
Tribological characteristics of C/C-SiC braking composites under
dry and wet conditions
LI Zhuan(李 专)1, XIAO Peng(肖 鹏)1, XIONG Xiang(熊 翔)1, 2, ZHU Su-hua(朱苏华)2
1. State Key Laboratory of Powder Metallurgy, Central South University, Changsha 410083, China;
2. Hunan Boyun New Material Co. Ltd, Changsha 410205, China
Received 8 October 2007; accepted 11 January 2008
Abstract: C/C-SiC braking composites, based on reinforcement of carbon fibers and matrices of carbon and silicon carbide, were fabricated by warm compaction and in situ reaction process. The tribological characteristics of C/C-SiC braking composites under dry and wet conditions were investigated by means of MM-1000 type of friction testing machine. The influence of dry and wet conditions on the tribological characteristics of the C/C-SiC composites was ascertained. Under dry condition, C/C-SiC braking composites show superior tribological characteristics, including high coefficient of friction (0.38), good abrasive resistance (thickness loss is 1.10 μm per cycle) and steady breaking. The main wear mechanism is plastic deformation and abrasion caused by plough. Under wet condition, frictional films form on the worn surface. The coefficient of friction (0.35) could maintain mostly, and the thickness loss (0.70 μm per cycle) reduces to a certain extent. Furthermore, braking curves are steady and adhesion and oxidation are the main wear mechanisms.
Key words: C/C-SiC; wet condition; tribological characteristics; braking composites
1 Introduction
C/C-SiC, carbon fiber reinforced carbon and SiC matrix composite, has been developed to use as braking material since the end of 1990s[1-4]. It is promising candidate for advanced braking system [2]. In comparison with grey cast iron or carbon/carbon, C/C-SiC braking composite exhibits high coefficient of friction(COF), extremely low wear rate, and high thermal shock resistance, especially strong environmental adapta- bility. Some countries, such as China, Germany, America and France have launched its theoretic and applied research gradually[1,5-7]. For example, researchers of Stuttgart University and German Aerospace Center(DLR) have applied C/C-SiC composites to friction domain since the middle of 1990s, and have developed C/C-SiC braking lining applied in 911 Turbo of Porsche.
At present, the main preparation methods of C/C-SiC composites include: 1) a gas phase route, also referred to as chemical vapor infiltration(CVI); 2) a liquid phase route including the polymer impregnation/ pyrolysis(PIP), and liquid silicon infiltration(LSI), also called as (reactive) melt infiltration (RMI or MI) processes, 3) a ceramic route, i.e. a technique combining the impregnation of the reinforcement with a slurry and a sintering step at high temperature and high pressure, also referred to as high pressure-sintering process (HP- Sintering). Each of the formed routes displays advantages and drawbacks. CVI and PIP with long preparation process are mainly used to manufacture thermal structural C/C-SiC composites for spaceflight [8-11]; RMI has the best figuration and short fabrication period, but the cost of preforms is high[12-13]. HP- sintering does harm to carbon fibers and further impacts the composites performance. So preparation method has become an obstruction on the development path of C/C-SiC braking composites. In order to promote the application of C/C-SiC braking composites, the authors invented warm compaction and in situ reaction process (WCISR)[3,6]. C/C-SiC braking composites fabricated by WCISR have successfully applied on magnetic levitation vehicle, high-speed train, advanced car and so on.
Nowadays, reports about C/C-SiC braking composites mainly concentrate under their preparation methods, tribological characteristics on dry condition and application[3,6-7], while reports about tribological characteristics under wet condition are less. However, tribological characteristics under wet condition are key indicators for braking composites[1,3]. In this work, the authors fabricated C/C-SiC braking composites with WCISR, and the different influences of dry and wet conditions on the tribological characteristics of the C/C-SiC composites were studied.
2 Experimental
2.1 Material preparation
Reinforcement was T700 short carbon fiber of Toray with 3-10 mm in length. Matrices were originated from graphite powders (75 μm), furfural resin, agglutinants and Si powders (38 μm, 99.3%). WCISR was based on four steps (as shown in Fig.1). Firstly, these materials were mixed in a fiber-mixing machine. Secondly, the manufacture of C/C-Si green preforms was conducted at moderate temperature and pressure. Thirdly, a subsequent carbonization of the green preforms was carried out at temperature between 800 ℃ and 1 100 ℃, and resin was transformed to resin carbon as parts of carbon matrices. Finally, the C/C-Si green performs had in-situ reaction between 1 500 ℃ and 1 750 ℃ during high temperature treatment(HTT). Thereby, the Si reacted with the carbon matrices and formed SiC matrix which was β-SiC. The density of the resulting C/C-SiC was about 2.0 g/cm3, and the open porosity was about 10%, with 30% β-SiC embedded in the carbon matrices (graphite and resin carbon) and carbon fibers. The content of residual Si lays is below 8%.
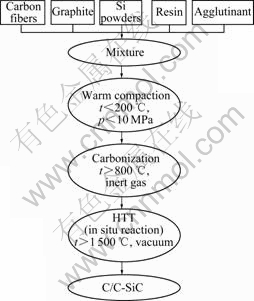
Fig.1 Fabrication process of C/C-SiC braking composites
2.2 Experimental methods
Tribological tests were carried out on a MM-1000 friction testing machine with C/C-SiC composites as static plate and corresponding steel disks as moving plate. The sizes of test specimens and corresponding steel disks were d75 mm(outer diameter)×d53 mm (inner diameter) ×16 mm. The experimental conditions were: the initial linear speed of braking 20 m/s (i.e. rotational speed 6 500 r/min), the running inertia 1 kg·cm·s2, and the braking pressure 0.5 MPa. The experimental conditions were divided into dry condition and wet condition. The tested specimens were soaked in water for 2 min before friction test to simulate wet condition. The tests were performed for 20 cycles under each kind of condition.
The thickness losses of test specimens and corresponding steel disks were measured with the help of the micrometer. The coefficient of friction(COF) was taken as the average value of each cycle. The microstructure of the composites, morphology of worn surfaces and wear debris were examined using POLYVAR-MET type optical microscopy(OM), JSW-5600LV type scanning electron microscopy(SEM) and VANTAGE type energy dispersive analysis of X-ray (EDAX). The components were analyzed by X-ray diffractometry(XRD).
3 Results
3.1 Microstructure of C/C-SiC composites
The C/C-SiC composites fabricated by WCISR have dense and uniform microstructure (as shown in Fig.2). From the EDAX results, it is obvious that the round and filiform components are short carbon fibers that distribute in the composite evenly. The bright white matters are residual Si. The gray regions around residual Si are SiC. Other regions are carbon matrices, including graphite and resin carbon.
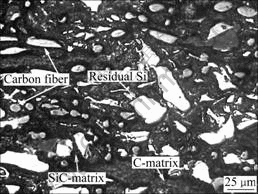
Fig.2 Microstructure of C/C-SiC composites fabricated by WCISR
3.2 Tribological performances
The tribological performances of C/C-SiC composites under dry and wet conditions are listed in Table 1. It is obvious that there is no much difference between dry and wet conditions. The COF (0.35) under wet condition could maintain mostly of that under dry condition (0.38). The COF of the C/C-SiC composites does not decline under wet condition. The C/C-SiC braking composites show strong environmental adaptability which is one of the great advantages in comparison with other braking composites[14]. The main difference is that the thickness loss under wet condition (0.70 μm per cycle) is only two third of that under dry condition (1.10 μm per cycle). The thickness losses of the corresponding steel disks have the same trend as well. Other tribological performances are quite similar.
Table 1 Tribological performances of C/C-SiC under different conditions

3.3 Braking curves on different conditions
The first braking coefficient curves of C/C-SiC composites under dry and wet conditions are shown in Fig.3. It can be seen that two friction coefficient curves are basic consistent, except that the curve under dry condition is rougher (Fig.3(a)). The two braking coefficient curves arise gradually in the beginning period of the braking, appearing the so-called “first peak” phenomenon. Afterward, the COF reduces and the curves tend to change smoothly. At the end of the braking, the COF starts to increase again and the curves have the so-called “rise of the tail” phenomenon.
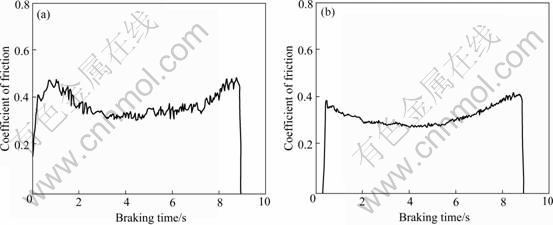
Fig.3 First braking curves of C/C-SiC on different condition: (a) Dry condition; (b) Wet condition
3.4 Morphology of worn debris
Some of the worn debris remain on the worn surface of the tested C/C-SiC composites during braking with a few worn debris adhered to the corresponding steel disk. The SEM photographs of the worn debris under dry and wet conditions are shown in Figs.4(a) and (b), respectively. It can be seen that the worn debris on dry condition are ball-like, appearing to be a typical characteristic of abrasive wear. However, the worn debris on wet condition are flake-like, which means that there are serious sticky sliding and plastic deformation in the braking period.
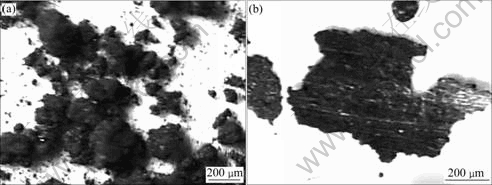
Fig.4 SEM photographs of worn debris of C/C-SiC under different conditions: (a) Dry condition; (b) Wet condition
4 Discussion
Braking is mutually affected by two worn surfaces. The tribological characteristics are usually determined by composite microstructure and worn surfaces under certain braking condition. In this work, the microstructure of the tested C/C-SiC composites is the same while the braking conditions are different. It is certain that the tribological characteristics under wet condition are different from those under dry condition due to the water and worn films.
According to the morphologies of worn surfaces on the C/C-SiC composites, as shown in Fig.5, the photograph under dry condition shows the morphology of grooves (appearing as “plough” in Fig.5(a)). The C/C-SiC composites have many micro convex bodies on the worn surface, including hard SiC phase, resin carbon, and second hard phase Si. During the braking, the micro convex bodies break off under the shearing and compressive force. The hard Si particles can not be cut by the force. They are easily be broken along the interface between Si particles and C/C-SiC composite matrix due to lower plasticity. At the same time, the micro convex bodies scrape the corresponding steel disk, which can be proved by the morphologies of worn sur-face of the corresponding steel disk (Fig.5(b)). These hard particles cause the increase of the COF at the beginning of breaking. After the accommodating period of the two contacted surface, the COF decreases and breaking becomes more steady as seen from their braking curves in Fig.3(a). Additionally, the local surface of C/C-SiC composites adheres to the corresponding steel disk easily due to the lack of self-lubricants.
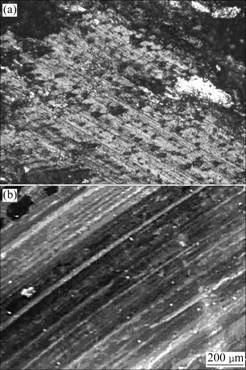
Fig.5 SEM photographs of C/C-SiC worn surfaces and corresponding steel disk under dry condition: (a) C/C-SiC composites; (b) Corresponding steel disk
At the same time, Fe on steel disk reacts with resin carbon or graphite under the condition of higher external stress and temperature[15-16]. Fig.6 shows the XRD result of worn debris of C/C-SiC composites under dry condition. There are Fe3C and FeC. Undoubtedly, Fe and carbon reacted with each other. From the above discussion, it is concluded that the main wear mechanism of the C/C-SiC composites braking under dry condition is plastic deformation and abrasion caused by plough, which leads to unsteady braking curves, ball-like worn debris, high COF (0.38) and thickness loss of 1.10 μm per cycle.
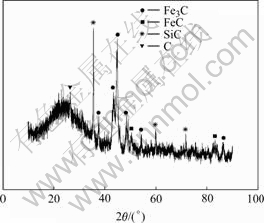
Fig.6 XRD pattern of C/C-SiC worn debris under dry condition
The SEM photograph of the worn surface under wet condition is shown in Fig.7. The grooves are shallow and the worn surface is smooth. Furthermore, there are frictional films attached on the worn surface, and some friction films overlap each other. Under wet condition, SiC matrix reacts with adsorbing moisture that evaporates under friction heat and produces SiO2·xH2O or H2SiO3, and Fe has chemical reaction with water and forms Fe(OH)3 as well[17-18]. Fig.8 shows the EDAX spectrum of frictional film under wet condition. There are Fe and O elements.
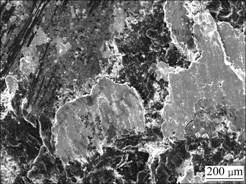
Fig.7 SEM photograph of C/C-SiC worn surface under wet condition
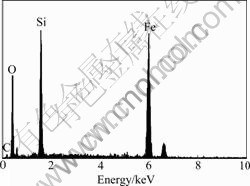
Fig.8 EDAX spectrum of C/C-SiC friction film under wet condition
Nevertheless, these films combine with the subsurface of C/C-SiC composites feebly, leading to low shearing strength and high brittleness. They are difficult to form ultra-slippery surface and tend to break partially into worn debris at the impaction of shearing and compressive forces[19]. On the other hand, these worn debris tend to be reunited or fill the pits in the worn sur- face. The reunited debris are extruded and spread continually until the formation of friction films started again. This process repeats continuously during braking under wet condition. As a result, the C/C-SiC composites braking under wet condition could not only maintain most of their COF under dry condition, but also reduce the thickness losses for themselves and corresponding steel disk to certain extent. Adhesion and oxidation are the primary wear mechanism.
5 Conclusions
1) C/C-SiC braking composites fabricated by WSICR, show superior tribological characteristics, including high COF (0.38), good abrasive resistance (thickness loss is 1.10 μm per cycle) and steady breaking under dry condition.
2) C/C-SiC braking composites have strong environmental adaptability. When braking under wet condition, not only the COF (0.35) of the composites could be mostly maintained compared with that under dry condition, but also the thickness loss (0.70 μm per cycle) is reduced.
3) Frictional films formed on the worn surface of C/C-SiC braking composites under different braking condition have different wear mechanisms. The main wear mechanism under dry condition is plastic deformation and abrasion caused by plough, while adhesion and oxidation are the main mechanisms under wet condition.
Acknowledgements
The authors would like to thank JIANG Nan, Dr. CHEN Jie and Dr. YAN Zhi-qiao of Center South University for their help.
References
[1] KRENKEL W, HEIDENREICH B, RENZ R. C/C-SiC composites for advanced friction systems [J]. Advanced Engineering Materials, 2002, 4(8): 427-436.
[2] GADOW R, KIENZLE A. Processing and manufacturing of C-fiber reinforced SiC-composites for disk brakes [C]// NIIHARA K. Proc 6th Int Symp on Ceramic Mat and Components for Engines. Japan: Arita, 1997: 412-418.
[3] XIAO Peng, XIONG Xiang, ZHANG Hong-bo, HUANG Bai-yun. Progress and application of C/C-SiC ceramic braking materials [J]. The Chinese Journal of Nonferrous Metals, 2005, 15(5): 667-674. (in Chinese)
[4] Developing ceramic materials for heave vehicle brake rotors[EB/OL]. http:// www. trucks. doe. gov/ research/ materials/ CMC-brakes. htm, 2002
[5] KRENKEL W, BERNDT F. C/C-SiC Composites for space applications and advanced friction systems [J]. Materials Science and Engineering A, 2005, 412: 177-181.
[6] XIAO Peng, XIONG Xiang, REN Yun-yun. Effect and mechanism of different components of C/C-SiC composites on friction and wear behavious [J]. The Chinese Journal of Nonferrous Metals, 2005, 15(7): 1040-1044. (in Chinese)
[7] HEIDENREICH B, RENZ R, KRENKEL W. Short fiber reinforced CMC materials for high performance brakes [C]// 4th International Conference on High Temperature Ceramic Matrix Composites (HT-CMC4). Germany: Munich, 2001: 68-74.
[8] XU Yong-dong, ZHANG Li-tong, CHENG Lai-fei. Three dimensional carbon fiber reinforced silicon carbide composites prepared by chemical vapor infiltration [J]. Journal of the Chinese Ceramic Society, 1996, 24(5): 485-489. (in Chinese)
[9] NASLAIN R. CVI composites [M]// Warren R. Ceramic Matrix Composites. London: Chapman and Hall, 1992: 199-243.
[10] GONON M, FANTOZZI G. Densification of SiC/C/SiC composite materials by successive impregnation pyrolysis cycles with an organ metallic precursor [M]// NASLAIN R. High Temperature Ceramic Matrix Composites. Bordeaux: Woodhead, 1993: 437-445.
[11] KIM Y W, SONG J S, PARK S W, LEE J G. Nicalon fiber reinforced silicon carbide composites via polymer solution infiltration and chemical vapor infiltration [J]. J Mater Sci, 1993, 28: 3866-3868.
[12] KRENKEL W. Cost effective processing of CMC composites by melt infiltration (LSI-process) [J]. Ceramic Engineering and Science Proceeding, 2001, 22(3): 443-454.
[13] HILLIG W B. Making ceramic composites by melt infiltration [J]. American Ceramic Society Bulletin, 1994, 73(4): 56-62.
[14] XIONG Xiang, HUANG Bai-yun, XU Hui-juan, JI Dong-ying, PENG Jian-xin. Frictional and wear behaviors of C/C composites from carbon fiber cloth at different braking speeds [J]. The Chinese Journal of Nonferrous Metals, 2002, 12(2): 255-259. (in Chinese)
[15] WEN Shi-zhu. Principles of tribology [M]. Beijing: Tsinghua University Press, 1991. (in Chinese)
[16] WASCHE R, KLAFFKE D. Wear of multiphase SiC based ceramic composites containing free carbon [J]. Wear, 2001, 249: 220-228.
[17] ANDERSSON P. Water-lubricated pin-on-disk tests with ceramics [J]. Wear, 1992, 154: 37-45.
[18] LANCASTER J K, A review on the influence of environmental humidity and water on friction, lubrication and wear [J]. Tribol Int, 1990, 23(6): 371-380.
[19] ZUM GAHR K H. Sliding wear of ceramic–ceramic, ceramic–steel and steel–steel pairs in lubricated and unlubricated contact [J]. Wear, 1989, 133: 1-8.
Foundation item: Project(2006AA03Z560) supported by the Hi-tech Research and Development Program of China; Project(06JJ1007) supported by Excellent Youth of Hunan Province, China
Corresponding author: XIAO Peng; Tel: +86-731-8830131; E-mail: xiaopeng@mail.csu.edu.cn
(Edited by YANG Bing)