J. Cent. South Univ. (2016) 23: 2329-2335
DOI: 10.1007/s11771-016-3291-x

Resistivity and thermal infrared precursors associated with cemented backfill mass
XU Wen-bin(徐文彬)1, 2, HOU Yun-bin(侯运炳)1, SONG Wei-dong(宋卫东)3,
ZHOU Yi-pei(周逸沛)1, YIN Tian-jun(殷天军)1
1. Faculty of Resources & Safety Engineering, China University of Mining &Technology, Beijing 100083, China;
2. State Key Laboratory of Safety and Health for Metal Mines, Ma’anshan 243000, China;
3. School of Civil and Environmental Engineering, University of Science and Technology Beijing,Beijing 100083, China
Central South University Press and Springer-Verlag Berlin Heidelberg 2016
Abstract: The stability of cemented backfill mass is important to keep miners and equipment safe in underground backfill miming. The stress-strain behavior, resistivity and thermal infrared (TIR) characteristics of backfill mass under uniaxial compression were investigated. The monitoring system consisted of a TIR observation system, a stress-strain monitoring system and a resistivity measurement system. Precursory information for impending failure of cemented backfill mass was collected, including TIR, strain and resistivity precursors. The sensitivity and difference of different monitoring information to the same failure event were compared. The results show that the time-space evolution process of the resistivity and TIR is basically the same as the whole process from compression deformation to failure of backfill mass, and the time variation of resistivity and TIR is obviously characterized by stage. The resistivity precursor turns out earlier than the TIR and the strain. The resistivity relation with loading compression is anti-symmetry, decreasing as the compression stress increases before the peak strength of backfill mass. However, when the backfill mass enters into the phase of failure, the resistivity starts to increase as the stress increases. The change of the resistivity growth direction can be regarded as the resistivity-caution-point for the failure of backfill mass under uniaxial compression. It is also indicated that the TIR information mainly represents the surface temperature evolution in the process of compression before the backfill enters into the plastic-yield state. It can be a valuable tool to obtain the precursors for failure of cemented backfill mass for backfill mines.
Key words: cemented backfill mass; thermal infrared characteristic; resistivity; uniaxial compression
1 Introduction
Cemented backfill mining technique is one of the most effective mining methods to release “Three Unders” mineral resource under building, railway and water, to reinvigorate resources and preserve the ecologic environment. Backfill slurry, a certain concentration compounded with water, aggregate (tailings and gangue) and cemented materials, is usually transported to underground mined-out area through pipe. The slurry pumped into the mined-out can gradually coagulate through hydration reaction and finally be solidified into backfill mass. The strength of solidified backfill mass is enhanced, thus preventing the deformation/ subsidence of overburden strata and ensuring the safety of mining operator, equipment in adjacent stope. Therefore, the monitoring and analysis on the mechanical properties and relevant characteristic parameters of cemented backfill mass in the whole process from damage to failure under compression will not only be beneficial to deeply understand backfill mass damage failure mechanism and guarantee safe production in mines, but also lay the foundation for prediction and forecasting method of backfill mass occurrence state. Hence, for mine safety production and a better understanding of cemented backfill mass damage failure mechanism, it is of significant to capture the deformation and failure process of backfill mass and determine its strength and deformation parameters.
Resistivity of rock mass can reflect the conductive ability of pre-existing flaws such as pore, fracture and particle clearance of samples in saturated (unsaturated water) condition. At present, extensive researches are carried out on the resistivity of concrete, rock and soil. Resistivity method is employed to study the hydration process of cement base material, setting time, strength, the effect and influence of admixture [1-3]. A lot of research was carried on the resistivity of rock, and revealed that the resistivity of the rock is proportional to liquid resistivity and inversely proportional to porosity [4-5]. Rock resistance exhibits a significant fluctuation during fracture propagation. Presence of crack and the saturation state of liquid in the rock are the two most important factors controlling the change of the resistivity before rock failure [6]. The method of combining mechanical and electrical parameters is adapted to study the electrical effect of compression stress on sodium chloride solution contained in limestone and sandstone, and the corresponding resistance-strain curve equation is obtained by CHEN et al [7-8]. The change rules of rock resistivity at each stage under uniaxial compression through indoor experiment are obtained by JI et al [9].
Recently, many researchers have reported the infrared radiation energy during the fracture of coal, and rock and concrete [10-14]. However, the abovementioned research results mainly focus on the evolution characteristics of a single parameter (resistivity or temperature) of coal, rock or soil during the whole failure process, which is not convincing. Moreover, little has been conducted in the field of failure behaviors of backfill mass by using the resistivity and thermography technique simultaneously.
In the present work, both infrared thermography and resistivity technique are employed to record the entire deformation process of backfill mass samples. Uniaxial compression tests have been conducted on backfill mass samples, associated with TIR observation system and resistivity measurement system in real time. The strain, resistivity and infrared radiation (IRR) are compared to investigate the precursory characteristic of backfill specimen failure. The objective of the work is to investigate the IRR and resistivity characteristic of backfill mass failure under uniaxial compression.
2 Experiment and methods
2.1 Sample preparation
Raw materials in this test were selected from the backfill bottom flow of an iron mine plant of Wuhan Iron and Steel Corporation, China. The selected backfill minerals consisted of quartz, calcite, chlorite and diopside and a small amount of gypsum, sericite and pyrite. Its chemical components are given in Table 1. As can be seen, the main chemical components in tailings are SiO2, Al2O3, CaO, FeO and MgO, accounting for 61.27%. According to the calculation formula of the mineral chemistry index, the chemical composition is analyzed. We can conclude that its basicity coefficient is 0.56, thus this backfill material can be classified to acidic tailings with quality coefficient standing at 0.90 and activity coefficient at 0.47. According to the quality standard of tailings division, it belongs to the category II. Overall, the average particle size is 45.13 μm and specific surface area is 6400 cm2/g. 56.7% of the particles are less than 25 mm, with median standing at 24 mm. 32.5# cement is used as cementing material.
The cylinder samples are 50 mm in diameter and 100 mm in height. Two sets of samples were prepared with cement-to-sand ratio of 1:6 and 1:8, respectively. The mass fraction is kept at 65%, 68% and 70% for different samples. All the specimens were put in a curing box with temperature keeping at (20±1) °C and relative humidity at 90%.
The size distribution of tailings samples was determined using a LS-C (II A) laser particle size analyzer (Table 2). In general, to retain sufficient water and hence to form a steady fluid paste, the tailings material used in the CPB mixture must conation at least 15% of fine particles (<20 μm in size). Fines (<20 μm) contents of tailings were found to be 53.7%, significantly higher than the threshold level of 15% required to produce a perfect paste slurry. It can be classified as fine tailings.
2.2 Experiment setup and procedure
A synchronized experimental system, composed of a loading control system, a strain gauge, a resistivity monitor and an infrared thermal imaging system, was set up. The electrical material testing apparatus, CSS-44100 with the maximum loading of 60 kN and precision of 0.5%, was used for uniaxial compressing test. The infrared thermal imaging system, IR913A, with a temperature resolution of 0.06 °C, spatial resolution of 1 mrad and graphic resolution of 320×240 pixels, was adopted to detect the temperature changes of the backfill mass samples. The spectral range varied from 8 to 14 μm. The highest graphic recording rate of the TIR system was 50 fps and the images were stored in the computer continuously without size limit of the image file. The strain gauge, DRA-30A, with A/D resolution 112 bit, was adopted to measure the vertical deformation. A resistivity monitor, with A and B electrode at bottom of samples and M, N electrode at 1/4 of specimen near two bottoms, was applied to record the resistivity information automatically [15]. Figure 1 shows the schematic of the experiment system, which is aimed at capturing all the information by resorting the infrared thermography and the resistivity techniques simultaneously and continuously during the entire backfill mass deformation process [15-16].
Table 1 Chemical component of unclassified tailings
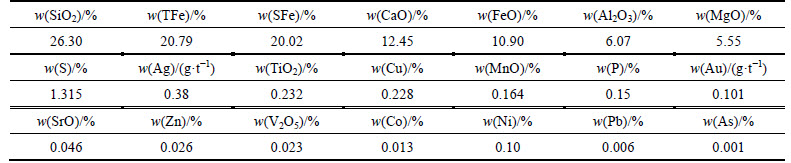
Table 2 Grain size distribution of unclassified tailings used

Before the experiment, the time of different monitoring systems was unified. The TIR monitor apparatus was located 1-1.5 m away from the backfill mass sample. The loading speed was controlled at 0.1 mm/min.
3 Experiment results and discussion
3.1 Stress-strain-resistivity curves of backfill mass under uniaxial compression condition
The loading history is shown in Fig. 2. Figure 2(a) shows one typical example of the axial stress and the resistivity as the functions of the axial strain of cemented backfill mass specimen with cement-to-sand ratio of 1:8, mass fraction of 70% and curing time of 28 d. It is noteworthy that the axial strain and the resistivity have different change characteristics with the increase of the stress. The stress begins to increase steadily but the resistivity decreases gradually before the strain reaches 0.8×10-3 (t=125 s). This implies the closure of interior pore and compaction of loose structure. As the axial strain goes up to 1.82×10-3, the axial stress increases to the peak value and a sudden drop is found, associated with volumetric change in mode. It can be concluded that the unstable crack growth and initiation of macroscopic failure of the backfill mass specimen occur in this stage. This strain level is defined as a precursor of resistivity to the impending failure. Then, before the axial strain increases to 3.45×10-3 (t=345 s), the stress decreases steadily, while the resistivity value climbs up to 320 Ω·m, followed by declining to the lowest value (245 Ω·m). This stage suggests that crack and macroscopic displacement of sample, as shown in Fig. 3. As the axial strain increases beyond 3.45×10-3, the stress fails to 0.45 MPa and the resistivity has a significant increase, peaking at 1050 Ω·m.
Figures 2(b)-(d) illustrate the resistivity of different backfill mass specimens under different conditions. All the curves depicted in Figs. 2(b)-(d) show a similar trend of tress-strain and resistivity–strain behaviors, as compared to Fig. 2(a). This phenomenon is mainly due to the similar inner structure and the stress distribution of the backfill mass specimen.
Figure 2(a) presents a typical resistivity and stress behaviors of different backfill mass specimens during the whole process under uniaxial compression and a diagrammatic sketch of the locations of different precursory stages. The resistivity and stress features can be classified into three types: 1) resistivity decreasing gradually to low value and the stress increasing to peak values, defined as a failure precursor, as shown in the part I and II of curves of Fig. 2(a); 2) resistivity increase starting to increase and then decreasing again and the stress starting to increase and then decreasing again and the stress increasing first, followed by another decrease, showing another failure precursor by low resistivity value, as illustrated in the part III trace of Fig. 2(b); and 3) resistivity starting to increase again with failure precursor by peak value, and the stress continuing to decrease gradually. The results show that the stress and resistivity have different features and precursors for backfill structural damage or impending failure. Likewise, similar tendency is found from the results obtained by the different proportions and mass fraction of backfill masses. Figure 2 comprehensively presents the strain-stress-resistivity feature of backfill mass under the whole uniaxial compression process. It is interesting to note that the resistivity decreases at the beginning and then increases again.
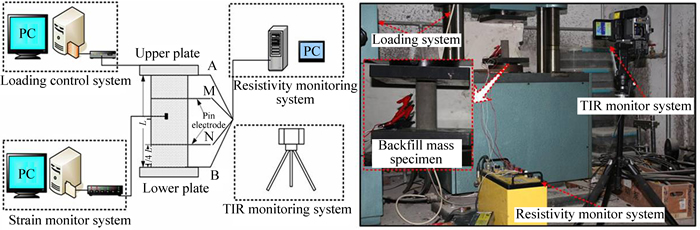
Fig. 1 Component diagram of experiment system setup
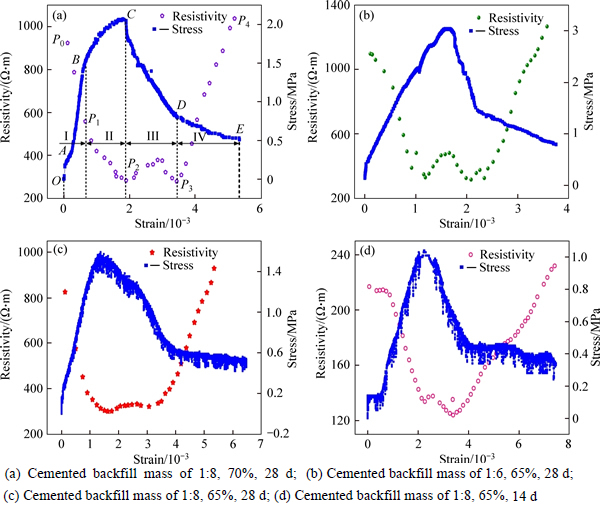
Fig. 2 Monitoring results for uniaxial compression test on different samples:
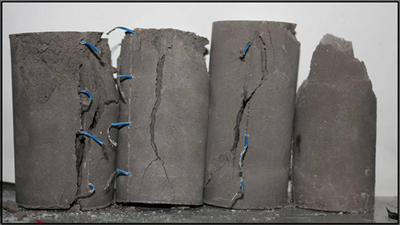
Fig. 3 Failure of some cemented backfill mass samples
3.2 Infrared radiation curves of backfill mass under uniaxial compression condition
Figure 4 shows a typical curve of the average IR temperature (AIRT) in two regions (Monitor point No. 1 and Monitor point No. 2 as shown in Fig. 5) on the sample surface of the cemented backfill mass specimen with cement-to-sand ratio of 1:6, mass fraction of 70% and curing time of 28 d. The curves also indicate that AIRT is a function of time. Figure 4(a) shows that the AIRT at the region No. 1 begins to decrease steadily and then increases again before the loading time increases to 125 s (εa=0.8×10-3). This stage suggests that the compacting of the interior porosity and loose structure lead to discharging fissure air and reducing the surface temperature. This stage (t=125 s, εa=0.8×10-3) is defined as a precursor of AIRT to the impending failure. As the loading time reaches 345 s, the AIRT dropped and failed suddenly after it increased to the peak value. The loading time (t=345 s, εa=3.45×10-3) is defined as another precursor of AIRT to the failure.
Figure 4(b) shows same example of the AIRT at the region NO. 2. Such experimental result indicates that the feature of AIRT failure precursor for different backfill mass specimen is similar to Fig. 4(a). It is characterized that increasing in temperature with failure precursor by low temperature and high temperature respectively, comparison of the resistivity with failure precursor, gets the same results.
As illustrated in Fig. 5, the infrared thermographs indicate that the overall surface TIR temperature decreases first, then changes to increase and finally decreases again. This shows the temperature abnormalities at 125 s and 345 s with corresponding strain levels of 0.8×10-3 and 3.45×10-3, respectively. The occurrence of high infrared thermography temperature at 345 s is associated with the failure of sample and intrinsic energy dissipation. Meanwhile, the AIRT precursors along the fracturing plane as backfill mass fragments striping from the sample can be identified from the IR images (t=312-420 s).
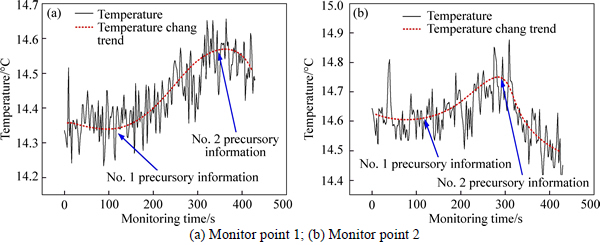
Fig. 4 IR curves of backfill mass specimen at different monitoring regions:
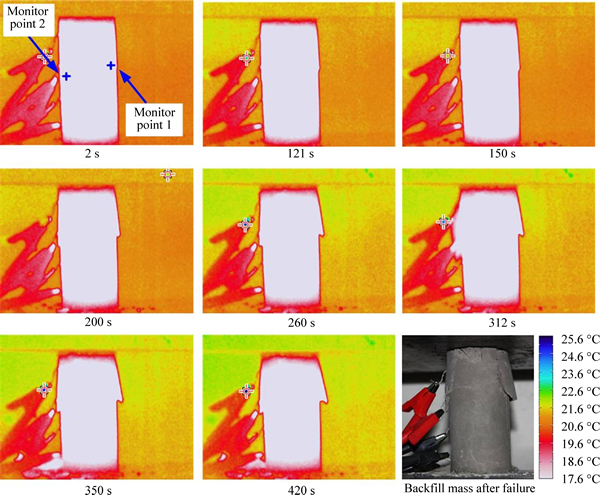
Fig. 5 IR images of cemented backfill mass at different loading times under uniaxial compression
3.3 Quantity analysis and comparison of failure precursor of resistivity
The precursors corresponding to instantaneous backfill mass failure in underground backfilling mines are complex and difficult to be identified. Generally, the time manifestation of various behavior parameters prior to failure is difficult. In this work, to evaluate the sequence of precursors for backfill specimen failure, two precursory events of damage or failure are monitored and selected. The onset time of different precursors for the same event is analyzed comparatively.
To analyze the precursory parameter of backfill mass under uniaxial compression comparatively, the ratio of the critical stress (or resistivity) of backfill mass from elastic state into plastic state to the peak value is defined as the precursor of stress (resistivity) to the impending failure, namely the No. 1 precursor, as shown in Fig. 6. The No. 2 precursor of stress (or resistivity) to the failure of backfill mass is defined by the proportional ratio of the plastic failure stress (or resistivity) to the peak value. The precursory formulae are as follows:




where σle and σp are the critical stress in the state from elastic state into plastic stage, and peak stress, respectively. Its corresponding positions in the strain- stress are the B point and C point in Fig. 6. σs is the yield failure stress, and its corresponding position is D point in Fig. 6; ρle and ρs are the resistivity when the backfill mass turns into plastic stage and yield failure, respectively. Their corresponding positions are P1 and P3 in Fig. 6. ρ0 stands for initial resistivity, and corresponding position is P0 in Fig. 6; λ1 and λ2 are the proportional ratios of the initial and final precursory resistivity, respectively; ω1 and ω2 are the proportional constants of the initial and final precursory stress, respectively.
The statistical results for the uniaxial compression as well as the resistivity and stress precursor are listed in Table 3, based on the abovementioned formula. It is indicated that for the backfill mass specimen with cement-to-sand ratio of 1:6, mass fraction of 65% andcuring time of 28 d, 0.59σp and 0.41σp can be considered as the precursors for the No. 1 precursor and No. 2 precursor events of backfill mass failure under the uniaxial compression, respectively. Meanwhile, 0.45ρ0 and 0.27ρ0 can be taken as the precursors for the No. 1 precursor and No. 2 precursor events of failure shown in Fig. 6. The resistivity precursor seems to turn out earlier than the TIR and the strain. Moreover, the curing time has great influence on the emergence sequence of different precursors to failure. The backfill mass specimen of 14 d curing age takes shorter time to reach the No. 1 stress precursor and more time is needed to get the No. 2 stress precursor.
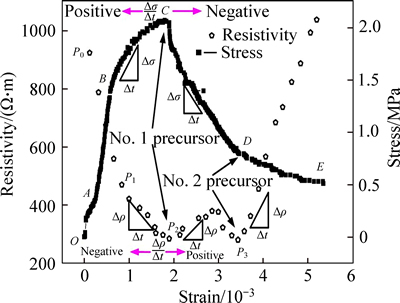
Fig. 6 Position precursor information of cemented backfill mass under uniaxial compression
Table 3 Precursor information of backfill mass under uniaxial compression
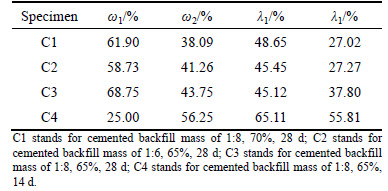
It is also found that there is much resemblance and comparability between the stress-strain precursors, thermal infrared precursors and resistivity precursors. In the early stage of failure, the rate of stress increment is positively correlated to the loading compression. It turns negative after the stress exceeds the peak value. In the later stage after failure, the rate of stress increment is small, and a clear strain softening behavior is shown. On the contrary, the rate of resistivity increment is negative to the uniaxial compression and then turns positive in the early stage before failure. After the failure, the increase rate of resistivity shortly falls to minimum value and then rises to the maximum. The resistivity can provide more comprehensive precursory information to failure of backfill mass. The non-contact too such as IR radiation detection is also a valuable method to acquire the failure precursor on the surface of backfill mass [17]. However, the IR radiation precursors should be analyzed very carefully, because the AIRT of several different regions on sample surface varies considerably from one to another. The above features might be helpful for selecting the multiple tools on evaluating the potential instantaneous failure of backfill mass and for improving the accuracy of evaluation.
4 Conclusions
1) It is revealed that the resistivity shows clear stages along with the compression process. The changing rule of resistivity in every stage is closely related to the internal structure of backfill mass and the subjected stress. Before the failure, the resistivity of the backfill mass gradually decreases with the increases of strain level. In the early post-failure stage, the resistivity first increases then decreases, and eventually the resistivity will see a considerable increase before the failure of backfill mass.
2) The experimental result indicates that the feature of AIRT failure precursor for different backfill mass specimen is similar. It is characterized by increase in temperature with failure precursor by low temperature and high temperature respectively, and comparison of the resistivity with failure precursor.
3) The responses of different monitoring techniques to the backfill specimen failure are different. The results of precursor obtained by three ways of monitoring techniques indicate that resistivity is the most sensitive way compared with AIRT, stress and strain. The AIRT has been proven to be an effective technique to predict the impending failure of backfill mass. However, the AIRT in different regions on the sample surface is mainly focused on the evolution characteristic of backfill mass after being subjected to plastic yield.
4) With the self-designed integrated monitoring system of resistivity, thermal infrared and stress-strain to define multi-parameter change of precursory information to failure in the compression can precisely and comprehensively evaluate the stability state of backfill mass under uniaxial compression, and improve the accuracy of evaluation.
References
[1] WEI Xiao-sheng, XIAO Lian-zhen. Activation energy of Portland cement hydration by electrical resistivity measurement [J]. Journal of the Chinese Ceramic Society, 2011, 39(4): 676-681. (in Chinese)
[2] WEI Xiao-sheng, XIAO Lian-zhen, LI Zong-jin. Hyperbolic method to analyze the electrical resistivity curve of Portland cements with super plasticizer [J]. Journal of Wuhan University of Technology: Materials Science Edition, 2008, 23(2): 245-248. (in Chinese)
[3] LI Zong-jin, XIAO Lian-zhen, WEI Xiao-sheng. Determination of concrete setting time using electrical resistivity measurement [J]. Journal of Materials in Civil Engineering, 2007, 19(5): 423-427.
[4] ARCHIE G E. The electrical resistivity log as an aid in determining some reservoir characteristics [J]. Transactions of American Institute Mining, Metallurgical and Petroleum Engineers, 1942, 14(6): 54-62.
[5] SREEDEEP S,RESHMA A,SINGH D.Generalized relationship for determining soil electrical resistivity from its thermal resistivity [J].Experimental Thermal and Fluid Science, 2005, 29(2): 217-226.
[6] HAO Jin-qi, FENG Rui, ZHOU Jian-guo, QIAN Shu-qing, GAO Jin-tian. Study on the mechanism of resistivity changes during rock cracking [J]. Chinese Journal of Geophysics, 2002, 45(3): 426-434.
[7] CHEN Geng-ye, LIN Yun-mei. Stress–strain–electrical resistance effects and associated state equations for uniaxial rock compression [J]. International Journal of Rock Mechanics & Mining Sciences 2004, 41(2): 223-236.
[8] CHEN Geng-ye, YE Zeng-ping, WANG Yuan, GU Chuan-hong. Relative permeability coefficient of concrete through injecting water and electrical resistance monitoring [J]. Journal of Jilin University (Engineering and Technology Edition), 2006, 36(6): 1019-1024. (in Chinese)
[9] JI Hong-guang, XIANG Peng, ZHANG Lei, HAN Fang, YANG Zhan-jun. Experiment study and detection analysis of mechanical properties variability rock mass in excavation disturbance [J]. Chinese Journal of Rock Mechanics and Engineering, 2011, 30(11): 2352-2359. (in Chinese)
[10] WU L X, WANG J Z. Infrared radiation features of coal and rocks under loading [J]. International Journal of Rock Mechanics & Mining Sciences, 1998, 35(7): 969-976.
[11] WU L X, LIU S J, WU Y H, WU H P. Changes in IR with rock deformation [J]. International Journal of Rock Mechanics & Mining Sciences, 2002, 39(6): 825-831.
[12] LIU Shan-jun, WU Li-xin, ZHANG Yan-bo. Temporal-spatial evolution features of infrared thermal images before rock failure [J]. Journal of Northeast University: Natural Science, 2009, 30(7): 1034-1038. (in Chinese)
[13] LIU Shan-jun, ZHANG Yan-bo, WU Li-xin, LI Guo-liang, CHEN Qun-long. Infrared radiation feature of concrete during fracturing and water seepage process [J]. Chinese Journal of Rock Mechanics and Engineering, 2009, 28(1): 53-58. (in Chinese)
[14] MA Li-qiang, LI Qi-qi, CAO Xin-qi, ZHOU Tao. Variation characteristics of internal infrared radiation temperature of coal-rock mass in compression process [J]. Journal of China University of Mining & Technology, 2013, 42(3): 331-336. (in Chinese)
[15] ZHAO Yi-xin, JIANG Yao-dong, HAN Zhi-ru. Experiment study on acoustic and thermal infrared characteristics of bump-prone coal [J]. Chinese Journal of Rock Mechanics and Engineering, 2007, 26(5): 965-971.
[16] LIU Jie, ZHANG Qian-li, YANG Feng, CHENG Yuan-shui. Test study on the infrared radiation features of high strength concrete during fracturing process under pressure [J]. China Railway Science, 2013, 34(2): 36-40. (in Chinese)
[17] ZHAO Yi-xin, Jiang Yao-dong. Acoustic emission and thermal infrared precursors associated with bump-prone coal failure [J]. Internal Journal of Coal Geology, 2010, 83(1): 11-20.
(Edited by YANG Bing)
Foundation item: Projects(51504256, 51004109) supported by the National Natural Science Foundation of China; Project(zdsys006) supported by State Key Laboratory of Safety and Health for Metal Mines, China; Project(2013BAB02B04) supported by the National Science and Technology Support Plan, China
Received date: 2015-05-06; Accepted date: 2015-06-05
Corresponding author: XU Wen-bin, PhD; Tel: +86-18612987658; E-mail: xuwb08@163.com