Trans. Nonferrous Met. Soc. China 20(2010) s916-s920

Characterization of thixoforming process of 100Cr6 steel
K. P. SO?EK 1, A. RASSILI 2, J. C. PIERRET 2, G. VANEETVELD 2
1. AGH University of Science and Technology, av. Mickiewicza 30, 30-059 Kraków, Poland;
2. Thixo-Unit ULg, PiMW (B56), University of Liège, Bd de Colonster 4, B-4000 Liège, Belgium
Received 13 May 2010; accepted 25 June 2010
Abstract:The main goal of this work is to analyze the semi-industrial process of steel thixoforming. The process was carried out using industrial equipment. This equipment consists of a heating device, industrial robots and a hydraulic press. The globular microstructure ensuring thixotropic properties was obtained using the SIMA method. It is one of the simplest and cheapest methods which could be easy applied in the case of steel alloys. In this work, the hot forged rods, commercially produced from 100Cr6 steel, were used. The first part of the work concerned the determination of the proper temperature range, for thixoforming of 100Cr6 steel. Next, some heating tests were carried out in order to obtain as uniform temperature distribution as possible. Heating process was executed using inductive heating. Microstructure analysis of heated samples reveals globular particles surrounded by liquid phase. At last, the thixoforming process was carried out using closed-die forming technique. Completely filled die cavity and good microstructure of the part show that applied process parameters were properly selected.
Key words: thixoforming; globular microstructure; rheological properties; physical modeling; numerical modeling
1 Introduction
At present, thixoforming processing of steel alloys is mainly investigated in the laboratory scale. It results from lack of the industrial application. In this way, most of important aspects of this technology are analyzed separately. Industrial trials make possible to optimize the process parameters in order to obtain good quality products. Within the confines of this work some industrial trials of steel thixoforming were carried out. During these experiments the heating and forging parameters were determined.
The globular microstructure ensuring thixothropic properties was obtained using the SIMA (strain induced melt activated) method. The SIMA method involves a hot plastic deformation of alloy above the critical reduction and heating to the temperature above the solidus point. In this work, the hot forged rods, commercially produced from 100Cr6 steel, were applied. In the SIMA method recrystallization takes place during heating and melting starts at the boundaries of fine recrystallized grains. Liquid phase is located at high angle grain boundaries and alloy achieves a microstructure consisting of almost spherical solid particles. These particles are separated by a low melting-temperature liquid phase. Among other things the size of these particles depends on chemical composition of the alloy, which determines the solidus-liquidus temperature interval, microstructure at the beginning of melting, heating rate below the solidus and holding time in the semi-liquid state.
Before the experiments some investigations were performed in order to establish proper initial temperature of material, which should be obtained before deformation in the semi-solid state. It is necessary to avoid steel solidification before complete die filling (in the case of too low initial temperature) or phase segregation (in the case of too high initial temperature). At first, the measurement of viscosity versus temperature was done. Next, the thermodynamic calculations were executed in order to determine the liquid fraction versus temperature. Also an observation of the material melting using the high temperature optical microscope was done. In this case it is possible to determine the solidus and liquid flow temperatures (the temperature when the shape of the sample collapses under influence of terrestrial gravity force).
2 Description of material
Prior to thixoforming experiment, a thermodynamic calculation was carried out in order to estimate the solidus and liquidus temperatures, liquid fraction versus temperature and transformation reactions which are caused by phase changes. These calculations were made on the basis of the chemical composition shown in the Table 1. The chemical analysis was carried out using the FOUNDRY-MASTER compact emission spectrometer for process-control and the chemical analysis of metals supplied by Worldwide Analytical Systems AG.
Table 1 Chemical composition of investigated 100Cr6 steel alloy
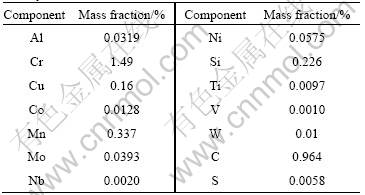
The thermodynamic calculations were made using the ProCAST database. It is a special module used for determination of the phase composition and other thermo-physical properties. The determined liquid fraction versus temperature is shown in Fig.1.
The liquidus and solidus temperatures were determined at 1 457 ?C and 1 132 ?C, respectively.
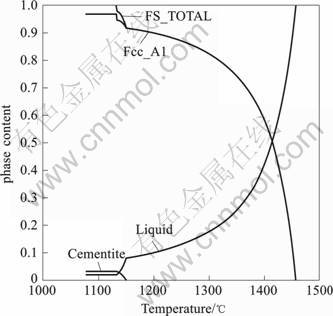
Fig.1 Phase composition of 100Cr6 steel in semi-solid state
Next, an analysis of the steel alloy viscosity was made. The measurement was made using the high temperature viscometer, equipped in the furnace allowing to heat up to 1 600 ?C[1]. This apparatus is shown in Fig. 2.
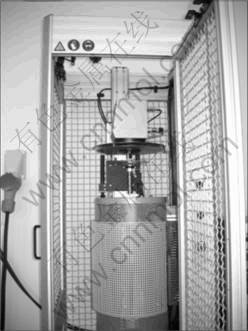
Fig.2 High temperature viscometer
Measurement of the metal viscosity in the semi-solid state is difficult due to high viscosity and relatively high sensitivity of the material even to small changes of temperature. During the measurement, slipping of tested alloys on the tools surface can occur. In order to avoid it, the special crucibles and spindles were designed with profiled surfaces. Their drawings are shown in Fig.3. The apparatus shown in Fig.2 allows to measure relatively high torque, up to 200 mNm. Such torque makes possible to analyze the viscosity of the material which has only 50% of liquid fraction. The measured viscosity of 100Cr6 steel alloy is shown in Fig. 4.
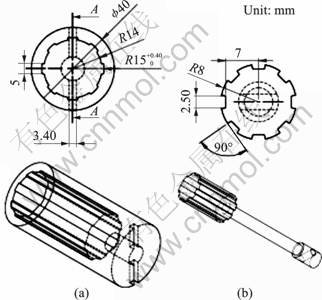
Fig.3 Drawings of crucible (a) and spindle (b) used for viscosity measurement
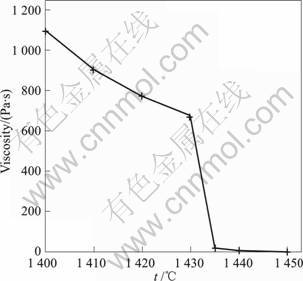
Fig.4 Measured viscosity of 100Cr6 steel alloy versus temperature
The viscosity was investigated for the range of temperature related to 50%-90% liquid fraction. The values of viscosity shown in Fig. 4 were measured for a shear rate of 5 s-1.
At the end, the analysis of the material using high temperature microscope was carried out. The main goal of this analysis was determination of the material behavior in the temperature range between solidus and liquidus points. It allowed determining both deformation and sphere temperatures. Taking into account of thixothropic behavior of the semi-solid steel alloy, the deformation temperature means the softening of the material. The sphere temperature means breaking-up of the solid skeleton. Such results can be useful for determination of shaping temperature range. Measurements were carried out using high temperature optical microscope, Hesse Instruments, model EM 2001. It is a new generation microscope produced by Leitz company, as shown in Fig.5. Shade profiles in a high temperature microscope at deformation and sphere temperatures are shown in Fig.6.
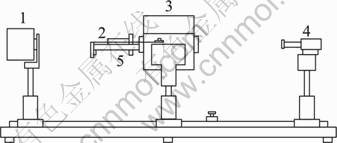
Fig.5 Scheme of high temperature optical microscope EM 2001: 1-Halogen lamp; 2-Specimen t.c.; 3-Furnace with double t.c.; 4-CCD-camera; 5-Specimen carriage
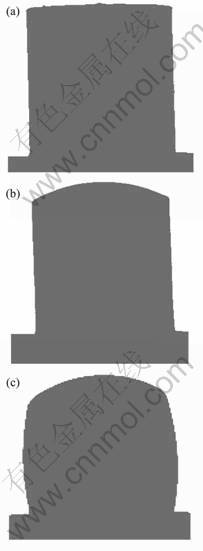
Fig.6 Shade profiles in high temperature microscope at ambient (a), deformation (1 434 ?C) (b) and sphere temperature (1 448 ?C) (c)
On the basis of this material analysis, the initial temperature of the feedstock was determined to be about 1 400 ?C. It corresponds to 40% liquid fraction.
3 Thixoforging experiment
The experiment of 100Cr6 steel thixoforming was carried out using industrial equipment. This equipment consists of a hydraulic press, an inductive heating device and two industrial robots. All these elements can cooperate automatically. It allows obtaining repeatability of the process conditions. The hydraulic press makes possible simultaneous operation of the set of three dies; upper die, lower die and the piston. The lower die, with the cavity used for shaping, is shown in Fig.7. The white stains are remnant of the BN protective layer.
The dies are made entirely from steel. In order to avoid quick destruction of them, the contact with semi-solid steel was limited only to shaping time. Moreover, they were protected from the high temperature of the material by a Boron Nitride layer.
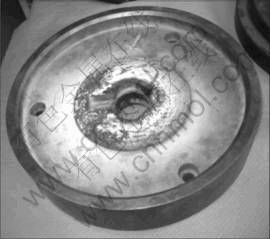
Fig.7 Lower die used for thixoforging experiments with cavity for shapes forging
4 Results
The first part of experimental work was devoted to calibration of the inductive heating device generator. Three heating trials were executed for samples made of 100Cr6 steel. The validation of the heating was carried out on the basis of comparison of measured and assumed temperature. Temperatures were measured at two points; inside of sample and close to lateral surface (see Fig.8). The validation of thermal distribution homogeneity was performed in this way.
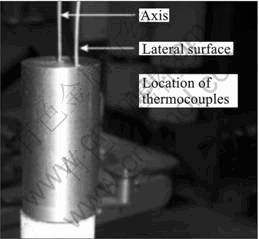
Fig. 8 Location of thermocouples during calibration of heating device
Finally, a three-step heating cycle was established. The heating rate equals 40 ?C/s during first step, 20 ?C /s during second and 1.6 ?C /s during third. The profile of temperature versus time is shown in Fig.9. It is easy to observe that the temperature inhomogeneity is not higher than 10 ?C.
The microstructure of the heated sample shows the solid globular particles surrounded by liquid (Fig.10). Thus, such microstructure can be applied for thixoforming.

Fig. 9 Temperature of sample at axis and by lateral surface
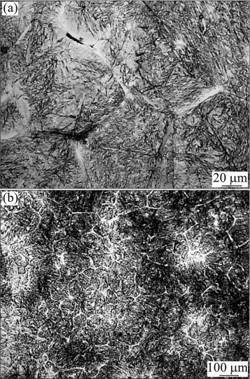
Fig. 10 Microstructures of sample heated to 1400 ?C: (a) High magnification: (b) low magnification
The micrographs seem to be not clear, probably due to natal etching (alcoholic solution of nitric acid 5% HNO3). Ref.[2] suggested to use Bechet and Beaujard's etchant (CrO3-NaOH picric acid solution,), most successful for prior-austenite solution grain with small amount boundaries
The photograph of obtained thixoforged part is shown in Fig.11. The conditions of the process were rather right. A full filling of the dies was achieved. Around this forging one can see thin flash. It appeared in the place of contact of the upper and lower dies. Occurrence of this flash shows that the liquid fraction was too high, and so do the cracks on the part surface. Thus, it is desirable that the liquid fraction should be 20%-30%, not 40% just like in this case.
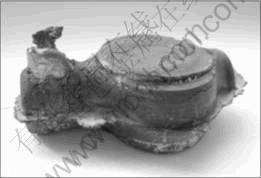
Fig. 11 Part obtained from 100Cr6 steel alloy
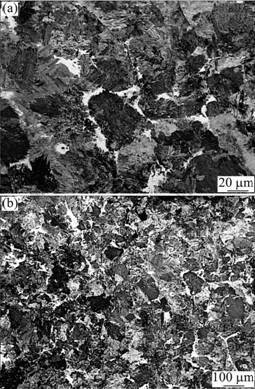
Fig. 12 Microstructures of forging shaped at 1400 ?C: (a) High magnification; (b) Low magnification
The microstructure of the forging shows also the solid globular particles surrounded by liquid (Fig.12). Thus such microstructure proves that applied process parameters are proper for thixoforming.
5 Conclusions
1) Thermodynamic calculation of the liquid fraction versus temperature for 100Cr6 bearing steel shows wide temperature window (1200–1425 ?C) in which semi-solid state occurs (10%-60% liquid fraction).
2) Application of the high temperature viscometer allows to measure relatively high viscosity of semi-solid slurry, even up to 50% liquid fraction.
3) The initial thermo-mechanical treatment of 100Cr6 steel makes possible for obtaining well pronounced globular microstructure surrounded by eutectic. Good results were obtained at relatively high fraction (about 40%) of liquid phase. But results of experiment show that lower liquid fraction should allow avoiding such big flash and decreasing possible phase segregation.
Acknowledgements
The research was supported by Polish Science Financial Resources for years 2007-2010 (common research grant for AGH-UST and IMMS-PAS, No. 28.28.110.7006) and by European Science Foundation (COST Action 541)
References
[1] MEZGER T G. The rheology handbook: For users of rotational and oscillatory rheometers [M]. 2nd ed. Hannover: Vincentz Network, 2006.
[2] ZHANG L, GUO D C. A general etchant for revealing prior-austenite grain boundaries in steels [J]. Materials Characterization, 1993, 30(4): 299-302.
(Edited by YANG Hua)
Foundation item: Projects(AGH-UST and IMMS-PAS, 28.28.110.7006) supported by Polish Science Financial Resources for Years 2007-2010; Project (COST Action 541) Supported by European Science Foundation
Corresponding author: K. P. SO?EK; Tel: +48-12-6172602; E-mail: gmsolek@cyf-kr.edu.pl