Trans. Nonferrous Met. Soc. China 20(2010) s794-s797

Design of experiments for determination of influence of different parameters on mechanical properties of semi-solid extruded parts
V. POUVAFAR, S. A. SADOUGH, F. HOSSEINJ, M. R. RAHMANI
Center of Excellence in Solid Mechanics, Mechanical Engineering Department,
AmirKabir University of Technology (Tehran Polytechnic), 15914 Tehran, Iran
Abstract: Near net-shape production of complex parts with higher mechanical properties is one of the most important final goals of the recent researches on the semi-solid processing. Having the knowledge of the influence of every parameter on the properties of final parts is the key in the production of high quality complex parts. Among these parameters forming temperature and velocity, and reheating and holding times have the greatest effects on the final mechanical properties of the parts. The influence of the parameters of non-dendritic billet production, forming speed, temperature and holding time on the properties of semi-solid extruded parts were investigated. Cooling-slope method was employed in order to produce non-dendritic billets. The material used was A356 aluminum alloy. Since the number of the parameters influencing the final properties of the parts was high (these parameters include: cooling slope angle, ram velocity, temperature and holding time), the final number of the experiments required would be n4, in which n is the number of the states of the parameters (5 in our case). In order to reduce this amount, design of experiments Tachuchi method was employed (design L25). Using this method the number of required experiments was reduced to 25. For the experiments the prepared semi-solid samples were extruded under isothermal condition and with 5 different ram speeds. Standard tensile tests were conducted on the extruded parts and the mechanical properties of the parts were determined. The obtained results analyzed with MiniTab and the influence of each of the parameters and also the percentage of its influence were calculated. Finally an optimum region for the parameters was determined. The temperature, ram speed, slope angle and holding time have more important effects descendingly.
Key words: semi-solid extrusion; Tachuchi method; A356 alloy; mechanical properties
1 Introduction
The key to all semisolid processes is spherical and nondendritic particles suspended in a liquid matrix. SPENCE[1] discovered this phenomenon while running hot tear test on Sn-15 Pb alloy Along with the advantages of semi-solid forming, such as lower cycle time, increased die life, reduced porosity, reduced solidification shrinkage and improved mechanical properties, the semi-solid processes are less limited in the part geometry, mainly concerning the wall thickness. In these processes, thin and thick sections are possible in the same part, allowing the major design flexibility[2].
Besides aforementioned advantages, excess of process parameters influencing the final properties of the produced parts contributes to the complexity of the semi-solid processes. Near net-shape production of complex parts with higher mechanical properties is one of the most important final goals of the recent researches on the semi-solid processing. Having the knowledge of the influence of every parameter on the properties of final parts is the key in the production of high quality complex parts.
Many researchers have tried to relate the influence of certain parameters on the final properties and formability of the semi-solid materials both numerically[3-7] and experimentally[8-14]. Some of these numerical works lack the verification of their results by experiments[3,7], most of the others investigate only one or two parameter independently, neglecting the effect of any other parameter[3-14]. The complex nature of semi-solid processes requires that all the parameters be considered together to get the most optimum results in drawing process window. In fact, it is not possible to take into account all the process parameters simultaneously. Though, a great challenge for overcoming a part of this problem is to design the required experiments.
In this work, Tachuchi method was employed to design experiments to determine the influence of the forming temperature and velocity, and reheating and holding times and also billet preparation parameter on the mechanical properties of final parts. Also the percentage of the influence of each parameter was calculated.
2 Experimental Procedure
2.1 Material
The alloy used in this research was a commercial hypoeutectic Al-cast alloy, A356. It was received in the as-cast condition without any modifications or refinements. Its chemical composition is presented in Table 1. Ingots of A356 aluminum alloy was melted in an electric furnace at 640 ?C and then poured through a cooling slope into a metallic cylindrical die. For our research purpose 5 different slope angles were used. The prepared billets were machined and cut into d 25 mm×25 mm pieces.
Table 1 Chemical composition of A356 alloy(mass fraction/%)
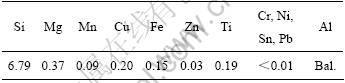
2.2 Design of experiments
In order to determine the influence of the forming temperature and velocity, and reheating and holding time and also cooling slope angle on the mechanical properties of final parts, 5 different conditions for each parameter were chosen (Table 2). As a result, the final number of required tests would be 625. Since the number of required tests was high, Tachuchi method was employed to reduce this amount. Using this method, Design L25 reduced the number of required tests to 25. Two extra tests were also added as verifiers of the Tachuchi analysis final results. The commercial software MINITAB was used to design and analyze the experiments.
Table 2 Different conditions for each parameter
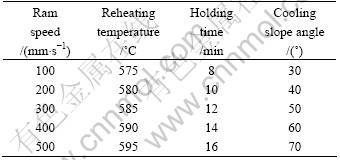
2.3 Experiments
The extrusion tests were carried out using a hydraulic high speed press and under isothermal conditions. For this purpose an electric furnace was placed under this press and the tests were carried out in the furnace. As mentioned earlier, 27 tests with different parameters were carried out. Fig.1 shows 2 samples of extruded parts.
Fig.1 Samples of extruded parts
The extruded parts were cut and machined into standard tensile specimens and finally tensile tests and also Vickers hardness tests were carried out on the prepared specimens. The obtained results were analyzed using Tachuchi method.
2.4 Tachuchi Analysis
The results of 25 different tests were entered into Tachuchi results section. These results were analyzed using Minitab software and the results of the 600 remaining experiments were calculated. For the verification of the results, the obtained tensile stresses of the verifier specimens were compared with the calculated result. This comparison verified the calculations. The effect of each parameter individually on the mechanical properties of the extruded parts and also the percentage of its effect were then calculated and plotted.
3 Results and discussion
The influences of different parameters on the mechanical properties of the extruded parts are discussed bellow. For each plot the average of the values is considered.
3.1 Temperature
Fig.2 shows the influence of temperature variations on the final mechanical properties of the extruded parts. It can be seen that the increase of the temperature results in the reduction of the tensile stress. This phenomenon can be related to the amount of work done on the solid skeleton of the semi-solid billets. At high temperatures solid fraction of semi-solid billets decreases, and as a result, the amount of the work done on the solid skeleton decreases. Finally the tensile stress decreases.
At temperatures above 585 ?C, a slightly constant tensile stress can be assumed. This is because the solid skeleton above this temperature completely breaks apart and less or no work is done on the suspended solid particles.

Fig.2 Effect of temperature on tensile strength
3.2 Ram speed
Fig. 3 shows the influence of ram speed on the final mechanical properties of the extruded parts. The forming speed effects can be related to two opposite events. One is liquid segregation that is present in low forming speed and the other is liquid splash that can be seen in high forming speed. In other words, low forming speed gives the liquid phase enough time to skip away from the solid skeleton. This segregation lowers the mechanical properties of the formed parts. Contradictorily, high forming speeds overcome segregation problem while it leads to liquid splash. In addition, when the forming speed increases the probability of the generation of entrapped gases and porosities increases.
As a result there must be a region that these two criteria come to an optimum state and the tensile strength increases. This fact describes the ascending and descending behavior in Fig.3.
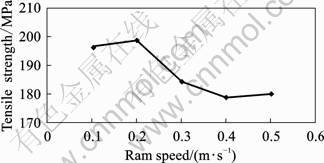
Fig.3 Effect of ram speed on tensile strength
3.3 Holding Time
The effect of holding time on the tensile strength of the extruded parts is shown in Fig.4. It can be seen that the tensile strength increases while the holding time increases. The reason can be related to the degree of spheroidization and shape factor of the solid particles. While lower holding times prevents excessive particle growth, some time is needed for the solid particles to become complete spheroids, which is an essential parameter for a successful semi-solid process. On the other hand, longer holding time results in particle growth which indeed reduces the mechanical properties of the parts. Although in our experiments chosen holding times were not too long to experience the particle growth, but as we will discuss later holding time has less effect on the tensile strength of the parts. This is true of course while the holding times are not shorter than a critical time required for the solid particles to spheroidize.
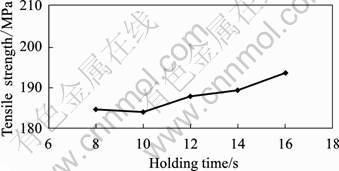
Fig.4 Effect of holding time on tensile strength
3.4 Cooling slope angle
Fig.5 shows the influence of slope angle on the final mechanical properties of the extruded parts. Like the ram speed, cooling slope angle has contradictory effects on the mechanical properties of the extruded parts. In lower angles the number of the crystals generated during the billet casting is high and thus the overall particle size of the billet is lower. On the other hand, higher angles promote turbulent flow which indeed results in spherical particles.
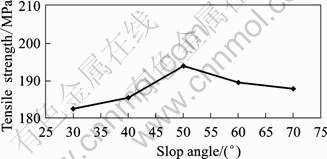
Fig.5 Effect of slope angle on tensile strength
These require that there must be a region in which the mechanical properties are higher. This region was found to be between 45? and 55?.
3.5 Importance of parameters
In order to indentify which parameter has a great impact on the mechanical properties of the extruded parts, percentage of the importance of the parameters was calculated. The results are shown in Fig.6. As can be seen, temperature with 43% has the greatest effect on the final mechanical properties of the extruded parts, while holding time with 14% has the least effect.
Therefore, considerable attention should be paid to the temperature and forming speed when designing semi-solid processes.
The contour plot of tensile strength versus temperature and ram speed is shown in Fig.7 so that it is possible to find the regions with higher mechanical properties.
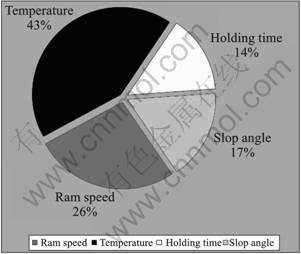
Fig.6 Importance of parameters

Fig.7 Contour plot of tensile strength vs ram speed and temperature 4 Conclusions
1) Lower temperatures in semi-solid range of medium solid fractions are preferred in order to get higher mechanical properties.
2) The optimum range of ram speed would be about 0.2 m/s.
3) Increasing the holding time till the start of grain growth, would result in better spheroids and thus better mechanical properties.
4) The optimum range of slope angle for better mechanical properties was between 45? and 55?.
5) The importance of parameters calculations revealed that temperature, ram speed, slope angle and holding time have 43%, 26%, 17% and 14% effectiveness on the mechanical properties of extruded parts respectively.
References
[1] SPENCER D B. A study of the description matching problem [D]. Cambridge MA: MIT, 1971.
[2] GIARDANO P, CHIARMETTA G, The new technologies evolution in semisolid aluminum casting [C]// Proceedings of the 8th International Conference on Semi-Solid Processing of Alloys and Composites. Cyprus, 2004.
[3] ALEXANDROU A, LE MANN P, GEORGIOU G, ENTOV V. Flow instabilities of Herschel Bulkley fluids[J]. J Non-Newtonian Fluid Mech, 2003, 116: 19-32.
[4] ITAMURA M, ADACHI M, MURAKAMI K, HARADA T, TANAKA M, SATO S, MAEDA T. Tensile properties of cast and mushy state rolled Al45Cu alloy and in situ Al45Cu5TiB2 compositie [J]. Int J Cast Met Res, 2002, 15: 173-178.
[5] MODIGELL M, KOPP R, SAHM P R, NEWSCHUTZ D, PETERA J. Basic investigations for optimization of the process parameters of thixoforming [C]// Proc 7th Int Conf on Advanced Semi-Solid Processing of Alloys and Composites. Tsukuba, Japan, 2002: 77-82.
[6] ALEXANDROU A, DUC E, ENTOV V. Inertial, viscous and yield stress effects in Bingham fluid filling of a 2-D cavity[J]. J Non-Newtonian Fluid Mech, 2001, 96: 383-403.
[7] ZAVALIANGOS A, LAWLEY A. Numerical simulation of thixoforming[J]. J Mater Eng Perform, 1995, 4: 40-47.
[8] ZUDE Z, QIANG C, HONGYING C, SHUHAI H, Microstructural evolution and tensile mechanical properties of thixoforged ZK60-Y magnesium alloys produced by two different routes[J]. J of Materials and Design, 2010, 31: 1906-1916
[9] MORADI M., NILI A, HEIDARIAN B, ASHURI S. Defect control and mechanical properties of thixoformed Al–Si alloy, J. of Alloys and Compounds, 2009, 487: 768-775.
[10] BAYOUMI M A, NEGM M I, El-GOHRY A M. Microstructure and mechanical properties of extruded Al-Si alloy (A356) in the semi-solid state[J]. J Materials and Design, 2009, 30: 4469-4477.
[11] CHEN Y N, WEI J F, ZHAO Y Q, SUN J. Effect of semi-solid forging temperature on microstructure and mechanical properties of Ti14 alloy[J]. J of Alloys and Compounds, 2009, 487: 314-320.
[12] GUO Hong-min, YANG Xiang-jie, ZHANG Meng. Microstructure characteristics and mechanical properties of rheoformed wrought aluminum alloy 2024[J]. Trans Nonferrous Met Soc China, 2008, 18 (3): 555-561
[13] KANG C G , SEO P K, KANG S S. The effect of injection velocity on liquid segregation and mechanical properties in arm part fabricated by semi-solid die casting process[J]. J of Materials Processing Technology, 2006, 176: 32-40.
[14] CHO W G , KAN C G , Mechanical properties and their microstructure evaluation in the thixoforming process of semi-solid aluminum alloys[J]. J of Materials Processing Technology, 2000, 105: 269-277.
(Edited by CHEN Ai-hua)
Corresponding author: V. POUYAFAR; Tel: +98-914-4020916; E-mail: vpouyafar@yahoo.com