Article ID: 1003-6326(2005)06-1322-06
Effects of pyrolysis temperature and fillers on
joining of ceramics via silicone resin
SUO Jun(所 俊), CHEN Zhao-hui(陈朝辉),
ZHENG Wen-wei(郑文伟), HAN Wei-min(韩卫敏)
(Key Laboratory of Advanced Ceramic Fibers and Composites,
College of Aerospace and Materials Engineering, National University of Defense Technology,
Changsha 410073, China)
Abstract: The joining of graphite, ceramic SiC and Cf/SiC composites via preceramic silicone resin(SR) at high temperature (800-1400℃) was studied. The curing and pyrolysis process of SR, pyrolysis temperature, inert and active fillers were especially discussed. The results show that the curing process of SR was accomplished by consuming Si—OH. The temperature of 1200℃ is the appropriate treating temperature for graphite and SiC ceramic, and the temperature of 1400℃ is suitable for Cf/SiC composites. Inert filler SiC powder(5%, mass fraction) has much positive influence on the shear strength of the joints. Active filler nano Ai, Si powder can greatly improve the properties of the joints treated at high temperature. The improvement is over 700%.
Key words: preceramic; silicone resin; pyrolysis temperature; inert filler; active filler; joining CLC
number: TB323 Document code: A
1 INTRODUCTION
Ceramic matrix composites(CMC) have many advantages, such as high strength at high temperature, high rigidity, high wearability, high endurance of chemical erode, and low coefficient of thermal expansion[1, 2]. But it is difficult to manufacture complex ceramic or CMC components. So joining simple components into complex ones is necessary under such a situation. Joining techniques of ceramics and CMC have been researched in the areas of solid phase diffusion, high temperature welding and the methods by the similar mechanisms. The disadvantages of these methods lie in huge energy waste at high temperature, high facility cost of the process, and severe damage to the substrates[3, 4]. Pyro-joining ceramics and CMC with preceramic at high temperature is a relatively new joining process[5-8] which relies on the joining by the ceramic pyrolyzed from the preceramic with enhancing the joining properties of the materials at high temperature. Compared with other methods, it needs low joining temperature, short heat preservation, no pressure and vacuum, which can be widely applied with relatively simple process. The method can also maintain the similar joining phase compared to the substrates. In this paper, joining between 3D-Cf/SiC composites by ceramics pyrolyzed from SR was realized. The influences of pyrolysis temperature, inert and active filler (Si powder and Al/Si nano-powder respectively) were researched. In the mean while, the joining of graphite and SiC ceramic as the components of the 3D-Cf/SiC composites was discussed.
2 EXPERIMENTAL
2.1 Main raw materials
Preceramic SR (chemical pure) is produced by Dow Corning, USA. SiC powder (industrial pure) with average grain diameter of 0.4μ is made by Zhengzhou No.2 Grinding Wheel Works, China. Al nano-powder (average diameter is 30-70nm) with purity of 98%-99.9% is produced by Zhongkangda Nanotech Institute. Si nano-powder (average diameter ≤30nm) with purity over 99% is produced by Institute of Metal Research, Chinese Academy of Sciences. Graphite is produced by Xiangbei Graphite Works. SiC ceramic (relative density 99%) is fabricated by hot press method in the laboratory. 3D-Cf/SiC composites are prepared by precursor infiltration process with carbon fiber (Jilin Carbon Corp., China) as reinforcement and 8∶1∶1 as the fiber volume fraction in X, Y, Z directions. The fiber volume fraction is 45%.
2.2 Experimental process and testing characterization
SR(adding SiC powder or Al/Si nano-powder partially) and ethanol were mixed in solution and daubed on the substrates whose surfaces had been polished and ultrasonically cleaned. Then the joints were cured at 250℃ for 2h and pyrolyzed in Ar atmosphere with heating speed of 2℃/min to a certain temperature. They were cooled down at the same speed. Shear strengths were tested, and infrared ray (IR, Hitachi270-30) spectrum, thermogravimetry analysis(TGA, TAS10-0), X-ray diffraction(XRD, Siemens-D500) and scanning electron microscope(SEM, JSM-5600LV) information were got from the joints.
3 RESULTS AND DISCUSSION
3.1 Curing and pyrolysis of SR
3.1.1 Curing of SR
The IR spectra of SR cured at 250℃ for 2h are shown in Fig.1.
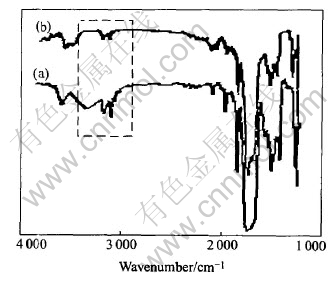
Fig.1 IR spectrums of SR before(a) and after(b) curing at 250℃ for 2h
As illustrated in Fig.1, Si—O—Si bonds are the main chain in general, and —CH3, —OH, —Ph are in the side chains. Evident Si—OH peak exists in 3600-3000cm-1. Comparing curves (a) with (b) in Fig.1, it can be seen that the curing of SR is accomplished by the method of consuming Si—OH. The reaction is

Si—O—Si structure is formed by dehydration reaction in SR. The poly molecules construct a structure of highly cross-linked reticulation that is not melted and dissolved, and gain higher stability and ceramic yield at high temperature.
3.1.2 Pyrolysis of SR
TGA of SR pyrolyzed at 5℃/min is shown in Fig.2. As shown in Fig.2, SR emits molecular fragments and loses its mass gradually with the increasing heating temperature. The remarkable mass loss between 400 and 600℃ is mainly due to the breaks of the side chains of SR and the emitted molecular fragments. With the temperature going up to about 1000℃, the mass-loss ratio reduces to a low level and the former SR changes to Si—O—C ceramic structure.
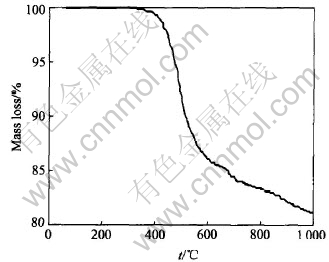
Fig.2 TGA curves of SR
In Fig.3, the XRD curves of Si—O—C ceramics pyrolyzed at 800 and 1000℃ are smooth with a protuberant shape at about 2θ=21°, corresponding to the amorphous C. No SiO2 and SiC crystals exist under thus conditions. Small peaks appearing in the XRD curve at 1200℃ means SiO2 and SiC crystals begin to appear, but most of these matters are amorphous. Under this condition, the crystals are generally small, which is beneficial to the property of the joints[9].
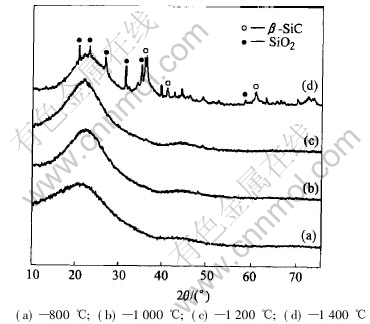
Fig.3 XRD patterns for SR pyrolyzed at different temperatures
3.2 Influence of pyrolysis temperature
Different structures and properties of the joints are achieved at different pyrolysis temperatures. Table 1 lists the properties of the joints achieved from the SR/ethanol solution treated at different temperatures for 5h.
Table 1 Shear strengths of joints made by 4g/mL SR/ethanol solution treated at different temperatures for 5h(MPa)
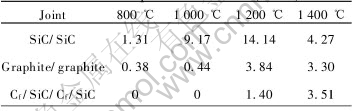
As listed in Table 1, the shear strengths have been enhanced until the temperature of 1200℃, while decrease when the temperature is beyond 1400℃. The structures and properties of Si—O—C ceramics achieved at different pyrolysis temperatures are the main reason of the tendency. The ceramic yield alters from 84% at 800℃ to 78% at 1400℃.
Fig.4 shows the SEM photographs of the joints made by 6g/mL SR/ethanol solution treated for 5h at different temperatures. Fig.4 shows that the higher the pyrolysis temperature is, the thinner the joints are. For instance, the thickness of the bonding layer between graphite treated at 1000℃ is about 40μm, while it is about 5-6μm at 1400℃. The thickness of the bonding layer between Cf/SiC treated at 1200℃ is about 25μm, while it is about 1μm at 1400℃. Suitable thin bonding layer is good for the properties of the joints.
Fig.5 shows the SEM photographs of the joints treated at different temperatures for 5h. The bonding layer treated at 1200℃ is more compact than that at 1400℃ as shown in Fig.5. Although in the bonding layer there are cracks, which are vertical to the interface, they are not the source of cracks in the shear strength test and do no harm to the properties of the joints. The ruptures of the samples treated at 1400℃ often occur in the interface between the bonding layer and the substrates. It is mainly because of the growth of the crystals, loose bonding layer and defects created at such temperature. So the temperature of 1200℃ is the appropriate treating temperature for graphite and SiC ceramic, and the temperature of 1400℃ is suitable for Cf/SiC composites. The reason is probably that the ceramic pyrolyzed from SR is located on the complex and rough surface of the composites to enhance the properties of the joints. Its mechanism is to be further investigated in the future research.
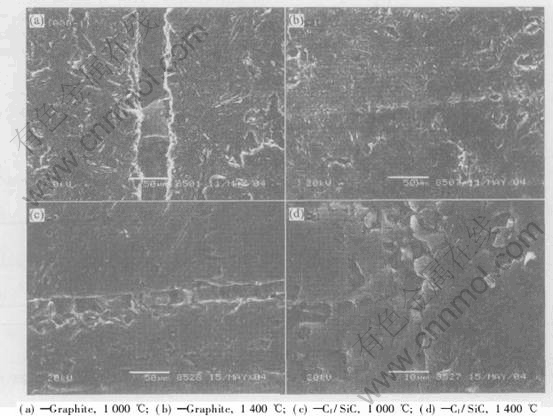
Fig.4 SEM photographs of joints made at different temperatures(6g/mL SR/ethanol with heating rate 2℃/min)
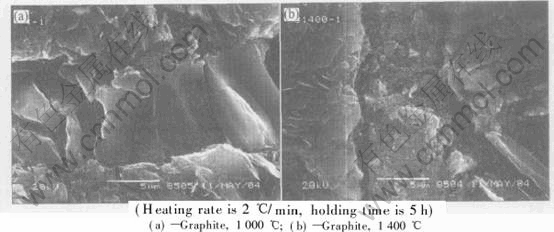
Fig.5 SEM photographs of joints made at different temperatures
3.3 Influence of inert filler
Appropriate amount of inert filler SiC powder is added into the SR/ethanol solution to decrease the volume shrinkage of the Si—O—C ceramic during the process of the pyrolysis.
The shear strengths of the joints with different contents of SiC powder treated at 1400℃ for 2h with heating rate of 2℃/min are shown in Table 2.
Table 2 Shear strengths of joints with SiC powder
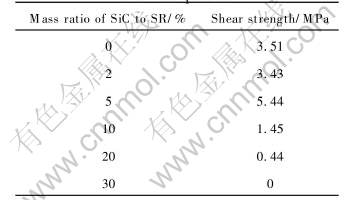
Table 2 indicates that adding SiC powder greatly influences the shear strength of the joints. The main mechanism of inert filler SiC powder enhancing the properties is to restrict the volume shrinks of the Si—O—C ceramic during the pyrolysis. When the mass fractions of SiC powder are too low, the powder can not control the volume shrinks of the SR, but is just the impurity in the ceramic which decreases the properties of the joints. Too high mass fraction of SiC powder decreases the mass fractions of the pyrolyzed ceramic, and increases the probability of SiC powder existing at the surface of the joints, which decreases the actual contacting area and the properties of the joints[10]. Furthermore, too much SiC powder also makes the bonding layer much thicker, which will increase the appearing probability of cracks and defects, and decrease the properties of the joints. Deduced from Ref.[11], the critical volume fractions (which make the volume shrinkage 0 when the preceramic is pyrolyzed) of the preceramic and the inert filler φ(SR, c) and φ(IF, c) are
φ(SR, c)=q/(1-αβ)(2)
φ(IF, c)=1- q/(1-αβ)(3)
where q is the pore fraction, α is the mass ratio of the ceramic and the preceramic, i.e. ceramic yield. β is the density ratio of the preceramic and the ceramic. In the paper, q≈0.56, α≈0.83, β≈0.51, so φ(IF, c)≈0.02. The critical mass fraction is converted to be 0.05. The calculating result accords with the experimental test. That is to say, low shrinkage of the preceramic in the process of the pyrolysis is an important factor to enhance the properties of the joints.
3.4 Influence of active filler
Active filler can react with the production of the pyrolysis and the protective atmosphere, and enhance the ceramic yield of the preceramic. The result of the reaction is to form new ceramic phase and change the volume. So adding active filler is an effective method to increase the ceramic yield of the preceramic, and decrease volume shrinkage and the pore fraction. SR/ethanol solution(SR/Al-Si=1.67(mass ratio, %, the same below), Al/Si=80/20) with nano Al and Si powder is used to make the joints treated at 1200℃ for 1h with heating rate 2℃/min.
The ceramic yield of SR with nano active filler is enhanced from 82% to 96% measured by tests, which is beneficial to increase the densification and decrease the pore fraction in the ceramic.
Table 3 shows that the active filler enhances the shear strengths of the joints. The reactions that may occur during the pyrolysis of the SR with
Table 3 Influence of inert and active fillers on shear strength
nano Al, Si powder as
4Al+3SiO2→2Al2O3+3Si(4)
4Al+3C→Al4C3(5)
3Si+Al4C3→4Al+3SiC(6)
Si+C→SiC(7)
According to[13]

According to the raw data in Ref.[13], the changes of Gibbs functions of the reactions during 800 to 1400℃ are shown in Table 4.
Table 4 Gibbs functions of reactions between SR and active fillers at different temperatures(kJ/mol)
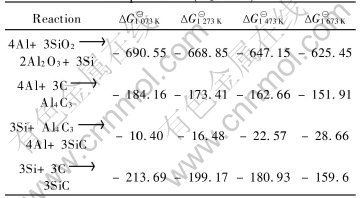
Table 4 indicates that Reactions (4) and (7) have relatively great tendency to occur at appropriate temperature. However, the reaction to produce harmful phase Al4C3 is relatively not easy to occur.
Fig.6 shows the SEM image of the leftover of the active filler in the ceramic pyrolyzed from SR. It can be seen from Fig.6 that the Si—O—C ceramic is very compact. Some leftover of the nano powder (be reunited) does not have much influence on the integrality and the density of the ceramic.
Fig.6 SEM image of pyrolyzed SR added with active filler
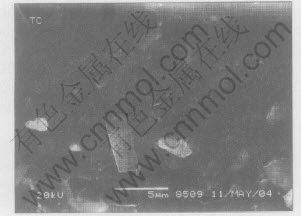
Fig.7 shows the XRD patterns of the ceramics pyrolyzed from SR treated at 1200℃. There are peaks of Si, Al4C3 and Al besides the peaks of Al2O3, SiC and SiO2 anticipated in the patterns. The chemical ratio of the active filler is inappropriate to make some reactants directing the left[15].
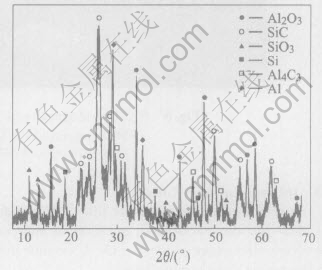
Fig.7 XRD pattern for pyrolyzed SR added with active fillers
4 CONCLUSIONS
The curing of SR is accomplished by consuming Si—OH. The main mass loss occurs between 400℃ and 600℃. With the temperature going up to about 1 000℃, the mass-loss ratio reduces to a low level and the former SR changes to Si—O—C ceramic structure. Effective joining at high temperature is realized by Si—O—C ceramic pyrolyzed from SR/ethanol solution. The temperature of 1200℃ is the appropriate treating temperature for graphite and SiC ceramic, and the temperature of 1400℃ is suitable for Cf/SiC composites. Inert filler SiC powder (5%) has much positive influence on the shear strength of the joints. Active filler nano Al, Si powder can greatly improve the properties of the joints treated at high temperature. The improvement is over 700%.
REFERENCES
[1]Kikuo N. Fabrication and characterization of three dimensional carbon fiber reinforced silicon carbide and silicon nitride composites [J]. Journal of American Ceramic Society, 1995, 78(10): 2811-2814.
[2]Riccitiello S. 3-D ceramic matrix composite development [J]. Journal of Advanced Materials,1994, 1: 22-26.
[3]REN Jia-lie, WU Ai-ping. Joining of Advanced Materials [M]. Beijing: Mechanical Industry Press, 2000. 153.(in Chinese)
[4]Seyferth D. Pre-ceramic polymers: past, present and future [J]. Materials Chemistry, 1995, 245(2): 131-160.
[5]Colombo P, Riccardi B, Donato A, et al. Joining of SiC/SiCf ceramic matrix composites for fusion reactor blanket application [J]. Journal of Nuclear Materials, 2000, 278: 127-135.
[6]Colombo P, Sglavo V, Pippel E, et al. Joining of reaction-bonding silicon carbide using a preceramic polymer [J]. Journal of Materials Science, 1998, 33: 2405-2412.
[7]Pippel E, Woltersdorf J, Colombo P, et al. Structure and composition of interlayers in joints between SiC bodies [J]. Journal of European Ceramic Society, 1997, 17: 1259-1265.
[8]Sherwood W J, Whitmarsh C K, Jacobs J M, et al. Joining ceramic composites using active metal/HPCS preceramic polymer slurries [J]. Ceramic Engineering and Science Proceeding, 1997, 18(3A): 177-184.
[9]WANG Ling-sen. Special Ceramics [M]. Changsha: Central South University of Technology Press, 1998. 218.(in Chinese)
[10]Rice R W. Effects of amount, location, and character of porosity on stiffness and strength of ceramic fiber composites via different processing [J]. Journal of Materials Science, 1999, 34(13): 2769-2772.
[11]XIE Zheng-fang, CHEN Zhao-hui. Dimensional change models for active filler-controlled preceramic polymer pyrolysis [J]. Acta Metallurgica Sinica, 2002, 38(4): 443-448.(in Chinese)
[12]SHI Jun. Handbook of Chemical Engineering (Part A) [M]. 2nd ed. Beijing: Chemical Industry Press, 2002. 1-101.(in Chinese)
[13]Dean J A. Langes Handbook of Chemistry [M]. 15th ed. Beijing: Science Press, 2002.(in Chinese)
[14]SUO Jun, CHEN Zhao-hui, HAN Wei-min, et al. Pyro-joining of Cf/SiC composites via preceramic silicone resin—influence of inert and active fillers on joining properties [J]. Acta Materiae Compositae Sinica, 2005, 4: 435-439.(in Chinese)
(Edited by LONG Huai-zhong)
Foundation item: Project(04JJY3002) supported by the Natural Science Foundation of Hunan Province, China
Received date: 2005-03-03; Accepted date: 2005-08-24
Correspondence: SUO Jun, PhD candidate; Tel: +86-731-4576441; E-mail: mrsuo@163.com