和Ni金属箔带,纯度均在99.95%以上,箔带厚度均为0.1 mm。
表1 0Cr17钢的化学成分
Table 1 Chemical composition of 0Cr17 steel (mass fraction, %)
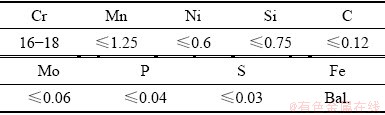
1.2 实验方法
采用电火花线切割机将待焊母材钨和钢切割成d 25 mm×15 mm的圆柱形试样用于扩散连接实验。采用150#、400#、800#、1200#和1500#的金相砂纸对钨与钢以及各中间层材料的待焊表面进行逐级打磨并抛光。然后,采用超声波清洗器(设置清洗温度35 ℃)将待焊材料依次在无水乙醇、丙酮、无水乙醇内清洗各15 min,以去除待焊试样表面的油污和杂质。将待焊试样按钨/复合中间层/钢的“三明治”结构(见图1)装配在高纯石墨模具中于真空热压机(PVPHP-R-10FRET-40)中进行扩散连接实验。工艺参数选为(850~1050 ℃)/1 h(间隔50 ℃)和950 ℃/(0.5~2 h) (间隔0.5h),连接压力为10 MPa,真空度≥1×10–3 Pa,具体工艺流程见文献[12]。
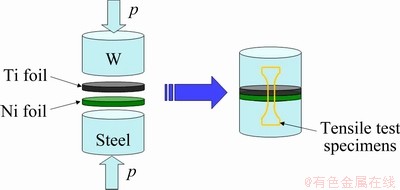
图1 钨/Ti/Ni/钢连接试样装配图
Fig. 1 Schematic representation of sample assembly
采用有限元分析软件(ANSYS 14.5)对钨/Ti/Ni/钢扩散连接接头的残余应力分布特征进行分析,有限元模型及模拟参数见文献[14]。连接实验完成后,结合连接试样的接头界面结构及元素浓度分布曲线(见图2),对钨/Ti/Ni/钢扩散连接接头的断裂行为进行分析。采用美国Instron 3369型力学试验机对钨/Ti/Ni/钢扩散连接接头进行室温拉伸强度的测试,图1显示了拉伸测试取样位置,连接接头焊缝位于拉伸试样中心部位,拉伸试样具体尺寸见文献[11]。采用美国FEI公司Nova Nano SEM230 场发射扫描电子显微镜观察连接接头的界面组织和拉伸断口形貌,结合SEM自带的能谱装置(EDS)对断口成分进行分析,采用Tecnai G2 F20 S-TWIN TMP场发射透射电镜对连接界面物相进行分析,采用瑞士CSM公司UNHT+MCT纳米力学性能综合测试仪对界面区域显微硬度进行测试。
2 结果与讨论
2.1 接头断裂行为特征
表2所列为分别采用Ti/Ni复合中间层扩散连接钨与钢所得接头强度及其断口位置,当工艺参数不同时,接头强度发生明显的波动,其接头断裂失效特征也呈现出复杂的变化。

图2 钨/Ti/Ni/钢扩散连接接头界面形貌及元素浓度分布曲线
Fig. 2 SEM-BSE image(a) and EPMA elemental concentration profile across W/Ti(b), Ti/Ni(c) and Ni/steel interfaces(d) for joint bonded at 950 ℃ for 0.5 h
表2 不同工艺参数下钨/Ti/Ni/钢扩散连接接头的拉伸强度及断口位置
Table 2 Joint strength and fracture position of W/Ti/Ni/steel joint bonded at different processing conditions

图3(a)所示为(800 ℃, 1 h)工艺条件下钨/Ti/Ni/钢扩散连接接头的断口SEM像。由图3(a)可知,其断口无明显特点,而且有抛光过程中留下的划痕印记存在,说明在低的连接温度下,待焊表面缺乏充分接触,连接界面变形程度不够,导致连接界面扩散反应有限,呈现出抛光处理的原始表面特征。EDS面扫描分析表明断口表面组成为96.4%的W(摩尔分数)和少量的Ti,说明断裂发生在W/Ti连接界面。当连接温度升高到850 ℃和900 ℃时,钨/Ti/Ni/钢接头断口呈现出相似的形貌特征,EDS分析均显示断口表面成分为富W相(W(Ti))。当温度继续升高到950 ℃,连接时间为0.5 h时,断口表面存在凸起,平整度变差,且黏附着不连续的黑色岛状物(见图3(b)),其化学成分组成为100%的Ti,表明此处W基体与中间层Ti实现了强的冶金结合。因此,在低的连接温度或短的连接时间下,钨/Ti/Ni/钢接头断裂以界面失效为主,这是由于待焊材料表面接触和相互扩散不充分。但随着连接温度不断升高,接头断口形貌从平整无特征,甚至还存在抛光划痕向夹杂有中间层断裂的特征变化,表明连接界面各元素之间的相互扩散随着温度的升高逐渐加强,此时界面强度不断升高,接头强度也随之提高。
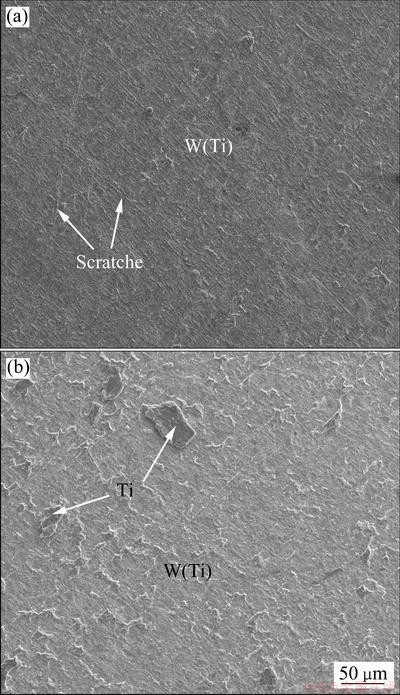
图3 (800 ℃, 1 h)和(950 ℃, 0.5 h)工艺下钨/Ti/Ni/钢连接接头拉伸断口形貌
Fig. 3 Fractured surfaces of W/Ti/Ni/steel joint bonded at 800 ℃ for 1 h(a) and 950 ℃ for 0.5 h(b), respectively
图4所示为(950 ℃, 1 h)工艺条件下钨/Ti/Ni/钢扩散连接接头的断口SEM像。断裂发生在两处特征明显不同的区域,图中浅黑色物质无规则黏附在浅白色物质表面的平整断裂区域与低连接温度下观察到断口表面相似,经EDS分析表明为W(Ti)相,即W/Ti界面,另一个呈浅灰色的不平整断裂位置为W相,即断裂发生在W基体。当连接温度为950 ℃,连接时间延长到1.5 h,其断裂也发生在W基体和W/Ti连接界面的混合区域。这种断裂特征反映了当连接温度升高或连接时间延长后,各连接界面原子相互扩散进一步增强,界面强度提高,断裂从单一W/Ti界面失效转向部分进入W基体内。前期研究[14]表明,由于钨与钢大的热物理性能差异,钨/钢异种材料连接接头内存在较大的残余应力,且主要集中在靠近连接界面的W基体内。因此,钨/Ti/Ni/钢连接接头靠近W/Ti界面的W基体内存在较大的残余应力,残余应力的存在将明显降低脆性材料W的静载强度,成为整个接头承受拉伸载荷最薄弱的位置之一,导致W基体断裂的发生。
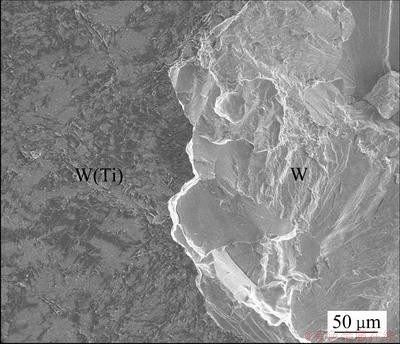
图4 (950 ℃, 1 h)工艺下钨/Ti/Ni/钢连接接头拉伸断口形貌
Fig. 4 Fractured surfaces of W/Ti/Ni/steel joint bonded at 950 ℃ for 1 h
图5所示为(950 ℃, 2 h)工艺参数下钨/Ti/Ni/钢接头的典型断口SEM像,其断口呈现多种不同连接结构之间的断裂。EDS分析其断口成分由Ti和Ni组成,表明断裂发生在中间层Ti和Ni的反应层区域。图5(a)显示了断口存在3种断裂面,分别取断裂位置A和B进行分析,如图5(b)和(c)所示,其中呈细小多晶状的断面成分为23.2%~28.9%的Ti和剩余含量的Ni,表明为TiNi3金属间化合物相,呈小刻面台阶状的断面元素浓度配比为48.6%~ 51.7%的Ni和剩余含量的Ti,表明该断面层物相为TiNi,而呈河流状花样的断口元素组成为63.7%~ 68.1%的Ti和剩余含量的Ni,为Ti2Ni金属间化合物相。Ti-Ni金属间化合物的存在将对钨/钢连接接头质量产生不利影响,随着连接温度升高或连接时间延长,Ti-Ni金属间化合物层不断长大,接头强度转向由Ti-Ni化合物层控制,Ti-Ni反应层成为整个接头最薄弱的区域,导致断裂在Ti-Ni反应层发生。
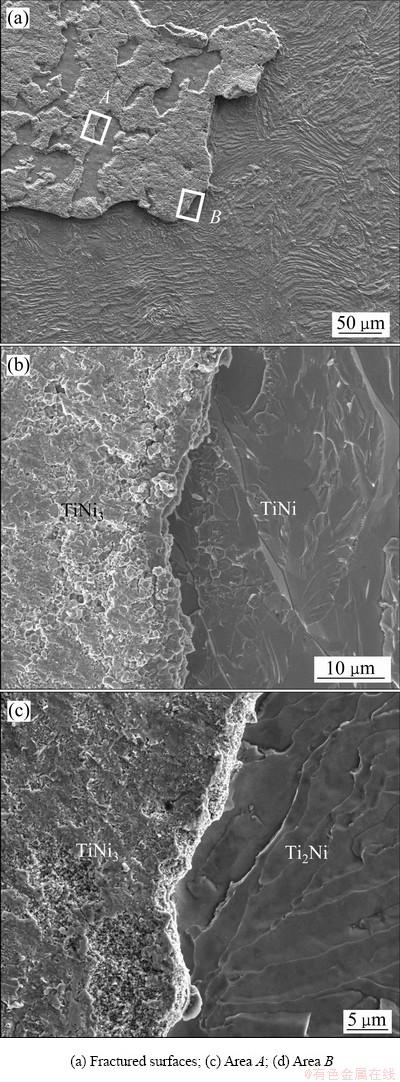
图5 (950 ℃, 2 h)工艺参数下钨/Ti/Ni/钢连接接头拉伸断口形貌
Fig. 5 Representative fractured surfaces of joint bonded at 950 ℃ for 2 h
当连接温度分别为1000 ℃和1050 ℃时,钨/ Ti/Ni/钢接头断口形貌与(950 ℃, 2 h)工艺参数下的断口形貌相似,接头断裂也发生在Ti-Ni反应层,但同时也出现了发生在单一Ti-Ni金属间化合物层的断裂方式,如当温度升高到1050 ℃时,发生了沿Ti2Ni层的断裂失效(见图6)。因此,在长的连接时间或高的连接温度下,接头易于在Ti-Ni金属间化合物层中发生断裂,导致接头强度下降。
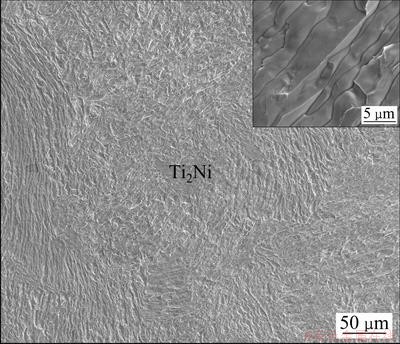
图6 (1050 ℃, 1 h)工艺参数下下钨/Ti/Ni/钢连接接头的典型断口形貌
Fig. 6 Representative fractured surfaces of joint bonded at 1050 ℃ for 1 h
2.2 接头断裂模式与路径
由上述断口分析可知,钨/Ti/Ni/钢扩散连接接头的断裂失效模式可划分为3大类:界面断裂、反应层断裂和混合断裂,如图7所示。
断裂类型Ⅰ为界面断裂,特征是断裂发生在W基体与中间层材料Ti之间的连接界面,其断裂路径如图7(a)所示。造成这种断裂模式的原因是连接温度低或连接时间短,导致连接界面原子扩散不够充分,界面强度不足,与其对应的接头强度低。而钨/Ti/Ni/钢连接接头存在W/Ti、Ti/Ni和Ni/steel 3个界面,可见,相比于Ti/Ni和Ni/steel界面,W/Ti界面结合强度最弱。这可能与低的连接温度下W 的扩散能力有限有关。一般地,在固态扩散连接过程中,连接材料组元熔点越高,其所要求的扩散温度越高。由于W和Ti均为难熔金属,特别是W,熔点高达3420 ℃,其扩散连接的优化温度为0.67 Tm(2200 ℃)[15],在本实验所采用的连接温度下无法激活W的真空扩散机制,导致无法实现W与Ti的充分扩散,界面微观组织分析也表明W/Ti界面扩散区域非常薄(2~5 μm)。因此,钨/钢界面断裂归因于低的连接温度下钨与中间层材料Ti的不完全相互扩散。

图7 钨/钢连接接头断裂路径示意图
Fig. 7 Schematic diagram of fracture paths of W/steel joints during tensile tests
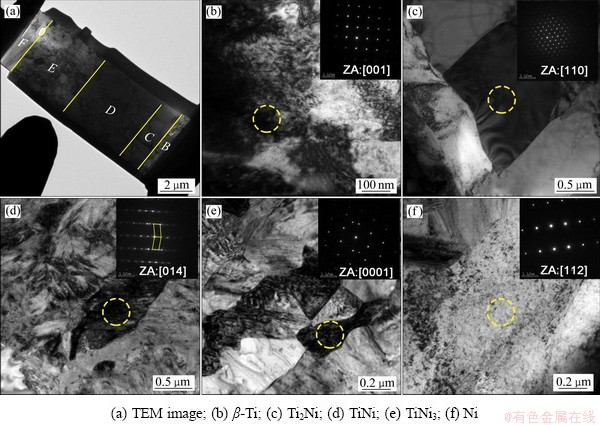
图8 钨/Ti/Ni钢连接接头Ti/Ni界面物相组成的TEM分析结果
Fig. 8 TEM images of phase composition of Ti/Ni diffusion zone
断裂模式Ⅱ为反应层断裂,表现为断裂发生在中间层Ti和Ni的反应层内,其断裂路径如图7(b)所示。对于钨/Ti/Ni/钢扩散连接体系,采用Ti/Ni复合中间层成功阻止了钨/钢连接界面FeW或金属碳化物等脆性相的生成,但Ti/Ni复合层的加入仍然没有完全避免金属间化合物等有害产物的生成,在Ti/Ni连接界面生成了大量Ti-Ni金属间化合物。采用透射电镜对Ti/Ni连接界面进行分析,结果如图8所示。图8(a)所示为界面区域整体TEM像,可以看出界面区域包括5个界面平直的中间层和反应层,分别标记为B、C、D、E和F,每层区域对应的TEM明场像和选区电子衍射如图8(b)~(f)所示。根据对应的选区电子衍射分析可知层B和F分别为 BCC结构的β-Ti相和FCC结构的Ni相(见图8(b)和(f)),对应中间层Ti和Ni。根据Ti-Ni相图,Ti的α-β晶型转变温度为882 ℃,当Ti与Ni发生相互扩散时,Ni成为β相稳定元素,Ni原子迁移进入Ti晶格,使Ti的α-β多晶转变温度降低到765 ℃。因此,在本实验800 ℃以上的连接温度下,中间层Ti主要以β-Ti相存在。根据图8(c)~(e)的选区电子衍射结果可知,层C、D和E分别对应金属间化合物Ti2Ni、TiNi和TiNi3相,其厚度分别为1.3 μm、4.4 μm和4.0 μm。其中Ti2Ni属于复杂立方结构,对比明场像TEM像可知其晶粒尺寸明显大于TiNi和TiNi3相。TiNi相属于BCC结构,呈现为马氏体组织形貌,对应的选区电子衍射结果(见图 8(d))证明在马氏体内部存在栾晶,这是由于在高温扩散连接过程中TiNi相发生热诱导马氏体相变引起的[16]。TiNi3相属于六方结构,可以发现在TiNi3层存在大量的小晶粒(见图8(e))。在多层金属间化合物存在的界面区域,裂纹萌生与扩展与各层金属间化合物的性质显著相关。在Ti2Ni、TiNi和TiNi3三相中,TiNi相具有较高的塑形,是常用形状记忆合金相成分,而Ti2Ni具有较高的刚度和硬度,但塑形和韧性较差[17-18],这是造成钨/钢接头拉伸断裂发生在单一Ti2Ni金属间化合物层的原因。
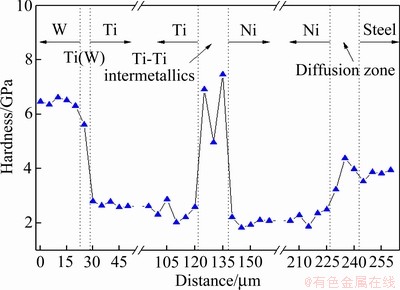
图9 钨/Ti/Ni/钢扩散连接接头界面的硬度分布曲线
Fig. 9 Hardness profile across W/Ti/Ni/steel interface for joint bonded at 950 ℃ for 2 h
图9所示为钨/Ti/Ni/钢连接接头界面区域的硬度分布曲线。由图9可知,由于各连接界面扩散区域的化学组成和厚度不同,各界面硬度分布呈现显著的变化,反映了各接头界面的扩散反应及固溶体和金属间化合物生成等关系。在整个连接接头中, Ti/Ni界面区域硬度最高,最大可达7.5 GPa,这与所生成的脆硬性Ti-Ni金属间化合物有关。可见,Ti-Ni金属间化合物层是整个连接接头硬度最高的区域,从而也将成为承受机械负荷甚至残余应力最薄弱的区域之一。此外,在高的连接温度下,Ti/Ni界面Ti-Ni金属间化合物Ti2Ni、TiNi和TiNi3不断长大,厚度过大造成钨/钢接头拉伸失效行为受Ti-Ni反应层性能控制。因此,钨/钢反应层断裂是Ti-Ni金属间化合物层过厚导致反应层脆化,成为整个连接接头承受拉伸载荷最薄弱的区域,与其对应的接头强度低。
断裂模式Ⅲ为混合断裂,表现为断裂发生在W基体和连接界面的混合区域,其断裂路径如图7(c)所示。该断口位置贯穿多种连接结构,说明接头中不存在对连接强度起完全控制作用的薄弱部位,所获得的接头强度较高。断裂部分发生在W/Ti界面反映了钨与中间层Ti的界面结合强度仍然是整个接头较薄弱的区域,而断裂部分发生在钨基体则与接头残余应力大小及分布有关。图10(a)所示为钨/Ti/Ni/钢连接接头等效应力分布等值线图,由图10(a)可知,钨/Ti/Ni/钢接头残余应力主要集中在接头区域,且最大残余应力均位于靠近连接界面的钨基体内。对钨基体内的残余应力进行定量分析,图10(b)所示为沿对称轴方向钨基体内的残余应力大小分布图。从图10(b)可知,与未添加中间层相比,其残余应力分布规律相似,但添加Ti/Ni复合中间层的连接接头残余应力较无中间层的接头残余应力有较明显的降低,说明Ti/Ni复合中间层具有较好的缓和钨/钢接头残余应力的效果。此外钨/Ti/Ni/钢连接接头最大残余应力出现在离连接界面约0.2 mm的钨基体内,此位置为钨基体承受外加载荷最薄弱的区域,使钨基体在远低于其屈服点的外应力作用下就发生脆性断裂,这是造成钨/Ti/Ni/钢接头断裂发生在钨基体的原因。因此,钨/Ti/Ni/钢扩散连接接头断裂失效表现为:首先由于接头内残余应力集中,裂纹产生于靠近W/Ti界面的W基体内,然后迅速沿着钨晶粒扩展,并逐渐延伸至W/Ti连接界面。该断裂类型的断口呈现出界面断裂和W基体断裂两种不同的断裂组织,这种断裂方式反映了残余应力和界面强度的共同影响,同时从侧面说明了所获得的接头不存在明显的薄弱部位,与其对应的接头强度较高。
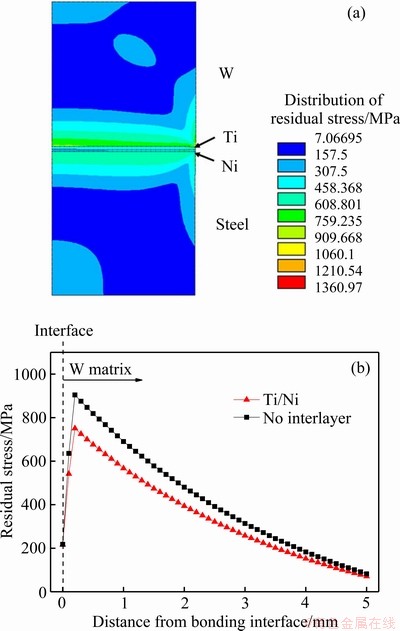
图10 钨/Ti/Ni/钢直接连接接头的等效应力分布等值线图及钨侧的等效应力分布曲线
Fig. 10 Distribution of residual stress in W/Ti/Ni/steel joints(a) and residual stress profile in W substrate as function of distance from bonding interface(b)
2.3 接头解离断裂的微观机制
钨/Ti/Ni/钢扩散连接接头呈混合断裂时主要表现为解理脆性断裂,其解理断裂过程可以分为启裂和裂纹失稳扩展两个阶段。根据Griffith断裂理论[19],脆性材料内存在许多亚微观缺陷、微型裂纹或其它用常规方法无法检测的非常小的不均匀粒子,这些统称为Griffith缺陷,成为断裂发生的裂纹源。在外加力学载荷的作用下,微缺陷处于应力集中状态,其局部应力可达外加应力的好几倍,裂纹开始脱离平衡状态,随后裂纹失稳扩展,导致断裂的发生。
图11所示为在(900 ℃, 1.5 h)下制得的W/Ti/Ni/ steel扩散连接接头W/Ti界面的高倍形貌图,在W/Ti界面区域有孔洞和细小微裂纹的存在,这可能是由于界面两侧元素相互扩散不均匀引起的[20-21]。ZHONG等[6]在采用Ti作中间层扩散连接钨与钢时发现W/Ti界面有横向微裂纹的产生,其主要原因是W与Ti之间的原子尺寸相差较大,当W与Ti在高温下发生强烈的相互扩散时,会导致界面裂纹等缺陷产生。此外,脆性钨基体材料内部孔洞、杂质也是微裂纹缺陷的来源。因此,W/Ti界面区域孔洞、微裂纹等缺陷的存在将成为钨/钢接头断裂的裂纹源,而且该区域是整个接头残余应力最集中的地方,导致该区域的裂纹源应力集中最严重,极易引发界面开裂失效。
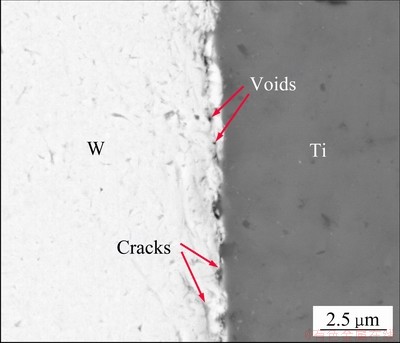
图11 在(900 ℃, 1.5 h)下钨/Ti/Cu/钢连接接头W/Ti界面SEM像
Fig. 11 SEM image of W/Ti interface of joint bonded at 950 ℃ for 1.5 h
对于钨/钢扩散连接接头,微裂纹的形成并不一定能够引发解理断裂,只有在外加载荷作用下,施加到微裂纹源上的局部应力超过临界应力时,微裂纹才能扩展。含裂纹材料发生断裂时的应力
为[22]:
(1)
式中:E为材料的弹性模量;γ为材料的表面能;c为材料微裂纹尺寸(长度);γp为裂纹尖端向前扩展单位长度时的塑性功,通常γp比γ大2~3个数量级。可见,材料内部微裂纹尺寸越大,材料断裂所需外加载荷越小。当钨/钢接头处于拉伸负荷作用下,接头内微裂纹扩展形成长度足够大的裂纹时,将造成钨/钢接头的解理断裂。

图12 钨/钢扩散连接接头在拉伸负荷作用下于钨/中间层界面区域断裂过程示意图
Fig. 12 Schematic diagrams of tensile fracture process of W/interlayer diffusion zone
图12所示为钨/钢扩散连接接头在拉伸负荷作用下于钨/中间层界面区域断裂失效的微观机制示意图。在施加拉伸应力前,连接界面和钨基体内存在孔洞、杂质和微裂纹等缺陷,缺陷处于高应力状态,如图12(a)所示。在拉伸应力的作用下,空洞聚集、微裂纹开始扩展如图11(b)所示。随着拉伸应力的不断加大,这些微裂纹不断扩展、长大,当弹性释放能远大于表面能时,裂纹把剩余能量积累为动能,裂纹可持续扩展,如图12(c)所示。解理裂纹的扩展是高速进行的,当微裂纹与拉伸直接造成的主裂纹汇合后,就沿钨/中间层连接界面或钨基体发生断裂,如图12(d)所示。
3 结论
1) 在不同工艺参数下,钨/Ti/Ni/钢接头断裂失效特征呈现出3种类型,分别为界面断裂、反应层断裂和混合断裂。
2) 在连接温度低于950 ℃和短的连接时间下,钨/Ti/Ni/钢扩散连接接头呈界面断裂,断裂发生在W基体与中间层Ti之间的连接界面,表现为弱的W/Ti界面结合强度。
3) 在连接温度高于950 ℃和长的连接时间下,钨/Ti/Ni/钢扩散连接接头呈反应层断裂,断裂发生在中间层材料Ti和Ni的反应层,这与Ti/Ni界面生成了厚度较大的硬脆性Ti-Ni金属间化合物相有关。
4) 在(950 ℃, 1 h)的连接工艺下,钨/Ti/Ni/钢扩散连接接头呈混合断裂,断裂发生在W基体和W/Ti界面的混合区域,反映了接头性能受界面强度和残余应力共同控制,获得了最高的接头强度。
5) 钨/Ti/Ni/钢扩散连接接头W/Ti连接界面区域存在孔洞、微裂纹等缺陷,在外加载荷作用下容易发生应力集中,随后裂纹失稳扩展,引发界面开裂失效。
REFERENCES
[1] NORAJITRA P, ANTUSCH S, GINIYATULIN R, et al. Progress of He-cooled divertor development for DEMO[J]. Fusion Engineering Design, 2011, 86: 1656-1659.
[2] BASUKI W W, AKTAA J. Investigation of tungsten/ EUROFER97 diffusion bonding using Nb interlayer[J]. Fusion Engineering Design, 2011, 86: 2585-2588.
[3] BASUKI W W, AKTAA J. Investigation on the diffusion bonding of tungsten and EUROFER97[J]. Journal Nuclear Materials, 2011, 417: 524-527.
[4] ZHONG Zhi-hong, JUNG Hun-chea, HINOKI T, et al. Effect of joining temperature on the microstructure and strength of tungsten/ferritic steel joints diffusion bonded with a nickel interlayer[J]. Journal of Materials Processing Technology, 2010, 210: 1805-1810.
[5] ZHONG Zhi-hong, HINOKI T, KOHYAMA A. Effect of holding time on the microstructure and strength of tungsten/ferritic steel joints diffusion bonded with a nickel interlayer[J]. Materials Science and Engineering A, 2009, 518: 167-173.
[6] ZHONG Zhi-hong, HINOKI T, NOZAWA T, et al. Microstructure and mechanical properties of diffusion bonded joints between tungsten and F82H steel using a titanium interlayer[J]. Journal of Alloys and Compounds, 2010, 489: 545-551.
[7] WANG Ji-chao, WANG Wan-jing, WEI Ran, et al. Effect of Ti interlayer on the bonding quality of W and steel HIP joint[J]. Journal Nuclear Materials, 2017, 485: 8-14.
[8] BASUKI W W, AKTAA J. Diffusion bonding between W and EUROFER97 using V interlayer[J]. Journal Nuclear Materials, 2012, 429: 335-340.
[9] BASUKI W W, AKTAA J. Process optimization for diffusion bonding of tungsten with EUROFER97 using a vanadium interlayer[J]. Journal Nuclear Materials, 2015, 459: 217-224.
[10] LIU Wen-sheng, CAI Qing-shan, MA Yun-zhu, et al. Microstructure and mechanical properties of diffusion bonded W/steel joint using V/Ni composite interlayer[J]. Materials Characterization, 2013, 86: 212-220.
[11] CAI Qing-shan, LIU Wen-sheng, MA Yun-zhu, et al. Microstructure, residual stresses and mechanical properties of diffusion bonded tungsten-steel joint using a V/Cu composite barrier interlayer[J]. International Journal of Refractory Metals and Hard Materials, 2015, 48: 312-317.
[12] CAI Qing-shan, LIU Wen-sheng, MA Yun-zhu, et al. Influence of intermetallic compounds on the microstructure and strength properties of diffusion bonded W-steel joints using Ti/Ni composite interlayer[J]. Fusion Engineering and Design, 2018, 132: 110-118.
[13] CAI Qing-shan, LIU Wen-sheng, MA Yun-zhu, et al. Effect of joining temperature on the microstructure and strength of W-steel HIP joints with Ti/Cu composite interlayer[J]. Journal of Nuclear Materials, 2018, 198: 198-207.
[14] CAI Qing-shan, ZHU Wen-tan, MA Yun-zhu, et al. Rational design of composite interlayer for diffusion bonding of tungsten-steel joints[J]. International Journal Refractory Metals and Hard Materials, 2018, 70: 155-161.
[15] KAZAKOV N F, KVASNITSKY V F. Bonding of refractory and active metals and their alloys[M]. KAZAKOV N F, ed. Diffusion Bonding of Materials. Moscow: Mir Publisher, 1985.
[16] 窦海啸. NiTi合金多步马氏体相变规律及原位透射电镜研究[D]. 北京: 北京工业大学, 2012.
KOU Hai-xiao. Study of multi-step martensitic transformations in NiTi alloy by TEM and in situ TEM[D]. Beijing: Beijing University of Technology, 2012.
[17] HITOSHI H, TAKASHI I, HIROFUMI S, et al. Cavitation erosion mechanism of NiTi coatings made by laser plasma hybrid spraying[J]. Wear, 1999, 231: 272-278.
[18] ZHANG You-jing, CHENG Xing-wang, CAI Hong-nian, et al. The effects of thickness of original Ti foils on the microstructures and mechanical properties of Ti2Ni/TiNi laminated composites[J]. Materials Science and Engineering A, 2017, 684: 292-302.
[19] 钟群鹏, 赵子华. 断口学[M]. 北京: 高等教育出版社, 2006: 349.
ZHONG Qun-peng, ZHAO Zi-hua. Fractography[M]. Beijing: Higher Education Press, 2006: 349.
[20] SABETGHADAM H, HANZAKI A Z, ARAEE A. Diffusion bonding of 410 stainless steel to copper using a nickel interlayer[J]. Materials Characterization, 2010, 61(6): 626-634.
[21] YILMAZ O, AKSOY M. Investigation of micro-crack occurrence conditions in diffusion bonded Cu-304 stainless steel couple[J]. Journal of Materials Processing Technology, 2002, 121(1): 136-142.
[22] 张志明. 金属材料断裂韧性的研究[D]. 上海: 上海交通大学, 2011.
ZHANG Zhi-ming. Research on fracture toughness of metallic materials[D]. Shanghai: Shanghai Jiao Tong University, 2011.
Fracture characterization of W-steel joints diffusion bonded with Ti/Ni composite interlayer
CAI Qing-shan, DUAN Xin-yun, ZHU Wen-tan, WANG Jian-ning, LIU Wen-sheng, MA Yun-zhu
(National Key Laboratory of Science and Technology for National Defence on High-strength Structural Materials, Central South University, Changsha 410083, China)
Abstract: Composite isolation diffusion bonding technology is an effective method to fabricate high performance tungsten/steel dissimilar metal structural parts. In this paper, the joint fracture characterization of Ti/Ni composite interlayer diffused W-steel was studied, and the influences of intermetallic compounds and residual stresses on the properties and fracture modes of W-steel joints were analyzed. The results show that the W/Ti/Ni/steel diffusion joint presents three fracture modes under tensile load: interfacial fracture, reaction layer fracture and mixed fracture. Under low bonding temperature and short holding time, the main failure mode of W/steel joint is interface fracture, as the connection temperature increases, the fracture of the tungsten/steel joint occurs in the mixed area between the tungsten matrix and the W/Ti interface. The joint strength reaches its maximum at (950 ℃, 1 h), and is controlled by the residual stress and the interface strength. However, with the further increase of the connection temperature, the Ti/Ni interface hard and brittle intermetallic compounds Ti2Ni, TiNi and TiNi3 continue to grow, and the excessive thickness causes the tungsten/steel joint to break in the Ti/Ni intermetallic compound layer. Finally, the micro mechanism of cleavage fracture of W/steel joint is revealed.
Key words: fracture; diffusion bonding; tungsten; composite interlayer; residual stress
Foundation item: Project(51931012) supported by the National Natural Science Foundation of China
Received date: 2021-02-25; Accepted date: 2021-05-10
Corresponding authors: LIU Wen-sheng; Tel: +86-731-88877998; E-mail: liuwensheng@csu.edu.cn
MA Yun-zhu; Tel: +86-731-88877825; E-mail: zhuzipm@csu.edu.cn
(编辑 王 超)
基金项目:国家自然科学基金资助项目(51931012)
收稿日期:2021-02-25;修订日期:2021-05-10
通信作者:刘文胜,教授,博士;电话:0731-88877998;E-mail:liuwensheng@csu.edu.cn
马运柱,教授,博士;电话:0731-88877825;E-mail:zhuzipm@csu.edu.cn